Coursework on the modernization of the gearbox in the milling machine 6R82



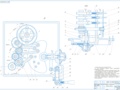
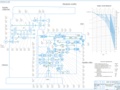
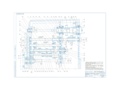
- Added: 28.02.2022
- Size: 5 MB
- Downloads: 3
Description
The work consists of a note and drawings
The note consists of
Introduction. 4
1 Description of the design and kinematic scheme being developed. 5
1.1 General. 5
1.2 Description of the design of the basic variant. 8
2 Calculation of cutting modes. 11
3 Design part. 14
3.1 Kinematic calculation of the gearbox. 14
3.2 Power and tensile calculations of parts. 18
3.3 Design calculation of gears. 20
3.4 Sizing of gears and gears. 22
3.5 Calculation of shafts. 29
3.6 Selection and calculation of bearings. 35
3.7 Calculation of the spline connection. 38
3.8 Description of the lubrication system. 40
3.9 Description of the control system. 41
Conclusion. 43
List of sources used. 44
The drawings include
Kinematics of the A1 machine
Sweep of the A1 speed box
A1 speed box convolution
Lids A3
Shaft A3
Pulley A3
Gear A3
Project's Content
![]() ![]() ![]() |
![]() ![]() ![]() ![]() |
![]() ![]() ![]() |
![]() ![]() ![]() ![]() |
![]() ![]() ![]() ![]() |
![]() ![]() ![]() |
![]() ![]() ![]() ![]() |
![]() |
![]() ![]() ![]() |
![]() ![]() ![]() ![]() |
![]() ![]() ![]() ![]() |
![]() ![]() ![]() ![]() |
![]() ![]() ![]() ![]() |
![]() ![]() ![]() |
![]() ![]() ![]() ![]() |
![]() ![]() ![]() ![]() |
![]() ![]() ![]() |
![]() ![]() ![]() |
![]() ![]() ![]() |
![]() ![]() ![]() ![]() |
![]() ![]() ![]() |
![]() ![]() ![]() ![]() |
![]() ![]() ![]() ![]() |
![]() ![]() ![]() ![]() |
![]() ![]() ![]() |
Additional information
Contents
Introduction
1 Description of the developed structure and kinematic diagram
1.1 General information
1.2 Description of Base Case Design
2 Calculation of cutting modes
3 Design part
3.1 Kinematic calculation of speed box
3.2 Power and strength calculations of parts
3.3 Design calculation of gears
3.4 Sizing gears and gears
3.5 Calculation of shafts
3.6 Selection and calculation of bearings
3.7 Calculation of splined connection
3.8 Lubrication system description
3.9 Description of the control system
Conclusion
List of sources used
Applications
Introduction
Machine tool construction is an industry that determines the technological safety of the country. Only in the presence of machines can all other types of machines and mechanisms be produced. Since the machines are designed to produce production facilities.
Therefore, it is so important to constantly improve them, increase productivity, reliability and the degree of automation.
In design, various mechanisms using hydraulics, electrics, pneumatics are used to give the machine the required qualities and functions; They also use details of complex structural forms with high requirements for their quality indicators, introduce progressive design principles (aggregation, unification); search for the most rational layout of machines, develop new cycle control systems.
Along with the development and improvement of existing processing methods, machines appeared on the basis of fundamentally new technological processes. Such processes include electroerosion processing, electrochemical processing methods, high-energy focused beam treatment, high-pressure thin jet treatment, ultrasonic method, and other methods.
Thus, the machines, which are referred to as metal cutting machines, include a wider group of machine tools that process not only metals but also other materials by various methods.
In order to perform such a variety of technological tasks with high requirements for product quality and processing performance, the latest engineering advances must be used in machine design.
Description of the developed structure and kinematic diagram
1.1 General information
Machine 6P82 is intended for milling of various details from steel, cast iron and non-ferrous metals by cylindrical, disk, shaped, angular, face, trailer and other mills in the conditions of individual and mass production. The possibility of adjusting the machine to various semi-automatic and automatic cycles allows you to successfully use the machine to perform work of an operational nature in in-line and automatic lines in large-scale production.
The machine can handle vertical and horizontal planes, slots, corners, frames, gears, etc.
Technological capabilities of the machine can be expanded using a dividing head, a rotary round table, an overlay universal head and other devices.
Accuracy class of machine H as per GOST 8-77.
Peculiarities of machine design are wide ranges of table feed values; quick-change tool attachment; availability of a feed retardation mechanism; deceleration of the working supply in the automatic cycle; ability to operate in automatic cycles, including frame processing; automatic lubrication of units; application of contactless fast-acting electromagnetic couplings in feed drive; improved accuracy of the machine due to the location of the transverse feed screw along the cutter axis; possibility of moving the table simultaneously along two and three coordinates; possibility of using a DC motor in a supply drive; possible further automation of machines due to the use of digital indication and operational control devices.
Machines are designed to perform various milling operations in conditions of both individual and large-scale production. In large-scale production, machines can also be successfully used for operational work.
The technical characteristics and high rigidity of the machines make it possible to fully use the capabilities of both fast-cutting and hard-alloy tools.
In order to reduce the auxiliary time and ease of control in the machines:
- duplicated control of push-button handle type (front and left side of machine);
- start and stop of spindle and actuation of fast moves of machine by means of buttons;
- control of table movements from handles, direction of rotation of which coincides with direction of table movement;
- Changing the speeds and feeds by means of single-hand selective mechanisms allowing to obtain any speed or feed by turning the limb without passing through the intermediate stages;
- DC braking.
Machines are automated and can be tuned to various, automatic cycles, which increases labor productivity, eliminates the need to service machines with high-skill workers and facilitates the possibility of organizing multi-site maintenance.
Conclusion
In the course project, the modernization of the horizontal cantilever freer universal machine 6P82 was carried out. Thanks to the rational selection of materials and shapes of parts, it is possible to ensure high efficiency, reliability and durability of the modernized unit. A speed switching control system was also developed and a lubrication system for the machine was selected. In the design part of the course project, a kinematic calculation was made, as a result of which the number of gear stages z = 22 and the control range: 180... 2000 min-1 were provided.
To solve the task of modernizing the main movement drive, the following technical innovations were used in the course project:
- in order to increase processability of manufacturing and greater repairability, as well as reduce dimensions, weight and cost, the whole gear blocks are replaced by prefabricated ones. Fastening is carried out using a key and pins;
- the pulley unloads the transmission to the speed box housing, which allows reducing the forces acting on the input shaft of the speed box and using a shaft with lower weight and size characteristics in the design;
- different heat treatment is assigned for gear and pinion (hardening plus high tempering (... 35 40 HRC). Machining of the toothed rim, vol. followed by low leave (50... 52 HRC).
List_3_KS_Svertka_A1.cdw

List_1_Kinematicheskaya_skhema_A1.cdw

Val.cdw

Shesternya.cdw

Kryshka.cdw

List_1_Kinematicheskaya_skhema_A1.cdw

List_2_KS_Razvertka_A1.cdw

List_3_KS_Svertka_A1.cdw

Shesternya.cdw

Shkiv.cdw

Val.cdw

Shkiv.cdw

Kryshka.cdw

List_2_KS_Razvertka_A1.cdw

Similar materials
- 22.01.2022