Технологический процесс изготовления вала




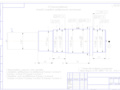
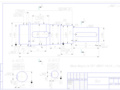
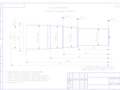
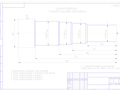
- Добавлен: 25.10.2022
- Размер: 838 KB
- Закачек: 0
Описание
Состав проекта
![]() |
![]() ![]() |
![]() ![]() ![]() |
![]() |
![]() ![]() ![]() ![]() |
![]() ![]() ![]() ![]() |
![]() ![]() ![]() ![]() |
![]() ![]() ![]() ![]() |
![]() ![]() ![]() ![]() |
![]() ![]() ![]() ![]() |
![]() ![]() ![]() ![]() |
![]() ![]() ![]() ![]() |
![]() ![]() ![]() ![]() |
![]() ![]() ![]() ![]() |
![]() ![]() |
![]() ![]() |
![]() ![]() |
![]() ![]() |
![]() ![]() |
![]() ![]() |
![]() ![]() |
![]() ![]() |
![]() ![]() |
![]() ![]() |
![]() ![]() |
![]() ![]() |
![]() ![]() |
![]() ![]() |
![]() ![]() |
![]() ![]() |
![]() ![]() |
![]() ![]() |
![]() ![]() |
Дополнительная информация
4. 015 Установ Б.dwg

8. 015 Установ Д(получист.).dwg

3. 015 Установ А.dwg

1. вал-задание.dwg

6. 015 Установ Г (черн.).dwg

2. 005 Заготовительная.dwg

7. 015 Установ Г (получист.)..dwg

10. 025 Установ Б шлифование.dwg

9. 025 Установ А шлифование.dwg

5. 015 Установ В (черн.).dwg

Рекомендуемые чертежи
- 24.01.2023
Свободное скачивание на сегодня
- 22.08.2014
- 29.08.2014