Технологический процесс изготовления вала цапфа


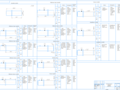
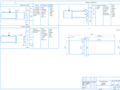
- Добавлен: 24.01.2023
- Размер: 293 KB
- Закачек: 1
Узнать, как скачать этот материал
Подписаться на ежедневные обновления каталога:
Описание
Технологический процесс изготовления вала цапфа
Состав проекта
![]() |
![]() |
![]() ![]() ![]() ![]() |
![]() |
![]() |
![]() ![]() ![]() ![]() |
![]() ![]() ![]() |
Дополнительная информация
Контент чертежей
аня.2cdw.cdw

аня.cdw

КР технология.doc
Брянский Государственный
Технический Университет
“Технология машиностроения”
Технологический процесс изготовления и сборка крана
Описание конструкции и назначение детали технических требований к точности и чистоте поверхностей .. .6
Анализ технологичности конструкции деталей 8
Выбор типа производства (единичное серийное массовое) . 10
Выбор и обоснование размеров заготовки и способа их получения .. 11
Выбор и обоснование баз способов закрепления для заготовки .. 18
Проектирование технологических операций обработки заготовки с оценкой чистоты поверхностей после каждой операции.. 20
Расчёт режимов резания и нормирование штучного времени 22
Выбор станков и режущего инструмента обеспечение точности обработки..27
Выбор контрольно-измерительных инструментов для оценки точности обработки .29
Описание назначения узла и оценка технологичности сборки 30
Выбор типа сборочного процесса. .. .. 31
Проектирование сборочных операций 32
Выбор и обоснование необходимых приспособлений для обеспечения сборки и измерительного инструмента .. ..33
Разработать схему крана .. 34
Список литературы 35
Описание конструкции и назначение детали технических требований к точности и чистоте поверхностей
Валы получили широкое применение в конструкциях различных машин в том числе и ПТМ. Валы служат для передачи крутящего момента. При выборе валов необходимо учитывать нагрузки действующие на вал по сколько если напряжения на валу будут критическим произойдет его разрушение. А разрушение вала может привести к тяжелым последствиям для всего механизма где он установлен.
Проанализируем последовательно эти требования с точки зрения их обоснованности и соответствия служебному назначению детали.
Наружную поверхность вала для повышения срока службы подвергают поверхностной закалке и шлифуют с обеспечением шероховатости поверхности 5 мкм при обработке по 12-му квалитету.Улучшить НВ 240 -260
Должна быть соблюдена соосность наружной поверхности с посадочным отверстием (радиальное биение не более 005 мм). Поскольку в противном случае в сопряжении вала с отверстием не будет обеспечен линейный контакт из-за возможного перекоса осей возможно также защемление вала.
Вал изготовляют из стали 40 Х по ГОСТ 4543-61 применяя паковку. Поковка позволяет на производить заготовку с достаточной степенью точности размеров после чего уже можно производить операции для получения требуемых размеров по чертежу.
Заданные шероховатости для вала являются Rz = 20 мкм для торцевой поверхности поскольку она не участвует во взаимодействии. И Rz = 5 мкм на поверхностях которые участвуют в взаимодействии с другими элементами (подшипниками манжетами и т.д.)
Несимметрирование боковых поверхностей шлицев относительно оси не более 002 мм на длине 100мм.
На торцах допускаются следы утопающих центров
Острые кромки притупить.
Результат анализа используют при разработке технологии изготовления детали и выборе средств контроля.
Анализ технологичности конструкции деталей.
В соответствии с ГОСТ 14.205—83 технологичность — это совокупность свойств конструкции изделия определяющих ее приспособленность к достижению оптимальных затрат при производстве эксплуатации и ремонте при заданных показателях качества объеме выпуска и условиях выполнения работ.
Производственная технологичность конструкции детали — это степень ее соответствия требованиям наиболее производительного и экономичного изготовления. Чем меньше трудоемкость и себестоимость изготовления тем более технологичной является конструкция детали.
Технологичность конструкции детали анализируют с учетом условий ее производства рассматривая особенности конструкции и требования качества как технологические задачи изготовления.
Оценка технологичности конструкции бывает двух видов: качественная и количественная.
Качественная оценка технологичности является предварительной обобщенной и характеризуется показаниями: «лучше — хуже» «рекомендуется — не рекомендуется» «технологично — нетехнологично» и т.п. Технологичной при качественной оценке следует считать такую геометрическую конфигурацию детали и отдельных ее элементов при которой учтены возможности минимального расхода материала и использования наиболее производительных и экономичных для определенного типа производства методов изготовления. В связи с этим проанализируем чертеж детали например с точки зрения:
степени унификации геометрических элементов (диаметров длин резьб фаски). В данной детали является приемлемой поскольку размеры входят в размерный ряд вала;
наличия удобных базирующих поверхностей обеспечивающая возможность совмещения и постоянства баз присутствует для нашего вала;
существует возможности свободного подвода и вывода режущего инструмента при обработке вала;
контроля точностных параметров детали производить удобно;
методы обработки детали позволяют успешно решить задачу по требуемому значению шероховатости на различных поверхностях изделия.
Количественная оценка технологичности выражается показателем численное значение которого характеризует степень удовлетворения требований к технологичности. Применительно производству количественную оценку технологичности производят по суммарной трудоемкости и технологической себестоимости а также по техническим показателям определение
которых возможно из чертежа детали. К ним относятся коэффициенты точности КТ и шероховатости Кш.
Из чертежа видно что суммарное количество указанных на чертеж размеров составляет 8 из которых два размера выполняются по 12 квалитету точности 6 размеров по 8 квалитету. В то же время 2 поверхность имеют значение шероховатости 20 мкм и 6 поверхностей 20 мкм.
Выбор типа производства (единичное серийное массовое).
Одной из основных характеристик типа производства является коэффициент закрепления операций Кз.о.
Коэффициент Кз.о. показывает отношение числа всех операций выполняемых или подлежащих выполнению в цехе (на участке) в течение месяца к числу рабочих мест т.е. характеризует число операций приходящихся в среднем на одно рабочее место в месяц или степень специализации рабочих мест.
При Кз.о. производство массовое; если 1 Кз.о. 10 — крупносерийное; если 10 Кз.о. 20 — среднесерийное; если 20 Кз.о. 40 — мелкосерийное в единичном производстве Кзо не регламентируется.
- суммарное число различных операций;
- явочное число рабочих подразделения выполняющих различные операции;
КВ - коэффициент выполнения норм Кв = 13;
Ф - месячный фонд времени рабочего при работе в одну смену час;
- суммарная трудоемкость программы выпуска час;
- программа выпуска каждой - й позиции номенклатуры;
Тi — трудоемкость - й позиции час.
В то же время условное число однотипных операций По выполняемых на одном рабочем месте может быть определено как
- нормативный коэффициент загрузки рабочего места всеми закрепленными за ним операциями;
- фактический коэффициент загрузки данной операцией. Рассчитывается фактический коэффициент загрузки по формуле:
где Кв - коэффициент выполнения норм;
- действительный годовой фонд времени работы оборудования час.
Приняв по справочным данным:
Производство крупносерийное. Кроме того данная серийность производства соответствует серийности по массе детали и условиям программы выпуска.
Определение вида заготовок и способов их изготовления
Материал является одним из важных признаков определяющих метод получения заготовок. Наиболее широко используемые материалы объединены в 7 групп. Код группы определяется по табл. 3.1 на основе данных чертежа детали.
Выбираем код материла – 6
Чтобы найти серийность производства необходимо знать массу детали и задаться конкретной программой выпуска. Код серийности определяется по табл. 3.3.
Конструктивные формы деталей общего машиностроения делятся на 14 видов. Соответствующий код выбирается на основе сравнения реальной детали с описанием типовых деталей представленных в табл. 3.2.
По массе заготовки сгруппированы в 8 диапазонов которые выбираются по табл. 3.4 и 3.5.
Для удобства использования в работе по выбору возможных вариантов наиболее часто применяемые способы получения заготовок в машиностроении закодированы в интервале от 1 до 11 и представлены в табл. 3.6.
Таким образом определив коды по каждому из четырех факторов составим перечень возможных видов и способов получения заготовок для данной детали согласно табл. 3.7:
По коду материала детали находим соответствующие строки таблицы.
По коду серийности производства уточняем место строки внутри соответствующего материала.
Код конструктивной формы определяет окончательное место строки данных в соответствующем коде серийности.
Код массы детали уточняет горизонталь в строке нужного кода формы детали которая указывает перечень кодов вида заготовок.
Из табл. 3.7 по определенным ранее кодам 6 — 4—2 — 3 из графы таблицы «Вид заготовки» выписываем рекомендуемые коды видов: 1.
— поковка на молотах и прессах;
— поковка на горизонтально-ковочных машинах;
Технико-экономическое обоснование выбора заготовки
Проводимые на первом этапе исследования позволяют определить рекомендуемые способы получения заготовок для чертежей деталей. Окончательное решение о выборе конкретного способа из полученного перечня (результаты первого этапа) принимается после определения и сравнения себестоимости получения заготовки для каждого из рекомендуемых видов.
Себестоимость производства заготовок без учета затрат на предварительную механическую обработку для способов поковка и обработки давлением определяется по зависимости
где С — базовая стоимость 1 т заготовок руб.т (табл. 3.9—3.12);
—коэффициент доплаты за термическую обработку и очистку заготовок руб.т (табл. 3.13);
—масса заготовки кг;
КТ — коэффициент учитывающий точностные характеристики заготовок (табл. 3.14);
Кс —коэффициент учитывающий серийность выпуска заготовок (табл. 3.15—3.17);
— масса детали кг (см. чертеж детали);
—стоимость 1 т отходов (стружки) руб.;
Кф — коэффициент учитывающий инфляцию (по отношению к ценам 1991 г.).
Оптовая цена 1 т поковка руб.
Выбираем из данных таблицы массы
)поковка на молотах и прессах
Находим базовую себестоимость
Находим себестоимость заготовки
)поковка на горизонтально-ковочных машинах;
Вывод На основании проведенных расчетов можно сделать вывод о том что наиболее целесообразно (по себестоимости единицы продукции) будет использовать поковку для производства данного вала .
Разработка технологических процессов обработки элементарных поверхностей
Предварительный выбор методов обработки элементарных поверхностей и числа необходимых переходов (операций) производят на основе данных справочных таблиц экономической точности обработки или на основе обобщенных таблиц примерных маршрутов (см. прил. 3) исходя из требований предъявляемых к конечной точности и качеству поверхностей вида исходной заготовки свойств материала и типа производства.
Определив первый и окончательный переходы устанавливают Необходимость промежуточных переходов число которых тем больше чем ниже точность исходной заготовки и выше конечные Требования к поверхности. Число вариантов обработки поверхности может быть довольно большим (см. прил. 3) и их сокращение возможно с учетом некоторых нюансов к которым относятся например целесообразность обработки данной поверхности на одном станке за несколько последовательных переходов и ее обработки совместно с другими поверхностями заготовки за один установ ограничение возможности применения некоторых методов из-за недостаточной жесткости детали и т.п.
Припуск — слой материала удаляемый с поверхности заготовки в целях достижения заданных свойств обрабатываемой поверхности детали. Припуск на обработку поверхностей детали может быть назначен по справочным таблицам или на основе расчетно-аналитического метода. Расчетной величиной припуска является минимальный припуск на обработку достаточный для устранения на выполняемом переходе погрешностей обработки и дефектов поверхностного слоя полученных на предшествующем переходе и для компенсации погрешностей возникающих на выполняемом переходе.
Минимальный припуск:
при обработке поверхностей вращения в центрах
Отклонение расположения Е необходимо учитывать у заготовок (под первый технологический переход) после черновой и получистовой обработки лезвийным инструментом (под последующий технологический переход) и после термической обработки. В связи с закономерным уменьшением величины Е при обработке поверхности за несколько переходов на стадиях чистовой и отделочной обработки ею пренебрегают.
На основе расчета промежуточных припусков определяют предельные размеры заготовки по всем технологическим переходам. Промежуточные расчетные размеры устанавливают в порядке обратном ходу технологического процесса обработки этой поверхности т.е. от размера готовой детали к размеру заготовки путем последовательного прибавления (для наружных поверхностей) к исходному размеру готовой детали промежуточных при
пусков или путем последовательного вычитания (для внутренних поверхностей) от исходного размера готовой детали промежуточных припусков. Наименьшие (наибольшие) предельные размеры по всем технологическим переходам определяют округляя их увеличением (уменьшением) расчетных размеров до того знака десятичной дроби с каким дан допуск на размер для каждого перехода. Наибольшие (наименьшие) предельные размеры вычисляют путем прибавления (вычитания) допуска к округленному наименьшему (наибольшему) предельному размеру.
Предельные значения припусков определяют как разность наибольших (наименьших) предельных размеров и как разность наименьших (наибольших) предельных размеров предшествующего и выполняемого (выполняемого и предшествующего) переходов.
Определяем отклонения
Подрезание торца черновое
отклонения от перпендикулярности
радиус наружной поверхности
радиус внутренней поверхности
. Подрезание торцов чистовое
Подрезание торцов чистовое
Подрезание торцов черновое
Шлифование черновое
- коэффициент уточнения
Минимальные припуски на диаметральные размеры для каждого перехода рассчитываем
Подрезание торца чистовое
Расчет наименьших размеров по технологическим переходам начинаем с наименьшего размера детали по конструкторскому чертежу
Подрезание торца чистовое
Наибольшие предельные размеры по переходам
. Подрезание торца чистовое
Расчет максимальных припусков
) 224016-224006=001мм
) 224036-224016=002 мм
) 22429-224036=0254мм
) 38215-38072=0143мм
Расчет минимальных припусков
) 223606-2236=0006мм
) 223612-223606=00059 мм
) 223713-223612=0101 мм
) 22381-223713=01014мм
) 2652059-265201=00059 мм
) 265201-265=0201 мм
) 38062-37977=0055мм
)381358-38062=0073мм
)382658-381358=013мм
Общий припуск наибольший
Общий припуск наименьший
Результаты расчета припусков на обработку и предельных размеров по технологическим переходам
Элементы припуска мкм
Допуск на промежуточные размеры мкм
Принятые (округленные) размеры заготовки по переходам мм
Предельный припуск мкм
минимальный размер мм
Выбор и обоснование баз способов закрепления для заготовки.
Конструкторские базы назначаются конструктором изделия при простановке размеров на рабочем чертеже. На выбор той или иной схемы при простановке размеров влияют как конструкторские так и технологические требования. Выбранная схема в значительной степени предопределяет последовательность обработки выбор баз конструкцию приспособления и т. д.
Выбирая схему простановки размеров конструктор должен исходить из обеспечения принципа технологичности конструкции. Более технологичной является та конструкция на изготовление которой затрачивается меньше времени требуется более простое приспособление а заданная точность достигается просто и надежно.
Базирование заготовки в приспособлении производится как правило двумя или тремя базами причем оно сводится по существу к базированию ее отдельных баз. Обнаружено что в группе баз значимость каждой из них для данной операции неодинакова. Среди них выделяется основная база. Заготовка устанавливаемая этой базой в приспособление получает почти полную ориентацию лишаясь трех или четырех степеней свободы. Для лишения заготовки остальных степеней свободы используются другие вспомогательные базы. Основную базу необходимо выделять из группы баз еще и потому что способ ее базирования принципиально отличается от способа базирования остальных баз.
В связи с этим представляется возможным рассматривать типовые способы базирования основной базы определенной формы безотносительно к форме и размерам заготовок тем более что круг поверхностей используемых в качестве основной базы ограничен тремя видами — плоской поверхностью цилиндрическим отверстием и цилиндрической наружной поверхностью.
Основную базу выбирает конструктор приспособления. Иногда это делает технолог при разработке технологического процесса проставляя на операционном эскизе значками тип опорного элемента и число опорных точек. За основную базу предпочтительно брать поверхность которая обеспечивает заготовке устойчивое положение в приспособлении даже при базировании только одной этой базы. Наиболее полно такому требованию отвечает плоская поверхность заготовки располагающаяся снизу и обладающая достаточной протяженностью. Если у заготовки такой поверхности нет выбирают другую поверхность достаточной протяженности — боковую плоскую поверхность цилиндрическое отверстие либо цилиндрическую наружную поверхность.
Выполнение всех операций производим базированием левой или правой частей валов как показано на рисунке 1 и 2.
- данная схема базирования показывает что применяем трехкулачковый патрон.
Кроме того применяем установ А и Б которые показывают как изменяется положение вала при выполнении различных операцей.
Проектирование технологических операций обработки заготовки с оценкой чистоты поверхностей после каждой операции.
На первых (одной-двух) операциях обрабатывают поверхности которые будут использоваться в качестве технологических баз на всех или большинстве операций технологического процесса
Используя чистовые базы обрабатывают остальные поверхности в последовательности обратной их степени точности т.е. чем точнее должна быть обработана поверхность тем позже ее обрабатывают.
Используя разработанные ранее маршруты обработки отдельных поверхностей выявляют необходимость расчленения процессов изготовления детали на стадии обработки. Стадия обработки — это часть технологического процесса включающая однородную по характеру и точности обработку различных поверхностей и детали в целом.
Целесообразность разделения технологического процесса на стадии обработки обусловлена необходимостью получения деталей заданной точности и рационального использования оборудования так как это связано с числом и содержанием операций технологического процесса. На каждой стадии выполняют операции обеспечивающие примерно одинаковую точность обработки.
Операция подрезание торца черновое выполняется на правом торце значение шероховатости Rz=50мкм требуемый квалитет 14. Производим проверку соответствия шероховатости соотнося полученные значения с образцами шероховатости.
Операция подрезание торца черновое выполняется на левом торце значение шероховатости Rz=50мкм требуемый квалитет 14. Производим проверку соответствия шероховатости соотнося полученные значения с образцами шероховатости.
Операция подрезание торца чистовое выполняется на правом торце значение шероховатости Rz=5 мкм требуемый квалитет 8. Производим проверку соответствия шероховатости соотнося полученные значения с следующим рядом образцов шероховатости
Операция подрезание торца чистовое выполняется на левом торце значение шероховатости Rz=5 мкм требуемый квалитет 8. Производим проверку соответствия шероховатости соотнося полученные значения с следующим рядом образцов шероховатости
Операция подрезание нарезание фаски значение шероховатости Rz=20 мкм требуемый квалитет 10. Производим проверку соответствия шероховатости соотнося полученные значения с следующим рядом образцов шероховатости
Операция подрезание нарезание торцов значение шероховатости Rz=50мкм требуемый квалитет 14. Производим проверку соответствия шероховатости соотнося полученные значения с образцами шероховатости.
Операция точение черновое выполняется на внешней поверхности заготовки значение шероховатости Rz=20мкм требуемый квалитет 12. Производим проверку соответствия шероховатости соотнося полученные значения с образцами шероховатости кроме того используем микрометр для определения размера внешнего диаметра. На данной стадии совмещают окончательную обработку неточных поверхностей и предварительную обработку точных поверхностей.
Операция точение чистовое выполняется на внешней поверхности заготовки значение шероховатости Rz=10мкм требуемый квалитет 10. Используем тот же способ определения полученных размеров что и для чернового точения. На данной стадии предварительную обработку точных поверхностей.
Операция шлифование черновое выполняется на внешней поверхности заготовки значение шероховатости Rz=10мкм требуемый квалитет 8. Определение значений полученных после шлифования производим используя скобы и кругломер. На данной стадии проводят окончательную обработку точных поверхностей
Операция шлифование черновое выполняется на внешней поверхности заготовки значение шероховатости Rz=5мкм требуемый квалитет 8. Определение значений полученных после шлифования производим используя скобы и кругломер. На данной стадии проводят окончательную обработку точных поверхностей
Расчёт режимов резания и нормирование штучного времени.
При этом наиболее выгодными считаются такие режимы обработки которые обеспечивают наименьшую себестоимость механической обработки при удовлетворении всех требований к качеству продукции и производительности обработки.
В общем случае необходимо соблюдать определенную последовательность назначения режимов резания которая включает следующие этапы:
Выбор глубины резания t (мм) по условию удаления припуска под обработку за один рабочий ход но в зависимости от требований по точности и шероховатости предъявляемых к обработанной поверхности припуск разделяют по стадиям обработки: предварительная окончательная и отделочная.
Определение глубины резания за один рабочий ход:
а) при обработке поверхностей тел вращения
б) при односторонней обработке плоских поверхностей
где— соответственно диаметр и линейный размер после
— соответственно диаметр и линейный размер до обработки.
подрезание торца черновое.
подрезание торца чистовое.
шлифование черновое.
шлифование чистовое.
Выбор подачи на один оборот (ммоб) или подачи на один зуб (для многозубных инструментов) (ммзуб) с учетом стадии обработки (предварительная чистовая или отделочная) и нагрузочно-прочностных характеристик технологической системы.
Подачу при черновой обработке выбирают максимально возможную учитывая следующие ограничения: прочность механизмов привода и подачи станка прочность инструмента прочность заготовки жесткость и прочность технологической системы. Мощность станка как правило не ограничивает подачу при недостатке мощности в большинстве случаев следует снижать не подачу а скорость.
При чистовой обработке подачу выбирают в зависимости от требований к точности и шероховатости поверхностей.
(ммоб) подрезание торца черновое. [5 таб.15стр.268]
(ммоб) подрезание торца чистовое [5 таб.15стр.268]
(ммоб) точение черновое. [5 таб.11стр.266]
(ммоб) точение чистовое. [5 таб.14стр.268]
(ммоб) шлифование черновое. [5 таб.55стр.301]
(ммоб) шлифование чистовое. [5 таб.55стр.301]
Определение скорости резания V(ммин) с учетом выбранных свойств обрабатываемого и режущего материалов геометрии и стойкости инструмента по эмпирическим зависимоcтям имеющим общий вид
где Сv т х у — коэффициенты учитывающие вид обработки;
Т — период стойкости инструмента мин;
kv — коэффициент учитывающий конкретные условия обработки
коэффициент учитывающий влияние материала заготовки.
- коэффициент учитывающий состояние поверхности.
- коэффициент учитывающий материал инструмента.
Сv=47; т=02; х=-; у=08;1;085;065;
kv =05525 [5 таб.1-5стр.262]
Сv=237; т=025; х=-; у=066;1;085;03;
kv =0255 [5 таб.1-5стр.262]
подрезание торца черновое5
Сv=47; т=02; х=-; у=08;1;085;065;
точение черновое. [5 таб.8стр.14]
Сv=340; т=02; х=015; у=045;1;1;035;
kv =035 [5 таб.1-5стр.262]
Сv=420; т=02; х=015; у=02;1;1;035;
шлифование черновое. [5 таб.55стр.301]
шлифование чистовое. [5 таб.55стр.301]
Сверление отверстия.
Сv=98; т=02; q=04; у=05;1;085;065; kv =05525
Наиболее выгодные периоды стойкости принимаются по нормативам с учетом сложности изготовления и наладки инструментов.
Определение частоты вращения (мин-1) либо числа двой-
ных ходов заготовки или инструмента.
По паспортным данным станка определяют n близкую к расчетной nр. При отсутствии этих данных ряд частот вращения можно определить по зависимости
где nпр — принимаемая (ближайшая меньшая) частота вращения;
— минимальная частота вращения для данного станка;
— знаменатель ряда геометрической прогрессии условно принимаемый равным 126;
Нормирование затрат труда на выполнение операции.
Одним из основных требований при проектировании технологических операций является требование минимума затрат труда на ее выполнение. Критерием оценки трудоемкости является норма штучно-калькуляционного (ТШК) или штучного (Тшт — для массового производства) времени мин:
Основное время можно определить по зависимости а значение
подготовительно-заключительное время мин на партию запуска заготовок в производство = 12 минут.
вспомогательное время = 7 минут.
время установки и снятия заготовки = 4 минуты.
время связанное с выполнением перехода = 2 минуты.
время на измерение = 1 минута.
время обслуживания рабочего места = 2 минуты.
время перерывов в работе = 2 минуты.
мин. [4 таб.10стр.18]
мин. [4 таб.7стр.13]
шлифование черновое .
Выбор станков и режущего инструмента обеспечение точности обработки.
) Для выполнения операций: подрезание торца черновое подрезание торца чистовое обработка внутренней поверхности и подрезания торца чернового применяем одношпиндельный токарно-многорезцовый полуавтомат (токарный многорезцовый копировальный полуавтомат 1 П 707 Ф2).
Мы принимаем данный полуавтомат т.к. на токарных многорезцовых копировальных полуавтоматах возможна обработка цилиндрических фасонных конических и торцовых поверхностей деталей. Станки серийного выпуска позволяют обрабатывать заготовки диаметром до 80 мм длиной до 400 мм. Мы используем данный полуавтомат для обработки торцевых поверхностей и диаметр детали составляет 40 мм. Т.е. те операции которые данный станок в состоянии выполнить по своим техническим данным.
Проектирование наладок. Для описанных выше операций нам необходимо что бы выполнялись требования по квалитету точности. Необходимы следующие квалитеты – 10 12 14. На токарных многорезцовых копировальных полуавтоматах обеспечивается точность обработки 11 —13-го квалитета. При правильном выборе наладки и технологической оснастки точность может быть повышена до 6 —9-го квалитета. Т.е. по условию обеспечения точности станок подходит.
Для данного станка характерно использования резцов из быстрорежущей стали.
Выбираем резец токарные отрезные из быстрорежущей стали Р9 по ГОСТ 18874-73. Выбираем данный тип резца поскольку он обладает удовлетворительной прочностью повышенной износостойкостью при средних и повышенных скоростях резания узким интервалом оптимальных закалочных температур повышенной пластичностью при температурах горячей деформации.
) Для выполнения просверливания отверстий используем станок сверлийный 2М57.
Выбираем данный тип станка поскольку он подходит по частоте вращения кроме того он обеспечивает просверливание отверстия необходимого диаметра. Так же на данном станке выполняется зенкерование – предварительная обработка литого отверстия под последующее протягивание. При точности отверстия 11-13 квалитета что как раз является необходимыми условием для нас.
Производим выбор сверла спирального из быстрорежущей стали (усиленное) по ГОСТ 18874-73. Так как данное условие удовлетворяет следующим требованиям: обеспечивает при обработке деталей в кондукторах точность расположения отверстия 015 мм удовлетворяет глубину сверления и точность отверстия.
) Для нарезания шлицов применяем станок Токарный
одношпиндельный автомат продольного точения 1М10В.
Диаметр точения щлицов 40 мм длина 250 мм. По данным значениям станок соответствует требованиям предъявляемым деталью. При нарезании обеспечивается необходимая нам точность обработки 14 квалитета. Параметры шероховатости протягиваемого паза Rz =50мкм.
Резец токарный из быстро режущей стали по ГОСТ 18874-73
) Для точения чернового и точения чистового применяют токарно-револьверный полуавтомат 1П410Ф3.
Выбор данного станка обусловлен следующими причинами: поверхности обрабатываемые сверлами позволяют достичь точности 12—14-го квалитета и допустимого биения в пределах допуска на диаметр. Так же станок обеспечивает соблюдения необходимой соосности при обработке детали диаметр детали входит в допустимый ряд для данного станка длина детали так же находится в допустимых значениях.
Выбираем резец проходной прямой с пластинами из твердого сплава по ГОСТ 18879-73.Выбор данного сверла обусловлен повышенной прочностью повышенной вторичной твердостью и износостойкостью.
) Операция чернового шлифования выполняется на круглошлифовальном станке 3У132.
Данный станок позволяет обеспечить соблюдение рабочего цикла шлифования. Снимаемый припуск за каждый оборот детали или глубина Т срезаемого слоя не остаются постоянными они изменяются на протяжении всей операции и определяют структуру рабочего цикла шлифования.
Черновое шлифование целесообразно выполнять v= 50-60 мс. отличие от токарной обработки обдирочное шлифование обеспечивает более высокую точность обработки (8—9-го квалитета) шероховатость поверхности Rа = 25 - 50. Данные значения шероховатости соответствуют тем требованиям которые предъявляются к данной детали.
Выбор шлифовального круга ПП 4А 50 -28 2 К 5ППС 50 20 связано с тем что он подходит по диаметру высоте твердости. Так же содержание абразивных элементов и зернистость являются приемлемой для того что бы выполнить требуемые условия по шлифованию.
Выбор контрольно-измерительных инструментов для оценки точности обработки.
Микрометр (для измерения наружного диаметра). Микрометры широко используют для измерения диаметра шлифуемой поверхности преимущественно в инструментальном производстве
Кроме того применяют образцы шероховатостей. Что позволяет быстро и четко определить полученные значения и сравнить с требуемыми. Для уточнения размеров тормозного шкива используются все выше перечисленные контрольно-измерительные инструменты применение тех или иных инструментов связана с тем какую поверхность и после какой операции необходимо измерить.
Описание назначения лебедки и оценка технологичности сборки.
Согласно общепринятому определению лебёдка - машина для перемещения грузов посредством движущегося гибкого элемента - каната или цепи. Тяговое усилие гибкому элементу передаётся с барабана или звёздочки приводимых в движение через передаточные механизмы. Различают лебедки: стационарные и передвижные с ручным и машинным приводом (от двигателей - электрического внутреннего сгорания реже - паровых гидравлических пневматических нашли применение также рычажные лебедки. При качательном движении приводной рукоятки канат попеременно зажимается двумя захватами и проталкивается через тяговый (рычажный) механизм. Тяговые усилия (грузоподъёмность) лебедок регламентированные государственными стандартами находятся в пределах от 25 до 200 кН (от 025 до 20 тс).
Лебедки применяются как самостоятельные машины при производстве погрузочно-разгрузочных строительных монтажных ремонтных складских работ на маневровых работах с подвижным составом для трелёвки леса и штабелирования древесины швартовки судов и подъёма якорей (кабестаны брашпили) а также как часть землеройных и дорожных машин подъёмных кранов копров канатных дорог скреперных и бурильных установок и др.
Что бы оценить технологичность сборки рассмотрим производственную эксплуатационную и ремонтную технологичности.
С точки зрения производственной технологичности лебедка удовлетворяет всем условиям легкого монтажа унификации большого числа элементов входящих в конструкцию лебедки. С точки зрения эксплуатационной так же техническое обслуживание может легко осуществляться ко всем элементам имеется удобный подход. Текущий ремонт лебедки не должен вызывать каких либо трудностей. Ремонтная - проявляется в малых затрат средств и времени на выполнение ремонта изделия благодаря конструкции данного изделия. Т.е. можно сделать вывод что технологичность лебедки находится на уровне удовлетворяющим всем требованиям. Простате в сборе монтаже и дальнейшей эксплуатации.
Выбор типа сборочного процесса.
Зная исходные данные установленные методы сборки изделия и принятый тип производства выбирают организационную форму сборочного процесса. На выбор организационной формы сборки влияют конструкция изделия его размеры и масса программа и сроки выпуска. Организационные формы сборки устанавливают отдельно для изделия и его составных частей. В общем случае они могут быть разными.
Тот или иной вариант организационной формы сборки конкретного изделия выбирают на основе расчетов себестоимости выполнения сборки с учетом сроков подготовки и оснащения производства необходимым технологическим и подъемно-транспортным оборудованием. На выбор разновидности поточно-конвейерной сборки влияют удобство сборки и доступность к изделию с разных сторон. Подвесной конвейер например удобнее для сборки сложных изделий средних размеров чем конвейер пластинчатого типа.
Маршрутная технология включает установление последовательности и содержания технологических и вспомогательных операций сборки. Последовательность сборки определяется на основе технологических схем. Содержание операций устанавливают в зависимости от выбранного типа производства и темпа сборки. При массовом производстве содержание операции должно быть таким чтобы ее длительность была равна темпу (несколько меньше темпа) или кратна ему. Выполняемая работа должна быть по своему характеру однородной и должна отличаться определенной законченностью. Лебедку изготавливают в количествах позволяющих применить поточную сборку на конвейерах с непрерывным или периодическим движением. Поточная форма отличается специализация каждого рабочего места на определенной операции согласованное и ритмичное выполнение всех операций технологического процесса. Так как конструкция лебедки не позволяет одновременно проводить несколько операций то данный технологический является наиболее оптимальным. И позволяет наиболее рационально загрузить работников поскольку после выполнения одной операции принимается работать другой работник. Последовательное выполнение работ является основой поточного типа.
Проектирование сборочных операций.
Для проектирования операций необходимо знать маршрутную технологию общей и узловой сборки схему базирования и закрепления изделия намеченное ранее содержание операций а также темп работы если операции проектируют для поточной линии. При проектировании операции уточняют ее содержание устанавливают последовательность и возможность совмещения переходов во времени окончательно выбирают оборудование приспособления и инструменты (или дают задание на их конструирование) назначают режимы работы сборочного оборудования корректируют нормы времени устанавливают схемы наладок. Проектирование сборочной операции — задача многовариантная. Варианты оценивают по производительности и себестоимости. Проектируя сборочную операцию стремятся к уменьшению штучного времени. Это позволяет сократить потребное количество оборудования и рабочую силу. Штучное время увязывают с темпом работы поточной линии.
Возможности перекрытия элементов штучного времени зависят от схемы построения сборочной операции. По числу устанавливаемых для сборки изделий схемы операций делят на одно- и многоместные а по числу инструментов на одно- и многоинструментные. По последовательности работы сборочных инструментов и расположению собираемых изделий операции могут быть последовательного параллельного и параллельно-последовательного выполнения. При различном сочетании указанных признаков образуется ряд схем значительно отличающихся друг от друга по производительности и себестоимости.
Для лебедки назначаем следующие сборочные операции: необходимо провести сбор оси и элементов на ней (ось в сборе) после того как данная операция завершится необходимо проверить правильность установки элементов.
Следующая операция включает в себя соединение между собой 2 осей и вала-шестерни необходимо что бы произошло зацепление между зубчатыми колесами и шестерней. Следующая операция включает в себя закрепление осей и вала по средствам крышки гайки и винтов. Для затяжки винтов необходимо использовать отвертку. Следующим этапом является установка подшипников втулок крышек. Подшипники необходимо одевать с натягом. Крепление звезды к крышке производится болтами. Для этого используют гаечный ключ и необходимую силу затяжки. Затем проводят операцию по зубчатому зацеплению между зубчатыми колесами пятна контактов зуба контролируют при этом. Затем снова одевают подшипники втулки крышки закрепляя их болтами с соблюдением затягивающего усилия.
Выбор и обоснование необходимых приспособлений для обеспечения сборки и измерительного инструмента.
Определение типа сборочного оборудования. Содержание операций определяет тип основные размеры и техническую характеристику сборочного оборудования технологической оснастки (приспособлений рабочего и измерительного инструмента) Так для сборки сопряжений с натягом (подшипники) применяют прессы — при средних усилиях запрессовки (15 — 5 кН) механические приводные.
Для стягивания поджима и выравнивания отдельных элементов используем винтовые прижимы: струбцины зажимы. Кроме того необходимы отвертки гаечные ключи. И инструменты контроля установки деталей. Необходим шуп для контроля зазора в собранных сопряжениях контрольными приспособлениями производим контроль радиального и осевого биения.
Разработать схему сборки лебедки передвижения грузовой тележки.
Составление технологических схем сборки. Изучение собираемого изделия завершается составлением технологических схем общей и узловой сборки. Эти схемы являясь первым этапом разработки технологического процесса в наглядной форме отражают маршрут сборки изделия и его составных частей. Технологические схемы сборки составляют на основе сборочных чертежей изделия.
На последовательность сборки влияют функциональная взаимосвязь элементов изделия конструкция базовых элементов условия монтажа силовых и кинематических передач постановка легко повреждаемых элементов в конце сборки размеры и масса присоединяемых элементов а также степень взаимозаменяемости элементов изделия.
При производстве невзаимозаменяемых изделий на последовательность сборки влияют пригоночные работы промежуточные разборка и сборка соединений дополнительная обработка очистка и контроль деталей.
Технологические схемы сборки являются основой для последующего проектирования технологических процессов сборки. Сначала составляют схему общей сборки а затем схемы узловой сборки. Технологические схемы узловой сборки разрабатывают в этом случае параллельно что сокращает время на подготовку производства. Вариант схемы сборки выбирают с учетом удобств работы и контроля качества сборки числа сборщиков уменьшения необходимой оснастки и оборудования сокращения времени и себестоимости сборки а также возможности применения средств ее механизации и автоматизации. Принятый вариант схемы на последующих этапах проектирования технологии сборки может быть скорректирован с учетом необходимости догрузки сборщиков на отдельных сборочных постах.
Сборка лебедки осуществляется в следующем порядке: проводят операции связанные с тем что на ось одевается шпонка зубчатое колесо втулка подшипник и получается ось в сборе после этого собирают также и другую ось а затем проводим соединение вала-шестерни с этими осями по средствам зубчатого зацепления между колесом зубчатым и шестерней при этом необходимо соблюдение соосности. Следующим шагом является установка крышки гайки и винтов также устанавливаются подшипник втулка звезда прокладка манжета крышка гайки болты (при этом необходимо соблюдение затягиваемого усилия) эти действия позволяют достичь герметичности корпуса. Производим введения в корпус зубчатого колеса и зацеплением с зубчатыми колесами на оси. После этого проводим действия аналогичные проводимым выше с той же целью добиться герметичности. Лебе-дка в сборе.
Технология машиностроения. Сборник задач и упражнений. В.И. Аверченко и др. –М.: ИНФРА-М2005.-288 с.
Ковшов А.И.Технология машиностроения. – М.; Машиностроение1987. – 320 с.;
Косилова А.Г. Сухов М.Ф. Технология производства подъемно – транспортных машин. –М.:Машиностроение1982.-301 с.
Справочник технолога-машиностроения. В 2-х т. Под ред. А.Г. Косиловой и Р.К. Мещерякова. – М.: Машиностроение1985.- 656 с. Том 1.
Справочник технолога-машиностроения. В 2-х т. Под ред. А.Г. Косиловой и Р.К. Мещерякова. – М.: Машиностроение1985.- 656 с. Том 2.
Рекомендуемые чертежи
- 24.01.2023
Свободное скачивание на сегодня
Обновление через: 10 часов 29 минут
Другие проекты
- 24.10.2015