Технологический процесс изготовления детали «Стакан левый»




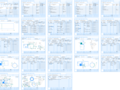
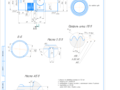
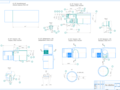
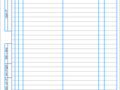
- Добавлен: 04.11.2022
- Размер: 1 MB
- Закачек: 2
Описание
Состав проекта
![]() |
![]() |
![]() ![]() ![]() |
![]() ![]() ![]() |
![]() ![]() ![]() |
![]() ![]() ![]() ![]() |
![]() ![]() ![]() ![]() |
![]() ![]() ![]() ![]() |
![]() |
![]() ![]() ![]() |
![]() |
![]() ![]() ![]() |
![]() ![]() ![]() ![]() |
Дополнительная информация
Чертеж стакана.cdw

патрон трех.cdw

Спецификация.cdw

цепи.cdw

Рекомендуемые чертежи
- 24.01.2023
- 13.12.2022
Свободное скачивание на сегодня
- 22.08.2014
- 29.08.2014