Technology of construction of a three-storey brick building


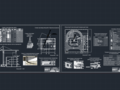
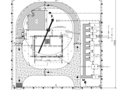
- Added: 04.04.2022
- Size: 4 MB
- Downloads: 2
Description
Course project on the discipline "Technology of construction of buildings" on the topic "TECHNOLOGY OF CONSTRUCTION OF THREE-STOREY
BRICK BUILDING"
The technological map was developed for brickwork and installation of precast concrete structures of a 3-storey residential building, the dimensions in the axes of which are 17.2 x 12.6 m.
The following works should be considered in the technological map:
- brickwork of external brick walls;
- masonry of internal brick walls;
- laying of lintels;
- installation of precast concrete elements with related works.
Project's Content
![]() ![]() ![]() ![]() |
![]() ![]() ![]() |
Additional information
Contents
Introduction
SECTION 1. JOB INSTRUCTION
1.1 Scope of application
1.2 Process Technology and Organization
1.2.1 Method of installation works
1.2.2 Method of transportation of structures to construction site
1.2.3 Conformity of design (materials) to the project
1.2.4 Methods of storage, pre-layout
1.2.5 Method of structure slinging and its arrangement before installation
1.2.6 Diagram of organization of works during erection of brick building
1.2.7 Features of brick walls
1.2.8 Instructions for the production of masonry
1.2.9 Instructions for installation of floor slabs
1.2.10 Instructions for installation of staircases
1.2.11 Instructions for installation of stair flights
1.2.12 Strap Mounting Instructions
1.2.13 Organization and methods of labor of workers
1.3 Requirements for quality and acceptance of works
1.4 Calculation of labor costs for construction of multi-storey brick residential building
1.5 Calculation of labor costs for the construction of a typical floor
1.6 Logistical resources
1.7 Technical and economic parameters of Job Instruction
1.8 Occupational safety
SECTION 2. Construction Site Organization
2.1 Selection of tower construction crane
2.1.1 Calculation of required parameters of tower crane and their selection
2.1.2 Anchoring of crane towers
2.1.3 Determination of crane impact zones
2.2 Selection of main machines and mechanisms
2.3 Layout of the object construction plan
2.4 Calculation of requirements for temporary buildings and structures
2.5 Calculation of storage areas
2.6 Calculation of water demand
2.7 Calculation of Electricity Demand
2.8 Calculation of construction site lighting requirements
2.9 Calculation of compressed air demand
2.10 Technical and economic indicators
2.11 Labor protection, fire protection measures at the construction site and environmental protection
2.11.1 For cranes and mechanization of works
2.11.2 On Roads and Pedestrian Routes (Traffic Diagram)
2.11.3 By power grids (between TP and building - 15-20 m)
2.11.4 By water supply networks
2.11.5 For temporary administrative and economic buildings and household structures
2.11.6 Fire Safety
2.11.7 Fire fighting measures
2.11.8 Ensuring electrical safety
2.11.9 Environmental protection
LIST OF LITERATURE
Introduction
Capital construction is one of the most important branches of material production. Capital construction includes new construction, expansion, reconstruction and technical re-equipment of existing enterprises, buildings and structures.
One of the capital construction systems is construction production - a set of production processes carried out directly on the construction site, including construction and installation and special processes during the preparatory and main construction periods.
The end result of a set of production processes is construction products, which mean individual parts of the facilities under construction, as well as completed buildings and structures.
Construction production combines two subsystems: technology and organization of construction production, each of which has its own essence and scientific basis.
Technology is a set of methods of processing, manufacturing, changing the state, properties, shape, raw materials, material or semi-finished product carried out in the process of production of construction products .
The technology of construction production, in turn, is a combination of two subsystems: the technology of construction processes and the technology of erection of buildings and structures .
The technology of construction processes defines the theoretical foundations, methods and methods of performing construction processes that ensure the treatment of building materials, semi-finished products and structures with a qualitative change in their condition, physical and mechanical properties, geometric dimensions in order to obtain products of a given quality. At the same time, the concept of "method" includes the principles of performing construction processes based on various methods of influencing labor objects using tools .
The technology of erection of buildings and structures defines theoretical foundations and regulations for practical implementation of certain types of construction, installation and special works, their interconnection in space and time in order to obtain finished products in the form of buildings and structures.
Process design of construction includes:
construction organization projects (PIC);
Work Execution Projects (WP);
routines for complex construction processes;
Labour process maps
process diagrams of operations execution.
In this course project, a process plan for the construction of a brick building is being developed. The use of the Job Instruction contributes to the better organization of construction processes, maximum reduction of manual labor, achievement of the greatest efficiency in the performance of construction and installation works, as well as reduction of the terms of preparation of the WP.
Section 1. routing
Scope of Application
The process map was developed for brickwork and installation of prefabricated reinforced concrete structures of a 3-story residential building, the dimensions in the axes of which are 17.2 x 12.6 m.
The following works shall be considered in the Job Instruction:
- brickwork of external brick walls;
- masonry of internal brick walls;
- lintel laying;
- installation of prefabricated reinforced concrete elements with associated works.
1.2 Process Technology and Organization
1.2.1 Method of installation works
Installation methods should be selected on the basis of technological and structural features of the building, as well as technical equipment of the construction and installation organization, taking into account modern methods of installation work, which allow to increase quality and speed, as well as reduce the cost of installation .
Depending on the installation sequence, the following methods shall be used:
differentiated (sequential);
parallel and mixed.
For brick buildings, a mixed method should be used, in which individual processes proceed sequentially, the main in parallel. In addition, you must select several construction flows, determined by the number of installation cranes.
The construction of a brick building is carried out by several flows.
To ensure maximum reduction of labour intensity of construction and installation works, it is necessary to select the correct method of works execution and to select a set of construction machines and other means of mechanization. When choosing the type and capacity of construction machines, they are based on the scope of work and the conditions for their execution, which determines the technological parameters of the machines. When choosing the methods of work and types of construction machines, it is necessary to be guided by considerations of economic expediency .
Selection of rational (optimal) method of production of main construction and installation works for specific construction conditions is made on the basis of comparison according to technological and technical and economic parameters of several versions of the works considered as part of the project.
Key estimates include cost, labour and duration.
The construction of the facility is divided into two periods: preparatory and main. The on-site works of the preparatory period include works related to the development of the construction site and ensuring a normal start, and the development of the main construction period, including:
creation by the customer of a control geodetic network (red lines, benchmarks, main axes of the building, reference construction grid );
development of the construction site (clearance of the territory, demolition of buildings );
engineering preparation of the site (planning of the territory with organization of surface water runoff, installation of permanent or temporary roads, transfer of existing networks and installation of new ones to supply construction with water and electricity );
arrangement of temporary facilities ;
device of communication means for construction control.
The main period of construction of a residential building should be planned in three cycles, each of which consists of a certain complex of work .
The first cycle is the construction of the underground part of the house. Installation of basement structures should be considered the leading process. To reduce the duration of construction, the house is divided into grabs. The object is divided into captures. This allows you to explode work and organize it in-line .
All work related to the construction of the underground part should begin with the development of the pit. Use the Volvo EC170D excavator to dig a technical underground pit. Part of the soil required for backfilling of the foundation sinuses from the outside is laid in a dump, the rest of the soil is taken away on dump trucks. Installation of prefabricated foundations is carried out simultaneously with manual soil mining and sand bed filling. For installation of foundation blocks, basement walls and floor slabs above the technical underground use MKG40 boom crane .
In addition to the main work on the installation of structures, work should be carried out on the arrangement of horizontal insulation, waterproofing of walls, the arrangement of releases and inputs of communications.
The arrangement of outlets and inputs of communications (sewage, drainage, water supply, heating, gas supply, power supply, telephonisation, dispatch communication) is provided before filling the sinuses of the pit from the outside .
Pit sinks shall be filled outside after installation and welding of the floor. For backfilling, the Komatsu D65EX16 bulldozer is used, and the compaction is carried out by the DU rink 62. Arrange the paving immediately after backfilling.
An excavating method of complex mechanization of earthworks is expedient, since the versatility of single-bucket excavators, as well as the possibility of their work with various modes of transport, make it possible to apply this method to soils of various groups.
The selection of a set of machines is made on the basis of a mechanized volume of earthworks with loading on dump trucks and in a dump.
Use a Volvo EC170D excavator and a 153 kW Komatsu D65EX16 bulldozer to extract and move soil.
For transportation of soil the automatic dump truck MAZ555102 is selected. Soil leveling is carried out by the Komatsu D65EX16 bulldozer. Use Komatsu PW2007 replaceable equipment for soil tillage. The Komatsu D65EX16 bulldozer must be selected to clean and plan the ground. Use DC62 vibration roll with power of 30 kW for soil compaction.
Based on the excavator ladle capacity - 0.63 m3; load capacity of dump trucks - 10.7 tons.
The second cycle - the construction of the above-ground part of the building includes: the construction of the above-ground part of the house with related work, civil work, special work.
The leading process of this cycle is the installation and masonry of the structures of the aboveground part of the house. It is divided into grips, the value of which is taken to be equal to the floor of the house.
The basis for the construction of multi-section buildings regardless of their design, it is necessary to lay down the following technological principles: installation of structures with several parallel flows using several tower cranes; combined with installation of subsequent civil and special works. In this case, the building needs to be divided into two sections, and each section, in turn, into grabs.
Construction works combined with installation of structures should be carried out simultaneously in two sections, but at other stages and grips.
When compiling the schedule, in addition to purely installation work, it is necessary to take into account the supply to the floor of various component materials and parts - prefabricated elements of ventilation ducts and garbage ducts, electric panels, heating devices, billets of pipe wiring. In parallel with the installation of structures, work is underway to build fences for stairs and balconies. With a lag of 1-2 floors, plan civil work.
Design of production of special works - sanitary and wiring - is carried out in coordination with general construction and finishing. Special works are performed in parallel in two stages:
Stage I - up to plaster work with one to two floors behind the installation. The works are planned by grips with a step equal to the rhythm of the floor installation ;
Stage II - on the cycles of readiness of painting work (does not coincide for sanitary and electrical works). Completion of all special works corresponds to completion dates. The work of this stage is performed, as a rule, outside the flow - without division by grips;
The first stage of sanitary works includes installation of internal cold and hot water supply, heating and gas supply systems. In winter, additional work is envisaged on the installation of temporary systems for heating the decked floors;
Phase II of sanitary works begins after the first cycle of painting works, when the preparation for the last painting is completed in sanitary units and kitchens, which opens the front for the installation of sanitary equipment. All sanitary works are performed by one team, which does not exclude internal specialization (link for assembly of sewage cast iron pipelines, link for welding of steel pipes).
The first stage of electrical installation works includes: marking of routes, punching and drilling of sockets, stem and furrow, laying of risers, pipes and hoses for hidden wiring, laying of wires with partial sealing in walls and in preparation for floors, installation of junction boxes, floor cabinets and boards, etc.;
The II stage of electrical and low-current works begins after painting the ceilings and ends after gluing (painting) the walls. Work at this stage is carried out outside the flow without division by grips. After painting - "opening" of ceilings in apartments, suspension of cartridges and lamps is performed. Following the gluing or painting of the walls, switches, sockets, calls, placings are installed. Upon completion of finishing works, low-current wiring of radio broadcasting communication and fire alarm is performed in the house. As a rule, both high-current and low-current works perform the same links, but in conditions of high concentration of construction, low-current devices mount specialized organizations .
Lifting works are performed by specialized subcontracting organizations. Tubing elevators are installed by a complex team mounting the house. Elevator assembly fitters begin to reconcile the elements and install the elevator units during the installation of the upper floors in time to ensure the timely completion of work. The beginning of these works in 6 storeys falls on the end of the assembly of seven floors. Alignment of elements and installation of elevator units is carried out on grips, free from installation of house structures in the subsequent period.
The third cycle is the production of finishing work in a residential building. Plaster works in brick buildings shall be performed by specialized teams (links) of finishing CS. Depending on the deadlines and the availability of labor, plasterers must occupy the entire front of work at once or perform work in-line, taking the floor of the house as a grab and moving in a step equal to the installation of the floor. Tile work must be performed in the same cycle as plaster .
Finishing work should be carried out on all floors simultaneously, with a breakdown into two stages. At the I stage, cover and paint ceilings, paint loggia, balconies, external slopes of windows, prepare for lining with wallpaper and paint walls and carpentry .
The flooring of the parquet and linoleum with the device of plinths can be started after the last wet process - "opening the ceilings" and, like painting work, performed outside the stream. As these works are completed, the front is opened for the II stage of painting work .
At the second stage of finishing works one performs lining with wallpaper, painting of walls and carpentry .
The combination of plaster and tile, painting and parquet, painting and special works is achieved by separating the front of work within the section, floor and even apartment.
Performing painting work, broken down into grips by stages, is impractical.
1.2.2 Method of transportation of structures to construction site
Delivery to the object of the brick must be carried out in packages in specially equipped on-board machines, while they must be carefully strengthened in order to protect against overturning of longitudinal and transverse displacement. Packages shall be supported by wooden inventory gaskets and liners .
Installation of prefabricated elements on vehicles shall be carried out taking into account the following requirements :
the elements shall be in a position close to the design;
The elements shall be supported by wooden inventory gaskets and liners located in the places indicated in the working drawings. The thickness of the gasket and lining shall be not less than 25 mm and not less than the height of the hinges of other protruding parts ;
In multi-level transport, the liners and gaskets must be placed strictly along the same vertical ;
the elements must be carefully strengthened to prevent the longitudinal and transverse displacement from overturning.
The solution is delivered by solvents and discharged to a solution mixing and dispensing unit (dispenser bin).
1.2.3 Conformity of design (materials) to the project
Ceramic bricks coming to the installation site shall be in accordance with the design, valid GOST, each batch shall be provided with a quality certificate.
1.2.4 Methods of storage, pre-layout
The necessary stock of structures in the warehouse must be established by the Production Works Project (PDP) taking into account the installation schedule .
On average, the stock of structures should contain at least five days of demand for them.
When storing structures in an object warehouse, it is necessary to:
The storage site shall be carefully leveled and planned;
lay out the prefabricated elements and place the stacks in the area of the installation crane, taking into account the sequence of their installation ;
structures having a large mass should be located in the vicinity of the crane;
store the prefabricated elements under conditions preventing their deformation and contamination;
the passages between the stacks in the longitudinal direction should be located through every two adjacent stacks, and in the transverse direction not less than after 25 m. The width of the passages should be at least 0.7 m, and the gaps between the stacks should be at least 0.2 m ;
place the structural elements so that their factory marking on the side of the passage or passage is visible;
cover plates shall be stored in stacks in horizontal position.
Accepts the designs of the mounting organization .
External inspection shall check compliance of the face surface of the article with the design requirements, absence of deformations and damages, shells, cracks, strakes, embedded parts, releases of reinforcement and protective coatings.
To store prefabricated structures in the installation area, wooden gaskets with a thickness of 100150 mm are used .
Cement is packed in bags of 50 kg. Brick consumption is assumed based on consumption per 1 m3 of masonry - 405 pcs, solution consumption per 1 m3 of masonry - 0.25 m3. The brick is imported on pallets and stored in two rows.
Brick is unloaded from vehicles and delivered to the warehouse and workplace in packages using a sling grip. At the same time, it is mandatory to protect the bottom of the packages with canopy aprons from bricks. The solution is supplied to the workplace by an inventory dispenser hopper and in metal boxes.
1.2.8 Instructions for the production of masonry
Work on the construction of stone structures should be carried out in accordance with the design. Selection of the masonry solution composition should be carried out in accordance with the consumption standards of materials for the preparation of solutions .
Masonry of brick basements of buildings must be made of full ceramic brick.
It is not allowed to loosen stone structures with holes, furrows, niches, installation openings not provided for by the design.
In case of forced breaks, masonry must be performed in the form of an inclined or vertical stroke .
When breaking the masonry with a vertical strap, a mesh (reinforcement) made of longitudinal rods with a diameter of not more than 6 mm, of transverse rods - not more than 3 mm with a distance of up to 1.5 m in masonry height, as well as at the level of each slab, should be laid in the joints of masonry. The number of longitudinal reinforcement rods is taken on the basis of one rod for every 12 cm of wall thickness, but not less than two with a wall thickness of 12 cm.
The height difference of the erected masonry on adjacent grips and when laying the joins of the external and internal walls should not exceed the height of the floor, the height difference between the adjacent sections of the foundation masonry should not exceed 1.2m.
Erection of stone structures of the next floor is allowed only after laying of load-bearing structures of floors of the erected floor, anchoring of walls and grouting of seams between slabs.
The maximum height of the free standing stone walls shall not exceed the values specified in the table. If it is necessary to erect free-standing walls of higher height, use temporary fasteners.
Vertical verticality of faces and angles of brick masonry, horizontal level of its rows must be checked in the course of masonry execution (after 0.50.6 m) with elimination of detected deviations within the level.
After the masonry of each floor, you must perform a instrumental check of the horizontal and elevation of the top of the masonry, regardless of the intermediate checks of the horizontal of its rows.
Stamens in masonry must be laid out of whole bricks. Regardless of the system adopted for dressing seams, the laying of stamen rows is mandatory in the lower (first) and upper (last) rows of structures being erected, at the level of trimmings of walls and pillars, in protruding rows of masonry.
In multi-row dressing of seams, the laying of pincers for supporting parts of structures is mandatory. With single-row dressing of joints, it is allowed to rest structures on spoon rows of masonry.
Horizontal and transverse vertical seams of brickwork of walls, as well as seams in lintels, spacers and poles should be filled with mortar, with the exception of masonry in wasteland .
During masonry, the depth of the seams not filled with mortar on the front side shall not exceed 15 mm in the walls and 10 mm (vertical seams only) in the pillars .
Steel reinforcement of row brick bridges should be laid along the formwork in the mortar layer under the lower row of bricks. The number of rods must be at least three.
Smooth rods for reinforcement of bridges must have a diameter of at least 6 mm, end with hooks and be embedded in the spacers by at least 25 cm.
When holding brick lintels in the formwork, it is necessary to observe the deadlines specified in the table.
All embedded reinforced concrete prefabricated elements shall be provided with temporary anchorages until they are pinched with overlying masonry .
Ventilation ducts in the walls should be made of ceramic full-white bricks of at least 150 grade.
For reinforced masonry, observe the following requirements:
the thickness of the joints shall not exceed the sum of the diameters of the intersecting reinforcement by not less than 4 mm with the thickness of the joint not more than 16 mm;
at longitudinal reinforcement of masonry steel bars of reinforcement along the length should be connected to each other by welding ;
when making joints of reinforcement without welding, the ends of smooth rods must end with hooks and be connected by wire to the overlap of the rods by 20 diameters
Курсовой проект.dwg

Similar materials
- 24.01.2023
- 24.01.2023
- 24.01.2023
- 29.07.2014