Course project "Development of the manufacturing process of the part" Cover "and stamp design"




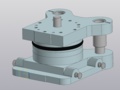
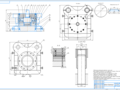
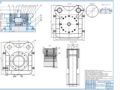
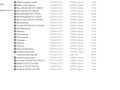
- Added: 06.04.2021
- Size: 3 MB
- Downloads: 3
Description
Course project "Development of the manufacturing process of the part" Cover "and stamp design." In this work there are 3E stamp models, calculation of drawing parameters of a part, calculation of design parameters of a stamp, economic justification of selection of this stamp. Also a complete manufacturing process of the part, a sketch map, and a route no-operation map.
Project's Content
![]() |
![]() |
![]() ![]() ![]() ![]() |
![]() |
![]() ![]() |
![]() ![]() |
![]() ![]() |
![]() ![]() |
![]() ![]() |
![]() ![]() |
![]() ![]() |
![]() ![]() |
![]() ![]() |
![]() ![]() |
![]() ![]() |
![]() ![]() |
![]() ![]() |
![]() ![]() |
![]() ![]() |
![]() ![]() |
![]() ![]() |
![]() |
![]() |
![]() |
![]() ![]() |
![]() ![]() |
![]() ![]() |
![]() ![]() |
![]() ![]() ![]() ![]() |
![]() ![]() ![]() |
![]() ![]() ![]() ![]() |
![]() ![]() ![]() ![]() |
![]() ![]() ![]() |
![]() |
![]() ![]() ![]() ![]() |
![]() ![]() ![]() ![]() |
Additional information
Contents
CONTENTS
INTRODUCTION
1 Process section of the project
1.1 Part Constructability Analysis
1.2 Drawing up versions of the part manufacturing plan and choosing the appropriate one
1.2.1 Drawing up versions of the part manufacturing plan
1.2.2 Determination of the batch size for starting parts into production
1.2.3 Normalization of versions of the part production plan according to the enlarged standards and determination of its labour intensity
1.2.4 Calculation of part process cost
2 Calculation of process parameters
2.1 Calculation of workpiece dimensions
2.2 Selection of sheet cutting option
2.3 Selection of scissors
2.4 Calculation of blank cutting force
2.5 Selection of cutting press
2.6 Determination of the number of drawing operations
2.7 Calculation of drawing force
2.8 Selection of press for drawing operation
2.9 Calculation of allowance cutting force
2.10 Selection of press for allowance cutting
3 Development and design of routing and operational process
4 Design section of the project
4.1 Substantiation of the structural diagram of the stamp
4.2 Description of the stamp design
4.3 Determination of tool actuating dimensions
4.5 Organization of the stamping machine workplace
4.6 Safety precautions for sheet stamping
CONCLUSION
LIST OF SOURCES USED
Paper
Course design: 33 pages, 5 figures, 1 table, 3 annexes, 15 sources.
Graphic documentation: 1 sheet of A0 format, 2 sheets of A3 format, 4 sheets of A4 format.
PART, MANUFACTURING PROCESS, PROCESS MAP, GUILLOTINE SCISSORS, PRESS, DRAWING, BILLET.
The object of the study is an axisymmetric part, material Steel 20, thickness 1 mm.
Purpose of work:
- perform part design analysis;
- determine the size of the workpiece;
- develop a map of sheet cutting;
- determine the punching force of the workpiece and punching holes in the tool die;
- select the press to perform the combined operation on the equipment catalog;
- determine the drawing force of the workpiece;
- select the press to perform the drawing operation;
- develop and execute the routing process of part manufacturing on the Job Instructions forms.
As a result of the work, all the necessary sizes, forces and equipment were determined, a package of technical documents was drawn up.
Introduction
The reliability and durability of the aircraft, assemblies or assemblies of the machine depends on the quality of the parts from which it is assembled. The quality of the part is to a large extent determined by the workpiece, which is obtained by one or another method: casting, welding, cutting or pressure treatment - bulk or sheet stamping.
In the mass-produced machine-building industry, the most common use was made of sheet stamping tools, i.e. using tool dies. The development of machine-building production is based on the improvement of technological processes and methods for calculating the deformation characteristics of sheet stamping operations. This, as well as increasing requirements for product quality, while minimizing material and energy costs, requires ensuring a high level of technological training for university graduates.
On the basis of numerous experimental and theoretical studies conducted by researchers and factory technologists, calculation methods, as well as general rules and standards for the design of sheet stamping technological processes, have been developed. Their use guarantees high operational characteristics of the obtained parts, minimizing power consumption, reducing the labor intensity of stamping; increase of resource saving (increase of material usage coefficient). All this makes it possible to expand the technological capabilities of sheet stamping.
Drawing is a process of converting a flat blank into a hollow part of any shape (or further changing its dimensions) and is carried out on drawing dies.
Prepare Part Fabrication Plan Versions and Select Appropriate Parts
Prepare Part Fabrication Plan Versions
The comparative complexity and duration of production preparation, the high cost of dies require a particularly careful and thoughtful development of the stamping process. In this regard, when designing the process, we will draw up several versions of the manufacturing plan for the part. Of these, we will choose the most appropriate option, and on the basis of it we will develop an extensive technological process, for which further calculations are being carried out.
Consider two manufacturing schemes for the part.
1 Variant
Cut the sheet into stripes
Cutting down the workpiece
Part Drawing
2 Variant
Cut the sheet into stripes
Blanks cutting and drawing
We will evaluate the two production diagrams of the part and choose from them the most expedient.
Conclusion
Inthis work, the technological process of manufacturing the part by drawing was developed, the processability of the part design was analyzed, the dimensions of the billet 164.5 mm from the material Steel 20 S = 1.0 mm were determined, the most profitable version of cutting the sheet with a size of 171.7 × 1000 mm was calculated, and the parameters of cutting the billet and drawing were calculated. Equipment was selected for these operations.
A routing process for manufacturing the part has been developed. The drawing die is constructed. Working drawings of the die are made. Health and safety requirements for the stamping operation are described.
103 ПК 01. 65101 01 000.801.spw

БУфер кольцевой сжатый__.m3d

Буфер у выталкивателя__.m3d

Винт 1092-2051_060 ГОСТ 18786-80.m3d

Винт 7095-0021 ГОСТ 8922-69.m3d

Винт М10-6gx100 ГОСТ 11738-84.m3d

Винт М10-6gx60 ГОСТ 11738-84.m3d

Втулка 1032-2755 ГОСТ 13120-8333.m3d

Выталкиватель.m3d

Колонка 1030-6103 ГОСТ 13118-8333.m3d

Конечная деталь__.m3d

Матрица__.m3d

Плита верхняя.m3d

Плита нижняя.m3d

Подкладка.m3d

Прижим__.m3d

Пуансон__.m3d

Пуансоно держатель__.m3d

Хвостовик 1034-0627 ГОСТ 16715-7111.m3d

Штифт 10-120 ГОСТ 3128-7000.m3d

Штифт 10-70 ГОСТ 3128-7000.m3d

Штифт 6-16 ГОСТ 3128-7000.m3d

Выталкиватель.cdw

Матрица.cdw

Прижим.cdw

Пуансон.cdw

СБ.cdw

Similar materials
- 09.02.2015
- 29.07.2014