Development and design of round shaped cutter and cylindrical cutter


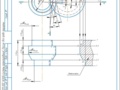
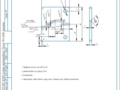
- Added: 06.05.2021
- Size: 2 MB
- Downloads: 0
Description
Calculation of round shaped cutter and drill bit is presented in the work. Calculated caliber and countercalibre.
CL profiling is represented in the graphical and analytical method.
Project's Content
![]() |
![]() |
![]() |
![]() ![]() ![]() |
![]() |
![]() ![]() ![]() ![]() |
![]() ![]() ![]() ![]() |
![]() ![]() ![]() ![]() |
![]() ![]() ![]() ![]() |
![]() ![]() ![]() ![]() |
Additional information
Contents
TASK
1. DESIGN OF ROUND SHAPED CUTTER
1.0 General Information
1.1 Selection of structural and overall dimensions of round cutter
1.2 Rear and front angles of shaped cutter
1.3 Selection of cutter material
1.4 Profiling of shaped cutters
1.5 Graphic construction of profile of round shaped cutter
1.6 Analytical method of determining profile of round shaped cutter
1.7 Calculation of actuating dimensions of caliber and counter-caliber
1.8 Calculation of height dimensions of tolerance for articles
1.9 Calculation of axial dimensions of caliber
1.10 Main types of holders for shaped cutters
2. SPIRAL DRILL DESIGN
2.1 General Information
2.2 Selection of tool material
2.3 Definition of Drill Part Elements
2.4 Calculation of drill neck and shank
2.5 Calculation of cutting, sizing, working and total drill length
CONCLUSION
BIBLIOGRAPHIC LIST
1. design of round shaped cutter
1.0 General Information
Cutters are the simplest tools. They are widely used for machining parts on lathe, turret and semi-automatic machines. Incisors are divided into simple and shaped.
In mechanical engineering, shaped cutters have been widely used for processing shaped surfaces on turning machines and revolving machines, which are divided into prismatic and round in shape and design. By installation relative to the machined part, shaped cutters are divided into radial and tangential.
Shaped cutters are widely used in mass and large-scale production to process the complex profile of parts of bodies of revolution. On parts of bodies of revolution both external and internal surfaces are treated.
Shaped cutters have a number of advantages over conventional turning cutters. They provide high performance, high accuracy in the shape and size of the profile of the workpiece, ease of operation and a large number of wipes. Disadvantages of shaped cutters include: design complexity; complexity of manufacture; the need for accurate installation; high cost; different cutting conditions at edge cutting points. This results in different angles, cutting speeds, different cutting paths, and individual edges being worn out differently.
However, the cost of shaped cutters is higher than simple turning cutters, but in mass large-scale production they are very profitable.
Shaped incisors are divided: in shape - into round and prismatic; by the appearance of the treated surface - on external and internal; by installation and direction of supply - to radial and tangential; by the location of the cutter relative to the part - with parallel location of the body (without) or with rotated; on the location of the front surface - without inclination and with inclination at an angle?.
1.3 Selection of cutter material
The selection of the material from which the round shaped cutter is made depends on the stock material. For the treatment of the part from cast iron SCH 4060, alloy P6M5 is selected as the tool material.
1.4 Profiling of shaped cutters
Profile of shaped cutter is determined in section normal to its rear surface (diametrical section). In this section, dimensions of tool profile are calculated and controlled.
The profile of the shaped cutter is different from that of the machined part. However, in some cases, when the front surface of the cutter with the diametrical section of the part and the front and rear angle of inclination of the blade are zero, the profile of the cutter exactly coincides with the profile of the product. Only using cutters with this geometry is not always appropriate.
Presence of front and rear corners not equal to zero on shaped cutters results in mismatch of cutter part profile. Therefore, in order to obtain the correct product profile, it is necessary to produce a profile other than the product profile in the normal (radial) section of the cutters. The size distortion of the cutter profile increases as the ѱ=α+γ correction angle increases. Only the height dimensions of the profile of the shaped cutter are subject to correction, the axial dimensions remain unchanged (for cutters with an axis parallel to the part axis) and change for cutters with an inclined axis (installation base).
The dimensions of the cutter profile shall be calculated to an accuracy of 0.001 mm for linear dimensions and to 1 "for angular dimensions. The final results are rounded to 0.01 mm.
There are several methods for calculating the profile of a shaped cutter [6]:
- graphic;
- analytical.
In the first case, the cutter profile is obtained by a graphical construction. To obtain the required accuracy, it is necessary to draw the profile of the part and the cutter on a large scale.
This method is very simple and clear.
In the second case, the cutter profile is defined in several ways:
- trigonometric;
- three-membered equations;
- in a general analytical way.
Spiral Drill Design
2.1 General Information
Drills are axial cutting tools used to drill and drill holes in a solid material.
The main types of drills are :
- spiral;
- alignment;
- feathers (for deep drilling);
- heads (for circular drilling).
Advantages:
- good chip removal (due to the presence of screw grooves);
- positive front angle;
- large margin for overflow;
- good direction during operation (due to the presence of drill ribbons).
The cutting part performs the main cutting work. The calibrating part controls the drill during operation. Shank and working part are connected by neck. The front angle of the drill γ decreases from the periphery to the center of the drill. The leading angle results in uneven wear of the cutting edge. The leading angle is selected depending on the treated material and can be from 10 ° to 20 °, the trailing angle = 9... 12 °. Since the leading angle from the periphery to the center decreases, the trailing angle must increase in order to maintain an equal-strength wedge.
Drill is sharpened on rear surface by 3 methods:
- sharpening in plane (for drilling of small diameter 3-5 mm);
- by cone;
- on the helical surface.
Drill Design Improvement Methods:
- double sharpening - increases the length of the cutting part, reduces heat removal from the cutting zone, while the resistance of the drill increases by 25... 30 %.
- triple sharpening;
- the method of strap spotting - reduces its length (when cutting the strap, the centering of the drill improves);
- capping of the band - reduced friction of the link against the walls of the treatment surface, reduced wear, increased resistance of the drill.
Hard alloy drills are used in the treatment of cast iron, non-ferrous metals and metal alloys.
Drills up to 6 mm in diameter can be made whole or composite.
Deep Drill Drills - Drill holes 5 times or more in depth. During processing, as a rule, the drill does not rotate.
Deep Drill Requirements:
- straight to the hole axis;
- concentricity of hole axis;
- the cylindrical length of the hole.
Conclusion
The course work was performed in accordance with the issued task.
In the course work, the design of a round shaped cutter and the design of a spiral drill were presented. The grade of the material from which the cutter is made depends on the workpiece material being processed. Cast iron SCH 4060 was selected for the part treatment, steel P6M5K5 was selected for the drill, in accordance with the task.
Derzhavka_kruglogo_fasonnogo_reztsa.cdw

Graficheskoe_opredelenie_profilya_reztsa.cdw

Kalibr_i_kontrkalibr.cdw

Rabochiy_chertezh_kruglogo_fasonnogo_reztsa_1.cdw

Sverlo.cdw
