Технологический процесс изготовления вала электродвигателя


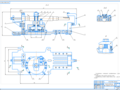
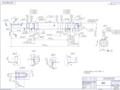
- Добавлен: 04.07.2022
- Размер: 931 KB
- Закачек: 1
Описание
Курсовой проект по технологии машиностроения
Состав проекта
![]() |
![]() |
![]() ![]() ![]() ![]() |
![]() ![]() ![]() ![]() |
![]() ![]() ![]() ![]() |
![]() ![]() ![]() |
![]() ![]() ![]() ![]() |
![]() ![]() ![]() ![]() |
![]() |
![]() ![]() ![]() ![]() |
![]() ![]() ![]() ![]() |
![]() ![]() ![]() ![]() |
![]() ![]() ![]() ![]() |
![]() ![]() ![]() ![]() |
![]() ![]() ![]() ![]() |
![]() ![]() ![]() ![]() |
![]() ![]() ![]() ![]() |
Дополнительная информация
Вал.cdw

Лист 1.cdw

Белорусско-Российский
Операция 010 -Токарная с ЧПУ
Лист2.cdw

университет гр.ТМА-021
Операция 030 - круглошлифовальная
Операия 020 - вертикально-сверлильнпя
Операция 025 - сверлильная с ЧПУ
Операция 015 - вертикально - фрезерная
ПЗ.doc
Министерство образования и науки Российской Федерации
Государственное учреждение высшего профессионального образования
Белорусско-Российский университет
Кафедра «Технология машиностроения»
По дисциплине: “Технология автоматизированного производства”
На тему: “Технологический процесс изготовления вала электродвигателя
Назначение и конструкция детали ..5
Анализ технологичности конструкции детали ..7
Определение типа производства .9
Анализ базового техпроцесса 10
Принятый маршрутный техпроцесс . 12
Расчет припусков на обработку 15
Расчет режимов резания .21
1 Расчет режимов резания аналитическим методом 21
2 Расчет режимов резания по нормативам 23
Расчет норм времени ..27
Расчет точности операции 33
Экономическое обоснование принятого варианта техпроцесса ..35
Расчет и проектирование станочного приспособления 39
1 Назначение и устройство приспособления .39
2 Выбор и расчет привода приспособления ..40
3 Расчет приспособления на прочность .43
4 Расчет приспособления на точность 44
Список использованных источников 47
Приложение А. Комплект документов на технологический процесс изготовления вала ГВИЕ.715123.004 .48
Приложение Б. Спецификация КП.021.80.21.00 СБ 49
Важнейшими условиями ускорения научно-технического прогресса являются рост производительности труда повышение эффективности общественного производства и улучшение качества продукции. Повышение эффективности машиностроительного производства переход к рыночным принципам ведения хозяйства усиление конкуренции предполагает расширение номенклатуры изделий уменьшение их числа в серии. В результате этого возрастает число предприятий и цехов ориентированных на серийный и мелкосерийный типы производства
Одним из путей повышения производительности труда и снижения себестоимости изготовления изделий является совершенствование действующих технологических процессов и их замена более прогрессивными.
Эта работа проводится на основе комплексного анализа как конструкции изделий (деталей) так и технологии их изготовления начиная с выбора более прогрессивных методов получения заготовок. Серьёзное внимание уделяется повышению качества выпускаемых изделий повышению их надёжности и долговечности.
Учитывая то что завод “Электродвигатель” на сегодняшний день не имеет достаточных средств на приобретение нового технологического оборудования основное внимание уделяется совершенствованию технологических процессов на основе имеющегося оборудования применению более совершенных приспособлений и инструментов.
Для автоматизации токарной обработки валов используется роботизированный технологический комплекс для которого разрабатывается базовая компоновка с выбором промышленного робота основного и вспомогательного оборудования. Применение РТК наиболее эффективно в условиях частой смены объектов производства что характерно для среднесерийного производства а также для автоматизации ручного низко квалифицированного труда.
Изменение технологического процесса позволяет не только улучшить форму организации производства но и в некоторых случаях получить ощутимый эффект от внедрения новых методов получения заготовки и обработки деталей.
Назначение и конструкция детали
Данная деталь относится к деталям типа “валы”. Она является валом асинхронного электродвигателя.
Асинхронный электродвигатель (рис. 1.1) - электрическая асинхронная машина для преобразования электрической энергии в механическую.
Рисунок 1.1 – Асинхронный электродвигатель
Принцип работы асинхронного электродвигателя основан на взаимодействии вращающегося магнитного поля возникающего при прохождении трёхфазного переменного тока по обмоткам статора с током индуктированным полем статора в обмотках ротора. В результате указанного взаимодействия возникают механические усилия заставляющие ротор вращаться в сторону вращения магнитного поля при условии что частота вращения ротора n меньше частоты вращения поля n1.Таким образом ротор совершает асинхронное вращение по отношению к полю.
Частоту вращения асинхронного электродвигателя регулируют в основном изменением числа пар полюсов сопротивления включенного в цепь ротора изменением частоты питающего тока а также каскадным включением нескольких машин. Направление вращения электродвигателя изменяют переключением любых двух фаз обмотки статора.
Асинхронные электродвигатели благодаря простоте в производстве и надёжности в эксплуатации широко применяют в электрическом приводе. Основные недостатки асинхронного электродвигателя — ограниченный диапазон регулирования частоты вращения и значительное потребление реактивной мощности в режиме малых нагрузок.
Двигатели серии АИР изготавливаются для внутреннего рынка и для поставок на экспорт в страны с умеренным климатом. Взрывозащищенные двигатели предназначены для приводов машин и механизмов работающих во взрывоопасных зонах помещений и наружных установках в соответствии с главой 73 ПУЭ (правил устройства электроустановок) и другими нормативными документам регламентирующими установку электрооборудования во взрывоопасных зонах для работы от сети промышленной частоты 50 Гц – для внутреннего рынка 50 и 60 Гц для поставки на экспорт.
Поверхности ø25(k6) предназначены для установки подшипников качения и являются основными поверхностями.
Поверхность ø30(t7) предназначена для посадки ротора электродвигателя и является вспомогательной поверхностью. Точность этого размера обеспечивается по седьмому квалитету с целью недопущения зазора между валом и ротором. Также посадочная поверхность ø30(t7) имеет достаточно жесткие допуски радиального биения Т = 003 мм.
На поверхности вала ø243 имеется глухое отверстие ø55 которое используется для установки вентилятора.
Вал изготавливается из стали 45 по ГОСТ4543-71. Химический состав стали приведен в таблице 1.1 механические свойства в таблице 1.2.
Таблица 1.1 – Химический состав стали 45 ГОСТ4543-71
Таблица 1.2 – Механические свойства стали 45 ГОСТ 2990-78
Анализ технологичности конструкции детали
Анализ технологичности конструкции детали будем производить в соответствии с рекомендациями изложенными в [1].
Выполним качественную оценку технологичности конструкции детали.
Вал ГВИЕ.715123.004 является цилиндрической деталью заготовка которой может быть получена как из проката так и штамповкой. Но в результате того что перепады диаметров у вала небольшие целесообразнее в качестве заготовки использовать прокат.
Точность поверхностей детали является вполне достижимой (порядка 7-14 квалитета) и может быть получена широко применимыми методами токарной обработки и шлифованием.
В большинстве операций вал может быть обработан при базировании в центровых отверстиях что обеспечивает минимальные значения торцового и радиального биения обрабатываемых поверхностей.
Обработка заготовки может проводиться с применением универсального режущего инструмента.
Все канавки для выхода шлифовального круга имеют одинаковые размеры что позволяет использовать для их получения один и тот же инструмент.
Конфигурация вала позволяет производить обработку на токарных станках различного типа.
Жесткость вала обеспечивает достижение необходимой точности при обработке так как выполняется условие отношение длины к диаметру меньше десяти.
Также наблюдается уменьшение диаметральных размеров шеек вала от середины к торцам что существенно упрощает их обработку.
Проанализировав изложенные выше пункты делаем вывод о том что данная деталь с качественной стороны является технологичной.
Выполним количественную оценку технологичности конструкции изделия. Составляем таблицу точности обработки таблица 2.1 и таблицу шероховатости поверхностей детали таблица 2.2.
Таблица 2.1 – Точность обработки детали
Квалитет точности IT
Количество размеров П
По формуле вычислим средний коэффициент точности обработки Kт.ч.
где Аср. – средний квалитет точности;
Тогда по формуле (2.1)
Таблица 2.2 – Шероховатость поверхностей детали
Шероховатость Ra мкм
Количество поверхностей П
Коэффициент шероховатости поверхности Kт.ч определяем по формуле
где Rаср – средняя шероховатость поверхностей мкм;
Тогда по формуле (2.3)
Так как расчетное значение коэффициента точности обработки больше нормативного равного 08 и значение коэффициента шероховатости поверхностей также больше нормативного равного 018 (ГОСТ 14.201-83) можно сделать вывод о том что с количественной оценки конструкция вала технологична.
Проанализировав технологичность детали с качественной и количественной стороны можно сделать вывод о том что деталь достаточно технологична. Отсюда следует что получение детали не требует применения сложных и дорогостоящих видов и методов обработки а соответственно больших затрат металла и материальных ресурсов.
Определение типа производства
Тип производства определяем ориентировочно по годовому объему выпуска используя указания [1].
Рассчитаем число деталей в партии nпо формуле
где N – годовой объем выпуска N = 12550 шт.;
a –количество дней запаса деталей на складе a = 7 дней;
m – число рабочих дней в году m = 254;
По полученному значению величины партии и массе детали принимаем среднесерийный тип производства.
Окончательное уточнение значения типа производства произведем после расчетов норм времени на каждую операцию в разделе 9.
Анализ базового техпроцесса
Анализ базового техпроцесса будем проводить с точки зрения обеспечения качества детали и организации технологического процесса.
В базовом техпроцессе применен наиболее рациональный способ получения заготовки из круглого сортового проката что снижает стоимость изделия и позволяет увеличить коэффициент использования металла.
Сортовой прокат ø32 мм применяемый в базовом варианте не полностью соответствует чертежу детали в отношении фактических припусков на обработку и выполнении всех технических требований. По расчетам припусков на обработку принимаем сортовой прокат ø34 мм (раздел 7).
При обработке вала выполняется принцип постоянства баз но не выполняется принцип единства баз. Первая операция базового технологического процесса изготовления вала ГВИЕ. 715123.004 – фрезерно-центровальная. Эта операция необходима для обработки торцов заготовки и создания искусственных технологических баз для последующих операций – центровых отверстий.
В качестве базы на фрезерно-центровальной операции при сверлении центровых отверстий используется поверхность 34 мм которая имеет достаточную протяженность и обеспечивает удобную установку заготовки в призмах.
В базовом технологическом процессе предусмотрена токарная обработка:
- черновая – на гидрокопировальном станке;
- чистовая - на токарном станке с ЧПУ.
Фрезерная операция выполняется на горизонтально-фрезерном станке FNW32*500.
Для контроля размеров используется универсальный мерительный инструмент а также приспособление для контроля симметричности шпоночного паза.
Так как производство вала среднесерийное то применение токарного и сверлильного станков с ЧПУ целесообразно.
Для обеспечения точности и высоких скоростей резания в базовом техпроцессе используются токарные резцы с механическим креплением твердосплавных пластин Т15К6 а также осевой инструмент из быстрорежущей стали Р6М5.
Приведенное количество операций и их последовательность обеспечивают получение необходимой точности поверхностей детали форму и их взаимное расположение однако возможна более рациональная форма организации технологического процесса с точки зрения минимизации общих затрат и трудоемкости на изготовление детали.
Относительно базового техпроцесса можно внести ряд изменений по его совершенствованию. Следует заменить токарно-копировальную операцию на токарную с ЧПУ на которой будет производиться как черновая так и чистовая обработка и следует заменить дорогостоящий и крупногабаритный горизонтально-фрезерный станок FNW 32*500 на более дешевый аналог для фрезерования шпоночного паза.
Метод получения заготовок определяется назначением и конструкцией детали материалом техническими требованиями масштабом и серийностью выпуска а также экономичностью изготовления. Выбрать заготовку – значит установить способ ее получения наметить припуски на обработку каждой поверхности размеры и указать допуски на неточность изготовления.
Для рационального выбора заготовки необходимо одновременно учитывать все вышеперечисленные исходные данные так как между ними существует тесная взаимосвязь.
В качестве заготовки для вала ГВИЕ 715123.004 может использоваться как прокат так и штамповка. Так как вал не имеет больших перепадов диаметров то целесообразнее использовать прокат. Можно использовать как круглый прокат так и поперечно-клиновой. Но изготовление круглого проката дешевле чем поперечно-клинового.
Таким образом согласно разделу 7 (расчет припусков на обработку) выбираем в качестве заготовки по ГОСТ 2590-71 сортовой круглый прокат обычной точности ø34 мм длиной 3196-16 мм.
Технические требования к прокату:
кривизна прутка не должна превышать 2мм;
Способ разделки проката на заготовки принимаем аналогичным базовому техпроцессу (см. раздел 6).
Основные размеры заготовки приводим на рисунке 5.1.
Рисунок 5.1 Параметры заготовки после заготовительной операции.
Принятый маршрутный техпроцесс
После анализа базового техпроцесса в проектируемый вариант был внесен ряд изменений.
В принятом варианте технологические базы остались аналогичными базовому техпроцессу. На операциях токарной и шлифовальной обработки чистовыми технологическими базами остались центровые отверстия (искусственные технологические базы) на фрезерно-центровальной операции в качестве технологической базы – наружная цилиндрическая поверхность заготовки и ее торец от которых обрабатываются центровые отверстия и торцы. Выбор баз полностью обоснован с позиции получения требуемой точности размеров детали.
Разрезка проката на заготовки будем производить на кривошипном прессе модели КА 2534.
Импортный фрезерно-центровальный станок FNW-160 был заменен на МР-73М который занимает на 04 м2 меньше производственной площади и в 13 раза дешевле. Две токарные операции выполняемые на станках с ЧПУ модели 16К20Ф3С39 и две токарно-копировальные выполняемые на гидрокопировальном токарном полуавтомате 1713 были заменены одной производимой на токарном станке с ЧПУ 16К20Ф3 с двумя установами. Шпоночно-фрезерная операция выполняемая на станке модели FNW32*500 была заменена на операцию производимую на вертикально-фрезерном станке модели 6Р13. Круглошлифовальную операцию для поверхности ø30t7 оставляем без изменений так как станок 3Б161 полностью обеспечивает требуемую точность а круглошлифовальную операцию для последовательного шлифования шеек ø25k6 ø248k6 и торцев на станке модели 3Б151 заменяем на торце-круглошлифовальную операцию на станке модели 3Т160
Принятый вариант техпроцесса приводим в приложении А. В данном приложении представлены маршрутные карты операционные карты с картами эскизов карты контроля.
Определим необходимое общее уточнение о для поверхности ø30t7 по формуле
где Tзаг – допуск на изготовление заготовки Tзаг = 11 мм;
Tдет – допуск на изготовление детали Tдет = 0021 мм;
Определим общее уточнение пр для принятого маршрута обработки по формуле
где 1 – величина уточнения полученная при черновом точении;
– величина уточнения полученная при чистовом точении;
– величина уточнения полученная при чистовом шлифовании.
Величины уточнений для переходов определяем по формуле
Тогда по формуле (6.2)
Полученное значение показывает что при принятом маршруте точность обработки поверхности ø30t7 () обеспечивается так как выполняется условие
Окончательный вариант проектируемого техпроцесса изготовления вала представляем в таблице 6.1.
Таблица 6.1 – Принятый маршрутный техпроцесс изготовления вала
Наименование и краткое содержание операции
Технологические базы. Режущий инструмент
Фрезерно-центровальная
Фрезерование торцов.
Сверление центровых отверстий.
Базы: поверхность заготовки 34 торец.
Р.И.: фреза торцовая 60 Т15К6
Сверло центровое 315 Р6М5.
Токарная с ЧПУ 16К20Ф3
Черновое точение поверхностей 3078 263 253
Чистовое точение поверхностей
Точение канавок 238 245.
Черновое точение поверхностей
Точение канавок 188 245.
Базы: центровые отверстия.
Р.И.: Резец проходной черновой T15K6 ГОСТ 26611–85.
Резец проходной чистовой ЦМ–332 ГОСТ 26611–85.
Резец канавочный Т15К6 ГОСТ 18881-73
Вертикально-фрезерная
Фрезерование паза L = 35 h=365.
Базы: наружные поверхности 193 и 30 торец
Р.И.: фреза концевая 6 Р6М5 ГОСТ 9140–78.
Вертикально-сверлильная
Сверление отверстия 55 L =3
Р.И.: сверло ГОСТ 10902-77
Сверление отверстия 67 L =257
Зенкерование отверстия 84 L =82
Р.И.: сверло ГОСТ 10902-77 зенкер ГОСТ 3231-71 зенковка 2353-0127 Р6М5 ГОСТ 14953-80 метчик М8×2 ГОСТ 3266-81.
Чистовое шлифование поверхности 30.
Р.И.: шлифовальный круг 600×63×305
Расчет припусков на обработку
Рассчитаем припуски на обработку и промежуточные предельные размеры на поверхности ø30t7() мм и 3175h11()мм используя [1].
Технологический маршрут обработки поверхности ø30 мм состоит из чернового и чистового обтачивания и чистового шлифования. Так как обработка ведется в центрах погрешность установки в радиальном направлении равна нулю. Суммарное значение пространственных погрешностей ρз мм вычисляем по формуле
где rк.о. – общая кривизна заготовки мм;
rц – погрешность зацентровки мм;
где Dк – удельная кривизна стержня Dк = 015 мкммм;
(выбираем по таблице 4.8)
L – длина заготовки L = 3175 мм;
Погрешность зацентровки определим по формуле
где з – допуск на поверхность используемой в качестве базовой на фрезерно-центровальной операции з = 11 мм;
Остаточное пространственное отклонение rост мкм для чернового и чистового обтачивания вычислим по формуле
где kу – коэффициент уточнения формы. Для чернового точения kу = 006 для чистового kу = 004.
После чернового обтачивания rост1
После чистового обтачивания rост2
Расчет минимальных значений припусков zmin мкм производим по формуле
ρi-1 – суммарное значение пространственных отклонений образованных на предшествующей операции мкм.
Под черновое обтачивание
Под чистовое обтачивание
Под чистовое шлифование
Определим расчетный размер dр мм для каждого из переходов
Наибольшие предельные размеры вычислим путем прибавления допуска к округленному наименьшему предельному размеру
Предельное значение максимального припуска мм определяем как разность наибольших предельных размеров
Предельное значение минимального припуска мм определяем как разность наименьших предельных размеров
Рассчитаем общие припуски zоmin zоmax мм суммируя промежуточные припуски
Номинальный припуск zоном мм в данном случае определяем с учетом несимметричного расположения поля допуска заготовки
где Нз – нижнее отклонение размера заготовки Нз = 07 мм;
Нд – нижнее отклонение допуска детали Нд = 0041 мм;
Тогда номинальный размер заготовки dзном мм находим по формуле
Проверка правильности расчетов
Проверка выполнена. Все расчеты сводим в таблицу 7.1 а графическое изображение припусков и допусков представляем на рисунке 7.1.
Таблица 7.1 – Расчет припусков по технологическим переходам на обработку поверхности вала ø30t7() мм.
Технологические переходы обработки поверхности ø90
Элементы припуска мкм
Предельный размер мм
Предельные значения припусков мм
Рисунок 7.1 Схема графического расположения припусков и допусков на обработку поверхности ø30t7() мм.
Исходя из расчетов принимаем в качестве заготовки круглый сортовой прокат обычной точности ø34 мм.
Технологический маршрут обработки поверхности 3175h11() мм состоит из фрезерования чернового.
Запишем технологический маршрут обработки а также соответствующие заготовке и каждому технологическому переходу значения элементов припуска в таблицу 7.2.
Суммарное значение пространственных погрешностей ρз мм принимаем равной величине рассчитанной выше
где rкор. – погрешность заготовки по короблению мм;
rт – отклонение от перпендикулярности торцов к оси заготовки мм;
Отклонение от перпендикулярности торцов к оси заготовки rт мм вычислим по формуле
Суммарное значение пространственных погрешностей ρз мм
Расчет минимальных значений межоперационных припусков zmin мкм производим по формуле (7.6).
Под черновое фрезерование
Предельные значения максимальных припусков мм определяем как разность наибольших предельных размеров
Предельные значения минимальных припусков мм определяем как разность наименьших предельных размеров
Номинальный припуск zоном мм в данном случае определяем с учетом несимметричного расположения поля допуска заготовки по формуле (7.7)
где Нз – нижнее отклонение поля допуска заготовки Нз = 18 мм;
Нд – нижнее отклонение поля допуска детали Нд = 036 мм;
Тогда номинальный длина заготовки Lзном мм
Все математические расчеты сводим в таблицу 7.2 а графическое изображение припусков и допусков представляем на рисунке 7.2.
Таблица 7.2 – Расчет припусков и предельных размеров по технологическим переходам на обработку поверхности 3175h11() вала мм.
Фрезерование черновое
Рисунок 7.2 Схема графического расположения припусков и допусков на обработку поверхности 3175h11().
Расчет режимов резания
1Расчет режимов резания аналитическим методом
Рассчитаем режимы резания на две операции по эмпирическим формулам теории резания используя формулы и данные из таблиц [3].
Операция № 030 Круглошлифовальная.
Чистовое шлифование шейки ø30t7().
Эффективная мощность NкВт
где СN – коэффициент учитывающий обрабатываемый материал СN =014 [3таблица 56];
з – скорость вращения заготовки з = 25 ммин [3таблица 55];
d – диаметр шлифования d = 30 мм;
sр – радиальная подача sр = 0002 ммоб [3таблица 55];
r – показатель степени r = 08 [3таблица 56];
q – показатель степени q = 02 [3таблица 56];
z – показатель степени z = 10 [3таблица 56];
Операция № 020 вертикально-сверлильная.
Сверление отверстия ø55+0012.
Определим скорость резания v ммин.
где Сv – коэффициент учитывающий обрабатываемый материал Сv =7 [3таблица 28];
D – диаметр сверла D=55 мм;
T – стойкость инструмента T = 15 мин. [3таблица 30];
s – подача на оборот s = 01 ммоб [3таблица 25];
q – показатель степени q = 04 [3таблица 28];
y – показатель степени y = 07 [3таблица 28];
m – показатель степени m = 02 [3таблица 28];
Кv – общий поправочный коэффициент на скорость резания.
Определим коэффициент Кv по формуле
где Кмv – коэффициент учитывающий качество обрабатываемого материала;
Киv – коэффициент учитывающий материал инструмента Киv=1;
Кпv – коэффициент учитывающий состояние поверхности Кпv=1;
Значение коэффициента Кмv рассчитаем по формуле
где GB – предел прочности GB = 610 МПа;
KГ – коэффициент учитывающий группу стали KГ = 10;
nv – показатель степени nv = 09 (табл. 2);
Тогда по формуле (8.1.2) скорость резания
Определим крутящий момент Мкр Н·м
где СM – коэффициент учитывающий обрабатываемый материал СM = 00345 [3таблица 32];
S – подача на оборот s = 01 ммоб [3таблица 25];
Кр – общий поправочный коэффициент на силу резания;
y – показатель степени y = 08 [3таблица 32];
q – показатель степени q = 2 [3таблица 32];
где n – показатель степени учитывающий материал инструмента n = 09 [3таблица 9];
Тогда по формуле (8.1.5) крутящий момент Н·м
Определим осевую силу Ро H по формуле
где СР – коэффициент учитывающий обрабатываемый материал СР = 68 [3таблица 32];
y – показатель степени y = 07 [3таблица 32];
q – показатель степени q = 1 [3таблица 32];
Тогда по формуле (8.1.7) осевая сила Н
Определим эффективную мощность резания Nе кВт по формуле
где n – частота вращения инструмента мин-1
Тогда по формуле (8.1.8) эффективная мощность резания кВт
2Расчет режимов резания по нормативам
Все расчеты производим по формулам и таблицам из [5].
Операция № 005 фрезерно-центровальная.
Переход 1: сверление центровых отверстий ø315 мм.
Длина рабочего хода Lр.х мм
где Lрез – длина резания Lрез = 7 мм;
у – длина подвода врезания y = 15 мм [5с. 303];
Выберем подачу на оборот шпинделя sо ммоб
Определяем нормативную скорость резания v ммин
где vтабл – табличная скорость резания vтабл = 26 ммин [5с. 115];
K1 – коэффициент учитывающий материал обработки K1 = 08 [5с. 116];
К2 – коэффициент учитывающий стойкость сверла К2 = 125 [5с. 116];
К3 – коэффициент учитывающий отношение длины к диаметру сверла К3 = 10 [5с. 117];
Определяем рекомендуемую частоту вращения шпинделя n мин-1
где d – диаметр обработки d = 67 мм;
Уточняем число оборотов шпинделя по паспорту станка.
Определим основное машинное время обработки tм мин
Операция № 015 вертикально-фрезерная.
Фрезерование паза L = 35 мм h=365мм.
Длина рабочего хода суппорта Lр.х. мм
где Lрез – длина резания Lрез = 35 мм;
у – длина врезания y =3 мм [5с. 303];
Выберем подачу на зуб фрезы Sz ммpe [5с. 83];
где vтабл – табличная скорость резания vтабл = 34 ммин;
K1 – коэффициент учитывающий материал обработки K1 = 1 [5с. 91];
К2 – коэффициент учитывающий стойкость резца К2 = 11 [5с. 91];
К3 – коэффициент учитывающий размеры обработки К3 = 1 [5с. 90];
Определяем рекомендуемую частоту вращения шпинделя n мин-1 по формуле (8.2.3)
где d – диаметр обработки d = 6 мм;
Определим основное машинное время обработки tм мин по формуле (8.2.4)
Аналогично рассчитываем режимы резания на все стальные операции и результаты записываем в таблицу 8.1.
Таблица 8.1 – Сводная таблица режимов резания
Наименование операции перехода
Глубина резания t мм
Длина резания Lрез мм
Частота вращения n мин-1
Минутная подача sм мммин
Черновое точение поверхностей
Чистовое точение поверхностей
Вертикально-фрезерная
Вертикально-сверлильная
Сверление отверстия ø55Н12
Зенкерование отверстия
Зенкование поверхности
Чистовое шлифование поверхности
Рассчитаем нормы времени для операций на которые рассчитаны режимы резания в разделе 8 пользуясь формулами приведенными в [13].
В серийном производстве определяется штучно-калькуляционное время tшт-к мин
где tп.з. – подготовительно-заключительное время
n – число деталей в партии.
Рассчитаем штучное время tшт мин
где tо – основное время мин;
tв – вспомогательное время мин;
tобс – время на обслуживание рабочего места мин;
tотд – время на отдых и личные надобности мин.
Фрезерование паза L = 35 h=365мм..
Определяем основное время обработки tо1 мин
где Lр.х. – длина рабочего хода фрезы мм;
sм. – минутная подача при фрезеровании мммин;
y – величина врезания y= 3 мм.
Определяем минутную подачу SM мммин
где sz – подача на зуб при фрезеровании sz. = 001 ммзуб;
z – число зубьев фрезы z = 4;
n – частота вращения фрезы обмин;
K1 – коэффициент учитывающий материал обработки K1 = 1;
К2 – коэффициент учитывающий стойкость резца К2 = 11;
К3 – коэффициент учитывающий размеры обработки К3 = 1;
Определяем рекомендуемую частоту вращения шпинделя n мин-1
Тогда по формуле (9.5)
Тогда по формуле (9.3)
Определяем вспомогательное время tв мин
где tуст. – время на установку и снятие детали tуст. = 008 мин;
tз.о – время на закрепление и открепление детали tз.о = 0024 мин;
tупр – время на приемы управления станком tупр = 025 мин;
tизм. – время на измерение детали tизм. = 016 мин;
к поправочный коэффициент к = 185;
Время на отдых и обслуживание рабочего места:
Тогда штучное время tшт мин по формуле (9.2) равняется
Тогда по формуле (9.1) tшт-к мин
Операция № 030 круглошлифовальная
где Lр.х. – длина рабочего хода шлифовального круга Lр.х. = 02 мм;
sо – подача при шлифовании sо = 0002 ммоб;
n – частота вращения заготовки обмин;
Определяем рекомендуемую частоту вращения заготовки n
где d – диаметр обработки d = 30 мм.
Принимаем скорость вращения заготовки v ммин [3таблица 55];
Тогда по формуле (9.11)
Тогда по формуле (9.10)
Определяем вспомогательное время операции tв мин с учетом поправочного коэффициента на серийность производства
tупр – время на приемы управления станком tупр = 01 мин;
tизм. – время на измерение детали tизм. = 027 мин;
к поправочный коэффициент к = 185.
Таблица 9.1 Сводная таблица норм времени
Наименование операции
Основное время to мин
Вспомогательное время tв мин
Оперативное время toп мин
tобс и отдыха tотд мин
Штучное время tшт мин
Подготовительно –заключит. время tп.з мин
Штучно – калькуляцион. время tшт-к мин
Вертикально сверлильная
На основании рассчитанных норм времени производим уточнения типа производства используя данные таблицы 9.1. Все расчеты сводим в таблицу 9.2.
Определяем расчетное количество станков mр по формуле
где N – годовой объем выпуска деталей N = 12550 шт.;
tшт-к – штучно-калькуляционное время;
FД – действительный фонд времени FД = 4029 ч;
з.н. – нормативный коэффициент загрузки оборудования з.н. = 085 [1].
Фактический коэффициент загрузки рабочего места з.ф. вычисляется по формуле
где P – принятое количество станков.
Количество операций О выполняемых на рабочем месте определяется по формуле
Рассчитанные параметры по приведенным формулам заносим в сводную таблицу 9.2.
Таблица 9.2 – Параметры для уточнения типа производства
Определим коэффициент закрепления операций Кз.о.
По ГОСТ 3.1121-84 рассчитанному коэффициенту закрепления операций соответствует крупносерийный тип производства (Кз.о. = 2 10).
Расчёт точности операции
Расчёт точности выполним для операции чистовой токарной обработки шейки вала ø30() которая выполняется на токарном станке с ЧПУ методом автоматического получения размеров в соответствии с порядком изложенным в [7]. В результате проведения расчёта необходимо подтвердить достижение точности на данной технологической операции. Это значит что величина суммарной погрешности не должна превышать величины допуска на получаемый размер.
расчетный диаметр обработки dр = 3078 мм;
величина поля допуска получаемая при чистовом точении = 210 мкм;
расчетная длина обработки L = 33 мм;
подача при чистовом точении sо = 04 ммоб.
Величина суммарной погрешности обработки DS по диаметральным и продольным размерам в общем виде в серийном производстве определяется по формуле
где Dи – погрешность обусловленная износом инструмента мкм;
Dн – погрешность настройки станка мкм;
Dсл – поле рассеяния погрешности обработки обусловленных действием случайных факторов мкм;
Dу – погрешность установки заготовки мкм.
Погрешность обработки обусловленную износом режущего инструмента рассчитаем по формуле
где uо – относительный износ инструмента uо = 05 мкмкм [7таблица 3.3];
l – путь резания при обработке деталей м.
где d - диаметр обрабатываемой поверхности d = 3078 мм;
L - расчетная длина обработки L= 33 мм;
n – количество деталей в настроечной партии n = 25;
sо – подача инструмента sо = 04 ммоб.
Определяем погрешность настройки станка
где Dсм – смещение центра группирования размеров пробных деталей относительно середины поля рассеивания размеров мкм;
Dрег – погрешность регулирования положения режущего инструмента на станке Dрег = 10 мкм [7таблица 3.11];
Dизм – погрешность измерения пробных деталей Dизм = 15 мкм [7таблица 3.13].
где m – количество пробных деталей m = 5 шт;
Dсл – мгновенная погрешность обработки Dсл = 40 мкм.
Таким образом по формуле (10.4)
Поскольку обработка заготовки производиться в центрах погрешность установки заготовки
Суммарная погрешность обработки по формуле (10.1)
При сравнении с точностью заданного размера суммарной погрешности обработки можно сделать вывод о том что в данных условиях имеется возможность обеспечить требуемую точность обработки так как выполняется условие
Экономическое обоснование принятого варианта техпроцесса
Экономическое сравнение базового и принятого техпроцессов проводим по текущим и приведенным капитальным затратам на единицу продукции для токарно-копировальной операции (базовой) и токарной с ЧПУ (проектируемой) в соответствии с порядком изложенным в главе 12 [8].
Исходные данные экономического обоснования сводим в таблицу 11.1.
Общая площадь на один станок м2
Мощность электродвигателя кВт
Годовой объем выпуска изделий шт.
0.Токарно-копировальная
Проектируемый вариант
Таблица 11.1 Исходные данные для экономического обоснования.
Приведенные затраты З руб для двух сравниваемых вариантов техпроцесса рассчитываются по формуле
где C – технологическая себестоимость руб.;
Ен – коэффициент экономической эффективности капитальных вложений (Ен = 05);
Кс и Кз – удельные капитальные вложения в станок и здание соответственно.
Расчет технологической себестоимости по сравниваемым операциям производим по формуле
где Сз – основная и дополнительная зарплата с начислениями руб.;
Сэксп – часовые затраты по эксплуатации рабочего места руб.
Расчет основной и дополнительной зарплаты с начислениями выполняется по формуле
где Сч – часовая тарифная ставка рабочего 5 – го разряда Сч = 1800 руб.час;
Кд – коэффициент учитывающий дополнительную зарплату и начисления (Кд = 17);
Зн – коэффициент учитывающий зарплату наладчика (Зн = 10);
Ко.м – коэффициент учитывающий оплату рабочего при многостаночном обслуживании (Ко.м = 17).
Зарплата рабочего-станочника 5 разряда для сравниваемых вариантов будет
Расчёт часовых затрат по эксплуатации рабочего места Сэксп руб выполняется по формуле
где Сч.з. – часовые затраты на базовом рабочем месте Сч.з .= 890 Сч.з. = 1090 руб.час для базового и проектируемого варианта соответственно;
Км – коэффициент показывающий во сколько раз затраты связанные с работой данного станка больше чем аналогичные расходы у базового станка Км = 07 Км = 14 для базового и проектируемого варианта соответственно.
Определяем часовые затраты по эксплуатации рабочего места базового варианта
Определяем часовые затраты по эксплуатации рабочего места проектируемого варианта
Технологическая себестоимость сравниваемой операции для базового варианта по формуле (11.2) будет равна
Технологическая себестоимость сравниваемой операции для проектируемого варианта будет равна
Рассчитаем капитальные вложения.
Удельные капитальные вложения включают в себя вложения в технологическое оборудование и здание приходящие на единицу продукции.
Капитальные вложения в оборудование Кс млн. руб. рассчитываются по формуле
где Цс – отпускная цена станка млн.руб.;
Км – коэффициент учитывающий затраты на транспортировку и монтаж (Км = 11);
Сп – принятое число станков на операцию;
N – годовой объем выпуска деталей.
Определим капитальные вложения в оборудование для базового варианта
Определим капитальные вложения в оборудование для проектируемого варианта
Удельные капитальные вложения в здание рассчитываются по формуле
где Спл – стоимость одного квадратного метра площади Спл = 300000 рубм2;
Пс – площадь занимаемая одним станком с учетом проходов м2;
Сп – принятое число станков на операцию (Сп = 10).
где f – площадь станка в плане (длина к ширине) м2;
Кс – коэффициент учитывающий дополнительную производственную площадь (К = 35 при f = 2 4 м2; К = 3 при f = 4 6 м2 К = 4 при f 2 м2).
Тогда площадь занимаемая одним станком с учетом проходов Пс для базового и проектируемого варианта будет соответственно равна
Определим удельные капитальные вложение в здание по базовому варианту
Удельные капитальные вложения в здание по принятому варианту
Рассчитаем величину годового экономического эффекта для чего определяем приведенные затраты для базового и проектируемого техпроцесса по формуле (11.1)
Годовой экономический эффект на единицу Э руб. продукции от внедрения принятого варианта техпроцесса определяем по формуле
где Збаз – приведенные затраты по базовому техпроцессу на единицу изделия;
Зпр – приведенные затраты по проектируемому техпроцессу на единицу изделия;
Все полученные результаты сводим в таблицу 11.2.
Таблица 11.2 Расчет удельных капитальных затрат на оборудование
Расчет и проектирование станочного приспособления
1Назначение и устройство приспособления
Проектируемое приспособление предназначено для сверления отверстия на цилиндрической поверхности вала в кондукторной втулке на вертикально-сверлильном станке модели 2А125.
По сравнению с базовым вариантом в конструкцию приспособления были внесены усовершенствования:
для точного направления и позиционирования откидного фиксатора установленного на плиту используется направляющая шпонка.
Окончательную конструкцию приспособления приводим в приложении Б. Приспособление состоит из следующих сборочных единиц и деталей: корпус стойка кондукторная плита кондукторная втулка прихват вал упор.
Базирование заготовки в приспособлении происходит в призмах с упором в торец. Для получения отверстия на одной образующей со шпоночным пазом используется откидной фиксатор.
Базирование приспособления на стол станка осуществляется по плоскости плиты и боковым поверхностям шпонки.
2Выбор и расчет привода приспособления
В процессе обработки отверстий сверлением обрабатываемая заготовка находится под воздействием крутящего момента М и осевого усилия Ро. Сила подачи и сила зажима действуют в одном направлении прижимая заготовку. Под действием крутящего момента резания М деталь стремится повернуться вокруг оси. Этому противодействует момент трения Мтр создаваемый осевым усилием зажима Q. Расчётная схема приспособления представлена на рисунке 12.1
Рисунок 12.1 - Расчётная схема приспособления
Рассчитаем величину необходимого усилия закрепления на штоке пневмокамеры Q’ Н используя формулы из [9]
где М – крутящий момент на сверле М=155Н·м (пункт 8.1);
d – диаметр сверла d=55мм;
k – коэффициент запаса;
R – расстояние от центра сверла до центра заготовки R=1215мм;
Р0 – осевое усилие Po=7015Н (пункт 8.1);
f – коэффициент трения;
R1– расстояние от середины опорной площадки до центра заготовки R1=120мм
Коэффициент запаса рассчитывается по формуле из [9]:
k=k0*k1*k2*k3*k4*k5*k6 (12.2.2)
где k0=15 –гарантированный коэффициент запаса;
k1=12 – коэффициент учитывающий степень износа инструмента;
k2=11 - коэффициент учитывающий увеличение силы резания от затупления сверла;
k3=1 - коэффициент учитывающий условия обработки при прерывистом резании;
k4 =1 - коэффициент учитывающий непостоянство сил закрепления;
k5=1 - коэффициент характеризующий степень удобства расположения рукояток в ручных зажимах;
k6=15 - коэффициент учитывающий только наличие моментов стремящихся повернуть заготовку на опорах;
Тогда по формуле (12.2.1):
Рассчитаем величину развиваемого усилия закрепления на штоке пневмоцилиндра Q Н используя формулы из [9]
где D – диаметр диафрагмы D =71 мм;
d – диаметр опорной шайбы d=56 мм;
p – давление воздуха в цилиндре p = 04 МПа;
Р – усилие возвратной пружины Р =48 Н [9 с.222]
– коэффициент полезного действия пневмоцилиндра = 09;
Определим необходимый диаметр диафрагмы Dрмм.
Сравниваем значение диаметра диафрагмы D с расчетным Dр делаем вывод что пневмопривод позволяет вести обработку на заданных режимах резания.
3Расчет приспособления на прочность
Произведем проверку на прочность болтовых соединений неподвижного корпуса с плитой пользуясь рекомендациями [11]. По формуле 1.32 [11] рассчитаем необходимый внутренний диаметр резьбы d1 мм
где Fр – суммарная нагрузка на болт Н;
допускаемое напряжение = 160 МПа [11табл.1.1и 1.2];
Вычислим расчетную суммарную нагрузку на болт по формуле
где Fзат сила затяжки болта Н;
F внешняя нагрузка Н;
где F1 главная составляющая силы резания F1 = 7015 Н;
F1 горизонтальная составляющая силы резания F1 = 282 Н;
F3 величина усилия зажима F3 =9016 Н;
n – число болтов крепящих неподвижный корпус n = 4;
где Кзат коэффициент затяжки Кзат = 4 (стр.41 [11]);
Тогда по формуле (12.3.1)
По полученному значению внутреннего диаметра резьбы выбираем болт М8.
4Расчет приспособления на точность
Расчет приспособления на точность будем производить в соответствии с методикой изложенной в [12].
Определяем допуск на изготовление приспособления Тпр мм для обеспечения точности размера ø (расстояние от оси отверстия до торца вала) по формуле
где Т – допуск на обработку мм;
Kт – коэффициент учитывающий отклонение рассеяния значений составляющих величин от закона нормального распределения kт = 11;
Kт1 коэффициент учитывающий уменьшение предельного значения погрешности базирования при работе на настроенных станках kт1 = 07;
Kт2 коэффициент учитывающий долю погрешности обработки в суммарной погрешности вызванной факторами не зависящими от приспособления kт2 = 08;
б погрешность базирования заготовки мм;
з погрешность закрепления мм;
у погрешность установки приспособления на станке мм;
и погрешность связанная с износом элементов приспособления мм;
п погрешность от перекоса режущего инструмента мм;
w экономическая точность обработки отверстия w = 0340 мм (табл. П10 [12]);
Погрешность базирования заготовки в соответствии с рекомендациями таблицы 3.1 [12] принимаем равной
Погрешность закрепления исключаем из расчетов т.к. пневмопривод обеспечивает постоянное усилие зажима.
Вследствие надежного контакта установочной плоскости приспособления с плоскостью стола станка принимаем погрешность установления приспособления на станке равной
Погрешность связанную с износом элементов приспособления принимаем равной и = 0
Так как в приспособлении присутствуют направляющие элементы то погрешность от перекоса инструмента будет равна
Таким образом по формуле (12.4.1) имеем
Делаем вывод что допуск параллельности оси упора относительно плоскости плиты должен составлять Т = 0061 мм.
В результате выполнения данного курсового проекта был проведен полный анализ и разработка технологического процесса получения вала в условиях среднесерийного производства
По отношению к базовому техпроцессу был предложен ряд изменений:
импортный фрезерно-центровальный станок FNW-160 был заменен на МР-73М который занимает на 04 м2 меньше производственной площади и в 13 раза дешевле;
две токарные операции выполняемые на станках с ЧПУ модели 16К20Ф3С39 и две токарно-копировальные выполняемые на гидрокопировальном токарном полуавтомате 1713 в базовом техпроцессе были заменены одной производимой на токарном станке с ЧПУ 16К20Ф3 с двумя установами. Это в свою очередь экономит производственные площади и уменьшает число обслуживающего персонала;
шпоночно-фрезерная операция выполняемая на импортном станке модели FNW32*500 была заменена на операцию производимую на вертикально-фрезерном станке модели 6Р13 который занимает на 098 м2 меньше производственной площади и в 14 раза дешевле;
на токарной операции вместо цельных резцов используются резцы с механическим креплением твёрдосплавных пластинок Т15К6
был применен РТК на токарной операции который в интеграции со станком с ЧПУ является наивысшей степенью автоматизации.
Горбацевич А.Ф. Курсовое проектирование по технологии машиностроения Шкред В.А.. - Мн.: Выш. школа 1983 – 256 с.
Справочник технолога-машиностроителя: Т.1 Под ред. А.Г. Косиловой и Р.К. Мещерякова. 4-е изд. перераб. и доп. М.: Машиностроение 1985.
Справочник технолога-машиностроителя: Т.2 Под ред. А.Г. Косиловой и Р.К. Мещерякова. 4-е изд. перераб. и доп. М.: Машиностроение 1985.
Обработка металлов резанием: Справ. Под ред. Г.А. Монахов В.Ф. Жданович Э.М. Радинский и др. М.: Машиностроение 1974. 600 с.: ил.
Руденко П.А. Проектирование и производство заготовок в машиностроении: Учеб. пособие Ю.А. Харламов В.М. Плескач; К.: Выща шк. 1991.247 с.; ил.
Режимы резания металлов: Справочник Под ред. Ю.В. Барановского – М.: Машиностроение 1972.
Дипломное проектирование по технологии машиностроения: Учеб. пособие для вузов В.В. Бабук П.А. Горезко К.П. Забродин и др.; Под ред. В.В. Бабука. Мн.: Выш. школа 1979. 464 с. ил.
Проектирование технологических процессов в машиностроении: Учеб. пособие для вузов И.П. Филонов Г.Я. Беляев Л.М. Кожуро и др.; Под ред. И.П. Филонова. Мн.: УП ”Технопринт” 2003. 910 с.
Ансеров М.А. Приспособления для металлорежущих станков. М.: Машиностроение 1975. 651с.: ил.
Технологическая оснастка. Учебник для студентов машиностроит. специальностей вузов М.Ф. Пашкевич Ж.А. Мрочек Л.М. Кожуро В.М. Пашкевич; Под ред. М.Ф. Пашкевича. – Мн .:Адукацыя и выхаванне 2002. – 320 с .: ил.
Иванов М.Н. Детали машин: Учеб. для студентов втузов Под ред. В.А Финогенова. 6-е изд. перераб. М.: Высш. школа 1998. 383 с.: ил.
Горохов В.А. Проектирование и расчет приспособлений: Учеб. пособие для студентов вузов машиностроительных специальностей Мн.: Выш. шк. 1986. – 238 с.: ил.
Лукашенко В.А. Курсовое проектирование по технологии машиностроения. Методические указания по курсовому проектированию для студентов специальности Т.03.01.00 – Технология и автоматизация машиностроения. – Могилев: МГТУ 2001. 48 с.
Комплект документов на технологический процесс
Спецификация КП.021.80.21.00 СБ
Приспособление.cdw

Приспособление комлектуется распределительным краном
Маркировать 7309-4408 БИПМ 715123.001 АИР100.
Периодическому контролю подлежат деталь поз.8 - износ до
Спецификация приспособление 1.spw

КП.021.80.21.00.00.00
КП.021.80.21.00.01.00
КП.021.80.21.00.02.00
КП021.80.21.00.03.00
КП.021.80.21.00.00.01
КП.021.80.21.00.00.02
КП.021.80.21.00.00.03
КП.021.80.21.00.00.04
Планка направляющая
КП.021.80.21.00.00.05
КП.021.80.21.00.00.06
КП.021.80.21.00.00.07
КП.021.80.21.00.00.08
КП.021.80.21.00.00.09
Фрагмент.frw

Белорусско-Российский
Фрагмент1.frw

Фрезерно-центровальная
Наименование операции
Обозначение программы
Сталь 45 ГОСТ 2990-78
ГОСТ 3.1404-86 Форма 3
Фрезеровать поверхности 1
Сверлить центровые отверстия 3
Приспособление при станке; фрезы торцовые 2214-4348
14-4349 Т15К6 ГОСТ 26595-86; штангенциркуль
Приспособление при станке; сверла центровые 2317-0012 Р6М5 ГОСТ 14952-75; штангенциркуль
Контроль рабочим 100%
Фрагмент2.frw

Патрон поводковый; резец 2102-4317 Т15К6 ГОСТ 26611-85; скоба СР 50 ГОСТ 11098-75;
штангенглубиномер ШГ-250-0
Патрон поводковый; резец 2102-4332А ЦМ-32 ГОСТ26611-85;
скоба СР50 ГОСТ11098-75;
концевые меры 2-Н1 ГОСТ 9038-90;
Патрон поводковый; резец 2100-2195 Т15К6 ГОСТ26611-85;
Наименование операции
Обозначение программы
Сталь 45 ГОСТ 2990-78
ГОСТ 3.1404-86 Форма 3
Установ А 1. Переход1. Точить поверхность 1-3
Точить поверхность 1-6
Фрагмент3.frw

Патрон поводковый; резец 2102-4317 Т15К6 ГОСТ 26611-85; скоба СР 50 ГОСТ 11098-75;
штангенглубиномер ШГ-250-0
Патрон поводковый; резец 2102-4332А ЦМ-32 ГОСТ26611-85;
скоба СР50 ГОСТ11098-75;
концевые меры 2-Н1 ГОСТ 9038-90;
Патрон поводковый; резец 2100-2195 Т15К6 ГОСТ26611-85; шаблон
Наименование операции
Обозначение программы
Сталь 45 ГОСТ 2990-78
ГОСТ 3.1404-86 Форма 3
Установ Б 1. Переход4. Точить поверхность 1-3
Точить поверхность 1-5
Фрагмент4.frw

Фрагмент5.frw

Фрагмент6.frw

Приспособление сверлильное; метчик М 8
Р6М5 ГОСТ 3266-81; штангенциркуль ШЦ
Наименование операции
Обозначение программы
ГОСТ 3.1404-86 Форма 3
пробка 8221-3111 (М8-6Н) ГОСТ 17758-72; шаблон
Контроль рабочим 100%
Сталь 45 ГОСТ 2990-78
Фрагмент7.frw

Центр 7032-0029 Морзе 4 ГОСТ 13214-79; хомутик 7107-0072 ГОСТ 16488-70; круг шлифовальный 600
П С1 ГОСТ 2424-83; эталон 8736-4087; концевые меры 2-Н1 ГОСТ 9038-90;набор образцов
Контроль рабочим 100%
Наименование операции
Обозначение программы
Сталь 45 ГОСТ 2990-78
ГОСТ 3.1404-86 Форма 3
Шлифовать поверхность 1
штангенглубиномер ШГ-250-0
Рекомендуемые чертежи
- 24.01.2023