Проектирование привода транспортера




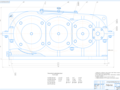
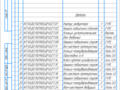
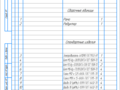
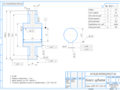
- Добавлен: 24.01.2023
- Размер: 1 MB
- Закачек: 0
Описание
Проектирование привода транспортера
Состав проекта
![]() |
![]() |
![]() ![]() ![]() |
![]() ![]() ![]() ![]() |
![]() ![]() ![]() ![]() |
![]() |
![]() ![]() ![]() ![]() |
![]() ![]() ![]() ![]() |
![]() ![]() ![]() ![]() |
![]() |
![]() ![]() ![]() ![]() |
![]() ![]() ![]() ![]() |
![]() ![]() ![]() ![]() |
![]() |
![]() ![]() ![]() ![]() |
![]() ![]() ![]() ![]() |
Дополнительная информация
ПОЯСНИТЕЛЬНАЯ ЗАПИСКА.doc
Ливенский филиал ГОУ ВПО Орел ГТУ
Кафедра технологии машиностроения
по дисциплине: «Детали машин»
Тема: «Проектирование привода транспортера»
Выбор электродвигателя. Кинематический расчёт ..3
Расчет цепной передачи 5
Расчет зубчатых колес редуктора .7
1. Расчет тихоходной ступени 9
2. Расчет быстроходной ступени .13
3 Расчёт промежуточной ступени 17
Предварительный расчет валов редуктора .20
2 Валы промежуточные 20
Конструирование корпусных деталей и деталей передач 22
Эскизная компоновка конструкции редуктора ..24
Конструктивная проработка опор и подбор подшипников .25
2 Вал промежуточный ..28
3 Вал промежуточный ..31
Уточненный расчет и окончательная проработка валов редуктора ..37
1 Вал ведущий .. .37
2 Вал промежуточный ..39
3 Вал промежуточный ..40
Конструирование и расчет соединений вращающихся деталей с валами ..44
Смазка редуктора тепловой расчет .45
Подбор и проверка прочности муфт привода .46
Конструирование рамы привода ..48
Список используемой литературы 50
Спецификация редуктора
Спецификация привода
Подбор электродвигателя привода кинематический расчет
Определим КПД привода:
где: 1 - КПД пары зубчатых колес;
- коэффициент учитывающий потери пары подшипников качения;
- коэффициент учитывающий потери в опорах вала приводного барабана;
– КПД открытой цепной передачи
По табл. 1.1 стр.5 [1] :
= 098; 2=099; 3=092; 4=099
=0982· 0993· 099·095=084.
Определим мощность на валу барабана:
Где: Fл – полезная сила передаваемая конвейером Н;
V – скорость цепи мс
РБ= 8800·055=4851Вт=4851кВт
Определим требуемую мощность электродвигателя:
Р тр.дв.=4851084=576кВт
По табл. П1 стр.390[1] подбираем двигатель 4А112М2 n=3000 обмин N=75 кВт скольжение S=25%.
Номинальная частота вращения двигателя:
nном=n1=n-n·S100%=3000-3000·25100%=2925обмин
Определим передаточное отношение привода:
i=nномnвых=292530=975
Выбираем передаточное отношение ступеней редуктора по ГОСТ 2185
iцn=i ip=9753105=315
Определим частоту вращения валов редуктора:
n2=n1 iцn =2925315=9285обмин
n3=n4= n2 iБ =928540=232обмин
n5=n6=n4 iп=232315=736 обмин
n7=n5 iт=73625=295 обмин
Угловые скорости вращения валов:
дв=1=· nдв30 =p·292530=3063 сек-1
=1 iцn =3063 2=972 сек-1
= 4= 2т=9725=243 сек-1
= 6= 4 iп=24328=77 сек-1
= 5 iт=7725=309 сек-1
Определим крутящие моменты на валах:
Т1=Ртр.дв.дв =84·1033068=188·103 Н·мм
Т2=Т1· ipn=188·103·2=592·103 Н·мм
Т3= Т3=Т2· iБ =592·103·315=2368·103 Н·мм
Т5= Т6= Т3· iт=2368·25=746·103 Н·мм
Т7= Т5· iт=746·25=1865·103 Н·мм
Расчет цепной передачи.
Исходные данные: передаваемая мощность Р=576кВт n1=2925обмин i=3.15.
Вращающий момент на ведущей звездочке:
Число зубьев на ведущей звездочке Z1=37-2i=37-2·315=31
Число зубьев ведомой звездочки: Z2=Z1·i=31·3.15=98
Тогда iцп= 9831=316.
Отклонение передаточного отношения составит что допустимо.
Расчетный коэффициент нагрузки Кэ=Кд·Ка·Кн·Кр·Ксм·Кп=1·1·1·125·14·1=175
Р0=185МПа (табл. 13.1 [1])
что больше допустимой скорости для роликово-втулочной цепи.
принимаем t=12.7мм по стр. 302 [1]:
Цепь зубчатая ГОСТ13552-81 с параметрами:
Q=49кН q=2.70кгм t=12.7мм h=13.4 мм h1=7.0 мм s=1.5 мм w=4.76 [S]=30 (стр 155 [1]).
Число звеньев цепи: ZΣ=Z1+Z2=31+98=129
a=40t=40·12.7=508 аt=40
Принимаем Lt действ.=148мм
Уточняем межосевое расстояние по формуле:
Для свободного провисания цепи предусматриваем возможноть уменьшения межосевого расстояния на 04%. 513·004=2мм
Определяем диаметры делительных окружностей звездочек:
Определяем диаметры наружных окружностей звездочек
Определяем силы действующие на цепь.
Сила от провисания цепи
Расчетная нагрузка на валы
Проверяем коэффициент запаса прочности s по формуле:
15>30 (табл. 7.22 стр. 157 [1])
Расчет зубчатых колес редуктора
По табл.8.8 стр.163[2] назначаем термообработку для колес и шестерен – закалка на ТВЧ.
Твердость: для колес – НRC 45
для шестерен – НRС 50
Предел прочности : в=1600 МПа
Предел текучести: т=1400 МПа
Допускаемые контактные напряжения определяем по табл.8.9 стр.168[2] :
Sн=12 – коэффициент безопасности
но1=17·50+200=1050 МПа – для шестерни
но2=17·45+200=965 МПа – для колеса
Допускаемое напряжение:
[н] = ( ноSн) ·КнL (2.1) - формула 8.55 стр.167 [2]
где КнL- коэффициент долговечности
КнL= ≥ 1 но ≤ 24 (2.2) - формула 8.59 [2]
Коэффициент Nне по формуле 8.63 стр.171 [2]
Nне = 60·с·Σ (ТТmax)3·n i·ti (2.3) - формула 8.63 [2]
с=1 – в зацеплении с одним колесом одновременно находится одно колесо
t – число часов работы передачи
tΣ = 365·L· Ксут ·Кгод ·24 (2.4) – формула 8.66 [2]
где L- срок службы годы
Кгод Ксут – коэффициенты использования передачи в году и сутках
tΣ = 365·5·029·05·24·=6351 час
По рисунку 8.40 стр.169 [2] для НRC 50 – NHO1=80 · 106
Для HRC 45 - NHO2 = 60 · 106
Для быстроходной ступени:
NHE=60·1·(13·0002+053·08)·928·6351=36·107
Для тихоходной ступени:
NHE=60·1·(1·0002+053·08)·30·6351=116·106
Для промежуточной ступени:
NHE=60·2·(13·0002+053·08)·232·6351=9·106
1. Расчет тихоходной ступени
Определяем коэффициент долговечности по формуле 859 стр 170 [2]
[H] =1050·1.29=1361 МПа
Определяем допускаемые напряжения изгиба.
По таблице 8.9[2] FO=550 МПа SF=175
[F] = (FOSF)·КFC·КFL (2.5) - формула 8.67 [2]
где: КFC – коэффициент учитывающий реверсивность передачи
КFL – коэффициент долговечности
NFO = 4·106 – рекомендуемая величина для всех сталей стр.174[2]
NFE= 60 с·Σ (Тi Тmax)9·ni·ti (2.7) - стр.174 [2]
NFE=60·1(19·0002+059·08) ·30·6351=40·103
KFL==102 принимаем KFL=1
[F] =550×1·1175=314 МПа
Допускаемые напряжения при перегрузках:
-максимальные контактные напряжения
Hmax=H [H]max (2.8) - стр.174[2]
[H]max= 40 НRC= 40·45=1800 МПа
-максимальное напряжение изгиба
Fmax = F (Tmax Tном) ≤[F]max (2.9) стр.174 [2]
[F]max= 1430 МПа стр.168 [2]
По рекомендации табл. 8.4 [2] ва = 04 ; вd max =11
По формуле 8.12 [2] вd=05 ва (u+1)=05·04(25+1)=07
По графику рис.8.15 [2] КH=105 КF=104
Модуль упругости Епр=21·105 МПа
По формуле 8.13[2] находим межцентровое расстояние:
awT= 085 (u+1)· (2.10)
Округляем по стандартному ряду до ат=180мм
Находим ширину колеса b7:
b7=ваT· awT=0.7·180=126 мм
b6=b7+5=126+5=131 мм
По табл.8.5 принимаем m =35
Модуль m =b m =12635=36мм
Принимаем модуль mт=35 мм
Суммарное число зубьев:
Принимаем коэффициент осевого смещения перекрытия =12 по формуле 823 [2] стр 146 определяем угол наклона зубьев:
=6º5' – в рекомендуемых пределах.
Принимаем z6=28число зубьев колеса z7= z6·iT=28·2.5=70
Уточняем значение угла наклона:
Делительные диаметры шестерни и колеса:
d6=mт·z6 cos 6=35·28098=103мм
d7=mт·z7 cos 7=35·70098=257мм
Окружная скорость колеса:
V4=3092572·103=0.397мс
назначаем девятую степень точности.
Выполняем проверочный расчет на усталость по контактным напряжениям.
По табл. 8.3[2] КHv=104 КFv=101
По формуле 8.29[2] находим:
где: ZНb – коэффициент повышения прочности контактным напряжениям.
ZНb= (2.18) ф–ла 8.28 [2]
КНa=113 табл. 8.7 [2]
ea=[188-32(1z6+1z7)cosb] (2.19) ф–ла 8.25 [2]
ea=[188-32(128-170)0975]=17
H=118×08 =1601 МПа[H]=1865 МПа
Выполняем проверочный расчет по напряжениям изгиба:
F= YF· Ft·КТ ·Y· КFα b6·mпт [F] (2.20) - формула 8.32 [2]
По графику 8.20 стр 140 [2] при К=0 YF6=380кН YF7=3.61кН т.к. [k6]= [k7] то следовательно расчёт ведём для шестерни.
По графику рис. 8.15 [2] КF=1.35
по табл. 8.3 [2] КF=104
Окружная сила Ftт= 2Т6 d6=2·1865·103103= 18106Н
Радиальная сила Frт= Ftт·tgcos 7=18016·tg20ºcos 11º47=6724 Н
Осевая сила Faт= Ftт· tg7=6724tg11º47=1364 Н
По табл. 8.7 стр 182 [2] KFα=1.35
F =18106·0918×414·135·115(2.5·11.47)=213.5 МПа[F]=314 МПа
Выполняем проверочный расчет на заданную перегрузку:
max=1601·=1836 МПа[H]max=1865 МПа
Fmax=213.5·1314=244.7 МПа[F]max= 1430 МПа
условия прочности выполнены.
2. Расчет быстроходной ступени
КHL1= =1.13 ; - для шестерни
КHL2==1.079 ; -для колеса
[H1] =1050×112=954МПа
[H2 ] =965×112=847МПа
[H] = ([H1]+ [H2 ])2=(954+847)2=898МПа
Определяем допускаемое напряжение изгиба:
Коэффициент долговечности: КFL=
NFE = 60·1·(19·0002+055·08) ·3972· 18800=24·106
КFL==108 принимаем КFL=1
[F] =550·1·1175=31429 МПа
Принимаем коэффициент: ba=025; bd max=08
bd= 05ba (u+1)=05×025(4+1)=0625
По графику рис.8.15 [2] КH=105 ; КF=108
Находим межцентровое расстояние:
Выбираем по стандартному ряду до аб=100 мм
Находим b= ba аБ =025100=25 мм
По таблице 8.5 принимаем m=20
Модуль m= b m =2520=125 мм
Принимаем модуль mБ=125 мм
=10º8' – в рекомендуемых пределах.
Принимаем z1=31число зубьев колеса z2= z1·iT=31·4=124
d1= mБ ·1 cos1=125·31096875=40 мм
d2= mБ 2 cos1=125·124096875=160 мм
Ширина колеса: b2= ba аБ=025·100=25мм
Ширина шестерни: b1= b2+5=25+5=30мм
V2= 2d2 2·103 =9721602·103=489 мс
По табл.8.2[2] назначаем 8-ую степень точности.
Выполняем проверочный расчет по контактным напряжениям.
По табл.8.3 [2] : КHV=103 КFV=105
КH=КH КHV =113105=119
ea=[095-16(1z1+1z2)cosb] (2.19) ф–ла 8.25 [2]
ea=[095-16(131-1124)099206]=171
По формуле 8.29 [2] находим:
=118078=973МПа≤[H]=1014МПа
- Окружная сила: FtБ=2Т1 d1=259221031008=1175 Н
- Радиальная сила: FrБ= FtБ· tgα сos1=1175tg20º 099206=431 Н
- Осевая сила: FаБ= FtБ·tg1=1175· tg7º23' =148 Н
Коэффициент: КF =КF КFV=108·105=1134
По графику рис.8.20 [2] при Х=0: YF1=397 YF2=365
Отношение [F]YF меньше для шестерни следовательно расчет ведем для шестерни.
F=3971175×1134(1×35)=152 МПа[F]
Fmax=152×16=2432 МПа[H]max=1430 МПа
Hmax=973×=1225 МПа[F]max= 1800 МПа
3 Расчёт промежуточной ступени.
КHL1= =086 ; - для шестерни
КHL2==03 ; -для колеса
[H1] =1050×112=875МПа
[H2 ] =965×112=804МПа
[H] = ([H1]+ [H2 ])2=(875+804)2=840МПа
NFE = 60·1·(13·025+053·075) ·4652· 9855=94·107
КFL==07 принимаем КFL=1
[F] =650·1·1175=371 МПа
Принимаем коэффициент: ba=025; bd max=10
bd= 05ba (u+1)=05×025(315+1)=0518
По графику рис.8.15 [2] КH=102 ; КF=103
Выбираем по стандартному ряду до ап=160 мм
Находим b= ba ап =025160=40мм
Модуль m= b m =4020=2 мм
Принимаем модуль mБ=2 мм
=1085º – в рекомендуемых пределах.
Принимаем z3=38число зубьев колеса z5= z1·iT=38·315=120
d3= mп ·3 cos3=2·3809875=77 мм
d5= mп 5 cos5=2·12009875=243 мм
Ширина колеса: b5= ba аБ=025·160=40мм
Ширина шестерни: b3= b5+5=40+5=45мм
V5= 5d5 2·103 =243772·103=099 мс
По табл.8.2[2] назначаем 9-ую степень точности.
По табл.8.3 [2] : КHV=104 КFV=101
КH=КH КHV =102104=10608
ea=[188-32(1z3+1z5)cosb] (2.19) ф–ла 8.25 [2]
ea=[188-32(138-1120)09875]=1823
=118079=1106МПа≤[H]
- Окружная сила: FtБ=2Т1 d1=274610377=19401 Н
- Радиальная сила: FrБ= FtБ· tgα сos1=19401tg20º 09875=7151 Н
- Осевая сила: FаБ= FtБ·tg1=7151· tg9º6' =1140 Н
Коэффициент: КF =КF КFV=118·101=119
По графику рис.8.20 [2] при Х=0: YF1=379 YF2=38
F=37919401×119·095·135(2×40)=1093 МПа[F]
Fmax=1093×16=1748 МПа[H]max=1800 МПа
Hmax=1093×=1398 МПа[F]max= 1430 МПа
Предварительный расчет валов редуктора.
Диаметр входного конца вала при допускаемом напряжении на кручение
dв1 = (3.1) – ф-ла 8.16 стр.161 [1]
dв1==28 мм. Принимаем диаметр вала 30мм.
Диаметр вала электродвигателя d дв =32 мм
Для удобства соединения валов редуктора и двигателя стандартной муфтой соблюдаем условие: d в1 = 25мм
Диаметр вала под подшипник dп1 =25мм
Вал изготовлен за одно целое с шестерней.
2.Валы промежуточные II.
У промежуточного вала расчетом на кручение определяем диаметр опасного сечения по пониженным допускаемым напряжениям.
Принимаем диаметр вала под колесом dк =50мм
Диаметр вала под подшипник dп=45мм
Принимаем диаметр вала под колесом dк =70мм
Диаметр вала под подшипник dп=65мм
Диаметр выходного конца вала при [к] = 25 МПа
Диаметр вала под подшипник dп4 =75мм
Диаметр вала под колесом dк4 =75мм
Диаметры остальных участков валов назначаем исходя из конструктивных соображений при компоновке редуктора.
Конструирование корпусных деталей и деталей передач.
Толщина стенок корпуса и крышки
= 0025 ат +3=0025×180+3=75 принимаем =8 мм
= 002 ат +3=002×180+3=66 принимаем 1=8 мм
Толщина фланцев поясов корпуса и крышки:
-верхнего пояса корпуса и крышки
в1= в=15 =15×8=12 мм
-нижнего пояса корпуса
р = 235 =235×8=188»20 мм принимаем р =20 мм
- фундаментных d1= (003 – 0036) ат +12 =(003-0036) ×180+12=183 мм
принимаем болты с резьбой М18
- крепящих крышку к корпусу у подшипников
d2=(07-075) d1=(07-075)×18=135 мм
принимаем болты с резьбой М14
- соединяющих крышку с корпусом d3= (05-06) d1=(05-06)×18=99 мм
-принимаем болты с резьбой М10
Определяем конструктивные размеры шестерни и колеса.
Быстроходная ступень.
- шестерня Z1=31 -кованая
d1= 40 мм – делительный диаметр
dа1= d1 + 2mБ=40+2×125=425 мм – диаметр вершин
df1= d1 -25mБ=40-25×125=36875 мм-диаметр впадин
b1=30 мм – ширина шестерни
Шестерня изготовлена заодно с валом.
- колесо Z2=124-кованое
dа2=160+2×125=1625 мм
df2=160-25×125= 15685 мм
dст=16 dк=16×50=78 мм- диаметр ступицы
lст= (12 – 15) dк =(12-15)×50=63 мм-длина ступицы.
- шестерня Z5=28-кованая изготовлена заодно с валом.
dа5=103+2×35=110 мм
df5=103-2.5×35=94.5 мм
- колесо Z6=73-кованое
df6=257-25×35=25125 мм
lст= (12 – 15)dк=(12 – 15)75=975мм
Эскизная компоновка конструкции редуктора.
Компоновочный эскиз служит для приближенного определения зубчатых колес относительно опор для последующего определения опорных реакций и подбора подшипников.
Размеры подшипников и их грузоподъемность определяем по табл.П3 стр.392[1].
Данные сводим в таблицу 5.1.
Условное обозначение подшипнка
Компоновочный чертеж выполняем в одной проекции – разрез по осям валов при снятой крышке редуктора. Посередине листа параллельно его длинной стороне проводим горизонтальную осевую линию затем проводим три вертикальные линии – оси валов. Вычерчиваем шестерни и зубчатые колеса в виде прямоугольников. Принимаем зазор от окружности вершин зубьев колес до внутренней стенки корпуса А=8 мм
И очерчиваем внутреннюю стенку корпуса. Для предотвращения вытекания смазки внутрь корпуса и вымывания пластичного смазывающего материала устанавливаем мазеудерживающие кольца. Их ширина 8 мм. Измерением устанавливаем расстояния между опорами:
- на первом промежуточном валу
- на втором промежуточном валу
- на ведомом валу l1 =95 мм l2=197мм.
Конструктивная проработка валов и подбор подшипников.
Рисунок 1. Расчетная схема вала ведомого.
Из предыдущих расчетов имеем:
Frт=6724 Н;Fтт=18106 Н; Fат=1364 Н
Из первого этапа компоновки l1=36мм l2=135мм
- Ftтl1+R2x(l1+l2)=0
- Ftтl2+R1x(l1+l2)=0
Подбираем подшипник по более нагруженной опоре 1.
Назначаем радиальные шариковые подшипники 315 для которых d=75 D=160 B=37 С=112кН С0=725кН
Эквивалентная нагрузка по формуле 9.3
в которой радиальная нагрузка Pr1=15638H осевая нагрузка Pa=1364Н V=1 (вращается внутреннее кольцо).
Коэффициент безопасности для приводов ленточных конвейеров Кб=1 (табл. 9.19 1 ) Кт=1 (табл. 9.20 1 ).
Этой величине по таблице 9.18 соответствует e=0.19
Отношение что больше 019
Рэ=(0566345+231364)=669064Н
Расчетная долговечность млн. об:
Расчетная долговечность в часах:
Рисунок 2. Расчетная схема вала ведущего.
Из предыдущих расчетов имеем:
Ftб=1175H Faб=148Н Frб=431Н
Из первого этапа компоновки l1=119 l2=132 l3=110
Нагрузка на вал от цепной передачи Fв=3474Н
Составляющие этой нагрузки: Fвх=Fвц=Fвsinγ=3474sin45º=2456H
Проверка: R 9531+4674-2456-1175=0; 0=0 верно.
Назначаем радиальный подшипник 305. d=25мм D=62мм В=17мм r=2мм С=225кН С0=114кН.
Эквивалентная нагрузка по формуле 9.3:
В которой радиальная нагрузка Pr1=1113.4Н осевая нагрузка Pa=Fa=148H V=1 вращается внутреннее кольцо. Коэффициент безопасности для приводов ленточных конвейеров Кб=1 (табл. 9.19 1 ) Кт=1 (табл. 9.20 1 ).
Отношение что меньше 019
3 Расчет первого промежуточного вала.
Рисунок 3. Расчетная схема первого промежуточного вала
Fтп=9401Н Frп=7151Н Faп=1140Н
Fтб=1175H Faб=148Н Frб=431Н
Из первого этапа компоновки l1=100мм l2=75мм l3=73мм
Реакции опор в плоскости XZ:
Проверка R1+R2-Rrп-Prб=0 0=0
Подбираем подшипник по более нагруженной опоре 2. Назначаем радиальный шарикоподшипник 309 с параметрами d=45мм D=100мм В=25мм r=25мм С=527кН С0=30кН.
В которой радиальная нагрузка Pr1=5428 Н осевая нагрузка Pa=Fa=1140H V=1 вращается внутреннее кольцо. Коэффициент безопасности для приводов ленточных конвейеров Кб=1 (табл. 9.19 1 ) Кт=1 (табл. 9.20 1 ).
Этой величине по таблице 9.18 соответствует e=0.22
Отношение что меньше 022
4 Расчет второго промежуточного вала.
Рисунок 4. Расчетная схема второго промежуточного вала.
Из первого этапа компоновки l1=30мм l2=120мм l3=30мм
Проверка R1+R2-Rrп-Prт=0 0=0
Подбираем подшипник по более нагруженной опоре 2. Назначаем радиальный шарикоподшипник 313 с параметрами d=65мм D=140мм В=33мм r=35мм С=923кН С0=56кН.
В которой радиальная нагрузка Pr2=15258 Н осевая нагрузка Pa=Fa=1140H V=1 вращается внутреннее кольцо. Коэффициент безопасности для приводов ленточных конвейеров Кб=1 (табл. 9.19 1 ) Кт=1 (табл. 9.20 1 ).
Уточненный расчет и окончательная проработка валов редуктора.
Принимаем что нормальные напряжения от изгиба изменяются по симметричному циклу а касательные – по отнулевому (пульсирующему). Уточненный расчет состоит в определении коэффициентов запаса прочности S для опасных сечений и сравнении их с допускаемыми значениями.
Прочность соблюдена при условии S≥[ S]
Будем производить расчет для предположительно опасных сечений каждого из валов.
Материал вала такой же как и шестерни т.к. они выполнены заодно – сталь 40ХН термообработка – улучшение.
Пределы выносливости:
-1=043 в =043930=400 МПа
-1= 058 -1=058400=232 МПа
Это сечение при передаче вращающего момента от электродвигателя через муфту рассчитывается на кручение. Концентрацию напряжений вызывает наличие шпоночной канавки.
Коэффициент запаса прочности:
где амплитуда и среднее напряжение отнулевого цикла:
v= m= мах2=Т12Wк нетто(7.2)
Wк нетто = pd316 – bt1(d - t1)22d(7.3) - стр. 165[1]
по табл. 8.9 стр.169[1] при d=25 мм b=6 мм t1=4 мм
Wк нетто =p25316-6×4(25-4)2225=2855 мм2
v= m=548·1032855=32 МПа
К= К =193 по табл.8.5 стр. 165[1]
= =081 по табл.8.8 стр. 166[1]
=015; =025 стр. 165[1]
ГОСТ 16162-85 указывает на то чтобы конструкция редукторов предусматривала возможность восприятия радиально консольной нагрузки приложенной в середине посадочной части вала. Приняв у ведущего вала длину посадочной части под муфту равной длине ступицы звездочки L=65 мм получим изгибающий момент в сечении А-А от консольной нагрузки.
М=25L2=25652=352 Нмм
Коэффициент запаса прочности по нормальным напряжениям:
где амплитуда нормальных напряжений равна:
= М(2 Wк нетто)=352(22855)=0061 МПа
среднее напряжение: =4FаБ (7.5) – стр. 163[1]
Результирующий коэффициент запаса прочности:
коэффициент получился близким к S=29 это свидетельствует о том что консольные нагрузки рассчитанные по крутящему моменту и согласованные с расточками стандартных полумуфт оказываются прочными и учет консольной нагрузки не вносит существенных изменений.
2 Вал промежуточный II
Материал вала – сталь 40ХН термообработка – улучшение.
В этом сечении наибольший изгибающий момент. Концентрацию напряжений вызывает наличие шпоночной канавки. Диаметр вала в этом сечении d =45 мм
= =076 по табл.8.8 стр. 166[1]
=015 ; =025 стр. 165[1]
Крутящий момент Т2=2368·103 Нмм
Изгибающий момент в горизонтальной плоскости:
М1= Rх1(l1+l2) – Ftт l2=2033(95+118)- 25955 85=741675 Нмм
Изгибающий момент в вертикальной плоскости:
М2=-Rу1(95+118) + Fаnd32 + FаБd22=-781(85+85)+187.6432+138962=128736.6 Нмм
Суммарный изгибающий момент:
Момент сопротивления кручению:
Wк нетто = pd316 – bt1(d - t1)22d =p40316-1255(40-55)2240=11578мм3
Момент сопротивления изгибу:
Wнетто = pd332 – bt1(d - t1)22d =p40332-1255(40-55)2240=5298 мм3
Амплитуда и среднее напряжение цикла касательных напряжений:
v= m= мах2=Т22Wк нетто=172.6·103211578=7.4 МПа
среднее напряжение = 0
Амплитуда нормальных напряжений:
= МБ-БWнетто=1185735298=22.4 МПа
Коэф-т запаса прочности по нормальным напряжениям:
Коэф-т запаса прочности по касательным напряжениям:
Результирующий коэф-т запаса прочности:
3 Вал промежуточный III
В этом сечении наибольший изгибающий момент. Концентрацию напряжений вызывает наличие шпоночной канавки. Диаметр вала в этом сечении d=65 мм
Крутящий момент Т4=746·103 Нмм
М1= Rх1(l1+l2+ l3) – Ftn( l2+ l3)-Ftт l3=3446(64+85+85)+ 25955·(85+85)-12082·85=220629 Нмм
М2=-Rу1(l1+l2+ l3) +Frn·(l2+ l3)+ Fаnd52 +Frm l3+ Fаmd72-Fan(d62)=-1314(64+85+85)-968(85+85)+187.61332+4510·85+3632712-187.6·1332=40250 Нмм
Wк нетто = pd316 – bt1(d - t1)22d =p55316-166(55-6)2255=30556мм3
Wнетто = pd332 – bt1(d - t1)22d =p55332-166(55-6)2255=14230 мм3
v= m= мах2=Т22Wк нетто=746·103214230=17 МПа
= МБ-БWнетто=22427014230=16 МПа
Материал вала – сталь45 термообработка –нормализация.
-1=043 в =043570=246 МПа
-1= 058 -1=058246=142 МПа
Наиболее опасным является сечение А-А на выходном валу так как в этом сечении наименьший диаметр. В этом сечении наибольший изгибающий момент. Концентрацию напряжений вызывает наличие шпоночной канавки. Диаметр вала в этом сечении d=75 мм b=20 мм t1=75 мм
К=15; К =17 по табл.8.5 стр. 165[1]
=073; =076 по табл.8.8 стр. 166[1]
Крутящий момент: Т5=1865·103 Нмм.
Изгибающий момент в сечении Д-Д от консольной нагрузки.
МГ-Г =25L2=251912=261×103 Нмм
Wк нетто = pd316–bt1(d-t1)22d =p75316-2075(75-75)2(275)=78237 мм3
Wнетто = pd33 –bt1(d - t1)22d =p75332-2075(75-75)2(275)=36840мм3
v= m= мах2=Т52Wк нетто=12082·103278237=77 МПа
= МГ-ГWнетто=261×10336840=328 МПа
Конструирование и расчет соединений вращающихся деталей с валами.
На всех валах применяем шпонки призматические с округленными торцами по ГОСТ 23360-78. Материал шпонок – сталь 45 нормализованная. По табл. стр.169 определяем размеры сечений шпонок.
Напряжения смятия и условие прочности определяется по формуле:
Допускаемые напряжения при стальной ступице = 100 120 МПа
Расчет шпонки ведем под полумуфтой так как шестерня изготовлена за одно целое с валом.
dв=25мм; bh=8х7мм; t1=4 мм; lшп=80мм
Крутящий момент Т1=188×103 Н×мм
Диаметр вала под колесом dк=40 мм;
bh=14х9мм; t1=6мм; lшп=45мм
Крутящий момент Т2=548×103 Н×мм
Диаметр вала под колесом dк=65 мм;
bh=18х11мм; t1=7мм; lшп=56мм
Крутящий момент Т5=746×103 Н×мм
Диаметр выходного конца вала dв=75мм;
bh=20х12мм; t1=75мм; lшп=80мм
Крутящий момент Т7=1865×103 Н×мм
Смазка редуктора тепловой расчет.
1 Смазывание зубчатых зацеплений и подшипников уменьшает потери на трение предотвращает повышенный износ и нагрев деталей а также предохраняет детали от коррозии. Снижение потерь на трение обеспечивает повышение КПД редуктора. Смазывание осуществляется окунанием зубчатых колес в масло заливаемое внутрь корпуса. При смазывании окунанием объем масляной ванны редуктора принимаем из расчета 05 08 л на 1 кВт требуемой мощности.
V=(05 08)Nтр =08×485=388 л принимает V=39 л.
По табл. 10.8 стр.253 устанавливаем вязкость масла 70×10-6м2с. По табл. 10.10 стр.258 выбираем сорт масла И-70А.
При работе редуктора потери мощности вызываемые трением в зацеплении и подшипниках перемешиванием масла приводят к нагреву деталей редуктора и масла. Для зубчатых редукторов малой и средней мощности тепловой расчет производить нет необходимости так как КПД этих редукторов высок и теплоотделение невелико.
Подбор и проверка прочности муфт привода.
Выбираем упругую муфту со звездочкой по ГОСТ 14084-76. Работоспособность резиновой звездочки определяется напряжением смятия и может быть рассчитана по формуле:
sсм= - ф–ла 17.33 стр. 362
Т – крутящий момент Нмм
к – коэф-т безопасности к=115
D – наружный диаметр звездочки мм
принимаем по ГОСТ 14084-76 (стр.279[1]) D=63 мм
h – ширина звездочки мм
h=(022 03)D=03×63=19мм принимаем h=20 мм
условия прочности выполнены
На сборку поступают детали соответствующие чертежу и техническим требованиям на их изготовление. Перед сборкой внутреннюю часть корпуса редуктора тщательно очищают и покрывают маслостойкой краской обычно красного цвета. Сборку производят в соответствии с чертежом общего вида редуктора.
Перед общей сборкой собирают валы с насаживаемыми на них деталями.
На оба конца вала первыми надевают мазеудерживающие кольца согласно чертежу а затем устанавливают подшипники предварительно нагретые в масле до 80-1000С.
Промежуточный и ведомый валы.
В начале закладывают шпонку и напрессовывают зубчатое колесо до упора его в буртик вала; затем надевают мазеудерживающие кольца и устанавливают подшипники предварительно нагретые в масле.
Собранные валы вместе с подшипниками укладывают в основание корпуса редуктора. Далее надевают крышку корпуса с рым-болтами устанавливают конические штифты крышку и основание корпуса стягивают болтами. Предварительно плоскости стыка крышки и основания покрывают клеем БФ-2. После этого ставят крышки подшипников с прокладками прикрепляют их к корпусу болтами. Проверяют проворачиванием вала отсутствие заклинивания подшипников (при малой толщине прокладки). Камеры подшипников набивают консистентной смазкой.
Перед постановкой крышек подшипников ведущего и ведомого валов в специальные проточки крышек закладывают манжетные уплотнения. Далее на конец ведомого вала закладывают шпонку и устанавливают полумуфту.
Затем ввертывают пробку маслоспускного отверстия с прокладкой и жезловый маслоуказатель. Перед постановкой крышки смотрового люка внутрь корпуса заливают масло после чего крышку люка с прокладкой закрепляют болтами.
Собранный редуктор подвергают обкатке и испытанию.
Конструирование рамы привода проверка прочности крепежных деталей.
Конфигурация и размеры рамы зависят от типа редуктора и электродвигателя и от их размеров. Расстояние между ними зависит от подобранной соединительной муфты. Затем подрисовывают тонкими линиями контуры электродвигателя и редуктора. После этого вычерчивают контуры рамы.
На главном виде вычерчивают контур рамы и приступают конструированию рамы на виде сверху. Для этого в контурах электродвигателя и редуктора наносят центры и контуры опорных поверхностей. Опорные поверхности под лапы электродвигателя и редуктора на раме выделяют в виде платиков и подвергают механической обработке. Ширину и длину платиков назначают больше ширины bэ
bр и длины lо lр опорных поверхностей электродвигателя и редуктора на величину Со = 8 10 мм
Длину рамы определяют по формуле на стр. 324 [3]
L = l10 + lБ + l3 + (l0 - l10)2 + lр2 + 2Со + 8 12
где l10 l3 – расстояние между болтами крепления электродвигателя и редуктора.
L =140+330+292+(260-140)2+582+2·10+12=670мм
Высоту рамы определяющую жесткость назначают в зависимости от L
Н = (012 015) L =012·670=80мм
принимаем швеллер №10
Ширину и В2 рассчитывают по зависимостям:
В1 = b10 + bэ + 2Со + 8 12
В2 = b1 + bр1 + 2Со + 8 12
где b10 и b1 – расстояние между болтами крепления электродвигателя и редуктора.
В1 =190+42+2·10+12=240мм
В2 =423+121+2·10+12=400мм
Список используемой литературы.
«Курсовое проектирование деталей машин» С.А. Чернавский К.Н. Боков И.М. Чернин и др. М. Машиностроение 1988 416 с.
«Детали машин» М.Н. Иванов М. Высшая школа 1991. 383 с.
«Курсовое проектирование деталей машин» В.Н. Кудрявцев Ю.А. Державец И.И. Арефьев и др. Л. Машиностроение 1983 400 с.
Привод А1.cdw

Непараллельность осей звездочек не более 0
Смещение венцов звездочек для цепной передачи не должно
Цепь устанавливаемая на звездочках
отрегулирование на натяжение
Привод обкатать без нагрузки в течение не менее 1 часа. Резкие
шумы и стук не допускаются
После обкатки масло из редуктора слить
индустриальное И-70А ГОСТ 20799-75 в количестве 3
Ограджения муфты и цепи условно не показаны. После сборки
привода ограждения установить и окрасить в желтый цвет.
Технические характеристики
Вид главный А1.cdw

КП.10.ДО.150900.ДМ.027.
Поверхности соединения корпус-крышка перед сборкой покрыть
уплотнительной пастой типа Герметик
После сборки валы редуктора должны поворачиваться свободно
без стуков и заедания
Редуктор наполнить маслом И-70А ГОСТ 20199-75
Редуктор обкатать по 10-15 минут на всех режимах нагрузки
Вал ведомый А3.cdw

Вид сверху А1.cdw

Спецификация транспортер.spw

Расчетно-пояснительная записка
Электродвигатель 4А112М2 ГОСТ19523-81
Болт М12-8g x 38.109.30ХГСА ГОСТ 15589-70
Болт М12-8g x 50.109.30ХГСА (S18) ГОСТ 15589-70
Болт М18-8g x 70.109.30ХГСА ГОСТ 15589-70
Шайба 12 БрКМц3-1.099 ГОСТ 6402-70
Шайба 18 БрКМц3-1.099 ГОСТ 6402-70
Шайба 12.31 ГОСТ 10906-78
Шайба 18.31 ГОСТ 10906-78
Швеллер 16П ГОСТ8240-89 l=725
Швеллер 16П ГОСТ8240-89 l=697
Швеллер 16П ГОСТ8240-89 l=632
Швеллер 16П ГОСТ8240-89 l=344
Швеллер 16П ГОСТ8240-89 l=226
Звездочка ведомая z=98
Звездочка ведущая z=31
b=55.5мм ГОСТ13552-81
Вал шестерня А3.cdw

Термообработка - нормализация
Кромки притупить R=0.3мм
Общий припуск по ГОСТ 30389-1М
КП.10.ДО.150900.ДМ.027.24
Сталь 40ХН ГОСТ 4543-81
Крышка глухая А3.cdw

Общие допуски по ГОСТ 30893-1-с
Отливка второго класса группа "а" по ОСТ2-МТ 21-2-33
Колесо зубчатое А3.cdw

КП.10.ДО.150900.ДМ.027.26
Сталь 40ХН ГОСТ 4543-81
Радиусы закруглений - 5 мм
Общие допуски по ГОСТ 30893.1-с
Точность зубчатого колеса в соответствии с ГОСТ 1643-81
Спецификация редуктор.spw

КП.10.ДО.150900.ДМ.027.
Пояснительная записка
КП.10.ДО.150900.ДМ.027.01
КП.10.ДО.150900.ДМ.027.02
Крышка подшипника сквозная
КП.10.ДО.150900.ДМ.027.05
Кольцо уплотнительное
КП.10.ДО.150900.ДМ.027.06
КП.10.ДО.150900.ДМ.027.08
Крышка подшипника глухая
КП.10.ДО.150900.ДМ.027.11
Вал-шестерня промежуточный
КП.10.ДО.150900.ДМ.027.12
Кольцо мазеудерживающее
КП.10.ДО.150900.ДМ.027.13
КП.10.ДО.150900.ДМ.027.14
Колесо зубчатое цилиндрическое
КП.10.ДО.150900.ДМ.027.15
КП.10.ДО.150900.ДМ.027.17
КП.10.ДО.150900.ДМ.027.18
КП.10.ДО.150900.ДМ.027.19
КП.10.ДО.150900.ДМ.027.20
КП.10.ДО.150900.ДМ.027.24
Вал-шестерня ведущий
КП.10.ДО.150900.ДМ.027.25
КП.10.ДО.150900.ДМ.027.26
КП.10.ДО.150900.ДМ.027.27
КП.10.ДО.150900.ДМ.027.30
КП.10.ДО.150900.ДМ.027.31
КП.10.ДО.150900.ДМ.027.32
КП.10.ДО.150900.ДМ.027.40
КП.10.ДО.150900.ДМ.027.41
КП.10.ДО.150900.ДМ.027.42
Маслоуказатель жезловый в сборе
КП.10.ДО.150900.ДМ.027.47
-Ст3Гпс ОСТ 26.260.460- 99
Болт М6-8g x 20.109.30ХГСА ГОСТ 15589-70
Болт М10-8g x 20.109.30ХГСА ГОСТ 15589-70
Болт М10-8g x 38.109.30ХГСА ГОСТ 15589-70
Болт М14-8g x 95.109.30ХГСА ГОСТ 15589-70
Болт М14-8g x 200.109.30ХГСА ГОСТ 15589-70
Гайка М10-6H.04 ГОСТ 5927-70
Гайка М14-6H.04 ГОСТ 5927-70
Подшипник305 ГОСТ 8338-75
Подшипник309 ГОСТ 8338-75
Подшипник313 ГОСТ 8338-75
Подшипник315 ГОСТ 8338-75
Шайба 6 БрКМц3-1.099 ГОСТ 6402-70
Шайба 10 БрКМц3-1 ГОСТ 6402-70
Шайба 14 БрКМц3-1 ГОСТ 6402-70
Шайба 18 ГОСТ10450-78
Пресс-масленка М10х1 ГОСТ 20905-75
Крышка редуктора А1.cdw

Поверхности соединения корпус-крышка перед сборкой покрыть
уплотнительной пастой типа Герметик
После сборки валы редуктора должны поворачиваться свободно
без стуков и заедания
Редуктор наполнить маслом И-70А ГОСТ 20199-75
Редуктор обкатать по 10-15 минут на всех режимах нагрузки
Рекомендуемые чертежи
- 04.06.2015
- 02.10.2019