Belt conveyor drive - course - machine parts


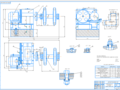
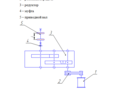
- Added: 26.01.2022
- Size: 2 MB
- Downloads: 1
Description
Course project on DM PNRPU var 02-07
Project's Content
![]() ![]() ![]() ![]() |
![]() ![]() ![]() ![]() |
![]() ![]() ![]() ![]() |
![]() ![]() ![]() ![]() |
![]() ![]() ![]() ![]() |
![]() ![]() ![]() |
![]() ![]() ![]() ![]() |
![]() ![]() ![]() ![]() |
Additional information
Contents
INTRODUCTION
TASK
1. KINEMATIC CALCULATION OF DRIVE
1.1 Electric motor selection
1.2 Determination of drive gear ratios
1.3 Determination of rotation speeds
1.4 Determination of angular velocity
1.5 Determination of torque on shafts
1.6 Determination of capacity on shafts
1.7 Service life of drive device
1.8 Compilation of the final table
2. BELT TRANSMISSION DESIGN
2.1 Design calculation
2.2 Verification calculation
3. GEARBOX CALCULATION
3.1 Slow-moving stage
3.1.1 Material Selection
3.1.2 Transmission Calculation
3.2 High speed stage
3.2.1 Material Selection
3.2.2 Transmission Calculation
4. SKETCHED COMPOSITION
4.1 Calculation of driving shaft diameters
4.2 Calculation of intermediate shaft diameters
4.3 Calculation of driven shaft diameters
4.4 Bearing Selection
5. COUPLING SELECTION
6. CALCULATION OF SHAFTS
6.1 Calculation of high-speed shaft
6.1.1 Determination of support reactions and construction of bending and torques epures
6.1.2 Shaft check calculation
6.2 Calculation of intermediate shaft
6.2.1 Determination of support reactions and construction of bending and torsional moments
6.2.2 Shaft check calculation
6.3 Calculation of low-speed shaft
6.3.1 Determination of support reactions and construction of bending and torques epures
6.3.2 Shaft check calculation
7. BEARING CALCULATION
7.1 High speed shaft
7.2 Intermediate shaft
7.3 Slow-moving shaft
8. CALCULATION OF KEYBOARDS
8.1 Connection of wheel on slow-moving shaft and shaft
8.2 Connecting the wheel on the intermediate shaft
8.3 Connecting the pinion on the intermediate shaft
8.4 Coupling of half-coupling and slow-moving shaft
8.5 Connection of pulley and high-speed shaft
9. GEARBOX DESIGN
9.1 Packing of bearing units
9.2 Housing and Cover Design
9.3 Lubrication Selection
LIST OF LITERATURE USED
LIST OF LITERATURE USED
Introduction
The drive designed in this work consists of a 5.5kW AIR100L2 electric motor, a two-stage cylindrical reduction gear with a torque on a slow-moving shaft 905 Nm and a gear ratio of 22.6 and an open belt transmission with a gear ratio of 2.8. Output shaft of reduction gear is connected to drive shaft by means of clutch. Engine and reduction gear box are attached to common frame. It is welded, consists of channels and is attached to a concrete base. The drive shall provide torque transmission from the electric motor to the actuator with minimum losses and specified angular speed on the output shaft of the reduction gear box .
Gearbox Design
9.1 Packing of bearing units
Seals of bearing units prevent oil leakage and protect the bearing from dust, dirt, acid vapors and other harmful substances that cause rapid wear and corrosion of bearings.
In cuff seals oil-resistant rubber pressed by spring against shaft is used as sealing element. Seals of this type have a low coefficient of friction, create good tightness and have the ability to compensate for wear.
9.2 Housing and Cover Design
Body structures for the purpose of weight reduction are usually thin-walled. It is advisable to increase their strength and rigidity not by thickening the constituent elements, but by rational arrangement of the material and the use of reinforcing ribs, partitions (diaphragms), lugs (bosses), etc.
Gearbox housings and covers are rather complex in shape and are typically cast from SCh 1228 or SCh 1532 cast iron.
Mutual position of housing base and cover is fixed by two conical pins installed before bore of seats for bearings; body base and cover are bolted together. Gaskets are not installed in the place of the connector, since the bearing fit in the housing can be disturbed. To prevent oil leakage, the connector area is sealed. Inspection window closed by cover is made in upper part of reduction gear box for inspection of oil engagement and filling. In case a large amount of heat is generated in the reducer, to prevent pressure increase inside the housing and air leakage together with oil to the outside, a perfume is installed through the seals in the cover of the inspection hatch.
In the lower part of the housing, a threaded hole is made for lowering the spent oil and washing the reduction gear box. The hole is closed with a plug with a gasket made of oil-resistant rubber or leather.
Two push-out bolts are installed on the cover flange to facilitate separation of the cover from the housing during disassembly of the reduction gear box.
9.3 Lubrication selection.
Crankcase lubrication is carried out by dipping the gears into the oil bath, and in order to avoid significant losses for mixing oil at high circumferential speeds, the gears are immersed at no more than the height of the tooth.
This type of lubricant is usually used for gears at circumferential speeds in engagement up to 12 m/s.
In multistage gears, the diameters of the wheels of individual stages can vary significantly in size, this will cause immersion in the oil of some wheels to a greater depth. Immersion of the slow-moving stage wheel in oil to a depth of more than one third of the radius is not allowed. If the circumferential speeds are high, the oil level is set on the wheel with the maximum diameter to reduce the mixing and spraying losses, and the lubrication of the other stages is carried out using an oil mist.
During dipping lubrication, the volume of the oil bath of the reduction gear box is set at 0.51.0 liters of oil per 1 kW of transmitted power. Oil from common oil bath is used for lubrication of bearing units. At that oil penetrates into bearings in the form of splashes or oil mist.
The oil volume is 3-6 liters. Oil grade is selected according to Table 10.29 [2, p. 255]. At a contact tension σН <600 N/mm2 and district speeds of teeths of v= up to 2 m/s we choose I-G-A-68 oil.
Spetsifikatsia2.spw

Reduktor_2.cdw

Val_A2.cdw

Koleso_A3.cdw

spetsifikatsia.spw

Obschiy_vid.cdw

Reduktor_1.cdw

Similar materials
- 26.10.2015
- 04.06.2015