Разработка технологии и оборудования для сборки и сварки мобильной автозаправочной станции










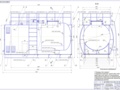
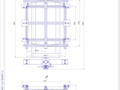
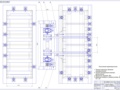
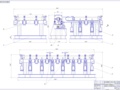
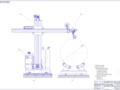
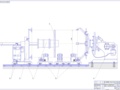
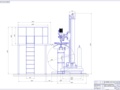
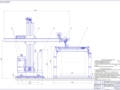
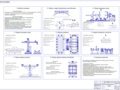
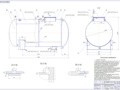
- Добавлен: 14.05.2021
- Размер: 5 MB
- Закачек: 7
Описание
Выпускная квалификационная работа состоит из 10 листов (формат А1) графической части и 103 страниц пояснительной записки, содержащей 39 рисунка, 16 таблиц и список использованных источников из 22 наименования.
Целью выпускной квалификационной работы является повышение качества сварных швов контейнерной мобильной автозаправочной станции за счет применения нового технологического процесса.
В работе проанализированы свойства углеродистой стали. Выбран способ сварки в среде защитных газов. Описана сущность выбранного способа сварки. Выбраны материалы для сварки. Определены оптимальные технологические параметры. Разработан технологический процесс автоматизированной сварки изделия. Предложен проект сварочного комплекса. Рассчитан экономический эффект от применения комплекса. Рассмотрены вопросы обеспечения безопасности труда на производстве.
Выполнены графические иллюстрации:
- Контейнерная автозаправочная станция станция КАЗС-10 – 1 лист (А1);
- Резервуар горизонтальный одностенный РГС 10 – 1 лист (А1);
- Технологический лист – 1 лист (А1);
- Комплекс оборудования сварки продольных швов – 2 листа (А1);
- Комплекс оборудования сборки и прихватки кольцевых швов – 1 лист (А1);
- Стенд сварки кольцевых швов – 1 лист (А1);
- Стенд сборки и сварки основания – 2 листа (А1);
- Приспособления для сборки и сварки каркаса – 1 лист (А1).
Состав проекта
![]() ![]() ![]() ![]() |
![]() ![]() ![]() |
![]() ![]() ![]() ![]() |
![]() ![]() ![]() ![]() |
![]() ![]() ![]() ![]() |
![]() ![]() ![]() ![]() |
![]() ![]() ![]() ![]() |
![]() ![]() ![]() ![]() |
![]() ![]() ![]() ![]() |
![]() ![]() ![]() ![]() |
![]() ![]() ![]() ![]() |
![]() ![]() ![]() ![]() |
![]() ![]() ![]() ![]() |
![]() ![]() ![]() ![]() |
![]() ![]() ![]() ![]() |
![]() ![]() ![]() ![]() |
![]() ![]() ![]() ![]() |
![]() ![]() ![]() ![]() |
Дополнительная информация
Содержание
СОДЕРЖАНИЕ
ВВЕДЕНИЕ
1 АНАЛИЗ СОСТОЯНИЯ ИЗДЕЛИЯ
1.1 Назначение изделия и условия эксплуатации
1.2 Материал изделия и его свариваемость
1.3 Обоснование выбора способа сварки
1.4 Сущность и основные параметры сварки в защитных газах
1.5 Цель работы и постановка задач
2 ТЕХНОЛОГИЧЕСКИЙ РАЗДЕЛ
2.1 Выбор сварочных материалов
2.2 Определение параметров режима сварки
2.3 Разработка технологического процесса
2.4 Проведение контроля качества
3 КОНСТРУКТОРСКИЙ РАЗДЕЛ
3.1 Описание основного сварочного оборудования
3.2 Выбор вспомогательного оборудования
3.3 Стенд для сборки и сварки продольных швов обечаек
3.4 Стенд для сборки и прихватки кольцевых швов
3.5 Стенд для сварки кольцевых швов
3.6 Стенд для сборки и сварки основания
3.7 Приспособление для сборки и сварки каркаса корпуса контейнера
4 ЭКОНОМИЧЕСКИЙ РАЗДЕЛ
4.1 Общие положения
4.2 Расчёт капитальный вложений
4.3 Штучно-калькуляционное время
4.4 Расчёт потребного количества оборудования
4.5 Расчет затрат на материалы
4.6 Расчёт численности рабочих
4.7 Расчёт заработной платы
4.8 Амортизация оборудования
4.9 Определение затрат на технологическую электроэнергию
4.10 Определение затрат на силовую энергию
4.11 Затраты на ремонт и техническое обслуживание
4.12 Расчет годового эффекта и срока окупаемости
5 БЕЗОПАСТНОСТЬ ЖИЗНЕДЕЯТЕЛЬНОСТИ
5.1 Охрана труда
5.2 Защита в чрезвычайных ситуациях
ЗАКЛЮЧЕНИЕ
СПИСОК ИСПОЛЬЗОВАННЫХ ИСТОЧНИКОВ
Введение
На данный момент в обороте много изделий такого типа, которые имеют разные наименования, но по сущности выполняемых функций они схожие. К ним можно отнести: мобильные АЗС, контейнерные АЗС, топливозаправочные модули, топливные модули, и т.д. МЧС распределяет и объединяет их как контейнерные АЗС (КАЗС), а собственно: "Контейнерная автозаправочная станция – это и открытый наземный резервуар с внутренним технологическим отделением для ТРК, что в комплексе означает емкость для хранения топлива, и предохранительный в контейнере резервуар, называющийся "топливный модуль" – все это контейнерные АЗС [17]. Безразлично, как они спроектированы и называются. Главное, чтобы они были как единое изделие.
Согласно правилам МЧС, утвержденными в РФ, вероятность использования КАЗС с одностенной емкостью очень ограничена. Такие АЗС возможно использовать только вне населенного пункта, емкость не должна превышать 10м3 [15]. Под КАЗС необходимо сконструировать основание, вмещающее объем возможного розлива всего топлива в полость КАЗС, что само по себе довольно дорого и снижает возможность мобильного переноса АЗС на другое место, так как потребуется сооружать новый поддон. Таким образом, для спокойной и комфортной эксплуатации КАЗС альтернативы двустенному резервуару нет.
Анализ состояния изделия
1.3 Обоснование выбора способа сварки
Для сварки данной конструкции изделия выполненной из конструкционных углеродистых сталей в целях механизации и автоматизации процесса сборки и сварки применимы следующие способы сварки: автоматическая и механизированная сварка в углекислом газе.
Механизированная сварка в среде защитных газов может проводиться несколькими различными способами, в зависимости от того, какой тип защиты используется для нее. В данном случае применить механизированную сварку в защитном газе более экономично и не трудоемко, так как в настоящее время выпускается большое количество моделей аппаратов, у которых очень широкий выбор параметров, дополнительных функций и прочих особенностей. Таким образом, специалист может подобрать технику практически для любой сферы применения [2,19].
Здесь отлично сочетаются свойства газовой и электрической сварки, но главной особенностью является использование механизированного устройства подачи. Оно единственное, которое работает здесь в автоматическом режиме, так как сама сварка производится вручную. Благодаря его наличию методика и получила название полуавтоматической.
Полуавтоматическая сварка в защитном газе очень широко распространена благодаря своей универсальности. С ее помощью можно соединять не только обыкновенные углеродистые стали, но и металлы, сложно поддающиеся сварке. Правильно подобранный режим и газ для защиты позволит совершить сварку любого изделия, будь то алюминиевые детали, трубы из нержавейки. Разнородные металлы в одной конструкции и так далее.
Для сварки протяженных швов конструкции, таких как продольные и кольцевые швы обечаек целесообразно применить автоматическую сварку, так как автоматические сварочные аппараты, обеспечивают [2]:
– автоматическое выполнение основных технологических перемещений электрода и дуги с поддержанием постоянства заданных параметров сварочного режима напряжения дуги, сварочного тока, скорости сварки.
Сварочные автоматы состоят из следующих основных узлов: сварочной головки, механизма перемещения, аппаратуры управления, механизма поддержания постоянства длины дуги, а также аппаратуры, обеспечивающей подачу в зону сварки защитного газа.
Большую группу аппаратов для дуговой автоматической сварки составляют подвесные сварочные головки. Их применяют главным образом в установках, когда в процессе сварки передвигается изделие или когда головка закреплена на перемещающейся части установки. Часто в качестве подвесных сварочных головок применяют отдельные узлы самоходных аппаратов. Однако в некоторых случаях подвесные сварочные головки выпускаются заводами изготовителями в виде автономных агрегатов, оснащенных пультом управления и шкафом электроаппаратуры [19].
Подвесные головки, как правило, состоят из сварочной горелки, механизма подачи присадочной проволоки, механизмов для установочных перемещений горелки, катушки для электродной проволоки и устройства для закрепления головки на консоли или траверсе.
Таким образом, можно выявить что механизированная и автоматическая сварка, при производстве этой конструкции не заменимы тем что:
– возможно, сваривать детали из разнообразных металлов разной толщины;
– возможность сварки в различных пространственных положениях, так как это требует конструкция изделия;
– широкое разнообразие моделей современных инверторов, которые с каждым годом все больше развиваются.
– возможность наблюдения за образованием шва и легкость механизации и автоматизации процесса.
К недостаткам этих способов можно отнести:
– необходимость применения защитных мер против световой и тепловой радиации дуги, возможность нарушения газовой защиты при сдувании струи и, в некоторых случаях, трудность осуществления водяного охлаждения горелок.
– много параметров для выставления правильного режима;
– работа с газом всегда остается опасной для сварщика и окружающих.
1.5 Цель работы и постановка задач
В ходе рассмотрения и анализа конструкции изделия, описания материала применяемого при изготовлении и его свариваемости, выбран способ сварки, который будет значительно влиять на качество сварных соединений и технологический процесс производства данного изделия. Так как технологический процесс – это не только наличие определенных механизмов и машин для осуществления сборочных и сварочных операций, но и их правильное применение при производстве.
Тем самым, дальнейшей целью этой работы, является:
– назначение сварочных материалов;
– определение параметров режима сварки, в целях оптимизации процесса;
– подбор специализированного и вспомогательного оборудования;
– рассмотрение вопросов о охране труда и действиях в чрезвычайных ситуация при производстве;
– расчет экономической эффективности предлагаемой технологии.
Технологический раздел
2.3 Разработка технологического процесса
Разработка технологического процесса производства контейнерной автозаправочной станции представляет собой комплекс операций, которые включают в себя поэтапную сборку и сварку отдельных частей конструкции изделия. И так первой операцией технологического процесса является сборка и сварка резервуара, в котором будет храниться, и эксплуатироваться топливо.
Операция № 1
Процесс производства емкостей такого типа включает в себя входной контроль всех деталей емкости, а также сварочных материалов, которые будут влиять на качество сварных соединений и их воздействие на общую составляющую конструкции при производстве.
Все детали и сварочные материалы при строительстве стальных горизонтальных резервуаров для хранения эксплуатации нефтепродуктов их качество и входной контроль должны соответствовать ПБ 0338400.
После входного контроля осуществляет заготовительный процесс деталей, который включает в себя зачистку, разметку, наметку, оправку и их резку необходимых размеров. Далее заготовленные детали поступают на пост гибки листов обечаек с помощью трехвалковых станков. И так после выше описанных операций начинается процесс сборки и сварки продольных швов полуобечаек.
Операция № 2
С помощь тельферного крана переместить заготовленные листы полуобечаек на пост сборки и сварки продольных швов. Сборка и сварка этих деталей осуществляется на вспомогательном приспособлении клавишного типа для этого нужно:
– подготовить приспособление для дальнейших действий;
– проверить его исправность;
–задать параметры усилия зажатия кромок на стенде;
– наладить и настроить сварочную аппаратуру;
– обеспечить беспрепятственное перемещение сварочной головки вдоль стыка;
– прихватить с обоих концов выводные пластины в соответствии с РД 26.260.2252001 [20].
– завести кромки обечаек в клавишное приспособление и стыковать с пределом допуска указанном в ГОСТ 1477176 [6].
– подать давление воздуха в пневмосистему и зажать стыкуемые кромки детали.
– задать выше представленные параметры сварки стыковых соединений и начать процесс сварки;
– после сварки разжать кромки свариваемого стыка и вывести сваренную деталь;
– удалить выводные пластины и зачистить сварной шов.
Использованное оборудование:
– приспособление клавишного типа;
– сварочная колонна КС 200;
– сварочная головка производства ИТС;
– источник питания ВС450;
– сварочный инвертор;
Параметры режима сварки;
– сварочный ток, А 110;
– напряжение на дуге, В 22.4;
– скорость подачи электродной проволоки, м/ч 127;
– скорость сварки, м/ч 18;
– расход газовой смеси, л/час 10.
Сварочные материалы:
– электродная проволока ПСГ 0301;
– газовая смесь CO2+O2.
Операция № 3
После операции сборки и сварки продольных швов, обечайки поступают на пост сборки кольцевых стыков полуобечаек и днищ. Процесс сборки кольцевых стыков будет осуществляться помощью подкладных колец, так как толщина свариваемых деталей составляет меньше допустимой нормы для сварки без них. Расположение и сборка колец жесткости должны соответствовать ГОСТ 170322010 [18]. Сборка днищ должна проводиться в соответствии с ГОСТ 343472017 [16, 18]. Для сборки кольцевых стыков следует:
– установить обечайки на приводные роликоопоры;
– подвести кромки стыкуемых обечаек;
– подвести тележку с установленной на ней консолью, с которой сопряжено распорное кольцо;
– завести заранее подготовленное подкладное кольцо и стыковать обечайки в соответствии с ГОСТ 1477176 С5 [6];
– подать воздух в пневмосистему распорного кольца;
– прихватить стыкуемые кромки;
– далее, на гидравлический позиционер с захватным механизмом, расположить днище;
– подвести прихваченные обечайки к позиционеру и состыковать днища в соответствии с ГОСТ 1477176 С6 [6];
– прихватить стыкуемые кромки.
Комплекс используемого оборудования:
– роликовая опора с приводом;
– тележка с консолью;
– распорное кольцо;
– позиционер гидравлический;
– источник питания ВС450;
– подающий механизм Форсаж со сварочной горелкой.
Сварочные материалы:
– электродная проволока ПСГ 0301;
– газовая смесь CO2+O2.
Операция № 4
После механизированной сборки кольцевых стыков изделие на роликоопорах перемещается на пост сварки. При сварке кольцевых стыков цилиндрических деталей является, правильно отлаженное сварочное и вспомогательное оборудование. Процесс сварки должен проходить стабильно, без проскальзывании изделия в роликоопорах, заедания сварочной головки и т.п. Для сварки кольцевых швов следует:
– настроить сварочную колонну;
– подвести и настроить сварочную головку на свариваемый стык;
– убедиться в исправности сварочного оборудования;
– проверить газобаллонную аппаратуру и задать параметры сварки;
– сварить кольцевые швы обечаек и днищ в соответствии с ГОСТ 1477176 [6] тип сварных соединений обечаек С5 и С6;
– после сварки зачистить и провести визуальный осмотр швов.
Комплекс использованного оборудования:
– роликовая опора с приводом;
– сварочная колонна КС 200;
– сварочная головка производства ИТС;
– источник питания ВС450;
Параметры режима сварки;
– сварочный ток, А 112
– напряжение на дуге, В 23,2
– скорость подачи электродной проволоки, м/ч 143
– скорость сварки, м/ч 14
– расход газовой смеси, л/час 12.
Сварочные материалы:
– электродная проволока ПСГ 0301;
– газовая смесь CO2+O2.
После завершительной сборки и сварки кольцевых швов обечаек и днищ к резервуару привариваются горловина люка лаза, патрубки и прочая запорная арматура. Далее изготовленный резервуар устанавливается на несущие седловые опоры изготовленные по ОСТ 26209193 [17] и поступает на пост покрытия изделия антикоррозионными веществами в соответствии с ГОСТ Р 526302012 [16, 18].
Операция № 5
Данная операция является комплексной операцией сборки и сварки несущей конструкции изделия. Сборка основания будет осуществляться с помощью специализированного стенда книжного типа, преимуществом которого является одновременная сборка и сварка рамы и настила. Для сборки и сварки основания следует:
– заготовленные профиля рамы уложить на основание стенда, соблюдая допуски и отклонения от осей конструкции;
– убедиться, что ничего не препятствует правильной сборке рамы;
– на стенде сварки в нормальном положении расположить настил основания рамы;
– подать воздух в пневмосистему стенда для сварки в обратном положении.
Операция № 6
Сварка основания рамы и настила:
– настроить параметры режима сварки тавровых и нахлесточных швов;
– начать процесс сварки профилей;
– после сварки с обратной стороны раму повернуть на 180 градусов встроенным кантователем, и расположить на стенд сварки в нормальном положении для приварки верхнего настила.
– начать процесс приварки настила;
– по окончанию сварки основания разжать пневмосистему и с помощью крана вывести его из стенда.
Использованное оборудование:
– стенд для сборки и сварки основания;
– источник питания ВС450;
– подающий механизм Форсаж со сварочной горелкой.
Параметры режима сварки;
– сварочный ток, А 127
– напряжение на дуге, В 26
– расход газовой смеси, л/час 15
Сварочные материалы:
– электродная проволока ПСГ 0301;
– газовая смесь CO2+O2.
Операция № 7
На данном этапе комплексной сборки и сварки изделия осуществляется процесс установки емкости с седловыми опора на изготовленное основание изделия. После установки емкости на основание в соответствии размеров и допусков, указанных на чертеже: ДП206899915.05.0100000001 начинается операция сборки и сварки каркаса корпуса контейнера. Для этого следует на приспособлении поворотного стола чертеж: ДП206899915.05.0100000010 осуществить процесс сборки каркаса в порядке действий:
– для наклона стола ослабить тормоз;
– привести устройство в горизонтальное положение;
– ослабить элементы направляющих для установки параметров каркаса;
– уложить элементы каркаса и закрепить их с помощью зажимов;
– скорректировать отклонения параметров каркаса;
– уравновесить конструкцию перед началом сварки первого узла;
– ослабить прижимное кольцо;
– придерживая конструкцию, ослабить тормоз и поднять ее до верхнего вертикального положения, закрепить тормоз;
– установить шток цилиндра вертикально над осью поворота и зажать тормозное кольцо;
– придерживая конструкцию отпустить тормоз;
– в цилиндры пневматической системы набрать воздух, закрыть воздушный кран.
Операция № 8
– привести конструкцию в позицию для сварки;
– задать параметры режима сварки;
– сварить каркас в верхнем положении, затем перевернуть стол и сварить с обратной стороны;
– для снятия каркаса привести его в горизонтальное положение;
– ослабить все зажимные элементы и снять каркас.
После сварки каркаса установить его на основание конструкции и приварить его с помощью полуавтоматической сварки. Далее осуществить комплексный процесс сборки и их сварки всей конструкции: обшивки, верхней площадки, лестницы дверей и прочих сборочных единиц. Подвергнуть изделие визуальному и измерительному контролю. Убедиться, что размеры и общий вид конструкции соответствуют проекту.
Операция № 9
Контроль качества сварных соединений следует провести:
а) визуальным осмотром и измерением;
б) физическими методами;
в) гидравлическим испытанием.
Контроль качества поверхностей конструкции на наличие трещин, закатов, расслоений, снижающих качество продукции, следует проводить в первую очередь визуальным осмотром.
Визуальный контроль, включая измерения, необходимо проводить после очистки швов и прилегающих поверхностей от шлака, брызг и других загрязнений. Контролю и измерению подлежат все сварные швы для выявления наружных недопустимых дефектов.
В сварных соединениях не допускаются следующие дефекты:
– трещины всех видов;
– свищи и пористость наружной поверхности шва;
– подрезы глубиной более 0,25 мм, протяженность более 10% длины шва;
– наплывы, прожоги и незаплавленные кратеры;
– смещение кромок свариваемых элементов более 10% номинальной толщины свариваемых элементов;
– угловатость;
– местный внутренний непровар, расположенный в зоне смыкания корневых швов, глубиной более 10% толщины стенки и суммарной протяженностью более 5% длины шва.
Если конструкция изделия не позволяет при техническом освидетельствовании проведения гидравлического испытания и/или визуального и измерительного контроля (наружного или внутреннего) в объеме, требуемом в ГОСТ 343472017 [18], должны быть предусмотрены компенсирующие меры при расчете и проектировании изделия. В технической документации должны быть указаны методика, периодичность и объем контроля, выполнение которых обеспечит своевременное выявление и устранение дефектов [20].
Заключение
В данной дипломной работе рассмотрена и разработана технология и оборудование сборки и сварки контейнерной мобильной автозаправочной станции объемом 10 кубометров, предназначенной для хранения и транспортировки горючих жидкостей.
Для разработки технологического процесса проведен анализ состояния вопроса, производства данного изделия, охарактеризованы материал и его свариваемость, рассмотрены и определены наиболее подходящие способы сварки конструкции изделия. Подобраны все необходимые сварочные материалы в соответствии с требованиями сварки данного материала изделия, определены режимы сварки и составлен технологический процесс его сборки и сварки, подобран необходимый комплекс сварочного и вспомогательного оборудования, описаны мероприятия при контроле качества и испытаниях сварных соединений, рассмотрены вопросы охраны труда рабочего персонала и их действий при чрезвычайных ситуациях в производственном процессе.
Данная технология позволит сократить общее время, на производство изделия, сохраняя качество сварных соединений в данный срок эксплуатации. Расчет экономической эффективности показал, что применение данной технологии целесообразно и экономически эффективно.
7 Комплекс оборудования сварки кольцевых швов.cdw

Газобаллонная аппаратура
ДП-02068999-23-004.07.00.000
ДП-02068999-23-004.07.00.001
ДП-02068999-23-004.07.00.002
ДП-02068999-23-004.07.00.003
2 Изделие РГС 10.cdw

Неуказанные предельные отклонения по H14
Плотность хранимых продуктов не более 1300 кгм³
Максимальная температура хранимого продукта не
минимальная – не ниже минус 65 °С.
(РГСН) руководствоваться
следующими нормативными документами:
ГОСТ 34347-2017 «Сосуды и аппараты стальные сварные.
ПБ 03-384-00 «Правила проектирования
приемки сосудов и аппаратов стальных сварных»
ГОСТ 17032-2010 «Резервуары стальные горизонтальные
для нефтепродуктов. Технические условия»
ТУ 5265-002-30456536-2013.
Резервуар установить на седловые металлические
ложементы (опоры) по ОСТ 26-2091-93.
Сварные швы (№ 1 и 2) выполнить по ГОСТ 14771-76
сваркой в защитном газе. Сварные швы приварки горловины
люка и патрубка выполнить по ГОСТ 14771-76 механизи-
рованной сваркой в защитном газе.
Резервуар горизонтальный
ДП-02068999-23-004.02.00.000СБ
3 Технологический лист.cdw

Выпрямитель сварочный - ВС-450;
Стенд клавишного типа;
Проволока электродная ПГС-0301.
Расход газа 11-12 лч.
Проверить состояние документации на баллоны СО
Источник питания ВС-450;
Механизм подачи проволоки ФОРСАЖ-МП5.
Параметры режима сварки:
Сила сварочного тока
Скорость подачи проволоки
Сварочные материалы:
Сварочная проволока ПСГ-0301 диаметром 1
Защитный газ смесь СО
Выпрямитель сварочный - ВС-450;
Механизм подачи проволоки;
Проволока электродная ПГС-0301.
Расход газа 12-14 лч.
Напряжение U = 24.5 В
Расход газа 15-16 лч.
Стенд механизированной сборки;
Механизм подачи проволоки;
Приспособление для сборки;
Механизм подачи проволоки ФОРСАЖ-МП5;
Проволока электродная ПСГ-0301.
При сооружении резервуаров применить следующие виды контроля
качества сварных соединений:
- визуальный контроль;
геодезических приборов и т.д.;
- контроль герметичности (непроницаемости) сварных швов с
использованием проб «мел-керосин»
давления воздуха или цветной дефектоскопии;
- физический для выявления наличия внутренних дефектов:
радиография или ультразвуковая дефектоскопия
а для контроля наличия
поверхностных дефектов с малым раскрытием магнитография или
цветная дефектоскопия;
- гидравлический или пневматический прочностные испытания
конструкции резервуара.
ДП-02068999-23-004.03.00.000Д01
Сборка и сварка продольного шва обечайки
Сварка кольцевых швов
Сварка основания и настила
Оборудование и материалы:
Проверить наличие сертификатов на металл и соответствия
сертификатов с ГОСТом.
Проконтролировать сварочные материалы на соответствие
предъявляемым к ним.
Проверить наличие и целостность упаковки на сварочный
Проверить состояние проволоки на отсутствие задиров
правильность укладки проволоки.
Партия сварочных материалов считается пригодной
все механические характеристики технологических проб
отвечают нормативным требованиям.
Проверить свариваемый металл на отсутствие расслоений
Сборка кольцевых швов
Сварка каркаса корпуса котейнера
Сборка каркаса корпуса
6 Комплекс оборудования сборки и прихватки днищ.cdw

ДП-02068999-23-004.04.00.000
ДП-02068999-23-004.06.00.000
Приводная роликоопора
Привод подачи проволоки
Газобаллонная аппартура
ДП-02068999-23-004.06.00.001
ДП-02068999-23-004.06.00.002
ДП-02068999-23-004.06.00.003
4, 5 Комплекс оборуд. сварки продольных швов.cdw

ДП-02068999-23-004.03.00.000
ДП-02068999-23-004.04.00.000
ДП-02068999-23-004.05.00.000
Газобаллонная аппаратура
ДП-02068999-23-004.05.00.001
ДП-02068999-23-004.04.00.002
ДП-02068999-23-004.04.00.003
ДП-02068999-23-004.05.00.004
ДП-02068999-23-004.05.00.005
ДП-02068999-23-004.05.00.006
ДП-02068999-23-004.05.00.007
ДП-02068999-23-004.05.00.008
5 Комплекс оборудования сварки продольных швов обечаек.cdw

сварки продольных швов
ДП-02068999-23-004.05.00.000ВО
4 Комплекс оборудования сварки продольных швов.cdw

Диаметр свариваемых обечаек
Длина свариваемых кромок
Толщина свариваемых кромок
Усилие прижима на погонный см.при давлении воздуха
Расстояние между рядами прижимов
Технические требования
На данном виде лестничная площадка условно не показана
*Размеры для справок
Пневмосистему испытать на герметичность
. Утечки воздуха не допускаются.
Хобот должен свободно поворачиваться на оси в обе
стороны и надежно фиксироваться в рабочем положении.
Кромки прижимов должны быть параллельны и
установлены на равном расстоянии
относительно канавки
Допускаемое отклонение
Комплекс оборудования
сварки продольных швов
ДП-02068999-23-004.04.00.000ВО
8 Стенд сборки и сварки основания.cdw

6 Комплекс оборудования сборки и прихватки днищ.cdw

*Размеры для справок
Диаметр собираемого изделия
Длина собираемого зделия
Привод распорного кольца электро-
Привод позиционера гидравлический
ДП-02068999-23-004.06.00.000ВО
Комплекс оборудования
8, 9 Стенд сборки и сварки основания.cdw

Зажим пневматического привода
ДП-02068999-23-004.08.00.000
ДП-02068999-23-004.09.00.000
ДП-02068999-23-004.09.00.001
ДП-02068999-23-004.08.00.002
ДП-02068999-23-004.08.00.003
ДП-02068999-23-004.08.00.004
ДП-02068999-23-004.08.00.005
ДП-02068999-23-004.08.00.006
ДП-02068999-23-004.08.00.007
ДП-02068999-23-004.09.00.008
1 Изделие.cdw

Наружное покрытие: грунт один слой и
цвет по согласованию
Внутренне покрытие не предусмотрено
Межстенное пространство заполнить
ДП-02068999-23-004.01.00.000СБ
9 Стенд сборки и сварки основания.cdw

Принцип фиксации деталей
Привод кантователя электро-
Давление воздуха в пневмосистеме
ДП-02068999-23-004.09.00.000ВО
1 Изделие.cdw

Труба квадратная 20х2
Труба квадратная 30х2
ДП-02068999-23-004.01.00.001
ДП-02068999-23-004.01.00.002
ДП-02068999-23-004.01.00.003
ДП-02068999-23-004.01.00.004
ДП-02068999-23-004.01.00.005
ДП-02068999-23-004.01.00.006
ДП-02068999-23-004.01.00.007
ДП-02068999-23-004.01.00.008
ДП-02068999-23-004.01.00.009
ДП-02068999-23-004.01.00.010
7 Комплекс оборудования сварки кольцевых швов.cdw

* Размеры для справок
Диаметр свариваемых изделий
Толщина свариваемых кромок
Длина свариваемых изделий
Тип привода колонны электрический
Тип привода поворотного стола
Фиксирующий тормоз колонны
Тип привода роликоопор электро-
ДП-02068999-23-004.07.00.000ВО
10 Приспособление сборки и сварки каркаса.cdw

Рейка направляющая верхняя
Рейка направляющая нижняя
Привод пневматический
ДП-02068999-23-004.10.00.000
ДП-02068999-23-004.10.00.001
ДП-02068999-23-004.10.00.002
ДП-02068999-23-004.10.00.003
ДП-02068999-23-004.10.00.004
ДП-02068999-23-004.10.00.005
ДП-02068999-23-004.10.00.006
ДП-02068999-23-004.10.00.007
ДП-02068999-23-004.10.08.000
2 Изделие.cdw

ДП-02068999-23-004.02.00.000
Строповое устройство
Обечайка с отв. под люк
Прокладка паронитовая
ДП-02068999-23-004.02.00.001
ДП-02068999-23-004.02.00.002
ДП-02068999-23-004.02.00.003
ДП-02068999-23-004.02.00.004
ДП-02068999-23-004.02.00.005
ДП-02068999-23-004.02.00.006
ДП-02068999-23-004.02.00.007
ДП-02068999-23-004.02.00.008
ДП-02068999-23-004.02.00.009
ДП-02068999-23-004.02.00.010
10 Приспособление сборки и сварки каркаса.cdw

Максимальный размер рамы 2
Максимальная полезная нагрузка
Поворот на 180° с фиксацией
Диапазон вертикального поворота
Выравнивание нагрузки пневматическое.
ДП-02068999-23-004.10.00.000ВО
сборки и сварки каркаса
Рекомендуемые чертежи
- 20.06.2022
- 12.09.2021
- 29.07.2014
- 18.10.2021