Технологический процесс механической обработки корпуса




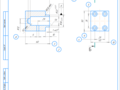
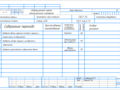
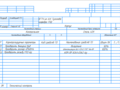
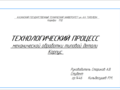
- Добавлен: 24.01.2023
- Размер: 422 KB
- Закачек: 0
Описание
Состав проекта
![]() |
![]() |
![]() ![]() ![]() ![]() |
![]() ![]() ![]() ![]() |
![]() |
![]() |
![]() |
![]() ![]() ![]() ![]() |
![]() |
![]() |
![]() |
![]() |
![]() |
![]() |
![]() |
![]() |
![]() ![]() ![]() ![]() |
![]() |
![]() |
![]() ![]() ![]() ![]() |
![]() |
![]() ![]() ![]() ![]() |
![]() ![]() ![]() ![]() |
![]() ![]() ![]() ![]() |
![]() ![]() ![]() ![]() |
![]() ![]() ![]() ![]() |
![]() ![]() ![]() ![]() |
![]() ![]() ![]() ![]() |
![]() ![]() ![]() ![]() |
![]() ![]() ![]() ![]() |
![]() ![]() ![]() ![]() |
![]() ![]() ![]() |
![]() ![]() ![]() ![]() |
Дополнительная информация
контроль.cdw

дд.cdw

титул.cdw

Карта кантроля 1.cdw

табл контроля.cdw

030.cdw

005.cdw

040.cdw

010.cdw

025.cdw

015.cdw

035.cdw

020.cdw

ЭСП.cdw

План.cdw

наладка.cdw

Рекомендуемые чертежи
- 26.05.2014
- 07.09.2016
- 02.05.2022