Apartment building with built-in retail premises


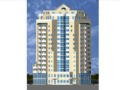
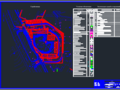
- Added: 02.02.2021
- Size: 66 MB
- Downloads: 4
Description
Residential complex - diploma
Project's Content
![]() |
![]() |
![]() ![]() ![]() |
![]() |
![]() |
![]() |
![]() ![]() ![]() |
![]() |
![]() ![]() ![]() ![]() |
![]() ![]() ![]() |
![]() ![]() ![]() |
![]() ![]() ![]() |
![]() |
![]() ![]() ![]() |
![]() |
![]() |
![]() ![]() ![]() |
![]() ![]() ![]() ![]() |
![]() ![]() ![]() |
![]() ![]() ![]() |
![]() |
![]() ![]() ![]() |
![]() ![]() ![]() ![]() |
Additional information
Contents
Introduction
1. Project Feasibility Study
1.1 Basis for project development
1.1.1 Design Input
1.1.2 Brief description of the object
1.1.3 Design capacity data of the facility
1.1.4 Fuel, water and electricity demand data
1.1.5 Information on the order of construction and urban planning complexes
1.1.6 Main technical and economic indicators of the residential complex project
1.1.7 Information on the approved design solutions
1.1.8 Basic solutions to ensure the living conditions of people with limited mobility
1.2 Information on engineering-geological, hydrogeological conditions of the construction area
1.2.1 Climatic conditions
1.2.2 Geomorphological conditions
1.2.3 Geological structure of the site
1.2.4 Hydrogeological conditions
1.2.5 Physical and geological processes and phenomena
1.3 Solutions and main indicators for the plot master plan and site improvement
1.4 Substantiation of the architectural and construction solution of a residential building No.
1.5 Protection of historical and cultural monuments
1.6 Compliance of space-planning and structural solutions with requirements and specifications established by the customer
1.7 Finishing of the building
1.7.1 Interior Finishes
1.7.2 Exterior Finishes
1.8 Considerations for the organization of construction
1.8.1 General Information
1.8.2 Characteristics of the object
1.8.3 Duration of residential building construction
1.8.4 Labour intensity and need for construction personnel
1.8.5 Organizational and technical measures
1.8.6 Production methods and technology
1.9 Electrical, explosion and fire safety measures
1.10 Measures to protect building structures from corrosion
1.11 Anti-Radiation Requirements
1.12 Water Supply and Sanitation Solutions
1.12.1 Water supply
1.12.2 Drainage
1.12.3 Internal water supply and sewerage
1.13 Heating and ventilation
1.13.1 Initial data for heating and ventilation design
1.13.2 Main Heating and Ventilation Solutions
1.14 Smoke protection and smoke removal
1.15 Power supply and electrical equipment
1.15.1 Power supply
1.15.2 Power electric receivers
1.15.3 Electric lighting
1.15.4 External electrical lighting
1.15.5 Lightning protection and grounding
1.15.6 Measurement and accounting of electricity
1.16 Communication
1.16.1 Telephony
1.16.2 Television
1.17 Protection of the environment
1.17.1 Brief information about the designed object
1.17.2 Protection and management of land resources
1.17.3 Planned environmental measures during construction
1.17.4 Protection of the air basin of the site area against pollution
1.17.4.1 Summary of physical, geographical and climatic conditions of the area and construction site
1.17.4.2 Characteristics of atmospheric air pollution level in the area of the facility location
1.17.4.3 Effect of the object on atmospheric air and characteristics of pollutant emission sources
1.17.4.4 Measures to control emissions under adverse meteorological conditions
1.17.4.5 Air Basin Monitoring Methods and Tools
1.17.5 Protection of surface and groundwater from depletion and pollution
1.17.6 Soil protection
1.17.7 Environmental protection in waste management
1.17.8 Protection of the environment from industrial noise and vibrations
1.17.9 Forecast of changes in the state of the environment under the influence of the designed object
1.18 Thermal design of the outer wall
1.18.1 Initial data
1.18.2 Procedure of Heat Engineering Calculation
2 Foundations and foundations
2.1 Physical and mechanical properties of soils
2.2 Calculation of the basis
3 Construction structures
3.1 General Information
3.2 Final Elements
3.3 Materials and Boundary Conditions
3.4 Loads and Loads
3.5 Calculation for own fluctuations
3.6 Calculation for forced fluctuations
3.7 Static Structural Calculation
3.8 Reinforcement of elements
3.9 Calculation using synthesized accelerograms
3.10 Composition of calculations of building structures
3.11 Conclusions and recommendations
4 Technology of construction production
4.1 Job Instruction
4.1.1 Scope of Job Instruction Application
4.1.1.1 Characteristics of operating conditions
4.2 Construction Process Organization and Technology
4.2.1 Preparation of the facility and requirements of readiness of previous works
4.2.2 Composition of works included in Job Instruction
4.2.3 Material warehousing and stock
4.3.1 Calculation of labor costs
4.4 Methods and sequence of works
4.4.1 Formwork and reinforcement of walls and floors
4.4.2 Concreting of walls and floors
4.4.3 Concrete holding and formwork wrapping
4.5.1 Number-qualified composition of links
4.6.1 Methods and methods of labor of workers on performance of work processes and operations
4.6.2 Quality control of finished products
4.6.3 Safety precautions during works performance
4.7.1 Annexes to Job Instruction
4.7.2 Logistical resources
4.7.3 Selection of load-gripping devices
4.7.4 Selection of installation crane by process parameters
4.7.5 Need for machines, equipment, tools and accessories
4.7.6 Technical and economic indicators
5 Construction Organization
5.1 Analysis of construction conditions
5.2 Methods of works execution
5.2.1 Earthworks
5.2.2 Concrete and reinforced concrete works
5.2.3 Stone and installation works
5.2.4 Finishing works
5.3 Selection of the main mounting mechanism
5.4 Construction plan
5.5.1 Calculation of construction personnel, areas of temporary buildings and structures, construction resources
5.5.2 Definition of the composition of temporary buildings and structures
5.5.3 Calculation of storage area requirements
5.5.4 Calculation of water demand
5.5.5.1 Calculation of Electricity Demand
5.5.5.2 Transformer substation selection
5.5.5.3 Calculation of the cross section of one cable or wire string to determine the group of consumers
5.5.6 Calculation of compressed air demand
5.5.7 Calculation of vehicle requirements
5.5.8 Calculation of heat demand
5.6 Work Schedule
5.7 Technical and economic indicators of the schedule
5.8 Technical and economic indicators
5.9 Occupational and Environmental Protection Measures
5.9.1 Occupational Safety and Safety Measures
5.9.2 Environmental protection measures
6 Life Safety
6.1 Occupational Safety
6.1.1 Site Safety Measures
6.1.2 Fire prevention measures
6.1.3 Safety measures during installation works
6.1.4 Measures during loading and unloading operations
6.2 Environmental Safety
6.2.1 Environmental safety measures in the calendar plan
6.2.2 Environmental safety measures on the construction plan
6.2.3 Environmental safety measures in Job Instruction for installation works
6.2.4 General environmental safety measures envisaged during the construction of the designed facility
6.3 Design Part
Bibliographic list
Applications
Application
Diploma Design Assignment
Application
Assignment of the Department of Foundations and Foundations
Application
Assignment of the Department of Construction Production Technology
Application
Assignment of the Department of Organization and Construction Management
Application
Assignment of Fire and Industrial Safety Department
Application
Estimate documentation
Application
Schedule of workers movement by object
Application
Schedule of main construction machines movement on the facility
Application
Master Goods Receipt Schedule for Object
Application
Patent search
Project Feasibility Study
1.1 Basis for project development
The feasibility study for the construction of a residential complex on the street. Vinogradnaya in the Central District of Sochi was carried out on the instructions of the customer - Donstroy LLC.
The basis for the sketched design is the documents attached in section 1.2.
In compliance with the Resolution MAYOR of Sochi of 29.12.2004 the land plot for performance of work on design and construction of a housing estate is allocated.
The author of the design solutions is the project company Geos.
Construction is supposed to be carried out by the general contractor construction company.
The feasibility study was developed in accordance with the data provided by the customer and the "Urban Planning Plan" of the proposed construction site in M 1:500 issued by Municipal Unitary Enterprise "Municipal Institute of the General Plan of Sochi."
1.1.1 Design Input
When developing a feasibility study for the construction of a residential complex on the street. Vinogradnaya in the Central District of Sochi, the following documents were used as initial data:
Decree of the Head of Administration of Sochi dated 11.12.2001 No. 699/1 "On Permission...";
Architectural and planning task of 11.01.2002;
Excavation from topoplane M 1:500;
Approval of the FSO of the Russian Federation dated 05.10.2004 No. 9/262179;
Conclusion of the State Fire Service of the Police Department of the Krasnodar Territory dated 14.10.2004 No. 23/9.42N on the placement of a residential complex;
Letter of the Directorate for the Protection, Restoration and Operation of Historical and Cultural Property of the Department of Culture of the Krasnodar Territory dated 30.09.2004 No. 3295 "On Belonging to Historical and Cultural Monuments";
Specification "Sochiteploenergo" dated 15.10.2004 No. T7/1 for connection to thermal networks;
Specification for power supply from 16.04.2003 No. 21101C26/2003;
Technical Specifications of the Office of Civil and Emergency Affairs of 29.03.2001 No. 32/29 of Civil Code;
Specification of Municipal Unitary Enterprise "Vodokanal" dated 23.09.2004 No. 0103/3630 for water supply and drainage;
Technical specifications of MU "Sochi vet" dated 21.09.2004 No. 05574 for external electric lighting;
Technical specifications of the branch of LLC UTK Sochielektrorosvyaz dated 22.10.2004 No. 07116/150 for telephoning;
Approval of the Federal Road Agency Uprdor Kuban to place the facility in the roadside of the federal highway;
Traffic police specification No. 7/5157735 dated 29.10.2004.
1.1.2 Brief description of the object
The designed residential complex is a group of high-rise residential buildings. Between residential buildings located on the street. Vinogradnaya there are 2-story attached buildings in which it is planned to place commercial enterprises. Non-residential 1st and 2nd floors in residential buildings are designed to accommodate small consumer service enterprises and offices.
One-section 16-story residential buildings are offered for 80 apartments each and their construction is provided for along the main highway in this part of the city - Vinogradnaya Street; three-section residential building of variable (from 12 to 16 floors) storeys with 162 apartments is located in the northern part of the site, on the street. Krasnoarmeyskaya. The composition of the complex was completed by a corner 16-story single-section residential building with built-in office premises located at the confluence of Vinogradnaya and Krasnoarmeyskaya streets.
It is proposed to build buildings using progressive technologies of monolithic house building.
1.1.3 Design capacity data of the facility
A feasibility study proposes to place 44,000 m2 of the total area of the housing stock or 482 apartments intended for the settlement of about 1,500 people on this site.
1.1.4 Fuel, water and electricity demand data
Power supply
The design capacity of electric receivers is - 1600.0 kVA.
Power supply source - at the 1st stage - a separate transformer substation 10/0.4 existing on the construction site with two transformers with a total capacity of 1800 kVA. At the subsequent stages of development, it is planned to build 2 separate 10/0.4 kV transformer substations with two transformers with a capacity of 2 x 40 kVA and 2 x 600 kVA.
Heat supply
The maximum heat consumption for heating, ventilation and hot water supply is 6.879 mW/h.
The heat supply source is centralized - from urban heating networks.
Water supply
The water consumption in the cold water supply system will be:
daily - 503.36 m3;
hourly - 21.1 m3;
second - 17.87 l;
internal fire extinguishing - 36.4 l/s.
The water flow rate in the hot water supply system will be:
daily - 236.62 m3;
hour - 9.93 m3;
second - 17.2 liters;
The water flow rate for external fire extinguishing of the building is 25 l/s.
The source of water supply is from the existing water supply networks in Sochi.
Sewerage
Amount of waste water discharged from residential buildings:
daily - 739.92 m3;
hourly - 31.02 m3;
1.1.5 Construction Order Information
and urban planning complexes
The construction of the facilities of the designed residential complex is supposed to be carried out in stages - launch complexes. In the 1st stage of construction, 80-apartment building No. 3 with external engineering communications in the amount necessary and sufficient for its commissioning is included.
Start-up complexes of residential buildings No. 1, 2, 4-6 with residential inserts and inserts for office premises include external engineering communications in the volumes proposed by the specifications and agreed by interested organizations.
1.1.7 Information on the approved design solutions
Pre-design materials were agreed with the Committee of Architecture and Urban Planning of the Sochi Administration in the "Urban Planning Opinion on the placement of a residential complex with a change in the target purpose of the site on the street. Vinogradnaya in the Central District of Sochi" dated 30.08.2004 No. HZ 135g04. The development scheme was agreed with the Directorate of Security in the Caucasus of the FSO of the Russian Federation (approval from 28.07.2004 No. 9/261664).
1.1.8 Basic solutions to ensure conditions
activities of low-mobility population groups
This project provides for the possibility of creating conditions for the life of representatives of a low-mobility population group.
Regulatory requirements are taken into account to create a living environment that ensures the needs of all low-mobility groups of the population - the elderly, the temporarily disabled, pedestrians with wheelchairs and preschool children, as well as more comfortable conditions for the rest of the population. For disabled persons with musculoskeletal system damage, including on a wheelchair or with additional supports, appropriate parameters of passages and passageways, limit slopes of the track profile, quality of the road surface are provided.
The topography of the site, which provides for the construction of residential buildings No. 4, No. 5 and No. 10, creates conditions for this category of people to live on the 1st residential floor with the arrangement of entrances to apartments directly from the courtyard of the site. Planning solutions make it possible to provide for at least 12 apartments for people with disabilities with limited mobility (if necessary, the number of apartments can be increased to 18 by arranging 1-2 room apartments instead of 2-3 room).
For apartments located on the ground floor, loggia (terraces) with access to the site are provided. The width of the loggia, adopted with a size of 1.5 m, based on the rotation of the wheelchair by 360 °.
In the lower floors of residential buildings, parking is provided for the storage of street strollers, technical care for the stroller, taking into account the place for transplantation. At the same time, the elevator reaches the floor level of the lower floor, and a ramp with a slope of no more than 5% is provided for the entry and exit of street strollers.
1.2 Information on engineering, hydrogeological conditions of the construction area
1.2.1 Climatic conditions
According to climatic conditions, B. Sochi belongs to the IV-B zone, allocated to the southern region of the Black Sea province. The main features of the climate are hot, humid summers, warm winters and autumn, long spring. The winter period is characterized by periodic instability associated with the invasion of cold air masses. In the coastal zone of B. Sochi, the duration of the frost-free period is 289310 days. The average annual air temperature is + 14.1 ° C, the absolute maximum is + 38 ° C, the annual amplitudes of the temperature variation are 1819 °. In valley lowlands, decreases to 20 ° are possible. The average relative humidity is 6870%, the amount of precipitation falling for the year is 1605 mm, in September-April 1279 mm falls, in May-August - 326 mm, the number of days with snow cover reaches 9, the snow cover capacity usually does not exceed 1030 cm. The average wind speeds of local circulation do not exceed 1.9 m/s. in summer and 2.8 m/s. - in winter. The maximum maximum wind speeds for the Tuapse-Sochi region are taken to be 25 m/s, the strongest winds are southeast. Fog on the coast occurs mainly in winter and spring, the number of days with them reaches 58. Seismicity of the construction site - 8 points.
1.2.2 Geomorphological conditions
Geomorphologically, the construction site is the remains of an ancient Black Sea terrace composed of light brownish-yellow clays, at the base of which lies the basal horizon of pebbles. The basement of the terrace is formed by the blurred surface of the argillites of the Sochi retinue of the lower Oligocene.
1.2.3 Geological structure of the site
The geological structure of the site is represented by indigenous deposits of the Paleogene and Quaternary formations of various genesis.
The indigenous base of the slope of the Sochi River Valley is composed of rocks of the Sochi retinue of the Oligocene - argillites gray, layered, with thin sandstone layers.
Quaternary deposits are represented by soils of various genesis: these are bulk man-made soils, deluvial-belt clays with landslide breccia of argillites, marine pebble deposits, elyuvium of native rocks.
According to surveys (including previous years), the following lithologenetic groups are identified in the geological structure of the site from top to bottom along the section to a depth of 32.0 m:
Class of man-made dispersed soils.
Group of disconnected natural displaced bulk formations. Layer 1 - Dispersed associated naturally displaced bulk clay non-swelling soils - brown clay, brownish - gray to gray, loose, with fragments of argillite, sandstone, with a large amount of construction debris (concrete, brick, household garbage). The thickness of bulk soils is 0.5-1.5 m, rarely increasing near underground structures and communications to 2-3 m. They are widespread almost everywhere.
Class of natural dispersed soils
B. Group of connected sedimentary polymineral clay soils. Layer 2 - Dispersed natural sedimentary deluvial-bearing soils - yellow-brown clay, gray spots, semi-solid, dense, swelling, with an admixture of sandy material, with pebbles (up to 1015%), with fragments of weathered argillite and sandstone (up to 1525% by layer). The thickness of the soils of layer 2 is on the surface of the Ancient Sea terrace 1112 m, decreasing higher along the slope (within the indigenous ledge) to 2-5 m. The soils of the layer are developed everywhere from the surface of the earth or under the embankment.
B. Group of incoherent sedimentary coarse soil.
Layer 3 - Dispersed incoherent natural ancient Roman pebble soils of the Karagant terrace - pebbles of sedimentary and metamorphic rocks, large and medium, gravel with sandy-clay aggregate up to 2025%, with large boulders of cooked sandstone. Pebbles have a power of 2-4 m.
B. Group of connected sedimentary polymineral clay soils.
Layer 4 - Dispersed coherent natural sedimentary eluvial soils - argillite brown to grayish-brown, wormless and obscure, weathered to hard clay and debris, weak, highly fractured. The thickness of the eluvium is marked in the roof of the indigenous massif. The thickness of the soils of layer 4 varies within 0.52.0 m. Soils of layer 4 are marked in the western part of the area under consideration .
Layer 5 - Dispersed incoherent sedimentary softening, waterproof, layered eluvial soils - argillite brownish-gray to gray, layered in the massif, iron-lined by steep cracks and spraying, with layers of sandstone brown, cracked. The soil of layer 5 is marked by local distribution in the western part of the area under consideration, in the roof of the bedrock, its thickness varies from 0.5-1.0 to 1-5 m. The soil is a transitional type of argillite from weathered differences to the bedrock.
Class of natural rock soils
G. Group of semi-rock soils.
Layer 6 - Semi-rock sedimentary low - low strength softened, low water permeable, layered, fractured soils - argillite gray, layered, at separate intervals broken, leafy, with vertical microcracks, with thin (2-7 cm) sandstone layers. During boreholes penetration in the core stratum, interlayers of brecciated, sheet argillite, sandstone stratum and calcite stratum are marked. The fall of rock formations is noted in azimuths of 260330 °, falling angles of 515 °.
1.2.4Hydrogeological conditions
Hydrogeological conditions of the site are characterized by the distribution of:
a) permanent aquifer confined to terrace sediments;
b) crack waters marked in the bedrock at depths more than 1220 m from their roof;
c) groundwater of the headwaters type.
The permanent groundwater horizon is confined to the lower reaches of the ancient Roman pebble terrace, which serves as a good natural groundwater collector - it discharges groundwater from the lower part of the slope. The groundwater mirror of this horizon is marked at abs. Elevations 23.0-24.0 m. Dense differences in the bedrock serve as a watershed for this horizon. The groundwater of the permanent horizon is fed mainly due to atmospheric precipitation and due to groundwater coming from the upper sections of the slope.
The groundwater horizon of the fractured type has a limited distribution, groundwater of this type is marked in eluvium or confined to zones of increased fracture in native rocks.
The headwater appears in the autumn-winter period in clay soils almost everywhere at depths of 3-4 m about 0.8-1.2 m. The headland is fed both due to atmospheric precipitation and due to leaks of domestic waters from dilapidated water-carrying communications.
The headwaters and groundwaters of ancient Roman pebble deposits are non-aggressive to concrete on all types of cement. Water - medium of fractured waters is weakly aggressive to concrete of W4 grade by waterproofness (SNiP 2.03.1185, vol. 6).
1.2.5 Physical and geological processes and phenomena
Unfavorable physical and geological features of the site include the fact that the designed construction is planned on an old-earth slope. The survey site is located in the contour of the ancient landslide G655 with a length of 300 m, a width of 425 m, a capacity of 7.0 m. The basis for the displacement of this landslide by SKGEC geologists is designated ul. Krasnoarmeyskaya. Landslide activity in the isolated circuit has not been manifested for more than 30 years.
1.3 Solutions and Key Indicators
according to the master plan and improvement of the site
The land plot provided for the design and construction of a residential building is located in the reconstruction zone of the central part of the city of Sochi, Krasnodar Territory.
The triangular section is bounded by the existing urban, multi-storey building and borders:
from the north - with 2-5 storey residential buildings;
from the east - bounded by the street. Krasnoarmeyskaya;
from the southwest - bounded by the street. Vinogradnaya, on the opposite side of which begins the territory of the Riviera park.
The relief of the site is flat, with a significant difference in elevation from 40.0 m to 18.0 m in the north direction and a sharp difference in elevations from 25.0 m to 12.6 m in the area adjacent to ul. Krasnoarmeyskaya.
Currently, the territory is built up with buildings and structures of the former brewery to be demolished. Communications existing on the site are partially subject to transfer, partially subject to complete dismantling.
Objects existing on the territory to be developed, as well as on residential buildings on plots adjacent to the quarter under consideration, are not included in the list of historical and cultural monuments.
The master plan is developed in accordance with the layout limitation scheme. Planning decisions of the master plan are made taking into account the specifics of the existing topography of the territory, when designing the vertical layout of cutting and filling of soil, they are provided in a minimum amount in order to preserve the existing topography in order to avoid the appearance of landslide processes after the development of the construction site.
The designed complex consists of single-section buildings of high storey freely arranged along the perimeter of the triangular section - a layout predetermined by the configuration of the section. The buildings are located along Vinogradnaya Street and in the northeastern part of the territory on the street. Krasnoarmeyskaya.
The vertical layout is solved taking into account the existing terrain, stormwater removal is carried out along driveways and platforms to lowered places.
The construction area is being improved. The main entrances to the complex are decided from ul. Vinogradnaya and st. Krasnoarmeyskaya. The driveways and turning platforms are supposed to be made with a two-layer asphalt concrete surface framed with on-board concrete stone BR 100.30.18 .
Pavements, areas in front of entrances to residential buildings are provided with concrete pavement. Paving of sidewalks and platforms in front of the entrances to public buildings uses paving tiles made of colored concrete .
The territory, free from development and hard coatings, is sown by lawn grass, landscaped by planting decorative trees of valuable species and shrubs.
The project provides for measures to ensure the life of low-mobility population groups.
1.4 Substantiation of architectural and construction solution of residential building No. 1
The peculiar configuration of the site allocated for the construction of a residential complex - a rectangular triangle, predetermined the basic principle of layout: four towers located along ul. Vinogradnaya - one-section 16-story buildings .
One-section 16-story residential building, pos. 3, provides for 80 apartments. The first two floors of the building are non-residential. They are supposed to accommodate offices and necessary for the normal service of residents of the complex of the consumer service enterprise (reception points of the laundry, dry cleaning, small ateliers for the repair of household appliances).
The layout of the interior of the residential part of the house meets the requirements of the standards and the customer's task. On each of the typical floors there are at least five apartments (one three-room, two two-room, two one-room). Apartments are provided with convenient layout, with a full set of internal equipment, enlarged glazed loggias. The building is equipped with two elevators: cargo - 630 kg, and passenger - 400 kg.
In the basements and technical floors there are engineering equipment of a residential building, including control frames, communication input units, electric switchboard, ventilation units that create air overpressure in corridors and elevator shafts and halls, ventilation installations of smoke removal.
The building is supposed to be monolithic. The external walls are multilayer, made of reinforced concrete, lined with fibropene concrete heat insulation plates. The basement is finished with stone plaster with rustication for limestone, granite.
Decorative elements of the facade of the main entrance should be made according to sketches agreed with the authors of the project and the main architect of the city.
1.5 Protection of historical and cultural monuments
Due to the absence in the territory of construction and adjacent in the northern part of residential development of objects classified as historical and cultural monuments, measures for the preservation of monuments or their restoration, this feasibility study does not provide.
1.6 Compliance of space-planning and structural solutions
requirements and specifications established by the customer
The main structural elements of the building are as follows:
Base
cast-in-situ reinforced concrete slab;
Basement walls
cast-in-situ reinforced concrete;
Building walls
cast-in-situ reinforced concrete lined with fibropene concrete slabs;
Slab Slabs
cast-in-situ reinforced concrete;
Coating plates
cast-in-situ reinforced concrete;
Partitions
fibropene concrete partition blocks as per TU 5767-033-02069119-2003
Roof
with an internal drain from a 4-layered ruberoid carpet;
Heater
Fibropene concrete TU 5767-033-02069119-2003
Floors
in residential rooms, built-in rooms, corridors - parquet, slag and steel tiles;
in elevator halls, common corridors, bathrooms - ceramic tiles;
in kitchens - linoleum;
Facade Finishes
high-quality colouring with organosilicon enamel.
1.8 Considerations for the organization of construction
1.8.1 General Information
This section is developed in accordance with the requirements of item 4.2. Construction Norms and Regulations of II0195 "About an Order of Development, Coordination, a Statement and Structure of the Project Documentation on Construction of the Enterprises, Buildings and Constructions".
1.8.3 Duration of residential building construction
The construction of the facilities of the designed residential complex is supposed to be carried out by launch complexes.
The duration of construction of the designed building is determined according to SNiP 1.040385 * "Standards for the duration of construction and backlog in the construction of enterprises, buildings and structures," part II M 1991 and amounts to:
80 sq. residential building (pos. 3 according to the general plan) - 14 months.;
Prior to commencement of construction of the residential building under consideration, existing buildings and structures located in the construction area of the designed facility shall be dismantled (demolished).
1.8.4 Labour intensity and need for construction personnel
Labor intensity and the need for personnel of builders is determined at the stage of development of the working project.
1.8.5 Organizational and technical measures
Administrative and household maintenance of employees, temporary power supply, water supply of the building under construction, sewage sewage, heat supply, air power supply, telephony and dispatch communications, organization of warehousing, as well as the need for temporary buildings and structures developed in the project of work.
1.8.6 Methods and procedure of works execution
The choice of the method and technology of work is due to the characteristic types of planned work, hydrogeological, seismic and other conditions of the construction area.
The construction of multi-storey residential buildings is planned to be carried out by the following mechanisms:
underground part (zero cycle) - using boom crane RDK25;
aboveground part (above elev. 0.000) - tower crane KB504 A2.
The organization of construction sites, the implementation of geodetic measures, the production of earthworks, concrete and reinforcement works, the selection of lifting mechanisms is made in the PPR.
Demolition of existing buildings is carried out mainly by disassembling them using an excavator (E4124) equipped with tooth rippers and a hydraulic hammer, a caterpillar crane (RDK25), an automobile crane (KS4562), a construction tower (BS22MS), a lifting tower on a GAZ63 car (PVG1 scaffolding) and hammering.
1.9 Electrical, explosion and fire safety measures
The fire resistance of the building is II.
To ensure fire safety of the workers, the following measures are provided:
structures and materials are accepted with fire resistance limits providing II degree of fire resistance of the building;
the number of evacuation exits from premises, floors and from the building is not less than two, except for cases permitted by SNiP 2.08.0289 * and SNiP 2.01.0285, SNiP 210197;
doors open in the direction of exits from the premises and the building, except in cases permitted by SNiP 2.08.0289 *.
To ensure electrical safety, the following measures are provided:
application of PE conductors;
use of RCD;
protective grounding and lightning protection device;
alignment of electrical potential of buildings.
1.10 Measures to protect building structures from corrosion
Corrosion protection of building structures is performed in accordance with SNiP 2.03.1185 "Protection of building structures against corrosion," SNiP 3.04.0385 "Protection of building structures and structures against corrosion" and provides for:
all metal parts, as well as anchor joints of the floor are protected by paint coatings.
1.11 Anti-Radiation Requirements
In accordance with the requirements of NRB76/87 and OSP7287, radiation control of the construction site by specialists of the State Sanitary and Epidemiological Supervision should be carried out before the construction of the house. Construction materials, products and structural elements used for the construction of a residential building must undergo radiation control.
During the commissioning of a residential building, it is necessary to carry out radiation control of all premises.
1.12 Water Supply and Sanitation Solutions
The following systems are provided for residential buildings:
potable and fire-fighting water supply;
hot water supply;
domestic sewerage system.
1.12.1. Water supply
The source of water supply for the systems of domestic, hot and fire-fighting water supply is urban water supply networks. Heating of water for hot water supply of buildings is carried out by a boiler house located on the territory of a residential complex.
The project provides for the supply of water to the residential complex through two water pipelines powered by various sections of the city water supply network (I - from the water supply on the street. Vinogradnaya, II - from the water supply on the street. Krasnoarmeyskaya).
The water flow rate in the cold water supply system will be:
daily - 503.36 m3;
hourly - 21.1 m3;
second - 17.87 l;
internal fire extinguishing - 36.4 l/s.
The water flow rate in the hot water supply system will be:
daily - 236.62 m3;
hour - 9.93 m3;
second - 17.2 liters;
The water flow rate for external fire extinguishing of the building is 25 l/s (Table 6 SNiP 2.04.0284 *). External fire extinguishing is carried out from fire hydrants installed on the external water supply network.
The necessary head for economic and fire protection needs is 65 m.v.
To ensure the necessary head, pump stations are installed in the buildings of residential buildings.
To account for water consumption, a water metering unit is installed in each building.
1.12.2. Water disposal
Household sewerage provides for the removal of sewage from sanitary devices to the street sewage collector.
Amount of waste water discharged from residential buildings:
daily - 739.92 m3;
hourly - 31.02 m3;
second - 43.13 liters.
1.12.3. Internal water supply and sewerage
The following systems are provided in residential buildings:
potable and fire-fighting water supply;
hot water supply;
domestic sewerage system.
Each residential building has two cold water inlets connected to different external water ducts.
To account for water consumption of the building, the following are provided:
water metering unit for cold water supply of the building (at each input);
heat metering unit.
In addition, cold and hot water meters are installed in each apartment.
To create the necessary head in the network in the basement of each residential building, an increase water pumping station is provided.
Pump station operation is provided in automatic mode depending on water pressure in water supply system.
Two groups of pumps are installed in the pump room:
1 group - fire-fighting water supply pumps 2 pcs.;
Group 2 - Household Water Pumps - Automatic Water Pump Unit based on pumps from GRUNDFOS Germany.
Pump station belongs to 1 category.
Domestic-drinking and fire-fighting water supply is provided for water supply to sanitary devices, irrigation and fire cranes. Hot water supply - for supply to sanitary devices and irrigation taps in garbage chambers.
The cold water supply system is made of 16-63 mm diameter PN10 polypropylene pipes manufactured by Firat, Turkey. Fire risers are made of 50 mm diameter steel water and gas pipes as per GOST 326275 *. The hot water supply system is made of PN20 polypropylene pipes with a diameter of 16-63 mm.
Household sewage system is designed to drain household wastewater from sanitary devices to a street sewage collector and is installed from PVC sewage pipes with a diameter of 50, 100 mm according to TU 61930786 and PND with a diameter of 100 mm according to GOST 22689.377.
1.13.2 Main Heating and Ventilation Solutions
Heating
Two independent heating systems are provided:
residential heating system;
heating system of public premises.
Cast iron radiators "MS140 M" GOST 869094 with nominal heat flow of 1 section 0.16 kW are used as heating devices. Heating system is provided with lower wiring of supply and return main pipelines.
The risers of the heating systems are designed for the residential part of the building with single-tube Twin, and for public premises with double-tube vertical.
To control the heat removal of heating devices on single-tube risers, double control valves are provided, and ball cranes are provided for double-tube risers.
Main pipelines of heating systems and heating risers pipelines are provided from steel water and gas pipes according to GOST 326275 * and steel electric welded pipes according to GOST 1070491.
In the basement of a residential building, in a separate room there is a control unit.
In the heat units of each residential building, heat measures are established that take into account the separate heat load on heating and hot water supply.
Hot water supply is carried out according to an open scheme with the installation of a temperature regulator.
Ventilation
Air exchanges of premises are determined for the residential part of the building by multiplicities, and for public premises from the conditions of providing a sanitary norm for the supply of outdoor air to these premises.
Ventilation of a residential building is accepted as natural supply.
Exhaust - through ventilation ducts located in kitchens, bathrooms and bathrooms, inflow unorganized through the looseness of window and door openings. Ventilation channels are rectangular and are located in internal capital walls.
In public premises, plenum ventilation is mechanical.
1.14 Smoke protection and smoke removal
The design provides for a smoke protection system for a residential building supplying air to the elevator shaft during a fire.
Floor smoke removal is carried out through smoke valves from the corridors of a residential building.
Simultaneous activation of the systems is carried out automatically from fire detectors, remotely from the duty room. Smoke valves also have automatic, remote and manual (in the shaft of their installation) control.
System fans are located in ventilation chambers with fire walls and floors of the 1st type, having a fire resistance rating of at least 0.75 hour. The vent chambers are in the attic.
1.15.2 Power electric receivers
Power electric receivers of the building are: electric drives of elevators, pumps of fire and household water supply, plumbing ventilation, technological current collectors of shops, cafes, sports and other facilities. All power current resins of a residential building are powered by water distribution devices.
1.15.3 Electric lighting
The project provides for the installation of working, emergency (evacuation), repair lighting in residential, commercial and administrative-public premises of a residential building. All electrical lighting networks are powered by water distribution devices.
1.15.4 External electrical lighting
The project provides for the arrangement of external electric lighting of the territory of a residential building - street lamps with high-pressure sodium lamps. Control of external electrical lighting is provided from the external electrical lighting panels of the designed transformer substations.
1.15.5 Lightning protection and grounding
The design provides for lightning protection of class I. Building grounding is provided by TNCS system. At the entrance to the building, there is a device for the grounding loop, combined with a lightning intake device (if provided), metal elements of building structures, plumbing ventilation and process equipment. The project provides for measures to equalize the electrical potential of the building.
1.15.6 Measurement and accounting of electricity
Accounting for electricity in the residential sector of the building is provided in apartment boards, and in apartment boards there is also provided for the installation of ultrasound. The project provides for the installation of apartment boards in each apartment. Electricity metering and RCD installation in the administrative-public premises of the building is provided in the water distribution device.
1.16 Communication
1.16.1 Telephony
Telephony of the designed residential building is provided from the existing city telephone networks.
Subscriber networks will be carried out at the request of subscribers as the building comes into operation.
1.16.2 Radialization
Radialization of the designed building is provided from existing urban radio networks.
1.16.3 Television
The project provides for the installation of a collective television antenna with a signal amplifier on the roof of the house.
1.17 Protection of the environment
This section was performed as part of the feasibility study for the construction of a residential complex in the Central District of Sochi on the street. Vinogradnaya in accordance with the requirements of SNiP 110195 and the Manual to SNiP 110195 for the development of the section "Environmental Protection."
The section considers certain areas of environmental protection, based on the possible environmental consequences of the operation of the designed residential complex .
Environmental justification of nature use is developed on the basis of environmental impact assessment of the designed facility, in order to:
Determining the conditions for the use of natural resources stipulated in the established procedure when placing a housing estate on the street. Vinogradnaya in the Central District of Sochi;
Definitions of environmental measures that are mandatory for further development in the preparation of working documentation.
The expected pollution of the natural environment in the zone of influence of the designed housing estate is carried out according to all ecospheres and factors of physical and other impact on the environment and human habitat.
The following are guidelines for the expected impact on the environment of the proposed activity, as well as project and environmental proposals in the context of the existing environmental situation in the territory under consideration, taking into account the decisions taken on its socio-economic development .
1.17.1 Brief information about the designed object
The feasibility study for the construction of a residential complex on the street. Vinogradnaya in Sochi was developed on the basis of the order of Donstroy LLC and the customer's task, approved by the General Director of Donstroy LLC.
Currently, the territory of the designed residential complex is built up with buildings and structures of the former brewery to be demolished .
Existing in the communication area are partially subject to transfer, and partially to complete dismantling.
Pavements and platforms in front of entrances to residential buildings are provided with concrete pavement; driveways and turning platforms are supposed to be made with a two-layer asphalt concrete surface framed with onboard concrete stone BR100.30.18.
The boundaries of the parcel are:
from the north - 2-5 storey residential buildings;
from the south-west - st. Vinogradnaya, on the opposite side of which the territory of the Riviera park begins;
from the east - st. Krasnoarmeyskaya .
The area, free from development and hard coatings, is landscaped with an appropriate assortment of ornamental trees of valuable species and shrubs and is sown with lawn grass.
1.17.2 Protection and management
land use
The designed residential complex is located on a land plot of 1.877 hectares, located along Vinogradnaya Street and in the north-eastern part of the territory on the street. Krasnoarmeyskaya in the reconstruction zone of the Central part of Sochi, Krasnodar Territory .
On the site there is a significant difference in elevations from 40.0 m to 18.0 m in the north direction and a sharp difference in elevations - from 25.0 m to 12.6 m in the territory adjacent to the street. Krasnoarmeyskaya .
In the area of influence of the designed object there are no territories subject to special protection .
The seismicity of the construction site, in accordance with the changes to SNiP II781 *, is 8 points .
Disposal of domestic sewage from sanitary devices is carried out on several outlets from the buildings of the complex along the on-site domestic sewage network to the existing street sewage collector.
Surface water removal is carried out along the planned territory: from trays to rainwater receivers, and from there directly to the city storm sewers.
All sites and pavements have a hard coating.
The project provides unhindered access to the infrastructure of the city for low-mobility groups.
1.17.3 Proposed environmental measures
during construction
In the preparatory period, before the start of the main work on the site of the housing estate, all earthworks, redevelopment of its territory and construction of buildings and structures are carried out in the necessary technological sequence, which will minimize damage to the plant world and prevent the development of negative engineering and geological processes and changes in the regime of ground and surface water.
The construction site of the object is equipped with an organized drainage of surface runoff.
Temporary dumps of uncompressed soil on the slopes of pits in the places of detection of springs and places of groundwater sinking (without their capping and drainage devices) are not allowed.
In the course of drilling operations when reaching aquifers, measures should be taken to prevent the outflow of groundwater.
Soil development when laying utility networks near green spaces is carried out by an excavator on pneumatic wheel travel with a ladle capacity of not more than 0.25 m3 or manually.
On the territory of the object under construction, it is not allowed to remove wood-shrub vegetation and fill root necks and trunks of growing trees and shrubs with soil, which is not provided for in the design documentation.
Preserved green spaces are fenced within a radius of 1-3 meters.
During construction and installation works at the facility, in order to reduce the dust content of the air, it is not allowed to dump them from the floors of road service facilities under construction during waste removal, without using closed trays and storage silos.
Incineration of combusted wastes polluting atmospheric air is prohibited.
To ensure transport accessibility of the construction site of the residential complex, the main entrances are used from ul. Vinogradnaya and st. Krasnoarmeyskaya.
During the construction period, selective dosimetric control of building materials and structures used in erecting the facility to the permissible level of radionuclides is carried out.
After the completion of construction work, all waste is exported to the established places in agreement with the sanepidnadzor and the nature conservation committee.
1.17.4.2 Characterization of atmospheric pollution level
of air in the area of the object location
Background air pollution in the area under consideration is within the limits of the norm, there are no sources of pollutant emissions.
1.17.4.4 Emission control activities
under adverse meteorological conditions
The functional activity of the housing estate in case of NMU will not have a negative impact on the environment.
1.17.4.5 Air Basin Monitoring Methods and Tools
In accordance with item 4.5.3. Environmental control of environmental impacts is not envisaged.
Construction production technology
4.1 Job Instruction
4.1.1. Scope of application of task list
4.1.1.1 Characteristics of the building and its structural elements
The process sheet was developed for the construction of a monolithic building with plan dimensions of 30.6x30.6 m, with a pitch of load-bearing walls of 3.27.2 m. The cast-in-situ floors are 220 cm thick from concrete of class B25. Cast-in-situ walls made of concrete of class B25.
4.1.1.2 Characteristics of the working conditions
Monolithic works shall be arranged in accordance with working drawings.
The work is planned in summer.
4.2 Construction Process Organization and Technology
4.2.1 Preparation of the facility and requirements of readiness of previous works
The following works shall be performed prior to the start of monolithic works:
construction of basement walls,
preparation for floors in the basement,
temporary lighting and power supply,
delivery of all necessary accessories, tools, equipment,
access roads and roads,
4.2.2 Composition of works included in Job Instruction
The works considered by the map include the following technological processes:
installation of large-shield formwork of load-bearing walls,
binding of rebar frame of walls,
installation of large-shield slab formwork,
binding of the rebar frame of the slab,
laying of concrete mixture in structures,
maintenance and care of concrete,
decompression of structures.
4.2.3 Material warehousing and stock
Main materials to be stored on site:
formwork panels
fittings packages
These materials are delivered to the construction site in accordance with the application for at least two grips.
Unloading and storage is carried out in the area of the assembly site, which is a planned and compacted section located in the crane operation area.
Valves shall be stored in accordance with GOST 756681, formwork panels with packages not more than 1.5 m. Between the packages there must be passages of at least 1 m.
4.4 Methods and sequence of works
4.4.1 Formwork and reinforcement of walls and floors
Installation and disassembly by crane of large-shield wood-metal formwork of walls. The formwork of one side of the wall is installed to the entire height of the wall and is fixed by braces and screw struts. The formwork of the second side of the wall is installed after installation of the wall reinforcement. During installation of the panels of the second side of the formwork, fights, temporary spacers and bolt ties are installed. Installation and disassembly of formwork is performed from scaffolding.
Installation of slab formwork located at a height of up to 5.5 m from the lower slab is carried out without preliminary arrangement of scaffolding. Panels of floor formwork are laid on walls, after which inventory sliding posts are brought under them, which are extended by the required length. Precise installation of the formwork boards is achieved by moving the jacks under the posts. Formwork of floors is installed from portable ladders.
The walls are reinforced together with the wall formwork. The reinforcement is supplied by a crane, tied into spatial frames.
Reinforcement of slabs is performed after arrangement of slab formwork. Reinforcement is supplied by a crane, tied into grids, set on concrete gaskets, fixed and adjusted.
4.4.2 Concreting of walls and floors.
To deliver the concrete mixture, SB92 concrete mixers with a drum capacity of 5 m3 are used. The required number of machines is considered in the application. The concrete mixture is supplied to the concreting site using a tower crane in buckets with a capacity of 1.5 m3.
Walls in disassembling formwork are concreted without interruption, with sections no more than 2 m high. The concrete mixture is compacted with depth vibrators.
When concreting walls from above, the lower part of the formwork is first filled to a height of 1020 cm with cement mortar of the composition 1: 2-1: 3 in order to avoid the formation of porous concrete in this part of the wall with a cluster of coarse aggregate.
4.4.3 Concrete holding and formwork wrapping.
The decompression is started after the concrete has achieved the required strength. Since the concrete hardening rate mainly depends on the ambient air temperature, the time after which the decontamination is carried out is set according to SNiP:
for slabs with a span of up to 3 m, 70% of the standard strength at a concrete temperature of 20 ° C is achieved at 7 days from the day of concreting.
When removing floor posts supporting the formwork of concreted floors of multi-storey buildings, they are guided by the following rules:
It is not allowed to remove the slab formwork posts located directly under the concreted slab,
the formwork post of the next underlying slab can be removed only partially, while under all beams with a span of 4 m or more, safety posts located one from the other at a distance of not more than 5 m are left;
formwork posts of the remaining underlying floors can be removed completely if the strength of these floors has reached the design level.
4.6.1 Methods and methods of labor of workers on performance of work processes and operations.
Works on installation of wall formwork and floors with simultaneous installation of reinforcement are performed in the following sequence.
Construction locksmith M 1-2 and S-3 performs marking of places of installation of formwork boards by layout axes. Locksmith M-4 and M-5 with spraying pistols apply emulsion layer on working surfaces of formwork shields. M-4-5 sling the shield for two mounting loops. Moving to a safe distance, the M-4 gives the command to the crane driver to lift the shield. M-1-2-3 receives the fed shield and orients it over the installation site. At the command of M1, the crane driver lowers the shield, and the M-1-3 locksmith sets it, combining the markup risks with the shield. After upset, the shield is temporarily fixed with braces and strubcins.
After installation of one of the sides of the formwork, the internal reinforcement of the walls is installed.
Installation of reinforcement frames is performed by a link of workers performing formwork installation.
M-4-5 reinforcement mesh is slung in accordance with the specification. Moving to a safe distance, the M-4 gives the command to the crane driver to lift. M-1-3 receive the grid and orient it to the installation site. After reconciliation and installation, the reinforcement mesh is welded to the reinforcement outlets and temporarily fixed. After that, the formwork board of the second side of the wall is installed. Shields are bolted, temporary spacers are installed. Mechanics
M-1-2 final reconciliation of installed formwork is performed using levels and plumbs. After that final attachment of formwork with braces, fights, struts and braces is performed.
The arrangement of the floor formwork begins after the installation of the formwork of all the walls of the room.
M-1-3 locksmiths are laid according to working drawings and diagrams. Extensible inventory girders are installed on the heads of the struts, which are attached to the heads of the struts with pressure strips, and in the top to the formwork of the floor slabs, the latter consists of metal shields connected to the panel using runs-bumps and spring vanes. Along the perimeter of the plate, frieze boards are installed to facilitate further unraveling. The final, accurate installation of the floor formwork is achieved by moving the jacks under the posts.
M-4-5 slings the reinforcement slabs and gives a signal to the crane driver for lifting.
M-1-3 concrete gaskets are brought up and laid with their fixing. Fed mesh is installed by means of crane into formwork. After that correctness of installation is verified according to drawings of concrete structures.
Concrete work is carried out by a link of two people: concrete workers of 4 and 2 categories.
The concrete mixture is delivered to the construction site by dump trucks and unloaded on a specially designated site directly to the taverns.
Badyas are fed by crane directly to the place of laying. Concrete workers M13, 14 before concrete is supplied, a receiving funnel is installed at the place of laying, the walls are concreted, bringing the concrete mixture from above through the funnels continuously to the entire height of the wall. The concrete mixture is laid in layers equal to 0.8-0.85 of the length of the working part of the vibrator tip. Concreting of slabs, monolithically connected to walls, begins not earlier than 1-2 hours after concreting of walls, due to the need for initial settlement of laid concrete mixture.
Before concreting, concreters M13, 14 install beacon racks, which are installed on the formwork in rows after 22.5 m and attached to bosses located on the formwork. The upper plane of the rack is located at the level of the top of the plate. After the racks and bosses are removed, the remaining recesses in the slab are sealed with concrete. The concrete mixture in the slabs is compacted with vibrobrus. The worker sets the vibrators to the initial position between the beacon racks, turns on the engine and together moves the vibrator to the end of the grip at a speed of 0.20.4 m/s. As concrete is concreted, concrete is shaken slightly with metal hooks, ensuring that a protective layer of concrete of the necessary thickness is formed under the reinforcement.
The expansion of wall structures and floors is carried out by link No. 5.
In the formwork of the walls, locksmiths M2527 first remove the tightening bolts, then horizontal fights from top to bottom. Then the shields are torn from the body of concrete. Then they are slung and removed with a crane.
In the floor formwork, the bars bordering the runs are removed, frieze boards are removed and, using jacks, the posts are smoothly lowered, the bottoms are torn off. Then struts between struts are removed and struts themselves are removed.
4.6.3 Safety precautions during works performance
Concrete works
When feeding, laying and caring for concrete, harvesting and installing reinforcement, as well as installing and disassembling the formwork, it is necessary to provide measures to prevent the following hazardous and harmful production factors related to the nature of the work:
location of workplaces near the difference in height of 1.3 m or more;
moving structures and loads;
collapse of loose structures and cargo;
fall of the above materials and tools;
rollover of machines, fall of their parts;
increased voltage in the electric circuit, the closure of which can pass through the human body.
In the presence of hazardous production factors, the safety of installation works should be ensured on the basis of the implementation of the following labor protection decisions contained in the organizational and technical documentation:
determination of crane grade, installation place and hazardous areas during its operation;
determination of mechanization facilities for transportation, supply and laying of concrete mixture;
determination of bearing capacity and development of formwork design, as well as sequence of its installation and disassembly order;
ensuring the safety of workplaces at altitude;
development of concrete care measures and products in cold and warm season.
The installation of formwork as well as installation of reinforcement frames shall be guided by the following requirements.
On the gripper where installation works are carried out, it is not allowed to perform other works and find unauthorized persons.
At construction of the building it is forbidden to perform the works connected with finding of people in one catch over which movement, installation, installation and temporary fixing of structural elements is made.
Installation of building structures should begin, as a rule, with a spatially stable part: a connecting cell, a stiffening core.
Installation of structures of each overlying floor of a multi-storey building should be carried out after fixing all installed installation elements according to the design and reaching the strength specified in the WDP with concrete of load-bearing structures.
Installation of stairways and building platforms shall be carried out simultaneously with installation of building structures. Fences shall be installed immediately on the mounted stairways.
Placement of equipment and materials on the formwork. It is not allowed to find people who are not directly involved in the work on the installed formwork structures.
To transfer workers from one workplace to another, ladders, transition bridges and ladders shall be used that meet the requirements of SNiP 120302.
When arranging the wall formwork, it is necessary to provide for the construction of working flooring with a width of at least 0.8m with fences.
Slab formwork shall be enclosed along the entire perimeter. All openings in the working floor of the formwork shall be closed. If it is necessary to leave these holes open, they should be tightened with wire mesh.
It is allowed to walk on laid reinforcement only on special slabs with a width of at least 0.6 m laid on the reinforcement frame.
Removable load-gripping devices, slings and packagings intended for concrete supply by lifting cranes shall be manufactured and inspected in accordance with PB10382.
Rack for concrete mix supply by dump trucks shall be equipped with baffle bars. passages of not less than 0.6 m shall be provided between baffle bars and fences. Cross bars shall be installed on dead end racks.
When cleaning the body of the car dump truck from the remains of the concrete mixture of the employee, it is forbidden to be in the body of the vehicle.
Elements of reinforcement frames must be packaged taking into account the conditions of their lifting, storage and transportation to the place of installation.
Bunkers (bunkers) for concrete mix shall comply with the requirements of the state standards. Movement of a loaded or empty hopper is permitted only when the closure is closed.
When laying concrete from a bunker, the distance between the lower edge of the bunker and the previously laid concrete should not be more than 1 m, if other distances are not provided for by the PPM.
It is necessary to check the condition of the container, formwork and sweeping facilities every day before the concrete is laid in the formwork.
When installing formwork elements in several tiers, each subsequent tier should be installed after fixing the bottom.
The formwork must be disassembled after concrete reaches the specified strength.
When disassembling the formwork, it is necessary to take measures against accidental fall of formwork elements, collapse of supporting scaffolding and structures.
When compacting the concrete mixture with electric vibrators, it is not allowed to move the vibrator behind the current-carrying wire, and when breaks and switching to another place, the vibrators must be disconnected.
Organization of construction
5.1 Analysis of construction conditions
The land area of 1160 m ² is located in the city of Sochi.
The site is located on the territory of the former brewery, the buildings and structures of which were demolished in 2004.
The site is limited by the existing urban multi-storey development and borders:
- from the west - detour st. Vinogradnaya;
- from the east - -the territory of the detour st. Krasnoarmeyskaya;
- from the north and south - intra-quarter roads of residential development.
The relief of the site is calm with slight decreases in elevation from north to south.
Groundwater level is marked at a depth of 3.0 m. Seismicity of the region is 10 points.
According to engineering and geological surveys, there are no landslide phenomena on the site.
Soil bases are clays with pebbles with a capacity of 6 m or more.
According to/1/the construction area belongs to the 4B climatic area.
5.2 Methods of works execution
The project of work execution at this facility established the preparatory and main construction periods.
In the preparatory period, work is carried out on the development of the construction site, the installation of access roads and roads, the equipment of the construction site and site-wide breakdown work. During the main period, construction and installation work is carried out on this facility.
The territory of the construction site is previously cleaned from trees, stumps, shrubs and released from boulder stones.
Trees are removed along with roots or sawing trunks and subsequently uprooting stumps. Tractors, bulldozers, tractor-mounted turret winches and excavators with special equipment are used to roll trees and root stumps. Shrubs and small piglets are removed by bulldozer or bush cutter.
Overhead lines and power transmission supports, when they interfere with the work, are moved to the side or taken out of the construction site. The overhead lines are raised to provide the necessary dimensions for traffic.
5.2.1 Earthworks
Earthworks shall be carried out in accordance with SNiP 3.02.01 - 87 "Earthworks, foundations and foundations."
Excavation works are permitted after geodetic survey works are carried out on removal of earthworks to the design and installation of corresponding layout marks.
Marking marks should be fixed on the ground by installation of pillars outside the location of earthworks and rings at the site of work. The breakdown of the facility prior to the commencement of work shall be inspected by the customer and the contractor, for which the corresponding certificate is drawn up.
Perform vertical layout in accordance with section "Vertical layout" of SNiP 3.02.01 - 87.
The development of soil for the foundation of the building is provided with the help of an excavator of type E303 with a bucket with a capacity of 0.65 m3 with the loading of excess cargo on the dump trucks and its transportation to the dump or reserve in the amount necessary for backfilling.
The arrangement of trenches for utility networks is provided with vertical walls protected from collapse by wooden shields, when developing trenches, soil is laid on an eyebrow in the volume necessary for backfilling, and a smaller part of it is taken to a dump.
Mechanized grinding of pit bottoms, arrangement of backfilling of trenches and external sinuses of pits and other mass haul movements shall be performed by DZ18 bulldozer.
Cut the plant layer with bulldozer DZ18 with subsequent placement in temporary reserve, and then use it for landscaping.
Quality control of earthworks shall be carried out in accordance with SNiP 3.02.01 - 87. which consists in systematic instrumental monitoring of compliance of performed works with the project and compliance with the requirements of standards.
5.2.2 Concrete and reinforced concrete works
Concrete and reinforced concrete works shall be carried out in accordance with the requirements of SNiP II2175 "Concrete and reinforced concrete structures. Design Standards "; SNiP III1576 "Concrete and reinforced concrete structures monolithic," SNiP III1576 "Concrete and reinforced concrete structures monolithic. Rules of Work Execution and Acceptance, "
The construction of cast-in-situ reinforced concrete structures is provided by the use of an inventory panel formwork, reinforcement grids, individual reinforcement bars, spatial frames .
Monolithic reinforced concrete designed: foundation slab, floors, frame columns, feed walls, staircase walls.
When constructing the underground part of structures, the concrete mixture is laid using a concrete pump; when erecting the structures of the above-ground part, concrete is supplied by a mounting crane using a badge of the "shoe" type.
The concrete mixture is delivered from the nearest plant of construction materials with concrete mixers.
Concreting is allowed only after inspection and acceptance according to the concrete preparation certificate, bracing, pressure slab, reinforcement of the slab and formwork, subject to written permission of the author's supervision in the work log.
The plan position, elevations and dimensions of reinforcement and formwork of the element prepared for concreting shall comply with the design and requirements of the corresponding SNiPs.
Garbage, dirt, snow and ice shall be removed in the places of fittings installation. Rods installed in reinforcement element must be degreased, cleaned of dirt, ice and snow, rust deposit.
Quality control of welded joints of reinforcement shall be carried out in accordance with GOST 1092275 "Reinforcement and embedded parts welded for reinforced concrete structures. Technical requirements. " The installed reinforcement shall be fixed against displacements and protected against damages that may occur during concreting.
Upon completion of concreting of each unit (gripping) it is necessary to:
protect hardening concrete from shocks, shocks and other mechanical effects;
perform measures to maintain freshly laid concrete to established strength (care for concrete).
5.2.3 Stone and installation works
Perform stone installation works in accordance with SNiP 3.03.01 - 87 "Bearing and enclosing structures."
Materials and products used in erection of structures, procedure of their acceptance, transportation, storage and testing shall comply with the requirements of standards and technical specifications.
It is strictly forbidden to transport brick in bulk and unload it by dropping, as well as unload the solution to the ground.
Before performing masonry, the longitudinal and end wall axes must be split using theodolite using reference axial benchmarks.
Quality control of these works shall be continuous and shall be limited to the following functions:
- quality control of the solution, its relaxability;
- control over transportation and unloading of bricks;
- control of geometric dimensions in vertical and horizontal direction;
- check of weld thickness.
Values of permissible deviations are fixed by act.
5.2.4 Finishing works
Perform finishing works in accordance with SNiP 3.04.02 - 87 "Insulation and finishing coatings." In order to achieve high quality and reduce the construction time, a flow-cycle method of organizing the finishing work is recommended.
The complex of finishing works is divided into 4 sequential cycles;
1 - plaster works;
2 - installation of articles subject to painting treatment;
3 - preparation for painting;
4 - work on the arrangement of floors.
All finishing works are carried out from suspended scaffolds - inventory-type columns adapted for movement through standard door openings.
The solution for plaster works brought to the construction site is unloaded to the receiving hopper of the solution receiving unit. The solution is then fed to the plaster workstations by a plaster station.
For painting works, a mobile painting station is used, from which compositions for whitening ceilings and walls are supplied to the workplace through hoses. Quality of work is checked by templates and visually.
5.4 Construction plan
The construction plan was developed for the period of construction of enclosing structures of the building. The purpose of the construction plan is to organize the construction farm on the site, which ensures the creation of the necessary working and rest conditions for workers, for mechanization of work, acceptance, storage. Laying of materials, structures, provision of works with water and energy resources.
The construction plan is part of the integrated construction documentation and is developed in accordance with the accepted work technology and construction deadlines established by the schedule.
During the development of the construction plan, the requirements of SNiP 3-4-80 "Safety in construction" are provided. In order to create favorable living conditions and reduce the cost of building temporary buildings and structures, they are located in areas not intended for development until the end of construction.
To avoid intermediate bulk unloading, all open warehouses are located in the crane area. Brick shall be stored on pallets and containers. For the storage of timber and metal elements, window and door bindings, canopies are provided.
Temporary buildings and structures by the number and composition of areas are determined by calculation (see Table). Crane and hazardous areas are indicated on the construction plan, warning signs are installed that limit the movement of people and cars on the construction site.
Roads on the construction site are designed according to the condition of ensuring the free passage of vehicles: permanent roads with a width of 6 m, temporary roads with a width of 3.5m, a turning radius of 12 m. At the turns, widening by 1 m is provided. Road slopes are linked to the terrain.
Water supply and sewerage, designed based on the conditions for providing industrial household and fire-fighting construction needs in water. The distance between hydrants does not exceed 150 m, they are located no further than 2 m from the road, 2 hydrants are provided.
To provide electricity from the existing network, an FTC unit with a capacity of 180 to W is provided. In order to ensure reliable power supply, an annular electrical support system has been designed, air lines are provided along the driveways, which makes it possible to use poles for outdoor lighting fixtures and facilitates operating conditions. In the areas of the site where the crane operates, cable laying is provided.
The entire territory of the construction site is fenced with a vertical fence of wooden shields. At the places of entry and exit there is a gate, along the entire perimeter of the construction site there is a lighting network with spotlights.
Кал. план.dwg

Архитектура выпуск.dwg

ТСП_Тех.карта( Моя).dwg

Similar materials
- 04.04.2016
Free downloading for today
- 22.08.2014
- 29.08.2014