Разработка технологического процесса изготовления деталей тестоокруглительной маашины




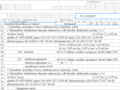
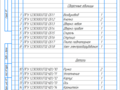
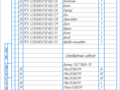
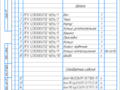
- Добавлен: 24.01.2023
- Размер: 3 MB
- Закачек: 1
Описание
Разработка технологического процесса изготовления деталей тестоокруглительной маашины
Состав проекта
![]() |
![]() |
![]() ![]() ![]() ![]() |
![]() ![]() ![]() |
![]() ![]() ![]() |
![]() ![]() ![]() |
![]() ![]() ![]() |
![]() ![]() ![]() |
![]() |
![]() |
![]() ![]() ![]() ![]() |
![]() ![]() ![]() ![]() |
![]() ![]() ![]() ![]() |
![]() ![]() ![]() ![]() |
![]() |
![]() ![]() ![]() ![]() |
![]() ![]() ![]() ![]() |
![]() |
![]() ![]() ![]() ![]() |
![]() |
![]() |
![]() ![]() ![]() ![]() |
![]() ![]() ![]() ![]() |
![]() |
![]() |
![]() |
![]() |
![]() |
![]() |
![]() ![]() ![]() ![]() |
![]() |
![]() ![]() ![]() ![]() |
![]() |
![]() |
![]() |
![]() ![]() ![]() ![]() |
![]() ![]() ![]() ![]() |
![]() |
![]() ![]() ![]() ![]() |
![]() |
![]() ![]() ![]() ![]() |
![]() ![]() ![]() ![]() |
![]() ![]() ![]() ![]() |
![]() ![]() ![]() ![]() |
![]() ![]() ![]() ![]() |
![]() |
![]() |
![]() |
![]() ![]() ![]() ![]() |
![]() ![]() ![]() ![]() |
![]() ![]() ![]() ![]() |
![]() |
![]() |
![]() |
![]() |
![]() |
![]() |
![]() ![]() ![]() ![]() |
![]() |
![]() ![]() ![]() ![]() |
![]() ![]() ![]() ![]() |
![]() |
![]() |
![]() |
![]() ![]() ![]() ![]() |
![]() |
![]() |
![]() ![]() ![]() ![]() |
![]() ![]() ![]() ![]() |
![]() |
![]() ![]() ![]() ![]() |
![]() ![]() ![]() ![]() |
![]() ![]() ![]() |
![]() ![]() ![]() ![]() |
![]() ![]() ![]() |
![]() ![]() ![]() ![]() |
![]() |
![]() |
![]() ![]() ![]() ![]() |
![]() |
![]() ![]() ![]() ![]() |
![]() ![]() ![]() ![]() |
![]() ![]() ![]() ![]() |
![]() |
![]() |
![]() ![]() ![]() ![]() |
![]() ![]() ![]() ![]() |
![]() |
![]() |
![]() ![]() ![]() ![]() |
![]() |
![]() ![]() ![]() ![]() |
![]() ![]() ![]() ![]() |
![]() |
![]() ![]() ![]() ![]() |
![]() |
![]() |
![]() |
![]() |
![]() ![]() ![]() ![]() |
![]() ![]() ![]() ![]() |
![]() ![]() ![]() ![]() |
![]() ![]() ![]() ![]() |
![]() ![]() ![]() ![]() |
![]() ![]() ![]() ![]() |
![]() ![]() ![]() ![]() |
![]() ![]() ![]() ![]() |
![]() ![]() ![]() ![]() |
![]() ![]() ![]() ![]() |
![]() ![]() ![]() ![]() |
![]() ![]() ![]() ![]() |
![]() ![]() ![]() ![]() |
![]() ![]() ![]() ![]() |
![]() ![]() ![]() ![]() |
![]() ![]() ![]() ![]() |
![]() ![]() ![]() ![]() |
![]() ![]() ![]() ![]() |
![]() ![]() ![]() ![]() |
![]() ![]() ![]() ![]() |
![]() ![]() ![]() ![]() |
![]() ![]() ![]() ![]() |
![]() ![]() ![]() ![]() |
![]() ![]() ![]() ![]() |
![]() ![]() ![]() ![]() |
![]() ![]() ![]() ![]() |
![]() ![]() ![]() ![]() |
![]() ![]() ![]() ![]() |
![]() ![]() ![]() ![]() |
![]() ![]() ![]() ![]() |
![]() ![]() ![]() ![]() |
![]() ![]() ![]() ![]() |
![]() ![]() ![]() ![]() |
![]() ![]() ![]() ![]() |
![]() |
![]() ![]() ![]() ![]() |
![]() ![]() ![]() ![]() |
![]() |
![]() |
![]() ![]() ![]() ![]() |
![]() ![]() ![]() ![]() |
![]() ![]() ![]() ![]() |
![]() ![]() ![]() ![]() |
![]() |
![]() |
![]() ![]() ![]() ![]() |
![]() |
![]() ![]() ![]() ![]() |
![]() |
![]() |
![]() |
![]() ![]() ![]() ![]() |
![]() |
![]() |
![]() ![]() ![]() ![]() |
![]() ![]() ![]() ![]() |
![]() ![]() ![]() ![]() |
![]() |
![]() |
![]() |
![]() ![]() ![]() ![]() |
![]() ![]() ![]() ![]() |
![]() |
![]() ![]() ![]() ![]() |
![]() |
![]() ![]() ![]() ![]() |
![]() |
![]() ![]() ![]() ![]() |
![]() ![]() ![]() ![]() |
![]() |
![]() |
![]() |
![]() |
![]() ![]() ![]() ![]() |
![]() ![]() ![]() ![]() |
![]() ![]() ![]() ![]() |
![]() ![]() ![]() ![]() |
![]() |
![]() |
![]() |
![]() ![]() ![]() ![]() |
![]() |
![]() ![]() ![]() ![]() |
![]() ![]() ![]() ![]() |
![]() |
![]() ![]() ![]() ![]() |
![]() ![]() ![]() ![]() |
![]() ![]() ![]() ![]() |
![]() ![]() ![]() ![]() |
![]() ![]() ![]() ![]() |
![]() ![]() ![]() ![]() |
![]() ![]() ![]() ![]() |
Дополнительная информация
Рис.9.cdw

Первая часть-1техмаш нужное.doc
1 Служебное назначение детали
Рассматриваемая деталь корпус входит в состав тестокруглительной машины которая предназначена для улучшения структуры заделки поверхностных пор и предания тестовым заготовкам поступающим из тесторазделительной машины круглой формы. Тестокруглительная машина применяется на предприятиях хлебопекарной промышленности при выпечке хлеба и хлебобулочных изделий.
Корпус является одной из основных частей тестокруглительной машины и выполняет две основные функции:
Как основание на нем крепиться электродвигатель привода который передает движение на червячную пару.
Как корпус редуктора в котором установлена червячная пара передающая движение на рабочий орган машины.
Анализируя действующие нагрузки на корпус приходим к выводу что основными нагрузками являются два фактора:
Вибрация электродвигателя.
Масса рабочих органов (чаша спираль) которые давят на корпус а также неравномерность вращения чаши со ступицей.
Принимая во внимание что эти нагрузки не особенно велики и конструкция корпуса достаточно жесткая чтобы их воспринимать (т.е. имеющиеся ребра жесткости толщина стенок достаточна) можно сделать вывод что условия работы корпуса легкие.
Рабочий чертеж обрабатываемой детали содержит все необходимые сведения дающие полное представление о данной детали т.е. все размеры и сечения совершенно четко и однозначно объясняют ее конфигурацию и возможные способы получения заготовки. На чертеже указаны все размеры с необходимыми допусками шероховатостью обрабатываемых поверхностей допускаемыми отклонениями от правильных геометрических форм а также с взаимным расположением поверхностей.
Основными рабочими поверхностями вала являются:
Поверхность основания – служит для установки корпуса (а следовательно и всей машины) на фундамент.
Поверхность 50Н7 – служит для установки оси на которой крепится ступица с червячным колесом а также спираль.
Поверхность 110 – служит для упорного подшипника закрепленного на оси.
Две поверхности 72Н7 – служат для установки подшипников качения вала червяка.
Верхняя поверхность и отверстия на ней – служат для установки и закрепления качающейся подмоторной плиты для электродвигателя.
На чертеже имеются все необходимые технические требования. В том числе:
определена точность отливки (10-6-14-10 по ГОСТ 26645-85);
определены неуказанные литейные радиусы (5 8 мм);
определено покрытие внутренних и наружных необработанных поверхностей;
определены допускаемые размеры и взаимное расположение раковин на обработанных посадочных поверхностях;
определены размеры допускаемых раковин в резьбовых отверстиях;
определена необходимость зачистить до блеска и законсервировать смазкой ПВК ГОСТ 19537-74 поверхность Г;
определена необходимость и место маркировки обозначения чертежа на детали.
Деталь изготовлена из серого чугуна СЧ20 ГОСТ 1412-85.
В состав чугуна входят следующие химические элементы:
сера – не более 0.15%;
фосфор – не более 0.2%.
Механические свойства чугуна:
Плотность – 7100 кгм3.
Линейная усадка – 1.2%.
Модуль упругости при растяжении - 85000110000 МПа.
Удельная теплоемкость
при температуре от 20о до 200оС – 480 Дж.
Коэффициент линейного расширения
при температуре от 20о до 200оС – 9.5х10-6 1оС.
Теплопроводность при 20оС – 54 Вт.
Рассмотрим технологический маршрут изготовления детали таблица 1.1.
Таблица 2.1 - Маршрут изготовления детали
Наименование и содержание операции
Оборудование и приспособления
Режущий и измерительный инструмент
Продольно-фрезерная.
Фрезеровать верхнюю плоскость предварительно в размер 24.5
Продольно-фрезерный 4-х шпиндельный 6642.
Болты 7002-2634 ГОСТ13152-67.
Прихваты 7011-0072 ГОСТ12937-67.
Оправка В-11390-000000.
Фреза 2214-0001 60о ВК8 ГОСТ24359-80 100.
Штангенциркуль ШЦ-I-125-0.1 ГОСТ 166-80.
Фрезеровать основание предварительно с припуском 0.5 на шлифовку придерживаясь размера 158.5 от центра отверстия.
Фреза 2214-0001 60о ВК8 ГОСТ24359-80 100.
Штангенрейсмасс ШР 250-0.05 ГОСТ 164-80.
Шлифовать верх детали в размер 24 мм.
Шлифовать основание до неплоскостности не более 0.03 мм выдержав размер 288±0.2.
Плоскошлифовальный станок 3Б724.
Плита магнитная ГОСТ 17519-72.
Шлифовальный круг ПП500х305х100 52С40ПСМ26К2 35 мс 2 кл.ГОСТ2424-75.
Штангенрейсмасс ШР 40-400-0.05
Линейка ШЛ-1-630 ГОСТ8026-75.
Щуп №2 кл2 ГОСТ 882-75.
Проверить шероховатость основания Ra3.2 Ra6.3.
Проверить неплоскостность основания не более 0.03 мм.
Проверить на соответствие выполнение размеров 26±0.5.
Образцы шероховатости ГОСТ 9378-73.
Линейка ШЛ-1-630ГОСТ8026-75.
Фрезеровать торец в размер 331±1.1 придерживаясь размера 191 мм от центра детали.
Болты 7002-2636 ГОСТ13152-67.
Упоры 7030-1091 ГОСТ 1555-67.
Фреза 2214-0011 60о-ВК8
Штангенциркуль ШЦ-III-400-0.1 ГОСТ 166-80.
Фрезеровать платики в размер 50±0.5.
Фрезеровать платики в размер 35±0.5.
Фреза 2214-0005 60о-ВК8
Фрезеровать бобышку 110 выдержав размер 31±0.2 [158-(42+85)].
Прихваты 7011-0070 ГОСТ12937-67.
Оправка В-112560-00000.
Фреза Р-20350-000000 72.
Угломер М-4012-0000000.
Горизонтально-расточная.
Зенкеровать отверстие 49.5 в бобышке 110.
Расточить отверстие до 49.7.
Расточить отверстие до 49.93.
Развернуть отверстие до 50Н7.
Горизонтально-расточной BFT-903.
Угольник 7080-0039 ГОСТ 12945-67.
Оправка В-4055-00000.
Сверло-зенкер Р-4008-0000000.
Резец 2142-0144 ГОСТ 9795-73.
Развертка 2363-0702 Н7 ГОСТ 1672-80.
Пробка 8133-0962 Н7 ГОСТ 14810-69.
Фрезеровать боковую плоскость размера 280придерживаясь центра
Оправка В-11391-000000.
Фреза 2214-0005 60о-ВК8 ГОСТ 24359-80.
детали за два прохода по ширине.
Фрезеровать вторую боковую плоскость выдержав размер 280-0.5 за два прохода по ширине до непараллельности не более 0.1 мм.
Зенкеровать отверстие 39.5.
Зенкеровать отверстие 61.5.
Зенкеровать отверстие 71.5.
Расточить отверстие до 72Н7.
Расточить фаску 2х45о.
Расточить отверстие до 72Н7 выдержав
размеры 158±0.2; 120±0.06 и обеспечив соосность 0.02 мм.
Сверло-зенкер Р-19144-000000.
Сверло-зенкер Р-60615-000000.
Сверло-зенкер Р-74479-000000.
Резец расточной Р-60189-00000.
Штангенциркуль ШЦ-II-250-0.1 ГОСТ 166-80
Пробка 8136-0110Н7 ГОСТ 14815-69.
Индикатор ИЧ02 кл0 ГОСТ 577-68.
Сверлить 8 отверстий 6.8 и два отверстия 5.
Зенковать 10 фасок 1.6х45о.
Нарезать резьбу М8-7Н в
Сверло 2301-0189 ГОСТ 10903-77.
Сверло 2301-4001 ГОСТ 10903-77.
Зенковка 2353-0011 МН 725-60
восьми отверстиях и резьбу М6-7Н в двух отверстиях.
Метчик 2620-1157 ГОСТ3266-81
Метчик 2620-1223 ГОСТ3266-81
Пробка 8221-3030-7Н ГОСТ17758-72.
Пробка 8221-3036-7Н ГОСТ17758-72.
Сверлить два отверстия 6.3.
Зенковать две фаски 1.6х45о.
Нарезать резьбу М8-7Н в двух отверстиях.
Сверлить четыре отверстий 6.8.
Зенковать четыре фаски 1.6х45о.
Нарезать резьбу М8-7Н в четырех отверстиях.
Вертикально-фрезерная.
Фрезеровать по 260-1.15 с одновременной фрезеровкой торца в размер 8±0.3
Фрезеровать отверстие до 210 предварительно.
Фрезеровать отверстие окончательно до 216+1.15.
Вертикально-фрезерный
Прихваты 7011-0065 ГОСТ 12937-67
Болты 7002-2564 ГОСТ 13152-67
Фреза 2223-0555 ВК8 ГОСТ 20538-75.
Фреза Р-4090-0000000
Фреза Р-4089-0000000
Фреза 2234-0205 ВК8 ГОСТ 16463-80.
Фреза Р-11398-0000000
Сверло 55 2301-0173 Гост10903-77
Штангенциркуль ШЦ-III-400-0.1 ГОСТ 166-80
Уступомер М-4013-0000000
Шаблон М-4058-0000000
Фрезеровать сальниковую канавку предварительно В=8 мм до 248+1.15.
Фрезеровать сальниковую канавку окончательно В=10 мм до 248+1.15 выдержав размеры 6±0.2; 10Н14; 15о±1.
Фрезеровать канавку В=6 мм выдержав 260-1.15; 272+1.35; 2±0.2.
Фрезеровать торец бобышки 110 предварительно.
Фрезеровать торец бобышки 110 окончательно выдержав перпендикулярность оси отверстия не более 0.02100 в размер 42±0.04.
Снять фаску 2.5х45о в отверстии 50Н7.
Обработка ведется по программе.
Меритель на перпендикулярность
Приспособление (на размер 42±0.04)
Радиально-сверлильная.
Сверлить три отверстия 4Н14 по канавке выдерживая координаты R=132.5±0.5; 30о±5о.
Радиально-сверлильный
Сверло 2300-7515 ГОСТ10902-77
Сверлить 12 отверстий 6.8 под резьбу М8-7Н.
Сверлить два отверстия 6.8 (под последующую обработку до 20Н14).
Сверлить отверстие 5 под резьбуМ6-7Н.
Сверлить два отверстия 10.2 под резьбу М12-7Н.
Сверло 2301-0189 ГОСТ10903-77
Сверло 2301-3001 ГОСТ10903-77
Сверло 2301-0400 ГОСТ10903-77
Пробка М-11451-000000
Пробка М-11450-000000
Пробка М-11454-000000
Зенковать фаску 1.6х45о в 13-и отверстиях под резьбу.
Рассверлить два отверстия до 20Н14.
Нарезать резьбу М8-7Н в 12-и отверстиях.
Нарезать резьбу М6-7Н в одном отверстии.
Нарезать резьбу М12-7Н в двух отверстиях.
Сверло 2301-0069 ГОСТ10903-77
Метчик 2640-0081-Н4 ГОСТ1604-71
Метчик 2640-0053-Н4 ГОСТ1604-71
Метчик 2640-0153-Н4 ГОСТ1604-71
Пробка 8221-3036-7Н ГОСТ17758-72
Пробка 8221-3030-7Н ГОСТ17758-72
Пробка 8221-3053-7Н ГОСТ17758-72
Зенковать фаску 2.5+0.5х45о в отверстии 50Н7 с другой стороны.
Зенковка Р-60529-000000
Маркировать деталь Т1-ХТН00.047.
Маркировочная плита.
Молоток 7850-0052 ГОСТ 2310-77
Произвести внешний осмотр визуально.
Проверить шероховатость поверхностей.
Проверить все размеры.
Проверить соосность отверстия 72Н7.
Проверить неперпендикулярность оси отверстия 50Н7 торцу бобышки 110 не более 0.02100.
Меритель согласно технологическому процессу.
Сравнивая маршрутный технологический процесс с типовым технологическим процессом на однотипные детали мы не находим существенных различий. Поэтому изменение порядка технологических операций можно считать нецелесообразным. Но рассматривая уровень прогрессивности методов обработки мы видим что они не достаточно производительны.
Анализируя технологический процесс можно рекомендовать после обработки наружных базовых поверхностей вместо остальных операций ввести горизонтальную сверлильно-фрезерно-расточную операцию на обрабатывающем центре с ЧПУ и вертикальную сверлильно-фрезерно-расточную операцию на обрабатывающем центре с ЧПУ что позволит значительно сократить время на обработку (за счет сокращения вспомогательного и подготовительно-заключительного времени) и увеличить точность обработки.
Проводя анализ уровня механизации и автоматизации технологического процесса можно сделать вывод что в нем практически не используется приспособления.
Исходя из этого рекомендуется разработать несколько приспособлений. В частности можно разработать приспособление для крепления детали горизонтальную фрезерно-сверлильно-расточную операцию с пневматическим зажимом также можно разработать пневматическое приспособление для зажима детали на вертикальную фрезерно-сверлильно-расточную операцию. Оба эти приспособления позволят сократить вспомогательное и подготовительно-заключительное время.
Оценивая применяемые методы и средства измерений в существующем технологическом процессе можно обнаружить что линейные размеры в большинстве операциях как правило контролируются штангенциркулем но в случае контроля более точных и ответственных размеров (например при растачивании отверстия 50Н7) используют пробки. При контроле резьбовых отверстий применяются пробки. Для контроля соосности отверстий 72Н7 применяется валик. Плоскостность контролируется с помощью набора щупов и линейки. Для контроля перпендикулярности поверхностей применяются специальные приспособления. Сальниковая канавка контролируется с помощью специального шаблона. Проанализировав применяемые методы и средства измерений в существующем технологическом процессе можно прийти к выводу что они обеспечивают необходимую точность контроля.
Третья часть.doc
1 Расчет зажимного приспособления на сверлильно-фрезерно-расточную операцию
Для установки и закрепления детали на сверлильно-фрезерно-расточной операции необходимо разработать специальное приспособление с пневматическими зажимами.
Конструкция приспособления.
Приспособление состоит из следующих основных частей и деталей: основание которое крепится непосредственно на стол станка; на которое устанавливается обрабатываемая деталь. На основании закреплены упоры которые служат для выставки детали а также трех пневматических прихватов которые служат для зажима детали.
При подаче воздуха в нижнею часть пневмоцилиндра там создается давление а так как поршень не имеет возможности передвижения (он соединен со штоком а шток неподвижен) то давление передается на нижнею крышку. Она в свою очередь под действием давления воздуха вместе с цилиндром перемещается вниз относительно штока в результате чего движение передается прихвату. Он опускается вниз и происходит зажим детали.
При переключении подачи воздуха в другую полость пневмоцилиндра крышка вместе с цилиндром поднимается вверх относительно штока перемещая прихват вверх. Происходит открепление детали.
Расчет приспособления.
Исходные данные для расчета:
Сила резания – =4500 Н.
Давление сжатого воздуха =039 Мпа.
Для обеспечения надежности зажима детали определяется коэффициент запаса :
=15 – постоянный коэффициент запаса.
=12 – коэффициент учитывающий состояние поверхности детали.
=14 – коэффициент учитывающий увеличение сил резания при затуплении инструмента.
=12 – коэффициент учитывающий увеличение сил резания при обработке прерывистых поверхностей.
=13 – коэффициент учитывающий постоянство сил зажима развиваемый приводом приспособления.
=10 – коэффициент учитывающий удобное расположение органов управления.
=15 – коэффициент учитывающий наличие моментов.
Необходимая сила зажима для обрабатываемой детали:
и – коэффициенты трения.
Определим расчетный диаметр пневматического цилиндра:
=0.85 – К.П.Д. привода.
По ряду стандартных чисел принимаем диаметр пневмоцилиндра =100 мм.
Определим действительную силу зажима:
Время срабатывания пневмопривода:
=40 мм – длина хода поршня.
=6 мм – диаметр воздухопровода.
=180 мс – скорость перемещения воздуха.
2 Расчет двухступенчатого сверла
Расчитать и сконструировать двухступенчатое сверло из быстрорежущей стали с цилиндрическим хвостовиком для обработки отверстия под метрическую резьбу М12-6Н.
Определим диаметр сверла.
Диаметр первой ступени для сверления отверстия под резьбу М10 в заготовке из алюминиевого сплава равен мм. Диаметр второй ступени для снятия фаски в отверстии равен мм.
Осевая составляющая силы резания
где -диаметр сверла мм мм;
-поправочный коэффициент;
Значения коэффициентов принимаем из таблицы 32 [2].
Момент сил сопротивления резанию
Значения коэффициентов принимаем из таблицы 31 [7].
Определим конус Морзе хвостовика сверла для этого найдем средний диаметр хвостовика
где - коэффициент трения сталь по стали =0096;
- половина угла конуса =1°26’16’’;
- отклонение угла конуса =5’;
Выбираем конус Морзе №2 с длинной хвостовика 80 мм.
где -длина рабочей части мм;
где -длина первой ступени мм =55мм;
-длина второй части мм =100мм;
-длина хвостовика мм =80мм.
Определяем геометрические и конструктивные параметры рабочей части сверла.
Угол наклона винтовой канавки ;
Угол между режущими кромками ;
Угол наклона поперечной кромки ;
Шаг винтовой канавки первой ступени
Толщина сердцевины сверла первой ступени
Утолщение сердцевины по направлению к хвостовику 15мм на 100мм длины.Обратная конусность сверла на 100мм длины рабочей части 005мм.
Высота затылка по стенке
Ширина пера первой ступени
Геометрические параметры канавки первой ступени:
Больший радиус профиля
Принимаем диаметр фрезы .
Меньший радиус профиля
Шаг винтовой канавки второй ступени
Толщина сердцевины сверла второй ступени
Ширина пера второй ступени
Геометрические параметры канавки второй ступени:
3 Расчет калибра пробки
Расчитаем калибр пробку для контроля отверстия мм. Его разработка вызвана необходимостью контроля допуска изготовления отверстия и отсутствием в ГОСТе калибров конкретного типоразмера.
Определим предельные размеры отверстия
где -максимальный диаметр отверстия мм;
-номинальный диаметр отверстия мм =102 мм;
-верхнее предельное отклонение мм =036 мм;
-минимальный диаметр отверстия мм;
-нижнее предельное отклонение мм =0мм.
Расчет исполнительных диаметров калибра:
Расчет проходного калибра
где -отклонение середины поля допуска на изготовление проходного калибра для отверстия относительно наименьшего предельного размера мм =70мкм=0007мм таблица 2 [21];
-допуск на изготовление калибра мм =25мкм=00025мм таблица 2 [21].
Расчет проходного изношенного калибра
где -допустимый выход размера изношенного проходного калибра для отверстия за границу поля допуска изделия мм =5мкм=0005мм;
-величина для компенсации погрешности контроля калибрами отверстий мм =0мм таблица 2 [21].
Расчет непроходного калибра
Схема полей допусков исполнительных размеров калибра представлена на рисунке 3.1.
Рисунок 3.1-Схема полей допусков исполнительных размеров калибра.
Вторая часть-техмаш д2222.doc
Деталь «Корпус» изготавливается из серого чугуна марки СЧ20 методом литья поэтому получение наружного контура детали а также внутренних поверхностей не вызывает значительных трудностей. Следует отметить что толщина стенок детали достаточна для их получения литьем. Далее следует отметить наличие ребер жесткости снизу детали которые увеличивают жесткость и прочность детали в данном месте как в процессе работы так и при механической обработке. Отсюда следует вывод что наличие ребер жесткости является технологичным. Также следует отметить отсутствие больших температурных узлов (т.е. мест где имеется большое скопление металла) что говорит о том что при заливке металла все места прольются хорошо и при остывании металла не будет возникать температурных перепадов которые приводят к возникновению трещин пор и т.д. А это говорит о том что деталь получится однородной с точки зрения механических свойств материала что в свою очередь увеличивает качество детали следовательно отсутствие данных узлов технологично.
Рассматривая и анализируя конструкцию детали а также требования к шероховатости и точности обрабатываемых поверхностей можно сделать вывод что деталь с точки зрения механической обработки достаточно сложна так как требует обработки практически со всех сторон. Однако следует отметить что все обрабатываемые поверхности открыты и доступны для механической обработки что в свою очередь позволяет применять высокопроизводительные методы обработки что также говорит о технологичности детали.
Приведем качественную оценку технологичности детали по коэффициенту технологичности Ктч; коэффициенту использования заготовки Кз; коэффициенту использования материала Км и сопоставим с нормами ГОСТ 14202-75.
где – средний коэффициент точности определяется по формуле
где – квалитет точности обработки;
– число размеров составляющих квалитет.
При деталь считается технологичной.
где – норма расхода материала;
где – масса отходов кг от массы заготовки.
Таким образом деталь по всем показателям ГОСТ 14262-75 технологична.
С точки зрения технологичности (как то точность обработки время обработки) следует отметить что данную деталь следует обрабатовать с применением станков с ЧПУ (типа обрабатывающего центра) а также для обработки отверстий 50H7 72Н7 и канавки для уплотнения следует разработать специальный режущий инструмент. Так для 72Н7 следует ввести длинный комбинированный инструмент сверло-зенкер что позволит обработать два отверстия 72Н7 за один проход что в конечном итоге сократит время обработки а также позволит получить необходимые размеры и отклонения. Для 50H7 следует применить тот же самый тип инструмента.
Для канавки наиболее рациональным режущим инструментом будет фреза типа дисковой.
3 Определение типа производства
Тип производства и соответствующие ему формы организации работы определяет характер технологического процесса и его построение. Поэтому перед проектированием технологического процесса механической обработки детали он должен быть известен.
Согласно ГОСТ 14004 - 83 основной характеристикой типа производства является коэффициент закрепления операций равный отношению всех различных технологических операций выполняемых или подлежащих выполнению в течение месяца к числу рабочих мест (Кзо) [3].
Коэффициент Кзо в соответствии с ГОСТ14004-83 принимают:
-для массового производства Кзо=1
-для крупносерийного производства 1 Кзо 10
-для среднесерийного производства 10 Кзо 20
-для мелкосерийного производства 20 Кзо 40
Тип производства определяем по коэффициенту закрепления операций :
где – сумма операций выполняемых на оборудовании в течении расчетного периода определяется по формуле
где – фактический коэффициент загрузки определяется по формуле
где – расчетное количество оборудования определяется по формуле
где – программа запускаопределяется по формуле
где – процент учитывающий брак в изготовление принимаем =2%;
– программа выпуска =500 шт.;
– штучно-калькуляционное время обработки мин. определяется по формуле;
где – основное время обработки мин. определяется по приближенным формулам:
Основное время при фрезеровании определяется по формуле
где – длина обрабатываемой поверхности мм;
– количество одинаковых поверхностей.
Основное время при сверлении определяется по формуле
где – обрабатываемый диаметр мм;
– длина обрабатываемой поверхности мм;
Основное время при нарезании резьбы
Основное время при растачивании
– коэффициент серийности для фрезерования сверления и нарезания резьбы =184; для растачивания =325. Приложение 1 [3].
Расчеты основного времени заносим в таблицу 2.2.
Таблица 2.2-Данные для расчета основного времени
Черновое фрезерование основания
Чистовое фрезерование основания
Черновое фрезерование верхней плоскости
Черновое фрезерование левого торца детали
Черновое фрезерование боковой поверхности
Черновое фрезерование бобышки 110
Черновое фрезерование бобышки с другой стороны
Чистовое фрезерование бобышки 110
Черновое фрезерование платиков
Фрезеровать отверстие 216
Фрезеровать сальниковую канавку
Сверлить 10 отверстий 6.8
Сверлить отверстие 5
Сверлить два отверстия 6.8
Сверлить два отверстия 10.2
Сверлить два отверстия 20
Сверлить два отверстия 4
Нарезать резьбу М8-7Н
Нарезать резьбу М12-7Н
Нарезать резьбу М6-7Н
Сверлить 8 отверстий 6.8
Сверлить два отверстия 5
Сверлить 4 отверстия 6.8
Нарезать резьбу М8-7Н в четырех отверстиях
Нарезать резьбу М8-7Н в двух отверстиях
Нарезать резьбу М6-7Н в 20 отверстиях
Черновое растачивание двух отверстий 72
Чистовое растачивание двух отверстий 72
Развернуть два отверстия 72
Черновое растачивание двух отверстий 50
Чистовое растачивание двух отверстий 50
Развертывание двух отверстий 50
Итого по операциям имеем:
– действительный годовой фонд времени при двухсменной работе оборудования =4015 ч. Таблица 5 [3]
– нормативный коэффициент загрузки =085 [3];
– принятое количество оборудования.
– сумма принятого оборудования (рабочих мест).
Определим расчетное количество оборудования на фрезерные операции
Определим расчетное количество оборудования на сверлильные операции
Определим расчетное количество оборудования на расточные операции
Определим фактический коэффициент загрузки по операциям:
Определим количество операций выполняемых на оборудовании в течении расчетного периода по операциям:
Определим коэффициент закрепления операций:
Так как полученный результат находится в интервале то производство среднесерийное.
Среднесерийное производство характеризуется ограниченной номенклатурой изделий изготавливаемых или ремонтируемых периодически повторяющимися партиями.
Определим количество деталей в партии для одновременного запуска по формуле
где – число дней на которое необходимо иметь запас деталей по рекомендациям [3] принимаем =10;
– число рабочих дней в году =253;
Используется универсальное и специализированное и частично специальное оборудование. Широко используются станки с ЧПУ обрабатывающие центры и находят применение гибкие автоматизированные системы станков с ЧПУ. Технологическая оснастка в основном универсальная однако во многих случаях создается высокопроизводительная специальная оснастка; при этом целесообразность ее создания должна быть предварительно обоснована технико-экономическим расчетом. Большое применение имеет универсально-сборная переналаживаемая технологическая оснастка позволяющая существенно повысить коэффициент оснащенности производства. В качестве исходных заготовок используется горячий и холодный прокат литье в землю и под давлением точное литье поковки и точные штамповки целесообразность которых также обосновывается технико-экономическими расчетами.
4 Обоснование выбора исходной заготовки
В качестве заготовки для изготовления корпуса принимается отливка выполненная из серого чугуна марки СЧ18 ГОСТ1412-85. Целесообразность применения этого вида заготовок однозначна вследствии сложности формы и конфигурации детали: значительных габаритов наличие большого количества поверхностей отверстий и полостей пересекающихся в различных плоскостях под разными углами.
При существующем в машиностроении большом выборе заготовок для данной детали другой альтернативы нет т. к. Получение других видов заготовок для этой детали очень затруднена.
В качестве метода получения отливки применяется литье в земляные формы с машинной формовкой в крупных опоках как наиболее простой и универсальный. Это заключение сделано в виду следующих факторов:
Небольшая программа выпуска деталей.
Отсутствие на производстве специального литейного производства.
Дешевизна заготовки.
В соответствии с ГОСТ 1855-55 применяется отливка III класса точности. Выбор данной отливки подтвердим расчетом.
Сравним методы получения отливок I и III класса точности.
Стоимость заготовки определяется по формуле:
где - базовая стоимость 1 тонны заготовок руб;
=20000 руб - для отливок III класса точности;
=22000 руб - для отливок I класса точности;
- масса заготовки кг;
=890 кг - для отливок III класса точности;
=845 кг - для отливок I класса точности;
- коэффициент зависящий от класса точности отливки;
=10 - для отливок III класса точности;
=11 - для отливок I класса точности;
- коэффициент зависящий от группы сложности отливки
=145 - для отливки I и III класса точности;
- коэффициент зависящий от массы заготовки таблица 11 [3];
=074 - для отливки I и III класса точности;
- коэффициент зависящий от марки материала заготовки
=154 - для отливки I и III класса точности;
- коэффициент зависящий от объема производства заготовок
=144 - для отливки I и III класса точности;
- масса готовой детали кг =820 кг;
- стоимость 1 тонны отходов руб =12000 руб.
Стоимость заготовки I класса точности:
Стоимость заготовки III класса точности
Из проделанных расчетов видно что заготовка из отливки III класса точности дешевле чем заготовка из отливки I класса точности. Поэтому используем отливку III класса точности.
Для данного типа отливок принимаем класс размерной точности (по ГОСТ 26645-85) – 10. Степень коробления – 6. Степень точности поверхностей отливок – 14. Точность массы отливки – 10.
Припуски на все поверхности обрабатываемые фрезеровкой принимаем равными 5 мм. Припуски под расточку отверстий – 10 мм.
5 Разработка маршрутного и операционного технологического процесса обработки детали с обоснованием последовательности операций и переходов
На основании рассчитанного типа производства а также учитывая возможность этапов механической обработки поверхностей на одной операции т.е. применяя станки типа «Обрабатывающий центр» можно составить следующий маршрут механической обработки детали таблица 2.3.
Таблица 2.3-Маршрут обработки детали
Краткое содержание операции.
Зачистить полости от формовочной земли и наплывов металла
Искусственное старение
Контролировать качество отливки
Одновременное фрезерование основания и одной боковой поверхности.
Контролировать полученные размеры
Одновременное фрезерование двух боковых поверхностей и верха детали.
Фрезерование боковой поверхности
Шлифование поверхности основания.
Вертикально-фрезерная
Фрезерование бобышки снизу.
Зачистить заусенцы притупить острые кромки
Вертикально-сверлильно-фрезерно-расточная с ЧПУ
Обработка верхних поверхностей детали:
Фрезерование платиков.
Обработка отверстия 216
Обработка отверстия 50Н7
Обработка отверстий М8-7Н
Фрезерование уступа размером 8.
Горизонтально-сверлильно-фрезерно-расточная с ЧПУ
Обработка боковых поверхностей детали:
Обработка отверстия 72Н7
Сверление отверстий под резьбу
Нарезание резьбы М6-Н7 М8-7Н
5.1 Обоснование выбора оборудования
Согласно технологическому процессу механической обработки выбираем следующее оборудование:
На продольно-фрезерной операции применим продольно-фрезерный станок модели 6Г610.
Краткая техническая характеристика:
Размеры рабочей поверхности стола – 1000х3150 мм
Число шпиндельных бабок:
Число скоростей шпинделя 20
Частота вращения шпинделя 161250 мин-1
Мощность главного привода 18.5х4 кВт.
Габариты 8700х5000х4050 мм
На вертикально сверлильно-фрезерно-расточную операцию применим сверлильно-фрезерно-расточной станок модели 21105Н7Ф4.
Размеры рабочей поверхности стола 500х800 мм
Вылет шпинделя 560 мм
Максимальный размер от торца шпинделя
до рабочей поверхности стола 950 мм
Частота вращения шпинделя252500 мин-1
Скорость быстрого перемещения10000 мммин
Вместительность инструментального магазина20
Общая мощность22.98 кВт.
Габариты4225х3695х3650 мм
На горизонтально сверлильно-фрезерно-расточную операцию применим сверлильно-фрезерно-расточной станок модели 6906ВМР2.
Размеры рабочей поверхности стола630х800 мм
Минимальное расстояние от
плоскости стола до оси шпинделя95 мм
Максимальное расстояние от
плоскости стола до оси шпинделя725 мм
Минимальное расстояние от торца шпинделя
до середины стола165 мм
Максимальное расстояние от торца шпинделя
до середины стола795 мм
Частота вращения шпинделя31.51600 мин-1
Вместительность инструментального магазина30
Мощность привода шпинделя8.0 кВт.
На плоскошлифовальную операцию выбираем плоскошлифовальный станок модели 3Б724.
Размеры рабочей поверхности стола400х2000 мм
Максимальная высота шлифуемой детали500 мм
Диаметр шлифовального круга500 мм
Число оборотов шлифовального круга1460 мин-1
Общая мощность80 кВт.
Габариты5660х2580 мм
На вертикально-фрезерную операцию выбираем вертикально-фрезерный станок модели 6Н12.
Размеры рабочей поверхности стола400х1600 мм
Число скоростей шпинделя18
Общая мощность11 КВт.
Габариты2560х2260 мм
5.2 Расчет припусков и межоперационных размеров
В машиностроении нашло применение несколько методик назначения припусков под механическую обработку.
В данном дипломном проекте использованы две основные методики получившие наиболее широкое применение: расчетно-аналитический и табличный метод.
Расчетно-аналитический метод более точен т. к. Он является комплексным и учитывает многие факторы влияющие на величину припуска: точность формы и величину пространственных отклонений погрешность установки детали в приспособлении. Но этот метод является трудоемким в осуществлении.
Табличный метод более приближенный и соответственно менее точный но тем не менее при достаточной достоверности величины припуска он значительно менее трудоемкий.
В данном дипломном проекте припуски на те поверхности к которым предъявлены более жесткие требования и которые требуют более тщательной проработки определялись расчетно-аналитическим методом. На поверхности более простые и нетребующие многооперационной обработки величина припуска назначалась табличным методом.
Расчет припусков и межоперационных размеров на обработку отверстия 72Н7. Все расчеты заносим в таблицу 2.4.
Маршрут обработки поверхности:
)Заготовка – литье в землю +=800 мкм таблица 6 [1];
)Рассверливание =63 мкм; =80 мкм таблица 27 [1];
)Зенкерование =50 мкм; =50 мкм таблица 27 [1];
)Растачивание тонкое =20 мкм; =20 мкм таблица 27 [1].
Минимальный расчетный припуск на данном переходе определяется по формуле
где – высота неровностей профиля на предшествующем переходе мкм;
– глубина дефектного поверхностного слоя на предшествующем переходе мкм;
– погрешность установки заготовки на выполняемом переходе мкм;
– сумарные отклонения расположения поверхности на предшествующем переходе мкм определяется по формуле:
где – отклонение плоской поверхности отливки от плоскостности мкм =0 т. к. базовые плоскости обработаны;
– смещение стержня в горизонтальной или вертикальной плоскостях мкм
где – допуск на размер в горизонтальной плоскости мкм =1200 мкм;
– допуск на размер в вертикальной плоскости мкм =1200 мкм;
Остаточные отклонения расположения заготовки после обработки мкм;
где – коэффициент уточнения для рассверливания =006 таблица 29 [1];
для зенкерования =004 таблица 29 [1];
Погрешность установки для рассверливания определяется по формуле
где – погрешность базирования мкм ;
где – допуск на вертикальный размер до отверстия 72 мкм;
При зенкеровании мкм;
Погрешность установки при тонком растачивании т. к. заготовка не переустанавливалась.
Минимальный припуск под рассверливание
При тонком растачивании:
Определяем расчетные размеры
Определяем предельные размеры
Для тонкого растачивания:
Определяем предельные значения припусков
Определяем общие припуски:
Определяем общий номинальный припуск:
Определяем номинальный размер заготовки:
Полученные значения припусков на обработку и предельных размеров по технологическим переходам заносим в таблицу 2.4.
Таблица 2.4 - Значения припусков на обработку и предельные размеры по технологическим переходам
Элементарная поверхность детали и технологический маршрут ее обработки
Расчетный размер dр мм.
Предельные размеры мм.
Предельные значения припусков мкм.
Растачивание тонкое IT7
Схему графического расположения припусков и допусков смотри на рисунке 2.1.
Рисунок 2.1-Схема графического расположения припусков и допусков на обработку
Припуски на механическую обработку назначаем в соответствии с ГОСТ26645-85 и сводим в таблицу 2.5.
Таблица 2.5 - Припуски на механическую обработку
Обрабатываемая поверхность
5.3 Обоснование выбора режущего инструмента
Чугуны имеют хорошую обрабатываемость допускают обработку на высоких скоростях резания при этом возникающие силы резания не велики и поэтому при обработке скорость износа инструмента низкая а также в процессе резания образуется легко удаляемая стружка. Износ инструмента определяется в основном адгезионными процессами и следовательно для обработки на более высоких скоростях и уменьшения износа следует применять твердосплавные инструменты.
Анализируя применение различных материалов используемых для изготовления режущей части инструментов и сравнивая их свойства можно прийти к выводу что применение режущих частей изготовленных из твердых сплавов позволяет увеличить скорость резания в 3-4 раза по сравнению с
режущими частями изготовленными из быстрорежущих сталей. Пользуясь рекомендациями для обработки чугунов следует применять твердые сплавы вольфрамовой группы типа ВК. Рассматривая структуру данных сплавов можно прийти к выводу что более высокое содержание кобальта – увеличивает предел прочности на изгиб снижает износостойкость инструмента; более низкое содержание кобальта напротив снижает предел прочности на изгиб но увеличивает износостойкость инструмента.
Отсюда можно сделать вывод что для черновой обработки надо применять крупнозернистые сплавы марки ВК8 где 8 – процент содержания кобальта. А для чистовой обработки надо применять мелкозернистые сплавы марки ВК6.
Рассмотрим физико-механические свойства этих твердых сплавов:
Предел прочности на изгиб =1666 МПа.
Плотность =1440014800 кгм3.
Предел прочности на изгиб =1519 МПа.
Плотность =1460015000 кгм3.
Суммируя все вышеизложенное приходим к следующему выбору материалов для режущей части инструментов:
для чернового фрезерования – ВК8;
для чистового фрезерования – ВК6;
для сверления – ВК6;
для зенкерования – ВК6;
для развертывания – ВК6;
Параметры по износу и стойкости инструмента сведем в таблицу 2.6.
Таблица 2.6 - Параметры по износу и стойкости инструмента
В зависимости от диаметра сверла.
В зависимости от диаметра зенкера.
В зависимости от диаметра метчика.
Сверла по ГОСТ 2092-77 ГОСТ 10902-77;
фрезы по ГОСТ 9473-80 ГОСТ 20538-80 ГОСТ 16463-80;
резцы по ГОСТ 9795-81 ГОСТ 18877-73;
цековки по ГОСТ 26258-84;
развертки по ГОСТ 1672-80;
метчики по ГОСТ 3266-81 на те поверхности на которые нет стандартного инструмента разрабатывается специальный инструмент.
5.4 Обоснование выбора мерительных инструментов
Контроль корпусных деталей производят как при выполнении наиболее ответственных операций технологического процесса так и после обработки. При этом контролируются точность размеров относительное положение плоских поверхностей и главных отверстий точность геометрической формы шероховатость базирующих поверхностей детали правильность относительного положения резьбовых и других мелких отверстий.
В условиях серийного производства контроль выполняют с помощью универсальных измерительных средств. Точность размеров и геометрическую форму плоских поверхностей контролируют с помощью линеек угольников уровней концевых мер различных шаблонов. Для контроля точности размеров относительных положений и геометрической формы отверстий дополнительно применяют микрометрические и индикаторные приборы.
Для контроля размеров корпуса применяются как стандартные средства контроля так и специально разработанные для данной детали.
Для контроля размера 8±0.3 был спроектирован специальный шаблон позволяющий контролировать отклонения размера по всей длине окружности.
Для контроля отклонения перпендикулярности отверстия 50Н7 к плоскости был спроектирован специальный измеритель который вкладывается в отверстие. Отклонение определяется с помощью щупа путем замера в двух противоположных точках.
Для контроля отверстий 10.2 под резьбу была разработана специальная пробка позволяющая определить точность обработки.
Для контроля отверстий 50Н7 и 72Н7 были применены пробки соответственно:
для 50Н7 – пробка 8133-0962 Н7 ГОСТ 14816-79.
для 50Н7 – пробка 8133-0010 Н7 ГОСТ 14816-79.
Для контроля резьбы применяются специальные резьбовые пробки:
для М6-7Н – пробка 8221-3030 7Н ГОСТ17758-72.
для М8-7Н – пробка 8221-3036 7Н ГОСТ17758-72.
для М12-7Н – пробка 8221-3037 7Н ГОСТ17758-72.
Для контроля расположения отверстий 50Н7 и 72Н7 относительно друг друга и относительно базовой поверхности был применен индикатор ИЧ02 КЛО ГОСТ 577-88.
Для контроля остальных размеров а также расположения резьбовых отверстий относительно друг друга были выбраны штангенциркули с пределами измерений до 125 мм и до 250 мм по ГОСТ 886-80. Величина отсчета по нониусу 0.1 мм что вполне удовлетворяет точности контролируемых размеров.
5.5 Расчет режимов резания
Операция 025. Продольно-фрезерная.
Фрезерование верхней поверхности и двух боковых одновременно.
Диаметр фрезы для фрезерование верхней поверхности=500 мм
Число зубьев =26; для фрезерования боковых поверхностей =250 мм Число зубьев =13.
Материал режущей части – твердый сплав ВК6
Глубина резания =5 мм.
Подача на зуб фрезы =02 мм.
где – период стойкости фрезы =420 мин.
Показатели степени: =032; =015; =035; =02;=0
– общий поправочный коэффициент на скорость резения:
где – коэффициент учитывающий качество обрабатываемого материала.
– коэффициент учитывающий состояние поверхности заготовки.
– коэффициент учитывающий материал инструмента.
где=200 – для чугуна СЧ20;
=08 - для чугунного литья.
=10 – в случае применения фрезы с пластинами из твердого сплава ВК6.
Частота вращения шпинделя:
Принимаем по паспорту станка =40 мин-1 =75 мин-1
Фактическая скорость резания:
Операция 035. Продольно-фрезерная.
Режимы резания такие же как на операции 025.
Операция 045. Продольно-фрезерная.
Режимы резания аналогичны при обработке боковых поверхностей на операциях 025 и 035.
Операция 050. Плоскошлифовальная. Режимы резания выбираем из
Глубина резания =01 мм.
Скорость круга =35 мс.
Скорость заготовки (стола) =15 ммин.
Продольная подача =25 ммход.
Операция 060. Вертикально-фрезерная.
Фрезерование бобышки 110. Режимы резания определим табличным методом.
Диаметр фрезы =150 мм.
Глубина резания =4 мм.
Подача на зуб фрезы =0.2 мм.
где – коэффициент зависящий от размеров обработки;
– коэффициент зависящий от состояния обработанной поверхности.
– коэффициент зависящий от стойкости и материала инструмента.
Операция 075. Вертикально-сверлильно-фрезерно-расточная с ЧПУ.
Переход 2. Определим режимы резания табличным методом [3].
Фрезерование уступа в размер 8±03 по 260-13.
Диаметр фрезы =50 мм.
Переход 4. Снятие фаски 1х45° на 260-13.
Переход 6. Фрезерование отверстия 216-115.
Глубина резания при черновом фрезеровании =4 мм.
Глубина резания при чистовом фрезеровании =1 мм.
Подача на зуб фрезы при черновом фрезеровании =02 мм.
Подача на зуб фрезы при чистовом фрезеровании =005мм.
где=0.7 (для чернового фрезерования).
=1.2 (для чистового фрезерования).
=0.7(для чернового фрезерования).
=0.9 (для чистового фрезерования).
=35ммин (для чернового фрезерования).
=50ммин (для чистового фрезерования).
Переход 8. Фрезеровать канавку 260272.
Диаметр фрезы =6 мм.
Глубина резания =2 мм.
Подача на зуб фрезы =015 мм.
Переход 10. Фрезерование канавки под сальник предварительно.
Диаметр фрезы =130 мм.
Подача на зуб фрезы =009 мм.
Переход 12. Фрезерование канавки под сальник окончательно.
Режимы резания аналогичны переходу 10.
Переход 14. Фрезерование бобышки 110.
Диаметр фрезы =70 мм.
Подача на зуб фрезы при черновом фрезеровании =021 мм.
Подача на зуб фрезы при чистовом фрезеровании =006мм.
где=08 (для чернового фрезерования).
=125 (для чистового фрезерования).
=07 (для чернового фрезерования).
=09 (для чистового фрезерования).
=35 ммин (для чернового фрезерования).
Переход 16. Сверлить отверстие в бобышке 40.
Режущий инструмент сверло.
– коэффициент зависящий от обрабатываемого материала;
– коэффициент зависящий от стойкости инструмента;
– коэффициент зависящий от глубины сверления.
Переход 18. Зенкеровать отверстие в бобышке 495.
Глубина резания =475 мм.
Переход 20. Растачивание отверстия 50 с получением фаски.
Глубина резания =05 мм.
Переход 22. Фрезерование платиков по контуру.
Материал режущей части – твердый сплав ВК8.
Переход 24. Центрование отверстий.
Сверло центровочное =25 мм.
Глубина резания =125 мм.
Переход 26. Сверление трех отверстий 4.
Переход 28. Сверление отверстий под резьбу М8.
Глубина резания =34 мм.
Переход 30. Расверливание отверстий 20.
Глубина резания =10 мм.
Переход 32. Расверливание отверстий под резьбу М12.
Глубина резания =51 мм.
Переход 34. Нарезание резьбы М8.
Переход 36. Нарезание резьбы М12.
Операция 090. Фрезерно-сверлильно-расточная с ЧПУ.
Расчет режимов резания ведется аналогично операции 075.
Переход 2. Зенкерование отверстия.
Глубина резания =30 мм.
Частота вращения шпинделя
Переход 4. Черновое растачивание отверстия.
Глубина резания =20 мм.
Переход 6. Чистовое растачивание отверстия.
Переход 8. Сверление отверстий под резьбу М8.
Глубина резания =3.4 мм.
Переход 10. Нарезание резьбы М8.
Переход 12. Фрезерование поверхности.
Переход 14. Сверление отверстий под резьбу М8.
Режимы резания аналогичны переходу 8.
Переход 16. Нарезание резьбы М8.
Переход 18. Зенкерование отверстия.
Режимы резания аналогичны переходу 2.
Переход 20. Черновое растачивание отверстия.
Режимы резания аналогичны переходу 4.
Переход 22. Чистовое растачивание отверстия.
Режимы резания аналогичны переходу 6.
Переход 24. Сверление отверстий под резьбу М8.
Переход 26. Нарезание резьбы М8.
5.6 Расчет технических норм времени
Для расчета технических норм времени определяется норма штучно – калькуляционного времени Тшт [3].
Операция 025 Продольно-фрезерная.
Одновременное фрезерования верхней поверхности и двух боковых.
Основное время обработки:
где-длина обработки мм;
– длина рабочего хода.
– величина врезания и перебега инструмента .
=580 мм; =10+10=20мм; =1; =208 мммин;
Вспомогательное время:
Время на обслуживание и отдых 7% от оперативного времени [3]:
Подготовительно-заключительное время Тпз=20мин.
Штучно-калькулиционное время:
Операция 035 Продольно-фрезерная.
Расчет аналогичен расчету операции 025.
=332 мм; =10+10=20мм; =1; =208 мммин; =40 мин-1;
Операция 045 Продольно-фрезерная.
=385 мм; =10+10=20мм; =1; =208 мммин; =40 мин-1;
Время на обслуживание и отдых 7% от оперативного времени
Операция 050. Шлифование поверхности.
где-длина обработки м;
– скорость заготовки (стола) =15 ммин.
- ширина обработки мм;
где - ширина обрабатываемой детали мм =405 мм;
– величина врезания и перебега инструмента
=580 мм; =50+50=100мм;
Вспомогательное время [4]:
Время на обслуживание и отдых 7% от оперативного времени:
Операция 060. Фрезерование бобышки.
=110 мм; =10+10=20мм; =1; =306 мммин;
Операция 075. Сверлильно-фрезерно-расточная с ЧПУ.
Переход 2. Фрезерование уступа в размер 8±0.3 по 260-13.
Время затраченное на холостой ход:
где-скорость быстрого перемещения =10000 мммин;
Операция 075. Серлильно-фрезерно-расточная с ЧПУ.
Норма штучного времени
где – время автоматической работы по программе.
где – время основной работы по программе.
где – длина рабочего хода;
– время вспомогательной работы по программе.
где – время автоматической вспомогательной работы;
– время технологических остановок.
где – длина холостого хода;
– скорость быстрого перемещения.
– время выполнения ручной вспомогательной работы.
где – время на установку и снятие детали;
– вемя на закрепление и открепление детали;
– время затраченное на измерение;
– поправочный коэффициент на время выполнения ручной вспомогательной работы учитывающий характер работы;
– время затраченное на организационно-техническое обслуживание рабочего места отдых и личные надобности.
Норма времени на обработку партии деталей:
где – количество деталей в партии =21 шт.;
– подготовительно-заключительное время =25 мин;
Норма штучно-калькуляционного времени на деталь.
Рассчитаем время основной работы по програмне:
Найдем время вспомогательной работы по програмне:
Найдем время автоматической работы по программе:
Найдем время выполнения ручной вспомогательной работы:
Учитывая что =13 мин
Время на закрепление и открепление детали =01 мин
Время затраченное на измерение =057 мин
Время связанное с управлением:
где – время затраченное на включение и выключение станка =004 мин;
– время затраченное на передвижку ленты в исходное положение =003 мин;
– время затраченное на перемотку ленты =05 мин.
составляет 12% от оперативного времени.
Найдем штучное время:
Найдем норму времени на обработку партии деталей:
Найдем штучно-калькуляционное время
Операция 085. Сверлильно-фрезерно-расточная с ЧПУ.
Расчет аналогичен расчету времени на операции 075.
6 Проектирование технологической оснастки
6.1 Описание конструкции и принципа работы приспособления
Для установки и закрепления детали на сверлильно-фрезерно-расточной операции необходимо разработать специальное приспособление с пневматическими зажимами.
Конструкция приспособления.
Приспособление состоит из следующих основных частей и деталей: основание которое крепится непосредственно на стол станка; на которое устанавливается обрабатываемая деталь. На основании закреплены упоры которые служат для выставки детали а также трех пневматических прихватов которые служат для зажима детали.
При подаче воздуха в нижнею часть пневмоцилиндра там создается давление а так как поршень не имеет возможности передвижения (он соединен со штоком а шток неподвижен) то давление передается на нижнею крышку. Она в свою очередь под действием давления воздуха вместе с цилиндром перемещается вниз относительно штока в результате чего движение передается прихвату. Он опускается вниз и происходит зажим детали.
При переключении подачи воздуха в другую полость пневмоцилиндра крышка вместе с цилиндром поднимается вверх относительно штока перемещая прихват вверх. Происходит открепление детали.
6.2 Расчет сил зажима и конструктивных параметров приспособления
Расчет приспособления.
Исходные данные для расчета:
Сила резания – =4500 Н.
Давление сжатого воздуха =039 Мпа.
Для обеспечения надежности зажима детали определяется коэффициент запаса :
где =15 – постоянный коэффициент запаса.
=12 – коэффициент учитывающий состояние поверхности детали.
=14 – коэффициент учитывающий увеличение сил резания при затуплении инструмента.
=12 – коэффициент учитывающий увеличение сил резания при обработке прерывистых поверхностей.
=13 – коэффициент учитывающий постоянство сил зажима развиваемый приводом приспособления.
=10 – коэффициент учитывающий удобное расположение органов управления.
=15 – коэффициент учитывающий наличие моментов.
Необходимая сила зажима для обрабатываемой детали:
где и – коэффициенты трения.
Определим расчетный диаметр пневматического цилиндра:
где =0.85 – К.П.Д. привода.
По ряду стандартных чисел принимаем диаметр пневмоцилиндра =100 мм.
Определим действительную силу зажима:
Время срабатывания пневмопривода:
где =40 мм – длина хода поршня.
=6 мм – диаметр воздухопровода.
=180 мс – скорость перемещения воздуха.
6.3 Расчет режущего и контрольно – мерительного инструмента
Расчет двухступенчатого сверла
Расчитать и сконструировать двухступенчатое сверло из быстрорежущей стали с цилиндрическим хвостовиком для обработки отверстия под метрическую резьбу М12-6Н.
Определим диаметр сверла.
Диаметр первой ступени для сверления отверстия под резьбу М10 в заготовке из алюминиевого сплава равен мм. Диаметр второй ступени для снятия фаски в отверстии равен мм.
Осевая составляющая силы резания
где -диаметр сверла мм мм;
-поправочный коэффициент;
Значения коэффициентов принимаем из таблицы 32 [2].
Момент сил сопротивления ре занию:
Значения коэффициентов принимаем из таблицы 31 [7].
Определим конус Морзе хвостовика сверла для этого найдем средний диаметр хвостовика
где - коэффициент трения сталь по стали =0096;
- половина угла конуса =1°26’16’’;
- отклонение угла конуса =5’;
Выбираем конус Морзе №2 с длинной хвостовика 80 мм.
где -длина рабочей части мм;
-длина первой ступени мм =55мм;
-длина второй части мм =100мм;
-длина хвостовика мм =80мм.
Определяем геометрические и конструктивные параметры рабочей части сверла.
Угол наклона винтовой канавки ;
Угол между режущими кромками ;
Угол наклона поперечной кромки ;
Шаг винтовой канавки первой ступени
Толщина сердцевины сверла первой ступени
Утолщение сердцевины по направлению к хвостовику 15мм на 100мм длины.Обратная конусность сверла на 100мм длины рабочей части 005мм.
Высота затылка по стенке:
Ширина пера первой ступени:
Геометрические параметры канавки первой ступени:
Больший радиус профиля:
Принимаем диаметр фрезы .
Меньший радиус профиля:
Шаг винтовой канавки второй ступени:
Толщина сердцевины сверла второй ступени:
Ширина пера второй ступени:
Геометрические параметры канавки второй ступени:
Принимаем диаметр фрезы :.
Расчет исполнительных калибров – пробки
Расчитаем калибр пробку для контроля отверстия мм. Его разработка вызвана необходимостью контроля допуска изготовления отверстия и отсутствием в ГОСТе калибров конкретного типоразмера.
Определим предельные размеры отверстия
-максимальный диаметр отверстия мм;
-номинальный диаметр отверстия мм =102 мм;
-верхнее предельное отклонение мм =036 мм;
-минимальный диаметр отверстия мм;
-нижнее предельное отклонение мм =0мм.
Расчет исполнительных диаметров калибра:
Расчет проходного калибра:
-отклонение середины поля допуска на изготовление проходного калибра для отверстия относительно наименьшего предельного размера мм =70мкм=0007мм таблица 2 [21];
-допуск на изготовление калибра мм =25мкм=00025мм таблица 2 [21].
Расчет проходного изношенного кали бра:
где -допустимый выход размера изношенного проходного калибра для отверстия за границу поля допуска изделия мм =5мкм=0005мм;
-величина для компенсации погрешности контроля калибрами отверстий мм =0мм таблица 2 [21].
Расчет непроходного калибра
Схема полей допусков исполнительных размеров калибра представлена на рисунке 2.2.
Рисунок 2.2 - Схема полей допусков исполнительных размеров калибра
Четвертая часть.doc
Основной задачей производства в области охраны труда является обеспечение безопасности работ выполняемых обслуживающим персоналом.
Вопросы охраны труда должны решатся комплексно с вопросами защиты окружающей среды и при проектировании технологического процесса должны учитываться требования законодательства по охране природы и охране окружающей среды.
1 Охрана труда при работе на металлорежущих станках
Общие положения по безопасности производственного оборудования и в частности металлорежущих станков определены системой стандартов безопасности труда ССБТ. Основными стандартами имеющими отношение к безопасности станков являются следующие:
ГОСТ предусматривает четыре класса опасных и вредных производственных факторов: физические химические биологические и психофизиологические. К вопросам безопасности при работе на станках главным образом относятся факторы физические (движущиеся машины и механизмы незащищенные подвижные элементы производственного оборудования передвигающиеся изделия заготовки материалы; повышенная запыленность уровень шума вибрации и др.) и психофизиологические (физическое и умственное перенапряжение нервно-психические перегрузки перенапряжение анализаторов эмоциональные перегрузки и др.).
Кроме общих требований по безопасному устройству производственного оборудования (с учетом опасных и вредных факторов) предусмотрено обязательное включение требований безопасности в техническую документацию по монтажу эксплуатации ремонту транспортированию и хранению оборудования.
К металлорежущим станкам с точки зрения безопасности труда предъявляется множество различных требований. Среди которых можно выделить следующие:
Станки и другое оборудование должны быть установлены на прочных основаниях или фундаментах тщательно выверены и надежно закреплены.
Движущие части станков и механизмов которые могут явиться причиной травмирования работающих должны быть укрыты соответствующими защитными ограждениями.
Конструкции ограждающих устройств должны быть достаточно прочными надежно крепиться не мешать производительной работе уборке и наладке станка. В зависимости от назначения и частоты использования ограждающие устройства следует выполнять в виде открывающихся или съемных кожухов.
Ограждения должны иметь рукоятки скобы и другие устройства для удобного и безопасного удержания их при съеме и установке.
Выступающие концы вращающихся валов и винтов оборудования должны быть закрыты глухими неподвижными кожухами или в случае необходимости телескопическими ограждениями.
Станки пилы и тому подобное оборудование должно быть оснащено экранами (ограждениями) надежно защищающими рабочих и находящихся около рабочих мест лиц от отлетающей стружки и осколков случайно поломавшегося инструмента или от брызг охлаждающе-смазывающей жидкости.
Конструкция экранов должна быть легкоподвижной и предусматривать возможность удобной и безопасной чистки смотровых окон от загрязнений.
Рабочим работающим на станках которые конструктивно или по другим обстоятельствам не могли быть обеспечены защитными устройствами администрация обязана выдавать удобные не мешающие работе защитные очки и постоянно следить за их применением во время работы на станках.
Переключение рычагов рукояток и других органов управления должно происходить плавно без заедания.
Все органы управления должны быть расположены в местах удобных для обслуживания и так чтобы при перемещении их руки рабочего не ударялись о соседнюю рукоятку или какую-либо часть оборудования и чтобы нельзя было случайным движением локтя или ноги привести их в движение.
Все органы управления должны иметь четкие и ясные надписи (символы) поясняющие их назначение.
Электрическая аппаратура и токоведущие части должны быть надежно изолированы и укрыты в корпусе станка или в специальные закрытые со всех сторон шкафы кожухи и тому подобное.
Не зависимо от способа защиты на всех дверцах крышках кожухах с лицевой стороны должны иметься четкие предостерегающие знаки «Молния».
Металлические конструктивные части станков а также отдельно стоящие электрические устройства (шкафы пульты управления и т. п.) которые могут оказаться под напряжением вследствие нарушении изоляции и замыкания на корпус должны быть заземлены в соответствии с Правилами устройства электроустановок.
Фрезерные станки должны быть оборудованы быстродействующими и надежными тормозными устройствами.
Передаточные валы карданные соединения выступающие задние концы шпинделей и шомполов фрезерных станков должны быть ограждены.
При установке и смене фрез должны применяться специальные приспособления предотвращающие порезы рук.
Для удаления стружки вблизи вращающейся фрезы рабочим должны выдаваться кисточки с деревянными ручками длиной не менее 250 мм.
Обрабатываемые детали должны устанавливаться и закрепляться в соответствующие приспособления (тиски кондуктора и т.п.) закрепляемые на столе станка.
Инструменты с забитыми или изношенными конусами и хвостовиками не должны выдаваться на рабочие места для использования их на станках. Неисправные инструменты должны быть изъяты с рабочего места.
Каждый шлифовальный станок должен быть оборудован местной вытяжной вентиляцией.
Рабочие при работе на металлорежущих станках должны соблюдать целый ряд правил записанных в различных инструкциях. В качестве примера можно привести ряд требований из инструкции по охране труда при работе на фрезерных станках:
Перед установкой на станок очистить от стружки и масла обрабатываемые детали и приспособления особенно соприкасающиеся базовые и крепежные поверхности для обеспечения правильной установки и прочности крепления.
Обрабатываемую деталь установить на станке правильно и надежно чтобы во время хода станка были исключены возможности ее вылета или какие-либо другие нарушения технологического процесса.
Деталь закреплять в местах находящихся как можно ближе к обрабатываемой поверхности.
При использовании для закрепления деталей пневматических приспособлений необходимо тщательно избегать механических повреждений трубки подачи воздуха.
Деталь к фрезе подавать тогда когда последняя получит рабочее вращение.
При смене обрабатываемой детали или ее измерении отвести фрезу на безопасное расстояние.
Врезать фрезу в деталь постепенно; механическую подачу включать до соприкосновении детали с фрезой.
При фрезеровании не вводить руки в опасную зону вращения фрезы.
Пользоваться только исправной фрезой.
Не допускать скопление стружки на фрезе и оправке.
Выколачивая фрезу из шпинделя не поддерживать ее не защищенной рукой – пользоваться для этого эластичной прокладкой.
Установленную и закрепленную фрезу проверить на биение. Радиальное и торцевое биение не должно превышать 0.1 мм.
Фрезерную оправку или фрезу закреплять в шпинделе только ключом включив перебор чтобы шпиндель не проворачивался.
При установке и съеме фрез остерегаться ранений о режущие кромки.
Зажим и отжим фрезы ключом на оправке путем включения электродвигателя запрещается.
Не становиться на движущий стол фрезерного станка и не переходить через него до полного останова станка.
Не оставлять ключ на головке затяжного болта после установки фрезы или оправки.
Останавливая станок выключить подачу затем отвести фрезу от обрабатываемой детали и выключить вращение фрезы (шпинделя).
Рабочие и служащие цехов и участков обработки резанием для защиты от воздействия опасных и вредных производственных факторов должны быть обеспечены спецодеждой спецобовью и предохранительными приспособлениями в соответствии с действующими типовыми отраслевыми нормами утвержденными в установленном порядке.
Спецодежду работающих в цехах и на участках следует периодически сдавать в стирку (химчистку) и хранить отдельно от верхней одежды. Химчистка и стирка спецодежды должна быть централизованной проводиться по мере загрязнения но не реже двух раз в месяц.
Инженерно-технические работники ответственные за проведение процесса обработки резанием (мастера технологи старшие мастера заместители начальников цехов и начальники цехов) при назначении на должность должны проходить проверку правил норм и стандартов основ технологических процессов требований безопасности устройств и безопасной эксплуатации металлорежущего подъемно-транспортного и другого применяемого оборудования выполнения погрузочно-разгрузочных работ пожарной безопасности и производственной санитарии в соответствии с их должностными обязанностями.
2 Обеспечение электробезопасности при работе на металлорежущих станках
Проходя через организм электрический ток оказывает термическое электролитическое и биологическое действие.
Термическое выражается в ожогах отдельных участков тела нагреве кровеносных сосудов нервов и других тканей. Электролитическое действие выражается в разложении крови и других органических жидкостей что вызывает значительные нарушения их физико-химических составов.
Биологическое действие является особым специфическим процессом свойственным лишь живой материи. Оно выражается в раздражении и возбуждении живых тканей организма а также в нарушении внутренних биоэлектрических процессов протекающих в нормально действующем организме и теснейшим образом связанных с его жизненными функциями. В результате могут возникнуть различные нарушения в организме в том числе нарушение и даже полное прекращение деятельности органов дыхания и кровообращения. Раздражающее действие тока на ткани организма может быть прямым когда ток проходит непосредственно по этим тканям и рефлекторным т. е. через центральную нервную систему когда путь тока лежит вне этих тканей.
Это многообразие действий электрического тока нередко приводит к различным электротравмам которые условно можно свести к двум видам: местным электротравмам и общим электротравмам (электрическим ударам).
Основные причины несчастных случаев от воздействия электрического тока следующие:
а) случайное прикосновение или приближение на опасное расстояние к токоведущим частям находящимся под напряжением;
б) появление напряжения на металлических конструктивных частях оборудования - корпусах кожухах и т. п. - в результате повреждения изоляции и других причин;
в) появление напряжения на отключенных токоведущих частях на которых работают люди вследствие ошибочного включения установки;
г) возникновение шагового напряжения на поверхности земли в результате замыкания провода на землю.
Основными мерами защиты от поражения током являются: обеспечение недоступности токоведущих частей находящихся под напряжением для случайного прикосновения; электрическое разделение сети; устранение опасности поражения при появлении напряжения на корпусах кожухах и других частях электрооборудования что достигается применением малых напряжений использованием двойной изоляции выравниванием потенциала защитным заземлением занулением защитным отключением и др.; применение специальных электрозащитных средств - переносных приборов и приспособлений; организация безопасной эксплуатации электроустановок.
Недоступность токоведущих частей электроустановок для случайного прикосновения может быть обеспечена рядом способов: изоляцией токоведущих частей размещением их на недоступной высоте ограждением и др.
Электрическое разделение сети - это разделение электрической сети на отдельные электрически не связанные между собой участки с помощью специальных разделяющих трансформаторов. В результате изолированные участки сети обладают большим сопротивлением изоляции и малой емкостью проводов относительно земли за счет чего значительно улучшаются условия безопасности.
Применение малого напряжения. При работе с переносным ручным электроинструментом - дрелью гайковертом зубилом и т. п. а также ручной переносной лампой человек имеет длительный контакт с корпусами этого оборудования. В результате для него резко повышается опасность поражения током в случае повреждения изоляции и появлении напряжения на корпусе особенно если работа производится в помещении с повышенной опасностью особо опасном или вне помещения.
Для устранения этой опасности необходимо питать ручной инструмент и переносные лампы напряжением не выше 42 В.
Кроме того в особо опасных помещениях при особенно неблагоприятных условиях для питания ручных переносных ламп требуется еще более низкое напряжение - 12 В.
Двойная изоляция - это электрическая изоляция состоящая из рабочей и дополнительной изоляции. Рабочая изоляция предназначена для изоляции токоведущих частей электроустановки обеспечивая ее нормальную работу и защиту от поражения током. Дополнительная изоляция предусматривается дополнительно к рабочей для защиты от поражения током в случае повреждения рабочей изоляции. Двойную изоляцию широко применяют при создании ручных электрических машин. При работе таких машин заземление или зануление их корпусов не требуется.
Защитное заземление - преднамеренное электрическое соединение с землей или ее эквивалентом металлических нетоковедущих частей которые могут оказаться под напряжением.
Назначение защитного заземления - устранение опасности поражения людей электрическим током при появлении напряжения на конструктивных частях электрооборудования т. е. при замыкании на корпус.
Область применения защитного заземления - трехфазные трехпроводные сети напряжением до 1000 В с изолированной нейтралью и выше 1000 В с любым режимом нейтрали.
Защитному заземлению подлежат металлические нетоковедущие части оборудования которые из-за неисправности изоляции могут оказаться под напряжением и к которым возможно прикосновение людей или животных. При этом в помещениях с повышенной опасностью и особо опасных по условиям поражения током а также в наружных установках заземление является обязательным при номинальном напряжении электроустановки выше 42 В переменного и выше 110 В постоянного тока а в помещениях без повышенной опасности - при напряжении 380 В и выше переменного и 440 В и выше постоянного тока. Лишь во взрывоопасных помещениях заземление выполняется независимо от значения напряжения установки.
Занулением называется преднамеренное электрическое соединение с нулевым защитным проводником металлических нетоковедущих частей которые могут оказаться под напряжением.
Область применения зануления - трехфазные четырехпроводные сети напряжением до 1000 В с глухозаземленной нейтралью.
Защитное отключение - быстродействующая защита обеспечивающая автоматическое отключение электроустановки при возникновении в ней опасности поражения током.
Такая опасность может возникнуть в частности при замыкании фазы на корпус электрооборудования; при снижении сопротивления изоляции фаз относительно земли ниже определенного предела; появлении в сети более высокого напряжения; прикосновении человека к токоведущей части находящейся под напряжением. В этих случаях в сети происходит изменение некоторых электрических параметров: например могут измениться напряжение корпуса относительно земли напряжение фаз относительно земли напряжение нулевой последовательности и др. Любой из этих параметров а точнее говоря - изменение его до определенного предела при котором возникает опасность поражения человека током может служить импульсом вызывающим срабатывание защитно-отключающего устройства т. е. автоматическое отключение опасного участка сети.
Устройства защитного отключения должны обеспечивать отключение неисправной электроустановки за время не более 02 с.
В процессе эксплуатации электроустановок нередко возникают условия при которых даже самое совершенное их выполнение не обеспечивает безопасности работающего и требуется применение специальных средств защиты. Например при работе вблизи токоведущих частей находящихся под напряжением существует опасность прикосновения к этим частям и поэтому требуется специальная изоляция инструмента и работающего; при работе на отключенных токоведущих частях - шинах проводах и т. д. - имеется опасность случайного появления напряжения на них поэтому должны быть приняты меры исключающие ошибочную подачу напряжения к месту работ и вместе с тем устраняющие опасность поражения током работающих в случае включении электроустановки под напряжение.
Такими средствами защиты дополняющими стационарные конструктивные защитные устройства электроустановок являются переносные приборы и приспособления служащие для защиты персонала работающего в электроустановках от поражения током от воздействия электрической дуги продуктов горения падения с высоты и т. п.
Средства защиты условно делятся на три группы: изолирующие ограждающие и предохранительные.
Среди всех средств защиты особое место занимают электрозащитные средства служащие для защиты от поражения током.
Изолирующие электрозащитные средства делятся на основные и дополнительные.
Основные изолирующие электрозащитные средства способны длительное время выдерживать рабочее напряжение электроустановки и поэтому ими разрешается касаться токоведущих частей находящихся под напряжением и работать на этих частях. К таким средствам относятся диэлектрические резиновые перчатки инструмент с изолирующими рукоятками и т. д.
Дополнительные изолирующие электрозащитные средства обладают недостаточной электрической прочностью и поэтому не могут самостоятельно защитить человека от поражения током. Их назначение - усилить защитное действие основных изолирующих средств вместе с которыми они должны применяться. К дополнительным изолирующим защитным средствам относятся диэлектрические галоши коврики и изолирующие подставки.
Ограждающие средства защиты предназначены для временного ограждения токоведущих частей (временные переносные ограждения-щиты ограждения-клетки и т. п.); для предупреждения ошибочных операций (пердупредительные плакаты); для временного заземления отключенных токоведущих частей (временные заземления).
Опыт показывает что для обеспечения безопасной безаварийной и высокопроизводительной работы электроустановок необходимо наряду с совершенным исполнением их и оснащением средствами защиты так организовать их эксплуатацию чтобы исключить всякую возможность ошибок со стороны обслуживающего персонала. Структура организации эксплуатации разработана в результате длительного опыта работы множества электроустановок и приведена в правилах технической эксплуатации электроустановок потребителей и правилах техники безопасности при эксплуатации электроустановок потребителей.
Основой организации безопасной эксплуатации электроустановок являются высокая техническая грамотность и сознательная дисциплина обслуживающего персонала который обязан строго соблюдать организационные и технические мероприятия а также приемы и очередность выполнения эксплуатационных операций в соответствии с правилами.
Все работы в электроустановке производят при обязательном соблюдении следующих условий:
а) на работу должно быть выдано разрешение уполномоченным на это лицом;
б) работу должны производить как правило не меньше чем два лица;
в) должны быть выполнены организационные и технические мероприятия обеспечивающие безопасность персонала.
3 Расчет защитного заземления
Подключенное на участке оборудование работает с опасным для жизни человека напряжением 380 В. Для обеспечения безопасной работы на участке необходимо наличие защитного заземления.
Произведем расчет защитного заземления с контурным заземляющим устройством которое характеризуется тем что его одиночные заземлители размещаются по периметру площади на которой находится заземляемое оборудование.
Используем искусственные заземлители. Вертикальные - трубы стальные горизонтальные - полосовая сталь.
Определим сопротивление одиночного стержневого заземлителя по формуле 4.1;
где - удельное сопротивление грунта ; =100 [15];
- коэффициент сезонности для вертикальных заземлителей; =16 [15];
- длина стержневого заземлителя м; =3 м [15];
- диаметр заземлителя м; =006 м [15];
- расстояние от поверхности земли до середины заземлителя м; =2.2 м [15];
Определим сопротивление растекания тока соединительной полосы по формуле 4.2;
где - коэффициент сезонности для горизонтального заземлителя =35 [15];
- длина полосы м; =96 м;
- ширина полосы м; =0012 м;
- глубина заложения полосы м; =08 [15];
Определим число заземлителей по формуле 4.3;
где - периметр контура м; =96 м;
- расстояние между заземлителями м; =2 м [15];
Определим общее сопротивление контура заземления по формуле 4.4;
где - коэффициент использования горизонтального заземлителя =041 [15];
- коэффициент использования вертикального заземлителя; =022 [15];
Полученное значение сопротивления заземляющего устройства не должно превышать наибольшего сопротивления допустимого правилами устройства электроустановок.
где - наибольшее допустимое сопротивление Ом; =4 Ом [15];
При соблюдении произведенных требований и расчетов по технике безопасности на участке можно гарантировать безопасность работ при изготовлении корпуса.
Рисунок 4.1-Схема выносного заземляющего устройства:
-заземляющие проводники;
-заземляемое оборудование.
Произведен анализ опасных и вредных факторов при технологическом процессе который показал что возникающие физические химические электрические психофизические и биологические вредные факторы сводятся к минимуму при правильно построенном технологическим процессе и выполнении правил и норм техники безопасности.
Рассмотрено обеспечение безопасности при работе на металлорежущих станках что позволило сделать вывод: для обеспечения безопасности рабочего работающего на станках нужно выполнять ряд норм и правил предъявляемых как к оборудованию так и к помещению заземлению огражденгию электропитанию.
Произведен расчет защитного заземления который показал что полученное значение сопротивления заземляющего устройства не превышает наибольшего сопротивления допустимого правилами устройства электроустановок.
Пятая часть-1.doc
Целью данного дипломного проекта является разработка технологического процесса изготовления корпуса и средств его оснащения.
Назначение спроектированного технологического процесса - изготовление корпуса заданной точности и качества в количестве не менее 500 штук в год.
Данный технологический процесс разработан на базе существующего технологического процесса который был предназначен для выпуска даного изделия в условиях массового производства. Поскольку годовая программа выпуска была уменьшена в несколько раз то возникла необходимость модернизации существующего технологического процесса с целью сокращения штучного времени изготовления детали и ее себестоимости. Для этого стали применяться станки с числовым программным управлением (ЧПУ) и специальные приспособления для уменьшения времени базирования закрепления и снятия заготовки.
Снижение штучного времени изготовления детали повлекло за собой снижение затрат на инструмент аммортизацию оборудования электроэнергию и т.д. что в свою очередь скажется на снижении себестоимости изделия.
Целью технико-экономических расчетов в дипломном проекте является решение вопросов сетевого планирования расчет затрат на проектирование технологического процесса и оценка экономической эффективности технологического процесса.
1 Расчет затрат на проектирование технологического процесса
Затраты на проектирование технологического процесса представляют собой стоимостную оценку использованных в процессе проектирования сырья материалов покупных комплектующих изделий и полуфабрикатов расходов на приобретение специального оборудования оплату труда занятых разработкой технологического процесса затраты по работам выполненным сторонними организациями и др.
Затраты на проектирование данного технологического процесса определяются по формуле:
В стоимость сырья и материалов включается стоимость использованного в процессе разработки данного технологического процесса сырья основных и вспомогательных материалов необходимых для проведения исследований экспериментов опытов испытаний и т. П.
В данном случае затраты на сырье и материалы включают в себя затраты на изготовление заготовок для проведения экспериментальных работ.
Стоимость сырья и материалов:
где - стоимость одной тонны заготовок руб;
- масса заготовки кг;
- коэффициенты зависящие от класса точностигруппы сложности массы марки материала и объема производства заготовок;
- цена одной тонны отходов руб;
- количество заготовок.
В состав основной заработной платы включаются выплты за фактически выполненную работу в соответствии с окладами тарифными ставками и расценками всему персоналу принимавшему участие в разработке данного технологического процесса: научным работникам
инженерно-техническим работникам лаборантам рабочим и служащим исследовательских и проектных подразделений рабочим экспериментальных и опытных цехов и др.
Расчет основной заработной платы осуществляется в табличной форме и сведем в таблицу 5.1.
Таблица 5.1-Рсчет основной заработной платы
Инженер III категории
Инженер II категории
Расточник VI разряда
Фрезеровщик VI разряда
В состав дополнительной заработной платы разработчиков включаются все виды выплат надбавок и доплат из фонда заработной платы за проработанное и непроработанное время (надбавки за профессиональное мастерство доплаты за условия труда работу в ночную смену выплаты отпускных вознаграждение за выслугу лет и др.).
Дополнительная заработная плата рассчитывается по формуле:
где - коэффициент дополнительной заработной платы.
Коэффициент дополнительной заработной платы устанавливается в каждой конкретной организации по данным базового или планового периода на основе сложившегося отношения между фондом дополнительной заработной платы и фондом основной заработной платы разработчиков в целом по проектной организации.
Отчисления на социальные нужды рассчитываются по формуле:
где - коэффициент отчислений на социальные нужды.
Коэффициент отчислений на социальные нужды в настоящее время составляет 26% и включает в себя:
В состав накладных расходов включаются затраты на аммортизацию ремонт и содержание зданий и других основных производственных фондов общего назначения содержание аппарата управления проектной организации почтово-телеграфные и канцелярские расходы налоги сборы и т. д.
Накладные расходы определяются по формуле:
где - коэффициент накладных расходов.
Коэффициент накладных расходов берется по данным конкретной роектной организации. Он определяется по базовым или плановым данным в конкретной организации исходя из сложившегося соотношения сметы накладных расходов организации и фондов основной заработной платы персонала организации.
Все расчеты затрат на проектирование технологического процесса сведем в таблицу 5.2.
Таблица 5.2-Затраты на проектирование технологического процесса
Наименование статей расхода
Основная заработная плата разработчиков технологического процесса
Дополнительная заработная плата разработчиков технологического процесса
Отчисления на социальные нужды
Итого затраты на проектирование
Цены на разработку устанавливаются на основе договора между заказчиком и исполнителем т.е. устанавливается так называемая договорная цена.
Для экономических расчетов и прогнозов цену на разработку экономически целесообразно устанавливать на основе прогнозируемого уровня рентабельности.
В этом случае цена вместе с налогом на добавленную стоимость (НДС) может быть рассчитана по формуле:
где - установленный или прогнозируемый уровень рентабельности %; =15-25%
- налог на добавленную стоимость %. =18%
2 Оценка экономической эффективности технологического процесса
Итоговым экономическим расчетом в организационно-экономическом разделе дипломного проекта является оценка экономической эффективности спроектированного технологического процесса.
На этапе разработки нового технологического процесса может быть рассчитан лишь его предварительный экономический эффект который носит потенциальный характер. Обусловлено это невозможностью на этапе разработки технологического процесса с достаточной степенью достоверности выявить для расчета реального эффекта всю совокупность факторов оказывающих влияние на состав и уровень эффекта от разработки и применения технологического процесса характерных для данного объекта внедрения разработанного нового технологического процесса.
Поэтому основной целью оценки экономической эффективности технологического процесса на этапе его разработки является не столько расчет неких абсолютных значений его эффективности сколько обеспечение соответствующих руководителей объективной достоверной и достаточной информацией для принятия или непринятия решения о разработке и применении нового технологического процесса.
2.1 Расчет капитальных вложений
При оценке экономической эффективности технологического процесса на этапе его разработки полные капитальные вложения могут быть рассчитаны по формуле:
где - затраты на проектирование технологического процесса руб;
- затраты на технологическое оборудование руб;
- затраты на средства технологического оснащения руб;
- стоимость производственных площадей занимаемых оборудованием руб;
- cтоимость средств программного обеспечения для станков с ЧПУ руб.
Капитальные затраты на проектирование технологического процесса рассчитываются лишь для нового варианта и рассчитаны выше
Капитальные затраты на технологическое оборудование:
где - коэффициент учитывающий расходы на транспортировку и монтаж оборудования;
- число групп оборудования;
- наименование группы оборудования;
- принятое число единиц оборудования;
- цена единиц оборудования руб;
- коэффициент учитывающий занятость оборудования.
Расчетное количество единиц оборудования:
где - годовая программа запуска шт.
- штучно-калькуляционное время обработки деталей на - той группе оборудования мин;
- действительный годовой фонд времени работ единиц оборудования час;
- средний коэффициент выполнения норм;
- коэффициент учитывающий неизбежные потери времени.
Расчет количества оборудования осуществляется в табличной форме.
Коэффициент занятости оборудования:
Капитальные затраты на средства технологического оснащения:
где - наименование типоразмера оснастки необходимой для обработки деталей данного наименования на всех операциях технологического процесса;
- количество типоразмеров оснастки необходимой для выполнения всех операций технологического процесса обработки деталей данного наименования;
- цена единицы оснастки руб;
- количество единиц оснастки;
- коэффициент занятости оснастки. При использовании специальной оснастки рассчитанной на обработку деталей только одного наименования . В остальных случаях:
Капитальные затраты на производственные площади занимаемые технологическим оборудованием:
где - производственная площадь занимаемая единицей оборудования ;
- коэффициент учитывающий дополнительную площадь;
- цена 1 производственной площади руб.
Капитальные затраты на средства программного обеспечения для станков с ЧПУ учитываются лишь для тех средств программного обеспечения стоимость которых за единицу превышает 1000 руб. и берется по фактическим данным.
Удельные капитальные вложения:
Расчет капитальных вложений для базового технологического процесса.
Расчет количества оборудования сведем в таблицу 5.3.
Таблица 5.3-Количество оборудования в базовом технологическом процессе
Горизонтально-расточная с ЧПУ
Вертикально-фрезерная с ЧПУ
Радиально-сверлильная
Капитальные затраты на производственные площади:
Полные капитальные вложения:
Расчет капитальных вложений для проектируемого технологического процесса
Расчет количества оборудования сведем в таблицу 5.4.
Таблица 5.4-Количество оборудования в проектируемом технологическом процессе
Сверлильно-фрезерно-расточная с ЧПУ
Фрезерно-сверлильно-расточная с ЧПУ
2.2 Расчет технологической себестоимости
Технологическая себестоимость обработки детали - это сово
купность затрат лишь непосредственно связанных с технологическим процессом ее изготовления.
Технологическая себестоимость обработки детали может быть рассчитана по формуле:
где - затраты на основные материалы руб;
- стоимость возвратных отходов руб;
- основная заработная плата производственных рабочих руб;
- дополнительная заработная плата производственных рабочих руб;
- отчисления на социальные нужды руб;
- аммортизационные отчисления по оборудованию руб;
- затраты на все виды ремонта и техническое обслуживание оборудования руб;
- затраты на силовую электроэнергию руб;
- затраты на ремонт восстановление и содержание средств технологического оснащения руб;
- затраты на восстановление средств программного обеспечения станков с ЧПУ руб;
- затраты на аммортизацию ремонт и содержание производственных площадей руб.
Основная заработная плата призводственных рабочих по отдельной технологической операции:
где - штучно-калькуляционное время операции мин;
- часовая тарифная ставка станочника соответствующего разряда руб;
- количество единиц оборудования обслуживаемого одним станочником.
Дополнительная заработная плата производственных рабочих:
Отчисления на социальные нужды :
Расчет основной заработной платы производственных рабочих осуществляется в табличной форме.
Для базового технологического процесса
Таблица 5.11-Основная заработная плата производственных рабочих
Для проектируемого технологического процесса
Таблица 5.17- Основная заработная плата производственных рабочих
Аммортизационные отчисления по каждой группе оборудования используемого в технологическом процессе:
где капитальные затраты на технологическое оборудование руб;
- годовая норма аммортизации оборудования %;
- годовая программа выпуска шт.
Расчет аммортизационных отчислений осуществляется в табличной форме.
Таблица 5.12-Аммортизационные отчисления
Таблица 5.18-Аммортизационные отчисления
Затраты на все виды ремонта и техническое обслуживание оборудования:
где - количество единиц ремонтосложности оборудования;
- нормативы годовых затрат на все виды ремонта осмотра и технического обслуживания на единицу ремонтосложности оборудования.
Расчет затрат на ремонт и техническое обслуживание оборудования осуществляется в табличной форме.
Таблица 5.13-Затраты на ремонт и техническое обслуживание
Таблица 5.19-Затраты на ремонт и техническое обслуживание
Затраты на силовую электроэнергию по каждой технологической операции:
где - цена 1 кВт электроэнергии руб;
- установленная мощность электродвигателя кВт;
коэффициент учитывающий использование электродвигателя по мощности;
- коэффициент учитывающий потери электроэнергии в сети;
- КПД электродвигателя оборудования.
Расчет затрат на силовую электроэнергию осуществляется в табличной форме.
Таблица 5.14-Затраты на силовую электроэнергию
Таблица 5.20-Затраты на силовую электроэнергию
Затраты на восстановление содержание и ремонт средств технологического оснащения:
где - продолжительность выпуска детали лет;
- коэффициент учитывающий затраты на ремонт и содержание оснастки.
Расчет затрат на восстановление содержание и ремонт средств технологического оснащения осуществляется в табличной форме.
Таблица 5.15-Затраты на содержание средств технологического оснащения
Наименование типоразмеров оснастки
Таблица 5.21-Затраты на содержание средств технологического оснащения
Приспособление специальное
Затраты на восстановление средств программного обеспечения станков с ЧПУ не учитываются.
Затраты на аммортизацию ремонт и содержание производственных площадей занимаемых оборудованием:
где - норматив годовых затрат на аммортизацию ремонт и содержание производственной площади руб.
Расчет затрат на аммортизацию ремонт и содержание производственных площадей занимаемых оборудованием производится табличным методом.
Таблица 5.16-Затраты на производственные площади
Таблица 5.22-Затраты на производственные площади
Приведенные затраты на одну деталь:
где - нормативный коэффициент эффективности капитальных вложений.
Расчет технологической себестоимости для базового технологического процесса.
Затраты на основные материалы с учетом стоимости возвратных отходов:
где - масса заготовки кг;
- цена одного килограмма материала заготовок руб;
- масса готовой детали кг;
- цена одной тонны отходов руб.
Технологическая себестоимость обработки детали:
Расчет технологической себестоимости для проектируемого технологического процесса.
Годовой экономический эффект:
Рентабельность производства
Пр- прибыль от реализации руб.
- выручка от реализации руб.
- 25580руб. (По данным завода изготовителя)
Рентабельность по базовому технологическому процессу.
Рентабельность по новому технологическому процессу.
Технико-экономическая оценка
Технические показатели
Время обработки Тшт.
Затраты на оборудова-
Затраты на площади Коп.
Удельные затраты Куд.
Экономические показатели
Зарплата основных рабочих Зо
Экономический эффект Эг
На основании проведенных расчетов видно что внедряемый технологический процесс обработки детали с применением станков с ЧПУ позволяет снизить себестоимость изготовления детали высвободить занимаемые площади а также сократить количество работающих с переводом их на другую работу. На основании этого можно рекомендовать данный технологический процесс к внедрению на производстве или быть принятым в качестве типового для разработки технологических процессов на подобные детали.
Во время выполнения дипломного проекта был разработан технологический процесс изготовления корпуса. Так же проведен анализ существующих технологических процессов с целью создания более выгодного варианта. В технологической части дипломного проекта подсчитаны режимы резания и проведено нормирование операций. В экономическом разделе подсчитаны затраты на проектирование технологического процесса и годовая эффективность от внедрения данного технологического процесса по отношению к существующему. Данные расчеты показали что разработанный технологический процесс более эффективен чем существующий. Исходя из этих расчетов предлагается внедрение этого технологического процесса взамен существующего на заводе “ПЕНЗТЕКСТИЛЬМАШ”.
Справочник технолога-машиностроителя. В 2-х т. Т.1 Под ред. А.Г.Косиловой и Р.К.Мещерякова - 4-е изд.перераб. и доп.-М.: Машиностроение. 1986. - 656 с. ил.
Справочник технолога-машиностроителя. В 2-х т. Т.2 Под ред. А.Г.Косиловой и Р.К.Мещерякова - 4-е изд.перераб. и доп.-М.: Машиностроение. 1986. - 496 с. ил.
Горбацевич А.Ф.Шкред В.А. Курсовое проектирование по технологии машиностроения. - 4-е изд. перераб. и доп. - Минск. : Высшая школа. 1983. - 256 с.
Краткий справочник металиста. Под.ред. А.М.Малова - М.: Машиностроение. 1972. - 767 с.
Общемашиностроительные нормативы времени вспомогательного на обслуживание рабочего места и подготовительно-заключительного для технического нормирования станочных работ. Серийное производство: Справочник. - М.: Центральное бюро промышленных нормативов по труду. 1968. - 410 с.
Гузенков П.Г. Краткий справочник к расчетам деталей машин. - 5-е изд. изд. перераб. и доп. - М. : Высшая школа. 1983. - 256 с.
Нефедов Н.А. Осипов К.А. Сборник задач и примеров по резанию металлов и режущему инструменту. -5-е изд. изд. перераб. и доп. - М. : Машиностроение. 1990. - 448 с. ил.
Режимы резания металлов : Справочник Под. ред. Ю.В.Бароновского - 3-е изд. изд. перераб. и доп. - М. : Машиностроение. 1972. - 408 с.
Грановский Г.И. Грановский В.Г. Резание металлов. - М. : Высшая школа. 1985. - 304 с.
Иноземцев Г.Г. Проектирование металорежущих инструментов. - М.: Машиностроение . 1984. - 273 с.
Литейное производство Под. ред. И.Б.Куманина. - М. : Машиностроение. 1971. - 319 с.
Дальский А.М. Технология конструкционных материалов. - М: Машиностроение. 1977. - 664 с.
Организация и планировка машиностроительного производства. М.И.Ипатов М.К.Захарова К.А.Грачева и др.; Под. ред. М.И.Ипатова В.И.Постникова М.К.Захарова. - М. : Высшая школа. 1988. - 367 с. ил.
Стукалов В.А. Шмелев И.В. Методическое указание по выполнению организационных экономических расчетов в курсовых и дипломных проектах. - Пенза. 1976. - 130 с.
Охрана треда в машиностроении. Под. ред. Е.Я.Юдина и С.В.Белова. - М. : Машиностроение. 1983. - 382 с.
Санитарные нормы проектирования промышленных предприятий. СН 245-71. - М.: Стройиздат. 1972. - 15 с.
СНиП 4-79. Строительные нормы и правила: естественное и искуственное освещение. - М: Стройиздат. 1980. - 18 с.
Анурьев В.И. Справочник конструктора-машиностроителя. В 3-х т. Т.3 - 5-е изд. перераб. и доп.-М.: Машиностроение. 1980. - 623 с. ил.
Допуски и посадки: Справочник. В 2-х и. В.Д.Мягков М.А.Полей А.Б.Романов В.А.Брагинский - 6-е изд. перераб. и доп.-Л.: Машиностроение. Ленинградское отделение 1982. - 4.1. 543 с. ил.
Обработка металлов резанием: Справочник технолога. А.А.Панова. - М: Машиностроение. 1988. - 736 с. ил.
ГОСТ 24853-81. Калибры гладкие для размеров до 500 мм. Допуски. Введ. 1.08.91. - М: Издательство стандартов. 1991. - 9 с.
ГОСТ 26645-85. Отливки из металлов и сплавов. Допуски размеров массы и припуски на механическую обработку. Введ. 1.07.88. - М: Издательство стандартов. 1989. - 56 с.
СП2..cdw

Крышка-А4.cdw

Каф."ТМ и О" гр.00МБ1
ПГУ 1.230300.07Д ЧД1.65
Покрытие Хим. Окс. прм
Колесо червячное-А3.cdw

Каф."ТМ и О" гр.00МБ1
ПГУ 1.230300.07Д ЧД1.68
Точность отливки 10-10 по ГОСТ26645-85.
На обработанных рабочих поверхностях зубьев не допускаются
сыпь и шлаковые включения.
На обработанной поверхности отверстия допускаются
раковины диаметром более5мм.
расположенные ближе 20мм. друг от друга
Коэффициент смещения червяка
Исходный производящий червяк
Степень точности по ГОСТ3675-81
Число витков сопряженного червяка
Вид сопряженного червяка
Диаметр делительной окружности
Межосевое расстояние
Корпус-А1.cdw

ПГУ 1.230300.07Д ЧД1.63
Точность отливки 10-10 по ГОСТ26645-85.
Неуказанные литейные радиусы R 5-8vv
На обработанных рабочих поверхностях не допускаются
раковины диаметром более 6мм.
расположенные ближе 15мм. друг от друга. Допусимое количество
поверхности не более 4шт.
В резьбовых отверстиях не допускаются раковины выходящие
за пределы 2 шагов резьбы.
Покрытие необработанных поверхностенй Эмаль ПФ-115
Ступица СБ1..cdw

ПГУ 1.230300.07Д СБ1.6
* Размеры для справок
обеспечить установкой деталей поз.9.
Перед установкой подшипники поз. 15
ЦИАТИМ201 ГОСТ6267-83.
Чаша- А1.cdw

ПГУ 1.230300.07Д ЧД1.62
Точность отливки 9-9 ГОСТ26645-80.
Отливку подвергнуть старению.
* Размер для справок.
На обработанных рабочих поверхностях и поверхности Е не
допускаются раковины диаметром более 5мм.
друг от друга ближе 15мм.
поверхности. После покрытия внутренней
поверхности и прохождения температурной обработки
заделать пластмассой АСТ-Т СТУ79-56-72 с последующей
зачисткой. На обработанных нерабочих поверхностях чаши не
доускаются раковины диаметра более 8мм. и глубиной более 15%
расположенные ближе 15мм друг от друга.
Допустимое количество раковин не более 6шт. на 100см
поверхности. Раковины должны быть заварены или заделаны
шпатлевкой по ГОСТ10277-76.
В резьбовых отверстиях не допускаются раковины выходящие
за пределы дух шагов резьбы.
Внутреннию поверхность чаши обработать жидкостью
гидрофибизирующей 136-41 ГОСТЬ10834-76.
Поверхность Д покрыть Эмаль ПФ-115
Кольцо-А4.cdw

Каф."ТМ и О" гр.00МБ1
ПГУ 1.230300.07Д ЧД1.67
Покрытие Хим. Окс. прм
СП1..cdw

Кольцо уплотнительное
Кольцо компесационное
Болт М8х25.58.019 ГОСТ7805-75
Винт М8-6gх12.58.019 ГОСТ17472-80
Винт М10-6gх25.58.019 ГОСТ11773-78
Подшипник 60210 ГОСТ8338-75
Подшипник 213 ГОСТ8338-75
Подшипник 8213 ГОСТ7872-89
ПГУ 1.230300.07Д СБ1.6
ПГУ 1.230300.07Д ЧД1.61
ПГУ 1.230300.07Д ЧД1.62
ПГУ 1.230300.07Д ЧД1.63
ПГУ 1.230300.07Д ЧД1.64
ПГУ 1.230300.07Д ЧД1.65
ПГУ 1.230300.07Д ЧД1.66
ПГУ 1.230300.07Д ЧД1.67
ПГУ 1.230300.07Д ЧД1.68
ПГУ 1.230300.07Д ЧД1.69
ПГУ 1.230300.07Д ЧД1.610
Вал-А4х4.cdw

Сталь 45 ГОСТ 1050-88
Каф."ТМ и О" гр.00МБ1
* Размер для справок
Покрытие Хим. Окс. прм
СП-стойка.cdw

Каф"ТМ и О" гр.00МБ1
ПГУ 1.230.300.07 Д.СБ1.5.1
ПГУ 1.230.300.07 Д.ЧД1.5.11
ПГУ 1.230.300.07 Д.ЧД1.5.12
СП-спираль.cdw

Каф"ТМ и О" гр.00МБ1
ПГУ 1.230.300.07 Д.СБ1.5.1
ПГУ 1.230.300.07 Д.ЧД1.53
ПГУ 1.230.300.07 Д.ЧД1.54
ПГУ 1.230.300.07 Д.ЧД1.55
ПГУ 1.230.300.07 Д.ЧД1.56
ПГУ 1.230.300.07 Д.ЧД1.57
ПГУ 1.230.300.07 Д.ЧД1.58
ПГУ 1.230.300.07 Д.ЧД1.59
Осеование спирали -А2.cdw

ПГУ 1.230300.07 Д.ЧД1.54
Точность отливки 10-10 по ГОСТ26645-85.
Неуказанные литейные радиусы 2-3мм.
Неуказанные предельные отклонения угловых размеров по 10
степени точности ГОСТ8908-75.
На обработанных посадочных поверхностях не допускаются
раковины диаметром более 5мм.
расположенные ближе 20мм. друг от друга
Стойка-А2.cdw

Каф. "ТМ и О" гр.00МБ1
* Размер для справок
На каждые 100мм сварного шва допускаются газовые поры
вольфрамовые и шлаковые включения:
а)- максимальный допустимый диаметр пор и включений 3мм.
б)- допустимое минимальное расстояние между отдельными порами
в)- суммарная площадь пор и включений не более 15мм
Кроме этого допускаются отдельные участки с подрезами
мм. и протяженностью не более 15% от длины
СпиральСБ-А1.cdw

Каф "ТМ и О" гр.00МБ1
* Размер для справок
Деталь поз. 5 подогнуть при сборке.
Сварные швы по ГОСТ14806-80.
На каждые 100мм сварного шва допускаются газовые поры
вольфрамовые и шлаковые включения:
а)- максимальный допустимый диаметр пор и включений 3мм.
б)- допустимое минимальное расстояние между отдельными порами
в)- суммарная площадь пор и включений не более 15мм
Кроме этого допускаются отдельные участки с подрезами
мм. и протяженностью не более 15% от длины
Наружные поверхности дет.3 и 4 обработать жидкостью
гидрофибизирующей 136-41 ГОСТ10834-76.
Покрытие внутренних нерабочих поверхностей Эмаль МЛ-12
Плита подмоторная СБ-А3.cdw

ПГУ 1.230300.07Д СБ1.7
* Размер для справок
Сварные швы по ГОСТ5264-80
Покрытие Хим. Окс. прм
СП-воздуховод.cdw

Болт М8х30.58.019 ГОСТ7805-70
Гайка М8.5.019 ГОСТ5927-70
Шайба 8.01.019 ГОСТ11371-78
Шайба 8.65Г.029 ГОСТ6402-70
ПГУ 1.230300.07Д СБ1.1
ПГУ 1.230300.07Д СБ1.11
ПГУ 1.230300.07Д ЧД1.12
СП-плита подмоторная.cdw

ПГУ 1.230300.07Д СБ1.7
ПГУ 1.230300.07Д СБ1.71
ПГУ 1.230300.07Д СБ1.72
Корпус-А3.cdw

ПГУ 1.230300.07Д ЧД126
Точность отливки 10-10 по ГОСТ26645-85.
Неуказанные литейные радиусы R 5-8мм.
На обработанных рабочих поверхностях не допускаются
раковины диаметром более 6мм.
расположенные ближе 15мм. друг от друга. Допусимое количество
поверхности не более 4шт.
В резьбовых отверстиях не допускаются раковины выходящие за
пределы 2 шагов резьбы.
Покрытие Хим. Окс. прм
ВоздуховодСБ-А2.cdw

Шкив дет -А2.cdw

Каф."ТМ и О" гр. 00МБ1
*Размеры для справок.
Точность отливки 10-10 по ГОСТ26645-85.
Отливку подвергнуть старению.
На поверхности ручьев допускаются следы выкрашивания
графита глубиной не более 0
диаметром не более 15мм
количестве не более 5шт. на 1см
На посадчной поверхности
Н7 не допускаюся раковины
расположенные ближе 15мм
в количестве более 4шт. на 1см
Покрытие поверхностей В - Эмаль ПФ-115
желтая. ГОСТ6465-76.
Червяк А4х3.cdw

Каф."ТМ и О" гр.00МБ1
ПГУ 1.230300.07Д ЧД120
* Размер для справок
Неуказаннные радиусы галтелей R 0.5max.
Покрытие Хим. Окс. прм
Коэффициент смещения червяка
Исходный производящий червяк
Степень точности по ГОСТ3675-81
Вид сопряженного червяка
Диаметр делительной окружности
Межосевое расстояние
Направление линии витка
Болт -А4.cdw

ПГУ 1.230300.07Д ЧД125
* Размер для справок
Покрытие Хим. Окс. прм
СБ-3.cdw

СБ-2.cdw

СП-лист2.cdw

Винт М8-6gх25.58.019 ГОСТ11738-72
ПГУ 1.230300.07Д.ЧД118
ПГУ 1.230300.07Д.ЧД119
ПГУ 1.230300.07Д.ЧД120
ПГУ 1.230300.07Д.ЧД121
ПГУ 1.230300.07Д.ЧД122
ПГУ 1.230300.07Д.ЧД123
ПГУ 1.230300.07Д.ЧД124
ПГУ 1.230300.07Д.ЧД125
ПГУ 1.230300.07Д.ЧД126
ПГУ 1.230300.07Д.ЧД127
ПГУ 1.230300.07Д.ЧД128
ПГУ 1.230300.07Д.ЧД129
ПГУ 1.230300.07Д.ЧД130
ПГУ 1.230300.07Д.ЧД131
ПГУ 1.230300.07Д.ЧД132
ПГУ 1.230300.07Д.ЧД133
СП-лист1.cdw

ПГУ 1.230.300.07 Д.СП
Узел электрооборудования
ПГУ 1.230300.07Д СБ1
ПГУ 1.230300.07Д СБ1.1
ПГУ 1.230300.07Д СБ1.2
ПГУ 1.230300.07Д СБ1.3
ПГУ 1.230300.07Д СБ1.4
ПГУ 1.230300.07Д СБ1.5
ПГУ 1.230300.07Д СБ1.6
ПГУ 1.230300.07Д СБ1.7
ПГУ 1.230300.07Д СБ1.8
ПГУ 1.230300.07Д.ЧД110
ПГУ 1.230300.07Д.ЧД111
ПГУ 1.230300.07Д.ЧД112
ПГУ 1.230300.07Д.ЧД113
ПГУ 1.230300.07Д.ЧД114
ПГУ 1.230300.07Д.ЧД115
ПГУ 1.230300.07Д.ЧД116
ПГУ 1.230300.07Д.ЧД117
СБ-4.cdw

СП-лист3.cdw

Манжета 1.1-30х52-4 ГОСТ8752-79
Подипник 7306 ГОСТ333-79
Шплинт 4х25-05 ГОСТ397-36
Ремень А-1180 ГОСТ1284.1-89
Электродвигатель 4АМ80А4У3
СБ-1.cdw

Каф."ТМ и О" гр.00МБ1
* Размер для справок
Перпендикулярный зазор между кромкой спирали и внутренней
конической поверхностью чаши не должен превышать 0
вертикальный зазор между спиралью и верхней кромкой чащи не
При сборке поверхность Б герметезировать герметиком.
В редуктор залить масло индустриальное И-40А ГОСТ20799-85
с добавлением присадки АКОР-1 ГОСТ15171-78 в количестве 15% в
соответствии с ГОСТ9.014-78.
Подшипники перед установкой смазать смазкой ЦИАТИМ-201
Остальные технические требования по ТУ6-10-1000-80.
Рис.6.cdw

Назначение изделия-1.doc
1 Анализ объекта разработки литературных и производственных данных постановка задач проектирования
1.1 Назначение изделия
Тестоокруглительная машина предназначена для улучшения структуры заделки поверхностных пор и придания тестовым заготовкам из пшеничной муки поступающим из тесторазделочной машины круглой формы.
Применяется на предприятиях хлебопекарной промышленности.
1.2 Патентные исследования
Анализируя конструкторские решения оборудования для получения тестовых заготовок проводим патентный анализ по отечественным и зарубежным образцам глубиной поисков не менее 5 лет.
Агрегат для замеса полуфабрикатов хлебопекарного производства.
Изобретение относится к пищевой промышленности и может быть использовано в хлебопекарном и кондитерском производстве.
Цель изобретения – устранение потерь муки и уменьшение пыления при загрузки тестомесильной машины.
На рисунке 1.1 изображен предлагаемый агрегат.
Агрегат содержит последовательно соединенные трубопровод 1 для подачи муки автомукомер 2 тестомесильную машину 3 и параллельно подключенные к ней дозаторы 4 жидких компонентов.Тестомесильная машина 3 герметично соединена по средством байпасного воздуховода 5 с трубопроводом 1 для подачи муки.
Агрегат работает следующим образом.
Мука по трубопроводу 1 подается в автомукомер 2 в котором производится отвешивание заданной порции после чего мука подается в тестомесильную машину 3.
Туда же подаются из дозаторов 4 жидкие компоненты. При подаче муки в емкость тестомесильной машины мучная пыль вместе с потоком воздуха увлекается по байпасному воздуховоду 5 в трубопровод 1 откуда с подаваемой мукой снова попадает автомукомер 2.
Формула изобретения.
Агрегат для замеса полуфабрикатов хлебопекарного производства содержащий последовательно соединенные трубопровод для подачи муки автомукомер тестомесильную машину и параллельно подключенные к ней дозаторы жидких компонентов отличающийся тем что с целью устранения потерь муки и уменьшения пыления при загрузке тестомесильной машины тестомесильная машина герметично соединена по средством байпасного воздуховода с трубопроводом для подачи муки.
Тестомесильная машина периодического действия.
Изобретении относится к оборудованию для хлебопекарного и кондитерского производства а именно к машинам для порционного замеса теста.
Цель изобретения – повышение проиводительности машины и снижение энергозатрат на замес.
На рисунке 1.2 изображена тестомесильная машина периодического действия.
Тестомесильная машина периодического действия содержит корпус 1 привод 2 с выходным валом 3 и не подвижную дежу 4. На валу закреплена петлеобразная месильная лопасть 5.
Наибольший линейный размер поперечного сечения лопасти 5 в направление перемещения лопасти больше наибольшего линейного размера того же сечения. Тестомесильная машина работает следующим образом.
Вал 3 привода 2 вместе с лопастью 5 совершает вращательное движение вокруг своей оси и одновременно перемещается вокруг главной оси привода. При этом из загруженных в дежу сухих и жидких компонентов замешивается тесто однородное по консистенции и влажности.
Предлагаемая форма поперечного сечения лопасти позволяет ликвидировать распыл муки и увеличить коэффициент дежи т.е. производительность.
Устройство для приготовления дрожжевого сыпучего полуфабриката теста.
Изобретение относится к пищевой промышленности и может быть использовано в технологических линиях по производству хлебопекарных изделий.
Цель изобретения – повышение качества продукта.
На рисунке 1.3 изображено предлагаемое устройство.
Устройство содержит камеру 1 смещения в виде усеченного конуса в верхней части которой размещен шнек 2 установленный с возможностью планетарного движения. Устройство дополнительно снабжено закрепленной на валу 3 шнека 2 винтовой лопастью 4 размещенной в нижней части камеры 1. При этом отношение длины шнека 2 к высоте лопасти 4 и длине камеры 1 соответственно составляет 2 – 25 и 06 – 08.
Устройство работает следующим образом.
При вращении шнека 2 вокруг своей оси происходит перемещения материала вверх вдоль внутренней стенки камеры 1 и последующее разбрасывание его в свободном объеме камеры. Орбитальное движение шнека 2 обеспечивает горизонтально – круговое движение продукта в камере 1 который ссыпается в ее нижнюю часть под действием сил тяжести. Винтовая лопасть 4 закрепленная на валу 3 вращается синхронно шнеку 2 и обеспечивает перемещение материала вверх где он подхватывается шнеком 2 транспортируется вверх и вновь ссыпается в нижнюю часть камеры 1 под действием сил тяжести. В результате этого предотвращается слеживаемость материала и сохраняется жизнедеятельность дрожжевых клеток что приводит к улучшению качества дрожжевого сыпучего полуфабриката теста.
Устройство для приготовления дрожжевого сыпучего полуфабриката теста содержащее камеру смешения в виде усеченного конуса в верхней части которой размещен шнек установленный с возможностью планетарного движения отличающееся тем что с целью повышения качества продукта оно дополнительно снабжено закрепляемой но валу шнека винтовой лопастью размещенной в нижней части камеры смещения при этом отношение длины шнека к высоте винтовой лопасти и к длине образующей камеры соответственно составляет 2 – 25 и 06 – 08.
Устройство для формирования круглых заготовок из теста.
Изобретение относится к бытовой технике в частности к устройствам для формирования круглых заготовок из теста.
Цель изобретения – расширение технологических возможностей и удобства использования (рисунок 1.4).
Один из дополнительных корпусов с лезвием устанавливают на одном из винтов первым лезвием обращенным от разделительной прокладки а остальные корпуса при свинчивании винтов образуют рукоятку устройство устанавливается на раскатанное тесто лезвием дополнительного корпуса. К рукоятке прикладывается от руки осевое усилие с поворотом устройства вокруг его оси. При необходимости получить заготовку другого диаметра корпуса с лезвиями меняются местами.
Устройство для формирования круглых заготовок из теста включающее корпус с лезвием и рукоятку отличающееся тем что с целью расширения технологических возможностей и удобства пользования оно снабжено дополнительными корпусами с лезвиями рукоятка образована с помощью соединенных между собой винтов укрепленных на последних разделительных прокладок а дополнительные корпуса установлены на рукоятке лезвиями обращенными к разделительной прокладке.
Устройством наиболее полно раскрывающим стоящую перед проектированием задачу является
Устройство для формирования тестовых заготовок тонкосортного хлеба.
Изобретение относится к хлебопекарной промышленности в частности к производству национальных сортов хлеба.
Цель изобретения – повышение качества изделий путем обеспечения равномерной по толщине заготовок. На рисунке 1.5 изображено устройство.
Устройство для формирования тестовых заготовок тонкосортного хлеба состоит из бункера 1 нагнетателя 2 с приводом экструзионной щели 3в которой с возможностью возвратно – поступательного движения установлены приводные шиберы 4и 5 с пальцами 6 и 7 для регулирования ширины щели 3.Нагнетатель 2 включает поршень 8 со штоком 9 и пружиной 10.Привод включает кулачек 11 для взаимодействия со штоком 9при этом привод шиберов 4 и 5 содержит пространственный кулак 12 который по средством валов 1314 и конической передачи 15 кинематически связан с кулачком 11.
При вращении пространственного кулачка 12 посредством пальцев 6 и 7 перемещаются шиберы 4 и 5 перекрывая щель 3.Одновременно через валы 13 и 14 и передачу 15 приводится во вращение кулачек 11 который перемещает поршень 8 нагнетателя 2.При этом тесто подается из бункера 1 через щель 3 приобретая вид заготовки заданной толщины.
Устройство для формования тестовых заготовок тонкосортного хлеба содержащее бункер нагнетатель с приводом экструционную щель в которой с возможностью возвратно – поступательного перемещения установлены приводные шиберы для регулирования ширины щели отличающееся тем что с целью повышения качества изделий путем обеспечения равномерной толщины заготовок нагнетатель выполнен в виде поршня а его привод включает кулачек для взаимодействия со штоком поршня при этом привод шиберов содержит пространственный кулак и кинематически связан с кулачком нагнетателя.
1.3 Технические требования предъявленные к конструкции машины
Технические характеристики изделия приведены в таблице 1.1.
Таблица 1.1 – Технические характеристики тестоокруглительной машины
Наименование параметра
Техническая производительность шт.мин.
Пределы массы тестовых заготовок кг
Частота вращения чаши обмин
Высота до места загрузки мм
Установленная мощность кВт не более
Габаритные размеры мм не более
Занимаемая площадь м2 не более
1.4 Технологический процесс реализуемый машиной
Заготовки из теста по промежуточному транспортеру от тестоделительной машины поступают к тестоокруглительной машине и сбрасываются на начальную часть спирали. Вращающейся чашей тестовая заготовка захватывается и направляется по желобу образованному между внутренней конической поверхностью чаши и наружной поверхностью спирали. Вращаясь в разных направлениях тестовая заготовка зажатая между стенками желоба проминается и за счет трения увлекается вверх по желобу принимая форму шара. При выходе из чаши округленная тестовая заготовка направляется на последующие технологические операции.
1.5 Устройство тестоокруглительной машины
Основными частями тестоокруглительной машины (рисунок 1.6) являются:
-основание с приводом 1
-механизм фиксации и регулировки положения спирали 4 (рисунок 1.8)
-электрооборудование 6
-Основание с приводом (рисунок 1.7) состоит из литого чугунного корпуса 7 электродвигателя 8 связанного клиноременной передачей 9 с червячным колесом 10 и червяком 11; ступицы 12 свободно посаженной на шарикоподшипниках на неподвижную ось 13.
-Электродвигатель установлен на плите 14 которая посредством двух болтов 15 и гаек 16 может наклоняться вокруг оси 17 увеличивая или уменьшая межцентровое расстояние клиноременной передачи регулируя этим натяжение клинового ремня.
-В передаче предусмотрены двухступенчатые шкивы 18 и 19 что позволяет перестановкой ремней получать две скорости вращения чаши.
-Червяк 11 (рисунок 1.7) установлен в корпусе 7 на двух роликовых конических подшипниках осевой люфт в подшипниках выбирается с помощью поджимного болта 21.
-В зацеплении с червяком находится колесо червячное 10 жестко закрепленное на ступице 12; ступица на двух радиальных и одном упорном шарикоподшипниках вращается на вертикально установленной в корпусе неподвижной оси 13.
Червячная пара привода работает в масляной ванне.
Для заливки и спуска масла в нижней части корпуса имеется устройство в котором имеются отверстия: для заливки масла закрытое крышкой и спускное отверстие закрытое пробкой. Верхний уровень масла Н1 в картере контролируется пазом имеющимся в крышке через который вытекает лишнее залитое масло а нижний уровень должен быть в пределах нижней точки паза Н2.
-Все крышки корпуса 7 установлены на уплотняющих прокладках для исключения возможности протекания масла находящегося в камере.
-Вся нижняя часть машины где расположен привод ограждена с двух противоположных сторон откидывающимися дверками на петлях которые сблокированы с приводом машины: при открывании дверок электродвигатель привода отключается и запуск его возможен только при закрытом ограждении.
-К верхнему фланцу ступицы 12 болтами прикреплена коническая чаша
Внутри чаши на неподвижную вертикальную ось 13 свободно насажена спираль 3 которая образует с внутренней поверхностью чаши желоб с изменяющимся к выходу углом наклона.
Механизм фиксации и регулировки положения спирали (рисунок 1.9)
-Верхняя часть спирали 3 закрыта крышкой 22 в которую завинчен винт 24 опирающийся на шарик 25 вложенный в углубление имеющемся на торце оси 13.
При завинчивании винта 23 спираль перемещается в осевом направлении поднимаясь или опускаясь относительно оси 13 создавая необходимый зазор между внутренней поверхностью чаши и кромкой спирали.
В верхней части оси 13 установлен диск 24 имеющий двенадцать расположенных по кругу отверстий. В крышке 22 запрессован фиксатор 25 который находясь в одном из отверстий диска 24 удерживает спираль от поворота.
При необходимости изменить положение спирали надо поднять ее до выхода фиксатора из отверстия в диске развернуть до необходимого положения и опустить попадая фиксатором в одно из отверстий диска. После чего установив необходимый зазор между внутренней поверхностью чаши и спиралью затянуть контргайку 26.
Неправильная регулировка зазора между внутренней поверхностью чаши и спиралью является причиной некачественного округления тестовых заготовок.
Спираль должна быть установлена с минимальным зазором по конической поверхности чаши.
Увеличение зазора свыше 045 мм ведет к отщипыванию кусочков теста касание спирали вращающейся чаши ведет к загрязнению тестовых заготовок.
Также необходимо следить за правильной установкой тестоокруглителя относительно устройства подающего заготовку. Вводимая заготовка должна попадать на начальную часть спирали. При попадании заготовки на дно чаши или основание стойки спирали происходит залипание заготовки и затягивание ее под спираль. В этом случае тестоокруглитель необходимо развернуть или повернуть спираль как указано выше.
Для предотвращения прилипания теста к рабочим органам и качественного округления тестовых заготовок необходимо производить подачу воздуха в зону формирования заготовок. Рекомендуемая температура подаваемого воздуха 30±5°С расход 2000 м3 ч.
Для этого на кронштейне установленном на крышке спирали и закрепленном колпаком имеются два воздуховода 5 через которые осуществляется соединение с общезаводской воздушной магистралью.
Кронштейн с укрепленными на нем воздуховодами может поворачиваться вокруг оси чаши сами воздуховоды перемещаются на кронштейне с помощью имеющихся в них пазов.
-Электрооборудование 6 обеспечивает управление электроприводом машины. Шкаф управления должен обеспечивать степень защиты не ниже IP42 по ГОСТ 14254-96 (МЭК 529 -89). Степень защиты электродвигателя и кнопочного поста должна быть не ниже IР44 по ГОСТ 14254- 96.
Вся электроаппаратура кроме кнопки управления SB1 блокировочного конечного выключателя SQ установлена на панели управления питание ко всему электрооборудованию подается через вводный пакетный выключатель QF. По окончании работы на машине его следует отключить чтобы снять напряжение со всего электрооборудования. Нулевая защита электропривода обеспечивается за счет самоблокировки магнитного пускателя КМ. Управление электроприводом производится при помощи кнопок «ПУСК» «СТОП» SB1 SB2. Предусмотрена блокировка электропривода с дверкой закрывающей вращающиеся части машины. При открывании дверки освобождается конечный выключатель SQ и размыкается цепь катушки пускателя КМ. В результате чего останавливается приводной электродвигатель М. Питание цепей управления осуществляется безопасным пониженным напряжением 36 В от понижающего трансформатора Т 22036 В а защита цепей управления плавкой вставкой предохранителя F4.
1.6 Подготовка к работе
Перед включением тестоокруглительной машины необходимо:
- проверить надежность закрепления крепежных соединений;
- проверить натяжение клинового ремня привода;
- провести внешний осмотр электродвигателя и электрической проводки;
- проверить наличие заземления;
- проверить систему обдува воздухом рабочих органов машины (надежность крепления воздуховодов);
- проверить рабочую зону (чашу и спираль) на наличие посторонних предметов;
- проверить зазор между конической поверхностью чаши и кромкой спирали (зазор должен быть не более 045 мм);
- проверить правильность затяжки роликоподшипников червяка и - проверить закрыты ли дверки ограждения;
- смазать машину согласно карты смазки
Включение тестоокруглительной машины производится в следующем порядке:
-произвести внешний осмотр изделия;
-после кратковременного включения электродвигателя (с целью проверки правильности вращения чаши) произвести запуск машины окончательно;
-подключить систему подачи воздуха.
При достижении конической чашей округлителя установившейся скорости вращения включить тесторазделочную машину.
1.7 Обслуживание и регулировка во время работы
Тестоокруглительная машина требует периодического наблюдения одного рабочего.
Во время работы машины необходимо:
-периодически следить за состоянием поверхностей рабочих органов. При необходимости остановить машину и очистить их.
Для остановки машины сначала нужно выключить тестоделитель а затем после выработки заготовок находящихся в тестоокруглительной машине выключить ее.
Во время остановки машины необходимо:
-очистить поверхность чаши тестоокруглительной машины скребком из алюминия ГОСТ21631 –76 толщиной 23 мм а через каждые 500 часов работы проводить чистку боковых стенок и дна чаши при максимально поднятой или снятой спирали;
-очистить и протереть сухой ветошью спираль тестоокруглительной машины;
-проверить натяжение ремня клиноременной передачи;
кромкой спирали он не должен превышать 045 мм. Зазор регулируется вращением винта расположенным в верхней части машины под съемным колпаком. Зазор контролируется щупом.
По мере необходимости с помощью перестановки клинового ремня на двухступенчатых шкивах с одного ручья на другой меняется частота вращения чаши: для обработки тестовых заготовок от 022 до 05 кг следует устанавливать большую частоту вращения чаши. Для этого ремень следует установить на ступенях шкивов: диаметром 130 мм – на электродвигателе;
диаметром 153 мм – на червяке. На развес от 05 до 12 кг частоту вращения чаши уменьшить. Для этого ремень следует переставить соответственно на ступени шкивов: диаметром 98 мм и диаметром 180 мм
При длительной эксплуатации машины возможен износ червячной пары требующий дополнительной регулировки и наладки:
-при замене червячного колеса необходимо обеспечить соосность его с червяком. Установку нормального зацепления следует производить с помощью индикаторного приспособления;
-осевой люфт червяка необходимо выбрать поджимая болт установленный в крышке редуктора и зафиксировать контргайкой
- при износе спирали когда не возможно обеспечить зазор между внутренней поверхностью чаши и кромкой спирали менее 045 мм заменить спираль новой
1.8 Техническое обслуживание
При ежедневном техническом осмотре необходимо:
-проверить натяжение клинового ремня;
-проверить щупом величину зазора между внутренней поверхностью
чаши и кромкой спирали;
-проверить работу блокирующего устройства;
-периодически производить чистку чаши и спирали
При еженедельном техническом осмотре:
-проверить крепление электродвигателя;
-проверить люфт червяка.
При техническом осмотре не менее 1 раза в 3 месяца:
-проверить уровень масла в картере;
-проверить состояние электродвигателя и электрооборудования;
-проверить червячное зацепление.
Не реже 1 раза в год проводить профилактический ремонт который включает в себя разборку и чистку деталей смену масла в корпусе редуктора промывку и смазку шарикоподшипников согласно карты смазки и замену изношенных деталей.
Таблица 1.2 – Карта смазки
Наименование смазываемой точки
Наименование и марка смазочного материала
Способ внесения смазочного материала
Периодичность смазки
Норма расхода смазочного материала на год кг
Подшипники ступицы и спирали
ЦИАТИМ-201 ГОСТ 6267-
ЦИАТИМ-203 ГОСТ 8773-
Корпус (подшипники червяка и червячного зацепления)
Масло индустриальное И-40А ГОСТ 20799-75
1.9 Возможные неисправности
Возможные неисправности тестоокруглительной машины и способы их устранения приведены в таблице 1.3.
Таблица 1.3 - Возможные неисправности тестоокруглительной машины
Тесто прилипает к поверхностям рабочих органов
Повышенная влажность теста.
Переброженное тесто.
Увеличен зазор между внутренней поверхностью чаши и кромкой спирали.
Недостаточный обдув воздухом.
Подавать нормальное тесто.
Отрегулировать зазор.
Увеличить подачу воздуха.
Отщипывание кусочков теста при округлении заготовки
Сдваивание тестовых заготовок при округлении
Неравномерное поступление тестовых заготовок.
Обеспечить равномерное поступление заготовок.
Машина не включается
Сработала блокировка на дверке закрывающей вращающиеся части машины.
Сработало тепловое реле.
Проверить напряжение на входе и выходе трансформатора.
Проверить предохранители.
Проверить и включить тепловое реле.
2 Разработка конструкции основных узлов объекта
2.1 Расчет основных конструктивных элементов
Исходные данные для расчета:
Необходимая частота вращения чаши n=50-60 мин
Выходная мощность на приводном валу Рвых=075 кВт
Примем следующую кинематическую схему привода (рисунок 1.10)
2.2 Необходимые параметры электродвигателя привода
пк - КПД подшипников качения; пк=099
чп - КПД червячной передачи; чп=08
рп - КПД ременной передачи; рп=095
Рэл.тр.=0750737=102 кВт
Необходимая частота вращения электродвигателя
Uчп –передаточное число червячной передачи;Uчп - (16 50)
Uрп - передаточное число ременной передачи Uрп - (2 4)
nэл=(50 65)(16 50)(2 4)=1600 13000 мин
Принимаем электродвигатель марки 4АМ80А4У3
Мощность электродвигателя N=11 кВт
Число оборотов n=1420 мин
Передаточное число привода
Примем передаточное число ременной передачи
Тогда передаточное число червячной передачи
Находим частоту вращения
n2=nэлUрп=1420155=916 мин
n3=n2Uчп=91619=482 мин
Находим передаваемые моменты
2.3 Расчет клиноременной передачи
Тип сечения ремня в зависимости от передаваемой мощности (N=11кВт) и при окружной скорости (до 5 мс) принимаем «А».
длина по средней линии bр=11 мм
площадь сечения F=81 мм
Межосевое расстояние принимаем Аw=375 мм
Диаметр ведущего шкива принимаем D1=984 мм
Диаметр ведомого шкива:
Принимаем D2=1524 мм
Находим необходимую длину ремня:
По ГОСТ1284.1-75 принимаем Lp=1120 мм
Находим необходимое число ремней в передачи:
Находим скорость ремня:
Число пробегов в секунду:
Исходя из полученного значения принимаем значение предварительного натяжения
Значение коэффициента Ко в зависимости от о и D1 принимаем Ко=165 Нмм2
Сα – коэффициент учитывающий влияние угла обхвата
α1 - угол обхвата ведущего шкива;
С - коэффициент учитывающий влияние скорости
Ср - коэффициент учитывающий режим работы
Р – окружное усилие Н
Принимаем в передачи 1 ремень.
Найдем расчетную долговечность ремня:
y – предел выносливости; yНмм2
ρ – плотность материала; ρ=12·103 кгм3
v=12·10-3·732·10-6=006 Нмм2
Eu – модуль упругости; Е=65Нмм2
max=258+006+528=792 Нмм2
m – показатель степени для клиновых ремней m=8
Сi – коэффициент учитывающий передаточное отношение Сi=135
Cн - коэффициент учитывающий не постоянство работы Cн=1
Что вполне достаточно.
Сила давления на валы
2.4 Расчет червячной передачи
Определим предварительную скорость скольжения:
n2 – число оборотов червяка; n2=916 мин-1
Т3 – крутящий момент на вале червячного колеса; Т3=162 Н·м
Исходя из полученной скорости скольжения для изготовления червячного колеса применим оловянную бронзу марки БрОЦ5-5 по ГОСТ613-79.
Предел прочности в=210 МПа
Предел текучести т=100 МПа
Допускаемые напряжения.
Контактные напряжения:
Материал для изготовления червяка примем Сталь 45 по ГОСТ1050-88;
Зубья червяка – 45 50HRC.
Число витков червяка Z1 принимаем в зависимости от передаточного отношения Uчп ; т.к. Uчп=19 следовательно Z1=2.
Число зубьев червячного колеса Z2=
Предварительное межосевое расстояние:
- предварительный коэффициент нагрузки.
Исходя из конструктивных значений межосевое значение червячной передачи примем dw=120 мм.
Значение коэффициента диаметра червяка q=10 мм
Осевой модуль передачи m=5 мм
Коэффициент смещения x=0
Находим угол подъема витков червяка
Проверка зубьев по контактным напряжениям.
Расчетное контактное напряжение
- коэффициент нагрузки;
Расчет геометрических параметров.
Делительный диаметр:
Диаметр вершин витков:
Диаметр впадин витков:
Длину нарезанной части червяка принимаем в=130 мм.
Диаметр делительной окружности:
Диаметр окружной вершины зубьев:
Диаметр окружности впадин зубьев:
Проверка зубьев по напряжениям изгиба:
коэффициент нагрузки
коэффициент формы зуба
Условие по напряжениям изгиба выполнено.
Находим силы которые действуют в зацеплении (рисунок 1.11).
Окружная сила на колесе:
Окружная сила на червяке:
Осевая сила на колесе:
Осевая сила на червяке:
2.5 Расчет вала червяка
Подшипник выбираем роликовый конический однорядный №7306 по
ГОСТ 333 – 79 (рисунок 1.12).
Частота вращения вала п- 916 мин-1;
Крутящий момент Т – 109 Нм;
Определение реакций опор (рисунок 1.13):
Суммарные реакции опор:
2.6 Подбор подшипников качения для вала червяка
Для вала червяка выбираем подшипники роликовые конические однорядные средней серии №7306 – 79.
Схема установки подшипников в “распор” (рисунок 1.14).
Необходимый ресурс подшипников Ln=5000 ч. (гарантийный срок работы).
Значение коэффициентов:
Находим значение осевых составляющих:
Следовательно осевые силы:
V – коэффициент вращения: 10
Находим эквивалентную динамическую нагрузку:
коэффициент безопасности: 14
коэффициент температурный: 10
Как видно из расчетов наиболее нагруженная опора “Б”.
Дальнейший расчет ведется по ней.
Расчетная долговечность подшипника:
коэффициент учитывающий свойства материала деталей
коэффициент степени: 103
выбранный подшипник удовлетворяет необходимому условию.
2.7 Проверка опасного сечения вала – червяка
Наиболее опасное сечение вала находится в опоре “Б” под подшипником.
Исходные данные для расчета.
Изгибающий момент в опасном сечении Mmax=60 Нм
Диаметр вала в опасном сечении dв=30 мм
Материал вала – сталь 45;
Предел прочности в – 900 МПа
Проверим вал на статическую прочность.
Коэффициент запаса прочности:
коэффициент запаса: 25
эквивалентное напряжение
осевой момент сопротивления
Условие по статической прочности выполнено.
Проверка опасного сечения вала на сопротивление усталости:
коэффициент запаса по нормальным напряжениям
коэффициент запаса по касательным напряжениям;
амплитуда напряжений цикла в опасном сечении;
полярный момент сопротивления
пределы выносливости вала в опасном сечении;
коэффициент шероховатости: 115;
коэффициент поверхностного упрочнения: 10;
Условие по сопротивлению усталости выдержано.
Проверка шпоночного соединения (рисунок 1.15).
Проверка шпоночного соединения «вал – шкив»
Шпонка фиксирующая шкив – 6×6×36.
- рабочая длина шпонки;
h – высота шпонки; h=6мм
t1 – глубина паза; t1=35мм
d – диаметр вала; d=22мм
Т – крутящий момент; Т=109Н·м
Выбранное шпоночное соединение удовлетворяет условию.
патенты Рис.1.1.cdw

Автомукомер 5. Воздуховод
Тестомесильная машина
Рисунок 1.1 - Агрегат для замеса полуфабрикатов
хлебопекарного производства
Пятая часть-1переправл.doc
Целью данного дипломного проекта является разработка технологического процесса изготовления корпуса и средств его оснащения.
Назначение спроектированного технологического процесса - изготовление корпуса заданной точности и качества в количестве не менее 500 штук в год.
Данный технологический процесс разработан на базе существующего технологического процесса который был предназначен для выпуска даного изделия в условиях массового производства. Поскольку годовая программа выпуска была уменьшена в несколько раз то возникла необходимость модернизации существующего технологического процесса с целью сокращения штучного времени изготовления детали и ее себестоимости. Для этого стали применяться станки с числовым программным управлением (ЧПУ) и специальные приспособления для уменьшения времени базирования закрепления и снятия заготовки.
Снижение штучного времени изготовления детали повлекло за собой снижение затрат на инструмент аммортизацию оборудования электроэнергию и т.д. что в свою очередь скажется на снижении себестоимости изделия.
Целью технико-экономических расчетов в дипломном проекте является решение вопросов сетевого планирования расчет затрат на проектирование технологического процесса и оценка экономической эффективности технологического процесса.
1 Расчет затрат на проектирование технологического процесса
Затраты на проектирование технологического процесса представляют собой стоимостную оценку использованных в процессе проектирования сырья материалов покупных комплектующих изделий и полуфабрикатов расходов на приобретение специального оборудования оплату труда занятых разработкой технологического процесса затраты по работам выполненным сторонними организациями и др.
Затраты на проектирование данного технологического процесса определяются по формуле:
В стоимость сырья и материалов включается стоимость использованного в процессе разработки данного технологического процесса сырья основных и вспомогательных материалов необходимых для проведения исследований экспериментов опытов испытаний и т. П.
В данном случае затраты на сырье и материалы включают в себя затраты на изготовление заготовок для проведения экспериментальных работ.
Стоимость сырья и материалов:
где - стоимость одной тонны заготовок руб;
- масса заготовки кг;
- коэффициенты зависящие от класса точностигруппы сложности массы марки материала и объема производства заготовок;
- цена одной тонны отходов руб;
- количество заготовок.
В состав основной заработной платы включаются выплты за фактически выполненную работу в соответствии с окладами тарифными ставками и расценками всему персоналу принимавшему участие в разработке данного технологического процесса: научным работникам
инженерно-техническим работникам лаборантам рабочим и служащим исследовательских и проектных подразделений рабочим экспериментальных и опытных цехов и др.
Расчет основной заработной платы осуществляется в табличной форме и сведем в таблицу 5.1.
Таблица 5.1-Рсчет основной заработной платы
Инженер III категории
Инженер II категории
Расточник VI разряда
Фрезеровщик VI разряда
В состав дополнительной заработной платы разработчиков включаются все виды выплат надбавок и доплат из фонда заработной платы за проработанное и непроработанное время (надбавки за профессиональное мастерство доплаты за условия труда работу в ночную смену выплаты отпускных вознаграждение за выслугу лет и др.).
Дополнительная заработная плата рассчитывается по формуле:
где - коэффициент дополнительной заработной платы.
Коэффициент дополнительной заработной платы устанавливается в каждой конкретной организации по данным базового или планового периода на основе сложившегося отношения между фондом дополнительной заработной платы и фондом основной заработной платы разработчиков в целом по проектной организации.
Отчисления на социальные нужды рассчитываются по формуле:
- коэффициент отчислений на социальные нужды.
Коэффициент отчислений на социальные нужды в настоящее время составляет 26% и включает в себя:
В состав накладных расходов включаются затраты на аммортизацию ремонт и содержание зданий и других основных производственных фондов общего назначения содержание аппарата управления проектной организации почтово-телеграфные и канцелярские расходы налоги сборы и т. д.
Накладные расходы определяются по формуле:
- коэффициент накладных расходов.
Коэффициент накладных расходов берется по данным конкретной роектной организации. Он определяется по базовым или плановым данным в конкретной организации исходя из сложившегося соотношения сметы накладных расходов организации и фондов основной заработной платы персонала организации.
Все расчеты затрат на проектирование технологического процесса сведем в таблицу 5.2.
Таблица 5.2-Затраты на проектирование технологического процесса
Наименование статей расхода
Основная заработная плата разработчиков технологического процесса
Дополнительная заработная плата разработчиков технологического процесса
Отчисления на социальные нужды
Итого затраты на проектирование
Цены на разработку устанавливаются на основе договора между заказчиком и исполнителем т.е. устанавливается так называемая договорная цена.
Для экономических расчетов и прогнозов цену на разработку экономически целесообразно устанавливать на основе прогнозируемого уровня рентабельности.
В этом случае цена вместе с налогом на добавленную стоимость (НДС) может быть рассчитана по формуле:
- установленный или прогнозируемый уровень рентабельности %; =15-25%
- налог на добавленную стоимость %. =18%
2 Оценка экономической эффективности технологического процесса
Итоговым экономическим расчетом в организационно-экономическом разделе дипломного проекта является оценка экономической эффективности спроектированного технологического процесса.
На этапе разработки нового технологического процесса может быть рассчитан лишь его предварительный экономический эффект который носит потенциальный характер. Обусловлено это невозможностью на этапе разработки технологического процесса с достаточной степенью достоверности выявить для расчета реального эффекта всю совокупность факторов оказывающих влияние на состав и уровень эффекта от разработки и применения технологического процесса характерных для данного объекта внедрения разработанного нового технологического процесса.
Поэтому основной целью оценки экономической эффективности технологического процесса на этапе его разработки является не столько расчет неких абсолютных значений его эффективности сколько обеспечение соответствующих руководителей объективной достоверной и достаточной информацией для принятия или непринятия решения о разработке и применении нового технологического процесса.
2.1 Расчет капитальных вложений
При оценке экономической эффективности технологического процесса на этапе его разработки полные капитальные вложения могут быть рассчитаны по формуле:
- затраты на проектирование технологического процесса руб;
- затраты на технологическое оборудование руб;
- затраты на средства технологического оснащения руб;
- стоимость производственных площадей занимаемых оборудованием руб;
- cтоимость средств программного обеспечения для станков с ЧПУ руб.
Капитальные затраты на проектирование технологического процесса рассчитываются лишь для нового варианта и рассчитаны выше
Капитальные затраты на технологическое оборудование:
- коэффициент учитывающий расходы на транспортировку и монтаж оборудования;
- число групп оборудования;
- наименование группы оборудования;
- принятое число единиц оборудования;
- цена единиц оборудования руб;
- коэффициент учитывающий занятость оборудования.
Расчетное количество единиц оборудования:
- годовая программа запуска шт.
- штучно-калькуляционное время обработки деталей на - той группе оборудования мин;
- действительный годовой фонд времени работ единиц оборудования час;
- средний коэффициент выполнения норм;
- коэффициент учитывающий неизбежные потери времени.
Расчет количества оборудования осуществляется в табличной форме.
Коэффициент занятости оборудования:
Капитальные затраты на средства технологического оснащения:
- наименование типоразмера оснастки необходимой для обработки деталей данного наименования на всех операциях технологического процесса;
- количество типоразмеров оснастки необходимой для выполнения всех операций технологического процесса обработки деталей данного наименования;
- цена единицы оснастки руб;
- количество единиц оснастки;
- коэффициент занятости оснастки. При использовании специальной оснастки рассчитанной на обработку деталей только одного наименования . В остальных случаях:
Капитальные затраты на производственные площади занимаемые технологическим оборудованием:
- производственная площадь занимаемая единицей оборудования ;
- коэффициент учитывающий дополнительную площадь;
- цена 1 производственной площади руб.
Капитальные затраты на средства программного обеспечения для станков с ЧПУ учитываются лишь для тех средств программного обеспечения стоимость которых за единицу превышает 1000 руб. и берется по фактическим данным.
Удельные капитальные вложения:
Расчет капитальных вложений для базового технологического процесса.
Расчет количества оборудования сведем в таблицу 5.3.
Таблица 5.3-Количество оборудования в базовом технологическом процессе
Горизонтально-расточная с ЧПУ
Вертикально-фрезерная с ЧПУ
Радиально-сверлильная
Капитальные затраты на производственные площади:
Полные капитальные вложения:
Расчет капитальных вложений для проектируемого технологического процесса
Расчет количества оборудования сведем в таблицу 5.4.
Таблица 5.4-Количество оборудования в проектируемом технологическом процессе
Сверлильно-фрезерно-расточная с ЧПУ
Фрезерно-сверлильно-расточная с ЧПУ
2.2 Расчет технологической себестоимости
Технологическая себестоимость обработки детали - это сово
купность затрат лишь непосредственно связанных с технологическим процессом ее изготовления.
Технологическая себестоимость обработки детали может быть рассчитана по формуле:
- затраты на основные материалы руб;
- стоимость возвратных отходов руб;
- основная заработная плата производственных рабочих руб;
- дополнительная заработная плата производственных рабочих руб;
- отчисления на социальные нужды руб;
- аммортизационные отчисления по оборудованию руб;
- затраты на все виды ремонта и техническое обслуживание оборудования руб;
- затраты на силовую электроэнергию руб;
- затраты на ремонт восстановление и содержание средств технологического оснащения руб;
- затраты на восстановление средств программного обеспечения станков с ЧПУ руб;
- затраты на аммортизацию ремонт и содержание производственных площадей руб.
Основная заработная плата призводственных рабочих по отдельной технологической операции:
- штучно-калькуляционное время операции мин;
- часовая тарифная ставка станочника соответствующего разряда руб;
- количество единиц оборудования обслуживаемого одним станочником.
Дополнительная заработная плата производственных рабочих:
- коэффициент дополнительной заработной платы.
Отчисления на социальные нужды :
Расчет основной заработной платы производственных рабочих осуществляется в табличной форме.
Для базового технологического процесса
Таблица 5.5 - Основная заработная плата производственных рабочих
Для проектируемого технологического процесса
Таблица 5.6 - Основная заработная плата производственных рабочих
Аммортизационные отчисления по каждой группе оборудования используемого в технологическом процессе:
капитальные затраты на технологическое оборудование руб;
- годовая норма аммортизации оборудования %;
- годовая программа выпуска шт.
Расчет аммортизационных отчислений осуществляется в табличной форме.
Таблица 5.7 - Амортизационные отчисления
Таблица 5.8 - Амортизационные отчисления
Затраты на все виды ремонта и техническое обслуживание оборудования:
- количество единиц ремонтосложности оборудования;
- нормативы годовых затрат на все виды ремонта осмотра и технического обслуживания на единицу ремонтосложности оборудования.
Расчет затрат на ремонт и техническое обслуживание оборудования осуществляется в табличной форме.
Таблица 5.9 - Затраты на ремонт и техническое обслуживание
Таблица 5.10 - Затраты на ремонт и техническое обслуживание
Затраты на силовую электроэнергию по каждой технологической операции:
- цена 1 кВт электроэнергии руб;
- установленная мощность электродвигателя кВт;
коэффициент учитывающий использование электродвигателя по мощности;
- коэффициент учитывающий потери электроэнергии в сети;
- КПД электродвигателя оборудования.
Расчет затрат на силовую электроэнергию осуществляется в табличной форме.
Таблица 5.11 - Затраты на силовую электроэнергию
Таблица 5.12 - Затраты на силовую электроэнергию
Затраты на восстановление содержание и ремонт средств технологического оснащения:
- продолжительность выпуска детали лет;
- коэффициент учитывающий затраты на ремонт и содержание оснастки.
Расчет затрат на восстановление содержание и ремонт средств технологического оснащения осуществляется в табличной форме.
Таблица 5.13-Затраты на содержание средств технологического оснащения
Наименование типоразмеров оснастки
Таблица 5.14 - Затраты на содержание средств технологического оснащения
Приспособление специальное
Затраты на восстановление средств программного обеспечения станков с ЧПУ не учитываются.
Затраты на аммортизацию ремонт и содержание производственных площадей занимаемых оборудованием:
- норматив годовых затрат на аммортизацию ремонт и содержание производственной площади руб.
Расчет затрат на аммортизацию ремонт и содержание производственных площадей занимаемых оборудованием производится табличным методом.
Таблица 5.15 - Затраты на производственные площади
Таблица 5.16 - Затраты на производственные площади
Приведенные затраты на одну деталь:
- нормативный коэффициент эффективности капитальных вложений.
Расчет технологической себестоимости для базового технологического процесса.
Затраты на основные материалы с учетом стоимости возвратных отходов:
- цена одного килограмма материала заготовок руб;
- масса готовой детали кг;
- цена одной тонны отходов руб.
Технологическая себестоимость обработки детали:
Расчет технологической себестоимости для проектируемого технологического процесса.
Годовой экономический эффект:
Рентабельность производства
Пр- прибыль от реализации руб.
- выручка от реализации руб.
- 5085 руб. (По данным завода изготовителя)
Рентабельность по базовому технологическому процессу.
Рентабельность по новому технологическому процессу.
Таблица 5.17 - Технико-экономическая оценка
Технические показатели
Программа выпуска Nв
Время обработки Тшт.
Затраты на оборудова-
Затраты на площади Коп.
Удельные затраты Куд.
Экономические показатели
Зарплата основных рабочих Зо
Экономический эффект Эг
На основании проведенных расчетов видно что внедряемый технологический процесс обработки детали с применением станков с ЧПУ позволяет снизить себестоимость изготовления детали высвободить занимаемые площади а также сократить количество работающих с переводом их на другую работу. На основании этого можно рекомендовать данный технологический процесс к внедрению на производстве или быть принятым в качестве типового для разработки технологических процессов на подобные детали.
патенты рис 1,5.cdw

Экструзионная щель 12. Пространственный кулак
Пальци шиберов 15. Коническая передача
Рисунок 1.5 - Устройство для формирования тестовых заготовок
Уступомер.cdw

ПГУ 1.230300.07Д ВО1
Каф."БМ и П" гр.00МБ1
Покрытие: Хим. Окс. прм.
кроме рабочих поверхностей.
Меритель.spw

Меритель пр.spw

Винт М6-6gх10.58.019 ГОСТ14776-75
Винт М6-6gх12.58.019 ГОСТ14776-75
Винт В1М3-6gх12.58.019 ГОСТ 17475-80
Пробка.cdw

Меритель пр.cdw

ПГУ 1.230300.07Д СБ4
Каф."БМ и П" гр.00МБ1
Порядок сборки сухарей поз. 6 с фиксатором поз. 4: пружина поз.10
одевается на сухарь поз. 6 и заводится в отверстие фиксатора
поз.4. С другой стороны сухарь фиксируется зажимом. После
установки всех сухарей
ввинчивается винт поз.5
устанавливается крышка поз.7 и крепится винтами поз.13. Затем
снимаются зажимы и освобождаются сухари.
Меритель.cdw

от перпендикулярности отв.
Каф."БМ и П" гр.00МБ1
ПГУ 1.230300.07Д СБ5
Отклонение от перпендикулярности поверхности А относительно
поверхности Б не более 0
Наладка унив-1.cdw

Продольно-фрезерный 4-х шпиндельный станок мод. 6Г610
одновременно с верхней
Операция 035. Продольно-фрезерная.
Каф.БМ и П" гр.00МБ1
ПГУ 1.230300.07Д ТН1
Наладки ЧПУ 1лист-1.cdw

Оборудование: Сверлильно-фрезерно-расточной станок модели 21105Н7Ф4
Схема инструментальной
Фрезеровать наружный диа-
Фрезеровать внутреннию поверх-
ность 2 по программе
Фрезеровать канавку 3
Фрезеровать канавку 5 окон-
чательно по программе
Фрезеровать поверхность
бобышки 6 по программе
Фрезеровать канавку 4 пред-
варительно по программе
Каф."БМ и П" гр.00МБ1
ПГУ 1.230300.07Д ТН2
Инструментальный переход 10
Инструментальный переход 4
Инструментальный переход 8
Инструментальный переход 12
Наладки ЧПУ 3лист-3.cdw

Сверлильно-фрезерно-расточной станок модели 21105Н7Ф4
Сверлить 3 отверстия 14
Нарезать резьбу 18 в 2
отверстиях по программе
Сверлить 2 отверстия 15
Сверлить 2 отверстия 16
Нарезать резьбу 17 в 10
Каф."БМ и П" гр.00МБ1
ПГУ 1.230300.07Д ТН4
Наладки ЧПУ 2лист-2.cdw

Сверлильно-фрезерно-расточной станок модели 21105Н7Ф4
Сверлить отверстие 8
Зенкеровать отверстие 9
Расточить отверстие 10
Фрезеровать платики 11
Центровать отверстия 12
Сверлить отверстия 13
Каф."БМ и П" гр.00МБ1
ПГУ 1.230300.07Д ТН3
КЭ17.cdw

КЭ20.cdw

КЭ2.cdw

КЭ30.cdw

КЭ13.cdw

КЭ22.cdw

КЭ25.cdw

КЭ27.cdw

КЭ29.cdw

КЭ5.5.cdw

КЭ4.cdw

КЭ10.cdw

КЭ11.cdw

КЭ1.cdw

КЭ8.cdw

КЭ21.cdw

КЭ18.cdw

КЭ4.4.cdw

КЭ28.cdw

КЭ14.cdw

КЭ31.cdw

КЭ15.cdw

КЭ5.cdw

КЭ23.cdw

КЭ19.cdw

кэ1.1.cdw

КЭ6.cdw

КЭ26.cdw

КЭ24.cdw

КЭ16.cdw

КЭ7.cdw

КЭ 2.2.cdw

КЭ9.cdw

КЭ3.cdw

МК3.cdw

Код. наименование оборудования
Обозначение документа
ГОСТ 3.1118082 Форма 1б
сб.единицы или материала
ИОТ N 91 Сборник типовых инструкций Москва Недра 1978
Продольно-фрезерный 4-х
шпиндельный станок 6Г610
ИОТ N 67 Сборник типовых инструкций Москва Недра 1978
Установить заготовку в тиски пневматические
Фрезеровать боковую поверхность
оправка В-11390-000000
фреза 2214-0001 ГОСТ 24359-80; Штангенциркуль ШЦ-III-500-0
t=5 мм; S=208 мммин; V=63 ммин; n=40 обмин
Установить деталь на магнитный стол
Шлифовать верхнюю поверхность
Плоскошлифовальный станок
t=5 мм; S=153 мммин; V=59 ммин; n=75 обмин
МК10.cdw

Код. наименование оборудования
Обозначение документа
ГОСТ 3.1118082 Форма 1б
сб.единицы или материала
Установить заготовку в тиски пневматические
Зенкеровать отверстие по программе выдерживая размер 37
Расточить отверстие начерно по программе выдерживая размер 38
Расточить отверстие начисто с получением фаски по программе выдерживая размеры 39
ммоб; V=25 ммин; n=100 обмин
Сверлить 4 отверстия под резьбу М8 по программе выдерживая размеры 41
и 43 согласно эскизу
Нарезать резьбу М8 по программе выдерживая размеры 44
ммоб; V=10 ммин; n=400 обмин
МК1.cdw

Код. наименование операции
Код. наименование оборудования
Обозначение документа
По отдельному техпроцессу
ИОТ N 87; 84 Сборник типовых инструкций Москва Недра 1978
Зачистить полости от формовочной земли и наплывов металла
ИОТ N 91 Сборник типовых инструкций Москва Недра 1978
ИОТ N 67 Сборник типовых инструкций Москва Недра 1978
Продольно-фрезерный 4-х
шпиндельный станок 6Г610
Контролировать качество отливки
МК5.cdw

Код. наименование оборудования
Обозначение документа
ГОСТ 3.1118082 Форма 1б
сб.единицы или материала
ИОТ N 91 Сборник типовых инструкций Москва Недра 1978
ИОТ N 67 Сборник типовых инструкций Москва Недра 1978
Установить заготовку в тиски пневматические
Фрезеровать по программе выдерживая размеры 10
притупить острые кромки
станок с ЧПУ 21105Н7Ф4
Вертикально-сверлильно-
t=4 мм; S=120 мммин; V=15
Фрезеровать по программе выдерживая размер 12
t=1 мм; S=93 мммин; V=48
МК6.cdw

Код. наименование оборудования
Обозначение документа
ГОСТ 3.1118082 Форма 1б
сб.единицы или материала
Фрезеровать предварительно сальниковую канавкцу по программе выдерживая размеры 16
Фрезеровать окончательно сальниковую канавкцу по программе выдерживая размеры 19
Фрезеровать бобышку по программе выдерживая размер 22
t=4 мм; S=252 мммин; V=22
t=2 мм; S=429 мммин; V=27 ммин; n=1430 обмин
Сверлить отверстие по программе выдерживая размер 23
Фрезеровать канавку по программе выдерживая размер 13
МК7.cdw

Код. наименование оборудования
Обозначение документа
ГОСТ 3.1118082 Форма 1б
сб.единицы или материала
Расточить отверстие по программе выдерживая размер 25
Фрезеровать платики по программе выдерживая размеры 26
Центровать отверстия по программе выдерживая размер 28
Сверлить три отверстия по программе выдерживая размер 29
Сверлить отверстия под резьбу М8 по программе выдерживая размеры 30
t=4 мм; S=552 мммин; V=72 ммин; n=460 обмин
Зенкеровать отверстие по программе выдерживая размер 24
МК13.cdw

Код. наименование оборудования
Обозначение документа
ГОСТ 3.1118082 Форма 1б
сб.единицы или материала
По отдельному техпроцессу
ИОТ N 87;84 Сборник типовых инструкций
Вытряхнуть стружку из корпуса
притупить острые кромки
проверить все ли места обработаны
доработать отверстия
удалить поломанные метчики
ИОТ N 91 Сборник типовых инструкций Москва Недра 1978
МК8.cdw

Код. наименование оборудования
Обозначение документа
ГОСТ 3.1118082 Форма 1б
сб.единицы или материала
Сверлить два отверстия по программе выдерживая размер 32
Сверлить отверстия под резьбу М12 по программе выдерживая размеры 33
Нарезать резьбу М8 по программе выдерживая размер 35
ммоб; V=10 ммин; n=400 обмин
ммоб; V=12 ммин; n=320 обмин
Нарезать резьбу М12 по программе выдерживая размер 36
фреза 2223-0555 ГОСТ 20538-75; фреза специальная; фреза 2234-0205 ВК8 ГОСТ 16463-80;
фреза специальная; сверло 2300-7515 ГОСТ 10902-77; сверло 2301-0189 ГОСТ 10903-77;
сверло 2300-3001 ГОСТ 10902-77; сверло 2301-0400 ГОСТ 10903-77; сверло двухступенчатое специальное
метчик 2640-0081 ГОСТ 1604-71; метчик 2640-0153 ГОСТ 1604-71;
МК11.cdw

Код. наименование оборудования
Обозначение документа
ГОСТ 3.1118082 Форма 1б
сб.единицы или материала
Фрезеровать поверхность по программе выдерживая размер 46
t=5 мм; S=153 мммин; V=59 ммин; n=40 обмин
Сверлить 2 отверстия под резьбу М8 по программе выдерживая размеры 47
и 49 согласно эскизу
Нарезать резьбу М8 по программе выдерживая размеры 50
Зенкеровать отверстие по программе выдерживая размер 52
Расточить отверстие начерно по программе выдерживая размер 53
ммоб; V=10 ммин; n=400 обмин
МК2.cdw

Код. наименование оборудования
Обозначение документа
ГОСТ 3.1118082 Форма 1б
сб.единицы или материала
Установить заготовку в тиски пневматические
ИОТ N 91 Сборник типовых инструкций Москва Недра 1978
Фрезеровать одновременно верхнюю поверхность и две боковые
выдерживая размеры 1
оправка В-11390-000000
фреза 2214-0157 ГОСТ 24359-80
фреза 2214-0001 ГОСТ 24359-80;
Штангенциркуль ШЦ-III-500-0
ГОСТ 166-80; Штангенрейсмасс ШР 40-400-0
t=5 мм; S=208 мммин; V=63 ммин; n=40 обмин
Продольно-фрезерный 4-х
шпиндельный станок 6Г610
ИОТ N 67 Сборник типовых инструкций Москва Недра 1978
выдерживая размеры 4
фреза 2214-0001 ГОСТ 24359-80; Штангенциркуль ШЦ-III-500-0
Штангенрейсмасс ШР 40-400-0
t=5 мм; S=153 мммин; V=59 ммин; n=75 обмин
МК.cdw

Зав. кафедрой "БМ и П
Разработчик: Вантеев Е.С.
Руководитель: Лобачев В.В.
ГОСТ 3.1118-82 форма 1
МК4.cdw

Код. наименование оборудования
Обозначение документа
ГОСТ 3.1118082 Форма 1б
сб.единицы или материала
ИОТ N 91 Сборник типовых инструкций Москва Недра 1978
Шлифовальный круг ПП500х305х100 52С40ПСМ26К2 мс 2 кл. ГОСТ 2424-75;
Штангенрейсмасс ШР 40-400-0
ГОСТ 164-80; Щуп №2 кл.2 ГОСТ 882-75
Вертикально-фрезерная
Вертикально-фрезерный
ИОТ N 67 Сборник типовых инструкций Москва Недра 1978
Установить заготовку в тиски пневматические
Фрезеровать поверхность
оправка В-11390-000000
фреза 2214-0001 ГОСТ 24359-80; Штангенциркуль ШЦ-I-125-0
ИОТ N 87; 84 Сборник типовых инструкций Москва Недра 1978
МК9.cdw

Код. наименование оборудования
Обозначение документа
ГОСТ 3.1118082 Форма 1б
сб.единицы или материала
ИОТ N 91 Сборник типовых инструкций Москва Недра 1978
ИОТ N 87; 84 Сборник типовых инструкций Москва Недра 1978
притупить острые кромки
Пробка 8133-0962 Н7 ГОСТ 14810-69; Штангенциркуль ШЦ-III-400-0
ГОСТ 166-80; шаблон специальный; шаблон специальный
меритель на перпендикулярность специальный; калибр пробка специальная; приспособление специальное мерительное
оправка В-4055-00000; зенкер специальный; резец 2142-0144 ГОСТ 9795-73; Штангенциркуль ШЦ-I-125-0
Пробка 8221-3036-7Н ГОСТ 17758-72; Пробка 8221-3053-7Н ГОСТ 17758-72.
Горизонтально-фрезерно-
сверлильно-расточной
станок с ЧПУ 6906ВМР2
ИОТ N 67 Сборник типовых инструкций Москва Недра 1978
МК12.cdw

Код. наименование оборудования
Обозначение документа
ГОСТ 3.1118082 Форма 1б
сб.единицы или материала
Расточить отверстие начисто с получением фаски по программе выдерживая размеры 54
Сверлить 4 отверстия под резьбу М8 по программе выдерживая размеры 56
и 58 согласно эскизу
Нарезать резьбу М8 по программе выдерживая размеры 59
ммоб; V=25 ммин; n=100 обмин
ммоб; V=10 ммин; n=400 обмин
Сверло 2301-3001 ГОСТ 10903-77; зенкер специальный
резец расточной специальный; сверло комбинированное
специальное; метчик 2620-1223 ГОСТ 3266-81; фреза 2214-0005 ГОСТ 24359-80; Штангенциркуль ШЦ-I-125-0
ГОСТ 166-80; Штангенциркуль ШЦ-III-400-0
ГОСТ 166-80; пробка 8221-3036-7Н ГОСТ 17758-72;
пробка 8136-0110Н7 ГОСТ 14815-69; приспособление специальное; индикатор ИЧ02 кл.0 ГОСТ 577-68.
Приспособление-1.cdw

фрезерно-расточной станок
ПГУ 1.230300.07Д СБ3
Каф."БМ и П" гр.00МБ1
Технические требования
Неперпендикулярность поверхности А относительно
поверхности Б не более 0
Техническая характеристика
Давление в пневмосети
Приспособление-1.spw

фрезерно-расточной станок
Винт М10 х 35.56 ГОСТ 11738-84
Гайка М24.56 ГОСТ 5916-70
Пневмораспределитель
крановый В71-23М-02-УХЛ4
ТУ 4151-002-00221287-96
Шайба 10.65Г ГОСТ 6402-70
Штифт 2.10 х 50 ГОСТ 3128-70
Тиски пневматические поворотные-1.cdw

ПГУ 1.230300.07Д СБ2
Технические требования
ставить на смазке ЦИАТИМ-201 ГОСТ6267-74.
Поршень поз.3 должен двигаться в цилиндре поз.6 плавно
Техническая характеристика
Давление в пневмосети
Тиски-1.spw

Болт М12 х 40.56.019 ГОСТ 7798-70
Винт М10 х 30.56.019 ГОСТ 1491-80
Винт М12 х 40.56.019 ГОСТ 11738-84
Винт М20 х 60.56.019 ГОСТ 11738-84
Гайка М20.5.019 ГОСТ 5915-70
Кольцо 080-092-50-2-4 ГОСТ 18829-73
Шайба 10.01.019 ГОСТ 11371-72
Шайба 20.01.019 ГОСТ 11371-72
Корпус (диплом).cdw

Каф."ТМ и О" гр.00МБ1
В резьбовых отверстиях не допускаются раковины
пределы двух шагов резьбы.
На обработанных посадочных поверхностях не допускаются
друг к другу в количестве более четырех на 1000мм поверхности.
Покрытие наружных необработанных поверхностей-эмаль ПФ-115
желтая ГОСТ 6465-76; внутренних необработанных
поверхностей-эмаль ПФ-115
красная ГОСТ 6465-76.
Корпус (диплом)отливка.cdw

Каф."ТМ и О" гр.00МБ1
Отливка 3-й группы ГОСТ 977-88. Точность отливки 10-6-14-10
Неуказанные литейные радиусы 5 8 мм.
Формовочные уклоны не более 3
Корпус (диплом)отливка2.cdw

Корпус (диплом)2.cdw

Сверло-1.cdw

ПГУ 1.230300.07Д ВО4
Стружечные канавки и подточки полировать Ra 0
Твердость рабочей части 55 60HRC
Покрытие профиля режущей части: Х6 9
Сверло-зенкер1.cdw

Каф."БМ и П" гр.00МБ1
ПГУ 1.230300.07Д ВО5
Материал: режущейй части-пластина С32-ВК6 ГОСТ 25395-82;
корпуса-сталь 40Х ГОСТ 4543-71.
Зенкер должен иметь на длине пластины только равномернуую
обратную конусность не более 0
Радиальное биение по ленточкам на всей рабочей части
зенкера относительно оси хвостовика не более 0
главных режущих кромок не более 0
Фреза дисковая.cdw

ПГУ 1.230300.07Д ВО3
Материпал: Реущей части - пластинка 61351(ВК8) ГОСТ5395-82
сталь 45 ГОСТ1050-88.
Число зубьев z = 10.
Радиальное биение главных режущих кромок относительно оси отвеостия двух
смежных зубьев не более 0.05мм.
двух противоположных зубьев не более 0.1мм.
Торцевое биение режущих кромок не более 0.001 мм.
Рис.7.cdw

ПАТЕНТЫ РИС 1.4.cdw

сыпучего полуфабриката теста
Рис.10.cdw

Рисунок 1.1 - Кинематическая схема привода
Рис.5.cdw

Рис.8.cdw

ПАТЕНТЫ РИС 1.3.cdw

Дополнительные корпуса
Рисунок 1.3 - Устройство для формирования круглых
патенты Рис.1.2.cdw

Рисунок 1.2. - Тестомесильная машина периодического действия
Рекомендуемые чертежи
- 24.01.2023
- 30.08.2014
- 29.07.2014