Gas supply to the district of the city of Tyumen and the heating boiler house of the kindergarten



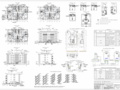
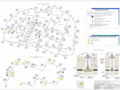
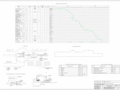
- Added: 04.02.2022
- Size: 15 MB
- Downloads: 3
Description
Graduation qualification work in the direction of 08.03.01 "Construction" profile "Heat and gas supply and ventilation". Topic: "Gas supply of the district of the city of Tyumen
and the kindergarten's heating boiler room."
Contents
1. Gas supply
2. Automation
3. Technology and organization of construction
Project's Content
![]() ![]() ![]() ![]() |
![]() ![]() ![]() |
![]() ![]() ![]() |
![]() ![]() ![]() ![]() |
![]() ![]() ![]() ![]() |
![]() ![]() ![]() ![]() |
Additional information
Contents
Summary
Introduction
1. Gas supply
1.1 Characteristics of the gasified area of the city of Tyumen
1.2 Substantiation of gas pipeline route and protection zone boundaries selection
of the gas pipeline to be connected
1.3 Gas control points
1.3.1 Determination of the number of gas control points in the area
1.3.2 Selection of GRP equipment
1.4 Identification of gas distribution system
1.5 Physicochemical properties of gas
1.6 Determination of density and lower combustion heat of gas fuel
1.7 Calculation of gas consumption by the area
1.7.1 Annual gas consumption by residential buildings
1.7.2 Annual heat consumption by utilities
population
1.7.3 Annual heat consumption for hot water supply, heating,
ventilation and food preparation of residential and public buildings
1.7.4 Determination of estimated gas hourly flow rates
1.8 Hydraulic calculations of gas pipelines of the region
1.8.1 Hydraulic calculation of high pressure gas pipeline
1.8.2 Hydraulic calculation of low pressure gas pipeline
1.9 Gas supply of the city district quarter
1.9.1 Substantiation of gas pipeline route selection
1.9.2 Substantiation of technical solutions of electrochemical protection device
corrosion protection of steel gas pipeline
1.9.3 List of measures to ensure safe operation of facilities
gas supply systems
1.9.4 Hydraulic calculation of low pressure intra-quarter gas pipeline
1.10 Gas supply of apartment building
1.10.1 Estimated gas requirements of capital construction facility
1.10.2 Description of technical solutions for gas flow metering and control,
automatic control systems used
1.10.3 Substantiation of technical solutions of electrochemical protection device
corrosion protection of steel gas pipeline
1.10.4 Measures to ensure safe functioning of the system facilities
gas supply
1.10.5 Energy efficiency of building gas supply system
1.10.6 Hydraulic calculation of internal gas pipeline
1.11 Boiler house gas supply
1.11.1 Information on the type and number of units consuming fuel
1.11.2 Description of technical solutions for accounting and control
gas flow rate
1.11.3 Calculation of boiler room gas flow rate
1.11.4 Hydraulic calculation of boiler room gas pipeline
1.11.5 Removal of gas combustion products from boilers
1.11.6 Thermal insulation of enclosing surfaces of units and thermal conductors
1.11.7 List of standby fuel system structures
1.11.8 External gas supply networks of boiler house and facilities on them
1.11.9 Electrochemical protection of steel gas pipeline against corrosion
1.11.10 List of safe operation measures
facilities of gas supply system
1.11.11 Boiler house internal gas supply
1.11.12 Determination of gas quantity in boiler house pipelines
1.11.13 Thermal mechanical solutions
1.11.14 Fuel lines
1.11.15 Heating and ventilation
2. Automation
2.1 General Information
2.2 Boiler room automation system
2.3 Gas Gas Control System of Apartment Building
3. Technology and organization of construction
3.1 General Information
3.2 Preparatory and earthworks
3.3 Transportation and storage of pipes and parts
3.3.1 Transportation and storage of steel pipes and parts
3.3.2 Transportation and storage of polyethylene pipes and connecting pipes
details
3.4 Welding operations
3.5 Installation and laying works
3.6 Cleaning the internal cavity of the pipeline
3.7 Laying of gas pipeline by method of inclined-directional drilling
3.8 Testing of gas pipelines
3.9 Safety precautions
3.10 Occupational safety and fire safety measures
3.11 Environmental protection measures
3.12 Calculation of labour intensity of works
3.13 Construction Schedule
3.14 Construction Plot Plan
3.15 Need for temporary buildings and structures
3.16 Technical and economic indicators
Conclusion
List of sources used
Appendix A Basic Symbols
Appendix B Design diagram of the internal house gas pipeline
Appendix B Boiler Room Gas Pipeline Design Diagram
Summary
In this final qualification work, a gas supply project was developed for the Tyumen district and a gas heating boiler house. Also presented are gas supply projects of a separate quarter, an apartment building and topics of boiler house automation and organization of construction production technology.
In the main part of the exhaust qualification work, a ring diagram of a low-pressure gas pipeline and a dead end diagram of a high-pressure gas pipeline for gas supply to the city area were developed. Gas consumption by the area is calculated taking into account various categories of gas consumers and hydraulic calculations of high and low pressure networks are performed. The gas supply project of the apartment block of apartment buildings was also completed and the gas supply network of 24 apartment 4-storey residential building was designed.
The gas supply project of the kindergarten boiler house was developed in the main part of the VKR. The issues of organization of accounting of gas consumption in the boiler house, removal of combustion products from boilers, supply and supply ventilation are covered, thermal and mechanical solutions are described.
In the automation section, a boiler room automation system was developed and automation tools for intra-apartment gas supply were selected.
In the third section aspects of organization of construction process of underground gas pipeline section are considered, labour intensity of works and development of construction schedule are calculated. Also, in the graphic part, the development of a construction master plan and a schedule for the movement of workers were carried out.
Keywords: gas supply scheme, gas control station, reduction line, throughput, disconnecting device, gas design flow rate, gas consumption rate, consumer category, hydraulic calculation, high and low pressure, gas-using equipment, maximum-hour flow rate, safety automation, inlet and internal gas pipeline, gas-gas detector, boiler room, construction technology, schedule, construction plot plan.
Introduction
Issues related to the gas supply in Tyumen and the construction of heating boilers operating on natural gas are very relevant, since today natural gas is the cheapest and most environmentally friendly energy carrier and its use is widely used in the field of consumer services of residential and public buildings, as well as in industry.
The priority tasks of gas supply project development are:
- reliable, uninterrupted and safe operation of the gas supply system through gas pipelines to consumers, taking into account the development of the territory for the estimated period;
- reduction of capital and operating costs during construction and operation of gas facilities;
- environmental and fire safety of gas supply system.
Gasification of the city district is an improvement in ecology, the timely start of the heating season and acceptable tariffs for heat and hot water for the population. Gas that came to the houses can significantly improve the life of residents. Gasification of the Tyumen region is an important socio-economic factor that is important for the development of the region as a whole.
The purpose of the graduation qualification work is to develop a gas supply project for the city district and a heating boiler house of a kindergarten, taking into account environmental and industrial safety.
To achieve this goal, the following objectives must be achieved:
- study theoretical aspects of gas distribution and gas consumption systems design in the city quarter;
- develop a gas distribution and gas consumption project in accordance with the current regulatory reference literature;
- analyze the gas distribution and gas consumption system in the city;
- develop a gas supply project for the boiler house in accordance with the current regulatory and reference literature.
The use of gas for industrial installations improves working conditions and increases its productivity. The use of natural gas in industry makes it possible to carry out fundamentally new, progressive and cost-effective processes. In addition, the use of gas as fuel makes it possible to significantly improve the living conditions of the population, increase the sanitary and hygiene level of production and improve the air pool in cities and industrial centers.
The practical significance of the graduation qualification work lies in the possibility of implementing the developed gas distribution and gas consumption system using the latest technical equipment.
Substantiation of the choice of the gas pipeline route and the boundaries of the protection zone of the connected gas pipeline
The design documentation was developed on the basis of the requirements of SP 62.13330.2011 "Gas distribution systems. Updated revision of SNiP 42012002 "as amended with revision No. 1.
The laying of external gas pipelines in the settlements should be provided, as a rule, underground. Above-ground and above-ground laying of gas pipelines is allowed inside residential quarters and yards, as well as on other separate sections of the route [1].
Along the route of the underground gas pipeline, the project provides for the installation of identification marks, which indicate the connections of the gas pipeline, its depth, gas pressure and the telephone of the emergency dispatch service (ADS) [1].
For the designed gas distribution network, a security zone is established in the form of a territory limited by conditional lines passing at a distance of 2 meters from each side of the gas pipeline.
In accordance with GOST 9.6022016, the selection of the route route of underground gas pipelines should be carried out taking into account the existing geological conditions of the design area.
Along the route of the gas consumption network, indicator plates are provided for identifying the location of characteristic points of the gas pipeline on the ground (angles of rotation, branches, diameter crossings, etc.). Indicator plates are installed on permanent reference points in well-viewed places. In addition to the information on the characteristic points and parameters of the gas pipeline, the telephones of the emergency dispatch service of the operating organization are indicated on the indicator plates. Notification of an emergency situation on the gas distribution network is provided by the population through wireless/wire communication. Installation of identification plates is executed by act.
The choice of the underground gas pipeline route is determined by the need to comply with the following basic requirements:
ensuring normal operating conditions of the gas distribution and gas consumption network and reducing risks of its damage;
provision of standard distances from the gas pipeline to buildings and structures, including adjacent utility networks in accordance with Appendix B to SP 62.13330.2011;
laying of gas pipeline along optimal trajectory of gas pipelines with minimum number of turns and butt joints;
reduction of capital costs for construction of gas consumption network.
The depth of gas pipelines shall be taken in accordance with SP 62.13330.2011 [1].
Gas control points
To reduce and maintain gas pressure in gas distribution and gas consumption networks within the specified limits, regardless of gas flow rate, installation of gas control points is provided. Gas control points shall be provided as separate.
The location of GRP in settlements is regulated by SP 62.13330.2011 [1].
At least two control lines (main and standby) shall be provided in FRG with gas inlet pressure above 0.6 MPa.
The FRG provides rooms for the arrangement of reduction lines, as well as auxiliary rooms, which may include rooms for the placement of heating equipment, instrumentation, automation and telemetry equipment, power supply equipment [1].
Separate PRGs are recommended to be located at distances from buildings and structures (except for utility networks) not less than those specified in Table 5 * SP 62.13330.2011 [1].
The FRG can be equipped with a filter, safety devices (safety and disconnection (protective) valves), control valves (pressure regulator, monitor regulator), shut-off valves, instrumentation and, if necessary, a gas flow metering unit [1].
The number of reduction lines in the FRG is determined based on the required throughput, gas flow rate and output pressure, the purpose of PRG in the gas distribution network, as well as on the conditions of uninterrupted supply of consumers and the possibility of scheduled operations [1].
Before the gas pipeline is introduced into the GRP room and after it, the installation of disconnecting devices in the underground version is provided.
At the introduction of the gas pipeline into the room, as well as after the FRG, it is provided to install indicating pressure gauges measuring the gas pressure before and after the FRG.
Filters are installed in FRG for gas cleaning from mechanical impurities. Filters installed in FRG shall have devices for determining pressure drop in them, which characterize the degree of clogging at maximum gas flow rate [1]. Before and after the filter, it is necessary to provide for the installation of instrumentation: two pressure gauges, a display thermometer, a differential pressure gauge to measure the pressure drop on the filter cassette.
After the filter, the gas pressure regulator is installed in the FRG. The pressure regulator is designed to reduce the gas pressure and maintain it at a given level, regardless of flow rate. Connection of pulse pipes from the pressure regulator, safety shut-off and discharge valves to the direct section of the common header is made at a distance of five diameters of the outlet gas pipeline after the last local resistance.
Disconnecting (protective) and safety valves shall ensure automatic limitation of gas pressure increase in the gas pipeline or its supply termination accordingly in case of changes not permitted for safe operation of gas-using equipment and technical devices [1]. For these purposes, the FRG provides for the installation of safety shut-off (SSC) and safety relief valves (UCS). The BSV is designed to cut off the gas supply when the pressure increases or decreases above or below the set one by 25%, respectively. UCS is designed to release gas into the atmosphere at pressure increase above the set one by 15%.
The internal air parameters in the RWG premises, except for the duty personnel room, should be taken:
- equal to ambient air temperature - for warm period of the year;
- not less than the temperature specified in the operational documentation for materials and equipment, but not less than 5 ° С - for the cold period of the year and transitional conditions [33].
Air removal should be provided from the upper area of the production premises of the FRG. Vents for air removal shall be placed not less than 0.4 m from the ceiling or cover plane to the top of the holes [33].
FRG rooms shall be equipped with natural and/or artificial working lighting in accordance with SP 52.13330. Electrical lighting devices, electrical equipment, instrumentation with electric output signal located in the room of reduction lines shall be made in explosion-proof design [33].
Electrically conductive parts inside the PWG shall be connected and connected to the protective grounding system. Grounding devices of electrical installations and lightning protection must be common and connected on the main grounding bus [33].
Discharge and blowdown pipelines shall be provided in the FRG. Blowdown pipelines in the FRG are provided, as a rule, after the first disconnecting device, before and after the regulator. Discharge pipeline is provided from safety relief valve.
The boiler house blow-down and discharge pipelines shall have a minimum number of turns and shall be brought out above the eaves of the building by at least 1 meter.
Gas pipelines of FRG are laid with a slope towards the main gas pipeline [1].
The gas pipeline is laid openly, without crossing the ventilation grids, with attachment to the columns of the building, to separate standing supports, as well as suspensions to the trusses using a fastener system of the type "Fischer" or its analogues.
To protect above-ground gas pipelines from corrosion, protective atmospheric paint coatings should be used, the declared service life of which should be confirmed by natural or accelerated tests and be at least five years.
The list of general measures aimed at ensuring the safe operation of the gas supply system includes monitoring the construction of the gas pipeline, including testing the gas pipeline for tightness and checking the coupling and welded joints of the gas pipeline by methods and in the volume provided for in Section 10 of SP 62.13330.2011 .
After completion of construction the gas pipelines are subjected to pneumatic leak test in accordance with SP 62.13330.2011.
Hydraulic calculations of gas pipelines of the region
The task of hydraulic calculation of gas pipelines is to select pipe diameters depending on the gas flow rate and allowable pressure loss.
Hydraulic calculations of the gas distribution network were made in accordance with the requirements of section 3 of SP 421012003 "General provisions for the design and construction of gas distribution systems made of metal and polyethylene pipes." When calculating the gas distribution network, consumers geographically located outside the boundaries of the planning territory are taken into account.
During calculations the following permissible values of gas pressure are accepted:
minimum design gas pressure in the designed high-pressure gas pipeline upstream the gas control points shall be at least 0.30 MPa;
the design pressure in the low pressure gas pipeline at the outlet of the gas control points is assumed to be at least 0.003 MPa (3.0 kPa).
The gas supply scheme adopts the designation of nominal (conventional) diameters of the designed gas pipelines in accordance with the requirements of GOST 2833889 "Pipeline connections and valves. Nominal diameters. "
The capacity of gas pipelines can be taken from the conditions for creating, at maximum allowable gas pressure losses, the most economical and reliable system in operation, ensuring the stability of the operation of FRG and gas control plants (GRU), as well as the operation of burners of consumers in permissible gas pressure ranges. [2]
The design internal diameters of gas pipelines are determined based on the condition of ensuring uninterrupted gas supply to all consumers during the hours of maximum gas consumption. [2]
Design pressure losses in high and medium pressure pipelines are accepted within the pressure category adopted for the gas pipeline. [2]
In this work, the calculation should be made for high and low pressure gas pipelines.
Boiler house gas supply
Gas supply source - operating high-pressure gas pipeline Ø225mm, laid in Tyumen.
The outer diameter of the gas pipeline at the connection point is 225 mm, the pipeline material is polyethylene, the system designation is G3.
The transported medium is natural gas that meets the requirements of GOST 554287 * with a low combustion heat of 35.59 MJ/m3 and a density of 0.723 kg/m ³ under normal conditions.
The maximum permitted pressure in the G3 system is 0.6 MPa, the operating pressure is 0.5 MPa.
The depth in the connection area is 1.01.5 meters from the actual ground surface.
The boiler house is built-in and designed for heat supply and hot water supply of kindergarten buildings in Tyumen. The distribution of flows for the needs of heating, ventilation and hot water supply is provided in thermal points.
The designed boiler building is one-story with plan dimensions in axes of 16.5x6.5 m. The height to the bottom of the roof beams is 3.5-4.2m.
From the boiler room there is an outlet directly to the outside. The boiler room does not provide for permanent stay of maintenance personnel. The external walls of the fuel warehouse are made of blocks of cellular concrete D600 300 mm thick according to STB111798. The external walls of the boiler house are made of wall sandwichpanels, the 100 mm thick coating is made of TRIMO roofing panels of the Sandwich type, 120 mm thick, resting on metal beams .
The finishing layer of the Sandwich coating panels is provided for factory readiness for final painting in site conditions in restrained light tones.
In the premises of the gas boiler room, lighting is carried out through window openings and ceiling fluorescent lamps.
1.11.1 Information on the type and number of units consuming fuel
The use of natural gas is provided for heating, ventilation and hot water supply.
The project provides for the installation in the boiler room of three steel hot water boilers RTQ418 from Riello (Italy) with a capacity of 418kW. The boilers are equipped with combined RLS50 burners with a tuning range of 145 - 581kW from Riello S.P.A (Italy) complete with the MB ZR DLE 412 gas multi-unit.
1.11.2 Description of technical solutions for gas flow metering and control
The project provides the SRP installation of the ITGAZ B/2492OYG25ET brand with the built-in measuring SGEKvzR0.7540/1.6 complex. The measuring complex is made on the basis of a rotary gas meter of the RABO G25 type with an expansion range of 1:80 and a temperature corrector EC270. The meter shall be installed prior to the pressure regulator. The installation of the gas control station is provided on a foundation common with the building, at a distance of at least 3.0m in radius from window, door and other openings.
The project provides for the installation of the intrinsically safe power supply unit BPEK02, MT to provide power to the electronic corrector of the gas counter and to install the telemetry device. The WSD heating method is gas.
In front of the hot water boilers, the project provides for the installation of rotary gas meters of the grade RVG G40 with an expansion range of 1:65.
Accounting of heat energy generated in the boiler house is carried out using the heat energy metering unit installed in the boiler house, brand TEM104 of the company "Arvas."
Automation
2.1 General Information
Automation is the use of a certain set of means, for the implementation of production processes under the control of a person, but without his direct participation.
An important advantage of using gas fuel is the possibility of using automation to control and control gas combustion processes.
For safe and rational use of gas, it is necessary to use instrumentation and other devices that operate automatically.
Advantages of using automation tools:
- Reduction and facilitation of human labour;
- safe and economical operation of units;
- increase of equipment service life;
- decrease of gas flow rate;
- reduction of the number of maintenance personnel.
Automation Tasks:
- management;
- measurement;
- monitoring;
- alarm;
- adjustment (maintaining the specified adjustable parameter).
Automatic alarm classification:
- preventive;
- executive;
- alarm (signaling to operator).
Safety automation is provided to stop the gas supply in case of violation of specified parameters, for example, when the burner flame goes off, unacceptable deviation from the specified gas pressure parameters, air supply to the burners is stopped).
The development of safety automation and regulation as part of complex systems is a promising direction in the field of automation. Currently, the vast majority of gas-consuming equipment is equipped with automation equipment. Main parameters controlled during operation of gas-consuming equipment: temperature, gas pressure, voltage, coolant (water) temperature at the boiler outlet, water pressure in the boilers, the ratio of the amount of fuel and air supplied to the gas burner. Control and control of the ratio of fuel to air supplied to the gas burner is necessary to ensure the most economical combustion of gas and to create the necessary vacuum and back pressure.
Significant savings in the use of the automation system are due to the reduction in the number of operational personnel, which are replaced by fewer dispatchers.
Telemechanization tools are used to improve the quality of signals transmitted over distance and maintain their quality.
In boiler house designs it is necessary to provide equipment protection (safety automation), alarm, automatic regulation, control included in the automated process control system of the boiler house [7].
In the boiler houses, regardless of the capacity, pressure and temperature of the coolant of the boilers used, monitoring, alarm and devices should be provided that automatically stop the supply of fuel to the burners when the gas content of the room reaches 10% of the lower explosive limit of natural gas with an air content of CO more than 20 mg/m2 [7].
During the automation project, mass-produced certified automation tools and complete control systems with microprocessor devices should be accepted. When the boiler room is included in the control system of the city, district or enterprise as per the design assignment, a set of devices should be provided for possible connection of dispatching systems to them [7].
Technology and organization of construction
3.1 General Information
Construction technology - the science of how to carry out construction work during the construction of buildings and structures, subject to labor protection conditions.
Organization of construction - a set of various measures of an organizational and technical nature, to control and observe the timing and quality of construction, taking into account the economic, technological and other interests of the construction participants.
Construction organization shall: ensure efficient distribution of capital investments and volumes of construction and installation works to buildings, structures and construction periods; eliminate unsustainable consumption of energy resources; Provide modern industrial and sanitary services for those working directly at the facilities [29].
The construction production is based on the following principles:
- Systemality (considering construction as a single system consisting of many elements);
- safety (ensuring the stability of the facility and ensuring compliance of structural, volumetric planning, organizational and technological solutions with environmental and social conditions);
- flexibility (ability to adapt to often changing conditions of work and to changes in technological and organizational parameters of construction production);
- resource saving (saving energy, material, labor, etc.);
- quality (compliance of construction processes with applicable codes, standards and design solutions, due to control at all stages of construction);
- efficiency (assessment of compliance of design solutions with final parameters of construction of the facility, which determine quality, time, resource consumption and cost).
In accordance with Federal Law No. 190FZ of 29.12.2004 The "Urban Planning Code of the Russian Federation," the implementation of work in the field of capital construction is allowed only if there are design estimates including the construction organization project (PIC).
The process of construction of gas pipelines includes three main stages:
1 stage - preparation. Preparation includes: approval of projects, preparation of construction site, geodetic breakdown of turning angles, breakdown and fixing of picket, delivery of construction materials and equipment to the site.
Stage 2 - construction and installation works. The types of work on the construction of the gas pipeline are different and depend on the peculiarities of the object (earthworks, binding of devices, introduction of the gas pipeline into the building, welding of the external, inlet, internal gas pipeline, laying of the gas pipeline by the method of inclined-directional drilling). All features of pipeline construction shall be provided in the detailed documentation.
Stage 3 - commissioning of the built gas supply system with signing of acceptance and testing certificates, execution of as-built documentation.
During the construction process, author supervision of construction and technical supervision shall be performed.
Organizational and technological documentation includes work execution projects, diagrams and instructions for work execution, quality control diagrams, flow charts, main provisions for the production of construction and installation works as part of the detailed documentation of standard mass use projects, as well as other documents containing decisions on the organization of construction production and technology of construction and installation works, executed, agreed, approved and registered in accordance with the rules in force in the organizations developing, approving and agreeing on these documents [29].
3.2 Preparatory and earthworks
Routing preparatory works include:
- breakdown and fixing of picket, geodetic breakdown of horizontal and vertical turning angles, marking of construction strip;
- clearing of the construction strip from the forest and shrubs, stumps, removal and storage in specially designated places of the vegetal (fertile) layer of land;
- draining of the construction strip (if necessary);
- building strip layout, boulder cleaning;
- preparation of technological passes;
- arrangement of protective enclosures.
The installation of traffic warning signs should be organized in places of transport. The layout of such signs and the organization of traffic for the period of work is coordinated with the traffic police of the city.
When performing work related to the development of soil on the territory of existing buildings, it is necessary to ensure the passage of special vehicles and passage to the structures by constructing bridges, pedestrian bridges, etc. [2]
Before the start of excavation work, it is necessary to determine the places of removal of excess soil from the gas pipeline construction site.
Place the soil dump from the trench on one side, at a distance of not less than 0.5 m from the brow. The other side of the trench shall be free for transportation and construction works.
At intersections of all types of underground communications, soil development in trenches is allowed only if there is written permission of the organization operating these communications and in the presence of responsible representatives of the construction organization developing the soil and the organization operating these communications.
Organizations operating underground communications are obliged to mark on the ground in the area of work with well-visible signs of the axis and boundaries of these communications before the start of the specified works.
Crossing points shall be opened by bore holes (width equal to trench width, length 2 m in each direction from crossing point) to design elevations of trench bottom and, if necessary, fixed.
Soil development by a mechanized method is allowed at a distance of at least 2 m from the side wall and at least 1 m above the top of the pipe, cable, etc. Soil left after mechanized development shall be completed manually without the use of impact tools; at the same time, measures should be taken to prevent the possibility of damage to these communications.
In case of detection of existing underground utilities and other structures not indicated in the available design documentation, earthworks must be suspended, representatives of organizations operating these structures are called to the place of work, at the same time the specified places are fenced and measures are taken to protect the discovered underground devices from damage.
Open electrical and communication cables shall be protected against mechanical damage and sagging by means of cases of polyethylene or metal pipes suspended from the bar.
Asbestos cement and ceramic pipes must be enclosed in wooden boxes made of boards with a thickness of 3-5 cm and suspended. The ends of the bar shall cover the trench by at least 0.5 m in each direction.
Opening of road surfaces shall be carried out after refinement of the work front and identification of intersected underground communications on the gas pipeline route. The place of work shall be fenced. To open the asphalt or cobblestone surface, bump pneumatic hammers and perforators are used. It is advisable to open concrete coatings using pneumatic concrete poloms.
The width of the opening of road surfaces should be more than the width of the upper part of the developed trench with improved pavement (asphalt, asphalt concrete) - by 10 cm (per side), with other pavement structures - by 25 cm (per side).
Materials from disassembly of pavements shall be stored within the fence of the place of work at least 1.5 m from the edge of the trench (pit) on the side opposite to the place of future soil dump.
Improved pavements can be opened using a bar installation complete with single bucket excavators. The selection of the process diagram and the complex of machines for opening the coating should be made depending on the width of the developed trench, the thickness of the coating, and the scope of work. It is advisable to open asphalt pavements using single-bar (BMG on tractor T74, KNP-2 on tractor C80) or double-bar (KNP3 on tractor C100), installations working with a single-bucket excavator.
Cutting of longitudinal parallel slots is carried out to the depth of asphalt surface. The movement of the machine should be carried out longitudinal with turns at the ends of the opened section or shuttle passages (with idle return movement in reverse). The opening width shall be greater than the upper part of the trench being developed by 10 cm (in each direction).
After cutting the longitudinal slots along the entire length of the opening section, the transverse slots should be cut to the depth of the coating with the passages of the bar installation forward. At the same time, the return of the machine and the transition to the neighboring position should be carried out in reverse.
The distance between the slits shall be such that the remaining cover pillars are equal to 0.80.9 of the excavator ladle width.
The outer pillars of the coating should be hacked with a bucket of a single bucket excavator. The distance between the working excavator and the beginning of the area where the bar plant operates must be at least 2030 m.
The base for the carpet shall be installed on the stamped soil after installation of the discharge tube. Drainage and control tubes of the structures on the gas pipeline should be installed in the center of the carpet perpendicular to the plane of its base. The space around the discharge pipe along the entire height within a radius of at least 1.0 m must be filled with sandy soil and indentations with a radius of 0.50.7 m. The distance between the cover of the carpet (or the manhole of the well) and the end of the outlet devices (discharge pipes, cranes, plugs) must be 1015 cm.
The minimum width of the trench shall be 0.5 m. Slope of trench slope in sandy sandy soils shall be 1: 0.25 at trench depth up to 1, 5 m and 1: 0.67 at trench depth up to 3, 0 m.
The size of the pit for welding joints in the trench should be: length - at least 1.0 m, width - at least 2.1 m, depth 0.7 m.
The need for temporary fastening of the walls of the trench and pits should be determined from the actual state of the soil, hydrogeological and other local conditions.
Development of the trench, in places where it is possible to use excavation mechanisms, be carried out by a single-bucket excavator of the EO 3322 type.
The development of trenches by a single bucket excavator should be carried out with the elimination of scallops at the bottom during digging, which is achieved by dragging the bucket along the bottom of the trench after the development of the face is completed.
The development of the trench should begin from the bottom to ensure the removal of groundwater and atmospheric water to places with low elevations. Soil dumping areas should be located from the side of a possible influx of rainwater. Removal of ground and surface water entering the trench is provided through pumping units, which are installed at the lower points of the gas pipeline route. Surface water removal should be carried out into the existing drainage network (storm sewer), while avoiding its clogging with garbage, fuel and lubricants and soil particles. When discharging underground and surface waters, the following should be excluded: flooding of structures, the formation of landslides, soil erosion.
If there is a strong influx of surface water (heavy precipitation, snow melting), digging of the trench should be carried out taking into account the provision of complete backfilling of the gas pipeline after the shift.
For the gas pipeline in the trench, make a sand base from class 1 coarse sand, as per GOST 87362014. The base thickness shall be at least 10 cm.
It is recommended to fill the gas pipeline at ambient temperatures close to its operating temperature. When filling the gas pipeline, it is necessary to ensure the preservation of the pipeline and insulation coatings, the tight abutment of the gas pipeline to the bottom of the trench and the design position of the gas pipeline [2]. Backfill shall be performed with coarse sand, layer of at least 20 cm above the upper generatrix of the pipe and then with soil from the dump. Soil from the dump should not contain large inclusions. Sections of the gas pipeline located under the driveways, as well as steel and vertical sections in a meter radius, are filled with coarse sand to the entire depth of the trench with layer-by-layer compaction.
Filling of trenches with laid gas pipeline shall be performed in two receptacles:
- first, pits and sinuses are filled with soft soil at the same time on both sides of the gas pipeline;
- then the trench is filled with the specified soil 0.2 m above the upper generatrix of the pipe with ensuring the safety of pipes, joints and insulation, at that the soil is filled with layers and compacted with manual, mechanical or pneumatic ramming.
Final filling of trenches shall be performed after gas pipelines leak test and insulation check by instruments. Backfilling should be carried out with soil without large inclusions. If ice and snow form in the trenches, it must be removed by an excavator before laying the pipeline.
Prior to the start of backfilling works, the gas pipeline must be fully installed, welded joints checked by physical control methods, steel joints must be insulated, the correct position of the gas pipeline and its tight abutment to the bottom of the trench should be checked, and the quality of the insulation coating should be checked.
Filling of gas pipeline in extended sections of the route is performed by bulldozer.
When filling the gas pipeline in winter with frozen soil on top of it, arrange a roller of soil taking into account its subsequent precipitation during thawing.
3.3 Transportation and storage of pipes and parts
3.3.1 Transportation and storage of steel pipes and parts
Transportation of pipes for the construction of gas pipelines is carried out by cars with trailers and roofs in a technically serviceable condition, having a reliable trailer coupling with the car, a safety shield for protecting the driver's cab from longitudinal movement of pipes, fasteners equipped with turnstile conics.
Trailer-dissolution is equipped with a turntable.
When transporting insulated pipes, car and trailer conics are equipped with special cradles with semicircular recesses covering at least 1/3 of the pipe perimeter.
The pitch of the recesses should prevent contact with each other. each cradle can be used for no more than two adjacent diameters of insulated pipes. It is recommended to install cradles from wood. The recesses shall be provided with felt or soft elastic material and shall have no corners or protrusions causing damage to the pipe insulation coatings. The width of the cradle measured along the axis of the pipe shall be not less than the width of the base of the conics.
Insulated pipes are laid on pipe locomotives in cradles. When transporting pipes in several rows, each row is laid in cradles separated from the lower row by soft gaskets (rubber, felt, etc.).
Dimensions of loaded pipeline must be not more than 2.5 m in width, and not more than 3.8 m in height. The loading height of the car conics and the trailer shall be on the same level. The overhang of the pipe by the conics of the trailer shall, as a rule, not exceed 2 meters.
To prevent longitudinal movement, the pipes are fixed by locking steel ropes at both ends. When carrying insulated pipes on stop ropes, soft gaskets shall be laid. Ropes must be in tensioned position.
Pipes are loaded and unloaded by autocranes.
Do not drop insulated pipes from the vehicle or roll them down.
For storage, factory-made connecting parts should be packed in wooden boxes weighing no more than 80 kg, lined with moisture-proof paper.
Transportation of pipe blanks and connecting parts to the construction site shall be carried out in wooden containers, to which a tag is attached with indication of transported units and parts.
In route conditions, pipes are placed on an open flat area. Insulated pipes should be laid with non-insulated ends on sunbeds or soft bulk earth shafts.
Conclusion
In this final qualification work, the goal was achieved, namely, the gas supply project of the city district and the heating boiler house of the kindergarten was developed, taking into account environmental and industrial safety.
Issues related to the gas supply of the city of Tyumen and the construction of heating boilers operating on natural gas were considered. Issues related to the automation of gas supply systems and technology and the organization of construction were also covered. They are very relevant, since today natural gas is the cheapest and most environmentally friendly energy carrier and its use is widely used in the field of consumer services of residential and public buildings, as well as in industry.
To achieve the goals, the following objectives were achieved:
- studied theoretical aspects of gas distribution and gas consumption systems design in the city area;
- A gas distribution and gas consumption project has been developed in accordance with the current regulatory reference literature;
- gas distribution and gas consumption system was analyzed;
- The boiler house gas supply project has been developed in accordance with the current regulatory and reference literature;
- calculation of the scope of work has been performed;
- development of work schedule, calculation of technical and economic indicators of construction.
The method of work was chosen in such a way that it provides increased labor productivity, reduced time and reduced construction costs.
The requirements for ensuring the best environmental conditions were taken into account in this graduation qualification work. This is an important part of the development of the project for the construction of gas distribution and gas consumption systems. The range of environmental impacts in the construction and operation of gas pipelines is very wide. Therefore, the design, construction and operation of gas distribution and gas consumption systems are impossible without taking into account environmental protection issues .
Such types of pipeline structures, construction and operation technologies, mechanization tools were provided, with which negative environmental impacts will be reduced and methods and means of mitigation and forecasting of possible environmental damage will be developed.
All design and technical solutions adopted in the final qualification work meet the requirements of fire, environmental and sanitary hygiene standards, existing codes of rules, regulatory documents approved in accordance with the established procedure in the territory of the Russian Federation and ensure safe operation of the facility.
Диплом 2020_Лист 5-7.dwg

Диплом итог_2020.pdf
Диплом 2020_Лист 3.dwg

Диплом 2020_Лист 4.dwg

Диплом 2020_Лист 1-2.dwg

Similar materials
- 09.08.2024
- 08.06.2024
- 01.07.2014
- 09.08.2014
- 14.05.2016