Проект участка механического цеха по изготовлению деталей СДМ



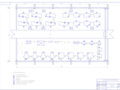
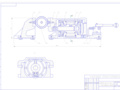
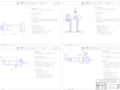
- Добавлен: 25.10.2022
- Размер: 724 KB
- Закачек: 1
Описание
Состав проекта
![]() |
![]() |
![]() ![]() ![]() ![]() |
![]() ![]() |
![]() ![]() |
![]() ![]() ![]() ![]() |
![]() ![]() ![]() ![]() |
![]() ![]() |
![]() |
![]() ![]() ![]() |
Дополнительная информация
цех.dwg

- Рабочее место возле оборудования
- Подвод электрической энергии
- Накопитель деталей
Условные обозначения:
КУРСОВОЕ ПРОЕКТИРОВАНИЕ
Приспособление А2.dwg

с переставными губками
КУРСОВОЕ ПРОЕКТИРОВАНИЕ
Карты эскизов к технологическому процессу1.dwg

Измерительный - штангенциркуль ШЦ-I-125-0.1
Станок вертикально-сверлильный 2Г125
Станок круглошлифовальный 3Б151
Патрон 400 7100-015 ГОСТ 2675-11
Режущий - шлифовальный круг
Измерительный - штангенциркуль
ШЦ-I-125-0.1 ГОСТ 166-80
Станок токарно-копировальный 1716Ц
Режущий - резец Т15К6 ГОСТ 18879-73
Курсовое проектирование
Записка ТОМ.docx
Харьковский национальный автомобильно-дорожный университет
Кафедра технологии машиностроения и ремонта машин
ПОЯСНИТЕЛЬНАЯ ЗАПИСКА
«Технологические основы машиностроения»
«ПРОЕКТ УЧАСТКА МЕХАНИЧЕСКОГО ЦЕХА ПО ИЗГОТОВЛЕНИЮ ДЕТАЛЕЙ СДМ»
Расчетно-пояснительная записка содержит 37 страниц 4 рисунка
В курсовом проекте приведены данные по расчету оптимальных параметров режимов резания технических норм времени рассчитаны элементы крепления детали в приспособлении представлена планировка производственного процесса цеха.
ДЕТАЛЬ МЕТАЛОРЕЖУЩИЙ СТАНОК ТЕХНОЛОГИЧЕСКИЙ ПРОЦЕС РЕЖИМЫ РЕЗАНЬЯ ПРИСПОСОБЛЕНИЯ ПОИЗВОДСТВЕННЫЙ УЧАСТОК
Технологический процесс изготовления детали 6
Расчет припусков и предельных размеров по технологическим переходам на обработку поверхности 7
Расчет режимов резания и нормирование операций технологического процесса .14
Разработка и расчет конструкции приспособления . .32
Проектирование производственного участка цеха 34
Список литературы .38
Степень развития машиностроения определяет технический прогресс данной страны. Широкое освоение передовой технологии автоматизацией и механизацией производства решает одну из важнейших и социальных задач которые ставило перед собой население сделать труд более производительным.
В настоящее время в нашей стране очень велика доля ручного труда механизированного труда особенно на вспомогательных операциях что значительно увеличивает время произведения операции тем самым не способствуя предприятию изготавливающему ту или иную продукций.
Это первый и важный момент в сокращении денежных затрат при производстве новых деталей для автомобильной техники. Указанные трудности успешно преодолеваются в условиях серийного и крупносерийного производства где созданы специализированные автоматические линии гибкие производственные системы по производству деталей автомобильной и другой техники. И здесь важное место и особую роль играет то что последние должны компенсироваться современным модернизированным технологическим оборудованием оснастки и инструментом и все же следует работать над созданием прогрессивных технологических процессов изготовления деталей поскольку технология везде стоит во главе узла.
Вал устанавливается на двух шариковых подшипниках в раздаточной коробке тракторов ХТЗ – 1504 – 09 ХТЗ – 17221 ХТЗ – 16331. Служит для передачи крутящего момента насосу НШ – 50 гидросистемы навески. На шлицах устанавливается шестерня и крепится от передвижения в осевом направлении гайкой М – 16. Шестерня имеет привод от центральной шестерни вращающейся от вала и от коленчатого вала двигателя. Таким образом вал постоянно вращается когда работает двигатель.
Определение размера партии детали и типа производства
Количество деталей в партии
где N – годовая программа в штуках;
n – количество дней запаса ( принимаем n = 7 )
– число рабочих дней в году (принимаем 253)
Пользуясь таблицей определяем что тип производства среднесерийный.
Деталь – вал – изготавливается из углеродистой стали 45 методом штамповки и проходит термическую обработку. Термическая обработка необходима для снятия внутренних напряжений.
ТЕХНОЛОГИЧЕСКИЙ ПРОЦЕСС ИЗГОТОВЛЕНИЯ ДЕТАЛИ
Для изготовления вал-шестерни разработан технический процес изготовления операции которого представлены в таблице 1.1
Наименование и содержание операции
Фрезерно-центровальная
Вертикально-фрезерный станок 6550
Вертикально-сверлильная
Станок вертикально-сверлильный 2П 125
Специальное приспособление
Токарно-копировальная
Станок токарно-копировальный 1716Ц
Патрон 3-х кулачковый
Станок зубофрезерный 5Д312
Станок круглошлифовальный 3Б151
Напильник 2820-0028 ГОСТ 1455-80
Технический контроль
РАСЧЕТ ПРИПУСКОВ И ПРЕДЕЛЬНЫХ РАЗМЕРОВ ПО ТЕХНОЛОГИЧЕСИМ ПЕРЕХОДАМ НА ОБРАБОТКУ ПОВЕХНОСТИ
Технологический маршрут обработки поверхности состоит из обтачивания предварительного и окончательного и шлифования предварительного и окончательного. Обтачивание и шлифование производится в центрах.
Записываем технологический маршрут обработки в таблицу а так же записываем соответствующие заготовке и каждому технологическому переходу значения элементов припуска. Так как в данном случае обработка ведется в центрах то погрешность установки в радиальном направлении равна нулю что имеет значение для рассчитываемого размера. В этом случае эта величина исключается из основной формулы для расчета минимального припуска и соответствующую графу можно не включать в расчетную таблицу.
1. Суммарное отклонение:
где ρСМ – суммарное отклонение смещения (принимаем ρСМ = 06);
ρКОР – погрешность короблению:
мкм (ρКОР = 0013 мм)
ρЦ – суммарное значение при центрировании заготовки
2. Допуск на поверхности используемые в качестве базовых рассчитываем по формуле:
где Нед – недоштамповка
ИШ – износ ручья штампа (ИШ =07)
Ку – коэффициент колебания усадки (Ку=10 мкммм)
Маршрут обработки поверхности 30 к6
Черновое обтачивание (предварительное обтачивание);
Чистовое обтачивание;
Предварительное шлифование;
Окончательное шлифование.
3. Остаточная величина пространственного отклонения:
после предварительного обтачивания:
после окончательного обтачивания:
после предварительного шлифования:
4. Расчет минимальных значений припусков производим пользуясь основной формулой:
5. Минимальный припуск:
под предварительное обтачивание:
под окончательное обтачивание:
под предварительное шлифование:
под окончательное шлифование:
6. Графа «Расчетный размер» заполняется начиная с конечного (чертежного) размера путем последовательного прибавления расчетного минимального припуска каждого технологического перехода:
7. Записав в соответствующей графе расчетной таблицы значения допусков на каждый технологический переход и заготовку в графе «Наименьший предельный размер» определим их значения для каждого для каждого технологического перехода округляя расчетные размеры увеличением их значений.
8. Предельные значения припусков определяем как разность наибольших предельных размеров и - как разность наименьших предельных размеров предшествующего и выполняемого переходов:
Полученные данные сводим в таблицу.
Таблица 2.1 - Расчетные значения припусков и предельных размеров по технологическим переходам на обработку поверхности крышки.
9. После составления таблицы производим проверку правильности выполненных расчетов:
4 = 30 – 15 =15 мкм;
3 = 100 – 30 =70 мкм;
2 = 350 – 100 =250 мкм;
1 = 2500 – 350 =2150 мкм.
РАСЧЕТ РЕЖИМОВ РЕЗАНИЯ
1. Расчет режимов резания при фрезеровании
Станок вертикально-фрезерный 6550
Инструмент – торцевая фреза со вставными ножами с пластинами из твердого сплава: D = 250 z=24
1.1. Определение глубины резания
1.2. Установление ширины
1.3. Определение подачи на режущий инструмент
Принимаем SZср=02 ммзуб
1.4. Определение периода стойкости фрезы
1.5. Расчет скорости резания при фрезеровании
где CV=332 – коэффициент учитывающий группу обрабатываемости материала;
q=02 – показатель степени принимаемый согласно справочника;
m=02 – показатель степени принимаемый согласно справочника;
Y=04 – показатель степени принимаемый согласно справочника;
K=02 – показатель степени принимаемый согласно справочника;
P=0 – показатель степени принимаемый согласно справочника;
где Kr=11 коэффициент учитывающий качество обрабатываемого материала;
=1200 МПа – временные напряжения;
KПV=08- коэффициент учитывающий состояние поверхности заготовки;
KUV=065- коэффициент учитывающий материал инструмента;
1.6. Расчет частоты вращения шпинделя станка
По паспортным данным станка принимаем nд=200 обмин.
1.7. Рассчитаем действительную скорость фрезерования
1.8. Расчет тангенциальной силы фрезерования
где CP=825 – коэффициент учитывающий группу обрабатываемости материала;
q=13 – показатель степени принимаемый согласно справочника;
W=02 – показатель степени принимаемый согласно справочника;
Y=075 – показатель степени принимаемый согласно справочника;
K=11 – показатель степени принимаемый согласно справочника;
1.9. Расчет мощности резания при фрезеровании
1.10. Проверка достаточности мощности привода станка
25>92 следовательно резание возможно.
1.11. Техническое нормирование операции
i=1 (число рабочих ходов).
2.Рассчет режимов резания при сверлении
Материал заготовки сталь 45 МПа сверло Р6М5.
Станок вертикально-сверлильный 2П125
2.1. Определение глубины резания
2.2. Определение подачи на режущий инструмент
Принимаем S = 021 ммоб
2.3. Определение периода стойкости инструмента
2.4. Расчет скорости резания при сверление
где = 98 – коэффициент учитывающий группу обрабатываемости материала;
q = 04 – показатели степени принимаемые согласно справочника;
y = 05 – показатели степени принимаемые согласно справочника;
= 019 – общий поправочный коэффициент на скорость резания
2.5. Определение частоты вращения сверла
Принимаем по паспортным данным станка n = 250 мин-1
2.6. Определяем скорость резания по станку:
2.7. Расчет крутящего момента при сверлении
q = 02 – показатели степени принимаемые согласно справочника;
y = 08 – показатели степени принимаемые согласно справочника;
2.8. Расчет мощности резания при сверлении
2.9. Расчет основного времени на сверление
3. Расчет режимов резания и техническое нормирование копировально-токарной операции
Материал заготовки сталь 45
Резец с пятигранными пластинами Т15К6
Рис. 3.1 – Эскиз токарной обработки
3.1. Определение глубины резания
3.2. Определение подачи
Принимаем среднюю величину подачи
Назначение стойкости режущего инструмента Т = 60 мин.
3.3. Расчет величины скорости резания
x=015-показатель степени (таб.17 ст. 269)
y=035-показатель степени (таб.17 ст. 269)
m=02-показатель степени (таб.17 ст. 269)
Значения коэффициентов периода стойкости Т и показателей степени принимаем из таблицы а общий поправочный коэффициент на скорость резания учитывающий фактические условия резания
где - коэффициент учитывающий качество обрабатываемого материала;
- коэффициент учитывающий состояние поверхности заготовки;
- коэффициент учитывающий материал инструмента.
3.4. Расчет частоты вращение шпинделя станка
Корректируем расчетную частоту вращения шпинделя станка по паспортным данным станка 1716Ц ().
3.5. Расчет действительной скорости резания
3.6. Расчет тангенциальной составляющей силы резания
где -поправочные коэф. учитывающие влияние геометричкских параметров режужей части на состав сил резания. Численные значения этих коэффициентов приведены в таблицах справочника
3.7. Определение мощности резания затрачиваемой на точение детали
3.8. Расчет мощности шпинделя
3.9. Проверка достаточности мощности привода станка для резания
Процесс резания возможен
3.10. Определение основного времени
L – общая длинна обрабатываемой поверхности.
l3 = 2 мм – величина перебега резца.
4. Расчет режимов резания при шлифовании
Станок шлифовальный ЗТ 161
Инструмент – круг шлифовальный DK=600 мм; nK=1112 обмин; B=80 мм; диаметр заготовки d=306 мм
4.1. Определение скорости вращения шлифовального круга
по ГОСТ 2424-83 до 35 мсек рассчитана верно
4.2. Скорость вращения детали
Принимаем Vд = 40 ммин
4.3. Определяем значение продольной подачи шлифовального круга
4.4. Расчет мощности на шлифование
d=306 - диаметр шлифования;
коэффициенты CN находим по справочнику[табл. 56 стр.303]
4.5. Проверка достаточности мощности станка
4.6. Расчет основного времени на шлифование
k=1 – коэффициент учитывающий условия работы.
РАСЧЕТ КОНСТРУКЦИИ ЭЛЕМЕНТОВ ПРИСПРОСОБЛЕНИЯ
1 Принцип работы и строение гидравлических тисков
Все более широкое распространение получают пневмогидравлические и гидравлические тиски различных конструкций. При повышенных давлениях жидкости они обладают большой компактностью. На рисунке 5.1 показаны гидравлические тиски питание которых жидкостью под давлением может производиться от групповой гидроаккумуляторной или от индивидуальной пневмогидравлической установки.
У этих тисков правая и левая части могут быть самостоятельно установлены и закреплены на столе станка что расширяет диапазон габаритов закрепляемых заготовок. Закрепление заготовок производиться посредством гидравлического привода поворотного типа встроенного в корпус стойки 3. Масло под давлением 50 60кгссм2 подается к фланцу 5 через трубку 7 и далее через отверстие во фланце 5 в полость А заставляя гайку 4 поворачиваться. При этом повороте винт 2 вместе с подвижным корпусом 1 перемещается влево зажимая заготовку 9.
При переключении направления потока масла посредством крана управления 6 происходит изменение поворота ротора а следовательно изменение направления движения винта 2при котором происходит раскрепление заготовки 9. винтовая пара 2 и 4 – самотормозящая что позволяет после закрепления заготовки снимать давление масла в гидроцилиндре. Для уменьшения потерь на преодоление трения гайка 4 смонтирована на радиально- упорных роликовых подшипниках 8.
Рисунок 4.1-Гидравлические тиски с переставными губками
2 Расчет параметров гидравлического привода
Исходными данными для расчета гидропривода являются:
- время зажима заготовки ;
- номинальное давление рабочей жидкости .
Секундная подача насоса определяется по формуле
где объемный КПД насоса;
Мощность потребляемая приводом насоса
где механический КПД насоса;
Внутренний диаметр всасывающего трубопровода определяется по эмпирической зависимости
где - минутная подача насоса;
- скорость протекания рабочей жидкости;
ПРОЕКТИРОВАНИЕ ПРОИЗВОДСТВЕННОГО УЧАСТКА ПРЕДПРИЯТИЯ
В соответствии с ОН ТП 02 – 86 принимает для производственного участка следующие режимы работы: пятидневная рабочая неделя продолжительность 40 час количество рабочих дней в году 253 количество смен 2.
Действительный годовой фонд режима работы
Количество единиц оборудования
1. Расчет нормированной численности основных и вспомогательных рабочих специалистов и служащих
Количество основных производственных рабочих
где T – трудоемкость работы;
- действительный фонд работы;
Принимаем m = 56 рабочих.
Количество дополнительных работников для основного вспомогательного производства а так же специалистов сотрудников МОП следует принимать в пределах 30 % от производственников. Количество специалистов – 18% сотрудников – 5% МОП – 1% от общего количества основных и вспомогательных работников.
Количество вспомогательных рабочих
Количество специалистов
Количество служащих
Количество младшего обслуживающего персонала
Расчет количества основного оборудования
К основному оборудованию относится оборудование предназначенное для выполнения технологических операций.
Общее количество оборудования распределяем по типам производства:
зубо – фрезерные 7 шт
2.Расчет величины площади проектируемого участка
Производственная площадь
N – количество единиц оборудования;
f – удельная площадь приходящаяся на единицу оборудования f = 610 м2;
K – коэффициент громосткости учитывающий проезды проходы и рабочие зоны;
где Н – ширина участка цеха м.
Поскольку нам необходимо обеспечить шаг колонн равный 6 метрам то длину участка цеха принимаем 30 метров. Соответственно пересчитываем площадь участка цеха:
На участке площадью 540 происходит расположение робочего оборудования согласно требованием с СНиП.
Косиловой А.Г. Мещеряков Р.К. «Справочник технолога машиностроителя»
Горбацевич А.Ф. «Проектирование дорожного машиностроения»
И.М. Колесов «Основы технологии машиностроения»
А.А. Маталин «Технология машиностроения»
Егоров «Проектирование производственных цехов»
Горошкин «Проектирование станочных приспособлений»
Курсовое проектирование по технологии машиностроения под ред. Горбацевича А.Ф.
Рекомендуемые чертежи
- 24.01.2023
- 07.09.2016
- 24.01.2023