Технологический процесс изготовления детали ролик




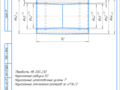
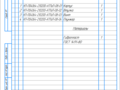
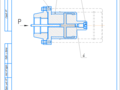
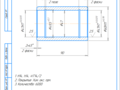
- Добавлен: 24.01.2023
- Размер: 724 KB
- Закачек: 1
Описание
Состав проекта
![]() |
![]() |
![]() ![]() ![]() ![]() |
![]() |
![]() ![]() ![]() |
![]() ![]() ![]() |
![]() |
![]() ![]() ![]() |
![]() ![]() ![]() |
![]() ![]() ![]() |
![]() ![]() ![]() |
![]() ![]() ![]() |
![]() ![]() ![]() ![]() |
![]() ![]() ![]() ![]() |
![]() |
![]() ![]() ![]() ![]() |
![]() ![]() ![]() |
![]() ![]() ![]() ![]() |
![]() |
![]() ![]() ![]() |
![]() ![]() ![]() ![]() |
![]() ![]() ![]() |
![]() ![]() ![]() |
![]() |
Дополнительная информация
Ролик - чертеж детали.cdw

002.frw

007.frw

004.frw

003.frw

001.frw

005.frw

006.frw

Карты наладок.cdw

оправка.cdw

Ролик - Заготовка.cdw

Эскизы операций.cdw

Спецификация.cdw

Рекомендуемые чертежи
- 24.01.2023
- 13.12.2022