Drawing of cylindrical reduction gear box. Full version. Gearbox calculation


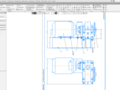
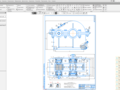
- Added: 24.06.2021
- Size: 4 MB
- Downloads: 0
Description
Content of the calculation and explanatory note: Motor selection and kinematic calculation of the drive. Calculation of chain and gear transmission. Design calculation of shafts. Gear design. Design of body parts. Selection and checking of keys. Check of bearings. Refined calculation of shafts for endurance. Choice of oil grade and determination of its volume. Selection of coupling and check of its operability.
List of graphic material: gearbox assembly drawing - 1 sheet of A1 format; drive mounting drawing - 1 sheet of A1 format; working drawing of sprocket - 1 sheet of A3 format; working drawing of gear wheel - 1 sheet of A3 format; working drawing of the driven shaft - 1 sheet of A3 format; bearing cover working drawing - 1 sheet of A3 format.
Project's Content
![]() ![]() ![]() ![]() |
![]() ![]() ![]() ![]() |
![]() |
![]() ![]() ![]() ![]() |
![]() ![]() ![]() ![]() |
![]() ![]() ![]() |
![]() ![]() ![]() ![]() |
![]() ![]() ![]() ![]() |
![]() ![]() ![]() ![]() |
![]() ![]() ![]() ![]() |
Additional information
Contents
INTRODUCTION
1. Motor selection and kinematic calculation
2. Calculation of chain transmission
3. Calculation of cylindrical transmission
4. Design calculation of shafts
5. Cylindrical Gear Design
6. Design of the Leading Star
7. Design of gearbox housing parts
8. Selection and checking of keys
9. Inspection of bearings
10. Refined calculation of shafts for endurance
11. Oil selection and volume calculation
12. Selection of main fits of drive parts
13. Coupling selection and serviceability check
LIST OF LITERATURE USED
Job for coursework
1. Topic: "Design of process equipment drive with single-stage spur gear and chain gear."
Initial data: drive operating life Lh = 12000 hours; drive driven shaft speed n3 = 100 min1; power on driven drive shaft P3 = 3.2 kW.
Approved by order of 13.03.2020 No. 108st.
2. Deadline for submission of the project (work) to the protection01.06.2020.
3. Content of the calculation and explanatory note: Motor selection and kinematic calculation of the drive. Calculation of chain and gear transmission. Design calculation of shafts. Gear design. Design of body parts. Selection and checking of keys. Check of bearings. Refined calculation of shafts for endurance. Choice of oil grade and determination of its volume. Selection of coupling and check of its operability.
4. List of graphic material: gearbox assembly drawing - 1 sheet of A1 format; drive mounting drawing - 1 sheet of A1 format; working drawing of sprocket - 1 sheet of A3 format; working drawing of gear wheel - 1 sheet of A3 format; working drawing of the driven shaft - 1 sheet of A3 format; bearing cover working drawing - 1 sheet of A3 format.
Introduction
The purpose of course design is to acquire skills in making independent design decisions, assimilate the sequence of development of general-purpose mechanisms, and fix the training material for calculating typical machine parts.
The task of the work is to develop a belt conveyor drive. Drive consists of electric motor connected by coupling with single-stage cylindrical reduction gear and chain gear connected with conveyor drum.
Rotary motion from electric motor is transmitted to reducer by elastic bushing-flange clutch. The electric motor is selected according to the required power and estimated rotation speed. Chain and gear gears are designed according to the criterion of contact strength of the active surface of the teeth, checked according to contact, bending stresses. Design calculation of shafts is carried out for net torsion at reduced permissible stresses. Bearings are selected by the nature of the load on the shafts and by the diameters of the shafts, checked for durability by dynamic lifting capacity. Key connections shall be checked for crushing. Shafts shall be checked for fatigue resistance by safety factor at joint action of bending and torsion taking into account scale factors and stress concentrators.
The lubrication method and oil level are due to the arrangement of the mechanism. Oil is selected based on effective contact stresses and circumferential speed in engagements.
As a result of the work, a compact and aesthetic design of the reduction gear must be obtained, which meets the modern requirements for the mechanisms of this purpose.
Val_vedomy.cdw

Montazhny_chertezh.cdw

Spetsifikatsia_Montazhny_chertezh.spw

Крышка бодшыбника.cdw

Звездочка ведущая.cdw

Колесо зубчетое.cdw

Spetsifikatsia_Sborochny_chertezh.spw

Sborochny_chertezh.cdw

Similar materials
- 15.02.2021