Проектирование автоматической переборной коробки для обрабатывающего центра


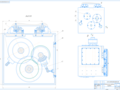
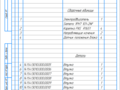
- Добавлен: 24.01.2023
- Размер: 2 MB
- Закачек: 0
Узнать, как скачать этот материал
Подписаться на ежедневные обновления каталога:
Описание
Проектирование автоматической переборной коробки для обрабатывающего центра
Состав проекта
![]() |
![]() ![]() ![]() ![]() |
![]() ![]() ![]() |
![]() ![]() ![]() ![]() |
Дополнительная информация
Контент чертежей
апк+свертка.cdw

кмм_пояснилка.doc
Основу автоматизации производства составляют станки с числовым программным управлением (ЧПУ) робототехнические комплексы (РТК) автоматизированные транспортно-складские системы (АТСС) и гибкие производственные системы (ГПС).
Современные темпы развития средств автоматизации и различных технологических средств вызывают существенные изменения в сфере производства всех отраслей промышленности. Это связано главным образом с постоянным совершенствованием и обновлением образцов продукции. Проблема постоянного обновления продукции а связи с этим необходимость систематической перестройки производства особенно остро стоит пред предприятиями отечественного машиностроения.
Для современного машиностроения характерно значительное увеличение объёмов продукции выпускаемой в условиях единичного мелкосерийного и серийного производства. В связи с этим наряду с решением проблем автоматизации определяющее значение приобретают задачи обеспечения гибкости производственных систем способных оперативно перестраиваться на выпуск новой продукции. Мехатронные станочные системы (МХСС) как станки с адаптивно-программным управлением являются более гибкими «переобучаемыми» по сравнению с обычными станками с ЧПУ.
Для обработки на станках деталей машин с разными размерами и режущим инструментом с различными режущими свойствами при большом числе технологических операций для получения оптимальных режимов резания необходимо изменять частоты вращения шпинделя в пределах от nmin до nmax.
Между наибольшей и наименьшей частотами вращения шпинделя промежуточные частоты могут быть расположены бесступенчато (плавно) или ступенчато (прерывисто). Применение бесступенчатого регулирования частоты вращения даёт возможность более просто осуществить оптимальные режимы резания. С применением бесступенчатого регулирования конструкция станка упрощается. В качестве электрического бесступенчатого привода применяют электродвигатели постоянного тока.
Ступенчатое регулирование даёт возможность установить ограниченное число частот вращения в заданных пределах. По этой причине величина регулирования не всегда может быть установлена оптимальной. Механизмы со ступенчатым регулированием компактны просты и имеют более высокий КПД по сравнению с бесступенчатым регулированием.
Проектирование модулей выполняется с целью закрепления теоретических знаний и приобретения практических навыков в области разработки станков с компьютерным управлением. Тематика курсового проектирования охватывает разработку мехатронных модулей на уровне элементов эскизного и технического проектов.
При создании современного станочного оборудования многими ведущими станкостроительными фирмами используется агрегатно–модульный принцип проектирования который позволяет повысить технологические возможности выпускаемого оборудования и снизить его стоимость. Этот принцип используется при разработке отдельных станков (в виде сочетания конструктивных модулей) и автоматизированных комплексов (в виде технологических модулей).
Анализ конструкции обрабатываемых деталей и уточнение технологии изготовления детали представителя.
Эскиз детали представителя.
Деталь используется в топливной системе авиационного двигателя АЛ-31Ф.
Наиболее ответственными являются торцевые поверхности детали так как они используются для образования сварных соединений.
Особенностью данной детали является наклонное отверстие для работы контрольного датчика.
Рис.1 Эскиз детали представителя
Материал детали и ее характеристики.
Деталь изготавливается по 7 квалитету точности шероховатость = 32. Предельные диаметры обработки детали – представителя:
Dma Dmin= 45 мм для группы деталей примем Dma Dmin= 45 мм.
Материал детали: титановый литейный сплав ВТ20Л ГОСТ 4832-95:
Процентное содержание элементов: [13]
Алюминий: 55 – 75 %;
Маршрут обработки по базовому технологическому процессу.
Таблица 1. Базовый технологический процесс.
Наименование операции.
Уточненный маршрут обработки.
Цель уточнения стандартной технологии: применение нового более совершенного оборудования как с точки зрения производительности так и с точки зрения качества и точности изготавливаемых деталей
В качестве основного станка для обработки принят станок вертикальный сверлильно-фрезерно-расточной с ЧПУ модели 400VS Стерлитамакского М.Т.Е.
Применение этого станка позволяет максимально концентрировать операции.
Главное удобство этого станка при обработке данной детали – возможность поворота заготовки что позволяет выполнять сверлильную операцию 45 без использования дополнительной оснастки. Система ЧПУ станка позволяет проводить операции сверления без использования кондуктора.
Рис. 2 Координатное сверление.
Таблица 2. Уточненный маршрут обработки.
Проектируемый станок
Выполняемые переходы обработки на проектируемом станке.
Фрезерование плоскостное;
Сверление координатное;
Точение продольное точение поперечное.
Определение основных технических характеристик модуля.
Основные технологические условия использования станка.
Обрабатываемые материалы и их предельные характеристики:
- титановый сплав ВТ20Л МПа;
- конструкционные стали sв = 440 МПа.
Основные переходы обработки: точение продольное и поперечное фрезерование плоское сверление.
- чистовая с глубиной резания t = 05 мм.
Вид материала режущей части инструмента: твердый сплав ВК6М ГОСТ 17163-90.
Предельные диаметры обработки: Dma Dmin= 45 мм.
Характерные сочетания технологических условий.
К этим сочетаниям относятся условия определяющие vmin Sma
Определение значений предельных режимов резания и наибольшей (расчетной) эффективной мощности.
Наибольшая подача Smax определяется по ([8] Таблице 2) согласно установленным характерным условиям обработки детали. Для чистового продольного точения титанового сплава (sв = 900 МПа в таблице 1 не учитывается) при диаметре обработки dmaх = 180 мм при использовании резца с пластиной из твердого сплава Т15К6 с вспомогательным углом в плане φ = 5 градусов с радиусом при вершине резца 05 мм принимаем подачу S =033 ммоб. Скорость резания назначаем по ([8] Таблица 4) с учетом характера обработки и физических характеристик материала. Принимаем V = 182 ммин при глубине резания t до 14 мм. Наибольшая скорость резания так же находится по. Для чистового поперечного точения конструкционной стали (sв = 440 МПа) с учетом глубины резания tmax = 05 мм (по ([8] Таблица 4) наименьшее значение составляет 14 мм) с наименьшей подачей 017 ммоб (по таблице 4 наименьшее значение составляет 025 ммоб) определяется vmax = 518 ммин.
Подача на зуб фрезы S ммзуб и скорость резания V ммин определяется по ([8] Таблица 1) согласно установленным характерным условиям обработки детали. Для фрезерования титанового сплава ВТ20Л наибольший диаметр фрезы dmax = 07 ×В (где В -наибольшая ширина детали)=07*18=126 мм dmin = 01 × dmax =126 мм. При использовании торцевой фрезы фирмы Sandvik Coromant R252.44 с пластинами твердого сплава SM30 без покрытия примем подачу на зуб равной S=01 ммзуб скорость резания V=70 ммин. ([8] Таблица 4)
Скорость резания V ммин и подача S ммоб определяется по согласно установленным характерным условиям обработки. Для сверления титанового сплава ВТ20Л цельными твердосплавными сверлами назначаем V = 8 ммин S = 002 ммоб.
Скорость резания V ммин и подача S ммоб определяется по Таблице 5[6] согласно установленным характерным условиям обработки. Для зенкерования конструкционной стали назначаем подачу S = 05 ммоб. По таблице (с учетом диаметра зенкера D мм и глубины резания t) принимаем V = 173 ммин.
Наибольшее (расчетное) значение эффективной мощности резания определяется при помощи программы «Rezim» [8] для условий обработки соответствующих vmin. При чистовом продольном точении титанового сплава (sв = 900 МПа) заготовки c диаметром D = 180 мм твердосплавным резцом с t = 05 мм S = 033 ммоб V = 182 ммин эффективная мощность резания Nэф = 85 кВт.
Так же необходимо найти эффективную мощность привода обеспечивающего вращательное движение сверла (зенкера метчика фрезы) – при токарной обработки на станках подобного типа вращение передается столу. При сверлении титанового сплава твердосплавным сверлом Nэф= 68 кВт.
Определение расчетных значений технических характеристик модуля.
Предельные частоты вращения стола определяются по формулам:
Мощность приводного электродвигателя стола:
где h - к.п.д. привода ориентировочно h = 08; kп – допускаемый коэффициент перегрузки двигателя kп = 08; при указанных коэффициентах Nэл = Nэф.
Предельные частоты вращения шпинделя станка также находятся по формулам (1) (2):
Максимальный и минимальный диаметры обработки взяты непосредственно с чертежа детали-представителя.
Анализ технических характеристик модулей аналогичных станков.
Таблица 3. Технические характеристики станков – аналогов.
Способ регулирования
частот вращения шпинделя z (количество передач)
Пределы частот вращения шпинделя
Мощность главного привода
Бесступенчатый в пределах 2 диапазонов
Типоразмерами данных станков (сверлильно-фрезерно-расточных) принимаются размеры стола.
Уточнение технических характеристик проектируемого модуля станка.
На основании таблицы 3 принимаем следующее:
)предельные частоты вращения шпинделя: 63 – 3150 обмин;
)мощность привода главного движения: 7 кВт;
)предельные частоты вращения стола: 0 – 4000 обмин;
)мощность привода стола: 85 кВт.
Выбранные технические характеристики проектируемого модуля станка позволяют обработать всю заданную гамму деталей изготовленных из титановых сплавов и конструкционных сталей. Режимы резания подбирались из условия обеспечения высокой точности и качества обработанной поверхности.
В рамках данной работы будет проектироваться шпиндель и привод главного движения.
Определение компоновок станка и модуля.
Для станка наиболее выгодно применение консольной компоновки. В этом случае станок занимает на 35 – 40 % меньшую площадь чем при портальной компоновке. Кроме того стол является неподвижным что обеспечивает высокую точность позиционирования. В качестве компоновки привода шпинделя принимаем раздельную компоновку (указано в задании на проектирование). Раздельная компоновка отличается выполнением коробки передач раздельно со шпиндельным узлом. Совместно со шпинделем выполняется переборная коробка.
Рис 3. Компоновка станка
– станина станка 2 – стол (перемещается продольно) 3 – поворотный стол (вращение вокруг вертикальной оси и поворот относительно горизонтальной оси) 4 – колонна (перемещается поперечно) 5 – шпиндельная бабка (вертикальное перемещение).
Подобная компоновка привода применяется в станке 2Р135Ф2.
Структура привода проектируемого модуля: сложенная.
Сложенные структуры позволяют обеспечивать большие диапазоны регулирования коробок скоростей при этом все значения передаточных отношений находятся в требуемых пределах. В этих структурах высокие скорости получаются с помощью коротких кинематических цепей что увеличивает КПД привода.
В выполняемой курсовой работе сложенную структуру имеет только переборная коробка коробка передач выполняется с нормальной множительной структурой.
Определение функциональных подсистем проектируемого модуля и разработка его структуры.
Тип проектируемого модуля: простой модуль главного движения.
Анализ схем обработки:
Таблица 4.Анализ схем обработки.
Метод формообразования
исполнительных движений
Фрезерование плоскостное
Метод следа и касания
Изменение частоты вращения
при изменении температуры резания и колебаний упругой системы станка с целью предотвращения резонансного режима работы.
Метод копирования и следа
Определение функциональных подсистем модуля.
Определим функциональные подсистемы модуля главного движения станка – аналога:
Таблица 5. Состав функциональных подсистем модуля станка аналога.
Простой модуль главного движения
РД1 [(1ПО1)ВН11СП11]
С учетом особенностей конструкции кинематики анализируемого станка и управления его работой при выполнении заданного перехода и с использованием классификации [5] определены функциональные подсистемы заданного модуля (Таблица 6).
По сравнению с станком – аналогом в состав модуля введены следующие подсистемы: обеспечения перемещения ПМ включающего в себя подсистему 3 уровня ВП (величины перемещения). Подсистема 3 уровня СТ (стабилизации скорости) заменена на подсистему 3 уровня ИС (изменения скорости в процессе обработки). Данные изменения проведены с целью достижения повышенной точности изготавливаемых деталей и наименьшей шероховатости поверхности.
Таблица 6 Функциональные подсистемы проектируемого модуля
Простой модуль главного движения (привод шпинделя)
ПО1 [П11УП11ТП11О11]
ПМ1[ВП11 (1ПО1) (1РД1) (1СД1) ]
С учетом станка – аналога и необходимых функциональных подсистем разработана блок – схема проектируемого модуля ( Рис. 4)
Рис. 4. Блок – схема проектируемого модуля.
ДС1 ДС2 – датчики скорости; ДТ – датчик температуры резания.
Использование датчика температуры резания позволяет контролировать температуру резания два датчика скорости обеспечивают контроль за скоростью вращения шпинделя что позволяет повысить точность и качество изготавливаемых деталей.
Рис. 5. Структура модуля главного движения
ЭД – электродвигатель; ПК – переборная коробка.
На Рис.5. показана структура модуля главного движения с учетом повышения точности изготавливаемых деталей. Структура данного модуля отличается от модуля станка – аналога введением дополнительных датчиков скорости и температуры резания и введением подсистемы обеспечения перемещения ПМ. Также введен дополнительный датчик колебаний ДК.
Разработка кинематической схемы модуля.
Выбор электродвигателя.
На основании данных полученных при определении технических характеристик модуля выбираем двигатель 105 – 2NF фирмы Siemens
Таблица 7. Характеристики электродвигателя привода.
Номинальный момент вращения
Определение диапазонов регулирования с постоянной мощностью и постоянным моментом.
Диапазон регулирования с постоянной мощностью:
где b=4 для фрезерных станков Rp = 315063 = 50
Диапазон регулирования с постоянным моментом:
Определение диапазона регулирования двигателя по полю с постоянной мощностью.
Диапазону регулирования двигателя по полю с постоянной мощностью определяется как отношение максимальных оборотов двигателя к номинальным:
Определение знаменателя ряда регулирования и числа ступеней переборной коробки.
Первоначально знаменатель ряда принимается равным диапазону регулирования двигателя по полю с постоянной мощностью .
Расчетное число ступеней коробки определяется по формуле:
Полученное расчетное число ступеней коробки округляется в большую сторону до целого числа: =3.
Уточняем знаменатель ряда регулирования:
Уточнение характеристик электродвигателя.
Уточнение диапазона регулирования электродвигателя:
Уточним минимальную и максимальную частоту вращения электродвигателя:
- минимальная частота вращения электродвигателя:
- максимальная частота вращения электродвигателя:
Определение характерных частот вращения шпинделя.
Определение компоновки АПК и построение структурной сетки.
Для сложенной структуры переборной коробки и нормальной структуры коробки перемены передач для полученного числа ступеней подойдет следующая структурная формула:
Z = 12121 1(1+1121) = 4(3)
Рис. 6. Принципиальная кинематическая схема привода.
Для обеспечения требуемых 3 ступеней одна передача принудительно блокируется. Блокируемая передача определяется непосредственно из структурной сетки.
Построим структурную сетку:
Рис. 7. Структурная сетка.
Блокируется передача работающая на более низких частотах вращения что позволяет снизить изгибающие моменты.
Далее строим график частот вращения шпинделя:
Рис.8 График частот вращения валов.
Утолщенной линией показана расчетная кинематическая цепь.
Используя график определяем передаточные отношения привода.
Далее пользуясь табличным методом определяем числа зубьев для каждой зубчатой передачи. Принимаем суммарное количество зубьев для зубчатого зацепления в коробке передач: в переборной коробке: . Тогда:
- для передачи i4: z7=26 и z8=41.
Затем выполняется проверка кинематического расчета. Определяются фактические частоты вращения с учетом принятых чисел зубьев.
Определим погрешности:
Условием проверки является неравенство
При . Условие проверки выполняется.
Проектирование автоматической переборной коробки.
1. Расчет мощностей на валах.
Мощность на первом валу:
Мощность на втором валу:
Мощность на третьем валу:
Мощность на четвертом валу:
Мощность на пятом валу:
В приведенных выше формулах
- кпд ременной передачи принимаем =098;
- кпд подшипников качения =0995;
- кпд зубчатой передачи =097 099 принимаем =099.
2. Расчет моментов на валах.
Момент на i-том валу определяется по формуле:
где -расчётная частота на i-том валу.
3. Проектный расчет валов.
Минимальный диаметр вала определяется в зависимости от крутящего момента на нём:
где - допустимое напряжения на кручение;=10 15 Нмм2.
Получаем минимальные диаметры валов:
4. Проектный расчет зубчатых передач.
Выбираем материал для зубчатых колес: сталь 40ХН закалка ТВЧ сквозная с охватом впадины допускаемое контактное напряжение допускаемое изгибное напряжение .
Расчёт модулей для зубчатых колёс выполняется по контактным и изгибным напряжениям по формулам:
- для контактной прочности
где Kd – вспомогательный коэффициент; для прямозубых передач Kd = 770;
z1 – число зубьев шестерни;
T1 – вращающий момент на шестерне Н×м;
u – передаточное отношение передачи;
sН – допускаемое контактное напряжение МПа;
KHb – коэффициент учитывающий распределение нагрузки по ширине венца;
где b – рабочая ширина венца зубчатой передачи;
d1 – делительный диаметр шестерни.
Принимаем = 03 для всех последующих расчетов.
- для изгибной прочности
где Km – вспомогательный коэффициент; для прямозубых передач Km = 14;
KFb – коэффициент учитывающий распределение нагрузки по ширине венца при изгибе;
sF – допускаемое изгибное напряжение МПа;
YF1 – коэффициент учитывающий форму зубьев шестерни.
Проектный расчет первой передачи.
=32; =118; =372; u=126; = 1055;
Контактная прочность.
Принимаем стандартный модуль m=2.
Проектный расчет второй передачи.
=19; =114; =368; u=279; = 115;
Принимаем стандартный модуль m=3.
Проектный расчет третьей передачи.
=26; =1115; =387; u=159; = 1069;
Проектный расчет четвертой передачи.
Принимаем стандартный модуль m=4.
Так как для одной группы передач модуль должен быть одинаковым то принимаем:
- для первой группы m1=3;
- для второй группы m2=4;
5. Геометрический расчет зубчатых передач.
Делительный диаметр:
Диаметр вершин зубьев:
Диаметр впадин зубьев:
Межосевое расстояние:
При m=4 для 5 и 6 зубчатых колес получаем:
Так как модуль и количество зубьев 5 и 7 6 и 8 колес совпадают
то 7 и 8 колеса будут иметь те же размеры.
6. Расчет ременной передачи.
Крутящий момент от коробки передач к 3 валу передается через зубчатую ременную передачу. Расчет ременных передач выполняется в программе «КОМПИР»[8]. В соответствии с заданием считается только ременная передача от коробки передач к 3 валу как входящую в переборную коробку.
Результаты расчета представлены на Рис. 16.
Рис.9. Расчет ременной передачи
Составим свертку валов автоматической переборной коробки и укажем на ней силы действующие в зубчатых зацеплениях.
С целью уменьшения габаритов АПК валы располагаются не в линию а под некоторым углом. Расстояние между 3 и 5 валом выбирается в таких пределах что бы обеспечить необходимую изгибную и контактную прочность для зубчатой передачи работающей между 3 и 4 валами.
Рис.10. Схема свертки валов АПК и силы действующие на 4 вал.
На Рис. 10 показаны силы действующие на 4 вал от зубчатых зацеплений.
Проверочные расчеты.
1 Проверочный расчет вала.
Эскиз вала приведен на Рис. 11.
В качестве материала вала принимаем Сталь 45 (термообработка – нормализация) ГОСТ 4543-71 с пределом прочности sв = 550 МПа.
Рис.11. Эскиз 4 вала.
Основным проверочным расчетом для валов является расчет на сопротивление усталости. Уточненные расчеты на сопротивление усталости отражают влияние разновидности цикла напряжений статических и усталостных характеристик материалов размеров формы и состояния поверхности.
Составим расчетную схему вала и определим действующие нагрузки.
Рис. 12. Расчетная схема вала и действующие нагрузки.
С помощью эпюр определяем силу действующую в наиболее опасном сечении.
Изгибающий момент действующий на вал в опасном сечении будет равен:
Запас сопротивления усталости определяется по формуле:
где: - коэффициент запаса только по нормальным напряжениям;
- коэффициент запаса только по касательным напряжениям.
Расчет проводится в программе «КОМПИР».
В этой же программе выполняется расчет подвижного шлицевого соединения по напряжениям смятия. В качестве исходных данных для расчета принимается длинна соединения (длина подвижного блока) и предел текучести материала вала.
Условия прочности и запаса выносливости выполняются однако запасы усталостной и статической прочности почти в 2 раза выше требуемых. Этот запас объясняется неточностью проектного расчета (13) где допускаемые напряжения кручения были занижены. Для экономии металла и снижения объемов механической обработки необходимо уменьшить диаметр вала и принять другой типоразмер для шлицев. Запас прочности по напряжениям смятия так же выше требуемого предельный передаваемый момент намного выше реального однако уменьшение длины соединения нецелесообразно.
Рис. 13. Проверочный расчет вала.
2. Проверочный расчет зубчатых передач.
Проверочный расчет зубчатых передач выполняется в программе «КОМПИР» МГТУ «СТАНКИН».
Исходными данными для проведения проверочного расчета являются:
)Число зубьев шестерни;
)Число зубьев колеса;
)Ширина зубчатого венца (определяется из известного межосевого расстояния и коэффициента );
)Крутящий момент шестерни;
)Частота вращения шестерни;
Так как действующие контактные и изгибные напряжения намного выше действующих будет целесообразно изменить:
Модуль передачи (при уменьшении модуля уменьшаются размеры зубчатых колес и действующие изгибные напряжения так как уменьшается высота зубьев);
Ширину зубчатого венца (при уменьшении ширины зубчатого венца возрастают действующие контактные напряжения однако появляется необходимость в увеличении размеров ступицы колеса);
Материал зубчатого колеса (выбрать сталь без легирующих добавок однако остается необходимость в особой термообработке);
Проверочный расчет первой и второй передачи можно не проводить так как для наиболее нагруженных передач условие прочности выполняется.
Рис. 14. Проверочный расчет третьей передачи.
Так же необходимо провести проверочный расчет постоянной передачи между 3 и 5 валом. Данный расчет проводится после составления свертки валов и вычисления геометрических размеров остальных передач так как межосевое расстояние между 3 и 5 валами можно определить только на основании свертки валов.
Рис. 15. Проверочный расчет четвертой передачи.
Относительную ширину колес по диаметру принимаем как и в предыдущих расчетах = 03 откуда находим ширину зубчатого венца b = 32 мм ; модуль принимаем m = 4 откуда находим число зубьев колес: Z = 30. Так как передаточное отношение i = 1 число зубьев шестерни и колеса будет равно.
Рис. 16. Проверочный расчет передачи между 3 и 5 валом.
3.Проверочный расчет шпиндельного узла.
Проверочный расчет проводится на жесткость шпиндельного узла в программе «SPINDL» МГТУ СТАНКИН [8].
Выбор основных параметров шпинделя.
Рис. 17. Выбор типа переднего конца шпинделя и схемы опор.
Так как в программе отсутствует нужная нам схема опор примем наиболее подходящий вариант с учетом рассчитанной программой быстроходности.
На данном этапе выбираются тип и серия подшипников. Серию подшипников назначаем из известной радиальной жесткости. Так как принятый тип подшипника отличается от примененного в эскизном проекте принимаем радиальную жесткость по примененной в эскизном проекте схеме. (Рис. 18)
На данном этапе возможны неточности в следствии не совпадения реально используемой монтажной схемы от рассчитываемой в программе.
Однако эти неточности можно компенсировать увеличением радиальной жесткости подшипников в программе то есть выбором более тяжелой серии.
Рис. 18. Выбор типа и серии подшипников.
Расчет жесткости шпинделя.
На следующем этапе определяется оптимальное межопорное расстояние и радиальная жесткость.
Если межопорное расстояние не совпадает с оптимальным его можно оставить по эскизному проекту.
На Рис. 19 представлен результат расчета при работе шпинделя через 4 вал. Значение b и силы в зубчатом зацеплении приняты для этого случая. Значение силы резания принято условно в зависимости от условного диаметра сверления и крутящего момента на шпинделе. Значения силы резания по проекциям принято условно по соотношению:
Из Рис.19 и Рис. 20 видно что наибольшая жесткость шпинделя будет при работе через 4 вал. Это объясняется тем что при работе напрямую плечо силы резания будет намного больше чем при работе шпинделя через 4 вал что приводит к большему изгибающему моменту. Кроме того межопорное расстояние было принято по эскизному проекту и достаточно сильно отличается от оптимального.
Рис. 19. Расчет радиальной жесткости шпинделя при работе через 4 вал.
Рис. 20. Расчет радиальной жесткости шпинделя при работе напрямую.
4. Проверка выбранных подшипников качения.
Проверку выбранных подшипников проводим только для 4 вала.
Расчет проводится в программе “BEARING_SKF” МГТУ СТАНКИН [8].
В качестве исходных данных указывается: тип подшипника; его посадочный диаметр; частота вращения вала на который он установлен; расчетная динамическая грузоподъемность и нагрузка на опору (находятся с помощью расчетной схемы вала). Программа выдает результат в виде эквивалентной нагрузки на опору и расчетной долговечности (в часах).
Как видно из Рис. 21 расчетная долговечность намного выше требуемой (15000 – 30000 часов до замены). Возможно применение вместо них подшипников с меньшим посадочным диаметром что приведет к уменьшению прочности вала.
Рис. 21. Проверка выбранных подшипников качения.
В ходе выполнения курсовой работы были разработаны элементы эскизного и технического проекта модуля главного движения станка с компьютерным управлением. Были определены технологическое назначение станка основные функциональные подсистемы модуля и его структура компоновка станка и модуля разработана кинематическая схема модуля.
Спроектированный модуль главного движения благодаря применению автоматической переборной коробки обладает более расширенным диапазоном регулирования по сравнению со станком-аналогом . Количество управляемых координат увеличено с трёх до шести благодаря применению стола глобусного типа.
Применение современных автоматизированных методов расчета позволило спроектировать наиболее оптимальный вид и конструкцию шпиндельного узла и модуля в целом.
Список использованной литературы.
Пуш В.И. «Проектирование металлорежущих станков». М.: Машиностроение 1987 г. 293 с. ил.
Дунаев П.Ф. Леликов О.П. Конструирование узлов и деталей машин: Учебное пособие для студентов вузов технических специальностей.- 8-е издание переработанное и дополненное. - М.: Академия 2003.- 496 с.: ил.
Анурьев В.И. «Справочник конструктора-машиностроителя». В 3-х томах. - 8-е издание перераб. и доп. Под ред. И.Н. Жестковой. - М.: Машиностроение 2001. – 920 с. ил.
«Справочник технолога-машиностроителя». В 2-х томах. Т. 2. Под редакцией А.Г. Косиловой и Р. К. Мещерякова. 4-е изд. - М.: Машиностроение 1986 год. 496 с.
«Проектирование приводов главного движения и подачи металлорежущих станков» Методические указания Составители: Куликов Кудояров и др. Уфа УАИ 1988 42 с.
«Методические указания к проектированию приводов с ЧПУ» Уфа УАИ 1980 с.54
Методические указания по автоматизированному проектированию шпиндельных узлов станков. Уфа. УАИ 1986. 32 с.
Комплекс прикладных программ МГТУ «СТАНКИН».
В.В. Бушуев и др. «Станочное оборудование автоматизированного производства» в 2 – х томах Т.2 Москва: изд – во «СТАНКИН» 1994 г. 656 с..
С.И. Куликов П.В. Волоценко «Сверлильные и хонинговальные станки.» - М. «Машиностроение» 1977.
Бушуев В.В. «Основы конструирования станков.» - М.: Станкин 1992 – 520 с.
ГОСТ 19807-91 «Титан и сплавы титановые деформируемые»;
ГОСТ 4543-71 «Прокат из легированной конструкционной стали. Технические условия»;
ГОСТ 24644-81 «Концы шпинделей и хвостовики инструментов сверлильных расточных и фрезерных станков»
Спецификация.spw

Siemens 1PH7 101-2NF
Направляющие качения
Датчик положения блока
Кольцо уплотнительное
Кольцо компенсаторное
Гайка М5-6Н.5 ГОСТ 15521-70
Кольцо 62 ГОСТ 13941-86
Кольцо 72 ГОСТ 13941-86
Кольцо 80 ГОСТ 13941-86
Кольцо 54 ГОСТ 13942-86
Кольцо 68 ГОСТ 13942-86
Кольцо 50 ГОСТ 13942-86
Кольцо 62 ГОСТ 13942-86
Кольцо 45 ГОСТ 13942-86
Подшипник 46212 ГОСТ 831-75
Подшипник 46209 ГОСТ 831-75
Подшипник 207 ГОСТ 8338-75
Подшипник 209 ГОСТ 8338-75
Подшипник 206 ГОСТ 8338-75
Подшипник 1000088 ГОСТ 8338-75
Шайба 6 Н ГОСТ 6402-70
Шайба 8 Н ГОСТ 6402-70
Шайба 5 Н ГОСТ 6402-70
Рекомендуемые чертежи
- 21.05.2024
- 01.07.2014
- 09.07.2014
Свободное скачивание на сегодня
Обновление через: 10 часов 23 минуты