Разработка процесса изготовления деталей


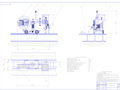

- Добавлен: 25.10.2022
- Размер: 854 KB
- Закачек: 1
Узнать, как скачать этот материал
Подписаться на ежедневные обновления каталога:
Описание
Разработка процесса изготовления деталей
Состав проекта
![]() |
![]() ![]() |
![]() |
![]() ![]() |
![]() |
![]() ![]() ![]() ![]() |
![]() ![]() ![]() |
![]() ![]() ![]() ![]() |
Дополнительная информация
Контент чертежей
Чертеж1.dwg
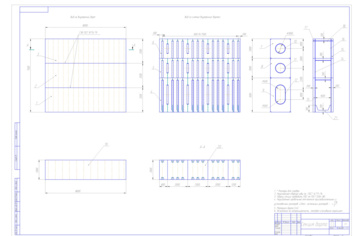
автомат.dwg
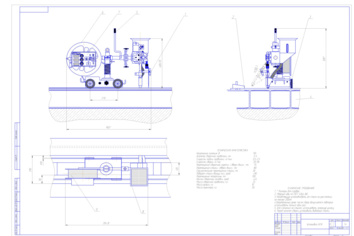
Рекомендуемые чертежи
- 24.01.2023
- 24.01.2023
- 30.08.2014
Свободное скачивание на сегодня
Обновление через: 4 часа 10 минут
Другие проекты
- 20.08.2014