Проект механического цеха с разработкой участка по изготовлению деталей редукторов дорожных машин





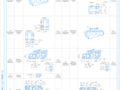
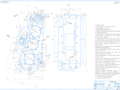
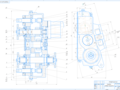
- Добавлен: 24.01.2023
- Размер: 5 MB
- Закачек: 1
Описание
Состав проекта
![]() |
![]() |
![]() ![]() ![]() ![]() |
![]() ![]() ![]() |
![]() ![]() ![]() ![]() |
![]() ![]() ![]() ![]() |
![]() ![]() ![]() ![]() |
![]() ![]() ![]() ![]() |
![]() ![]() ![]() ![]() |
![]() ![]() ![]() ![]() |
![]() ![]() ![]() ![]() |
![]() ![]() ![]() ![]() |
![]() ![]() ![]() ![]() |
![]() ![]() ![]() ![]() |
![]() |
![]() ![]() ![]() |
![]() ![]() ![]() |
![]() ![]() ![]() |
![]() ![]() ![]() |
![]() ![]() ![]() |
![]() ![]() ![]() |
![]() ![]() ![]() |
![]() ![]() ![]() |
![]() ![]() ![]() |
![]() |
![]() ![]() ![]() |
![]() ![]() ![]() |
![]() ![]() ![]() |
![]() ![]() ![]() |
![]() ![]() ![]() ![]() |
![]() ![]() ![]() |
![]() ![]() ![]() |
![]() ![]() ![]() |
![]() ![]() ![]() |
![]() |
![]() ![]() ![]() |
![]() ![]() ![]() |
![]() ![]() ![]() |
![]() ![]() ![]() |
![]() ![]() ![]() |
![]() ![]() ![]() |
![]() ![]() ![]() |
![]() ![]() ![]() |
![]() ![]() ![]() |
![]() ![]() ![]() |
![]() ![]() ![]() |
![]() ![]() ![]() |
![]() ![]() ![]() |
![]() ![]() ![]() |
Дополнительная информация
конвейер винтовой.cdw

наладка 015.cdw

наладка 065.cdw

Корпус.cdw

цех.cdw

Заготовка.cdw

экономика.cdw

Калибр.cdw

сборочный.cdw

Сравнение.cdw

Фреза.cdw

зажимное.cdw

030-1.frw

060.frw

075-1.frw

050-4.frw

030-2.frw

005-1.frw

070-2.frw

040-1.frw

045.frw

005-2.frw

065-2.frw

025-1.frw

015.frw

065-1.frw

010.frw

025-2.frw

050-3.frw

050-2.frw

055.frw

040-2.frw

050-1.frw

070-1.frw

075-2.frw

Рекомендуемые чертежи
- 07.09.2016
- 30.04.2024
- 24.01.2023