Development of adjustment of 5M14 and 6M83 metal cutting machines




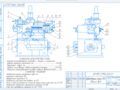
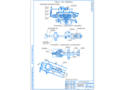
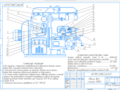
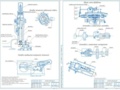
- Added: 22.11.2020
- Size: 4 MB
- Downloads: 1
Description
Design Input For Gear Cutting: Machine Model - 5M14; 3.1.2. Number of wheel teeth zK = 40; 3.1.3. Wheel tooth length b = 65 mm; 3.1.4. Module m = 5.5mm; 3.1.5 Number of passes k = 1; 3.1.6. Billet material - Steel 40; Wheel milling with oblique teeth: Machine model - 6M83; 3.2.3. Number of wheel teeth z = 40; 3.2.3. Module m = 5.0mm; 3.3.4. Inclination angle of teeth α = 22grad; 3.2.5. The direction of inclination of the tooth is right; 3.2.6. Wheel width b = 50mm; 3.2.7. Preparation material - SCh24.
CONTENTS
INTRODUCTION 4 1 ANALYSIS OF BASE MACHINE 5M14 5 1.1 Device, purpose, scope, principle of operation, machine design features 5 1.2 Description of kinematic chains of forming movements 7 1.3 Structural diagram and working area of equipment 11 1.4 Elements of equipment or units drive, ensuring consistency of separate movements 12 2 KINEMATIC ADJUSTMENT AND ADJUSTMENT OF MACHINE TOOL 5M14 16 2.1 Selection of workpiece and surface processing diagrams 16 2.2 Selection of applied cutting tool 17 2.3 Determination of machining allowances 18 2.4 Calculation of cutting modes 18 2.5 Calculations, providing adjustment and adjustment of equipment movements 20 2.6 Check of strength of the most loaded elements of machine adjustment 23 2.7 Equipment adjustment for processing, possible causes of failures and their rectification 24 3 ANALYSIS OF BASIC MACHINE 6M83 31 3.1 Device, purpose, scope, principle of operation, structural features of machine 31 3.2 Description of kinematic chains of forming movements 34 3.3 Structural diagram and working area of equipment 36 3.4 Elements of equipment or units drive, ensuring consistency of individual movements 38 4 KINEMATIC ADJUSTMENT AND ADJUSTMENT OF MACHINE 6M83 46 4.1 Selection of workpiece and surface treatment diagrams 46 4.2 Selection of applied cutting tool 47 4.3 Determination of machining allowances 48 4.4 Calculation of cutting modes 48 4.5 Calculations, providing adjustment and adjustment of equipment movements 50 4.6 Check of strength of the most loaded elements of machine adjustment 53 4.7 Equipment adjustment for processing, possible causes of failures and their rectification 56 5 STANDARDIZATION AND QUALITY CONTROL OF EQUIPMENT 59 6. EQUIPMENT SAFETY REQUIREMENTS 62 LITERATURE 67
Project's Content
![]() |
![]() ![]() ![]() ![]() |
![]() ![]() ![]() ![]() |
![]() ![]() ![]() ![]() |
![]() ![]() ![]() ![]() |
![]() ![]() ![]() ![]() |
![]() ![]() ![]() ![]() |
![]() ![]() ![]() |
![]() ![]() ![]() ![]() |
![]() ![]() ![]() ![]() |
Additional information
Contents
CONTENTS
INTRODUCTION
1 ANALYSIS OF 5M BASE MACHINE
1.1 Device, purpose, scope, principle of operation, structural features of the machine
1.2 Description of kinematic chains of mass-forming movements
1.3 Structural diagram and operating area of equipment
1.4 Elements of equipment drive or units ensuring consistency of individual movements
2 KINEMATIC ADJUSTMENT AND ADJUSTMENT OF 5M MACHINE
2.1 Selection of workpiece and surface machining schemes
2.2 Selection of the applied cutting tool
2.3 Determination of machining allowances
2.4 Calculation of cutting modes
2.5 Calculations providing adjustment and adjustment of equipment movements
2.6 Check of strength of the most loaded elements of machine adjustment
2.7 Adjustment of equipment for processing, possible causes of faults and their rectification
3 ANALYSIS OF BASE MACHINE 6M
3.1 Device, purpose, scope, operation principle, machine design features
3.2 Description of kinematic chains of mass-forming movements
3.3 Structural diagram and operating area of equipment
3.4 Elements of equipment drive or units ensuring consistency of individual movements
4 KINEMATIC ADJUSTMENT AND ADJUSTMENT OF 6M MACHINE
4.1 Selection of workpiece and surface machining schemes
4.2 Select the cutting tool to use
4.3 Determination of machining allowances
4.4 Calculation of cutting modes
4.5 Calculations providing adjustment and adjustment of equipment movements
4.6 Check of strength of the most loaded elements of machine adjustment
4.7 Adjustment of equipment for processing, possible causes of faults and their rectification
5 STANDARDIZATION AND QUALITY CONTROL OF EQUIPMENT
6. EQUIPMENT SAFETY REQUIREMENTS
Literature
APPLICATION
Introduction
Metal cutting machines form the main part of the process equipment. The share of mechanical workshops at machine-building enterprises is about 40%. Despite the fact that recently the share of other types of processing (stamping, casting, welding) has increased significantly, cutting is currently the main method of obtaining machine parts.
Metalworking equipment occupies a special place among the various equipment used in industry, because it is intended for the manufacture of parts of this equipment, that is, for the production of means of production.
A machine is a machine designed for dimensional processing of blanks in order to form given surfaces by removing chips. Processing is carried out mainly by cutting with blade or abrasive tools.
Cutting modes are initial data for calculations of machine units and drives. In most cases, they serve as the basis for the development of machine kinematics - speed numbers, stroke numbers, feed values; dynamics of the machine - power of the electric motor, forces arising during cutting, torque values on the spindles and shafts of the machine, strength and rigidity of individual parts and units of the machine, etc. On the basis of the selected cutting modes, the periodicity and procedure for changing cutting tools, the consumption of tools, the number of employees, salary funds, the number of machines necessary to fulfill a given program, the area of workshops and plots, the necessary investments and many other elements of the organization and economy of production are established.
The right choice of optimal cutting regimes is essential, ensuring the greatest economic impact, taking into account, where possible, all factors affecting productivity, technical quality and the economy of production.
The adjustment of a metal cutting machine is called its preparation together with technological equipment for the performance of certain work on the manufacture of a part in accordance with the established technological process to ensure the required productivity, accuracy and surface roughness.
The purpose of the course work is to acquire the skills of setting up metal cutting machines.
Define machining allowances
The allowance is a part of the removed material, the presence of which on the workpiece is caused by the need to ensure the specified requirements for the accuracy and quality of the surface as a result of cutting or other method with removal of the material layer. The condition of optimal allowances plays an important role in the development of technological processes for the manufacture of parts. Increased allowances lead to increased consumption of material and energy, introduction of additional technological transitions. All this increases labor intensity and increases the cost of manufacturing parts.
Toothing of the specified part is performed in one pass taking into account allowance for finishing by grinding after heat treatment of the gear wheel. We accept for the diameter of the wheel to be cut da = 231 mm and the module m = 5.5 mm allowance for finishing ∆z.f.=2,0 according to the standard of the tooth to be cut.,
Define machining allowances
The allowance is a part of the removed material, the presence of which on the workpiece is caused by the need to ensure the specified requirements for the accuracy and quality of the surface as a result of cutting or other method with removal of the material layer. The condition of optimal allowances plays an important role in the development of technological processes for the manufacture of parts. Increased allowances lead to increased consumption of material and energy, introduction of additional technological transitions. All this increases labor intensity and increases the cost of manufacturing parts.
The specified part is milled after the turning operation. Thus, the processing allowance is the amount of removed layer during turning of the workpiece.
Conclusion
In course work, an analysis was made of the 5M14 toothbrush and the 6M83 cantilever machine. The invention also describes the device, purpose, field of application, principle of operation and structural features of these machines. In addition, calculations were made to ensure the adjustment and adjustment of equipment movements.
The cutting modes were calculated, the hardness of the most loaded adjustment elements of the machine was checked, the equipment was adjusted for processing. A kinematic diagram and a schematic diagram of the adjustment of each machine have been developed.
During the work, the designs of these machines and their technological equipment were considered, ensuring safe operation and high quality of products.
кинематика 5М14.cdw

Кинематика 6М83.cdw

Наладка 6м83.cdw

Наладка5м14.cdw

общий вид 5м14.cdw

Общий вид 6м83.cdw

спецификация 5м14.cdw

Спецификация 6М83.cdw

Similar materials
- 24.01.2023
- 17.03.2024
- 25.10.2022