Расчет и проектирование двухступенчатого редуктора по соосной схеме




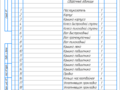

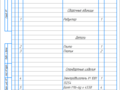

- Добавлен: 24.01.2023
- Размер: 4 MB
- Закачек: 0
Описание
Состав проекта
![]() |
![]() |
![]() ![]() ![]() |
![]() |
![]() ![]() ![]() ![]() |
![]() |
![]() ![]() ![]() |
![]() ![]() ![]() |
![]() ![]() ![]() |
![]() ![]() ![]() ![]() |
![]() ![]() ![]() ![]() |
![]() |
![]() |
![]() |
![]() ![]() ![]() ![]() |
![]() |
![]() ![]() ![]() |
![]() ![]() ![]() ![]() |
![]() ![]() ![]() ![]() |
![]() |
![]() ![]() ![]() ![]() |
![]() |
![]() |
![]() ![]() ![]() ![]() |
![]() |
![]() ![]() ![]() ![]() |
![]() ![]() ![]() ![]() |
![]() |
![]() |
![]() ![]() ![]() ![]() |
![]() |
![]() ![]() ![]() ![]() |
![]() |
Дополнительная информация
СОДЕРЖАНИЕ.docx
1 Определение КПД редуктора . .. 8
2 Определение требуемой мощности электродвигателя 8
3 Выбор электродвигателя 8
Определение передаточного числа редуктора и передаточных
чисел по ступеням ..9
1 Определение частот вращения зубчатых колёс . .9
2. Определение крутящих моментов на валах редуктора .. .9
Выбор материала зубчатых колес .. 10
Расчет допускаемых напряжений колес закрытой передачи . 11
1 Расчет допускаемых контактных напряжений . . .11
2 Расчет допускаемых напряжений изгиба . . . 12
Составление исходных данных для ввода в ПЭВМ . 15
Анализ результатов вариантных расчетов на ПЭВМ и
выбор оптимального варианта .. 16
Геометрический расчет передач редуктора 18
Проверочный расчет на прочность зубчатой передачи .20
1. По контактным напряжениям 20
2. По напряжениям изгиба 21
Проектирование валов редуктора . ..23
1. Быстроходный вал .23
2. Промежуточный вал 24
3. Тихоходный вал . 25
Геометрический расчет открытой передачи ..26
Проверочный расчет .. ..26
1 По контактным напряжениям ..26
2 По напряжениям изгиба . ..27
Расчет открытой цилиндрической зубчатой передачи 28
Конструирование зубчатых колес закрытой передачи .28
1 Определение размеров зубчатого колеса промежуточного вала ..28
2 Определение размеров зубчатого колеса тихоходного вала 29
Проверочный расчет промежуточного вала . . ..29
1. Исходные данные . . .. .29
2. Определение опорных реакций .. .. .30
3. Построение эпюр изгибающих моментов .. . .30
Проверка на статическую прочность 31
Расчет подшипников на заданный ресурс ..32
Проверка промежуточного вала на усталостную прочность .. .. 33
1 Сечение вала с шпоночным пазом .. 34
2 Ступенчатый переход с галтелью . 37
Расчет соединений . .39
1 Шпоночные соединения . . .39
1.1. Подбор шпонки для цилиндрического колеса. быстроходной ступени . 39
1.2. Подбор шпонки для цилиндрического колеса. тихоходной ступени 39
Конструирование корпусных деталей и крышек подшипников 40
1 Определение толщины стенки редуктора 40
2 Конструктивное оформление фланцев корпуса и крышки редуктора . . 41
3. Конструктивное оформление приливов для подшипниковых гнезд .. . .41
4 Крепление крышки редуктора к корпусу 41
5 Конструирование крышек подшипников 42
6.1. Крышки для быстроходного и помежуточног вала .42
6.2. Крышки для промежуточного вала . . .42
6.3. Крышки для тихоходного вала .. . .42
7. Фиксирование крышки относительно корпуса ..43
8. Конструктивное оформление опорной части корпуса . .. 43
9 Оформление прочих конструктивных элементов корпуса .. ..44
10. Конструктивное оформление крышки люка ..45
11. Смазочные устройства ..45
Проектирование чертежа приводной станции . .47
Чертеж2.cdw

Плоскость разьема покрыть щелочным
Мр-ТУ 38-5-6060-65.
Применение прокладок не допускается.
После сборки в редуктор залить
индустриальное масло И-Г-А-32.
Необработанные наружные поверхности
редуктора покрыть серой
эмалью ПФ-115 ГОСТ-6465-76.
Необработанные поверхности
находящихся в масляной ванне
красить маслостойкой красной эмалью.
Техническая характеристика
Наибольший вращающий
момент на выходном валу
Передаточное число редуктора - 27
Уфимский государственный авиационный технич.doc
ПОЯСНИТЕЛЬНАЯ ЗАПИСКА
(обозначение документа)
ДМ.doc
Рисунок 1.1 Кинематическая схема редуктора
Вращающий момент на выходном конце тихоходного вала Тт=760 H·м
Частота вращения на выходном конце тихоходного вала nт=75 обмин
Ресурс Lh=7500 часов
Массовое производство
Подбор электродвигателя
1. Определение КПД редуктора
где – КПД зубчатой цилиндрической передачи;
– КПД подшипников качения;
2. Определение требуемой мощности электродвигателя
Мощность на выходном валу
3. Выбор электродвигателя
Подбираем электродвигатель 2 таблица 24.9. с мощностью Pэд≥Pp. Выбираем асинхронный двигатель 112М22895 мощностью Pр=75 кВт с синхронной частотой вращения nc=3000 с-1.
Определение передаточного числа редуктора и передаточных чисел по ступеням
Быстроходная ступень:
Фактическое передаточное число
1. Определение частот вращения зубчатых колес
Частота вращения шестерни быстроходной ступени
Частота вращения колеса быстроходной ступени и шестерни тихоходной ступени
Частота вращения колеса тихоходной ступени
2. Определение крутящих моментов на валах редуктора
Момент на валу колеса тихоходной ступени:
Момент на валу колеса быстроходной ступени (на валу шестерни тихоходной ступени):
Момент на валу шестерни быстроходной степени
Выбор материала и вида термообработки зубчатых колес
В условиях среднесерийного производства целесообразно применять зубчатые колеса с высокотвердыми зубьями. Принимаем для зубчатых колес Сталь 40 а в качестве технологического упрочнения – улучшение и закалка ТВЧ.. При этом материал имеет следующие механические характеристики 3 таблица 2.2:
твердость сердцевины шестерни и колеса: 269 302 HB
твердость поверхности зубьев шестерни и колеса: 48 53HRС или 461 521 HB.
Расчет допускаемых напряжений колес закрытой передачи
1. Контактных допускаемых напряжений
Расчет контактных допускаемых напряжений при проектировочном расчете ведем по формуле 3:
– предел контактной выносливости 3 таблица 2.2:
SH – коэффициент безопасности 3:
ZH – коэффициент долговечности 3:
NHG – базовое число циклов перемены напряжений 3:
NHE – эквивалентное число циклов перемены напряжений 3:
H – коэффициент эквивалентности 3 таблица 23:
с – число зацеплений зуба за один оборот:
n – частота вращения того зубчатого колеса по материалу которого определяют допускаемые напряжения обмин:
Lh – время работы передачи в часах (ресурс):
По формуле (4.6) находим эквивалентное число циклов перемены напряжений
для шестерни быстроходной передачи:
для колеса быстроходной передачи:
для шестерни тихоходной передачи:
для колеса тихоходной передачи:
По формуле (4.4) находим коэффициент долговечности:
Из (4.1) находим допускаемые контактные напряжения
За допускаемое контактное напряжение принимаем наименьшее из значений для быстроходной и тихоходной передачи:
2. Допускаемых напряжений изгиба
Расчет допускаемых напряжений изгиба при проектировочном расчете ведем по
– предел выносливости зуба по напряжениям изгиба 3 таблица 2.2:
SF – коэффициент безопасности 3:
YA – коэффициент учитывающий влияние двустороннего приложения нагрузки 3:
YN – коэффициент долговечности 3:
NFG – базовое число циклов перемены напряжений 3:
NFE – эквивалентное число циклов перемены напряжений 3:
F – коэффициент эквивалентности 3 таблица 23:
По формуле (4.29) находим эквивалентное число циклов перемены напряжений
По формуле (4.27) находим коэффициент долговечности:
Из (4.23) находим допускаемые напряжения изгиба
За допускаемое напряжение изгиба принимаем наименьшее из значений для быстроходной и тихоходной передачи:
Составление исходных данных для ввода в ПЭВМ
Момент на колесе тихоходной передачи редуктора находим по формуле 1:
где – КПД подшипников качения;
Передаточное отношение редуктора 1:
Допускаемые контактные напряжения 1:
Коэффициенты относительной ширины колес 1:
Эквивалентное время работы 1:
где коэффициент Н определяем по таблице 4 таблица 8.10
Анализ результатов вариантных расчетов на ПЭВМ и выбор оптимального варианта
Из диаграммы показывающей изменение массы и объема в зависимости от рассматриваемого варианта следует что наиболее оптимальным является вариант №3.
Геометрический расчет передач редуктора
Принимаем суммарный коэффициент смещения Х1+Х2=ХΣ=0 тогда
делительные диаметры:
диаметры окружности вершин зубьев:
диаметры окружности впадин зубьев:
коэффициент перекрытия:
Проверочный расчет на прочность зубчатой передачи
1. По контактным напряжениям
Моменты на валах редуктора:
Контактное напряжение на шестерне быстроходной и тихоходной ступени:
коэффициент внутренней динамической нагрузки определим по таблице 4 таблица 8.3:
коэффициент концентрации нагрузки определим по графикам 4 рисунок 8.15:
Контактное напряжение на колесе быстроходной и тихоходной ступени:
2. По напряжениям изгиба
Напряжение изгиба на шестерне быстроходной и тихоходной ступени:
окружное усилие в зацепление колес:
коэффициент КНV определим по таблице 4 таблица 8.3:
коэффициент КН определим по графикам 4 рисунок 8.15:
коэффициент формы зуба 4 рисунок 8.20:
Напряжение изгиба на колесе быстроходной и тихоходной ступени:
коэффициент КFV определим по таблице 4 таблица 8.3:
коэффициент КF определим по графикам 4 рисунок 8.15:
Напряжение изгиба на колесе быстроходной ступени:
Проектирование валов редуктора
расчетные формулы берем из таблицы 3 таблица 3.1
Первая ступень вала:
Вторая ступень вала:
Третья ступень вала:
определить графически;
Четвертая ступень вала:
2. Промежуточный вал
определить графически
Седьмая ступень вала:
Шестая ступень вала:
Геометрический расчет открытой передачи3стр.39.
Определим модуль зацепления по формуле:
Геометрические размеры шестерни:
делительный диаметр: ;
диаметр вершин зубьев: ; (10.2)
диаметр впадин зубьев: ;
1 По контактным напряжениям:
Контактное напряжение на колесе тихоходной ступени
коэффициент КH определим по таблице 4 таблица 8.3:
коэффициент КHV определим по графикам 4 рисунок 8.15:
2 По напряжениям изгиба:
Напряжение изгиба на колесе тихоходной ступени
коэффициент КF определим по таблице 4 таблица 8.3:
коэффициент КFV определим по графикам 4 рисунок 8.15:
Расчет открытой цилиндрической зубчатой передачи 3 стр 38
Z3 – число зубьев шестерни открытой передачи;
- коэффициент ширины зубчатого венца колеса относительно модуля
- допускаемое напряжение изгиба зубьев шестерни;
Твых –момент на шестерне;
Делительный диаметр ;
диаметр вершин зубьев ;
диаметр впадин зубьев ;
Конструирование зубчатых колес закрытой передачи
1 Определение размеров зубчатого колеса промежуточного вала .
Для колеса промежуточной ступени.
Ширина торцов зубчатого венца:
Толщина диска колес:
Округляем до стандартного значения
2 Определение размеров зубчатого колеса тихоходного вала .
Для колеса тихоходной ступени.
Толщина диска колес:
Проверочный расчет промежуточного вала.
Заменяем конструкцию вала расчетной схемой с обозначением всех активных и реактивных сил действующих на вал
Силы действующие на вал:
Расстояния возьмем из сборочного чертежа:
2. Определение опорных реакций.
3. Построение эпюр изгибающих моментов
Суммарный изгибающий момент:
Проверка на статическую прочность
Построив эпюры видим что наибольший изгибающий момент проходит через сечение в т.С: для него и произведем расчет.
Касательные напряжения:
Оценку статической прочности проводят по энергетической теории прочности:
Допускаемые напряжения зависят от механических характеристик материала и коэффициента запаса прочности n:
Условие прочности выполняется.
Расчет подшипников на заданный ресурс.
Расчет будем производить для наиболее нагруженной опоры т.е. для опоры Д.
Предварительно был назначен подшипник шариковый радиальный легкой серии (по ГОСТ 8338-75 № 208 для которого грузоподъемность Сr = 32000Н Cr0 = 17800H.
Определим эквивалентную нагрузку
V = 1 - коэффициент вращения так как вращается внутреннее кольцо подшипника
Х – коэффициент радиальной нагрузки
Y – коэффициент осевой нагрузки
КБ = 10 - коэффициент безопасности для спокойной нагрузки без толчков
KT = 10 - температурный коэффициент при t до 100 °С.
Коэффициент осевого нагружения е = 0 при
- так как принимаем Х=1 а Y=0.
С учетом полученных данных:
Определим расчетный ресурс:
где к - показатель степени равен 3 для шариковых подшипников
а1=1 – коэффициент долговечности для вероятности безотказной работы 90%.
а23 = 08 – для шариковых подшипников.
Подшипник проходит по заданному ресурсу
Проверка промежуточного вала на усталостную прочность
Для каждого из предположительно опасных сечений определяем коэффициент:
где и – коэффициенты запаса по нормальным и касательным напряжениям определяемые по зависимостям:
где и – амплитуды напряжений цикла; и – средние напряжения цикла; и – коэффициенты чувствительности к асимметрии цикла напряжений для рассматриваемого сечения.
В расчётах валов принимаем что нормальные напряжения изменяются по симметричному циклу: и а касательные напряжения – по отнулевому циклу: и .
Пределы выносливости вала в опасном сечении определяем по формулам:
где и – пределы выносливости гладких образцов при симметричном цикле изгиба и кручения.
Значения коэффициентов снижения предела выносливости вычисляем по зависимостям:
1 Сечение вала с шпоночным пазом
Концентраторами напряжения являются шпоночный паз и натяг. Расчёт ведём с использованием табличных данных [2]:
Характеристики материала 40Х:
(при диаметре вала для изгиба и кручения легированной стали 40Х)
(т.к. поверхность вала выполнена без упрочнения).
Для шпоночного паза при выполнении паза концевой фрезой и : .
Для назначенного натяга при диаметре и :
Получаем для шпоночного паза:
Принимаем для данного сечения большие значения коэффициентов снижения предела выносливости от обоих концентраторов напряжений:
Тогда пределы выносливости вала в сечении 1-1 равны:
Напряжения в данном сечении равны:
где – результирующий изгибающий момент; – крутящий момент; и – моменты сопротивления вала при изгибе и кручении.
Таким образом получаем:
Коэффициент запаса прочности S должен быть не меньше 15 – 25 в зависимости от ответственности конструкции и последствий разрушения вала. Так как условие прочности для данного сечения выполняется.
2 Ступенчатый переход с галтелью
Концентратором напряжений является ступенчатый переход с галтелью:
(при шероховатости поверхности и )
Для ступенчатого перехода с галтелью :
Значения коэффициентов снижения предела выносливости:
Тогда пределы выносливости вала в сечении 2-2 равны:
1 Шпоночные соединения.
1.1. Подбор шпонки для цилиндрического колеса. быстроходной ступени
b h = 14 9 для d=47мм (ГОСТ 23360 -78).
Рис 8.1 Шпонка призматическая
Глубина шпоночного паза:
Определяем рабочую длину шпонки по формуле
где T- крутящий момент на валу
=130 180 МПа допускаемое напряжение на смятие.
1.2. Подбор шпонки для цилиндрического колеса. тихоходной ступени
b h = 20 12 для d=70 мм (ГОСТ 23360 -78).
Конструирование корпусных деталей и крышек подшипников.
Корпусные детали имеют довольно сложную форму поэтому их получим методом литья. Для изготовления корпусных деталей используем чугун СЧ15. Корпусная деталь состоит из стенок ребер бобышек фланцев и других элементов соединенных в единое целое. При конструировании корпусной детали стенки следует выполнять одинаковой толщины.
1 Определение толщины стенки редуктора.
Для редукторов толщину стенки отвечающую требованиям технологии литья необходимой прочности и жесткости корпуса вычисляют по формуле:
d = 13× принимаем толщину стенки редуктора d = 8 мм
2 Конструктивное оформление фланцев корпуса и крышки редуктора.
Конструктивные элементы:
f = (04 05)×d1= (04 05)× 8 = 4 мм
b = 15×d =15×8 = 12 мм
b1 = 15×d1 =15× = 12мм
l = (2 22)×d = (2 22)×8 = 16 мм
3. Конструктивное оформление приливов для подшипниковых гнезд.
l1 l2 - длина подшипниковых гнезд определяется конструктивно.
d = 8 мм - толщина стенки редуктора.
h1 = 05×d = 05× 8 = 4 мм
4 Крепление крышки редуктора к корпусу.
d = 125 × 10 мм - диаметр стяжного болта.
d = 125 × = 924 мм принимаем d = 10 мм
Конструктивные элементы.
K = 235×d = 235×10 = 235 мм
C = 11×d = 11×10 = 11 мм
D = 2×d = 2×10 = 20 мм
h' - определяют графически исходя из условия размещения головки болта на плоской опорной поверхности.
5 Конструирование крышек подшипников.
В данном редукторе используем закладные крышки.
6.1. Крышки для быстроходного и помежуточног вала.
6.2. Крышки для промежуточного вала.
d3 = H + 08×d = 8 + 08×6= 13 мм;
6.3. Крышки для тихоходного вала.
d1 = 12×d = 12×7= 84 мм;
7. Фиксирование крышки относительно корпуса.
Необходимая точность фиксирования достигается штифтами. Используются два конических штифта с внутренней резьбой которые устанавливаются по срезам углов крышки.
Поверхности сопряжения корпуса и крышки для их плотного прилегания шабрят и шлифуют. При сборке узла эти поверхности для лучшего уплотнения покрывают тонким слоем герметика.
8. Конструктивное оформление опорной части корпуса.
Опорная поверхность выполнена в виде четырех расположенных в местах установки болтов платиков. Такое расположение позволяет снизить расход металла и уменьшает время обработки опорной поверхности корпуса снижает нагрузки на резьбовые детали.
Диаметр винта крепления редуктора к раме:
Число винтов z=4 при .
9 Оформление прочих конструктивных элементов корпуса.
Для подъема и транспортирования крышки корпуса и редуктора в сборе предусмотрены проушины.
10. Конструктивное оформление крышки люка.
L - длина крышки назначается конструктивно.
d = (0010 0012)×L ³ 2 мм
d = (0010 0012)×L = (0010 0012)×150 = 2 мм - толщина листа.
d d1 = 6 мм - диаметр винтов крепления крышки люка где d1 =7 мм - толщина стенки крышки редуктора. h1 04×d1 = 04×7 = 3 мм
11. Смазочные устройства
При работе передач продукты изнашивания постепенно загрязняют масло. С течением времени оно стареет свойства его ухудшаются. Браковочными признаками служат увеличенное кислотное число повышенное содержание воды и наличие механических примесей. Поэтому масло залитое в корпус редуктора или коробки передач периодически меняют. Для замены масла в корпусе предусматривают сливное отверстие закрываемое пробкой с цилиндрической или конической резьбой.
Цилиндрическая резьба не создает надежного уплотнения. Поэтому под пробку с цилиндрической резьбой ставят уплотняющие прокладки из фибры алюминия паронита. Для этой цели применяют также кольца из маслобензостойкой резины которые помещают в канавки глубиной t чтобы они не выдавливались пробкой при ее завинчивании.
Для наблюдения за уровнем масла в корпусе устанавливают маслоуказатель.
При длительной работе в связи с нагревом воздуха повышается давление внутри корпуса. При интенсивном тепловыделении это приводит к просачиванию масла через уплотнения и стыки. Чтобы избежать этого внутреннюю полость корпуса сообщают с внешней средой путем установки отдушин в его верхних точках.
Проектирование чертежа приводной станции
При монтаже приводов состоящих из электродвигателя и редуктора должны быть выдержаны определенные требования точности относительного положения узлов. Для этого узлы привода устанавливают на сварных рамах.
В случае мелкосерийного производства экономически выгоднее применять сварные рамы из элементов сортового проката: швеллеров уголков полос листов.
Конфигурацию и размеры рамы определяют тип и размеры редуктора и электродвигателя. Расстояние между ними зависит от подобранной соединительной муфты.
По каталогу электродвигателей (табл. 24.7 [1]) определяют размеры опорных поверхностей двигателя а по чертежу редуктора - размеры . Для создания базовых поверхностей под двигатель и редуктор на раме размещают платики в виде узких полос.
Ширину и длину платиков на раме принимают большими чем ширина и длина опорных поверхностей электродвигателя и редуктора.
Основные размеры рамы:
Н=(008 010)L=32 40 мм.
Подбираем ближайший больший размер швеллера:
Раму при сварке сильно коробит поэтому все базовые поверхности обрабатывают после сварки. Высоту платиков после их обработки принимают h=5 6мм.
Швеллеры располагают полками наружу. В полках рамы высверлены отверстия на проход стержня болта. На внутреннюю поверхность полки накладывают косые шайбы выравнивающие опорную поверхность под головками гаек (рис. 11.1).
Для крепления рамы к полу цеха применяют фундаментальные болты с коническим концом (рис. 11.2). Фундаментальные болты установлены в скважины просверленные в полу твердосплавным инструментом. Используем болты М16 2 по ГОСТ 24379.1-80.
Вследствие погрешностей изготовления деталей и погрешностей сборки валы соединяемые муфтой как правило имеют смещения: радиальное угловое (перекос) и осевое Радиальные смещения уменьшают выверкой положения узлов на базовых плоскостях. В этом случае возможное радиальное смещение осей зависит от квалификации сборщиков. Осевое смещение уменьшают выверкой осевого положения валов.
В данном проекте применена муфта упругая втулочно-пальцевая (МУВП) ГОСТ 21424-93. Эти муфты получили широкое распространение благодаря относительной простоте конструкции и удобству замены упругих элементов. Однако их характеризует невысокая компенсирующая способность:
- радиальные смещения-010 .015мм;
Размеры муфты подбираем по атласу (стр. 303 [5]).
Проектирование приводов с цилиндрическими редукторами: Методические указания к выполнению расчетно-графической работы по дисциплине «Детали машин и основы конструирования» С.С. Прокшин А.А. Сидоренко В.А. Федоров С.М. Минигалеев. – Уфа: Уфимский государственный авиационный технический университет 2006. – 58 с.
Конструирование узлов и деталей машин: учебное пособие для студентов высших учебных заведений П.Ф. Дунаев О.П. Леликов. – 9-е изд. прераб. и доп. – М.: Издательский центр «Академия» 2006. – 496 с.
Расчет и конструирование одноступенчатого зубчатого редуктора: учебное пособие М.Ш. Мигранов О.Ф. Ноготков А.А. Сидоренко Л.Ш. Шустер. – М.: издательство МАИ 2002. – 125 с.
Иванов М.Н. Детали машин: Учебник для студентов высших технических учебных заведений. – 5-е изд. перераб. – М.: Высшая школа 1991. – 383 с.
Эскизы стандартных изделий
Болт с уменьшенной шестигранной головкой ГОСТ 7796-70
Винт М814 ГОСТ 17473-80.
Манжеты резиновые армированные 1-3558-1 и 1-6590-1 ГОСТ 8752-79.
Подшипники шариковые радиальные однорядные ГОСТ 8338-75.
Шайба пружинная 16 ГОСТ 6402-70.
Штифт конический с внутренней резьбой класс точности В
Спецификация на приводную станцию.spw

Привод общего назначения
Болт М16-6g x 65.58
Винт М10х90 ГОСТ 1491-80
Гайка М16-6Н.5 ГОСТ 5915-70
Шайба 14 ГОСТ 11371-78
Шайба 16Н ГОСТ 6402-70
Чертеж.cdw

Чертеж2.cdw

Плоскость разьема покрыть щелочным
Мр-ТУ 38-5-6060-65.
Применение прокладок не допускается.
После сборки в редуктор залить
индустриальное масло И-Г-А-32.
Необработанные наружные поверхности
редуктора покрыть серой
эмалью ПФ-115 ГОСТ-6465-76.
Необработанные поверхности
находящихся в масляной ванне
красить маслостойкой красной эмалью.
Техническая характеристика
Наибольший вращающий
момент на выходном валу
Передаточное число редуктора - 27
Спецификация на приводную станцию.spw

Привод общего назначения
Электродвигатель IM 1081
Болт М16-6g x 65.58
Винт М10х90 ГОСТ 1491-80
Гайка М16-6Н.5 ГОСТ 5915-70
Шайба 14 ГОСТ 11371-78
Шайба 16Н ГОСТ 6402-70
Чертеж.cdw

Приводная станция.cdw

Допустимое смещение валов электродвигателя и редуктора
Допускаемый перекос валов мммм
Техническая характеристика электродвигателя
Частота вращения приводного барабана 2850 обмин
Спецификация на редуктор.spw

Колесо быстроходной ступени
Колесо тихоходной ступени
Кольцо маслоотбойное
Уплотняющая прокладка
Винт М6 х 14 ГОСТ 17473-80
Винт М12 х 65 ГОСТ 7805-70
Шайба 12 Н ГОСТ 6402-70
Мaнжета 1-60 х 65-1 ГОСТ 8752-79
Подшипник 205 ГОСТ 8338-75
Подшипник 208 ГОСТ 8338-75
Подшипник 212 ГОСТ 8338-75
Штифт 8 х 26 ГОСТ 9464-79
Штифт 8 х 35 ГОСТ 9464-79
Шпонка 12 х 8 х 66 ГОСТ 23360-78
Шпонка 10 х 8 х 45 ГОСТ 23360-78
Шпонка 14 х 9 х 24 ГОСТ 23360-78
Шпонка 6 х 6 х 18 ГОСТ 23360-78
ЭПЮРЫ.cdw

Приводная станция.cdw

Допустимое смещение валов электродвигателя и редуктора
Допускаемый перекос валов мммм
Техническая характеристика электродвигателя
Частота вращения приводного барабана 2850 обмин
Спецификация на редуктор.spw

Колесо быстроходной ступени
Колесо тихоходной ступени
Кольцо маслоотбойное
Уплотняющая прокладка
Винт М6 х 14 ГОСТ 17473-80
Винт М12 х 65 ГОСТ 7805-70
Шайба 12 Н ГОСТ 6402-70
Мaнжета 1-60 х 65-1 ГОСТ 8752-79
Подшипник 205 ГОСТ 8338-75
Подшипник 208 ГОСТ 8338-75
Подшипник 212 ГОСТ 8338-75
Штифт 8 х 26 ГОСТ 9464-79
Штифт 8 х 35 ГОСТ 9464-79
Шпонка 12 х 8 х 66 ГОСТ 23360-78
Шпонка 10 х 8 х 45 ГОСТ 23360-78
Шпонка 14 х 9 х 24 ГОСТ 23360-78
Шпонка 6 х 6 х 18 ГОСТ 23360-78
Пром. вал.cdw

Неуказанные предельные отклонения размеров:
валы- по остальные по
Нормальный исходный контур
Коэффициент смещения
Сталь 40XH ГОСТ 4543-71