Проектирование редуктора согласно схеме и данным




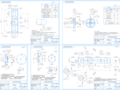
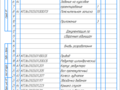
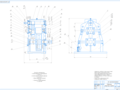
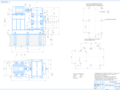
- Добавлен: 24.01.2023
- Размер: 549 KB
- Закачек: 0
Описание
Проектирование редуктора согласно схеме и данным
Состав проекта
![]() |
![]() ![]() ![]() ![]() |
![]() ![]() ![]() ![]() |
![]() ![]() ![]() ![]() |
![]() ![]() ![]() |
![]() ![]() ![]() ![]() |
![]() ![]() ![]() ![]() |
Дополнительная информация
ПРИВОД.cdw

деталировка.frw

сборка.cdw

КОРПУС.cdw

ВЕДОМОСТЬ КП.cdw

Рекомендуемые чертежи
Свободное скачивание на сегодня
Другие проекты
- 22.08.2014