Проектировка привода согласно схеме и исходным данных




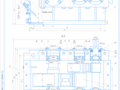
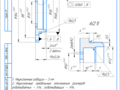
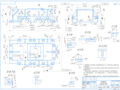
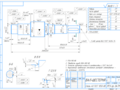
- Добавлен: 24.01.2023
- Размер: 703 KB
- Закачек: 0
Описание
Состав проекта
![]() |
![]() |
![]() ![]() ![]() |
![]() ![]() ![]() ![]() |
![]() ![]() ![]() ![]() |
![]() |
![]() ![]() ![]() ![]() |
![]() ![]() ![]() ![]() |
![]() ![]() ![]() ![]() |
![]() ![]() ![]() ![]() |
![]() ![]() ![]() ![]() |
![]() ![]() ![]() ![]() |
![]() ![]() |
![]() ![]() ![]() |
![]() ![]() ![]() |
![]() ![]() ![]() ![]() |
Дополнительная информация
Спецификация лист.DOC
Болт М16×30 ГОСТ 7805
Болт М16×60 ГОСТ 7805
Гайка М12-6Н.5 ГОСТ 5915
Гайка М16-6Н.5 ГОСТ 5915
Ремень А-2000 IV ГОСТ1284.1
Электродвигатель 4А80В2У3
Редуктор чистовик.cdw

уплотнительной пастой типа Герметик.
После сборки валы редуктора должны проворачиваться
без стуков и заедания.
Редуктор обкатать 15-20 минут на всех режимах нагрузки.
Техническая характеристика
+Крышка редуктора.cdw

Обработку мест под головки болтов (гаек) выполнить до чистой
Неуказанные предельные отклонения размеров: охватываемых -
Поверхность корпуса очистить и красить маслостойкой краской
+А3 вал 3.cdw

Неуказанные граничные отклонения размеров: охватываемых -
+А3-колесо зубч.cdw

Сталь 40 ГОСТ 1050-80
Радиус закруглений - 3мм
Точность зубчатого колеса в соответствии с ГОСТ 1643-81
Неуказанные предельные отклонения размеров: охватываемых -
+А4-Крышка.cdw

Неуказанные радиусы - 3 мм
Неуказанные предельные отклонения размеров:
охватываемых - охватывающих -
+А3 вал-шестерня 2.cdw

Сталь 40 ГОСТ 1050-88
Точность зубчатого колеса в соответствии с ГОСТ 1643-81
Неуказанные предельные отклонения размеров: охватываемых -
+А3 вал-шестерня 1.cdw

Сталь 40 ГОСТ 1050-88
Точность зубчатого колеса в соответствии с ГОСТ 1643-81
Неуказанные предельные отклонения размеров: охватываемых -
Привод .cdw

крепления рамы к редуктору
Ось электродвигателя
Схема расположения болтов
крепления элементов привода к раме
Прогиб ветви ремня под воздействием силы 100 Н не более 6мм
Непараллельность осей шкивов не более 0
Смещение рабочих поверхностей шкивов не более 0
Привод обкатать без нагрузки в течение не менне 1 часа. Стук
и резкий шум не допускаются.
После обкатки масло из редуктора слить и залить масло
индустриальное И-40А ГОСТ 20799-75 в количестве 0
Ограждения условно не показаны. Ограждения ременной передачи
установить и окрасить в оранжевый цвет.
Техническая характеристика
записка чистовик.doc
В курсовом проекте рассмотрены вопросы связанные с проектированием двухступенчатого цилиндрического редуктора и ременной передачи входящиих в привод.
Курсовой проект содержит:
а) пояснительная записка – листов;
б) количество разделов – 11
в) количество таблиц – 1
г) количество рисунков -- 19
г) количество использованных источников – 6
д) объем графической части – 5 листов А1 1 лист А3
Основная цель курсового проекта по деталям машин – приобретение навыков проектирования.
Одна из важнейших задач в подготовке инженера – научить творчески применять при решении поставленных задач приобретенные знания. Одной из целей выполняемого проекта является развитие инженерного мышления в том числе уметь использовать предшествующий опыт моделировать используя аналоги. Свойственная курсовому проекту по деталям машин многовариантность решений при одном и том же задании развивает у студентов мыслительную деятельность и инициативу.
Важнейшая задача курсового проектирования – развитие умения разрабатывать техническую документацию. Черчение наряду с устной речью писменностью математическими описаниями и т.д. является важнейшим средством коммуникации которым обязаны владеть инженеры. Базируясь на исходных предпосылках из курса графики машиностроительного черчения в процессе самостоятельной работы студенты овладевают свободным чтением и выполнением чертежей неограниченной сложности.
В данном курсовом пректе рассмотрены несколько возможных вариантов привода по заданным условиям – габариты мощность угловая скорость. Из них выбран наиболее предпочтительный с точки зрения максимальгого эффективного использования привода его компактности и т.д.
Выбор кинематической схемы
Рис. 1 Схемы привода
) Двухступенчатый цилиндрический редуктор с цепной передачей
) Двухступенчатый цилиндрический редуктор с ременной передачей
) Червячный редуктор с открытой конической передачей
) Одноступенчатый цилиндрический редуктор с ременной и цепной передачами
) Двухступенчатый цилиндрический редуктор с открытой цилиндрической передачей
Принимая во внимание КПД проектируемого привода а также возможные его габариты выбираем схему 2. Из приведенных выше схем приводов схема 2 имеет наибольший КПД.
Кинематические расчеты и выбор электродвигателя
1. Коэффициент полезного действия (КПД) привода
Величины берем по таблице 1.2.1. [1]
2. Расчетная мощность электродвигателя
3. На основании рекомендуемых передаточных чисел u для различных видов механических передач определяем максимальное и минимальное передаточное число привода
4. Расчетная частота вращения вала электродвигателя
5. По таблице 2.4.[2] выбираем электродвигатель из условия: и
А80В2У3 ( Pэд=22 кВт; nэд=2865 мин -1)
6. Действительное общее передаточное число привода
7. Действительные передаточные числа передач
uцил1=31; uцил2=31; uрем=208
8. Силовые и кинематические параметры валов привода
9. Предварительно определяем диаметры валов привода из расчета только на кручение при пониженных допускаемых напряжениях
где МПа – для всех валов (меньшие величины – для быстроходных валов большие – для тихоходных валов). Полученные значения округляем до ближайших больших целых величин
Все данные сводим в таблицу
Расчет зубчатых цилиндрических передач
1 Расчет зубчатой прямозубой передачи (вторая ступень).
Частота вращения n1=4443 мин -1; n2=1433 мин -1
Передаточное число u=31
Продолжительность работы передачи 5 лет
Kсут=0.6 ; Kгод=0.25
Материал для шестерни выбираем сталь45
для колеса выбираем сталь 35
шестерня: НВ1=240; =850 МПа; =580 МПа;
колесо: НВ2=187; =550 МПа; =315 МПа;
Допускаемые контактные напряжения
Базовое число циклов соответствующее пределу выносливости для
шестерни и зубчатого колеса
Эквивалентное число циклов
где с=1 – число зацеплений зуба за один оборот колеса
Коэффициент долговечности
Предел контактной выносливости
где SH1(2)=1.1 – для зубчатых колес с однородной структурой
Расчетные допускаемые контактные напряжения
Допускаемые изгибные напряжения
Базовое число циклов напряжений NF lim= цикл.
где КFE=(16·0.35)+(0.76·0.3)+(0.56·0.35)=0.39(3.6)
Предел выносливости зубьев при изгибе ([1]табл.4.1.4)
где YA – коэффициент учитывающий влияние двустороннего
приложения нагрузки:
при одностороннем приложении нагрузки YA=1
Допускаемые напряжения при действии максимальной нагрузки:
1.1 Прочностной расчет
Расчет межосевого расстояния и выбор основных параметров передачи
T1=417Н·м; T2=1246Н·м
Расчетное межосевое расстояние
где ka=-для прямозубых передач
=1.07 - коэффициент учитывающий неравномерность распределения нагрузки по ширине венца. Определяем по рисунку 4.2.2a[1]
KA=11 – коэффициент внешней динамической нагрузки определяем по таблице 4.2.9.[1]
=0.488 - коэффициент ширины шестерни относительно межосевого расстояния
Зубчатого колеса мм(3.13)
Принимая предварительно определяем модуль зацепления
Значение m’ округляем до ближайшей величины mnm в
соответствии с ГОСТ 9563 по таблице 4.2.2.[1] mn=35
Число зубьев шестерни
Число зубьев зубчатого колеса
Действительное передаточное число
uд=z2z1=5618=3111 (3.19)
Начальные диаметры зубчатых колес
Диаметры вершин зубьев
Диаметры ножек зубьев
1.2 Проверка расчетных контактных напряжений
окружная сила в зацеплении
окружная скорость колес
степень точности по таблице 4.2.8.[1] выбираем 9 степень точности в зависимости от параметров f(V )
Коэффициент учитывающий динамическую нагрузку в зацеплении табл.4.2.8[1] КHv=1.06
Коэффициент учитывающий неравномерность распределения нагрузки по ширине венца
Коэффициент учитывающий неравномерность нагрузки для одновременно зацепляющихся пар зубьев
-- для прямых зубьев
удельная расчетная окружная сила
расчетные контактные напряжения
где ZН=1.77 для прямых зубьев – коэффициент учитывающий форму сопряженных поверхностей зубьев
для прямых зубьев – коэффициент учитывающий суммарную длину контактных линий
Расчетные контактные напряжения не превышают допустимого значения т.е. прочность зубчатого колеса по контактным напряжениям обеспечена.
1.3 Проверка расчетных напряжений изгиба
Коэффициент учитывающий динамическую нагрузку в зацеплении табл.4.2.8[1] КFv=111
удельная расчетная окружная сила при изгибе
коэффициент учитывающий форму зуба
где эквивалентное число зубьев
z2E=z2=56 – для прямых зубьев
Далее производим расчет для элемента пары “шестерня-колесо” у которого меньшая величина
расчетные напряжения изгиба зуба
где - коэффициент учитывающий наклон зуба. Для прямых зубьев =1
- коэффициент учитывающий перекрытие зубьев. Для прямых зубьев =1
1.4 Проверка прочности зубьев при перегрузках
максимальные контактные напряжения
максимальные напряжения изгиба
1.5 Силы в зацеплении зубчатых колес
уточненный крутящий момент на шестерне
При перегрузках максимальные значения контактных напряжений и напряжений изгиба находятся в пределах допустимых значений.
2. Расчет зубчатой прямозубой передачи (первая ступень).
Частота вращения n1=13774 мин -1; n2=4458 мин -1
Передаточное число u=309
Расчет производим аналогично расчету первой ступени
Материал для шестерни выбираем сталь 45
шестерня: НВ 240; =850 МПа; =580 МПа;
колесо: НВ 187; =550 МПа; =315 МПа;
Так как то YN2=1 YN1=1
где YA – коэффициент учитывающий влияние двустороннего приложения нагрузки:
2.1. Прочностной расчет
T1=138·м; T2=416 Н·м
Расчетное межосевое расстояние принимаем из расчета первой ступени в связи с особенностью конструкции редуктора
Зубчатого колеса мм(3.14)
соответствии с ГОСТ 9563 по таблице 4.2.2.[1] mn=25
uд=z2z1=5618=311(3.20)
2.2. Проверка расчетных контактных напряжений
степень точности по таблице 4.2.8.[1] выбираем 8 степень точности в зависимости от параметров f(V )
Коэффициент учитывающий динамическую нагрузку в зацеплении табл.4.2.8[1] КHv=1.15
Необходимо увеличить параметр в2.
т.е. контактные напряжения превышают допустимое значение на незначительную величину что не отразится на прочности и работоспособности детали.
2.3 Проверка расчетных напряжений изгиба
Коэффициент учитывающий динамическую нагрузку в зацеплении табл.4.2.8[1] КFv=13
2.4. Проверка прочности зубьев при перегрузках
2.5 Силы в зацеплении зубчатых колес
Расчет клиноременной передачи
Р1=21кВт; n1=2865 мин-1; Т1=7 Н·м
Р2=199кВт; n2=11148 мин-1; Т2=1705 Н·м
Расчет производим для двух ближайших сечений ремня
Выбираем сечение ремня в зависимости от передаваемого крутящего момента [1] табл.2.2.1
Минимальный расчетный диаметр ведущего шкива
d1мин=d1действ= 63мм
d2мин= d2действ=90мм
Диаметр ведомого шкива
Действительный диаметр ведомого шкива
Действительное передаточное число передачи
Минимальное межосевое расстояние
Где Нр – геометрический параметр ремня [1 табл.2.2.1]
Расчетная длина ремня
Действительная длина ремня [1 табл.2.2.6]
Межцентровое расстояние
Угол обхвата ремнем меньшего шкива
-- коэффициент учитывающий влияние угла обхвата
Число ремней передачи
Сила нагружающая валы передачи
где Н – предварительное натяжение ремня
Ремень А – 2000 IV ГОСТ 1284.1
Для ременной передачи крутящего момента от электродвигателя к редуктору принимаем два ремня А – 2000 IV ГОСТ 1284.1. При этом сила нагружающая вал от передачи значительно меньше чем в случае с ремнем сечения Z(0). Кроме того для передачи данного крутящего момента требуется два ремня сечения А. Для передачи того же момента необходимо три ремня сечением Z(0).
1. Проектный расчет вала 1.
Составляем расчетную схему где вал рассматриваем как балку лежащую на шарнирных опорах а расстояния между опорами и от опор до точек приложения сил замеряем на компоновке редуктора. Принимаем материал вала – сталь 45.
Окружное усилие в зацеплении:
Радиальное усилие в зацеплении:
Давление оказываемое на вал со стороны ременной передачи:
Определяем опорные реакции в вертикальной плоскости (XOZ).
Рис.5.1 Эпюра изгибающего момента (плоскость XOZ)
Составив уравнение суммы моментов всех сил относительно опор A и B получим:
-Fрем·0.075-Fr1·0.055+RБХ·0.195=0
(-Fрем0.27+ Fr1.·0.14- RАХ·0.195)=0
Определяем опорные реакции в горизонтальной плоскости (YOZ).
Рис.5.2 Эпюра изгибающего момента (плоскость YOZ)
RBY=Ft1.·00550195= 2144 H
RAY=Ft1·0140195= 5456 H
Cтроим эпюры изгибающих моментов в вертикальной и горизонтальной плоскостях.
Суммарные изгибающие моменты приведенные в одну плоскость:
Строим эпюру суммарных изгибающих моментов.
Рис.5.3 Эпюра суммарного изгибающего момента
Рис.5.4 Эпюра крутящего момента
Эквивалентные моменты (от изгиба и кручения) определяются:
Рис.5.5 Эпюра эквивалентного момента
Суммарные реакции в опорах (приведенные в одну плоскость) которые потребуются при подборе подшипников:
Определяем диаметр вала в опасных сечениях:
Производим проверку вала на кратковременную перегрузку по крутящему моменту. Пиковая нагрузка предполагается случайной действующей ограниченное число раз и равной Tпик = 18 Tmax
Наибольшие напряжения изгиба и кручения в опасном сечении при кратковременной перегрузке следующие:
sF = = 309 Нмм2(5.6)
Эквивалентное напряжение:
sэ = = 329 Нмм2(5.8)
Проверяем вал по запасу статической прочности по формуле:
Sт = = 109 > [Sт] = 15(5.9)
где sт = 360 Нмм2 — предел текучести материала.
Коэффициент запаса прочности относительно текучести превосходит допускаемое значение что обеспечивает достаточный запас статической прочности увеличивая жесткость вала.
Принимаем следующую конструкцию вала
Рис.5.6 Эскиз вала 1
1.1 Проверочный расчет вала 1 на усталостную прочность
Производим проверочный расчет вала на выносливость для наиболее опасного сечения:
В сечении А-А (рис.5.6) действует изгибающий момент М = 458 Н·м и крутящий момент Т= 1705 Н·м.
Амплитуда номинальных напряжений изгиба при симметричном цикле изменения напряжений изгиба по формуле:
sа = sF = = 1696 Нмм2(5.10)
Коэффициент запаса прочности по нормальным напряжениям:
где Кs = 185 – эффективный коэффициент концентрации напряжений для ступенчатых валов с галтелью (табл.14.2 [3])
es=085–масштабный фактор в зависимости от диаметра вала
Ys = 02 – коэффициент учитывающий влияние постоянной
составляющей цикла на усталость вала (табл.14.4 [3]);
sm =0– постоянная составляющая цикла изменения напряжений.
Определяем коэффициент безопасности по кручению.
При нереверсивном вращении вала касательные напряжения для отнулевого цикла определяются по формуле:
tm = tа = = 432 Нмм2(5.12)
где WК=мм3 момент сопротивления(5.13)
Коэффициент безопасности для сечения на опоре по кручению:
где Кt=14 – эффективный коэффициент концентрации напряжений при кручении для ступенчатых валов с галтелью (табл.14.2 [3])
et=077–масштабный фактор при кручении в зависимости от диаметра
вала (табл.14.3 [3])
Yt = 01 – коэффициент характеризующий чувствительность материала к асимметрии цикла изменения напряжений (табл.14.4 [3]);
Общий коэффициент безопасности по усталостной прочности для сечения вала на опор:
S = = 75 > [S] = 25(5.15)
Прочность и жесткость вала обеспечены т.к. общий коэффициент безопасности превышает минимально допустимое значение.
2 Проектный расчет вала 2.
Составляем расчетную схему где вал рассматриваем как балку лежащую на шарнирных опорах а расстояния между опорами и от опор до точек
приложения сил замеряем на компоновке редуктора. Принимаем материал вала – сталь 45.
Первой ступени Fr2 = 2664 Н
Второй ступени Fr3 = 4754 Н
Определяем опорные реакции в вертикальной плоскости (XOZ) и строим эпюры изгибающих моментов.
Рис.5.7 Эпюра изгибающего момента (плоскость XOZ)
Fr2·0.055- Fr3·0.13+RБХ·0.195=0
Fr3·0.065- Fr2·0.14-RАХ·0.195=0
Определяем опорные реакции в горизонтальной плоскости (YOZ) и строим эпюры изгибающих моментов.
Рис.5.8 Эпюра изгибающего момента (плоскость YOZ)
Ft2.·0055- Ft3.·013+ RBY ·0195=0
Ft3.·0065-Ft2·014+ RAY·0195=0
Строим эпюру суммарных изгибающих моментов Нм.
Рис.5.9 Эпюра суммарного изгибающего момента
Рис.5.10 Эпюра крутящего момента
Рис.5.11 Эпюра эквивалентного момента
sF = = 574 Нмм2(5.6)
sэ = = 748 Нмм2(5.8)
Sт = = 46 > [Sт] = 15(5.9)
где sт = 350 Нмм2 — предел текучести материала.
Рис.5.12 Эскиз вала 2
2.1 Проверочный расчет вала 2 на усталостную прочность
В сечении А-А (рис.5.12) действует изгибающий момент М = 464 Н·м и крутящий момент Т= 417 Н·м.
sа = sF = = 172 Нмм2(5.10)
tm = tа = = 39 Нмм2(5.12)
S = = 74 > [S] = 25(5.15)
3 Проектный расчет вала 3.
Составляем расчетную схему где вал рассматриваем как балку лежащую на шарнирных опорах а расстояния между опорами и от опор до точек приложения сил замеряем на компоновке редуктора.
Давление оказываемое на вал со стороны муфты:
Рис.5.13 Эпюра изгибающего момента (плоскость XOZ)
FМ·0.25+Fr2·0.11-RБХ·0.17=0
FМ0.08- Fr2.·0.06- RАХ·0.17=0
Рис.5.14 Эпюра изгибающего момента (плоскость YOZ)
RBY=Ft2.·011017= 823 H
RAY=Ft2·006017= 4488 H
Рис.5.15 Эпюра суммарного изгибающего момента
Рис.5.16 Эпюра крутящего момента
Рис.5.17 Эпюра эквивалентного момента
Определяем диаметр вала в сечении в котором эквивалентный момент наибольший:
Sт = = 39 > [Sт] = 15
где sт = 400 Нмм2 — предел текучести материала.
Рис.5.18 Эскиз вала 3
3.1 Проверочный расчет вала 3 на усталостную прочность
Производим проверочный расчет вала на выносливость для наиболее опасного сечения А-А (рис.5.18) где действует максимальный изгибающий момент:
В сечении действует изгибающий момент М = 665 Н·м и крутящий момент Т= 1246 Н·м.
sа = sF = = 104 Нмм2(5.10)
es=088–масштабный фактор в зависимости от диаметра вала (табл.14.3 [3])
tm = tа = = 496 Нмм2(5.12)
S = = 122 > [S] = 25(5.15)
1 Расчет подшипников вала 1
dп = 30 мм - диаметр посадочной поверхности вала
n = 11148 мин–1 — частота вращения вала Lh = 2190 ч.
Определяем требуемую динамическую грузоподъемность подшипников:
СтрА=RА·= 36189 H(6.1)
где р = 3 — степенной показатель.
подшипник 1000906 ГОСТ 8338
2 Расчет подшипников вала 2
dп = 25 мм - диаметр посадочной поверхности вала
n = 4458 мин–1 — частота вращения вала.
СтрА=RА·= 3759 H(6.1)
подшипник 1000805 ГОСТ 8338
D=37 мм В=7мм С=312кН
3 Расчет подшипников вала 3
dп = 40 мм - диаметр посадочной поверхности вала
n = 1433 мин–1 — частота вращения вала.
СтрА=RА·= 1341 H(6.1)
подшипник 1000908 ГОСТ 8338
D=62 мм В=12мм С=75кН
Расчет шпоночных соединений
1 Расчет шпоночного соединения вала 1 со шкивом.
Принимаем материал шпонки — сталь 45 с [sсм] =100 Нмм2
Размеры шпонки для этого вала: bh = 87 мм табл.4.1[3]
Определим рабочую длину шпонки lp исходя из условия прочности на смятие:
где Т — передаваемый вращающий момент
[sсм] – допускаемое напряжение при смятии.
Полная длина шпонки:
L = lp + b = 49 +8 = 129 мм(7.2)
Принимаем по СТ СЭВ 189-75 для соединения вала с полумуфтой призматическую шпонку 8714 мм.
2 Расчет шпоночного соединения вала 2 с зубчатым колесом.
Т=147 Н·м — момент передаваемый валом
d = 30 мм — диаметр участка вала
Принимаем материал шпонки — сталь 45 с [sсм] =100 Нмм2
Подбираем шпонку с размерами: bh = 108 мм.
L = lp + b = 31+10 = 14 мм(7.2)
Принимаем по СТ СЭВ 189-75 призматическую шпонку 10814 мм.
3 Расчет шпоночного соединения вала 3 с зубчатым колесом
Т=1246 Н·м — момент передаваемый валом
d = 50 мм — диаметр участка вала
Для соединения этого вала с зубчатым колесом подбираем шпонку с размерами: bh = 1610 мм.
L = lp + b = 124+16 = 284 мм(7.2)
Принимаем по СТ СЭВ 189-75 призматическую шпонку 161032 мм.
Выбор и проверочный расчет муфты
Для соединения выходного вала редуктора и вала механизма принимаем фланцевую муфту. Она обеспечивает надежное соединение валов простая по конструкции и поэтому широко применяется в машиностроении.
Материал полумуфт – сталь 40
Болты соединяющие полумуфты становятся через один: половина болтов устанавливается без зазора а вторая половина – с зазором.
Муфта фланцевая 125-30-11 ГОСТ 20761
Условие прочности на срез болтов установленных без зазора
где Тр – расчетный момент 2ТрD0 – расчетная окружная сила
D0 – диаметр окружности проходящей через центры болтовых отверстий z – число болтов установленных без зазора dб – диаметр ненарезанной части стержня болта (для болтов не более М24 на 1мм больше диаметра резьбы).
Условие прочности выполняется
Выбор системы смазки смазочных материалов и
Для уменьшения потерь мощности на трение и снижение интенсивности износа трущихся поверхностей а также для предохранения их от заедания задиров коррозии и лучшего отвода теплоты трущихся поверхностей детали должны иметь надежную смазку.
Применяем картерную систему смазки. В корпус редуктора заливаем масло так чтобы в него были погружены зубья цилиндрической шестерни. При ее вращении масло увлекается зубом разбрызгивается попадает на внутренние стенки корпуса откуда стекает в нижнюю его часть. Внутри корпуса образуется взвесь частиц масла в воздухе которая покрывает поверхность расположенных внутри корпуса деталей. Наименьшую глубину шестерни в масло принято считать равной модулю зацепления.
Выбираем смазочный материал. Требуемая вязкость масла зависит от контактного напряжения и окружной скорости колес. По определенным скорости и контактным напряжениям находим требуемую кинематическую вязкость и марку масла – индустриальное И – 20А.
При работе передач масло постепенно загрязняется продуктами износа. С течением времени оно стареет свойства его ухудшаются. Поэтому масло необходимо периодически менять. Для этой цели в корпусе предусматриваем сливное отверстие закрываемое резьбовой пробкой с прокладкой что создает герметичное соединение.
При длительной работе в связи с нагревом масла и воздуха повышается давление внутри корпуса что приводит к просачиванию масла через уплотнения и стыки. Чтобы этого избежать внутреннюю полость корпуса сообщают с внешней средой путем установки отдушины в его верхних точках.
Уплотнительные устройства применяем для предохранения от вытекания смазочного материла из подшипниковых узлов а так же для защиты их от попадания извне пыли и влаги. Используем манжетные уплотнения. Манжету устанавливаем открытой стороной внутрь корпуса. В этом случае к рабочей кромке манжеты обеспечен хороший доступ смазочного масла.
Определение размеров корпусных деталей кожухов ограждений и установочной плиты
Для редукторов минимальная толщина стенки отвечающая требованиям необходимой жесткости корпуса равна 8мм.
Толщина наружных ребер жесткости у их основания принимают равной dреб = d = 8 мм
Толщина стенки крышки корпуса dкр = 09·d = 72 мм »8 мм(10.1)
Диаметры болтов соединяющих:
редуктор с рамой (фундаментных)
d1 = 20· = 16 мм(10.2)
корпус с крышкой у бобышек подшипников
d2 = 15· = 12 мм(10.3)
корпус с крышкой по периметру соединения
d3 = 10· = 8 мм(10.4)
корпус со смотровой крышкой
крышку подшипникового узла с корпусом
Ширина фланцев редуктора
S1 = +x+k1 = 8+2+40 = 50 мм(10.5)
корпуса и крышки (у подшипников)
S2 = +x+k2 = 8+2+32 = 42 мм(10.6)
корпуса и крышки (по периметру)
S3 = +x+k3 = 8+2+24 = 34 мм(10.7)
Толщина фланцев редуктора
фл1 = 23· = 19 мм(10.8)
корпуса (соединение с крышкой)
фл2 = 15· = 12 мм(10.9)
крышки (соединение с корпусом)
фл3 = 135· = 11 мм(10.10)
Размеры крышек подшипников
При Dп1=47 мм: диаметр установки болтов
D1 = Dп1+25·d5 = 47+25·6=62 мм(10.11)
наружный диаметр фланца
Dн1 = D1+2·d5 = 62+2·6=74 мм(10.12)
толщина фланца крышки
Для точной фиксации крышки редуктора относительно корпуса применяем 2 конических штифта. Кроме фиксирования штифты предохраняют крышку и корпус от сдвигов при растачивании отверстий. Размеры штифтов принимаем по ГОСТ 3129-70:
lш = фл2+ фл3+5=12+11+5=28 мм(10.13)
Принимаем dш = 8 мм; с = 12 мм
Высота осей редуктора
Опорную поверхность корпуса редуктора выполняем в виде 4-х небольших платиков расположенных в месте установки винтов.
Описание технологических мероприятий по восстановлению быстро изнашиваемых деталей механического привода
Для восстановления рабочих поверхностей быстро изнашиваемых деталей машин находит применение целый ряд способов основанных на методах сварки наплавки напыления и т.д.
С помощью различных видов сварки можно заваривать трещины в корпусных деталях приваривать накладки вставки наплавлять износостойкие материалы.
Наиболее распространенными способами восстановления размеров изношенных деталей и нанесения поверхностных слоев с заданными эксплуатационными характеристиками является наплавка. Среди известных её способов на практике широко применяются ручная дуговая наплавка штучными электродами механизированная под слоем флюса в среде защитных газов плавящимся и неплавящимся электродом плазменная вибродуговая и газоплазменная наплавка.
Наплавка позволяет получать на поверхности деталей слой небольшой толщины и необходимого состава обеспечивающего высокую твердость и износостойкость.
Ручная дуговая наплавка — наиболее распространенный метод преимуществами которого являются простота процесса и используемого наплавочного оборудования возможность его применения для ремонта деталей различной конструкции и размеров. К недостаткам относятся непостоянство качества неплавленного слоя низкая производительность и тяжелые условия труда.
При механизированной наплавке под слоем флюса в зону горения дуги с помощью специальных аппаратов подается электродная проволока или лента. Зона горения дуги и ванна расплавленного металла защищены гранулированным флюсом специального состава. Перемещение дуги вдоль изделия осуществляется автоматически поэтому размеры валиков и состав наплавленного металла являются более стабильными чем при ручной наплавке.
Наплавка выполняется при больших плотностях тока и является более производительным процессом в результате которого за 1 ч наплавляется 5-8 кг металла в то время как при ручном способе этот показатель составляет 1-2 кгч. К недостаткам механизированной наплавки под флюсом следует отнести невозможность применения этого способа для наплавки деталей сложной конфигурации а также потребность в специальном наплавочном оборудовании.
Распространенным методом является автоматическая и полуавтоматическая наплавка плавящимся электродом в среде защитных
газов. В этом случае зона горения дуги и расплавленный металл защищаются от воздуха струей инертного или углекислого газа. Этот метод наплавки применяют в тех случаях когда затруднена или невозможна наплавка под флюсом (при наплавке внутренних поверхностей глубоких отверстий мелких деталей или деталей сложной конфигурации кромок изделия когда удержание флюса на поверхности изделия представляет значительные трудности).
Наилучшая защита металла достигается при использовании инертных газов (аргон или гелий) применяемых для наплавки высоколегированных сталей а также цветных металлов и сплавов. При наплавке в углекислом газе активные легирующие элементы (хром алюминий титан и др.) интенсивно окисляются. Тем не менее данный способ распространен при наплавке углеродистых и легированных сталей при условии дополнительного введения в присадочные материалы активных раскислителей (марганца кремния и др.).
При наплавке цветных металлов и высоколегированных сплавов применяется наплавка в среде инертного защитного газа неплавящимся (вольфрамовым) электродом. В этом случае присадочный материал в виде отдельных прутков или проволоки подается в зону горения дуги вручную или с помощью специального подающего механизма (при механизированных способах наплавки). Этим же методом можно производить наплавку материалов предварительно нанесенных на поверхность изделия в виде паст и порошков.
Преимущество данного метода – возможность наплавки практически любого состава металла высокое качество наплавленных слоев малая глубина проплавления основного металла возможность нанесения тонких (до 05 мм) слоев. К недостаткам следует отнести значительную трудоемкость процесса и высокую стоимость защитных газов.
В некоторых случаях при наплавке в качестве неплавящегося электрода можно использовать графитовые или угольные стержни. Данный метод используется преимущественно для наплавки малоответственных изделий высокоуглеродистыми твердыми сплавами. Наплавка производится по слою гранулированной шихты.
Механизированная наплавка под флюсом и в среде защитных газов может производиться с применением проволок или лент. Порошковые проволоки представляют собой металлическую трубку заполненную шихтой состоящей из смеси порошков металлов или ферросплавов и шлако- и газообразующих компонентов. Поэтому многие порошковые проволоки используют для наплавки открытой дугой без дополнительной защиты зоны дуги флюсом или газом. При наплавке такими проволоками на поверхности швов образуется тонкий слой шлака который не мешает наплавке с перекрытием валиков без удаления шлаковой корки. Возможность видеть
дугу и управлять ею позволяет легко наплавлять детали сложной формы в различных пространственных положениях. Однако в данном случае имеют место потери металла на угар и разбрызгивание.
При ремонте цилиндрических деталей небольших диаметров (10-100 мм) получила применение вибродуговая наплавка. При этом способе на вращающуюся деталь наплавляют металл с помощью электрической дуги горящей между изделием и вибрирующей электродной проволокой колебания которой осуществляются специальным вибратором. Вибрация электрода вызывает кратковременные замыкания и разрывы сварочной цепи вследствие чего горение дуги и нагрев металла происходят в течение коротких промежутков времени и образуется сварочная ванна небольших размеров. Это позволяет наплавлять детали малых диаметров. Наплавка ведется в струе охлаждающей жидкости или пены выполняющей также функции защитной среды. Этот способ применяется преимущественно при восстановлении пальцев валов осей и других аналогичных изделий.
Напыление – это высокопроизводительный процесс обладающий рядом преимуществ: незначительное влияние на подложку возможность нанесения покрытия на крупногабаритные детали. Применяется для восстановления рабочих поверхностей типа “тело вращение” и “плоская поверхность” с величиной износа от долей миллиметра до десятка миллиметра для нанесения износостойких и защитных покрытий с особыми свойствами. Чаще всего напыление используется для восстановления цапф и других посадочных поверхностей валов.
Список использованных источников
Курмаз Л.В. Скойбеда А.Т. Детали машин. Проектирование. Учебное пособие.-Мн.:Технопринт2001.
Дунаев П.Ф. Леликов О.П. Конструирование узлов и деталей машин: учебное пособие для ВУЗов. – М.: Высшая школа 1985.
Кузьмин А.В. Чернин И.М. Козинцов Б.С. Расчеты деталей машин. Справочное пособие.-Мн.: «Вышэйшая школа» 1986.
Анурьев В. И. Справочник конструктора-машиностроителя. В 3–х томах. –М.: Машиностроение 1979.
Детали машин в примерах и задачах Под ред. С.Н. Ничипорчика. – Мн.: Вышэйшая школа 1981.
Горбацевич А.Ф. Шкред В.А. Курсовое проектирование по технологии машиностроения. – Минск: Выш. шк. 1983. – 256 с.
+Корпус.cdw

Обработку мест под головки болтов (гаек) выполнить до
Формовочные уклоны - 3
Литейные радиусы - 3
Неуказанные предельные отклонения размеров: охватываемых -
Поверхность корпуса очистить и красить маслостойкой
Рекомендуемые чертежи
- 14.09.2015
- 14.09.2015
- 14.09.2015