Технологический процесс обработки детали Стакан




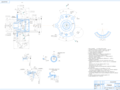
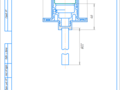
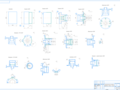
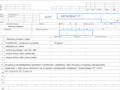
- Добавлен: 24.01.2023
- Размер: 1 MB
- Закачек: 2
Описание
Состав проекта
![]() |
![]() |
![]() |
![]() ![]() ![]() |
![]() |
![]() |
![]() ![]() ![]() ![]() |
![]() ![]() ![]() ![]() |
![]() ![]() ![]() ![]() |
![]() |
![]() |
![]() |
![]() |
![]() ![]() ![]() ![]() |
![]() |
![]() ![]() ![]() ![]() |
![]() ![]() ![]() ![]() |
![]() ![]() ![]() ![]() |
![]() ![]() ![]() ![]() |
![]() |
![]() |
![]() |
![]() |
![]() ![]() ![]() ![]() |
![]() |
![]() ![]() ![]() ![]() |
![]() |
![]() ![]() ![]() ![]() |
![]() ![]() ![]() ![]() |
![]() |
![]() |
![]() ![]() ![]() ![]() |
![]() |
![]() ![]() ![]() ![]() |
![]() |
![]() |
![]() |
![]() ![]() ![]() ![]() |
![]() ![]() ![]() ![]() |
![]() ![]() ![]() ![]() |
![]() ![]() ![]() ![]() |
![]() ![]() ![]() ![]() |
![]() ![]() ![]() ![]() |
![]() ![]() ![]() ![]() |
![]() ![]() ![]() ![]() |
![]() ![]() ![]() ![]() |
![]() ![]() ![]() ![]() |
![]() ![]() ![]() ![]() |
![]() |
![]() |
![]() |
![]() |
![]() ![]() ![]() ![]() |
![]() ![]() ![]() ![]() |
![]() |
![]() ![]() ![]() ![]() |
![]() ![]() ![]() ![]() |
![]() ![]() ![]() ![]() |
![]() ![]() ![]() ![]() |
![]() |
![]() |
![]() |
![]() ![]() ![]() ![]() |
![]() ![]() ![]() ![]() |
![]() ![]() ![]() ![]() |
![]() |
![]() ![]() ![]() ![]() |
![]() ![]() ![]() ![]() |
![]() ![]() ![]() ![]() |
![]() |
![]() ![]() ![]() ![]() |
![]() ![]() ![]() ![]() |
![]() ![]() ![]() |
Дополнительная информация
ПЗ.doc
1 Обоснование выбора материала изделия и его характеристика3
2 Анализ технологичности конструкции детали6
3 Обоснование метода и способа получения исходной заготовки6
Размерный анализ технологического процесса9
1 Анализ линейных размеров9
2.1 Совмещенная схема9
2.2 Уравнение размерных связей9
2.3 Неравенство допусков10
Назначение и расчет режимов обработки12
1 Расчет режимов резания на токарных операциях12
2 Расчет режимов резания на сверлильных операциях13
3 Расчет режимов резания на фрезерных операциях:14
Разработка технологических операций16
1 Выбор и обоснование механических операций оборудования режущих и мерительных инструментов16
1.1Выбор средств технологического оснащения17
1.2 Выбор режущего инструмента19
1.3 Выбор мерительного инструмента20
Разработка технологического процесса нанесения покрытия нитрид титана21
1 Назначение режимов ионно-плазменного осаждения покрытий21
2 Расчет режимов очистки поверхности детали в вакууме23
Список использованной литературы26
Маршрутная карта на механическую обработку.27
Технологический процесс напыления28
В данной работе разработан технологический процесс обработки детали «Стакан 046.60.0105». На начальной стадии разработки техпроцесса проектируется заготовка отвечающая требованиям данного вида производства. Размеры заготовки определяются предварительно по виду изготовления в данном случае поковка окончательные размеры определяются в процессе размерного анализа. Далее разрабатывается техпроцесс который должен обеспечивать выполнение всех требований чертежа: точность шероховатость. Для этого производится размерный анализ в результате которого выявляется соответствие результатов обработки конструкторским требованиям. Также в проекте производится анализ технологичности конструкции детали по качественным и количественным характеристикам.
Проектирование операции сложный процесс. Его варианты оценивают по производительности и себестоимости руководствуясь технико-экономическими показателями имея в виду максимальную экономию времени и высокую производительность.
Применение прогрессивных высокопроизводительных методов обработки обеспечивающих высокую точность и качество деталей методов упрочнения рабочих поверхностей повышающих ресурс работы деталей эффективное использование современных автоматических и поточных линий станков с ЧПУ электронных вычислительных машинах и другой новой техники – все это направлено на решение главных задач: повышение эффективности производства и качества продукции.
Для сохранения конкурентоспособности продукции необходимо постоянно совершенствовать разрабатывать и производить новые реконструировать цеха и заводы внедрять прогрессивные технологические процессы.
Анализ исходных данных
1 Обоснование выбора материала изделия и его характеристика
При современном уровне машиностроительного производства разработка конструкции изделий должна базироваться как на удовлетворении требований служебно-эксплуатационного характера так и производственных требований обусловленных возможностью применения высокопроизводительных и рентабельных технологических процессов с учетом конкретных условий и объема производства [10].
При проектировании конструкции особое значение имеет правильность выбора материала который определяет технологичность работоспособность стоимость изготовления и ремонта изделия.
В данном курсовом проекте деталь «стакан» изготовлена из титанового сплава ВТ5 используется в вертолетной технике. В таблице 1 представлен химический состав сплава ВТ5. Сплав ВТ5 отличается высокой технологичностью при обработке давлением из него изготавливают всевозможные виды полуфабрикатов.
Титановые сплавы имеют следующие преимущества по сравнению со сталями:
меньший удельный вес;
Плотность титановых сплавов составляет порядка 45 гсм3 в то время как плотность сталей примерно равна 78 гсм3.
коррозионная стойкость.
В среде влажного пара титановые сплавы не подвержены коррозии а следовательно и коррозионному растрескиванию которое является весьма опасным фактором разрушения высокая стойкость к капельной эрозии.
Физические свойства сплава ВТ-5 представлены в Таблице 2.
Марка сплава ВТ5 – это титановый деформируемый сплав ОСТ192020-72
Это сварные штампосварные детали и узлы работающие при температуре от -253 до 400 оС; коррозионная стойкость хорошая; класс по структуре .
без ограничений - сварка производится без подогрева и без последующей термообработки;
ограниченно свариваемая - сварка возможна при подогреве до 100-120 град. и последующей термообработке;
трудносвариваемая - для получения качественных сварных соединений требуются дополнительные операции: подогрев до 200-300 град. при сварке термообработка после сварки – отжиг.
Химический состав в % материала ВТ5
Физические свойства материала ВТ5
Твердость материала НВ =
По фазовому составу сплав ВТ5 относится к (a+b)-сплавам мартенситного типа. В связи с небольшим количеством b-фазы (коэффициент Кb=031) он примыкает к псевдоa-сплавам. После закалки в структуре сплава ВТ5-1 образуется мартенсит (α'-фаза). [9]
Прочность листов в отожженном состоянии sв³885 МПа относительное удлинение d³8%. В термоупрочненном состоянии прочность может достигать sв=1100 МПа [ГОСТ 22176-76]. Твердость HB 2534.
Рабочая температура деталей из ВТ5 от –196 до +450°С; в термоупрочненном состоянии до 400°С.
Сплав может применяться как в отожженном так и в закаленном и состаренном состояниях. Упрочняющей термической обработкой его предел прочности может быть увеличен на 2030 % по сравнению с отожженным состоянием. В связи с невысокой прокаливаемостью сплава детали предназначенные для упрочняющей термической обработки должны быть сечением не более 3040 мм. Сплав хорошо деформируется в горячем состоянии: куется штампуется прокатывается и т. п. Он удовлетворительно обрабатывается резанием. Обработку резанием можно производить как в отожженном так и термически упрочненном состоянии.
Сплав обладает высокой коррозионной стойкостью в отожженном и термически упрочненном состояниях во влажной атмосфере а также в некоторых других агрессивных средах как и технический титан.
Газонасыщение поверхности титанового сплава ВТ5. Изменение микротвердости от поверхности вглубь изделия в зависимости от температуры и времени выдержки представлено на рис 1. Микротвердость снижается от поверхности внутрь образца при всех режимах газонасыщения.
Рис. 1 Зависимость микротвердости титанового сплава ВТ5 от расстояния до поверхности после нагрева на воздухе в течение 1(а) 3 (б) и 6 (в) ч при 750 (1) 950 (2) 1050 (3) 1200°С (4).
Нагрев сплава ВТ5 при сравнительно невысоких температурах 7508000С в течение 1ч приводит к повышению поверхностной микротвердости от HV 300 до HV 400. Увеличение температуры и времени выдержки значительно интенсифицирует процесс газонасыщения вследствие увеличения скорости диффузии в результате поверхностная микротвердость сильно повышается (рис.1). Так увеличение времени выдержки от 1 до 6ч приводит при различных температурах к увеличению поверхностной микротвердости на HV 100200.
При повышении температуры и увеличении времени выдержки увеличивается глубина газонасыщенного слоя (рис.1). Газонасыщенный слой формируется практически при выдержке в течение 1ч а дальнейшее увеличение продолжительности газонасыщения мало влияет на глубину поверхностного газонасыщенного слоя.
Важнейшей с точки зрения аварийной безопасности характеристикой материала является трещиностойкость которая определяет живучесть рабочих лопаток. Высокая трещиностойкость материала повышает вероятность того что появившаяся в процессе эксплуатации трещина будет обнаружена либо с помощью систем диагностики в процессе работы либо при плановом осмотре паровой турбины. В случае низкой трещиностойкости материала любая трещина может привести к обрыву рабочей лопатки и соответственно аварии.
При изготовлении рабочих лопаток паровых турбин заготовки (прутки) подвергают горячей штамповке. Штампованные поковки лопаток подвергаются термической обработке для обеспечения требуемого уровня свойств контроля механических свойств при нормальной и повышенной температурах контроля макро- и микроструктуры по ОСТ 190002-86.
Нитрид титана разрабатывался как защитное покрытие для особо важных деталей военной техники от коррозии но вместе с тем титан в соединении с азотом приобретает золотистый цвет. Этим воспользовались производители и методом вакуумного напыления стали наносить это покрытие на различные предметы.
Нитрид титана помимо золотистого цвета имеет уникальные качества. Он упрочняет поверхность на которую наносится защищает от коррозии не разрушается на изгибах и поддается вытяжке (выколотке) в формах так как покрытие происходит в глубоком вакууме в плазме т.е. в момент нанесения покрытия ионы нитрида титана бомбардируют поверхность и внедряются в кристаллическую решетку т.е. намертво входят в поверхность.
2 Анализ технологичности конструкции детали
Оценка технологичности конструкции детали может быть качественной и количественной. При качественной оценке технологичность носит описательный характер без использования численных значений показателей. Количественная оценка сопровождается расчетом ряда коэффициентов имеющих численное значение [10].
Качественная оценка технологичности
Единым критерием технологичности конструкции изделия является ее экономическая целесообразность при заданном качестве и принятых условиях производства эксплуатации и ремонта. Отработка конструкции изделии на технологичность должна обеспечивать снижение трудоемкости и себестоимости изготовления изделия и снижения трудоемкости цикла и стоимости работ по обслуживанию изделия при эксплуатации [10].
В основном поверхности детали имеют простую форму (цилиндрическую или
плоскую) поэтому технологичны но существуют трудность при обработке получение шероховатости на некоторых поверхностях детали Ra0.8 и Ra1.6также допуски отклонения поверхностей 0.02 0.03 и ХТО операции.
Учитывая все сказанное выше можно сделать вывод что деталь не является технологичной.
Количественная оценка технологичности
Технологичность конструкции изделия оценивают количественно посредством системы показателей которые характеризуют технологическую рациональность конструктивных решений и преемственность конструкции или пригодность к использованию в составе других изделий.
Количественная оценка технологичности производится на основе анализа значений показателей технологичности изделия.
В качестве количественных показателей рассматриваются коэффициенты использования материала точности шероховатости.
3 Обоснование метода и способа получения исходной заготовки
При выборе заготовок учитывают форму размеры и массы детали материал (назначаемый исходя из эксплуатационных условий) масштаб производства периодичность повторения размеры припусков на обработку и точность размеров.
Материал заготовок обычно задается на рабочем чертеже конструктором. Вид заготовки форму и размеры определяют исходя из условий наибольшей простоты и экономичности обработки с учетом конкретных производственных возможностей заготовительных цехов и сроков окупаемости капитальных затрат на подготовку производства [1].
Правильное решение в выборе заготовок если по техническим условиям применимы различные их виды можно получить только на основе технико-экономических расчетов путем составления технологической себестоимости детали при том или другом виде заготовки. Однако при выборе заготовок можно руководствоваться некоторыми общими соображениями.
Заготовки в виде поковок получаемых ковкой и штамповок изготовляемых в штампах применяют для деталей работающих преимущественно на изгиб растяжение и кручение при значительной разнице в поперечных сечениях.
С точки зрения экономии материала снижения объема механической обработки целесообразно заготовку приближать по формам размерам и качеством материала поверхностного слоя к параметра готовой детали. Но при этом будут существенно возрастать затраты а получение заготовки в заготовительных цехах.
С другой стороны упрощение формы заготовки снижение требований к его точности качеству поверхностного слоя ведет к удешевлению заготовительного производства при одновременном увеличении затрат на механическую обработку и одновременно с этим коэффициента использования материала. Поэтому при проектировании технологического процесса и выбора варианта исходной заготовки рекомендуется рассматривать несколько вариантов и выбрать тот который позволит получить минимальную сумму технологических затрат по заготовительным и механообрабатывающим цехам.
Так как деталь имеет сложную форму то заготовку можно получить одним из двух методов: поковка или штамповка. Но учитывая условия эксплуатации детали а также материал детали мы принимаем в качестве метода получения заготовки - штамповку на горизонтально-ковочных машинах (ГКМ) которую выполняют в штампах с двумя плоскостями разъема: одна - перпендикулярна оси заготовки между матрицей и пуансоном вторая - вдоль оси разделяет матрицу на неподвижную половины.
Положительный эффект заключается в том что достигается экономия материала макроструктура поковки получается благоприятной и обеспечивает высокое качество детали работа на ГКМ легко автоматизируется. Проведем предварительный расчет размера заготовки.
Технологические требования предъявляемые к заготовкам обусловлены необходимостью соблюдать технические условия определяющая припуски классы шероховатости поверхностей твердость и обрабатываемость.
В соответствии с ГОСТ 7606-89 выбираем степень сложности поковки: С4. Далее выбираем группу стали в зависимости от содержания легирующих элементов: M3. В зависимости от точности изготовления выбираем класс (нормальная точность) Т3 по этим критериям назначаем исходный индекс. Припуски на сторону на механическую обработку поковок назначаем с исходного индекса 12 .
Основным показателем характеризующим экономичность выбранного метода изготовления заготовок наряду с приведенными выше соображениями является коэффициент использования материала [6]:
Мд – масса детали (изделия)
Мз – масса материала израсходованного на изготовление составной части изделия.
где - плотность материала
Объем заготовки рассчитываем по формуле:
Определяем Мд = 028 кг
Мз =25133×10-6 ×4400=1106 кг
Заготовка предоставленная в базовом технологическом процессе более технологична чем штамповка. Окончательный вариант заготовки представлен на чертеже (Приложение).
Размерный анализ технологического процесса
1 Анализ линейных размеров
Качество изготовления и сборки деталей обеспечивается в частности простановкой размеров на рабочих и сборочных чертежах. В большинстве случаев отдельные размеры отнесенные к одной или группе деталей находятся во взаимосвязи друг с другом; изменение одного из размеров этой взаимосвязанной группы влияет на один или несколько других размеров [2].
В комплексе задач проектирования технологического процесса важное место занимает расчет и обоснование значений геометрических параметров заготовки изменяющееся в процессе обработки от операции к операции. Исходная заготовка поступающая на первую операцию по своим размерам существенно отличается от размеров готовой детали.
Исходными данными для расчета размеров исходной заготовки является план технологического процесса или его часть чертеж или эскиз готовой детали со всеми необходимыми условиями эскиз исходной заготовки.
Математическая модель геометрических параметров технологического процесса изготовления детали представляет собой сложный комплекс взаимосвязанных размеров допусков и отклонений различных категорий изменяющихся на протяжении всего технологического процесса.
Размерный анализ является единственным методом расчета технологических размеров и допусков расположения поверхностей гарантирующим получение чертежных размеров и допусков а также снятие минимально необходимых припусков.
Основной посылкой является утверждение о том что все чертежные размеры и допуски расположения поверхностей непосредственно не выдерживаются но являются результатом выдерживания технологических размеров и допусков расположения [8].
Для определения геометрических параметров обрабатываемой заготовки вначале определяются размеры длин выдерживаемые в операциях технологического процесса. Для этого выявляют взаимосвязь указанных размеров путем построения графа с помощью совмещенной схемы обработки заготовки в виде комплексного эскиза содержащего все операционные размеры длин по технологическому процессу (Lon) чертежные размеры данной категории а также размеры припусков на обработку (zon). Прежде чем строить граф размеров необходимо убедиться в том что количество исходных ребер (размеров) равняется количеству производных. Так как исходное ребро является замыкающим (исходным) звеном размерной цепи путь заданный этим ребром окажется замкнутым поэтому сумма звеньев размерной цепи будет равна нулю. На этом основании по задаче составлены следующие уравнения [9].
2.1 Совмещенная схема
Совмещенная схема приведена в Приложении п. 3
2.2 Уравнение размерных связей
)(24)+l5-l4-l10-l11=0
)(265)+l11+l10+l4-l5+l2=0
)Z50”-l3-l4-l10-l11=0
2.3 Неравенство допусков
)T(24)Tl5+Tl4+Tl10+Tl11
)T(265)Tl11+Tl10+Tl4-Tl5+Tl2
)Z50”Tl3+Tl4+Tl10+Tl11
l9=- l8+(275)=275-021-25+008=25-013
l2=505-01-20+02=485-01
l7=11+009-25+008-15+024=702+007
l10=25-013-215+004-05+021=3-004
l5=(36)+ l4+ l2=36+02+215+004-485-01=9+034 928+006
l11=(24)+ l5- l4+ l10=24+019+928+006-215+004+3-004=1507-004
l3= l4- l10+ l11+ Z50”
l3=215+004-1507-004+3-004+05+024=1036-011
Назначение и расчет режимов обработки
1 Расчет режимов резания на токарных операциях
Определяется глубина резания с учетом величины припуска;
По действующему технологическому процессу назначаем подачу;
Назначаем период стойкости инструмента;
Определяем скорость резания V (ммин) по [3];
где СV - коэффициент зависящий от вида обрабатываемого материала;
Т- период стойкости инструмента;
t- глубина резания мм;
KV- коэффициент учитывающий влияние материала заготовки
По результатам расчёта скорости резания V (ммин) вычислена частота вращения шпинделя:
где D - диаметр обрабатываемой поверхности;
Найденная величина частоты вращения округляется до значения кратного пяти.
Расчет режимов резания осуществляем по операциям:
Оп10 выполняется на автоматическом токарном винторезном станке модели 16К20.
Материал режущей части резца Т14К8.
По справочнику определяем подачу и материал режущей части:
Материал режущей части Т15К6
Частота вращения шпинделя
Найденную величину частоты вращения округляем до значения кратного пяти из стандартного ряда для данного станка:
2 Расчет режимов резания на сверлильных операциях
Выбор маршрута обработки производят в зависимости от требований предъявляемых к готовому отверстию по точности размера и шероховатости поверхности с учетом конструктивных особенностей и заданного диаметра отверстия [4].
Определяется максимальная глубина резания при сверлении в зависимости от диаметра обрабатываемого отверстия и выполняемого перехода. При сверлении глубину резания принимают равной половине диаметра сверла. t = 0.5D
при рассверливании зенкеровании и развертывании t = 0.5 (D - d)
По действующему технологическому процессу назначаем подачу. В зависимости от отношения глубины сверления к диаметру и с учетом других условий обработки устанавливают следующие подачи:
) для глухих отверстий используют подачи соответствующие ;
) для деталей с пониженной жесткостью
) при сверлении с выходом в каналы с наклонной осью или других аналогичных
Определяем скорость резания при сверлении V (ммин) по [4];
При рассверливании зенкеровании развертывании
где СV - коэффициент зависящий от вида обрабатываемого материала
KV- коэффициент учитывающий влияние материала заготовки
ОП 25 сверлильная операция
Инструмент – зенкер диаметром 65 мм
Определяем глубину сверления
По справочнику определяем подачу и материал режущей части ВК6
СV = 70; y = 07 q = 04 m = 02 х = 015
Скорость резания при зенкеровании
СV = 180; y = 03 q = 06 m = 025
Скорость резания при сверлении
3 Расчет режимов резания на фрезерных операциях:
Определяется глубина резания при фрезеровании t
Sм = S* n = Sz * Z * n
где n – частота вращения фрезы об мин; z - число зубьев;
Определяем скорость резания при сверлении V (ммин) по [5];
По результатам расчета скорости резания V (ммин) вычислена частота вращения шпинделя:
Сила резания рассчитывается по формуле:
Определяем глубину резания t =5 мм
По справочнику определяем подачу и материал режущей части Т15К6:
СV=324; y=05; q=02; х = 011; u =02 ; p =0; m = 02
где Кmp=1– поправочный коэффициент;
Разработка технологических операций
1 Выбор и обоснование механических операций оборудования режущих и мерительных инструментов
Маршрутная технология разрабатывается в соответствии с заданными на чертеже параметрами шероховатости и точности. Разрабатываемый технологический процесс должен обеспечить быструю подготовку производства по выпуску изделия с самыми минимальными трудовыми и материальными затратами [10].
Все операции технологического процесса взаимосвязаны. Поэтому задачи решаемые в масштабе всего технологического процесса так и в отдельных операциях являются комплексными и взаимосвязанными. Однако без предварительной разбивки всего объема механической обработки на отдельные операции невозможно решить весь комплекс задач. Т.е. предварительно на начальном этапе проектирования технологического процесса необходимо наметить границы операций. Поэтому разработка технологического процесса выполняется в 2 стадии:
составление плана технологического процесса;
разработка операций технологического процесса.
Для серийного производства технологический процесс разрабатывается по принципу группового метода обработки деталей дающего возможность эффективно применять на универсальном оборудовании специализированную высокопроизводительную технологическую оснастку. Применение станков с ЧПУ позволяет увеличить производительность труда сократить сроки подготовки производства снизить себестоимость изготовления деталей а также использовать труд более низкой квалификации.
Маршрутная технология содержит краткое описание всех необходимых операций. Технологический процесс содержит черновые чистовые и окончательные операции. Так как деталь а следовательно и заготовка представляют собой тело вращения то основными операциями являются токарные. Предусмотрены черновые получистовые и чистовые токарные операции. Кроме механических операций в маршрутной технологии предусмотрены напыление нитрид титаном контрольные слесарные операции.
При построении технологического процесса руководствуются следующими правилами регламентированными в ГОСТ 14301-83 [1]:
В первую очередь следует обрабатывать поверхность которая будет служить технологической базой для последующих операций; каждая последующая операция должна уменьшать погрешность и улучшать качество поверхности.
Отделочные операции производить в самом конце технологического процесса т. к. при этом уменьшается опасность повреждения чисто обработанных поверхностей;
Обработку поверхностей с точным взаимным расположением следует по возможности включать в одну операцию и выполнять за одно закрепление заготовки;
Обработку ступенчатых поверхностей выполнять в такой последовательности при которой общая длина рабочих движений инструмента будет наименьшей;
Если деталь подвергается термической обработке то механическую обработку разделяют на две части: до термической обработки и после неё;
При определении последовательности переходов предусматривать опережающее выполнение тех которые подготавливают возможность осуществления следующих за ними переходов.
При формировании каждой операции используется принцип концентрации операции. Каждая операция строится в соответствии с требованиями чертежа.
В начале технологического процесса черновые токарные операции на которых подрезаются торцы и снимается грубая поверхность штамповки тем самым предупреждая базовые поверхности на чистовые операции.
На специальном сверлильном приспособлении просверливаться отверстия.
После идет напыление – покрытие нитрид титаном для повышения износостойкости.
Конечная это механическая операция контроль.
1.1Выбор средств технологического оснащения
В машиностроении широко применяется разнообразная технологическая оснастка под которой принято понимать приспособления вспомогательный режущий и мерительный инструмент.
От правильности выбора технологического оборудования зависит производительность изготовления деталей экономичное использование производственных площадей механизации и автоматизации ручного труда электроэнергии себестоимости изделия.
Выбор станочного оборудования производился по следующим показателям:
а) соответствие рабочей зоны станка габаритам обрабатываемой детали
б)соответствие мощности привода главного движения свойствам обрабатываемого материала
в)снижение основного времени за счёт применения станков с бесступенчатым изменением частоты вращения шпинделя
г) снижение вспомогательного времени за счёт применения станков с числовым программным управлением позволяющих автоматизировать часть вспомогательных переходов;
д) характер производства;
При выборе оборудования руководствуемся типом производства габаритами заготовки требуемой точностью и производительностью. Так как при формировании структуры операций использовался принцип концентрации то эти операции рационально выполнять на станках с ЧПУ. Большая часть токарных операций выполняется на станке модели 16К20 [3]:
максимальный диаметр обрабатываемого изделия: 400 мм;
мощность привода главного движения: до 10 кВт;
пределы частот вращения шпинделя: до 2000 обмин;
поперечное перемещение: 250 мм;
продольное перемещение: 900 мм;
количество позиций в револьверной головке: 8
пределы подач: по оси координат х – 005 2800
по оси координат y – 01 5600 мммин
мощность привода движения – 11 кВт
Фрезерная операция 400035 на фрезерном станке 6М13СН2 [4]:
размеры рабочей поверхности стола: 1250×4000 мм
подача мммин: по координате X 2-10000
по координате Y 1-10000
по координате Z 1-10000
подача стола:4700 мм;
мощность электродвигателя шпиндельной бабки кВт: 40;
Сверлильная операция 40025 выполняется на СС49Е [5]:
размеры рабочей поверхности стола: 450×500 мм
Габаритные размеры: длина 1030
В качестве приспособлений для токарных операций используют трехкулачковые самоцентрирующие патроны с механизированным приводом используют внутреннюю цангу для предотвращения в тонкостенной детали коробления. На фрезерно-сверлильной применяется специальное контурное приспособление с ручным зажимом который можно механизировать для уменьшения времени на установку и снятие заготовки.
Выбор приспособления для вакуумно-плазменной обработки зависит от: конфигурации габаритных размеров и массы детали. Приспособление должно обеспечивать надежное пространственное расположение обрабатываемой поверхности относительно потока плазмы. При этом оно не должно экранировать поверхность обработки и вносить изменения в химический состав покрытия при нанесении покрытия. Технологические экраны должны обеспечивать надежное экранирование защищаемой поверхности и также не ухудшать химический состав покрытия.
Конструкция вакуумных приспособлений во многом определяется свойствами используемых материалов. В дополнение к обычным требованиям прочности технологичности легкости и т.д. вакуумная техника выдвигает к конструкционным материалам ряд специфических требований: 1) упругость паров материала при рабочей температуре должна быть значительно ниже рабочего давления; 2) газовыделение материала при рабочем давлении и температуре должно быть минимальным; 3) газопроницаемость материала в рабочих условиях должна быть минимальной; 4) вакуумная герметичность при малых толщинах; 5) коррозионная стойкость; 6) отсутствие ползучести вплоть до температур Т=500-600°С; 7) немагнитность.
Если упругость паров материалов при рабочей температуре больше или равно рабочему давлению то это приводит к интенсивному распылению указанного материала и нежелательному образованию напыленных слоев на поверхности различных деталей например изоляторах электрических вводов.
Газовыделение материалов при рабочем давлении и температуре определяется наличием в объеме материала растворных газов а на поверхности – адсорбированных. Для удаления газов растворенных в металлах применяют их переплав под вакуумом. Поверхности вакуумных материалов должны быть тщательно очищены от загрязнений являющихся дополнительным источником газовыделения.
Для улучшения условий очистки внутренние поверхности элементов вакуумных систем желательно обрабатывать до шероховатости RZ=5 10 мкм для высоковакуумных и 05 3 мкм для сверхвысоковакуумных систем. Газовыделение конструкционных вакуумных материалов зависит от способа предварительной обработки. Эффективным способом уменьшения газовыделения является высокотемпературное вакуумное обезгаживание уменьшающее концентрацию газов растворенных в объеме материала. Уменьшение газовыделения водорода из нержавеющей стали можно добиться созданием оксидных пленок или нанесением покрытия из алюминия серебра меди и т.д. Наличие поверхностной пленки затрудняет переход растворенных атомов из кристаллической решетки на поверхность что при неизменной концентрации растворенных газов значительно снижает газовыделение.
Газопроницаемость материала в рабочих условиях свойственна многим материалам но в некоторых случаях она особенно велика. Так железо пропускает водород; стекло – гелий и водород; резина – гелий водород и азот.
Вакуумные материалы при малых толщинах должны быть герметичны. Литые материалы чаще всего не удовлетворяют этим требованиям так как обладают пористой структурой. Листовой и сортовой прокат имеет неодинаковые вакуумные плотности в различных направлениях. Шлаковые включения образуют волокна в направлении деформации материала при его обработке. Негерметичность таких волокон часто можно обнаружить только после прогрева в вакууме. Ремонт деталей в которых обнаружены такие течи практически невозможен так как припой не смачивает шлаковые включения а при разогреве во время сварки из них выделяются газы образующие поры. При проектировании тонкостенных деталей нужно следить за тем чтобы шлаковые волокна не были направлены поперек стенки например при проектировании днищ нежелательна замена листового проката сортовым. Наилучшей вакуумной плотностью обладают металлы подвергнутые вакуумному переплаву.
Коррозионная стойкость необходима вакуумным материалам в связи с тем что коррозия увеличивает газовыделение материалов уменьшает прочность тонкостенных деталей сопровождается появлением натеканий [7].
Требования к коррозионной стойкости материалов особенно велики при создании сверхвысоковакуумных установок которые должны регулярно прогреваться при температуре Т=400 500°С. Медь например при такой температуре в воздушной среде настолько быстро корродирует что ее нельзя применять в качестве материала для изготовления часто прогреваемых деталей соприкасающихся с атмосферой.
Нагруженные детали прогреваемых вакуумных установок не должны обладать заметной ползучестью вплоть до максимальных рабочих температур Т=500 600°С. Ползучесть материалов из которых изготовлены детали разборных фланцевых соединений приводит к их разгерметизации после определенного числа циклов прогрева вакуумных установок.
Немагнитность является специфическим требованием отдельных деталей вакуумных систем через которые осуществляется ввод магнитного потока в вакуумную камеру. Такие детали обязательно имеются в конструкциях магнитных вводов движения в вакуум магниторазрядных насосах и манометрических преобразователях [9].
В вакуумной технике широко применяются такие конструкционные материалы как чугун сталь медь тугоплавкие металлы специальные сплавы стекло керамика пластмассы резина масла замазки клей и т.д.
1.2 Выбор режущего инструмента
Выбирая режущий инструмент ориентируемся прежде всего на заводские нормали и ГОСТы. В необходимых случаях предусматривается специальный инструмент. При выборе режущего инструмента учитывается возможность его закрепления на выбранном оборудовании с достаточной жесткостью и точностью. На основе данных о детали и присоединительных поверхностях стандартного режущего инструмента выбирается вспомогательный инструмент. Для полного использования режущих свойств инструментов марку материала инструмента подбираем в соответствии со свойствами обрабатываемого материала. Инструментальные материалы должны обладать следующими необходимыми свойствами:
высокая твердость (твердость инструмента должна превышать твердость детали в 15 - 3 раза);
высокая износостойкость;
высокая термопроводность.
При выборе режущего инструмента учитываем вид обработки материал детали необходимую производительность и современные инструментальные материалы.
Для токарной обработки применяем токарные проходные резцы c с сечением державки 25х25мм. Толщина пластины – 64мм. Принимаем трехгранную форму пластины с углом при вершине 60о из твердого сплава Т14К8 для операций ГОСТ 18878-73. Также для токарной обработки применяются резцы с наименьшей технологически возможной длиной и наибольшим технологически допустимым сечением. Пластины из твердого сплава ВК6 [3].
Во фрезерной операции применяется концевая фреза 2530 с коническим хвостовиком ГОСТ 17026-71 из материала Т15К6 [4].
В сверлильной операции применяется сверла спиральные из быстрорежущей стали с коническим хвостовиком форма заточки инструмента нормальная для станков с ЧПУ ОСТ2 И20-2-80. материал режущей части ВК6 [5].
1.3 Выбор мерительного инструмента
В общем случае выбор мерительного инструмента как правило зависит от типа производства сложности конфигурации и габаритов детали (доступности к замеряемому размеру) а также от точности контролируемого размера. Поскольку изготовление данной детали проводится в серийном производстве то при выборе мерительного инструмента следует отдавать предпочтение специальным мерительным инструментам таким как скобы шаблоны калибры и др. которые обеспечивают достаточную точность быстроту и удобство измерений. Точность мерительного инструмента как правило в 5-10 раз выше допуска контролируемого размера. Обычно для контроля размеров с допуском до 001мм и свободным доступом к нему используют стандартный мерительный инструмент. Для контроля небольших линейных размеров с допуском не точнее 001 мм вполне достаточно использование штангенциркулей для более точных - специальные такие как скобы уступомеры глубиномеры индикаторные и др. Для контроля точных диаметральных размеров - калибры гладкие скобы. Для контроля точности изготовления углов радиусов фасок и др. - шаблоны. Часто контроль затруднен при непосредственном измерении поэтому приходится проектировать специальные мерительные приспособления - контрольные стапели или производить косвенный контроль при помощи синусных и тангенциальных линеек с последующим пересчетом полученных данных.
На токарных операций для замера наружных и внутренних диаметров и обхватываемых поверхностей применяются штангенциркули и штангенглубиномеры микрометр ГОСТ 6507-90 [1].
Разработка технологического процесса нанесения покрытия нитрид титана
Наименование операции
Промывка и обезжиривание
Предварительный нагрев
1 Назначение режимов ионно-плазменного осаждения покрытий
Назначение режимов ионно-плазменного осаждения покрытий выполняется в зависимости от требования чертежа детали в следующей последовательности:
назначают параметры режима обеспечивающие заданные физико-химические свойства покрытий;
задают расположение детали и размеры обрабатываемой зоны обеспечивающие заданную точность;
при выполнении первых заданных условий выбирают режимы с максимальной производительностью.
Установка ННВ 66-И1 предназначена для нанесения упрочняющих одно- многослойных покрытий на детали диаметром до 200мм и длиной до 250мм преимущественно форму тел вращения [11].
Сложность назначения расчета режимов обработки обусловлена тем что совместное действие управляющих факторов приводит к большому разбросу параметров покрытий.
Задаваясь технологическими режимами напыления можно рассчитать плотность ионного тока в произвольной точке вакуумной камеры по формуле:
Где - коэффициент эрозии катода;
- масса конденсирующего иона кг;
- расстояние от торца катода до поверхности обработки;
- расстояние от оси потока до поверхности обработки;
- средний заряд ионов.
Плотность ионного тока на оси катода находится простым соотношением:
Скорость роста покрытия находится из соотношения:
где - удельная масса конденсирующего вещества;
- коэффициент конденсации;
- коэффициент распыления.
Температура подложки находится из соотношения:
где - постоянная Стефана-Больцмана;
- интегральный коэффициент излучения подложки;
- потенциал подложки;
- средний коэффициент ионизации;
- энергия выделяющаяся при конденсации одного иона;
- температура среды.
Найдем скорость конденсации покрытия ТNi на поверхности расположенной на оси катода параллельно плоскости катода на расстоянии l=250 мм. Радиус катода Rк = 100 мм.
Режим напыления: Iр= 200 А; Uп= 150 В; Р = 5 · 10-3 Па [11].
При ускоряющем напряжении на подложке Uп= 150 В можно пренебречь распылением подложки и считать что коэффициент конденсации aк=1. Тогда из соотношения получим:
- удельная масса конденсирующего вещества
Подставив исходные данные р = 42 · 10-9 кгКл r = 79 · 103 кгм3
Найдем плотность тока по соотношению подставив исходные данные значения:
Z=144 m = 8632*10кг е = 16*10Кл получим:
Подставив исходные данные Тс = 300 К; Uп = 150 В; Qk = 6.47*10Дж ;
W =122*10Дж; U = 57*10Втм; = 07 получим:
Температура нагрева на первой операции термообработки составляет 540оС.
2 Расчет режимов очистки поверхности детали в вакууме
Состояние поверхности перед нанесением покрытий определяет качество конденсированного слоя и многие функциональные характеристики покрытий.
Необходимо обеспечить доступ атомов осаждаемого металла к поверхности подложки для чего необходимо удалить пленку загрязнений адсорбированные пленки а также активировать поверхность [9].
Для обеспечения качественной подготовки поверхности подложки перед металлизацией применяют тонкую химическую очистку в растворах неорганических кислот и щелочах а также в парах органических растворителей. Для интенсификации процесса очистки используют ультразвуковые ванны процесс очистки ведут как правило при повышенной температуре раствора.
После помещения в вакуумную камеру детали подвергаются финишной очистке путем ионной бомбардировки поверхности. При этом с поверхности удаляются оставшиеся после предварительной обработки тонкие пленки загрязнений оксидные пленки и адсорбированные поверхностью газы которые невозможно удалить обычными методами. В результате ионного травления обнажается и активируется поверхностная структура материала обрабатываемой детали что создает условия получения высокой адгезии материала покрытия к материалу детали. Однако важно учитывать температуру при которой происходит очистка потоком ионов. Она не должна превышать температуру последней термической обработки.
При разработке технологии ионной очистки необходимо учитывать следующее:
- процесс распыления начинается с преимущественного распыления одного из компонентов что приводит к изменению состава поверхности по сравнению с составом материала;
- при достижении равновесных условий состав поверхности и толщины слоя нарушенного состава не изменяется.
На поверхности любого материала существует оксидная пленка толщиной h. Для ее удаления необходимо время:
где n =287·1030 – текущее количество атомов адсорбированных на поверхности;
h =05 мкм – толщина оксидной пленки;
sp – коэффициент распыления.
При этом в результате бомбардировки потоком ионов с плотностью ji на поверхности протекают следующие процессы: адсорбция (ja) распыление (jp) и диффузия (jd) атомов поверхности. Тогда процесс эффективной очистки будет достигаться при условии: .
Тогда баланс частиц с течением времени будет:
где nс – максимальное количество атомов адсорбированных на поверхности;
αс – вероятность протекания процесса.
Так как ja и ji постоянные величины для данного режима jd убывающая функция то коэффициент распыления можно представить в виде:
где α – коэффициент зависящий от соотношения масс падающего иона и атома мишени. Обычно α бывает в пределах от 02 до 03;
Основной задачей при разработке технологического процесса упрочнения является определение оптимальных условий (чистота исходных материалов режимы упрочнения и так далее) обеспечивающих получение поверхностных слоев с требуемыми функциональными характеристиками и достаточной эксплуатационной надежностью.
Совершенствование технологического процесса изготовления детали должно одновременно решать две важнейшие задачи: повышение экономических показателей процесса и повышение эксплуатационных свойств. Основой совершенствования технологических процессов является применение таких режимов и условий обработки которые обеспечивают получение необходимого качества поверхностного слоя включая упрочнение методом вакуумной ионно-плазменной обработкой.
Любой технологический процесс начинается и заканчивается контрольной операцией чтобы проверить комплектность детали и соответствие техническим документам.
Выполнять сборочные операции работники должны в хб перчатках не допуская механических повреждений.
Работоспособность деталей в значительной степени зависит от состояния их поверхностного слоя перед ионно-плазменной обработкой поэтому следует рассмотреть влияние основных параметров поверхностного слой детали на качество наносимых покрытий и технологию подготовки поверхности под покрытие [].
Химическая чистота поверхности детали — одно из основных условий высокого качества производимой вакуумной ионно-плазменной обработкой. Загрязненность поверхности детали затрудняет взаимодействие покрытия с материалом подложки способствует возникновению несплошностей в покрытии и областей с высокими локальными напряжениями. Все это снижает прочность сцепления покрытия с подложкой и как следствие приводит к отслаиванию и растрескиванию покрытия (в процессе его нанесения).
После закрепления детали рабочая камера герметизуется и в ней создается вакуум. Физические методы подготовки поверхности включают воздействие на нее низкоэнергетических частиц (ионов электронов фотонов) а также тепловое воздействие (например вакуумный отжиг при котором выгорают жидкие органические загрязнения происходит дегазация металла).
Список использованной литературы
Анурьев В.И. Справочник конструктора- машиностроителя. В 3-х т. Т. 2.-5-е изд.перераб. и доп.-М: Машиностроение 1979. -559 с ил.
Допуски и посадки: Справочник. В 2-х ч. В.Д. Мягков М.А. Палей А.Б. Романов В.А. Брагинский.- 6-е изд. перераб. и доп.-Л. Машиностроение. Ленингр. Отд-ние 1983.-Ч.2 448 с ил.
Общемашиностроительные нормативы времени и режимов резания для нормирования работ выполняемых на универсальных и многоцелевых станках с числовым программным управлением. 41: Нормативы режимов резания. -М: Экономика 1990-208с.
Общемашиностроительные нормативы времени вспомогательного на обслуживание рабочего места и подготовительно-заключительного для технического нормирования станочных работ. -М: Машиностроение 1967-396с.
Общемашиностроительные нормативы времени и режимов резания для нормирования работ выполняемых на универсальных и многоцелевых станках с числовым программным управлением. 42: Нормативы режимов резания. -М: Экономика 1990- 474 с.
Справочник технолога-машиностроителя. В 2-х т.Т.2 Под редакцией А.Г. Косиловой и Р.К. Мещерякова.-4-е изд.перераб. И доп.-М: Машиностроение 1985 496 с.;ил.
Справочник технолога-машиностроителя. В 2-х т. Т.1 Под редакцией А.Г. Косиловой и Р.К. Мещерякова.-4-е изд.перераб. И доп.-М: Машиностроение 1986 656 с.;ил.
Технологические размерные цепи. Теория и расчет: Учеб. пособие Э.Г.Рахимов: УГАТУ. Уфа 1993 88 с
Рахимов Э.Р. Методические указания по разработке технологии изготовления деталей. - УфаУАИ1980 г
Данилевский В.В. Технология машиностроения. Изд. 4-е перераб. и доп. М. «Высшая школа» 1977
ПАСПОРТ на установку ННВ-6.6
Маршрутная карта на механическую обработку.
Технологический процесс напыления
Напыление3.frw

кнопки "Пуск" на пульте ВСВУ-630
Произвести ионную очистку
- включить кнопку "высокое" и на высоковольтном
Технологический режим
Уменьшить высокое напряжение
Подать в камеру натекателем газ - азот до давления
- тумблером вывести высокое напряжение;
- произвести ионную очистку;
Произвести напыление покрытия
МК3.frw

Обозначение документа
СМ Проф. Р УТ КР КОИД ЕН ОП Кшт Тпз Тшт
наименование оборудования
км Наименование детали
сб. единицы или материала Обозначение
код ОПП ЕВ ЕН КИ Н.расх.
Промывка2.frw

Упаковать деталь в полиэтиленовый пакет
с покрытыми деталями разрешается работать только
в хирургических перчатках
Техника безопасности труда с 1 по 5 переходы согласно требований ГОСТ 12.3.008-75
Технологический режим
Перчатки хирургические
Т С - 150 С. Сушить 1 час
фторопластовая под утюг
Утюг бытовой с терморег.
УТА-1000 ГОСТ 307-75
МК1.frw

наименование операции
Обозначение документа
СМ Проф. Р УТ КР КОИД ЕН ОП Кшт Тпз Тшт
наименование оборудования
Заготовка-поковка цеха
МК2.frw

Обозначение документа
СМ Проф. Р УТ КР КОИД ЕН ОП Кшт Тпз Тшт
наименование оборудования
км Наименование детали
сб. единицы или материала Обозначение
код ОПП ЕВ ЕН КИ Н.расх.
Напыление4.frw

Произвести охлаждение деталей до температуры
время напыления определяется необходимой толщиной
указанной в паспорте детали
Запиать в журнал № партии
Технологический режим
Напустить воздух в камеру
положить в специальную тару"
Напыление5.frw

Перед первым циклом необходимо обезгазить оснастку и экраны
выдерживая в камере при вакууме 133*10
предварительно проведя ионную очистку и нагрев в течении 5 и более минут (без детали)
В одном цикле разрешается напылять деталь только с требуемой
одинаковой толщиной покрытия
Технологический режим
Эскиз.frw

МК4_.frw

Обозначение документа
СМ Проф. Р УТ КР КОИД ЕН ОП Кшт Тпз Тшт
наименование оборудования
км Наименование детали
сб. единицы или материала Обозначение
код ОПП ЕВ ЕН КИ Н.расх.
Покрытие-нитрид титана
Окончательная сдача на СГД
Напыление1.frw

подготовить ее к работе
Эксплуатация электрооборудования производится в соответствии с требованиями "правил технической эксплуатации электроустановок
потребителей" и "правил техники безопасности при эксплуатации электроустаовок потребителей". Госэнергонадзором СССР
Наименование операции Материал Твердость ЕВ МД Профиль и размеры МЗ КОИД
Оборудование Обозначение программы
Подготовка установки к работе
Технологический режим
- подключить установку к сети 50Гц
- открыть вентиль подачи холодной воды
- открыть вентиль подачи сжатого воздуха
Нагрев.frw

Оборудование Обозначение программы
Предварительный нагрев
Протереть детали салфеткой
Технологический режим
Установить деталь в термопечь и нагреть до 200 С
Спирт ГОСТ 18300-72. Салфетки хлопчатоб.
бязевые ГОСТ 11680-65
Перчатки хирургические
Промывка1.frw

Оборудование Обозначение программы
Промывка и обезжиривание
Промыть деталь в моющем растворе состава:
- натр едкий (ГОСТ 2263-71) 8 12гл
Промыть деталь в ванне с горячей водой
Промыть деталь в ванне с холодной водой
Технологический режим
- тринатрий фосфат (ГОСТ 201-58) 20 50гл
- жидкое стекло натриевое (ГОСТ 13078-67) 25 30гл
Т С раствора 40-70 С
Напыление2.frw

Установить оснастку с деталью в вакуумную камеру
Включить питание блоков источников питания ВСВУ-530
Установить деталь на оснастку для тел вращения
Технологический режим
Проверить плавность вращения оснастки в камере
Откачать камеру до рабочего давления
Нажать кнопку вращения оснастки
Титульник ТП.frw

ГОСТ 3.1105-84 Форма 2
Руководитель проекта
УФИМСКИЙ ГОСУДАРСТВЕННЫЙ АВИАЦИОННЫЙ
ТЕХНИЧЕСКИЙ УНИВЕРСИТЕТ
МК7_.frw

Обозначение документа
СМ Проф. Р УТ КР КОИД ЕН ОП Кшт Тпз Тшт
наименование оборудования
км Наименование детали
сб. единицы или материала Обозначение
код ОПП ЕВ ЕН КИ Н.расх.
Отпуск стабилизирующий
МК3.frw

Обозначение документа
СМ Проф. Р УТ КР КОИД ЕН ОП Кшт Тпз Тшт
наименование оборудования
км Наименование детали
сб. единицы или материала Обозначение
код ОПП ЕВ ЕН КИ Н.расх.
МК9_.frw

Обозначение документа
СМ Проф. Р УТ КР КОИД ЕН ОП Кшт Тпз Тшт
наименование оборудования
км Наименование детали
сб. единицы или материала Обозначение
код ОПП ЕВ ЕН КИ Н.расх.
МК1.frw

наименование операции
Обозначение документа
СМ Проф. Р УТ КР КОИД ЕН ОП Кшт Тпз Тшт
наименование оборудования
Заготовка-штамповка цеха 2а
МК5_.frw

Обозначение документа
СМ Проф. Р УТ КР КОИД ЕН ОП Кшт Тпз Тшт
наименование оборудования
км Наименование детали
сб. единицы или материала Обозначение
код ОПП ЕВ ЕН КИ Н.расх.
МК2.frw

Обозначение документа
СМ Проф. Р УТ КР КОИД ЕН ОП Кшт Тпз Тшт
наименование оборудования
км Наименование детали
сб. единицы или материала Обозначение
код ОПП ЕВ ЕН КИ Н.расх.
МК4_.frw

Обозначение документа
СМ Проф. Р УТ КР КОИД ЕН ОП Кшт Тпз Тшт
наименование оборудования
км Наименование детали
сб. единицы или материала Обозначение
код ОПП ЕВ ЕН КИ Н.расх.
Отпуск стабилизирующий
МК8_.frw

Обозначение документа
СМ Проф. Р УТ КР КОИД ЕН ОП Кшт Тпз Тшт
наименование оборудования
км Наименование детали
сб. единицы или материала Обозначение
код ОПП ЕВ ЕН КИ Н.расх.
МК10_.frw

Обозначение документа
СМ Проф. Р УТ КР КОИД ЕН ОП Кшт Тпз Тшт
наименование оборудования
км Наименование детали
сб. единицы или материала Обозначение
код ОПП ЕВ ЕН КИ Н.расх.
Титульник ТП.frw

ГОСТ 3.1105-84 Форма 2
Руководитель проекта
УФИМСКИЙ ГОСУДАРСТВЕННЫЙ АВИАЦИОННЫЙ
ТЕХНИЧЕСКИЙ УНИВЕРСИТЕТ
МК6_.frw

Обозначение документа
СМ Проф. Р УТ КР КОИД ЕН ОП Кшт Тпз Тшт
наименование оборудования
км Наименование детали
сб. единицы или материала Обозначение
код ОПП ЕВ ЕН КИ Н.расх.
Свер25_2 лист.frw

выдержав размеры (3)
Зенкеровать 4 отв. (1)
ОП25_ОК.frw

Ток10.frw

Оборудование Обозначение программы
ПИ Д или В L t i S n V
Установить деталь в расточные кулачки трехкулачкового патрона и закрепить
выдержав размер (1).
РИ 2102-0025; МИ ШЦ-I-125-0
Точить поверхность (2)
РИ 2102-0007; МИ ШЦ-1-125-0
Притупить острые кромки фаской или R0
в местах указанных на эскизе стрелками
Свер25.frw

Оборудование Обозначение программы
ПИ Д или В L t i S n V
Установить деталь в кондуктор и закрепить
Сверлить 1 отв. (1). диаметр 6
; выдержав размер (3)
РИ 2300-0003; МИ ШЦ-I-125-0
Зенкеровать 1 отв. (1)
РИ 2102-0007; МИ ШЦ-1-125-0
Провести риску на диаметр 74
Зафиксировать по отв. 1
ОП10_ОК.frw

ОП35_ОК.frw

Фрез35.frw

устройство ЧПУ Обозначение программы
ПИ Д или В L t i S n V
Установить деталь в приспособление и закрепить
выдержав размеры (1)
РИ 2300-0003; МИ ШЦ-I-125-0
ОП10.frw

Оборудование Обозначение программы
Промывка и обезжиривание
Промыть деталь в моющем растворе состава:
- натр едкий (ГОСТ 2263-71) 8 12гл
Промыть деталь в ванне с горячей водой
Промыть деталь в ванне с холодной водой
Технологический режим
- тринатрий фосфат (ГОСТ 201-58) 20 50гл
- жидкое стекло натриевое (ГОСТ 13078-67) 25 30гл
Т С раствора 40-70 С
МК11.frw

наименование операции
Обозначение документа
СМ Проф. Р УТ КР КОИД ЕН ОП Кшт Тпз Тшт
наименование оборудования
Промывка и обезжиривание
Предварительный нагрев
Совм.сх.cdw

План обр.cdw

обработки детали стакан
Фрезерная с ЧПУ 40035
Фрезерная с ЧПУ 40060
Покрытие - нитрид титана 43000
Загот.cdw

термообработать по технологии термического цеха
до твердост dотн = 3
мм. Группа контроля 4 по
ОСТ1.00021-78. Т - место контроля твердости
зачистки не более 1мм
в сопроводительном документе отметить о выполнении
травление на удаление альфированного слоя.
Допустимый съем металла 0
Контроль на альфированный слой и водород разрешается
Приспособление.cdw

стакан.cdw

заготовки кг не более
Заготовка штамповка или поковка III группы ОСТ 1 9000-70
мм. Группа контроля 4 по ОСТ 1 00021-78
* Размеры обеспечить инструментами
контроль травлением в заготовке
Покрытие поверхностей Е и М вакуумным азотированием по
технологии ОГМет. Допускается покрытие кругом
Допускается покрытие поверхностей Е и М - нитрид титана по
технологии Главного сварщика
Допуск овальности и конусообразности поверхности Е - 0
(полуразность диаметров)
Произвести прокачку маслом ПТС-225 ТУ 38.401-58-1-90 или Б-3В
ТУ38ю101295-85 при давлении (0
Расход масла ПТС-225 через отверстие Д(0
Расход масла Б-3В - (0
Для обеспечения заданного расхода допускается отверстие Д разверуть
Масляный канал промыть по п.9 при давлении 0
) и температуре 60 80
С в течение 5 мин. Частота сливаемого
масла должна быть не грубее II класса по ГОСТ 17216-71
Произвети проверку направления масляной струи через отверстие Д
по иммитатору. Попадание масла в зазор иммитатора не менее 60% заданного
Клеймить электрохимическим способом шрифтом 3
Общие требования по ОСТ 1 00450-82
Тит.DOC
Кафедра технологии машиностроения
ПОЯСНИТЕЛЬНАЯ ЗАПИСКА
к курсовому проекту по дисциплине «Технология обработки материалов КПЭ»
(обозначение документа)
Рекомендуемые чертежи
- 24.01.2023