Construction of a multi-storey residential building in St. Petersburg



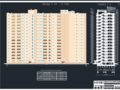
- Added: 30.06.2021
- Size: 6 MB
- Downloads: 3
Description
VKR on the construction of a multi-storey residential building in St. Petersburg
Project's Content
![]() ![]() ![]() ![]() |
![]() ![]() ![]() |
Additional information
Contents
Introduction
Characteristics of the construction area
Architectural and construction section
Calculation of Master Plan
Structural solution of the building
2.3 Engineering Systems and Equipment
2.4. Vertical transport
2.5. Electrical equipment
3 . Design section
3.1.1 Calculation of cast-in-situ flooring without beam reinforced concrete slab
3.1.2 Construction of reinforcement grids of cast-in-situ reinforced concrete slab
3.2. Calculation of precast reinforced concrete march
3.2.1 Determination of loads and forces
3.2.2.Presubscribe the size of the march
3.2.3. Selection of longitudinal reinforcement section area
3.2.4. Calculation of inclined section for transverse force
3.2.5 Calculation of ribs by deformations (deflections)
3.2.6 Calculation of stair flight deflection by approximate method
3.2.7.Recalculation by long-term crack opening
3.2.8.Recalculation by short-term crack opening
4. Procedure of works execution
4.1 Job Instruction for Earthworks
4.2 Job Instruction for Installation of Stair Flights
4.3 Job Instruction for Soft Roof Device
5. Organization of construction
5.1Development and calculations of the master work plan
5.2Building and calculations of the construction plan
6. Economic section
7. BJD Section
7.1 Occupational Safety
7.2. Civil Protection Measures
8. List of used literature
Introduction
One of the important problems for the Russian Federation and St. Petersburg in particular is the housing problem. The right and only way to overcome this problem is the intensive construction of residential buildings. Construction, being labor-intensive, material-intensive, capital-intensive, energy-intensive and knowledge-intensive production, contains a solution to many global and local problems, social, environmental. Cost reduction in architecture and construction is carried out by rational space-planning solutions of buildings, correct selection of construction and finishing materials, design facilitation, improvement of construction methods. The main economic reserve in urban planning is to increase the efficiency of land use. Currently, construction is carried out by large construction organizations that have advanced technologies, equipment, highly qualified permanent personnel and engineering and technical workers, as well as on the basis of progressive labor methods using efficient construction materials.
The diploma project reveals the possibilities of designing buildings that are most rationally inscribed in urban conditions. Therefore, a residential building was developed, which is the main type of housing in the cities of our country. Such houses allow rational use of the territory, reduce the length of engineering networks, streets, and urban transport structures. A significant increase in the density of housing stock (the amount of living space (m ²) accounted for 1 hectares of built-up territory) during residential development gives a noticeable economic effect. In addition, their high-altitude composition contributes to the creation of an expressive silhouette of development. To achieve this goal, it is necessary to use local building materials, that is, to reduce the cost of construction.
Structural solution of the building
The structural part of the residential building was developed on the basis of an individual project of a 16-story residential building made of ceramic brick with monolithic floors and a foundation, as well as in accordance with "recommendations for the design of structures of arceless buildings."
The choice of the direction of the structural walls is economically due to local features. Since the building is being built in an area with an estimated temperature of up to - 30 ° C, it is most advisable to build a building with longitudinal load-bearing walls.
Bases
The foundation for the building is solid of heavy concrete of class B30. It is made in the form of a flat plate and a pile field, as well as cross belts under the entire building.
The basement walls of the building are made of monolithic reinforced concrete with bitumen waterproofing made in two layers. Concrete class B25.
Enclosing structures
External enclosing walls are laid out of bricks of ordinary, full-body, single size 1NF, strength grade M150, average density class 2.0, frost resistance grade F50 with designation according to the standard (Brick KORP 1NF/150/2.0/50/GOST 5302007) Wall thickness (pie) 640mm.
Outside, the facade is finished with a protective layer of plaster with the brand Ceresit CT137 with reinforced glass mesh and mineral wool boards of the Facad BATTS brand (TC07072003). Internal walls are plastered with plaster mortar.
Internal surfaces of exhaust channels in walls are sewn with liquid clay sand solution.
In deformation seams, two layers of toll are laid along the entire height of the building and meticulous hemp is milled or mineral wool. Outside, the seams are sealed with cement mortar.
To preserve the monolithic nature of the load-bearing walls, ventilation channels are made in masonry (without switching on the ventilation units). Horizontal masonry seams are reinforced along the entire height with continuous belts in the level of floors, a place in areas weakened by niches and channels and exposed to concentrated loads (under and above beam-bridges), as well as additional angular connections in the lower floors.
Sanitary units are enclosed by ceramic concrete panels of partitions 60 mm thick, doubled in abutments to living rooms. Partitions are mounted at the end of floor wall masonry. Their panels are installed on soundproofing gaskets wrapped with a strip of ruberoid, and are fastened with propeller fasteners. The partitions are inter-apartment and inter-room, respectively, made of double and single gypsum concrete panels 80 mm thick.
Coverings and Floors
It is made of monolithic reinforced concrete since the erected building has atypical spans and a complex shape, of a beam-free type, 160 mm thick. Beam-free floors and coverings are flat slabs resting on walls. The use of floors and coatings of this type is due to the need to have a smooth ceiling. Coatings and floors are made using plywood metal formwork from Aluma System.
Ladders
The building uses large-element stairs. They consist of marches and platforms resting on the transverse walls of the building. The stairways are divided into the main ones - located between the floors, the basement - between the floor of the first floor and the porch and the basement - between the porch and the floor of the basement. They serve to communicate with floors and ways of evacuating people in case of emergency and fire.
Stairs use stairs and slab platforms. Frieze stages can be attributed to marches and sites. Accordingly, the slot in the rib of the march setting pad is the same in length or different in depth for descending and ascending marches. The last option avoids a seam at the floor level of the site. The upper platform always has a frieze stage in place of the ascending march.
The minimum width of the march, designed for oncoming traffic, is 1.05 m (recommended slope). The maximum width of the march, providing a safe descent of the crowd, 2.4 m.
Staircases are placed at and between floor levels. The width of the staircases is from 1.2 m, the interfringes are at least the width of the march, in front of the entrance to the elevator with open doors - 1.6 m. They are embedded in the masonry of brick walls with special protrusions. Special niches are provided in panels for support of intermediate platforms. Because the stair structures contribute to the stiffness of the building, the walkways and platforms are also welded together.
Height of flight fences is 900mm. Railings (railings) are arranged from steel links welded to embedded parts in the side plane of the march. The fence of the upper platform is attached in special sockets along the edge of the frieze stage, which are then marked with cement mortar. The handrail is made of plastic.
Windows
Jumpers above openings made of prefabricated reinforced concrete beams. The lower front row of the bridge is laid over the opening on the shelf of the steel corner.
Plastic glass windows PVC 4-chamber 2-section companies REHAU S730 Thermo Design are accepted.
1. Design principle
"The structure of the cells. A characteristic feature of the REHAU S730 Thermo Design window profile system is the section structure of the profiles on the principle of a four-chamber system. At the same time, the prechambers located outside and inside provide optimal heat protection, as well as - through the chamber located on the outside - a simple and hidden drainage. The presence of a large reinforcement chamber allows you to place in it metal profiles of the optimal section that meets static requirements.
- Location of seals. Due to the same thrust seal for the box and flap with a wide abutment surface, which runs along the entire perimeter of the window, excellent values of air permeability (coefficient "a") are achieved - load groups A, B and C.
2. System composition
- Two types of box profiles with different optical width, depth 60mm;
- Mullion/cross-piece profile 60 mm deep;
- Profile of single-plane flap with depth of 76 mm;
- Slat profile for balcony door;
- All profiles from REHAU S730/
3. Scope and types of opening
Depending on the purpose of the application, the REHAU S730 Thermo Design window system in combination with the REHAU S730 system allows you to make windows of various types of opening, as well as types of flaps for both reconstructed and new buildings of industrial and civil construction:
- Swivel windows and doors;
- Swivel-folding windows and doors;
- Folding windows;
- Windows and balcony doors of several parts, separated by mullions and crossbars;
- Double-leaf windows without rigid mullion;
- Curly and arched windows;
- Sloping and sliding doors.
4. Locking device
Due to the presence of slats in the profiles and the thrust profile for the average abutment of the window without a rigid mullion, a slot for fixing the device corresponding to the European norm (europase), all standard window locking devices of various manufacturers can be used.
5. Materials
- REHAU Window Profiles
The window profiles of the REHAU S730 Thermo Design system are made of RAUPVC, non-plasticized, specially designed for external use of polyvinyl chloride with high toughness according to DIN 7778. With 01.01.89, REHAU window profiles are manufactured without cadmium additives.
- REHAU window seals
Seals are made of RAUSR, EPDM elastomer, or RAUSIK, silicone elastomer.
The EPDM material has a number of characteristic properties, such as, for example, light atmospheric and ozone resistance. The area of long-term elasticity lies within the temperature range from 40 ° C to + 120 ° C.
REHAU silicone seals are excellent in elasticity and long-term elasticity even at temperatures up to 60 ° C. Due to this, the power loads on the locking device in winter are significantly reduced and their service life increases. Such seals can have different colors, the most common are white silicone seals.
6. Technical and technological features of the system
- Ventilation holes are performed by simple milling operation and hidden due to the structure of the external prechamber of the flap;
The drainage in the box is also hidden through the external prechamber. Water diversion can occur both forward and downward;
- The load-bearing parts of the locking device and hinges are attached by screws to the box or flap through at least two PVC walls or additionally through steel reinforcement;
To secure the thrust profile (studs) and parts of the device to the flap (for example, locking mechanism), special lugs are made in the flap profile to guide and firmly attach the screws;
Due to the 20 mm high surfacing, the edge zone of the glass pack is reliably protected from the destructive effects of UV rays;
- Staples with one leg snap along the entire length and provide reliable and durable fixation of glasses and double-glazed windows. A wide range of staples with extruded seal petals and various seal profiles makes it possible to use fillings of different thicknesses;
-Used reinforcement profiles are also used in S730 Basic Design and Brilliant Design. This simplifies the window manufacturing process and reduces storage costs;
- Thrust special bead in reinforcement chamber allows to use reinforcement without one shelf. In this case, it is not necessary to mill the handle holes through the steel mesh;
- Docking legs on the profiles of boxes give wide possibilities of various options of abutments to openings, transitions to finishing panels, joints of elements of seclusions with support profiles, etc.;
- Import or crossbar milling contour for sash and box mounting are the same.
7. Technical and economic features of the system
- External and internal contours of the seal of the inlet guarantee high water and air resistance;
- REHAU S730 Basic Design system window attracts elegant and harmonious design;
Due to the height of the plug of the box 20 mm from the outside of the window, the width of the fit of the seal is 8 mm. In combination with an internal fit with a width of also 8 mm, the seams are impermeable to load group C;
- Rain moisture penetrated into the falcon area is reliably discharged through a sufficiently wide profile chamber;
- Sloping folds ensure complete removal of penetrated moisture from the folds;
- The smooth surface of the base of the box counterfeit makes the removal of contaminants simple and easy.
Doors
Doors according to GOST 309702002 are provided to enter the premises. The entrance doors to the entrance are blind double-floor. The entrance doors to the apartment are deaf single-floor. The entrance doors to the common room are glazed single-floor. Balcony doors glazed single floor. All door types are swept.
To create balcony doors, plastic four-chamber PVC windows from REHAU S730 Thermo Design are accepted (see "Windows").
Floors
In a residential 16-story brick house in residential rooms are provided from piece parquet. Rivet with oblique edge is glued with KN glue - to cement-cloth brace. The joint of the floors in the doorways is flush with the plane of the door canvas. Individual parquet rivets are laid in place. The mounting seam in the underlying layer is filled with cement sand mortar.
The floors in the kitchens are made of linoleum on a warm basis (topoflex). Before laying, linoleum webs are painted and welded into a carpet exactly corresponding to the room. Unlike the usual linoleum, this carpet for preserving the elastic properties of a warm base is rolled dry directly along the reinforced concrete slab of the floor and covered with plinths. Above the cold underground, insulation from polystyrene cement slabs is glued to the reinforced concrete slab from below.
Heat and soundproofing gaskets are made of mineral wool plates, the steam insulation device eliminates condensate precipitation.
Prior to the laying of the underlying layer, the flooring of reinforced concrete slabs shall be carefully ground with the elimination of minor surface defects - cracks, holes, shells. In cement ties of the underlying layer, cracks, potholes and open seams are also not allowed. Horizontal tightening is checked by control rack with level.
When adjoining the floors to the walls, special attention is paid to sound insulation. Floors are separated from walls, partitions and pipelines by elastic gaskets made of the same materials as sound insulation gaskets of the underlying layer. Gaps of about 10 mm in the abutments of the floors to the walls are covered by plastic plinths. At the same time, plinths are attached to walls with a gap of 1-2 mm from the floor.
In sanitary units and corridors, floors are made of ceramic tiles on cement mortar. In sanitary units, a waterproofing carpet is placed on a wall to a height of 0.3 m. A plinth of ceramic tiles is arranged on top of it on cement sand mortar reinforced with steel mesh. The difference in floor levels in sanitary units is compensated by the slope of the row of tiles adjacent to the joint.
Roof
The roof (with a roof slope of 0.02) is two-layer rolled, built-up (stisol is built-up) with an internal drain. Roof flooring is made of cast-in-situ reinforced concrete covered with leveling bracing made of cement mortar 15 mm thick. There are water intake funnels. Ventilation channels are brought out above the roof in the walls of the elevator machine room. Leads of ventilation channels are protected by wind shields.
Engineering systems and equipment
The building is equipped with cold and hot water supply systems, sewerage system, heating and ventilation systems, as well as vertical transport and related electrical equipment.
Water supply and drainage:
Cold water supply
Water is supplied for household and drinking needs, internal fire extinguishing, irrigation of the territory, production needs, make-up of the heating system.
The following water supply systems are designed in the building:
drinking water supply system;
fire-fighting water supply system;
Water meters are installed at the water supply inputs in a special room, immediately behind the outer wall. Water meters are also installed on branches to water supply systems of built-in institutions and on branches to apartments.
Behind the meters are installed apartment fire cranes.
Internal networks of domestic drinking water supply are looped by inputs.
Internal networks of fire water supply - ring.
Fire pumps are installed to supply water to the fire water supply system:
Fire pumps/1 operating, 1 standby/type K6550160, with power of 5.5kW, capacity of 7 l/s, head 56 m.
Hot water supply
In the building, a centralized hot water supply system is designed with direct water intake through an individual heat station (ITP).
The diagram of the hot water pipeline is circular with lower wiring.
Hot water meters are installed on branches to the hot water supply system of built-in institutions and on branches to apartments.
Main pipelines are laid under the basement ceiling.
Main lines, connections to risers, risers are isolated from heat losses.
Internal networks of hot water supply are made of metal-polymer pipes.
Water disposal
Internal sewage systems are designed in the building:
domestic sewerage - for waste water removal from sanitary and technical devices of residential part;
domestic sewerage - from sanitary devices of built-in institutions exhaust part of systems - general;
industrial sewerage - for waste water disposal during flushing of heating systems;
internal drains - to divert rainwater and meltwater from the roof.
Domestic sewage networks are made of cast-iron sewage pipes GOST 694298, internal drain - of steel electric welded pipes GOST 1070491 in corrosion-resistant insulation.
Heating and ventilation:
Heating
Heating systems are connected from heating centers located in the basement.
For the residential part of the building, a double-tube heating system with lower routing of main pipelines is designed.
Coolant parameters 9570 ° C.
Steel panel radiators "Imas" are adopted as heating devices.
Air removal from heating systems is carried out through manual air exhaust plugs at the devices on each floor, as well as through Wind automatic air vents installed on each riser.
Optimum room temperatures are controlled by Danfoss RTDN temperature controllers installed on the heating devices. ASVM shutoff valves and ASVPV balancing valves are used as shutoff valves on risers.
For built-in rooms, a single-tube horizontal heating system with coolant parameters of 9570 ° C is provided.
Steel radiators RSV4 are used as heating devices.
Ball valves are provided for adjustment of heat transfer of instruments.
Air removal from the systems is carried out through air outlet plugs located at the instruments and at higher points.
Manual balancing valves USVI and ball valves shall be used as disconnecting valves on heating system branches.
Ventilation
In the residential building designed exhaust ventilation with a natural urge. Ventilation is brought to the roof.
Vertical transport
In each section of the building there are two elevators, lifting capacity 400 and 630 kg. The manufacturer is the Shcherbinsky Elevators plant.
Brief characteristics of elevators:
1. passenger elevator g/p 400kg for 16 stops, with a lifting height of 54.6 m. Lifting speed 2.0 m/s. The cabin with a capacity of 5 people has dimensions in the plan 980x1060 mm (width x depth). The cabin doors and shafts are automatic sliding with a width of 700 mm. Blind shaft with plan dimensions of 1580x1730 mm (width x depth). Pit depth 1400mm. The machine room is upper. Fire resistance of shaft doors is 0.5h.
2. passenger elevator gr/p 630kg for 16 stops, with a lifting height of 54.6m. Lifting speed 2.0 m/s. The cabin with a capacity of 8 people has dimensions in the plan 2100x1060 mm (width x depth). The cabin doors and shafts are automatic sliding with a width of 900mm. The total width of the doors is 1200mm. Blind shaft with plan dimensions of 2580x1730 mm (width x depth). Pit depth 1400mm. The machine room is upper. Fire resistance of shaft doors is 0.5h.
Electrical equipment
The main consumers of electricity of the designed residential building are:
- electric motors of fans and pumps;
- elevators;
- process electric receivers of PBX, control room and security rooms;
- consumer electric receivers;
- electrical receivers of security and fire alarms;
- external lighting;
- internal electric lighting.
All electric receivers of the designed residential building are low-voltage and are powered at 3NPE ~ 50Hz, 220/380V voltage from the designed inlet switchgears (GPU No. 1 and GPU No. 2) installed in the electric switchgears on the 1st floor .
In terms of ensuring the reliability of power supply, fire pumps, smoke removal and air pressure fans in case of fire, fire alarm devices, elevators, emergency lighting and electric receivers of individual heat points (ITP1 and ITP2) belong to the first category according to PUE, the remaining electric receivers of a residential building - to the second category..
All electrical receivers of the designed apartments are low-voltage and are powered at voltage 3NPE ~ 50Hz, 220/380V from the designed apartment boards (SCH) with protective shutdown devices (RCD) and electric power metering devices at the input.
The supply of apartment boards is provided from the corresponding storey combined electric panels with a compartment for low-current devices of the type of SHRE of the recessed type, installed on each residential floor in the floor corridors of a residential building in brick niches.
The height of installation of electrical installation products in apartments from the floor is:
switches - 1 m;
sockets in the kitchens of apartments - 0.9 m;
sockets in other rooms - 0.35m;
Electrical wiring in apartments, offices, corridors and stairs is provided for hidden and replaced by copper cables of the IWG brand. Cables shall be laid in PVC pipes in cast-in-situ walls and floors laid during their manufacture at the facility, as well as in bars of walls made of brick and slag concrete under a layer of plaster or in voids of partitions made of gypsum board.
Cable passes through walls and floors are provided in sections of steel pipes. After the cables are laid, the gaps in the pipes are sealed with non-combustible and easily penetrable material in accordance with SNiP 3.05.0685 and VSN 3382.
Evacuation lighting is provided with lamps with "Exit" indicator.
Emergency lighting of safety at voltage 1NPE ~ 50Hz, 220/380V is provided in rooms of control room, communication unit, electric panels, security, concierges, machine rooms of elevators, individual heat stations.
Lighting fixtures for the entrances to the building, garbage collection chambers, license plates are provided to be connected to the emergency lighting network.
Lightning protection
The designed building is protected from direct lightning strikes, using a lightning screen made of round steel with a diameter of 8mm with a cell pitch of no more than 10x10m, which is laid on the roof of the building under the insulation layer. The lightning-receiving grid is arranged with current leads made of round steel, with a diameter of 8 mm, laid along the perimeter of the building at least every 25 m, is connected to an external grounding conductor (ground loop of zero wire).
Excavation Technology
Removal of the vegetal layer of soil is carried out by bulldozer DZ42.
Rough development of the pit is performed by excavator EO4121, equipped with a reverse shovel with a bucket with teeth with loading on transport. The development of soil in the pit should be started from axial penetration, in the future work should be carried out by longitudinal penetration. Attach axes of excavator movement with hangers, two on each side in the area of visibility on the day surface.
Transportation of soil is performed by KamAZ-45143 dump truck with its unloading not closer than 10 m from the slope of the pit. Supply soil in the sinuses from the dump with bulldozer DZ42. During backfilling of sinuses perform layer-by-layer compaction of soil using electrical tamping IE4502. Thickness of compacted soil layer is 0.4m. The number of passes in one trace is 4.
Job Instruction for Installation of Staircases and Flights
Scope of Application
The process map was developed for the installation of staircases and flights of stairs, during the construction of a residential sixteen-storey building at the address: St. Petersburg, Vyborg district.
Organization and procedure of works execution
The works considered by the Job Instruction include:
- unloading of stair flights;
- installation of stair flights;
- installation of fencing;
- welding works;
- anti-corrosion coating of welded joints;
- termination of joints.
Installation of stair flights is performed in accordance with the requirements of federal and departmental regulatory documents, including:
- SNiP 12.012004. Organization of construction;
- SNiP 3.03.0187. Bearing and enclosing structures;
- SNiP 12.032001. Labor safety in construction. Part 1. General requirements;
- SNiP 12.042002. Labor safety in construction. Part 2. Construction production;
- PM 0122000 SWEAT. Intersectoral rules on labor protection at work at height;
- SanPiN 2.2.3.138403. Ministry of Health of the Russian Federation. Hygienic requirements for the organization of construction and construction works.
Performers:
a worker performing installation work, senior in a link;
a worker performing installation work;
a worker performing rigging operations.
Job Instruction for Soft Roofing Device Made of Roll Built-Up Material
1. Scope of Application
1.1. The Job Instruction has been developed for the device of soft roof made of the built-up roll material of isoplast .
1.2. The roll material consists of a cardboard, fiberglass or polyester base coated on the outer side with a layer of bituminopolymer binder, and on the inner side with a floating layer of bitumen mastic, which allows it to be used for the device of one-, two- and three-layer roofs without gluing mastic. The base is a reinforced concrete slab. Roll materials of different modification are provided for arrangement of lower and upper layers. The roll material type must match the design.
1.3. The works considered by the Job Instruction include:
- surface preparation (cleaning and drying);
- steam insulation device;
- arrangement of cement-part bracing;
- heat insulation layer arrangement;
- installation of gutters;
- surface bending with primer;
- roll carpet sticker (2 layers);
- adjoining device.
1.4. Installation of a soft roof made of built-up roll materials is carried out in accordance with the requirements of federal and departmental regulatory documents, including:
- SNiP 12.012004. Organization of construction;
- SNiP 3.03.0187. Bearing and enclosing structures;
- SNiP 12.032001. Labor safety in construction. Part 1. General requirements;
- SNiP 12.042002. Labor safety in construction. Part 2. Construction production;
- PM 0122000 SWEAT. Intersectoral rules on labor protection at work at height;
- SanPiN 2.2.3.138403. Ministry of Health of the Russian Federation. Hygienic requirements for the organization of construction and construction works.
1.5. Materials are supplied to the roof using KBK2 roof crane.
1.6. Work is performed in one shift in summer conditions during daylight hours.
2. Organization and procedure of works execution
2.1. The following organizational and preparatory measures and works shall be carried out prior to the beginning of the works on the foundation and roof covering from the built-up roll material:
- works on construction of load-bearing structures, roof parapets have been performed and accepted;
- embedded parts are installed;
- holes are made to pass communications;
- plastered sections of stone structures to the height of roofing carpet gluing;
- work permit for high-risk work has been issued;
- tools, accessories, equipment prepared;
- materials and products delivered to the workplace,
- performers are familiarized with the technology and organization of works.
2.2. The front of the work in the plan is divided into grabs, and the grabs into plots. Work on the plot is carried out within one day.
2.3. The structure of the base and roof covering from the built-up roll material are made in the following order:
- surface preparation (cleaning and drying);
- steam insulation device;
- heat insulation layer arrangement;
- installation of gutters;
- arrangement of cement-part bracing;
- surface bending with primer;
- roll carpet sticker (2 layers);
- adjoining device.
2.4. Surface dusting is performed with brushes, industrial vacuum cleaner or compressed air jet 1... 2 days before base cutting. The area of the provided area shall not exceed the replaceable working of the link on the cutting.
2.5. Drying of wet sections of the base is carried out by thermal method using heating devices and machines.
2.6. Leveling of the surface of slabs, as well as sealing of chips, potholes and shells with the size of more than 5 mm are performed with cement sand mortar of grade 50. Surface of solution is treated with ironing. The grout layer is maintained in accordance with regulatory requirements.
2.7. Vapour insulation from roll material is laid dry with overlapping of cloth 7 cm and sizing of cloth joints on cold bitumen mastic. Panels are laid starting from lowered sections and water intake funnels.
2.8. At arrangement of thermal insulation from mineral wool plates of increased rigidity on synthetic binder marks are removed, plates are prepared, plates are supplied and transported to coating, plates are laid with gluing with mastic or fixed with plastic buttons, sockets for apron of water intake funnels are cut with knife; water intake funnels are installed.
An insulator roofer with the help of a trolley carries to the workplace and then manually spreads the plates along the area starting from the upper point. Plates are pressed tightly to each other, shells and chips are filled with crumbs. The slabs are glued with bitumen mastic, which is applied in stripes with width 150... 200 mm with pitch 250... 300 mm.
Creation of longitudinal slopes to water-receiving funnels in grooves is carried out by sprinkling of perolisite. The roofer using a knife cuts off sections of the plates, creating smooth slopes to the water intake funnels.
2.9. The cement-part bracing is arranged with a thickness of at least 30 mm in the following order: guides are installed from pipes with a pitch of 1.5... 2.0 m; solution mixture is laid in strips with leveling and smoothing by the rule on guides in 2 stages: first odd strips, and after solidification of the solution in them, even.
Solution mixture is supplied by means of solution pumps through pipes or by means of bogies on pneumatic wheel travel.
Deformation seams with pitch of 4 meters are arranged in the tie-rod. In places of adjoining of roll carpet to walls, parapets, shafts and risers discharge with radius of not less than 100 mm is arranged.
After strength gain, cement-sand brace is cut with cold bitumen primer. Primer is applied with brushes, roller a with roof area more than 200 m.k. - with the help of a cracopult.
2.10. By the beginning of the roofing device, it is necessary to check the quality of the base and compliance with slopes, check the completion of other construction and installation work on the coating, check the availability and completeness of materials for the roofing device, prepare machines and equipment for transport and roofing work, prepare the construction site and workplaces for labor protection and fire safety, check the availability and readiness of tools and devices.
2.11. Webs of roll material are welded or glued by thinning of cover layer onto brace.
2.12. When the roll roof is installed, the processes and operations are performed in the following sequence: preparation of materials, mastic, compositions and parts; arrangement of cornice overhangs; supply of materials, mastic, compositions and parts to the coating; base bending; sticking of additional layers of roll material in places of installation of water intake funnels, flasks; sticking the roll material to the base layers; design of the water insulation layer adjoining the walls, shafts, parapets, pipes; quality control of processes.
2.13. Device of roll roof on grip is made from lowered sections to increased sections. The webs are rolled and glued in the direction opposite to the water flow.
2.16. The abutment of the water-insulating layer to the parapets is formed as follows. Ends of panels of the main roofing coating are brought to the discharge. After that, paintings of roll material with a length of 2... 3 m are prepared and glued to the abutment places. A pattern of roll material is laid on the abutment site and folded in half. First, the lower horizontal part of the picture is glued, and then the mastic is melted at the folded vertical part and pressed against the wall. So glue paintings in the first and subsequent layers. At that it is necessary to comply with SNiP requirements for overlapping in joints.
Previously, proantisepted racks are fixed to the parapet by shooting with dowels or nailing with nails to previously laid plugs, and metal drains are installed after sticking the paintings, they are fixed with self-cuts. Before installation of metal paintings, upper end of roll carpet is washed with hardening mastic.
2.17. Arrangement of roll carpet in places of installation of water intake funnels is performed in the following order. Before gluing the layers of the main roof coating, the marks of the made tie or the laid rigid insulation are checked (Fig. 15). Two layers of glass fabric on hot mastic are glued under collar of water intake funnel.
Then installers install lower branch pipe of funnel with collar. First, hot mastic is applied under collar. Along the perimeter of the collar, the seam is carefully poured with hot mastic. Joint of branch pipe with riser is thoroughly hemp.
After that, the main roof coating layers are glued. The cloths are glued onto the collar, then the hole is cut out.
Water intake funnel cap is inserted with its branch pipe into lower branch pipe. Previously, curable mastic is applied on walls of lower branch pipe. The cap is connected to the lower branch by screws. A seam along the perimeter of the cap is poured with hot bitumen mastic.
2.18. Roofing device is made of links from two roofers, including roofer 4 of category 1, 3 of category -1.
Quality andAcceptance Requirements
4.1. During the construction of the roof from the built-up roll material, production quality control is carried out, which includes: incoming control of materials and products; operational control of roofing works performance, as well as acceptance control of works performed. At all stages of the work, inspection is carried out by representatives of the customer's technical supervision.
4.2. The manufacturer shall accompany each batch of products with a quality document according to GOST 13015.3, which shall indicate:
- name and address of the manufacturer; Document number and date of issue Batch number name and grades of structures; date of fabrication of structures; specification designation.
The document on the quality of the products supplied to the consumer must be signed by the employee responsible for the technical control of the manufacturer.
4.3. Incoming quality control of materials consists in external inspection of their compliance with GOST, specification, project requirements, passports, certificates confirming the quality of their manufacture, completeness and compliance with their working drawings. Incoming control is performed by line personnel upon receipt of materials and products to the construction site. The shape and basic dimensions of the articles shall be as specified in the design.
All products are externally inspected to detect obvious deviations in geometric dimensions from the design. Dimensions and geometrical shape are checked selectively by single-stage control.
чертежи автокад.dwg

Similar materials
- 04.11.2022
- 09.07.2014
- 26.09.2022
- 09.07.2014
- 04.11.2022