Технологический процесс механической обработки стакана роликоподшипника редуктора электрической лебедки




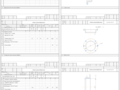
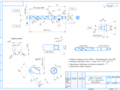
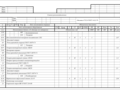
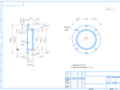
- Добавлен: 24.01.2023
- Размер: 1 MB
- Закачек: 1
Описание
Состав проекта
![]() |
![]() |
![]() |
![]() ![]() ![]() ![]() |
![]() ![]() ![]() ![]() |
![]() ![]() ![]() |
![]() |
![]() ![]() ![]() ![]() |
![]() ![]() ![]() ![]() |
![]() ![]() ![]() ![]() |
![]() ![]() ![]() ![]() |
![]() ![]() ![]() ![]() |
![]() ![]() ![]() ![]() |
Дополнительная информация
Карта 1.frw

сб. единицы или материала
наименование операции
Отливка СЧ 24 ГОСТ 1412-79
Стакан роликоподшипника
Обозначение документа
Восьмишпиндельный токарный полуавтомат 1282
Резец проходной упорный ГОСТ 18879-73
Патрон трехкулачковый самоцентоирующийся
Резец расточной ГОСТ 1888-73
Токарно-винторезный станок 16К20
Резец проходной отогнутый ГОСТ 18879-73
Резец проходной отогнутый ГОСТ 18879-73
Вертикально-сверлильный станок 2А135
Кондуктор скальчатый
Спиральное сверло ВК 8 ГОСТ 234-80
Токарно-револьверный станок 1П326
Карта 2.frw

сб. единицы или материала
наименование операции
Обозначение документа
Стакан роликоподшипника
Отливка СЧ 24 ГОСТ 1412-79
Пояснительная записка.doc
РЕМОНТА МАШИН И ОБОРУДОВАНИЯ
ПО ДИСЦИПЛИНЕ: «Технология сельскохозяйственного
Тема: «Технологический процесс механической обработки стакана роликоподшипника редуктора электрической лебедки»
Описание машины сборочного узла детали 5
2 Описание сборочного узла 6
4 Расчет типа производства 6
Выбор вида и метода получения заготовки 9
Разработка маршрутного технологического процесса 12
Выбор оборудования приспособления и режущего инструмента 13
Разработка операционного технологического процесса 14
1 Расчет операционного припуска 14
2 Расчет режима резания для токарной операции 15
3 Расчет режимов резания для сверлильной операции 19
4 Расчет режимов резания для расточной операции 23
Расчет геометрических параметров режущего инструмента 28
Проектирование приспособления 32
1 Описание разрабатываемого приспособления 32
2 Прочностные расчеты деталей приспособления 32
Определение технических норм времени 39
Расчет потребного количества станков 41
Расчет технико-экономических показателей 43
Курс «Технологии сельскохозяйственного машиностроения» рассчитан на студентов сельскохозяйственных вузов обучающихся по специальности «Технология обслуживания и ремонта машин в АПК». Он базируется на таких дисциплинах как «Материаловедение» «Технология конструкционных материалов» «Метрология стандартизация и сертификация» «Детали машин» и других. Успешное освоение дисциплин возможно при наличии у студентов хороших практических навыков работы на основных типах металлорежущих станков.
Курсовой проект по технологии машиностроения занимает особое место в системе подготовки инженеров-механиков.
Курсовой проект студенты выполняют в завершающем теоретическом обучении к предшествующему дипломному проекту. В курсовом проекте должны быть умело использованы минимальные знания полученные в процессе изучения общенормативных и специальных дисциплин учебного плана. При этом важно ориентировать курсовое проектирование по технологии машиностроения на генеральные направления технического процесса в машиностроении и разработку ресурсосберегающих технологий повышения качества продукции комплексную автоматизацию проектирования и производства.
Описание машины сборочного узла детали
Электрическая лебедка - машина с приводом от электродвигателя для перемещения грузов посредством движущегося гибкого элемента — каната или цепи. Тяговое усилие гибкому элементу передаётся с барабана или звёздочки приводимых в движение через передаточные механизмы.
Лебедки применяются в грузоподъемном оборудовании подъемно-транспортных машинах подъемных кранах а также при производстве погрузочно-разгрузочных строительных складских работах и др. Грузоподъемность лебедок составляет в среднем от 25 до 200 кН (от 025 до 20 т).
Лебёдка состоит из электродвигателя редуктора барабана рамы тормозной системы. В случае необходимости некоторые лебёдки сочетают с полиспастом.
Электрические лебедки подразделяются на:
- электрические лебедки с питанием от бытовой сети
- электрические лебедки с питанием от промышленной сети
- электрические автомобильные лебедки
Электрическая автомобильная лебедка
Электрическая автомобильная лебедка -это лебедка жестко закрепленная на автомобиле и предназначенная для его вытаскивания путем наматывания троса свободный конец которого зацеплен за неподвижный предмет значительно большей массы.
Такие лебедки работают от электромотора питающегося от бортовой сети автомобиля. На сегодняшний день это наиболее распространенный вид лебедок для внедорожников. Они отличаются простотой конструкции легкостью монтажа способностью работать при выключенном моторе.
Стаканы предназначены для размещения в них подшипников фиксирующей опоры вала червяка и опоры вала конической шестерни. Иногда стаканы применяют для удобства сборки. Стаканы для подшипников вала конической шестерни как правило перемещают при сборке для регулирования осевого положения конической шестерни. Другие стаканы чаще всего после их установки в корпус остаются относительно неподвижными.
Так как отверстия стаканов являются посадочными поверхностями для подшипников качения они должны иметь правильную геометрическую форму.
Стаканы изготавливают путем отливки и поковки.
4 Расчет типа производства
Различают следующие виды производств:
- единичное (индивидуальное);
- мелко- средне- крупносерийное;
Массовое производство может быть поточным (прерывным и непрерывным) наиболее производительной является непрерывно-поточная форма организации. Тип производства характеризуется коэффициентом закрепления операции Кзо. Для крупносерийного производства Кзо ≤ 10 для среднесерийного производства 10 ≤ Кзо ≤ 20 для мелкосерийного 20 ≤ Кзо ≤ 40 для единичного Кзо ≤ 40 для массового Кзо = 1.
Годовая программа изделий Пд = 5400 шт.
Для определения типа производства определяем такт выпуска данной детали и сравниваем его со временем длительности характерных операций [1 с 12].
где – такт выпуска деталей мин;
Фу – действительный годовой фонд времени станка ч.;
Пд – годовая программа выпуска детали.
где Фн – номинальный фонд времени ч.;
К1 – коэффициент учитывающий простой станка К1 = 094;
К2 – коэффициент простоя станка из-за отсутствия рабочего К2 = 092.
где m – количество недель в году m = 52;
n – количество рабочих часов в неделю n = 40;
f – число праздников f = 10;
с – продолжительность смены с = 8;
d1 – количество смен работы станка d1 = 2.
Определяем коэффициент закрепления операции: [1 c 12]
где о – число операций о = 7;
р – число рабочих мест р = 6.
Так как Кзо = 1.2 то тип производства – крупносерийный.
Крупносерийное производство - вид серийного производства при котором продукция изготовляется непрерывно в большом количестве. В крупносерийном производстве широко используются специализированное оборудование поточные линии и средства автоматизации.
Выбор вида и метода получения заготовки
Вид получения заготовки – отливка
Метод получения заготовки – литье в песочные формы отверждение вне контакта с оснасткой. Это наиболее распространенный способ получения отливок из серого чугуна для деталей средних и крупных размеров. Отливку производим в две полуформы с горизонтальной плоскостью разъема совпадающей с плоскостью симметрии детали.
Для выбранного способа литья из серого чугуна при наибольшем габарите отливки до 630 мм ГОСТ рекомендует классы точности размеров и масс 7т – 12 и ряды припусков 2 – 4. Меньшие значения классов точности и рядов припусков относятся к массовому а большие – к мелкосерийному или единичному производству отливок [1 c 20 таблица 1.14].
Для нашего случая выбираем класс точности размеров и масс 9 а ряд припусков - 3.
Таблица 1 – Допуски и размеры отливок мм
Дополнительный припуск
Наибольший наружный диаметр 190
Наименьший наружный диаметр 145
Наибольший внутренний диаметр 130
Наименьший внутренний диаметр 90
Определяем отношение наименьшего габаритного размера отливки к наибольшему. Это отношение:
что соответствует степени коробления. Для отливок из черных сплавов рекомендуются большие степени коробления.
Для габарита 197.8 мм и 7-й степени коробления предельное отклонение коробления составляет ± 0.4 мм которое из-за незначительности можно не учитывать.
При расстоянии между центрующем устройством формы до 630 мм и девятым классом точности размеров отливки предельное отклонение смещения форм не должно превышать ± 0.8 мм.
Определим максимальный возможный припуск на обработку заготовки по наружному диаметру.
Рисунок 1 – Схема для определения максимального диаметра заготовки
Максимальная высота конуса [1 c 29]
Тогда максимальный диаметр заготовки равен
С учетом допуска размер будет равен 2006±12 мм. Тогда возможный максимальный припуск по наружному диаметру на обработку (на сторону) равен
Разработка маршрутного технологического процесса
Маршрутная технология разрабатывается и оформляется с применением маршрутных технологических карт в которых перечисляются технологические операции приводятся данные о заготовке необходимом оборудовании приспособлениях и специальном инструменте. Нормы времени принимаются приближенно по опытным статистическим данным. Маршрутная технологическая карта может снабжаться эскизом детали. Вначале выполняются операции требующие снятия больших объемов металла (большие припуски) чистовые выполняются в конце.
0 Токарная - восьмишпиндельный токарный полуавтомат 1282
Приспособление – цанговый патрон
Инструмент – резец проходной упорный ГОСТ 18879 - 73
5 Токарная - токарно-винторезный станок 16К20
Приспособление – центровая оправка
Инструмент – резец проходной отогнутый ГОСТ 18879 - 73
0 Расточная - токарно-револьверный станок 1П326
Приспособление – патрон трехкулачковый самоцентрирующийся
Инструмент – резец расточной ГОСТ 1888 - 73
5 Токарная - Токарно-винторезный станок 16К20
Приспособление - цанговый патрон
Инструмент - резец проходной отогнутый ГОСТ 18879 - 73
0 Резьбонарезная - вертикально-сверлильный станок 2А135
Приспособление – кондуктор скальчатый
Инструмент – спиральное сверло ВК 8 ГОСТ 234 - 80
Выбор оборудования приспособления и режущего инструмента
Выбор станка производится в соответствии с характером обработки требований к точности и шероховатости на данной операции размерами обрабатываемой детали масштабом производства.
Размеры станка должны соответствовать размерам обрабатываемой детали. Нужно стремится к лучшему использованию производственных возможностей станка.
При выборе станка важными факторами является его стоимость и себестоимость обработки деталей на данном станке. При прочих равных условиях отдают предпочтение более дешевому станку или станку обеспечивающему минимальную себестоимость обработки.
Исходя из условий приведенных выше для выполнения токарной операции принимаем токарно-винторезный станок 16К20 для сверлильной операции принимаем вертикально-сверлильный станок 2А135 для расточной операции принимаем токарно-револьверный станок 1П326.
Для токарной операции выбираем приспособление: цанговый патрон.
Для сверлильной операции выбираем приспособление: кондуктор.
Для расточной операции выбираем приспособление: патрон трехкулачковый самоцентрирующийся.
Для токарной операции выбираем инструмент: резец проходной упорный.
Для сверлильной операции выбираем инструмент: спиральное сверло ВК8
Для расточной операции выбираем инструмент: резец расточной
Разработка операционного технологического процесса
1 Расчет операционного припуска
Операционный припуск – это слой металла удаляемый при выполнении одной технологической операции общий припуск на обработку представляет собой сумму всех операционных припусков.
Определяем операционные припуски допуски на обработку отверстия в стакане роликоподшипника:
Определяем операционный припуск и допуск на черновое растачивание:
Определяем операционный припуск и допуск на чистовое растачивание:
Определяем операционный припуск и допуск на шлифование:
z3 = (128 – Dзаг) = 128 – 123 = 5 мм;
Рисунок 2. Схема операционных припусков и допусков для отверстия
2 Расчет режимов резания для токарной операции
Станок: 16К20 Токарно-винторезный
Инструмент: Резец подрезной
Геометрические параметры инструмента:
Глубина резания согласно таблице равна t = 10 мм
Согласно паспортным данным станка принимаем S = 039 ммоб
Скорость резания [2 c 435]
где Сv – коэффициент в формуле скорости резания Сv = 685
Т – показатель периода стойкости Т = 60 мин;
m; yv – показатели степени в формуле скорости резания m = 02 yv = 04;
Кv – общий поправочный коэффициент на скорость резания [1 c 147]
где Kмv – коэффициент на качество обрабатываемого материала [1 c 158]
Knv – коэффициент на состояние поверхности заготовки Knv=08 [1 c 160];
Kφv Kφ1v Krv Kqv – коэффициенты на параметры резца Kφv=10 Kφ1v=094 Krv=103 Kqv=10;
Kuv – коэффициент на материал режущей части Kuv=10 [1 c 160].
Сила резания: [1 c 147]
где Ср – постоянная для данных условий резания Ср=92;
Кр – поправочный коэффициент [1 c 147]
где Кмр – поправочный коэффициент на качество материала
Кφр Кyp Kλp Krp – коэффициенты учитывающие влияние геометрических параметров резца на составляющие сил резания Кφр=10 Кyp=11Kλp=10 Krp=093;
где np - коэффициент учитывающий влияние механических свойств обрабатываемого материала на силы резания np=04
Частота вращения шпинделя [1 c 147]
где D – диаметр обрабатываемой заготовки
Согласно паспортным данным станка принимаем фактическую частоту вращения шпинделя nф=80 мин-1
Фактическая скорость резания [1 c 147]
Крутящий момент [1 c 166]
Мощность резания [1 c 148]
Основное время [1 c 148]
где L – длина рабочего хода резца
3 расчет режимов резания для сверлильной операции
Сверление 6 отверстий ø 11 мм
Станок: 2А135 Вертикально-сверлильный
Инструмент: Сверло ВК8 ГОСТ 234-80
Глубина резания [1 c 164]
где D – диаметр отверстия в мм после обработки D = 11мм
Принимаем S = 057 ммоб согласно паспортным данным станка;
Скорость резания [1 c 165]
где Сv – коэффициент в формуле скорости резания Сv = 171
m – показатели степени в формуле скорости резания qv = 045;
Кv – общий поправочный коэффициент на скорость резания [1 c 165]
где Кмv – коэффициент на качество обрабатываемого материала;
Кnv – коэффициент на инструментальный материал;
Кlv – коэффициент учитывающий глубину просверливаемого отверстия [1 c 169 таблица 25]
где НВ – твердость материала заготовки НВ = 135;
Кv = 15 * 083 * 1 = 12
Крутящий момент: [1 c 166]
где См – коэффициент для заданного условия резания См = 0012;
qм; yм – показатели степени в формуле крутящего момента qм = 22 yм = 08;
Кр – поправочный коэффициент учитывающий влияние механических свойств конструкционных сталей и стального литья серого и ковкого чугуна на силы резания.
где np – коэффициент зависящий от материала режущей части инструмента
Осевая сила: [1 c 166]
где Ср – коэффициент в формуле осевой силы Ср = 42
yp – показатели степени в формуле осевой силы qp = 12 yp = 075.
где n – число оборотов инструмента или детали; [1 c 166]
Основное время: [1 c 166]
По нормативам принимаем l2 = 3 мм
Нарезание резьбы 2 отверстий М12
Инструмент: метчик сталь У10А ГОСТ 17931 – 72
Мощность резания: [1 c 166]
4 Расчет режимов резания для расточной операции
Станок: 16К20 Токарно-револьверный
Инструмент: Резец токарный расточной для растачивания глухих отверстий ГОСТ 18883-73
Главный угол в плане φ=95°
Радиус при вершине r=1 мм
Согласно паспортным данным станка принимаем S=039 ммоб
Глубина резания согласно таблице равна t=10 мм
Скорость резания: [1 c 147]
где Сv – коэффициент в формуле скорости резания Сv = 292;
Кv – общий поправочный коэффициент на скорость резания.
где Kмv – коэффициент на качество обрабатываемого материала;
Knv – коэффициент на состояние поверхности заготовки Knv=08;
Kφv Kqv – коэффициенты на параметры резца Kφv=06 Kqv=116;
Kuv – коэффициент на материал режущей части Kuv=10
Кр – поправочный коэффициент
где Кмр – поправочный коэффициент на качество материала;
Кφр Кyp Kλp Krp – коэффициенты учитывающие влияние геометрических параметров резца на составляющие сил резания Кφр=089 Кyp=11Kλp=10 Krp=093
Частота вращения шпинделя: [1 c 147]
Согласно паспортным данным станка принимаем фактическую частоту вращения шпинделя nф=315 мин-1
Фактическая скорость: [1 c 147]
Момент инерции: [1 c 166]
Мощность резания: [1 c 148]
Основное время: [1 c 148]
Расчет геометрических параметров режущего инструмента.
Для выполнения сверлильной операции – сверление 6 отверстий 11 мм проектируем спиральное сверло.
Инструмент: Сверло спиральное ВК8 ГОСТ 234-80
Определяем диаметр сверла. По ГОСТ 19257-73 находим необходимый диаметр сверла для нарезания резьбы 12 мм. Диаметр сверла должен быть 107 мм; по ГОСТ 885-77 указанный диаметр имеется.
Режимы резания для сверлильной операции принимаем из расчета выполненного в пункте 51.
Подача S = 057 ммоб;
Определяем номер конуса Морзе хвостовика.
Момент трения между хвостовиком и втулкой: [3 c 209]
Приравниваем момент трения к максимальному моменту сил сопротивления резанию т.е. к моменту создающемуся при работе затупившемся сверлом который увеличивается до 3 раз по сравнению с моментом принятым для нормальной работы сверла.
Средний диаметр конуса хвостовика [3 c 212]
где Мср = 11 Нм – момент сопротивления сил резанию;
Рх = 2825 Н – осевая сила;
= 0096 – коэффициент трения стали по стали;
= 1°26’16’’ – половина угла конуса
Δ = 5’ – отклонение угла конуса;
Принимаем dcp = 12.2 мм.
Принимаем конус Морзе №1 со следующими основными размерами: D1 = 122 мм; d2 = 9 мм; l4 = 65.5 мм. [9 c 154 таблица 62]
Определяем длину сверла. По ГОСТ 10903-77 выбираем:
обща длина сверла L = 182 мм; длина рабочей части диаметр шейки d1 = D1 – 10 = 112 мм.
Принимаем d1 = 11 мм.
Центровое отверстие выполняется по форме В ГОСТ 14034-74.
Определяем конструктивные и геометрические параметры режещей части сверла. Находим форму заточки ДП (двойная с подточкой перемычки). Угол наклона винтовой канавки = 30°. Углы между режущими кромками: 2φ = 118°;
φ0 = 70°. Задний угол α = 12°. Угол наклона поперечной кромки = 55°.
Размеры подточки: А = 25 мм; t = 5 мм. [9 c 157]
Шаг винтовой канавки: [9 c 157]
Выбираем толщину dc = сердцевины сверла в зависимости от диаметра сверла.
Принимаем толщину сердцевины у переднего конца сверла равной 016D. Тогда dc = 016*D = 016*107 = 17 мм.
Утолщение сердцевины по направлению к хвостовику 14 – 18 мм на 100 мм длины рабочей части сверла принимаем это утолщение равным 15 мм.
Обратная конусность при длине сверла свыше D = 6 мм принимаем равную 008 мм.
Ширины ленточки f0 и высоту затылка по спинке К выбираем в соответствии с диаметром сверла. При D = 107 мм: f0 = 09 мм; К = 04 мм.
Ширина пера В = 058D = 058*107 = 62 мм.
Геометрические элементы профиля фрезы для фрезерования канавки сверла выполняют графическим или аналитическим способом. Воспользуемся упрощенным аналитическим методом.
Большой радиус профиля
Меньший радиус профиля Rk = Ck*D
где Ck = 0015*075 = 0192
Rk = 0192*107 = 205 мм
Ширина профиля [9 c 158]
B = R0 + Rk = 4.82 + 2.05 = 6.87 мм.
Проектирование приспособления
1. Описание разрабатываемого приспособления
В конструкцию любого скальчатого кондуктора входят постоянные сменные узлы. Постоянная часть кондуктора нормализуется и состоит из корпуса трех расположенных в нем скалок несущих кондукторную плиту механизма для перемещения скалок и зажима обрабатываемых деталей.
Сменные узлы состоят из установочно-зажимных узлов и сменной кондукторной плиты с комплектом кондукторных втулок. Для базирования и фиксации сменных колодок в корпусе и кондукторной плите предусматриваются установочные поверхности (центрирующие отверстия установочные пальцы и т.п.).
Кондуктор снабжен пневматическим устройством зажима заготовки.
Деталь предварительно центрируется на пальце а при опускании кондукторной плиты выравнивается по трем опорным штырям и окончательно центрируется на пальце. Отверстия сверлятся со стороны плоскости принятой за установочную базу. Для равномерного прилегания к трем опорам использован плавающий плунжерный механизм состоящий из пальца со сферической головкой накачивающегося диска и трех плунжеров направляемых втулками.
Необходимо чтобы при зажиме обрабатываемый стакан не упирался в пластину и поддерживался бы только плунжерами.
2. Прочностные расчеты деталей приспособления
Определение усилия рабочего необходимое для обеспечения достаточной затяжки болта М10. Болт в конструкции не должен работать на изгиб поэтому сила трения между листами должна быть не меньше внешней силы F. [10 c 59]
Затяжка Fз болта М10 создается при пользовании нормальным гаечным ключом. Коэффициент трения между листами f1 = 02 Коэффициент трения на опорной поверхности гайки fоп = 02 Коэффициент трения в резьбе f = 016. Допускаемая осевая нагрузка для болта М10 Ст3 равна [F] = 33 кН.
Определяем силу затяжки болта: [10 c 61]
Определяем момент завинчивания приложенный к гайке: [10 c 54]
где Ттр – момент затрачиваемый на преодоление сил трения в резьбе;
где – угол подъема резьбы = 2°30’;
φ – угол трения в резьбе;
d2 – средний диаметр резьбы d2 = 95 мм.
Определяем момент затрачиваемый на преодоление сил трения на опорной поверхности гайки: [10 c 54]
где rтр – радиус трения [10 c 55]
Определяем усилие затяжки [10 c 60]
Усилие рабочего необходимое для достаточной затяжки Q = 383 H. Расчетная осевая нагрузка Fз = 168 кН что равно 051 [F] где [F] = 33 кН.
Подбор посадки обеспечивающей соединение для передачи Т = 11 Н*м при следующих данных: d1 = 11 мм; d = 27 мм; d2 = 36 мм l = 24 мм. Материал – сталь 40 чистота поверхности – 7-й класс.
Принимаем коэффициент f = 008 и определяем давление на посадочной поверхности q обеспечивающее передачу заданного крутящего момента: [10 c 41]
Определяем расчетный натяг: [10 c 41]
где Е = 21*105 Нмм2 для стали; 1 = 2 = 03;
Определяем минимальный измеряемый натяг посадки: [10 c 44]
где Rz1 и Rz2 определяются в зависимости от шероховатости поверхности (Rz1 = Rz2 = 63 мкм) отсюда:
По СТ СЭВ 145-75 этому наименьшему натягу соответствует и отклонения отверстия будут 0 и 21 мкм отклонения вала +121 и +88; наименьший натяг m наибольший натяг max = 0 – 88 = - 88 мкм.
Проверяем допустимость такой посадки из условия работоспособности деталей. Опасными для данного случая являются точки на внутренней поверхности охватывающей детали. Проверку выполняем по наибольшему расчетному натягу (с учетом сглаживания неровностей) соответствующему выбранной посадке [10 c 44]
Находим максимальное давление которое вызовет максимальный расчетный натяг: [10 c 44]
Определяем наибольше эквивалентное напряжение: [10 c 44]
Для стали 40 Т = 320
Коэффициент запаса: [10 c 48]
3 Определение усилия зажима детали приспособлением
Для обеспечения запаса надежности зажима заготовки определяем коэффициент запаса надежности К.
где К0 – коэффициент гарантируемого запаса надежности закрепления К0 = 15;
К1 – коэффициент обработки при сверлении К1 = 12;
К2 – коэффициент учитывающий увеличение силы резания вследствие затупления инструмента К2 = 11;
К3 - коэффициент учитывающий постоянство силы закрепления в зажимах механизма К3 = 10;
К4 - коэффициент учитывающий эргономию зажимного механизма приспособления К4 = 10;
К5 - коэффициент учитывающий усилие при наличии моментов стремящихся повернуть заготовку К5 – 10.
Определяем необходимую силу зажима для сверления:
где Рz – сила резания Н
4 Экономическое обоснование выбора приспособления
Экономический расчет предназначен для выявления экономической целесообразности изготовления приспособления и определения годовой экономичности
Определяем себестоимость приспособления: [1 c 93]
где З – зарплата станочника отнесенная к одной детали руб;
Нц – цеховые накладные расходы на зарплату % (200 – 500 %);
Зпр – затраты на изготовление приспособления руб;
n – программа годового выпуска деталей шт;
Рпр – расходы связанные с применением приспособления Рпр = 20 %;
Апр – срок амортизации приспособления год Апр = 2.
Определяем зарплату станочника [1 c 94]
где Тшк – штучно-калькуляционное время операции ч;
S – часовая ставка рабочего первого разряда;
К – тарифный коэффициент К = 12.
Определение технических норм времени
Техническим нормированием называют определение норм времени (или норм выработки в единицу времени) на отдельные операции.
Технические нормы времени используют для расчета производственной мощности рабочего места участка цеха а также для определения затрат на зарплату рабочим и калькуляции себестоимости обработки.
Время затрачиваемое на данную операцию называют штучным.
Штучное время Тшт состоит из следующих времен: [1 c 78]
Тшт = То + Тв + Тоб + Тлп
где То – технологическое (основное) время;
Тв – вспомогательное время;
Тоб – время обслуживания;
Тлп – время перерывов в работе.
Сумму основного и вспомогательного времени называют оперативным временем Топ.
Оперативное время является основной составляющей штучного времени. Время на обслуживание рабочего места и время перерывов в работе обычно берется в процентах от оперативного времени (коэффициенты К1 и К2). В зависимости от характеристики обработки и масштаба производства время обслуживания рабочего места составляет К1 = 3 8% а время перерывов К2 = 4 9% от оперативного времени [1 c 79]
Для токарной операции:
К1 = 3 8% (То + Тв) = 0085;
К2 = 4 9% (То + Тв) = 0102.
Для сверлильной операции:
К1 = 3 8% (То + Тв) = 00195;
К2 = 4 9% (То + Тв) = 00273.
Для расточной операции:
К1 = 3 8% (То + Тв) = 00095;
К2 = 4 9% (То + Тв) = 00133.
Расчет потребного количества станков
Номинальный годовой фонд рабочего времени станка: [1 c 82]
где 52 – число недель в году;
– число рабочих часов в неделю
– число праздников в году;
– примерная продолжительность смены ч;
К – число смен работы станка К = 2.
Действительный годовой фонд времени станка: [1 c 82]
где К1 – коэффициент учитывающий простои оборудования из-за ремонта
К2 - – коэффициент учитывающий простои оборудования из-за отсутствия рабочих К2 = 092
Для определения потребного количества станков необходимо знать годовую производственную программу выпуска Пд данных деталей:
где Пм – годовая программа выпуска деталей;
n – число деталей на одну машину;
Расчетное количество станков для операции при крупносерийном производстве равно: [1 c 83]
где С – число партий деталей в год С = 12.
Расчет технико-экономических показателей
Обычно критерием целесообразности технологического процесса служит его экономичность в редких случаях – максимальная производительность. Следует иметь в виду что выполнение условия максимальной производительности процесса во многих случаях сопровождается повышением затрат на обработку в результате увеличенного расхода инструмента.
Себестоимость обработки детали [1 c 83]
где М – стоимость материала за вычетом стоимости отходов М = 12 руб;
З – основная заработная плата рабочих на изготовление одной детали руб;
α1 – процент накладных расходов α1 = 36%;
α2 – процент начислений на социальные расходы.
Основная заработная плата [1 c 84]
где Тшк – штучно-калькуляционное время операции ч [1 c 85]
Коэффициент времени 0 определяет долю машинного (основного) времени от общего времени выполнения операции [1 c 85]
Для токарной операции
Для сверлильной операции
Для расточной операции
Коэффициент загрузки оборудования по времени [1 c 85]
Перспективные задачи технологии машиностроения – повышение качества изготовляемых машин технологическими методами и рост производительности труда при изготовлении машин с минимально возможными капитальными вложениями. Рост производительности труда связан с сокращением малопроизводительного ручного труда экономией энергии и материалов.
При расчете технологического процесса изготовления стакана роликоподшипника были рассчитаны: коэффициент загрузки оборудования коэффициент основного времени.
Коэффициент загрузки оборудования для обработки данной детали менее единицы что говорит о непостоянной загруженности станков. Следовательно станки нужно загрузить обработкой других деталей.
Коэффициент основного времени также не высок что говорит о больших затратах на вспомогательное время.
Проектируемое приспособление позволяет сократить время на обработку детали за счет устранения разметочной операции а также уменьшает себестоимость детали на 14 %.
Курсовой проект по технологии сельскохозяйственного машиностроения содержит следующий материал:
расчетно-пояснительная записка;
лист формата– «деталь»;
лист формата– «заготовка;
лист формата– «режущий инструмент»;
лист формата– «схема сборки узла»;
лист формата А1 – «приспособление для сверлильной операции»;
лист формата А1 – «карта технологического процесса механической обработки заготовки»;
лист формата А4 – «спецификация»;
лист формата А4 – «маршрутная карта».
Общий вид.cdw

Отливка.cdw

Операционные карты.frw

обработать поверхность
Карты технологического
процесса изготовления
стакана роликоподшипника
Наименование операции
Установить и закрепить заготовку
Резец проходной упорный ВК6
Штангенциркуль 1-125-01 ГОСТ 166-80
Операционная карта механической обработки
Токарно-винторезный станок 16К20
Стакан роликоподшипника
Патрон трехкулачковый самоцентрирующийся
Вертикально-сверлильный станок 2А135
Метчик ГОСТ 17931-72
Нарезать резьбу в 2 отв.
Сверло ВК8 ГОСТ 234-80
Кондуктор скальчатый
Обозначение программы
Токарно-револьверный станок 1П326
Сверло.cdw

Материал хвостовой части - сталь 40Х по ГОСТ 4543-77.
Неуказанные предельные отклонения размеров
Допускается сварка трением.
Чертеж кондуктор.cdw

Схема сборки приспособления.cdw

Рекомендуемые чертежи
- 24.01.2023
- 26.05.2014