Расчёт горизонтального двухступенчатого цилиндрического редуктора




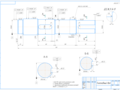
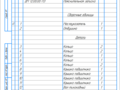
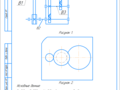
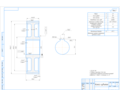
- Добавлен: 04.11.2022
- Размер: 772 KB
- Закачек: 0
Описание
Курсовой проект - Расчёт горизонтального двухступенчатого цилиндрического редуктора
Состав проекта
![]() |
![]() ![]() ![]() ![]() |
![]() ![]() ![]() |
![]() ![]() ![]() ![]() |
![]() ![]() ![]() ![]() |
![]() ![]() ![]() ![]() |
![]() ![]() ![]() ![]() |
Дополнительная информация
Chertezh_Tikhokhodnogo_vala.cdw

Размер обеспеч. инструмент.
Неуказанные предельные отклонения размеров
курсовая.docx
ЭНЕРГЕТИЧЕСКИЙ И КИНЕМАТИЧЕСКИЙ РАСЧЕТ ПРИВОДА5
РАСЧЕТ ОТКРЫТОЙ КЛИНОРЕМЕННОЙ ПЕРЕДАЧИ.7
1 Расчет тихоходной ступени12
2 Расчет быстроходной ступени20
ПРЕДВАРИТЕЛЬНЫЙ РАСЧЕТ ВАЛОВ27
1 Расчет диаметров быстроходного вала:27
2. Расчет диаметров промежуточного вала:28
3 Расчет диаметров тихоходного вала:28
1. Определение сил в зацеплении30
1.1 Быстроходная ступень30
1.2 Тихоходная ступень30
1.3 Консольные силы31
РАСЧЕТ ПОДШИПНИКОВ50
2 Промежуточный вал.51
1 Соединение колеса на тихоходном валу54
2 Соединение колеса на промежуточном валу54
3 Соединение муфты на тихоходном валу54
4 Соединение шкива на быстроходном валу54
КОНСТРУИРОВАНИЕ РЕДУКТОРА.55
1 Уплотнение подшипниковых узлов55
2 Конструирование корпуса и крышки55
5 Конструирование корпусных деталей и крышек57
СПИСОК ЛИТЕРАТУРЫ:60
Проектируемый в данной работе привод состоит из электродвигателя 4A100L4У3 мощности 4 кВт горизонтального двухступенчатого цилиндрического редуктора косозубая на первой и второй ступенях с моментом на тихоходном валу 71178 Н·м и передаточным отношением 1309. Выходной вал редуктора соединен с приводом упругой с торообразной оболочкой муфтой. Ременная передача передает момент от вала двигателя к быстроходному валу редуктора. Двигатель и редуктор крепятся к общей раме. Она сварная состоит из швеллеров и крепится на бетонное основание. Привод должен обеспечить передачу крутящего момента от электродвигателя к исполнительному устройству с минимальными потерями и заданной угловой скоростью на выходном валу редуктора.
ЭНЕРГЕТИЧЕСКИЙ И КИНЕМАТИЧЕСКИЙ РАСЧЕТ ПРИВОДА
Подбираем двигатель:
Выбираем тип двигателя из справочника: Pдв. = 4 кВт; nдв. =1500 обмин
Определение передаточного числа:
Определение скоростей на каждом валу:
Определение моментов и мощностей:
Частота Вращения nмин-1
Момент расчетный T Н·м
РАСЧЕТ ОТКРЫТОЙ КЛИНОРЕМЕННОЙ ПЕРЕДАЧИ.
1. Выбор сечения ремня:
Выбираем ремень нормального сечения А
2. Согласно табл. 5.4 2 минимально допустимый диаметр ведущего шкива: d1min = 90мм
3. Определяем расчетный диаметр ведущего шкива d1:
d1= 3 4 = 3 4 = 823 1097мм.
По нормальному ряду принимаем d1 = 100 мм.
4. Определяем диаметр ведомого шкива d2:
d2 = d1*u*(1-) =100*3*(1-002) = 294 мм
По нормальному ряду принимаем d2 = 315 мм.
– коэффициент скольжения.
5. Определяем фактическое передаточное число и проверяем его отклонение от заданного u:
6. Определяем ориентировочное межосевое расстояние а:
а ≥ 055(d1+d2)+h = 055*(100+315)+8 = 2363 мм
где – высота сечения клинового ремня (см. табл. К31 2);
По нормальному ряду принимаем a = 238 мм.
7. Определяем расчетную длину ремня
Полученное значение принимаем из стандартных значений по табл. К31 2:
8. Уточняем значение межосевого расстояния по стандартной длине:
9. Определяем угол обхвата ремнем ведущего шкива :
10. Определяем скорость ремня
11. Определяем частоту пробегов ремня
12. Определяем допускаемую мощность передаваемую одним клиновым ремнем [Pп]:
[Pп]= [Pо]*Сp*Cα*Cl*Cz=160*09*089*1*085=109
где [Pп]= 160 кВт – допускаемая приведённая мощность передаваемая одним клиновым ремнём С – поправочные коэффициенты выбираются по табл. 5.2 2
13. Определяем количество клиновых ремней z:
14. Определяем силу предварительного натяжения одного клинового ремня
15. Определяем окружную силу передаваемую комплектом клиновых ремней
16. Определяем силы натяжения ведущей F1 и ведомой F2 ветвей:
Fl = F0+ = 75+ =13875 H
F2 = F0 - = 75 - =1125 H
17. Определяем силу давления ремней на вал
= 2Fo z sin = 2*75*4*sin = 5563 H
18.Проверяем прочность одного клинового ремня по максимальным напряжениям в сечении ведущей ветви :
а)Напряжения растяжения:
А=81 мм2 – площадь сечения ремня по табл. К31 2
б)Напряжения изгиба:
u = Eu = 90* = 72 МПа
Еи = 80 100 – модуль продольной упругости при изгибе
в)Напряжения от центробежных сил:
ρ =1250 1400 кгм3 – плотность материала ремня.
max=171+72+0077=8987 МПа 10МПа
Условие прочности соблюдается.
Параметры клиноременной передачи Таблица № 2
Клиновой нормального сечения
Межосевое расстояние а мм
Угол обхвата ведущего шкива α1 °
Частота пробегов ремня U с-1
Диаметр ведущего шкива d1 мм
Диаметр ведомого шкива d2 мм
Максимальное напряжение Нмм2
Предварительное натяжение ремня F0 Н
Сила давления ремней на вал Fоп Н
1 Расчет тихоходной ступени
Исходные данные: Вращающий момент на тихоходном валу T4=71178Нм; угловая скорость шестерни тихоходной ступени 2=127 рад-1 угловая скорость колеса тихоходной ступени 3=399 рад-1 передаточное число тихоходной ступени редуктора u=318
1.1. Выбор материала
1.1.1 Выбор материала колес редуктора:
Так как в задании нет особых требований в отношении габаритов передачи выбираем материал со средними механическими характеристиками: для шестерни сталь 40XH термообработка улучшение твердость HB 269 302 при диаметре заготовки до D=200 мм для колеса сталь 40XH термообработка – улучшение твердость HB 235 262 при диаметре заготовки до D=315мм.
1.1.2 Допускаемые контактные напряжения
1.1.2.1 а) коэффициент долговечности для зубьев шестерни:
из таблицы 3.3 [1] =165
Т.к. меньше то принимаем
б) коэффициент долговечности для зубьев колеса:
где =573Lh=573399=27
из таблицы 3.3 [1] =10
Т.к. меньше то принимаем=1
1.1.2.2 Допускаемое напряжение:
а) шестерня []H01=18HBср+67=18+67=5809
б) колесо []H02=18HBср+67=182485+67=5143
1.1.2.3 Допускаемое контактное напряжение:
а) шестерня []H1=KHL1[]H01=5809
б) колесо []H2=KHL2[]H02=5143
выбираем []H=[]H2=5143 Нмм2
1.1.3 Допускаемые напряжения изгиба:
1.1.3.1 а) коэффициент долговечности для зубьев шестерни:
Т.к. меньше то принимаем =1
1.1.3.2 Допускаемое напряжение:
а) шестерня []F01=1.03HBср=103=294
б) колесо []F02=1.03HBср=1032485=256
1.1.3.3 Допускаемое контактное напряжение:
а) шестерня []F1=KFL1[]F01=294
б) колесо []F2=KFL2[]F02=256
выбираем []F=[]F2=256Нмм2
Механические характеристики материалов зубчатой передачи Таблица №3
1.2 Проектный расчет
1.2.1 Определяем межосевое расстояние по формуле 2 с.61:
Где: Кa=43 так как колесо косозубое
ba=036 – коэффициент ширины венца шестерни
КН =1- коэффициент неравномерности распределения нагрузки по длине зуба для колёс из прирабатывающихся металлов и при постоянной нагрузке
T3=Нм – момент вращения на тихоходном валу
UТ=318 – передаточное число тихоходной ступени
Принимаем: аw=170 мм по ГОСТ 6636-69
1.2.2 Определяем модуль передачи m мм:
Принимаем стандартный модуль: =25 мм
1.2.3 Определяем угол наклона зубьев для косозубых передач:
где -ширина венца колеса;
Принимаем из рекомендуемого интервала 8º 16º.
1.2.4 Определяем суммарное число зубьев шестерни и колеса:
1.2.5 Уточняем действительный угол наклона зубьев для косозубых передач:
1.2.6 Определяем число зубьев шестерни:
1.2.7 Определяем число зубьев колеса:
1.2.8 Определяем фактическое передаточное число uф и проверяем его отклонение U от заданного U:
uф= z2z1=101 32 = 316
1.2.9 Определяем фактическое межосевое расстояние для косозубой передачи мм:
1.2.10 Определяем основные геометрические параметры передачи:
da1=d1+2m=81.6+22.5=866 мм
da2=d2+2m=257.7+22.5=262.7 мм
df1=d1-2.4m=81.6-2.42.5=756 мм
df2=d2-2.4m=257.7-2.42.5=251.7 мм
b1=b2+4=612+4=652 мм
1.3 Проверочный расчет
1.3.1 Проверяем межосевое расстояние мм:
1.3.2 Проверяем пригодность заготовок колес: для шестерни Dmin=200 мм что значительно больше da1. Для колеса диаметр заготовки Dmin=315 мм. что значительно больше da2.
1.3.3 Проверяем контактные напряжения Нмм2:
где К = 376 вспомогательный коэффициент для косозубой передачи; 2 с.64
По таблице 4.2 2 с. 64 определяем степень точности которая равна 9
КН =101 - коэффициент учитывающий внутреннюю динамику нагружения таблица 4.3 2 с. 64
КН =1- коэффициент учитывающий неравномерность распределения нагрузки по длине контактных линий для прирабатывающихся зубьев
КН - коэффициент распределения нагрузки между зубьями
КН=115; график 4.2 2 с. 66
1.3.4 Определяем недогруз перегруз передачи:
1.3.5 Проверяем напряжениям изгиба зубьев шестерни и колеса:
где YF2=3.60 при Zv2=Z2cos3=101cos312.06=108
Y =1-100=1-12.83100=09139
KFα=1 при 9-й степени точности колеса;
KF =1 – для прирабатывающихся колес;
KFv=111 – при 9-й степени точности и v=1.64 мс
где YF1=3.75 при Zv1=Z1cos3=32cos312.06 = 34.2
Условие прочности на изгиб зубьев выполняется со значительным запасом следовательно нагрузочная способность передачи ограничивается контактной прочностью.
1.3.6 Проверяем условие статической прочности по пиковым нагрузкам в случае частого включения электродвигателя при
МПа – предел текучести материала.
2 Расчет быстроходной ступени
Исходные данные: Вращающий момент на промежуточном валу T3=23307 Нм; угловая скорость шестерни быстроходной ступени 2=523 рад-1 угловая скорость колеса тихоходной ступени 3=127рад-1 передаточное число быстроходной ступени редуктора u=412
2.1.2 Допускаемые контактные напряжения
2.1.2.1 а) коэффициент долговечности для зубьев шестерни
где =573Lh=573127=85
1.1.2.2 допускаемое напряжение:
1.1.2.3 допускаемое контактное напряжение:
2.1.3 Допускаемые напряжения изгиба:
2.1.3.1 а) коэффициент долговечности для зубьев шестерни:
2.1.3.2 допускаемое напряжение:
2.1.3.3 допускаемое контактное напряжение:
выбираем []F=[]F2=256 Нмм2
2.2 Проектный расчет
2.2.1 Определяем межосевое расстояние по формуле 2 с.61:
UТ=412 – передаточное число тихоходной ступени
Принимаем: аw=120 мм по ГОСТ 6636-69
2.2.2 Определяем модуль передачи m мм:
Принимаем стандартный модуль: =2 мм
2.2.3 Определяем угол наклона зубьев для косозубых передач:
Принимаем = из рекомендуемого интервала 8º 16º
2.2.4 Определяем суммарное число зубьев шестерни и колеса:
2.2.5 Уточняем действительный угол наклона зубьев для косозубых передач:
2.2.6 Определяем число зубьев шестерни:
2.2.7 Определяем число зубьев колеса:
2.2.8 Определяем фактическое передаточное число и проверяем его отклонение U от заданного U:
2.2.9 Определяем фактическое межосевое расстояние для косозубой передачи мм:
2.2.10 Определяем основные геометрические параметры передачи:
da1=d1+2m=4694+22=5094 мм
da2=d2+2m=19388+22=19788 мм
df1=d1-2.4m=-2.42=4214мм
df2=d2-2.4m=-2.42=18908мм
b1=b2+4=432+4=472 мм
2.3 Проверочный расчет
2.3.1 Проверяем межосевое расстояние мм:
2.3.2 Проверяем пригодность заготовок колес: для шестерни Dmin=200 мм что значительно больше da1. Для колеса диаметр заготовки Dmin=315 мм. что значительно больше da2.
2.3.3 Проверяем контактные напряжения Нмм2:
КН=111; график 4.2 2 с. 66
2.3.4 Определяем недогруз перегруз передачи:
2.3.5 Проверяем напряжениям изгиба зубьев шестерни и колеса:
где YF2=3.60при Zv2=Z2co=95co1048=100
Y =1-140=1-1048140=09251
KFv=104 – при 8-й степени точности и v=123 мс
где YF1=392при Zv1=Z1co=23co1048=242
Условие прочности на изгиб зубьев выполняется со значительным запасом следовательно нагрузочная способность передачи ограничивается контактной прочностью
2.3.6 Проверяем условие статической прочности по пиковым нагрузкам в случаечастого включения электродвигателя при
МПа – придел текучести материала
ПРЕДВАРИТЕЛЬНЫЙ РАСЧЕТ ВАЛОВ
В качестве материла валов выбираем сталь 45 термическая обработка-улучшение. При диаметре заготовки до 80 мм B=890 МПа; T=650 МПа;
-1=380 МПа; -1=058·380=2166 МПа
1 Расчет диаметров быстроходного вала:
Все ниже перечисленные значения диаметров и длин округляем в ближайшую сторону до стандартных; таблица 7.1 2 с.112
l1=15d1=15*25=375 мм
2. Расчет диаметров промежуточного вала:
3 Расчет диаметров тихоходного вала:
l2=15d2=15·65=975 мм
4 Предварительный выбор подшипников качения:
Подшипники шариковые радиальные однорядные (ГОСТ 8338-75)
1. Определение сил в зацеплении
1.1 Быстроходная ступень
угол зацепления α=20.
а) Окружная сила на колесе
б) Окружная сила на шестерне
в) Радиальная сила на колесе
г) Радиальная сила на шестерне
д) Осевая сила на колесе
е) Осевая сила на шестерне
1.2 Тихоходная ступень
2 Расчет быстроходного вала
Таблица №7: Нагрузки
Расстояние от левого конца вала мм
3 Расчет тихоходного вала
Таблица №8: Нагрузки
4 Расчет промежуточного вала
Таблица №9: Нагрузки
Подшипник 306 (d=30; D=72; Cr=29100 Н; Cor=14600 Н)
Подобрать подшипники качения для быстроходного вала редуктора: осевая сила в зацеплении Fаз = 4447 Н; радиальные нагрузки на подшипники FrA= RA = 177143H; FrВ = RВ = 83609H; диаметр вала под подшипники d = 30 мм; угловая частота вращения вала n = 500обмин.
а) по соотношению определяем e=0.26X=056 Y=1.71. табл. 9.2 с. 143 [2]
где V=1 при вращении внутреннего кольца подшипника
Определяем эквивалентную нагрузку:
Для AREA=(VRA+YFa)KТKб=(1177143+1.71·4447)131=32914
Для BREB=(VRв+YFa)KТKб=(183609+1.714447)131=20755
Kб =1.3 по таблице 7.4 [2] (Кратковременные перегрузки до 125% от расчетной нагрузки)
Определяем динамическую грузоподъемность:
Определяем долговечность
2 Промежуточный вал.
Подшипник 207 (d=35;D=72;Cr=25500 Н; Cor=13700 Н)
Подобрать подшипники качения для промежуточного вала редуктора: осевая сила в зацеплении Fаз = Н; радиальные нагрузки на подшипники FrA= RA = 356.52 H; FrВ = RВ = 3523.80 H; диаметр вала под подшипники d = 45 мм; угловая частота вращения вала n = 12136 обмин.
а) по соотношению определяем e=026 X=056 Y=171. табл. 9.2 с. 143 [2]
Для A REA=VRАKТKб=135652 131 =46348
Для B REB=VRBKТKб=1352380 1.31=458094
Kб=1.3 по таблице 7.4 [2] (Кратковременные перегрузки до 125% от расчетной нагрузки)
Определяем долговечность:
Подшипник 213 (d=65;D=120;Cr=56000 Н; Cor=34000 Н)
Подобрать подшипники качения для тихоходного вала редуктора: осевая сила в зацеплении Fаз = Н; радиальные нагрузки на подшипники FrA= RA = 1783.01 H; FrВ = RВ = 10481.38H; диаметр вала под подшипники d = 65 мм; угловая частота вращения вала n = 3816 обмин.
а) по соотношению определяем e=0.26X=056 Y=1.71 табл. 9.2 с. 143 [2]
Для BREB=VRBKТKб=110481.381.31=136258Н
Для AREA=VRAKбKТ=1·1783.01 1.31=23179Н
1 Соединение колеса на тихоходном валу
По диаметру вала d=70 мм выбираем шпонку: b=20 мм h = 12 мм t1=7.5 мм длина =63 мм.
2 Соединение колеса на промежуточном валу
По диаметру вала d=50 мм выбираем шпонку: b=16 мм h =10 мм t1=6 мм длина =45 мм.
3 Соединение муфты на тихоходном валу
По диаметру вала d=60 мм выбираем шпонку: b=18 мм h =11 мм t1=7 мм длина =80 мм.
4 Соединение шкива на быстроходном валу
По диаметру вала d=25 мм выбираем шпонку: b=8 мм h =7 мм t1=4 мм длина =28 мм.
КОНСТРУИРОВАНИЕ РЕДУКТОРА.
1 Уплотнение подшипниковых узлов
Уплотнения подшипниковых узлов предупреждают утечку масла и защищают подшипник от проникновения в него пыли грязи паров кислот и других вредных веществ вызывающих быстрый износ и коррозию подшипников.
В манжетных уплотнениях в качестве уплотняющего элемента используется маслостойкая резина прижимаемая пружиной к валу. Уплотнения этого типа обладают малым коэффициентом трения создают хорошую герметичность и обладают способностью компенсировать износ.
2 Конструирование корпуса и крышки
Корпусные конструкции с целью снижения массы как правило выполняются тонкостенными. Увеличения их прочности и жесткости целесообразней добиваться не утолщением составляющих элементов а рациональным расположением материала и применением усиливающих ребер перегородок (диафрагм) приливов (бобышек) и т.п.
Корпуса и крышки редукторов имеют довольно сложную форму и изготовляем из чугуна СЧ 15-32.
Взаимное положение основания корпуса и крышки фиксируют двумя коническими штифтами устанавливаемыми до расточки гнезд под подшипники; основание и крышку корпуса соединяют болтами. Прокладки в месте разъема не ставят так как при этом может нарушиться посадка подшипника в корпусе. Для предупреждения вытекания масла место разъема герметизируют. В верхней части редуктора делают смотровое окно закрываемое крышкой для осмотра зацепления и заливки масла. В том случае если в редукторе выделяется большое количество тепла для предотвращения повышения давления внутри корпуса и просачивания воздуха вместе с маслом наружу через уплотнения в крышке смотрового люка устанавливают отдушину.
В нижней части корпуса делается отверстие с резьбой для спуска отработанного масла и промывки редуктора. Отверстие закрывается пробкой с прокладкой из маслостойкой резины или кожи.
На фланце крышки устанавливают два отжимных болта для облегчения отделения крышки от корпуса при разборке редуктора.
Картерная смазка осуществляется окунанием зубчатых колес в масляную ванну причем во избежание значительных потерь на размешивание масла при больших окружных скоростях зубчатые колеса погружаются не более чем на высоту зуба.
Этот вид смазки обычно применяется для зубчатых передач при окружных скоростях в зацеплении до 125 мс.
В многоступенчатых редукторах диаметры колес отдельных ступеней могут значительно отличаться по величине это вызовет погружение в масло некоторых колес на большую глубину. Погружение колеса тихоходной ступени в масло на глубину более одной трети радиуса не допускается. Если окружные скорости велики то для уменьшения потерь на перемешивание и разбрызгивание уровень масла устанавливается по колесу с максимальным диаметром а смазка других ступеней осуществляется с помощью масляного тумана.
При смазке окунанием объем масляной ванны редуктора устанавливается из расчета 04-08 литра масла на 1 кВт передаваемой мощности. Для смазки подшипниковых узлов применяется смазывание пластичными материалами т.к. окружная скорость V2 мс. Смазочный материал набивают в подшипник вручную при снятой крышке подшипникового узла на несколько лет. Наиболее распространенные для подшипников качения – пластичные смазки типа солидол жировой (ГОСТ 1033-79).
Объем масла равен 3-6 литра. Сорт масла выбираем по таблице 10.29 2 с255. При контактном напряжении Н 600 Нмм2 и окружных скоростях зубьев v=до 2 мс выбираем масло И-Г-А-68.
Выбираем упругую с торообразной оболочкой муфту. Материал полумуфт –сталь Ст3 (ГОСТ 380 - 88); материал упругой оболочки - резина с пределом прочности при разрыве не менее 10 Нмм2.
Расчетный момент муфты:
где Кр - коэффициент режима нагрузки; таблица 10.26 2 с.251
ТТ - вращающий момент на тихоходном валу.
Принимаем упругую с торообразной оболочкой 1250-1-60-1-У2 ГОСТ 20884-93
5 Конструирование корпусных деталей и крышек
В качестве материала корпуса и крышки корпуса выбираем серый чугун СЧ 15
5.1 Определяем толщину стенок корпуса отвечающих требованиям технологии литья необходимой прочности и жесткости корпуса ;
5.2 Определяем внутренний r и внешний R радиусы сопряжений плоскостей стенок корпуса:
5.2 Определяем толщину р и высоту hр ребер жесткости:
5.3 Определяем толщину платиков обрабатываемых поверхностей h:
Определение размеров конструктивных элементов крепления крышки редуктора к корпусу:
5.4 Определяем диаметры болтов крепления крышки d:
5.5 Определяем ширину фланцев К:
5.6 Определяем расстояние от внешнего края фланца до оси болта С:
5.7 Определяем диаметр штифтов dшт:
5.8 Определяем диаметры болтов крепления редуктора к плите dк:
5.9 Определяем толщину проушин S:
«Размеры корпусных деталей» Таблица №10
Толщина стенок корпуса
Внутренний радиус сопряжения плоскостей стенок корпуса r
Внешний радиус сопряжения плоскостей стенок корпуса R
Толщину ребер жесткости р
Высота ребер жесткости hр
Высота платиков обрабатываемых поверхностей h
Диаметры винтов крепления крышки d
Расстояние от внешнего края фланца до оси винта С
Диаметры винтов крепления болтов крепления редуктора к плите dк
П.Ф. Дунаев О.П. Леликов Конструирование узлов и деталей машин.- М Высшая школа 1998.
Шейнблит А.Е. Курсовое проектирование деталей машин: учебное пособие. Калининград: Янтарный сказ 1999.
Chertezh_kolesa_tikhodnogo_vala.cdw

Нормальный исходный контур
Коэффициент смещения
Обозначение чертежа сопряженного
Радиусы скруглений 1
Неуказанные предельные отклонения размеров
Tekhnicheskoe_zadanie.cdw

Spetsifikatsia.spw

Пояснительная записка
Винт В.М6-6gx18 ГОСТ 17473-80
Манжета 1.1-30 x52-1 ГОСТ 8752-79
Манжета 1.1-65 x90-1 ГОСТ 8752-79
Подшипник 213 ГОСТ 8338-75
Подшипник 306 ГОСТ 8338-75
Подшипник 207 ГОСТ 8338-75
Шайба 12 Л ГОСТ 6402-70
Шайба 6 Л ГОСТ 6402-70
Шайба C 12.37 ГОСТ 10450-78
Шпонка 8х7х28 ГОСТ 23360-78
Шпонка 12х8х40 ГОСТ 23360-78
Шпонка 18x11x80 ГОСТ 23360-78
Шпонка 20x12x63 ГОСТ 23360-78
Штифт 10 x 40 ГОСТ 3128-70
Chertezh_Reduktora.cdw

Передаточное число редуктора u=13
Вращающий момент на тихоходном валу Т
Частота вращения быстроходного вала n
Технические требования
Редуктор залить маслом И-Г-А-68 ГОСТ 1749.4-87
Допускается эксплуатировать редуктор с отклонениями
горизонтального положения на угол до 5
должен быть обеспечен уровень масла достаточный
для смазки зацепления
Редуктор цилиндрический
Рекомендуемые чертежи
- 24.01.2023
- 13.04.2024
- 24.01.2023