Development of technology and equipment for assembly and welding of mobile filling station










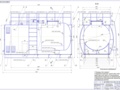
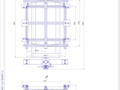
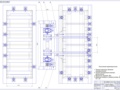
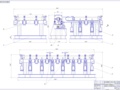
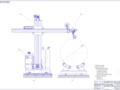
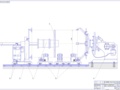
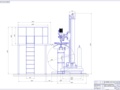
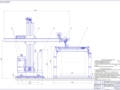
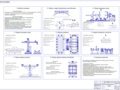
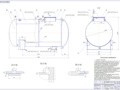
- Added: 14.05.2021
- Size: 5 MB
- Downloads: 7
Description
The graduation qualification work consists of 10 sheets (format A1) of a graphic part and 103 pages of an explanatory note containing 39 figures, 16 tables and a list of used sources from 22 names.
The purpose of the graduation qualification work is to improve the quality of the welded joints of the container mobile filling station due to the use of a new technological process.
The paper analyzed the properties of carbon steel. Method of welding in medium of protective gases is chosen. The essence of the selected welding method is described. Welding materials are selected. Optimal process parameters have been determined. The process of automated welding of the product has been developed. Proposed is welding complex design. The economic effect of the complex is calculated. Issues of occupational safety are considered.
Graphic illustrations made:
- KAZS-10 container filling station - 1 sheet (A1);
- Tank horizontal single-wall CSG 10 - 1 sheet (A1);
- A technological leaf - 1 leaf (A1);
- Complex of equipment for welding longitudinal joints - 2 sheets (A1);
- A complex of the equipment of assembly and a tack of ring seams - 1 leaf (A1);
- Ring welding bench - 1 sheet (A1);
- Base assembly and welding bench - 2 sheets (A1);
- Fixtures for assembling and welding the frame - 1 sheet (A1).
Project's Content
![]() ![]() ![]() ![]() |
![]() ![]() ![]() |
![]() ![]() ![]() ![]() |
![]() ![]() ![]() ![]() |
![]() ![]() ![]() ![]() |
![]() ![]() ![]() ![]() |
![]() ![]() ![]() ![]() |
![]() ![]() ![]() ![]() |
![]() ![]() ![]() ![]() |
![]() ![]() ![]() ![]() |
![]() ![]() ![]() ![]() |
![]() ![]() ![]() ![]() |
![]() ![]() ![]() ![]() |
![]() ![]() ![]() ![]() |
![]() ![]() ![]() ![]() |
![]() ![]() ![]() ![]() |
![]() ![]() ![]() ![]() |
![]() ![]() ![]() ![]() |
Additional information
Contents
CONTENTS
INTRODUCTION
1 ARTICLE CONDITION ANALYSIS
1.1 Purpose of the article and operating conditions
1.2 Article material and its weldability
1.3 Justification of welding method selection
1.4 Essence and main parameters of welding in protective gases
1.5 Purpose of work and setting of tasks
2 PROCESS SECTION
2.1 Selection of welding materials
2.2 Determination of welding mode parameters
2.3 Process Development
2.4 Performance of quality control
3 DESIGN SECTION
3.1 Description of main welding equipment
3.2 Selection of auxiliary equipment
3.3 Bench for assembly and welding of longitudinal joints of shells
3.4 Bench for assembly and tacking of ring seams
3.5 Ring Welding Bench
3.6 Base Assembly and Welding Bench
3.7 Accessory for assembly and welding of container body frame
4 ECONOMIC SECTION
4.1 General provisions
4.2 Calculation of capital investments
4.3 Piece and Calculation Time
4.4 Calculation of required quantity of equipment
4.5 Material Cost Calculation
4.6 Calculation of the number of workers
4.7 Payroll calculation
4.8 Equipment depreciation
4.9 Determination of Process Power Costs
4.10 Determining Power Costs
4.11 Repair and maintenance costs
4.12 Calculation of annual effect and payback period
5 SAFETY OF LIFE
5.1 Occupational Safety
5.2 Emergency Protection
CONCLUSION
LIST OF SOURCES USED
Introduction
At the moment, there are many products of this type in circulation that have different names, but in the essence of the functions performed they are similar. These include: mobile filling stations, container filling stations, fuel filling modules, fuel modules, etc. The Ministry of Emergency Situations distributes and combines them as container filling stations (KAZS), and in fact: "A container filling station is also an open ground tank with an internal process compartment for TRC, which in the complex means a fuel storage tank, and a container safety tank called a" fuel module "- all these are container filling stations [17]. It is indifferent how they are designed and called. The main thing is that they are like a single product.
According to the rules of the Ministry of Emergencies, approved in the Russian Federation, the probability of using a KAZS with a single-wall capacity is very limited. Such filling stations can be used only outside the settlement, the capacity should not exceed 10m3 [15]. For KAZS, it is necessary to design a base containing the volume of possible bottling of all fuel into the KAZS cavity, which in itself is quite expensive and reduces the possibility of mobile transfer of filling stations to another place, since a new tray will need to be built. Thus, for calm and comfortable operation of the KAZS, there is no alternative to a double-wall tank.
Product Status Analysis
1.3 Justification of welding method selection
For welding of this structure of the article made of structural carbon steels for the purposes of mechanization and automation of the assembly and welding process, the following welding methods are used: automatic and mechanized welding in carbon dioxide.
Mechanized welding in the environment of protective gases can be carried out in several different ways, depending on the type of protection used for it. In this case, the use of mechanized welding in protective gas is more economical and not labor intensive, since at present a large number of models of devices are produced, which have a very wide choice of parameters, additional functions and other features. Thus, a person skilled in the art can select a technique for almost any application [2.19].
The properties of gas and electric welding are perfectly combined here, but the main feature is the use of a mechanized supply device. It is the only one that works here in automatic mode, since the welding itself is done manually. Thanks to its presence, the technique was called semi-automatic.
Semi-automatic welding in protective gas is very widespread due to its versatility. With its help, it is possible to combine not only ordinary carbonaceous steels, but also metals that are difficult to weld. A properly selected mode and gas for protection will allow welding of any product, be it aluminum parts, stainless steel pipes. Heterogeneous metals in one design and so on.
For welding of extended seams of the structure, such as longitudinal and annular seams of shells, it is advisable to use automatic welding, since automatic welders provide [2]:
- automatic execution of the main technological movements of the electrode and arc with maintaining constancy of the specified parameters of the welding mode of arc voltage, welding current, welding speed.
Welding machines consist of the following main units: a welding head, a movement mechanism, control equipment, a mechanism for maintaining the continuity of the arc length, as well as equipment providing the supply of protective gas to the welding zone.
A large group of devices for arc automatic welding are suspended welding heads. They are mainly used in installations when the article is moved during welding or when the head is fixed on the moving part of the installation. Often, separate units of self-propelled vehicles are used as suspended welding heads. However, in some cases, suspended welding heads are manufactured by manufacturers in the form of autonomous units equipped with a control panel and an electrical equipment cabinet [19].
Suspension heads typically consist of a welding torch, an additive wire feed mechanism, a torch locating movement mechanism, an electrode wire coil, and a device for securing the head to a cantilever or crosspiece.
Thus, it is possible to identify that mechanized and automatic welding, when producing this structure, is not replaced by the fact that:
- it is possible to weld parts from various metals of different thickness;
- the possibility of welding in various spatial positions, as this is required by the design of the article;
- a wide variety of models of modern inverters, which are increasingly developing every year.
- possibility of observing the formation of the seam and ease of mechanization and automation of the process.
The disadvantages of these methods include:
- the need to apply protective measures against light and thermal radiation of the arc, the possibility of violation of gas protection during blowing of the jet and, in some cases, the difficulty of carrying out water cooling of burners.
- many parameters for setting the correct mode;
- working with gas always remains dangerous for the welder and others.
1.5 Purpose of work and setting of tasks
During the review and analysis of the design of the article, the description of the material used in the manufacture and its weldability, a welding method was chosen that will significantly affect the quality of the welded joints and the manufacturing process of this article. Since the technological process is not only the presence of certain mechanisms and machines for performing assembly and welding operations, but also their correct use in production.
Thus, the further objective of this work is:
- purpose of welding materials;
- determination of welding mode parameters in order to optimize the process;
- selection of specialized and auxiliary equipment;
- Consideration of occupational safety and emergency situations;
- calculation of economic efficiency of the proposed technology.
Process Section
2.3 Process Development
The development of the manufacturing process of the container filling station is a set of operations that include the step-by-step assembly and welding of individual parts of the product structure. And so the first step of the process is to assemble and weld the tank in which the fuel will be stored and operated.
Operation # 1
The process of producing containers of this type involves the incoming inspection of all parts of the container, as well as welding materials, which will affect the quality of the welded joints and their effect on the general component of the design during production.
All parts and welding materials during construction of steel horizontal tanks for storage and operation of oil products their quality and incoming control shall comply with PB 0338400.
After entrance control carries out procuring process of details which includes cleaning, a marking, a basting, a mandrel and their cutting of the necessary sizes. Then the prepared parts are fed to the shell sheets bending station by means of three-roll machines. And so after the above described operations, the process of assembling and welding the longitudinal seams of the half-shells begins.
Operation # 2
With the help of a telfer crane, move the prepared half-shell sheets to the post of assembly and welding of longitudinal welds. The assembly and welding of these parts is carried out on a keypad accessory for this purpose:
- prepare a device for further action;
- check its serviceability;
- set parameters of edge clamping force on the bench;
- set up and set up welding equipment;
- ensure unimpeded movement of the welding head along the joint;
- attach lead plates at both ends in accordance with RD 26.260.2252001 [20].
- install the shell edges into the key accessory and dock with the tolerance limit specified in GOST 1477176 [6].
- supply air pressure to the pneumatic system and clamp the connected edges of the part.
- set the above presented parameters of butt joint welding and start the welding process;
- after welding, open the edges of the joint to be welded and bring out the welded part;
- remove the lead plates and grind the weld.
Equipment used:
- keyboard type accessory;
- welding column KS 200;
- welding head manufactured by ITS;
- VS450 power supply;
- welding inverter;
Welding mode parameters;
- welding current, A 110;
- arc voltage, V 22.4;
- electrode wire feed rate, m/h 127;
- welding speed, m/h 18;
- gas mixture flow rate, l/h 10.
Welding Materials:
- PSG 0301 electrode wire;
- CO2 + O2 gas mixture.
Operation # 3
After the operation of assembly and welding of longitudinal seams, shells come to the post of assembly of ring joints of half-shells and bottoms. The process of assembling ring joints will be carried out using backing rings, since the thickness of the welded parts is less than the permissible norm for welding without them. Arrangement and assembly of stiffening rings shall comply with GOST 170322010 [18]. Bottom assembly shall be in accordance with GOST 343472017 [16, 18]. To assemble ring joints:
- install the shells on the drive roller supports;
- bring the edges of the connected shells;
- bring the trolley with the cantilever installed on it, with which the spacer ring is coupled;
- start the pre-prepared lining ring and connect the shells in accordance with GOST 1477176 C5 [6];
- supply air to the pneumatic system of the spacer ring;
- grab the edges to be joined;
- further, on hydraulic positioner with gripping mechanism, position the bottom;
- to bring the taken feedwells to a positioner and to join the bottoms according to GOST 1477176 C6 [6];
- grab the edges to be docked.
Complex of used equipment:
- roller support with drive;
- trolley with console;
- spacer ring;
- hydraulic positioner;
- VS450 power supply;
- feed mechanism Afterburner with welding torch.
Welding Materials:
- PSG 0301 electrode wire;
- CO2 + O2 gas mixture.
Operation # 4
After mechanized assembly of ring joints, article on roller supports moves to welding station. When welding ring joints of cylindrical parts, it is a properly debugged welding and auxiliary equipment. The welding process must be stable, without slipping the product in roller supports, jamming the welding head, etc. For welding of ring welds, it should be:
- adjust the welding string;
- bring and adjust the welding head to the joint to be welded;
- make sure that welding equipment is serviceable;
- check the gas balloon equipment and set welding parameters;
- weld ring joints of shells and bottoms in accordance with GOST 1477176 [6] type of welded joints of shells C5 and C6;
- after welding grind and perform visual inspection of joints.
Complex of used equipment:
- roller support with drive;
- welding column KS 200;
- welding head manufactured by ITS;
- VS450 power supply;
Welding mode parameters;
- welding current, A 112
- arc voltage, V 23,2
- electrode wire feed rate, m/h 143
- welding speed, m/h 14
- gas mixture flow rate, l/h 12.
Welding Materials:
- PSG 0301 electrode wire;
- CO2 + O2 gas mixture.
After final assembly and welding of ring seams of shells and bottoms, manhole manhole, branch pipes and other shutoff valves are welded to the tank. Then the produced tank is installed on the load-bearing saddle supports made according to OST 26209193 [17] and comes to the item coating station with anticorrosive substances in accordance with GOST R 526302012 [16, 18].
Operation # 5
This operation is a complex operation of assembling and welding a structural structure of a product. Assembly of the base will be carried out using a specialized book-type stand, the advantage of which is the simultaneous assembly and welding of the frame and flooring. To assemble and weld a base, you must:
- lay the prepared frame profiles on the bench base, observing tolerances and deviations from the structural axes;
- make sure that nothing prevents the correct assembly of the frame;
- position the frame base flooring on the welding bench in normal position;
- supply air to the pneumatic system of the bench for welding in the reverse position.
Operation # 6
Welding of frame base and flooring:
- adjust the welding mode parameters of the T-joints and the lap joints;
- start the process of welding profiles;
- after welding from the back, turn the frame by 180 degrees with the built-in tilter, and place it on the welding bench in the normal position for welding of the upper flooring .
- start the process of welding the flooring;
- at the end of base welding open the pneumatic system and remove it from the bench using a crane.
Equipment used:
- stand for assembly and welding of base;
- VS450 power supply;
- feed mechanism Afterburner with welding torch.
Welding mode parameters;
- welding current, A 127
- arc voltage, V 26
- gas mixture flow rate, l/h 15
Welding Materials:
- PSG 0301 electrode wire;
- CO2 + O2 gas mixture.
Operation # 7
At this stage of complex assembly and welding of the product, the process of installation of the container with saddle supports on the manufactured product base is carried out. After installation of the container on the base in accordance with the dimensions and tolerances specified in the drawing: DP20689915.05.0100000001, the operation of assembly and welding of the container body frame begins. For this purpose the drawing follows on adaptation of a rotary table: DP206899915.05.0100000010 to carry out process of assembly of a framework in an operations procedure:
- loosen the brake to tilt the table;
- set the device to horizontal position;
- loosen guide elements for setting frame parameters;
- lay the frame elements and attach them using clamps;
- adjust deviations of frame parameters;
- balance the structure before starting welding of the first assembly;
- loosen the pressing ring;
- hold the structure, loosen the brake and lift it to the upper vertical position, attach the brake;
- install the cylinder rod vertically above the turning axis and clamp the brake ring;
- holding the structure to release the brake;
- gain air into the cylinders of the pneumatic system, close the air valve.
Operation # 8
- bring the structure to the welding position;
- set the welding mode parameters;
- weld the frame in the upper position, then turn the table and weld from the back;
- to remove the frame to the horizontal position;
- loosen all clamping elements and remove the frame.
After the frame is welded, install it on the base of the structure and weld it with the help of semi-automatic welding. Then perform a complex process of assembly and their welding of the entire structure: skin, top platform, door stairs and other assembly units. Visually and measurably inspect the article. Ensure that the dimensions and overall view of the design are consistent with the design.
Operation # 9
Quality control of welded joints should be carried out:
a) visual inspection and measurement;
b) by physical methods;
c) hydraulic test.
Quality control of structural surfaces for cracks, sunsets, stratifications that reduce product quality should be carried out primarily by visual inspection.
Visual inspection, including measurements, shall be carried out after cleaning of joints and adjacent surfaces from slag, spatter and other contaminants. All welds shall be monitored and measured to identify external unacceptable defects.
The following defects are not allowed in welded joints:
- cracks of all kinds;
- fistula and porosity of the outer surface of the seam;
- undercuts with depth more than 0.25 mm, length more than 10% of seam length;
- surges, burning and unfused craters;
- displacement of edges of welded elements more than 10% of nominal thickness of welded elements;
- angularity;
- local internal non-rover located in the zone of closure of root seams, depth more than 10% of wall thickness and total length more than 5% of seam length.
If the design of the article does not allow during the technical inspection of the hydraulic test and/or visual and measuring control (external or internal) in the volume required in GOST 343472017 [18], compensating measures shall be provided for the calculation and design of the article. The technical documentation shall indicate the procedure, periodicity and scope of control, the execution of which will ensure timely detection and elimination of defects [20].
Conclusion
In this thesis, the technology and equipment for assembly and welding of a container mobile gas station with a volume of 10 cubic meters is considered and developed, designed for storage and transportation of combustible liquids.
For the development of the process, the state of the issue, the production of this product was analyzed, the material and its weldability were described, the most suitable methods for welding the design of the product were considered and determined. All the necessary welding materials were selected in accordance with the requirements of welding of this material of the product, welding modes were determined and the technological process of its assembly and welding was compiled, the necessary complex of welding and auxiliary equipment was selected, measures for quality control and testing of welded joints were described, issues of labor safety of workers and their actions in emergency situations in the production process were considered.
This technology will reduce the total time to manufacture the product, maintaining the quality of welded joints during the given service life. The calculation of economic efficiency showed that the use of this technology is reasonable and cost-effective.
7 Комплекс оборудования сварки кольцевых швов.cdw

2 Изделие РГС 10.cdw

3 Технологический лист.cdw

6 Комплекс оборудования сборки и прихватки днищ.cdw

4, 5 Комплекс оборуд. сварки продольных швов.cdw

5 Комплекс оборудования сварки продольных швов обечаек.cdw

4 Комплекс оборудования сварки продольных швов.cdw

8 Стенд сборки и сварки основания.cdw

6 Комплекс оборудования сборки и прихватки днищ.cdw

8, 9 Стенд сборки и сварки основания.cdw

1 Изделие.cdw

9 Стенд сборки и сварки основания.cdw

1 Изделие.cdw

7 Комплекс оборудования сварки кольцевых швов.cdw

10 Приспособление сборки и сварки каркаса.cdw

2 Изделие.cdw

10 Приспособление сборки и сварки каркаса.cdw

Similar materials
- 07.04.2022
- 12.09.2021
- 20.06.2022
- 29.07.2014