Настройка зубодолбежного 514 и токарно-винторезного 16к20п станков на обработку деталей




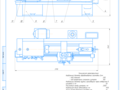
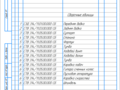
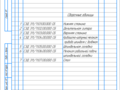
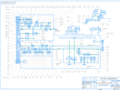
- Добавлен: 25.01.2023
- Размер: 2 MB
- Закачек: 1
Описание
Настройка зубодолбежного 514 и токарно-винторезного 16к20п станков на обработку деталей
Состав проекта
![]() |
![]() |
![]() ![]() ![]() ![]() |
![]() ![]() ![]() |
![]() ![]() ![]() |
![]() ![]() ![]() ![]() |
![]() ![]() ![]() |
![]() |
![]() ![]() ![]() ![]() |
![]() ![]() ![]() ![]() |
![]() ![]() ![]() |
![]() |
![]() |
![]() ![]() ![]() ![]() |
![]() ![]() ![]() ![]() |
![]() ![]() ![]() ![]() |
![]() ![]() ![]() ![]() |
Дополнительная информация
Спецификация2.spw

Ведомость технического проекта
Белорусско-Российский университет
Пояснительная записка
СТВ 31411.00.00.000 КЗ
Схема кинематическая
Гитара сменных колес
Записка ток.docx
характеристики станка 16К20П. Основные узлы принцип работы и движения
2 Назначение и обоснование выбора материала режущего
3 Описание кинематической схемы станка 16К20П. Уравнения кинематического баланса29
4 Определение оптимальных режимов обработки42
5 Мероприятия по технике безопасности42
Список использованных источник52
Настройка токарно-винторезного станка 16К25
1 Область применения назначение и технические характеристики станка 16К25. Основные узлы принцип работы и движения в станке 16К25
Станок 16К20П повышенной точности и выполнен на базе 16К20.
Станок 16К20П имеет широкие технологические возможности на нем можно обрабатывать детали как из незакаленной так и закаленной стали а также из труднообрабатываемых материалов. При использовании литого основания образующего со станиной рамную конструкцию возросла жесткость упругой системы станка что позволило увеличить виброустойчивость станка и точность обработки. В качестве шпиндельных опор применены подшипники особо высокой точности. Поэтому станок имеет повышенную жесткость шпиндельного узла и общую жесткость конструкции. Это позволяет вести обработку с большими силами резания полностью используя мощность привода
Для увеличения надежности и долговечности работы станка применена централизованная система обильного смазывания шпиндельной бабки и коробки подач причем масло поступающее в систему подвергается двойной очистке. Введены устройства для централизованного смазывания направляющих станины и суппорта.
Задняя бабка станка установлена на аэростатической опоре что значительно снижает давление при ее перемещении и изнашивание направляющих станины. Форма передней призматической направляющей станины выбрана с углами обеспечивающими более равномерное распределение износа по граням направляющих. Верхние и нижние направляющие станины закалены; они так же как и ходовой винт и валик надежно защищены от попадания мелкой стружки и пыли.
Применение перечисленных выше конструктивных и технологических усовершенствований а также использование для изготовления основных деталей материалов с повышенной износостойкостью привело к увеличению расчетного срока службы станка 16К20П до первого капитального ремонта до 10 лет. Область применения данного станка – единичное и мелкосерийное производство. Будучи снабжённым приспособлениями станок 16К20П может применяться в массовом производстве [7].
Таблица 2.1 – Техническая характеристика станка [8]:
Наибольший диаметр обрабатываемой заготовки:
-над поперечными салазками суппорта мм
Наибольший диаметр прутка проход. через отверстие в шпинделе
Расстояние между центрами
Наибольшая длина обтачивания
Число частот вращения шпинделя
Пределы частот оборотов прямого вращения
Пределы шагов нарезаемых резьб:
-дюймовых число ниток на 1 дюйм
Мощность электродвигателя главного привода кВт
Частота вращения вала электродвигателя
Рисунок 2.1 – Общий вид токарно-винторезного станка 16К20П
Рисунок 2.2 – Основные узлы токарно-винторезного станка 16К20П
Основные узлы станка 16К20П (см. рисунок 2.2):
- гитары сменных шестерен;
– электропусковая аппаратура;
- коробка скоростей;
Станина 4 служит для монтажа всех основных узлов станка и является его основанием. Наиболее ответственной частью станины являются направляющие по которым перемещаются каретка суппорта и задняя бабка.
Передняя бабка 1 закреплена на левом конце станины. В ней находится коробка скоростей станка основной частью которой является шпиндель. В некоторых станках коробка скоростей размещена в передней тумбе станины. В этом случае она связана со шпинделем ременной передачей. Такие станки называют станками с разделенным приводом.
Задняя бабка 3 служит для поддержания обрабатываемой заготовки при работе в центрах а также для закрепления инструментов при обработке отверстий (сверл зенкеров разверток) и нарезания резьбы (метчиков плашек). Задняя бабка станка 16К25 имеет плиту и может перемещаться по направляющим станины. Так же задняя бабка имеет пневматическое устройство которое служит для создания воздушной подушки облегчающей перемещение бабки по станине и снижающей изнашивание направляющих.
Коробка подач 10 служит для передачи вращения от шпинделя или от отдельного привода ходовому валу или ходовому винту а также для изменения их частоты вращения для получения необходимых подач или определенного шага при нарезании резьбы. Это достигается изменением передаточного отношения коробки подач. Коробка подач связана со шпинделем станка гитарой со сменными зубчатыми колесами. Муфты служат для передачи напрямую вращения ходовому винту и ходовому валику.
Фартук 6 предназначен для преобразования вращательного движения ходового вала и ходового винта в прямолинейное поступательное движение суппорта.
Суппорт 2 служит для закрепления режущего инструмента и сообщения ему движений подачи. Суппорт состоит из каретки (нижних салазок) которая перемещается по направляющим станины поперечных салазок скользящих по направляющим каретки поворотной части с направляющими по которым перемещается резцовая каретка (верхняя каретка). Поворотную часть суппорта можно устанавливать под углом к линии центров станка. У суппорта имеется задний резцедержатель который устанавливают на поперечных салазках и используют для прорезания канавок.
Резцедержатель станка 16К20П можно фиксировать и надежно закреплять с помощью конусного сопряжения с опорой. Фиксация в основных четырех положениях осуществляется подпружиненным шариком расположенным в резцедержателе и заскакивающим в гнезда конусного основания. При повороте резцедержателя рукояткой вначале колпак сходит по резьбе с центрального винта опоры затем подпружиненные фрикционные колодки связанные со штифтами прижимаются к расточке колпака и таким образом передают вращение на резцедержатель.
При зажиме вначале поворачивается колпак вместе с резцедержателем а после колпак преодолевая трение колодок навинчивается на винт окончательно надежно закрепляя резцедержатель [7].
Главным движением определяющим скорость резания является вращение шпинделя несущего заготовку.
Движением определяющим величины продольных и поперечных подач является движение суппорта на котором установлены резцы а при обработке детали концевым инструментом движение подачи получает задняя бабка или пиноль задней бабки [9].
Вспомогательными движениями в станке являются:
-ускоренная продольная и поперечная подача;
-ручное перемещение каретки (при обработке конических поверхностей);
-ручное перемещение пиноли задней бабки (только перемещение).
2 Назначение и обоснование выбора материала режущего инструмента
Основным инструментом при обработке на токарно-винторезных станках является резец.
Резец – это однолезвийный инструмент для обработки деталей с поступательным или вращательным главным движением резания и возможностью движения подачи в любом направлении.
Резец является наиболее распространенным инструментом его применяют на токарных револьверных карусельных расточных строгальных и долбежных станках токарных автоматах и полуавтоматах и на многих специальных станках.
В зависимости от вида станка и рода выполняемой работы применяют резцы различных типов отличающихся по назначению форме конструкции и размерам.
Резцы различают по следующим признакам:
Проходные резцы предназначены для обработки наружных цилиндрических
поверхностей. Проходные резцы могут быть прямыми и отогнутыми. Отогнутые резцы получили широкое распространение из-за универсальности позволяющей вести обработку не только цилиндрических но и торцовых поверхностей с поперечной подачей. Проходные упорные резцы имеют угол в плане φ = 90° их применяют при обтачивании ступенчатых валиков и при обработке нежестких деталей.
Подрезные предназначены для обработки торцовых поверхностей перпендикулярных оси вращения детали эти резцы работают с поперечной подачей.
Расточные предназначены для обработки отверстий.
Отрезные для отрезки заготовок или обработанных из прутка деталей. Резьбонарезные предназначены для нарезания резьбы.
Резцы для контурного точения обеспечивают возможность обработки тел вращения с фасонной образующей на станках с ЧПУ и на станках с копировальными устройствами. Эти резцы имеют увеличенные вспомогательные углы в плане.
Фасонные резцы предназначены для обработки деталей сложного профиля на токарных револьверных станках автоматах и полуавтоматах [3].
По характеру обработки: черновые чистовые для тонкого точения.
По установке относительно детали: радиальные тангенциальные.
По направлению подачи: правые левые.
По конструкции головки: прямые отогнутые изогнутые оттянутые.
По сечению корпуса: прямоугольные; квадратные круглые.
По конструкции: цельные; составныесборные.
По материалу рабочей части: из инструментальных сталей из твердого сплава из керамических материалов из алмаза из сверхтвердых синтетических материалов.
Рабочая часть резца представляет собой клин который под действием приложенного усилия деформирует слой металла после чего сжатый элемент металла скалывается и сдвигается передней поверхностью резца. При дальнейшем продвижении резца процесс скалывания повторяется и из отдельных элементов образуется стружка [10].
В качестве материала для режущей части наиболее часто используют спечённые твёрдые сплавы состоящие из карбидов вольфрама (WC) титана (T цифры в вольфрамовой группе – количество (процентный объём) кобальта а остальное карбид вольфрама; первые цифры в титановольфрамовой группе – количество карбида титана вторые – количество кобальта а остальное карбид вольфрама. Первые цифры в титано-тантало-вольфрамовой группе – суммарное процентное количество карбидов титана и тантала вторые – количество кобальта а остальное карбид вольфрама.
Твёрдые сплавы используют в виде пластинок определённой формы и размеров которые получают путём прессования порошков карбидов и кобальта в изделия необходимой формы и последующего спекания при 1250 – 1450 °С в атмосфере водорода или в вакууме. Твёрдосплавные пластинки припаивают к стержням резцов медными или латунными припоями или крепят механическим способом. Марку материала твердосплавной пластинки вместе с товарным знаком завода-изготовителя клеймят на боковой поверхности стержня.
Теплостойкость твёрдых сплавов 800 – 1000 °С.
Карбиды вольфрама и титана обеспечивают сплавам высокую твёрдость теплостойкость и износостойкость а добавка тантала увеличивает усталостную прочность снижает склонность к трещинообразованию при циклических изменениях температуры; кобальт обеспечивает сплавам необходимую прочность и связывает порошки карбидов.
Инструментами из сплавов группы ВК обрабатывают чугуны цветные металлы пластмассы а также весьма прочные закалённые стали.
Сплавы ТК имеют высокую износостойкость и теплостойкость и поэтому их применяют для обработки сталей дающих сливную стружку.
Трёхкарбидные сплавы применяют при тяжёлых условиях резания например строгании сталей с большими сечениями срезаемого слоя металла а также чистовой и получистовой обработке жаропрочных сталей [9].
С учетом выше сказанного для обработки заданной поверхности выбираем резец проходной 2100-0029 по ГОСТ 18878-73 ГОСТ 5688-61 и [4] оснащённый твердосплавной пластиной Т15К6. Основные размеры выбранного резца: L=125 мм h=20 мм b=16 мм f=13 мм P=32 мм l=9 мм.
Рисунок 2.3 – Подобранный резец
3 Описание кинематической схемы станка 16К25. Уравнения кинематического баланса
Рисунок 2.4 – Кинематическая схема станка 16К25
Привод главного движения
Вращение шпинделю передается от электродвигателя (N = 10 кВт; n = 1460 мин-1) через клиноременную передачу 146268 и коробку скоростей. Муфта М1 служит для включения выключения и изменения направления вращения шпинделя.
Движение от асинхронного электродвигателя на шпиндель может передаваться по двум кинематическим цепям:
а) по короткой цепи (без перебора) что дает 12 высших ступеней частот вращения шпинделя:
б) по длинной цепи (с перебором) что дает еще 12 частот вращения:
Таким образом шпиндель станка получает всего 24 значения частот вращения. Практически же шпиндель имеет только 22 частоты вращения так как значения n = 500 мин-1 и n = 630 мин-1 повторяются дважды. Станок должен быть налажен на заранее подобранную по режимам резания частоту вращения. Максимальная частота вращения шпинделя (при работе без перебора)
Минимальная (при работе с перебором)
Привод подач состоит из звена увеличения шага механизма реверса гитары сменных колес коробки подач и механизма передач фартука. Движение подачи осуществляется или непосредственно от шпинделя через пару зубчатых колес как показано на схеме (нормальное соединение) или через звено увеличения шага которое расположено в коробке скоростей и имеет три передаточных отношения:
Для изменения направления вращения ходового винта служит реверсивный механизм. Правое вращение винта производится через пару зубчатых колес левое - через передачу .
Дальше вращение передается сменным зубчатым колесам гитары: передачу применяют при нарезании метрических и дюймовых резьб и для подачи по ходовому валу.
Коробка подач имеет две основные кинематические цепи. Одна цепь служит для нарезания дюймовых резьб (16 вариантов):
Другая цепь предназначена для нарезания метрических резьб (16 вариантов):
В первом случае ходовой винт получает движение когда муфты М2 М3 и М4 выключены а М5 включена. Во втором случае муфта М2 выключена а муфты М3—М5 включены. Вторую кинематическую цепь используют также для получения продольной или поперечной подач при этом вращение с вала XVIII на ходовой вал передается через зубчатые колеса . Муфта М5 выключена.
При нарезании резьбы с повышенной точностью движение на ходовой винт передается напрямую т. е. коробка подач отключена а муфты М2 и М5 включены. Аналогично нарезают специальные резьбы. В обоих случаях резьбу на требуемый шаг настраивают подбором сменных зубчатых колес гитары.
Коробка подач станка состоит из основной и множительной передач. Первая дает возможность получать основной ряд стандартных резьб. Множительная передача предназначена для увеличения (в 4 раза) числа нарезаемых на станке стандартных резьб.
От ходового вала XXII вращение через передачу предохранительную муфту Мп и червячную пару передается зубчатому колесу z = 36. От этого зубчатого колеса движение на реечное колесо z = 10 для осуществления продольной подачи (правой или левой) происходит через передачи (включена муфта М8) или (включена муфта М7). Поперечная подача (правый или левый ход) включается муфтами М9 или М10. При этом движение винту поперечной подачи передается через передачу (включена муфта М9) или (включена муфта М10). Наличие в коробке подач муфты обгона М6 позволяет сообщать суппорту ускоренное движение от вспомогательного электродвигателя без выключения рабочей подачи.
Кинематическая цепь подачи связывающая шпиндель с ходовым валом должна обеспечивать за один оборот шпинделя перемещение суппорта на величину подачи S следовательно уравнение кинематического баланса для этой цепи имеет вид
об. шпинделя iпост iрев iгит iк.п. iфmzp=S ммоб(38)
где zp — число зубьев реечного колеса; m — модуль реечного колеса.
Общее уравнение кинематической цепи прямых продольных подач при положении блока зубчатых колес Б5 следующее:
Быстрые перемещения
Быстрые перемещения суппорта осуществляются от отдельного электродвигателя (N = 1 кВт; n — 1360 мин-1) расположенного с правой части станины станка.
Уравнения кинематических цепей от шпинделя к ходовому винту при нарезании резьбы составляют из условия чтобы за один оборот шпинделя суппорт с резцом переместился вдоль оси заготовки на шаг Р нарезаемой резьбы (при однозаходной резьбе).
Для нарезания метрической резьбы со стандартным шагом Р (в этом случае передача к коробке подач осуществляется непосредственно от шпинделя минуя звено увеличения шага) уравнение кинематической цепи от шпинделя к ходовому винту имеет следующий вид:
Для нарезания дюймовой резьбы с шагом Р (для дюймовой резьбы P=253k мм где k— число ниток на 1) уравнение кинематической цепи имеет вид:
Уравнение кинематической цепи от шпинделя к ходовому винту для нарезания резьбы повышенной точности с шагом Р имеет вид:
Резьбу с большим шагом нарезают используя звено увеличения шага т.е. передача движения от шпинделя в этом случае осуществляется не через зубчатые колеса а через звено увеличения шага в коробке скоростей.
На шпиндельной бабке станка помещена таблица частот вращения шпинделя подач и шагов нарезаемых резьб. Устанавливая рукоятки в соответствующие положения получают различные частоты вращения шпинделя. Первая рукоятка служит для установки подачи и шага резьбы и отключения механизма коробки подач при нарезании резьб повышенной точности. Она может занимать четыре фиксированных положения обозначенных буквами А В С и D и два промежуточных обозначенных стрелками при повороте в вертикальной плоскости. Четыре фиксированных положения I II III и IV может занимать вторая рукоятка служащая также для установки подачи и шага резьбы. Комбинируя положения первой и второй рукояток можно получить все значения подач и шагов резьбы.
Табличные значения подач могут быть получены только при установке сменных зубчатых колес . Установкой на станке сменных зубчатых колес создается возможность нарезания метрических и дюймовых резьб с шагами равными удвоенным значениям. Эти же сменные зубчатые колеса используют для получения удвоенных величин подач по сравнению с табличными значениями.
При дополнительных сменных колесах и сменных колесах основного набора на станке используя механизм коробки подач можно нарезать резьбы шаги которых приведены в другой таблице помещенной на внутренней стенке дверцы кожуха сменных зубчатых колес. Сменные зубчатые колеса для нарезания через механизм коробки подач для нарезания не приведенных в таблицах метрических и дюймовых резьб подбирают по формуле .
4 Определение оптимальных режимов обработки
Исходными данными для настройки на обработку токарно-винторезным станком 16К20П является чертеж детали выданный преподавателем с указанием обрабатываемой поверхности.
Рисунок 2.6 – Чертеж детали с указанием обрабатываемой поверхности для настройки станка 16К20П
Таблица 2.2 – Исходные данные
Диаметр заготовки D мм
Диаметр после обработки d мм
Длина обработки B мм
Обрабатываемый материал
Твёрдость обрабатываемого материала НВ
Материал режущей части
Определение оптимальных режимов обработки
Глубину резания t (в миллиметрах) определим по формуле
где D – диаметр заготовки;
d – диаметр после обработки.
Для определения наивыгоднеших (оптимальных) режимов резания введем ряд следующих ограничений:
– режущие возможности инструмента;
– мощность электродвигателя привода главного движения;
– заданную производительность станка;
– наименьшую возможную скорость резания;
– наибольшую частоту вращения шпинделя;
– наибольшую подачу допустимую прочностью и жесткостью станка;
– наименьшую подачу допускаемую кинематикой станка;
– наибольшую подачу допустимую кинематикой станка;
– наибольшую подачу допустимую требованиями предъявляемыми к шероховатости обработанной поверхности.
Таким образом при расчете оптимальных режимов резания необходимо учитывать минимум ограничений которые оказалось невозможно или нецелесообразно устранить.
Данные ограничения выбираем так как их невозможно или нецелесообразно устранить организационно и они оказывают самое большое влияние при процессе резания. От них напрямую зависит качество обработанной поверхности шероховатость и выбор оптимальных режимов резания. Существует еще несколько ограничений: прочность режущего инструмента и жёсткость технологической системы. Эти ограничения мы устраним организационно. Для повышения жесткости обработки мы будем использовать люнет. Для устранения ограничения по прочности режущего инструмента мы будем использовать инструмент с сечением достаточным для обеспечения обработки на максимальных условиях обработки.
Кроме перечисленных на выбор режимов резания влияют и другие ограничения: жесткость приспособления и обрабатываемой детали вибрации при резании нагрев детали усилие закрепления детали и ряд других. Многие из этих ограничений могут быть устранены при проектировании станка или технологического процесса часть же ограничений в настоящее время еще недостаточно хорошо изучена не поддается расчету и устраняется при экспериментальной проверке режимов резания.
Важнейшим и решающим ограничением является заданная производительность станка или линии так как никакой режим не может быть признан оптимальным если он не обеспечивает требуемой производительности.
Выбранные технические ограничения отражающие с определенной точностью физический процесс резания в совокупности с критерием оптимальности позволяют построить математическую модель процесса резания.
Критерием оптимальности целесообразно принять основное технологическое время.
Для обработки выбираем резец проходной L = 125 сечением державки 4032 мм с углом φ1 = 750 γ = 60 α = 150 r = 15 мм по ГОСТ 18878-73 оснащённый твердосплавной пластиной Т15К6 как в подразделе 2.3.
Уравнение характеризующее первое ограничение для точения выводится как и все последующие ограничения следующем образом [11]: экономическая скорость резания то есть скорость соответствующая экономической стойкости учитывая режущие возможности инструмента экономику производства и организацию инструментального хозяйства определяется для резцов при наружном продольном и поперечном точении по формуле:
Так как при точении всех видов показатели степеней zv uv rv равны нулю а поправочный коэффициент КНБ=200 [11] то получаем формулу:
где m – показатель степени при Тэк;
Сv – постоянный коэффициент учитывающий влияние на скорость резания обрабатываемого материала и другие факторы;
Кv – общий поправочный коэффициент характеризующий условия обработки;
D – диаметр инструмента или места обработки мм;
Тэк – расчетная экономическая стойкость инструмента мин;
t – глубина резания мм;
s – подача на оборот ммзуб;
HБ – твердость материала заготовки по Бринеллю;
xv yv zv nv uv rv – показатели степеней при переменных в формуле скорости резания.
Скорость резания определяемая кинематикой станка выражается формулой:
где n – число оборотов изделия или инструмента мин-1.
Приравнивая правые части формул (35) и (34) получаем:
Выделим в левую часть уравнения элементы режима резания подлежащие определению:
Для приведения полученных уравнений и неравенств технических ограничений и критерия оптимальности к линейным формам необходимо их логарифмировать.
Так как входящие в уравнения величины s t в ряде случаев имеют значения порядка 001 01 мм и им будут соответствовать отрицательные логарифмы. Для того чтобы исключить возможность появления отрицательных логарифмов умножим уравнение на 1000 и произведем соответствующие преобразования.
Логарифмируем правые и левые части полученного уравнения. В результате получаем:
где Т – период стойкости наибольшей производительности мин;
CV – постоянный коэффициент зависящий от условий обработки;
m х у – показатели степеней;
КV – общий поправочный коэффициент;
D – диаметр обработки мм.
Согласно [4 таблица 17] для CV = 350 m = 02; х = 015; у = 035.
Период стойкости соответствующий наибольшей производительности Т мин определим по формуле
Tпр.max = ( – 1) · tСМ(45)
где – величина обратная показателю относительной стойкости m. Для случая когда в качестве инструментального материала принимается твёрдый сплав а в качестве обрабатываемого материала выступает сталь по [11] таблица 4.1] принимаем m = 02;
tСМ – время на смену затупленного инструмента затрачиваемое за период его стойкости мин. Для проходного твердосплавного резца tСМ = 3 мин [11] тогда
Tпр.max = (5 – 1) · 3 = 12 мин.(46)
Общий поправочный коэффициент для скорости резания КV определим по формуле
KV=Kmv · Knv · Kuv(47)
где Kмv – коэффициент учитывающей влияние материала заготовки
Kпv – коэффициент учитывающий состояние поверхности заготовки;
Kuv – коэффициент учитывающий материал инструмента.
где КГ – коэффициент характеризующий группу стали по обрабатываемости по [4 таблица 2] при обработке стали 40Х твердосплавным инструментом КГ = 1;
в- придел текучести [12].
По [4 таблица 5] исходя из того что обрабатываемой заготовкой является прокат с коркой Knv = 09.
По [4 таблице 6] при обработке стали 45 инструментом оснащенным пластиной твёрдого сплава Т15К6 Kuv = 1.
KV = 117 · 09 · 1 = 10547(50)
Обозначив через х1 = ln (n) x2 = ln (1000 S) получим следующее уравнение.
Уравнение первого ограничения:
Х1 + 035Х2 ≤ 14091.(52)
Согласно исходным данным для обработки применяется станок 16К20П с наибольшей длиной обработки 1000 мм и мощностью привода главного движения Nn = 11 кВт; коэффициент полезного действия привода главного движения станка = 08.
Уравнение характеризующее второе ограничение для точения будет иметь вид:
(nZ + 1)1n(n) + YZ · 1n(1000S) ≤ 1n = b2(53)
Согласно [4 таблица 22] для CZ = 300 х = 1 у = 075 nz = -015.
Общий поправочный коэффициент КPZ определим по формуле
KPZ = Kmp · Kφp · Kγp · Kλp · Krp(54)
где Kmp – коэффициент учитывающей влияние материала заготовки;
Kφp – коэффициент учитывающий влияние значения главного угла в плане;
Kγp – коэффициент учитывающий влияние значения переднего угла;
Kλp – коэффициент учитывающий влияние значения угла наклона главного лезвия.
где в- придел текучести [12];
n – показатель степени [4].
По [4 таблица 23] Kφp = 094; Kγр = 10; Kλр = 1.
КPZ = 08878 · 094 · 1 · 1 = 08345(56)
b2 = 1n = 13017.(57)
Уравнение второго ограничения:
5Х1 + 075Х2 ≤ 13017(58)
Уравнение характеризующее третье ограничение (заданную производительность станка) для точения будет иметь вид:
n(n) + 1n(1000S) ≥ 1n = b3(59)
где L – длина рабочего хода инструмента мм.
у = 3 – величина врезания резца мм.
LPX = 595 + 3=598 мм(61)
Продолжительность цикла работы станка выражается следующей формулой:
где КЗ – коэффициент загрузки станка принимается в зависимости от типа производства. В нашем случае обработка осуществляется в условиях среднесерийного производства. Для этого типа производства K3 = 075 085.
rR =1 – число деталей обрабатываемых одновременно на одной позиции;
R – заданная производительность станка штч;
tВ – вспомогательное время мин.
Время цикла можно выразить и таким образом:
где ТО =04477 – основное технологическое время мин [12];
ТВ.Н – вспомогательное неперекрываемое время мин по [12 с. 101–105; 197–221].
Сумма всех вспомогательных неперекрываемых времён при работе состоит из затрат на отдельные приёмы ТBH.
ТBH = ТУС + ТЗО + ТУП + ТИЗ(62)
где ТУС – время на установку и снятие детали мин;
ТЗО – время на закрепление и открепление детали мин;
ТУП – время на приёмы управления мин;
ТИЗ – время на измерение детали мин.
При определении ТBH используем сведения и нормативную информацию приведённую в [12 с. 101–105; 197–221].
Туп = 2001+0025=0045 мин(65)
ТBH = 008 +0024 +0045 + 012=0269(67)
ТЦ = ТО + ТВ.Н=01049 + 0269=03739 мин.(54)
Тогда из формулы (53) зададимся производительностью станка:
Коэффициент загрузки станка принимается в зависимости от типа производства. В нашем случае обработка осуществляется в условиях среднесерийного производства. Для этого типа производства K3 = 075 085.
Уравнение третьего ограничения:
Уравнение характеризующее четвёртое ограничение (наименьшую скорость резания) для точения будет иметь вид:
Первая часть уравнения в скобках характеризует выбор минимальной скорости резания исходя из вида обработки и условий обработки. Так как для обработки применяется твердосплавный инструмент то целесообразность использования наступает от скорости резания Vmin = 50ммин [11] тогда частота вращения шпинделя соответствующая обработке нашей детали при принятой минимальной скорости nmin мин-1 определится по формуле
nmin = = 4823 мин-1(71)
По паспорту станка наименьшая частота вращения шпинделя nmin = 125 мин-1. Соответственно лимитирующей частотой вращения будет частота соответствующая скорости Vmin = 50 ммин и коэффициент рассчитаем по формуле
Уравнение четвертого ограничения будет иметь вид:
Получим значения соответствующие пятому ограничению. Рассмотрим общее уравнение учитывающее и максимальную скорость резания исходя из режущих способностей твердосплавного инструмента и максимальную скорость резания которую можно получить для данных условий обработки исходя из кинематики станка.
Как правило теплостойкость твердосплавного инструмента достаточно высока и главным ограничивающим фактором при выборе верхнего предела скорости резания при расчёте данного ограничения является наибольшая частота вращения по станку nст.max. По паспорту станка наибольшая частота вращения шпинделя nст.max = 1600 мин-1.
n(n) ≤ 1n(nCT.max) = b5(75)
b5 = 1n(1600) = 738(76)
Уравнение пятого ограничения будет иметь вид:
Уравнение характеризующее шестое ограничение (прочность механизма подачи станка) для точения будет иметь вид:
nS · 1n(n) + YS · 1n(1000S) ≤ 1n = b6(78)
Согласно паспорту станка наибольшее усилие допускаемое механизмом продольной подачи РCT.ДОП = 5884 Н.
Согласно [4 таблица 22] для СS = 339; ХS = 10; УS = 05; nS = -04.
Общий поправочный коэффициент КX определим по формуле
KS = Kmp · Kjp · Kγp · Kλp · Krp(79)
КMP = 08878; Kφp = 094; Kγp = 10; Kλp = 1; Krp = 10; KS = 1.
Уравнение шестого ограничения будет иметь вид:
-04Х1 + 05Х2 ≤ 029(81)
Уравнение характеризующее седьмое ограничение (наименьшая подача допускаемая кинематикой станка по паспарту [7]) для точения будет иметь вид:
n(1000S) ≥ 1n(SCT.min · 1000) = b7(82)
b7 = 1n(005 · 1000) = 391.(83)
Уравнение седьмого ограничения будет иметь вид:
Уравнение характеризующее восьмое ограничение (наибольшая подача допускаемая кинематикой станка по паспарту [7]) для точения будет иметь вид:
n(1000S) ≤ 1n(SCT.mах · 1000) = b8(85)
b8 = 1n(28 · 1000) = 794.(86)
Уравнение восьмого ограничения:
Уравнение характеризующее девятое ограничение (наибольшая подача допустимая требованиями предъявляемыми к шероховатости обработанной поверхности) для точения будет иметь вид:
n(1000S) ≤ 1n( = b9(85)
где Сн – коэффициент характеризующий условия обработки Сн =0008 [12];
r – радиус закругления при вершине резца r=15 [4];
t – глубина резания t= 4[4];
φ – главный угол в плане резца φ = 150 [4];
φ1 – вспомогательный угол в плане резца φ1=750 [4];
y – показатель степени y=14 [4];
u – показатель степени u=07 [4];
z – показатель степени z=035 [4];
Уравнение девятого ограничения:
В результате произведённых расчётов мы получили систему уравнений характеризующих процесс резания для данных условий обработки.
Целевая функция имеет вид:
f(x)=Х1 + Х2 max(89)
Найдем графически оптимальные значения Х1 и Х2.
Рисунок 2.7 – Графическое изображение математической модели процесса резания
Из графика Х1опт = 738; Х2опт = 6484.
Теперь найдем оптимальные значения Х1 и Х2 в табличном процессоре Microsoft Excel 2010 при помощи средства анализа “Поиск решения”.
Рисунок 2.8 – Оптимальные значения Х1 и Х2 в табличном процессоре Microsoft Excel 2010 при помощи средства анализа “Поиск решения”
Полученные графически оптимальные значения Х1 и Х2 полностью соответствуют оптимальным значениям Х1 и Х2 полученным в табличном процессоре Microsoft Excel 2010 при помощи средства анализа “Поиск решения”.
Соответствие оптимальных значений Х1 и Х2 полученных графическим путем и через средство анализа “Поиск решения” видно при сравнении рисунков 2.7 и 2.8 .
Максимальное значение целевой функции при пересечении области значений: Х1опт = 738 Х2опт = 6484.
Оптимальную частоту вращения шпинделя nопт определим по формуле
nопт = ех1 = 16036 мин –1(90)
Оптимальную подачу Sо определим по формуле
S0=ex21000=065 ммоб(91)
Полученные значения режимов резания являются оптимальными для заданных исходных данных. Так как обработка производится на станке с ступенчатым регулирование то полученные значения режимов резания округляем до станочных значений.
5 Мероприятия по технике безопасности
1. Работать только на станках к которым имеется допуск и выполнять работу которая поручена.
2. Сосредоточить внимание на выполняемой работе не отвлекаться на посторонние дела и разговоры не отвлекать других.
3. Не допускать на свое рабочее место лиц не имеющих отношения к порученной работе. Без разрешения мастера не доверять свой работающий станок другому рабочему.
4. Не опираться на станок во время его работы и не позволять делать это другим.
5. Заметив нарушение инструкции другим рабочим предупредить его о необходимости соблюдения требований по технике безопасности.
6. О всяком несчастном случае немедленно поставить в известность мастера или бригадира и обратиться в медицинский пункт.
7. При ремонте станка и пусковых устройств на станке должен быть вывешен плакат: «Не включать — ремонт».
8. Нельзя работать на неисправном и не имеющем необходимых ограждений станке. Не производить ремонт и переделку станка самостоятельно.
9. Не разрешать уборщику убирать у станка во время его работы.
10. Запрещается работать на станке в рукавицах или перчатках а также с забинтованными пальцами без резиновых напальчников.
11. Во избежание несчастных случаев и попадания грязи и стружки в механизмы станка запрещается обдувать воздухом из шланга обрабатываемую поверхность и станок.
12. Надежно и жестко закреплять обрабатываемую деталь на станке.
13.и габаритные размеры обрабатываемой детали должны соответствовать паспортным данным станка.
14. Устанавливать и снимать тяжелые детали и приспособления (массой более 16 кг) только с помощью подъемных механизмов. Не превышать нагрузку установленную для грузоподъемных средств.
15. Пользоваться грузоподъемными механизмами только после специального обучения и аттестации.
16. Деталь должна быть надежно застроплена; для подъема применять специально строповочно-захватные приспособления. Освобождать обрабатываемую деталь от стропов или захватных приспособлений только после надежной установки где надо — и закрепления детали на станке.
17. Отрегулировать местное освещение станка так чтобы рабочая зона была достаточно освещена и свет не слепил глаза. Протереть арматуру и светильник. Пользоваться местным освещением напряжением выше 36 В запрещается.
18. При всяком перерыве в подаче электроэнергии немедленно выключить электрооборудование станка.
19. Если на металлических частях станка обнаружено напряжение (ощущение тока) электродвигатель работает на две фазы (гудит) заземляющий провод оборван остановить станок и немедленно доложить мастеру о неисправности электрооборудования.
20. Если пол скользкий (облит маслом эмульсией) потребовать чтобы его посыпали опилками или сделать это самому.
21. Пользоваться деревянной решеткой и содержать ее в исправном состоянии.
22. Каждый рабочий обязан:
а) требовать от администрации цеха проведения инструктажа по технике безопасности до назначения на работу и при переводе на станок другой модели;
б) требовать от администрации цеха чтобы печатная инструкция о мерах безопасности при работе на данном станке находилась на рабочем месте станочника;
в) строго выполнять все правила безопасности;
г) обязательно пользоваться полагающейся спецодеждой спецобувью и индивидуальными защитными средствами (очками респираторами масками и др.);
д) при обнаружении возможной опасности предупредить товарищей и немедленно сообщить администрации цеха;
е) содержать в чистоте рабочее место в течение всего рабочего дня и не загромождать его деталями заготовками металлическими отходами мусором и т. п.;
ж) укладывать устойчиво на подкладках и стеллажах поданные на обработку и обработанные детали; высота штабелей не должна превышать для мелких деталей
м для средних — 1 м для крупных — 15 м;
з) применять только исправные гаечные ключи соответствующих размеров;
и) при работе ключами не наращивать их трубой или другими рычагами; нельзя пользоваться прокладками если ключи не соответствуют размерам гаек.
к) не мыть руки в масле эмульсии керосине и не вытирать их обтирочными концами загрязненными стружкой;
л) не принимать пищу у станка;
м) не оставлять свою одежду на рабочем месте.
23. На территории выполнять следующие правила:
а) быть внимательным к предупредительным сигналам автомашин и других видов движущегося транспорта;
б) не находиться под поднятым грузом;
в) не проходить в местах не предназначенных для прохода;
г) не заходить без разрешения за ограждения технологического оборудования;
д) не прикасаться к токоведущим частям электрооборудования клеммам и электропроводам к арматуре общего освещения не открывать дверцы электрошкафов; в необходимых случаях обращаться к электромонтеру;
е) не включать и не останавливать (кроме аварийных случаев) станки механизмы работа на которых Вам не поручена.
24. Работая с подручным или учеником обучать его безопасным приемам работы и следить за их выполнением.
25. К работе с грузоподъемными кранами могут быть допущены лица не моложе 18 лет специально обученные систематически инструктируемые сдавшие экзамен квалификационной комиссии и имеющие на руках удостоверение.
Требования безопасности перед началом работы [6]
1. Перед каждым включением станка убедиться что пуск станка никому не угрожает опасностью.
2. Привести в порядок рабочую одежду: застегнуть или подвязать обшлага рукавов надеть головной убор; женщины должны убрать волосы под косынку повязанную без свисающих концов.
3. Проверить хорошо ли убраны станок и рабочее место выявить неполадки в работе станка и принять меры по их устранению.
4. О неисправности станка немедленно заявить мастеру; до устранения неисправности к работе не приступать.
5. Приготовить крючок для удаления стружки ключи и другой необходимый инструмент. Не применять крючок с ручкой в виде петли.
6. Проверить наличие и исправность;
а) ограждений зубчатых колес приводных ремней валиков приводов и пр. а также токоведущих частей электрической аппаратуры (пускателей рубильников трансформаторов кнопок);
б) заземляющих устройств;
в) предохранительных устройств для защиты от стружки охлаждающих жидкостей;
г) устройств для крепления инструмента (отсутствие трещин надломов прочность крепления пластинок твердого сплава или керамических пластинок стружколомающих порогов и пр.);
д) режущего измерительного крепежного инструмента и приспособлений и разложить их в удобном для пользования порядке.
Работать только исправным инструментом и приспособлениями и применять их строго по назначению.
7. Если при обработке металла образуется отлетающая стружка то при отсутствии специальных защитных устройств на станке надеть защитные очки или предохранительный щиток из прозрачного материала.
8. При обработке вязких металлов дающих сливную стружку применять резцы со специальными стружколомающими устройствами.
9. При обработке хрупких металлов (чугуна бронзы и т. д.) дающих отлетающую стружку а также при дроблении стальной стружки в процессе обработки применять следующие защитные устройства: специальные стружкоотводчики прозрачные экраны или индивидуальные щитки (для защиты лица).
10. Проверить на холостом ходу станка:
а) исправность органов управления (механизмов главного движения подачи пуска останова движения и др.);
б) исправность системы смазки и охлаждения (убедиться в том что смазка и охлаждающая жидкость подаются нормально и бесперебойно);
в) исправность фиксации рычагов включения и переключения (убедиться в том что возможность самопроизвольного переключения с холостого хода на рабочий исключена);
г) нет ли заеданий или излишней слабины в движущихся частях станка особенно в шпинделе в продольных и поперечных салазках суппорта.
11. Для предупреждения кожных заболеваний рук при применении на станках охлаждающих масел и жидкостей по указанию врача перед началом работ смазывать руки специальными пастами и мазями.
12. Проверять доброкачественность ручного инструмента при получении его из кладовой:
а) ручка напильника и шабера должна иметь металлическое кольцо предохраняющее ее от раскалывания;
б) молоток должен быть насажен на рукоятку овального сечения расклиненную металлическим клином и изготовленную из твердых и вязких пород дерева; боек молотка должен иметь ровную слегка выпуклую поверхность; нельзя работать молотком со сбитым бойком имеющим трещины или насаженным на рукоятку из дерева мягких пород а также плохо закрепленным на рукоятке:
в) зубило и другой ударный инструмент должны быть длиной не менее 150 мм кернер— 100 мм и не иметь наклепа на бойке;
г) гаечные ключи должны быть исправными и соответствовать размеру гаек; запрещается работать гаечными ключами с прокладками удлинять их трубами и применять контрключи;
д) разложить инструмент и приспособления в удобном для пользования порядке.
13. Пользоваться режущим инструментом имеющим правильную заточку. Применение неисправного инструмента и приспособлений запрещается.
14. Проверить и обеспечить достаточную смазку станка; при смазке пользоваться только соответствующими приспособлениями.
15. Разместить шланги подводящие охлаждающую жидкость так чтобы была исключена возможность соприкосновения их с режущим инструментом и движущимися частями станка. Охлаждающую жидкость подавать только насосом.
16. Запрещается охлаждать режущий инструмент мокрыми тряпками или щетками.
17. Не допускать разбрызгивания масла и жидкости на пол. Для защиты от брызг устанавливать щитки.
Требования безопасности во время работы [6]
1. Выполнять указания по обслуживанию и уходу за станками изложенные в «Руководстве к станку» а также требования предупредительных таблиц имеющихся на станке.
2. Устанавливать и снимать режущий инструмент только после полного останова станка.
3. Не работать без кожуха прикрывающего сменные шестерни.
4. Остерегаться срыва ключа правильно накладывать ключ на гайку и не поджимать им гайку рывком.
5. Во время работы станка не брать и не подавать через работающий станок какие-либо предметы не подтягивать болты гайки и другие соединительные детали станка.
6. Остерегаться наматывания стружки на обрабатываемый предмет или резец не направлять вьющуюся стружку на себя. Пользоваться стружколомателем.
7. Не удалять стружку от станка непосредственно руками и инструментом пользоваться для этого специальными крючками и щетками-сметками.
8. Следить за своевременным удалением стружки с рабочего места и станка.
9. Остерегаться заусенцев на обрабатываемых деталях.
10. При возникновении вибрации остановить станок. Принять меры к устранению вибрации: проверить крепление резца и детали.
11. Обязательно остановить станок и выключить электродвигатель при:
а) уходе от станка даже на короткое время (если не поручено обслуживание двух или нескольких станков);
б) временном прекращении работы;
в) перерыве в подаче электроэнергии;
г) уборке смазке чистке станка;
д) обнаружении неисправности в оборудовании;
е) подтягивании болтов гаек и других соединительных деталей станка;
ж) установке измерении и съеме детали;
з) проверке или зачистке режущей кромки резца;
и) снятии и надевании ремней на шкивы станка.
12. Передвижение ремня по ступенчатым шкивам на ходу допускается только с применением переводок.
13. При обработке деталей применять режимы резания указанные в операционной карте для данной детали.
14. Не увеличивать установленные режимы резания без ведома мастера.
15. При закреплении детали в кулачковом патроне или использовании планшайб следует захватывать деталь кулачками на возможно большую величину. Не допускать чтобы после закрепления детали кулачки выступали из патрона или планшайбы за пределы их наружного диаметра. Если кулачки выступают заменить патрон или установить специальное ограждение.
16. При установке (навинчивании) патрона или планшайбы на шпиндель подкладывать под них на станок деревянные прокладки с выемкой по форме патрона (планшайбы).
17. Устанавливать тяжелые патроны и планшайбы на станок и снимать их со станка при помощи подъемного устройства и специального захватного приспособления.
18. Не свинчивать патрон (планшайбу) внезапным торможением шпинделя. Свинчивание патрона (планшайбы) ударами кулачков о подставку допускается только при ручном вращении патрона; в этом случае следует применять подставки с длинными ручками (для удержания рукой).
19. В кулачковом патроне без подпора центром задней бабки можно закреплять только короткие длиной не более двух диаметров уравновешенные детали; в других случаях для подпора пользоваться задней бабкой.
20. При обработке в центрах деталей длиной равной 12 диаметрам и более а также при скоростном и силовом резании деталей длиной равной восьми диаметрам и более применять дополнительные опоры (люнеты).
21. При обработке деталей в центрах проверить закреплена ли задняя бабка и после установки изделия смазать центр. При дальнейшей работе нужно периодически смазывать задний центр.
22. При работе с большими скоростями применять вращающийся центр прилагаемый к станку.
23. Нельзя работать со сработанными или забитыми центрами.
24. При обточке длинных деталей надо следить за центром задней бабки: периодически центр следует смазывать и проверять осевой зажим.
25. Во избежание травм из-за инструмента необходимо:
а) включить сначала вращение шпинделя а затем подачу; при этом обрабатываемую деталь следует привести во вращение до соприкосновения ее с резцом врезание производить плавно без ударов;
б) перед остановом станка сначала выключить подачу отвести режущий инструмент от детали а потом выключить вращение шпинделя.
26. Резцовую головку отводить на безопасное расстояние при выполнении следующих операций: центровании деталей на станке зачистке шлифовании деталей наждачным полотном опиловке шабровке измерении деталей а при смене патрона и детали отодвигать подальше также задний центр (заднюю бабку).
27. Следить за правильной установкой резца и не подкладывать под него разные куски металла; пользоваться подкладками равными площади резца.
28. Резец следует зажимать с минимально возможным вылетом и не менее чем тремя болтами. Нужно иметь набор подкладок различной толщины длиной и шириной не менее опорной части резца. Не следует пользоваться случайными подкладками.
29. Не затачивать короткие резцы без соответствующей оправки.
30. При подводке резца к оправке или планшайбе соблюдать осторожность и избегать чрезмерно глубокой подачи резца.
31. При надевании планшайбы на конец шпинделя очистить ее от стружки и загрязнения.
32. При обработке вязких металлов дающих сливную ленточную стружку применять резцы с выкрутками накладными стружколомателями или стружкозавивателями.
33. Не пользоваться зажимными патронами если изношены рабочие плоскости кулачков.
34. При скоростном резании на токарных станках работать с невращающимся центром запрещается.
35. Обрабатываемую поверхность располагать как можно ближе к опорному или зажимному приспособлению.
36. При установке детали на станок не находиться между деталью и станком.
37. Не класть детали инструмент и другие предметы на станину станка и крышку передней бабки.
38. При отрезании тяжелых частей детали или заготовок не придерживать отрезаемый конец руками.
39. При опиловке зачистке шлифовании обрабатываемых деталей на станке:
а) не прикасаться руками или одеждой к обрабатываемой детали;
б) не производить указанных операций с деталями имеющими выступающие части пазы и выемки (пазы и выемки предварительно заделывать деревянными пробками);
в) стоять лицом к патрону держать ручку напильника левой рукой не перенося правую руку за деталь.
40. Для обработки деталей закрепленных в центрах применять безопасные поводковые патроны (например чашкообразного типа) или безопасные хомутики.
41. После закрепления детали в патроне вынуть торцовый ключ.
42. При закреплении детали в центрах:
а) протереть и смазать центровые отверстия;
б) не применять центр с изношенными или забитыми конусами;
в) следить за тем чтобы размеры токарных центров соответствовали центровым отверстиям обрабатываемой детали;
г) не затягивать туго задний центр надежно закреплять заднюю бабку и пиноль;
д) следить за тем чтобы деталь опиралась на центр всей конусной частью центрового отверстия; не допускать упора центра в дно центрового отверстия детали.
43. Работать на станке без закрепления патрона сухарями предотвращающими самоотвинчивание при реверсе запрещается.
44. Не тормозить вращение шпинделя нажимом руки на вращающиеся части станка или детали.
45. Проверить крепление и прочность специальных ограждений обеспечивающих безопасность и удобство обслуживания расположенных на уровне 05 м и выше над полом.
Требования безопасности по окончании работы [6]
1. Выключить станок и электродвигатель.
2. Привести в порядок рабочее место: убрать со станка стружку инструмент приспособление очистить станок от грязи вытереть и смазать трущиеся части станка аккуратно сложить готовые детали и заготовки.
3. Убрать инструмент в отведенные для этой цели места. Соблюдать чистоту и порядок в шкафчике для инструмента.
4. По окончании смены о замеченных дефектах станка вентиляции и др. и о принятых мерах по их устранению сообщить мастеру.
5. О всякой замеченной опасности немедленно заявить администрации.
6. Вымыть лицо и руки теплой водой с мылом или принять душ.
Требования безопасности в аварийных ситуациях [6]
1. При обнаружении неисправности оборудования инструмента приспособлений оснастки работу приостановить и принять меры к ее устранению. В случае невозможности или опасности устранения аварийной ситуации собственными силами сообщить руководителю работ.
2. При появлении отклонений от нормальной работы станка немедленно остановить станок и сообщить руководителю.
3. При поражении электрическим током необходимо немедленно освободить пострадавшего от действия тока соблюдая требования электробезопасности оказать доврачебную помощь и вызвать работника медицинской службы поставить в известность руководство.
4. При возникновении пожара сообщить в пожарную охрану по телефону 101 руководителю работ и приступить к тушению.
5. При заболевании травмировании оказать доврачебную помощь сообщить в медицинское учреждение и руководителю.
При выполнении курсового проекта по “Металлорежущим станкам” были закреплены знания полученные за прошедший период обучения данной дисциплине.
Целью данного проекта является по исходным данным провести настройку зубодолбежного станка 514 на изготовление цилиндрического зубчатого колеса с винтовыми зубьями и провести настройку токарно-винторезного станка 16К20П на обработку поверхности заданной в условии.
В ходе решения поставленной передо мной задачей была освоена методика настройки станков получены навыки при помощи которых были настроены станки 514 и 16К20П. Зубодолбежный станок 514 был настроен на изготовление цилиндрического зубчатого колеса с винтовыми зубьями по данным из условия курсового проекта а токарно-винторезный станок 16К20П на обработку заданной поверхности.
Опыт и навыки полученные в ходе выполнения курсового проекта будут востребованы при выполнении как других курсовых проектов так и дипломного проекта и так же при работе на машиностроительном предприятии.
Список использованных источник
Паспорт зубодолбежного станка 514 – М.: Станкоимпорт СССР 1974. - 59с.
Тайц Б. А. Производство зубчатых колес: справочник Б. А. Тайц С. Н. Калашников А. С. Калашников Г. И. Коган – М. : Машиностроение 1990.–464с.
Шеменков В. М. Конспект лекций по дисциплине “Режущий инструмент”: лекции В. М. Шеменков – Могилев: БРУ 2006.–86с.
Косилова А. Г. Справочник технолога-машиностроителя: справочник в 2 т. А. Г. Косилова Р. К. Мещерякова – М. : Машиностроение 1985.–Т.2. –496с.
Иванов М. И. Детали машин: учебное пособие М. И. Иванов – М.: Высшая школа 1998.–383с.
И-11 Металлообработка. Сборник инструкций по охране труда – Минск: ЦОТиПБ 2011. - 120с.
Шахаев Ж. А. Металлорежущие станки и инструмент: методические указания к лабораторной работе “Наладка и кинематика токарно-винторезного станка 16К20П”: лаб. практикум Ж. А. Шахаев – О.: ОГУ 2003.–33с.
Паспорт токарно-винторезного станка 16К20П – М.: Станкоимпорт СССР 1976. - 67с.
Короткевич А. Ф. Конспект лекций по дисциплине “Станочное оборудование”: лекции А. Ф. Короткевич – Могилев: БРУ 2005.–169с.
Рыжанков Д. М. Теория резания: методические указания к лабораторным работам: лаб. практикум Д. М. Рыжанков – Могилев: БРУ 2009.–48с.
Горанский Г. К. Расчет режимов резания при помощи ЭВМ: справочник Г. К. Горанский – М.: ГИ БССР 1963.–191с.
Горбацевич А. Ф. Курсовое проектирование пои Технологии машиностроения: справочник А. Ф. Горбацевич В. А. Шкред – Минск: ВЫШЭЙШАЯ ШКОЛА 1983.–255с.
лист 5.cdw

характеризующие режущие возможности инструмента:
характеризующие мощность электродвигателя привода главного движения:
характеризующие заданную производительность станка:
Четвертое ограничение
характеризующие наименьшую возможную скорость резания:
характеризующие наибольшую частоту вращения шпинделя:
характеризующие наибольшую подачу
допустимую прочностью и жесткость станка:
характеризующие наименьшую подачу
допустимую кинематикой станка:
допустимую требованиями
предъявляемыми к шероховатости обработанной поверхности:
Уравнение целевой функции:
Поверхность для расчета
оптимизации процесса резания
Заготовка прокат стальной горячекатаный круглый ГОСТ 2590-88
Материал сталь 45 ГОСТ 1050-88
Оптимальная частота вращения шпинделя n
Оптимальная подача S
Графическое изображение математической модели
определение оптимальных режимов резания
Белорусско-Российский университет
Резец токарный проходной ГОСТ 18878-73
Пластина твердосплавная ГОСТ 2209-90
Записка готовая кориш1.docx
1 Настройка зубодолбежного станка4
1.1 Область применения и назначение станка4
1.2 Технические характеристики станка7
1.3 Основные узлы принцип работы станка8
2 Назначение и обоснование выбора материала режущего инструмента11
3Описание кинематической схемы станка. Уравнения кинематического баланса15
4 Определение требуемых режимов резания19
5 Подбор сменных колес21
6 Техника безопасности на зубообрабатывающих станках22
Настройка токарно-винторезного станка 16К20П .23
1 Область применения назначение и технические характеристики
станка 16К20П. Основные узлы принцип работы и движения в станке
2 Назначение и обоснование выбора материала режущего
3 Описание кинематической схемы станка 16К20П.
Уравнения кинематического баланса .. ..29
4 Определение оптимальных режимов обработки . ..34
5 Мероприятия по технике безопасности . .46
Список использованной литературы 55
Задача данной курсовой работы состоит в определении режимов резания для зубодолбежного станка модели 514 и токарно-винторезного станка модели 16К20П анализ кинематических схем станков составление уравнений кинематического баланса изучение общего вида станков и основных составляющих станков требования охраны труда на данных станках.
В первой части курсовой работы будем по рассчитанным режимам обработки производить настройку зубодолбежного станка 514.
Во второй части курсовой работы будем по заданному типу поверхности и способу обработки рассчитывать режимы резания с использованием ЭВМ для токарно-винторезного станка модели 16К20П. Составим математическую модель определения оптимальных режимов резания и решим ее используя САПР «Компас» и систему компьютерной алгебры MathCad.
Для выполнения курсовой работы нужно иметь представление об основных типах металлообрабатывающих станков и основных их характеристиках навыки кинематической настройки металлорежущего станка на определённые режимы резания полученные раннее при изучении дисциплины “Металлорежущие станки” а также ознакомится с основной литературой по данному курсу.
Зубодолбежный станок 514
Таблица 1-Исходные данные
Модель зубодолбежного станка
Обрабатываемый материал
1 Настройка зубодолбежного станка
1.1 Область применения и назначение станка
Работа зубодолбежных станков основана на принципе воспроизведения зацепления двух зубчатых колес при этом одно из колес (долбяк) является режущим инструментом которому кроме обкаточного вращения сообщается возвратно-поступательное движение параллельно оси заготовки. Нарезаемое колесо и колесо-долбяк имеют одинаковые модули и находясь в зацеплении вращаются со скоростью обратно пропорциональной числу их зубьев.
Для соблюдения такого вращения заготовка и долбяк соединяются кинематической цепью передаточное отношение которой определяется из соотношения:
где - число зубьев долбяка;
-число зубьев нарезаемого колеса.
Рисунок 1-Принципиальная схема зубодолбежного станка.
На рис.1 изображена принципиальная схема зубодолбежного станка. Долбяк закрепленный на шпинделе во время работы получает вращение п1 а для осуществления процесса резания — одновременно возвратно-поступательное движение (vp — рабочее и vx — холостое) параллельное оси заготовки.
Суппорт 1 перемещается по направляющим 2 станины осуществляя радиальную подачу Sp до достижения полной глубины впадины колеса (врезания). С этого момента радиальная подача прекращается и начинается нарезание зубьев. В случае нарезания в два — три прохода после каждого предыдущего прохода суппорт получает дополнительное перемещение к центру колеса при этом каждый проход рассчитан на полный оборот колеса.
В процессе нарезания вращение колеса (n2) и долбяка (n1 происходит непрерывно как во время рабочих (vp) так и холостых (vx) ходов долбяка. Во избежание повреждений колеса во время холостого хода стол 3 с заготовкой отводится от долбяка на 04— 05 мм а к началу рабочего хода вновь возвращается в исходное положение (v3).
Для выполнения основных движений станок имеет:
a)гитару скоростей для настройки двойных ходов долбяка;
b)гитару деления для согласования вращения долбяка и заготовки;
c)гитару круговых подач определяющую длину дуги начальной окружности долбяка на которую повернется его зуб за один двойной ход (sKp в ммдв. ход);
d)механизм радиальной подачи на глубину врезания;
e)механизм отвода стола с заготовкой во время холостого хода долбяка.
Зубодолбежные станки имеют весьма разнообразное назначение: на них можно нарезать цилиндрические колеса с прямыми и косыми зубьями наружного и внутреннего зацепления короткие шлицевые валики звездочки для цепных передач храповые колеса червяки зубчатые муфты колеса с торцовыми зубьями и др.
Некоторые виды зубчатых колес (например ступенчатые блоки зубчатые венцы с близко примыкающими буртиками колеса с внутренними зубьями небольшого диаметра) в основном нарезаются на зубодолбежных станках. На них также можно нарезать колеса для прерывистого вращения с помощью специального долбяка и зубчатые сектора.
1.2 Технические характеристики станка
В таблице 2 приведены технические характеристики зубодолбежного станка модели 514 согласно рекомендациям [3.стр.167табл.37]:
Таблица 2 - Технические характеристики зубодолбежного станка модели 514
Наибольший нарезаемый модуль m мм
Наибольший диаметр нарезаемых колес dк мм
Максимальная ширина венца колеса В мм
Число зубьев обрабатываемого колеса z
Угол наклона зубьев град
Расстояние между осями шпинделя и стола в мм
Максимальный диаметр долбяка dд мм
Максимальная длина хода L мм
Диаметр стола dст мм
Число двойных ходов в минуту n
Круговая подача долбяка( dд=100 мм) Sкр ммдв.ход
Радиальная подача Sрммдв.ход
Мощность главного привода N кВт
Габариты станка в плане axв м
1.3Основные узлы принцип работы станка
Рисунок 2-Общий вид зубодолбежного станка модели 514
Зубодолбежный станок модели 514 состоит из следующих основных узлов (рис.2.): нижней станины 1 верхней станины 5 суппорта 13 стола 2 коробки скоростей 7 автомата 15 коробки круговых подач 12 панелей 6 и 14.
Нижняя станина является основанием станка; в ней размещены гитара деления (под крышкой 20) электродвигатель М2 ременная передача быстрого вращения заготовки (под крышкой 19) червячная передача (1: 240) вращающая шпиндель стола на котором устанавливаются заготовка нарезаемого колеса кулачки и тяги счетного механизма механизма подвода и отвода стола. Под крышкой 21 расположены электрооборудование и электронасос для подачи охлаждающей жидкости а на крышке 21 — линейный выключатель 22.
Верхняя станина крепится к нижней и имеет направляющие для суппорта 13. В ней находятся главный электродвигатель М1 коробка скоростей 7 коробка круговых подач 12 с наружной крышкой 9 автомат 15 (аппарат автоматического управления станком) коробка 16 закрывающая гитару радиальных подач шатунный механизм 10 сообщающий штосселю возвратно-поступательное движение съемная рукоятка на квадрате 18 служащая для ускоренного подвода суппорта вручную и рукоятка 17. Поворачивая рукоятку 17 вправо начинают цикл обработки каждого колеса. Пружина 23 оттягивает винт с роликом влево прижимая последний (ролик) к кулачку K1.
Для отвода перед началом обратного хода долбяка и подвода его перед началом рабочего хода столу сообщается возвратно-поступательное движение.
Суппорт несущий шпиндель долбяка перемещается по направляющим верхней станины в радиальном направлении. В нем расположены червячная передача вращающая верхнюю втулку и шпиндель. Нижняя стальная втулка перемещается вверх и вниз от реечной шестерни сообщая одновременно движение штосселю вверх и вниз.
Перемещение суппорта по направляющим верхней станины производится вручную вращением съемной рукояткой квадратной головки 4. Отсчет величины перемещения осуществляется по лимбу 3.
Коробка скоростей предназначается для установления числа двойных ходов (в минуту) штосселя. Переключение производится двумя сблокированными между собой рукоятками 24.
Автомат 15 (рис.3) предназначен для перемещения в радиальном направлении суппорта 13 и осуществления цикла обработки каждой заготовки с выключением станка.
Рисунок 3-Схема механизма – автомата зубодолбежного станка модели 514
Коробка круговых подач 12 осуществляет через червячную передачу вращение шпинделя и сидящего на нем долбяка а также реверсирование шпинделей долбяка и стола. Изменение направления вращения производится съемной рукояткой 11 при этом в среднем положении рукоятки движения выключены. Вращение штосселя вручную производится с помощью квадрата 8. Под крышкой 9 находятся сменные колеса гитары круговых подач.
Панель 6 предназначена для пуска и остановки станка панель 14 — для пуска и остановки быстрого вращения стола.
Станок модели 514 осуществляет следующие движения:
а)движение резания (главное) — возвратно-поступательное движение штосселя (шпинделя) с долбяком;
б)движение подач — вращение долбяка относительно его оси (круговая подача) и радиальное перемещение шпиндельной головки в период врезания (радиальная подача);
в)движение деления — согласованное движение шпинделя и долбяка стола и заготовки;
г)вспомогательные движения — отвод стола с заготовкой от долбяка в момент его обратного хода быстрое вращение стола с заготовкой для проверки ее установки движение счетного механизма для автоматического выключения станка.
2 Назначение и обоснование выбора материала режущего инструмента
Долбяк- это режущие колеса того же модуля что и нарезаемые находящиеся с ними в зацеплении и совершающие кроме вращательного возвратно-поступательное движение. Такой режущий инструмент предназначен для чернового и чистового нарезания прямых косых и шевронных зубьев цилиндрических колес внешнего и внутреннего зацепления.
Долбяк — довольно сложный и дорогой инструмент. Долбяки изготовляются пяти типов и трех классов точности по ГОСТу 9323—79.
Класс точности долбяков выбирается в зависимости от требуемой точности нарезаемого колеса. В данной работе требуемая степени точности колеса 8 следовательно класс точности долбяка В.
Долбяки затачиваются с торца под углом у = 5° задний угол а у вершины зуба равен 6° а по боковым поверхностям 2—4°. Долбяки изготовляются из сталей Р18 и Р9 с твердостью режущей части 62—65 HRC. Основные технические характеристики долбяков для нарезания прямозубых цилиндрических колес выбирают по ГОСТу 9323-79.[1.стр.96табл.4.25.]
Таблица 3 - Основные технические характеристики чистовых зуборезных долбяков по ГОСТ 9323-79
Номинальный делительный диаметрdoмм
Диаметр посадочного отверстия d1мм
Номинальный угол наклона зубьев
Класс точности долбяка
Хвостовые прямозубые
Для обработки требуемого зубчатого колеса будем использовать дисковый прямозубый долбяк т.к. этот вид долбяков используется для обработки колес внешнего зацепления классов точности АА А В. Основные характеристики приведены в таблице №2.
Таблица 4 - Параметры долбяка
Диаметр делительной окружности d0
Диаметр посадочного отверстия d1
Диаметр вершин зубьев
Рисунок 5 - Упрощенный эскиз инструмента
Согласно ГОСТ 9323-79 принимаем долбяк 2530-0227.
Расчет зубчатого колеса. [2.стр.814]
Дополнительные технологические данные:
Угол профиля нарезаемого колеса –
Коэффициент высоты головки зуба –
Коэффициент радиального зазора –
Делительный диаметр колеса:
d=z·m=40·45=180 мм(1.3)
Диаметр вершин зубьев:
da=d+2·m= 180+2·45=189 мм(1.4)
Диаметр впадин зуба:
df=d-25·m= 180-25·45= 16875 мм(1.5)
h=225·m= 225·45=10125 мм(1.6)
Высота головки зуба:
hf=125·m= 125·45= 5625 мм(1.8)
Упрощенный эскиз зубчатого колеса:
Рисунок 5-Эскиз зубчатого колеса
3Описание кинематической схемы станка. Уравнения кинематического баланса
Рисунок 6-Кинематическая схема зубодолбежного станка модели 514
Движение резания. Движением резания является возвратно-поступательное движение долбяка. Вращение от электродвигателя М1 мощностью 22 кВт (п = 1420 мин-1) передается через клиноременную передачу 100—280 валу коробки скоростей (рис.6). На валу I расположены два двойных подвижных блока 22—37 и 29—46 благодаря которым вал II может получить четыре различных скорости вращения (в дв. ходмин) по следующей цепи:
На левом конце вала II закреплен кривошипный диск с радиальным пазом в котором установлен подвижной кривошипный палец XXI связанный шатуном XX с рейкой находящейся в зацеплении с шестерней 26 сидящей на валу III. При вращении вала II этот кривошипно-шатунный механизм сообщает возвратнопоступательное движение валу III которое с помощью такой же шестерни 26 сидящей на другом конце вала III и сцепленной с рейкой (т = 325 мм) закрепленной на гильзе штосселя преобразуется в возвратно-поступательное движение долбяка.
Движение подачи. Вращение от вала II цепной передачей 28—28 передается валу V и дальше кинематическая цепь подач разветвляется на круговую и радиальную.
Круговая подача измеряется длиной дуги делительной окружности долбяка (в мм) на которую поворачивается долбяк за один двойной ход. Движение подачи сообщается от вала V через червячную передачу 3—23 вал VI конический реверс 28—42 вал VII сменные колеса А и В гитары круговых подач вал VIII червячную передачу 1:100.
Так как двойной ход долбяка происходит за каждый оборот вала II то кинематическая цепь круговых подач должна иметь такое передаточное отношение которое обеспечит за каждый оборот вала II поворот долбяка по дуге начальной окружности на принятую величину круговой подачи.
К станку прилагаются три пары сменных колес что позволяет установить одну из шести круговых подач долбяка (табл 5.). Так как расстояние между осями сменных колес неизменно требуется чтобы сумма их зубьев всегда была равна 89 т. е. А+В= 89.
Таблица 5 - Набор сменных колес круговые подачи и число двойных ходов долбяка за один его оборот при dд=100мм
Число зубьев колеса А
Число зубьев колеса В
Круговые подачи в ммдв. Ход
Число двойных ходов долбяка за один его оборот
Радиальная подача долбяка осуществляется перемещением суппорта. Перемещение производится винтом XVIII входящим в гайку 30 закрепленную в суппорте. На правом конце винта XVIII укреплен ролик Р прижимаемый пружиной 23 (рис.6) к профильному кулачку К1. Вращение от вала V через сменные колеса гитары радиальных подач передается на вал XIV через конические колеса 24—48 валу XV и червячной передаче 1 : 40 через муфту М2 червячной передаче 2 : 40 валу XVII и кулачку радиальной подачи K1. Через ролик Р катящийся по кулачку движение передается винту XVIII а с ним суппорту несущему шпиндель IV с долбяком.
Величина радиальной подачи определяется из кинематической цепи
где Н - шаг подъема архимедовой спирали кулачка в мм.
Передаточное отношение гитары радиальных подач
Станок модели 514 снабжен сменными колесами осуществляющими следующие радиальные подачи (табл.6):
Таблица 6 - Набор сменных колес.
Радиальная подача в ммдв.ход
Указанные радиальные подачи выбираются в зависимости от модуля и твердости материала нарезаемого колеса.
Ручное радиальное перемещение долбяка производится съемной рукояткой квадратной головки 4. За каждый оборот головки гайка 30 перемещается по винту XVIII на мм (шаг винта t = 6 мм). Цена каждого деления лимба 3 равна 002 мм.
Движение деления от вала VIII и дальше через конические шестерни 30—30 вал IX конические шестерни 30—30 вал Xсменные колеса гитары деления вал XI червячную передачу 1—240 сообщается столу с заготовкой. Для согласованности движения долбяка и заготовки необходимо чтобы в то время как долбяк поворачивается на оборота заготовка тоже поворачивалась на оборота.
Кинематическая цепь связывающая вращение долбяка и вращение стола с заготовкой (от штосселя до шпинделя стола) имеет видоборотов заготовки
К станку для гитары деления прилагаются 36 сменных шестерен: 20; 23; 24; 25; 26; 30; 33; 34; 35; 37; 38; 40; 41; 43; 45; 47; 48; 50; 55; 58; 60; 62; 65; 70; 74; 80 (2 шт.); 85; 90; 92; 95; 96; 97; 98; 100; 120.
Рекомендуется число зубьев сменной шестерни брать равным zд или 2zд.
4 Определение требуемых режимов резания
Высокую экономичность при зубодолблении достигают при правильном выборе методов и режимов резания. Режимы резания выбирают в зависимости от требуемого качества поверхности и точности зубчатого зацепления модуля свойства материала заготовки и т.д. Основные параметры режимов резания при зубодолблении: скорость резания круговая и радиальная подачи и число рабочих ходов.
При ступенчатом радиальном движении подачи долбяк при взаимной обкатке с заготовкой врезается на определенную глубину и затем только при круговом движении подачи и за полный оборот колеса осуществляется обработка всех зубьев. Этот цикл обработки называют рабочим ходом. Зубодолбление внутренних и внешних зацеплений за один рабочий ход применяют очень редко в основном для зубчатых зацеплений с т 15 мм и муфт с укороченными зубьями. При увеличении модуля и высоты зуба заготовки число рабочих ходов при зубодолблении увеличивается.
Основное время (мин) при долблении зубьев [4.стр.220]:
где d - диаметр делительной окружности колеса мм; п - частота движения долбяка дв.ход.мин; Sкр Sр- соответственно круговая и радиальная подачи ммдв.ход; h - высота зуба мм.
Число рабочих ходов в минуту i=2 [4.табл.43] .
Круговую подачу принимаем Sкр=035 мм исходя из вида обработки модуля заготовки и мощности станка[1.табл.4.26].
Радиальную ступенчатую подачу определяют по формуле:
Sр =(01 03) Sкр =02·035= 007 мм.(1.17)
Скорость резания определяем из таблицы 4 [1.табл.4.27]:
Вносим поправки на параметры режимов резания исходя из таблицы 4:
Таблица 7 - Поправочные коэффициенты на параметры режимов резания для измненных условий работы.
на скорость резания Кv
на скорость резания К v
Твердость материала заготовки НВ:
Следовательно скорость резания V=1815 ммин
Число двойных ходов долбяка устанавливается в зависимости от принятой скорости резания и длины хода долбяка и определяется по формуле[3.стр.178]:
L- длина хода долбяка мм.
Определяется по формуле[1.стр.99]:
b- ширина венца нарезаемого колеса
-величина перебега инструмента в мм с одной стороны. Принимаем =6мм. [1.стр.99]
L=46+2·8=62 мм(1.20)
Принимаем n= 125 дв.ходмин
Находим основное время при долблении:
5 Подбор сменных колес
Цепь главного движения. Для подбора одного из четырех включений коробки скоростей iк.с. = или мы используем значение частоты движения долбяка n= 125 дв.ходмин что соответствует iк.с. = .
Настройка гитары деления. Для выполнения этой операции пользуются формулой
a=48; b=20; c=33; d=60;
Настройка гитары круговых подач. При черновой обработке зубьев устанавливают круговые подачи в пределах 021—044 мм.
Сменные колеса гитары круговых подач выбираются по табл. после выбора значения круговой подачи. Приняв за исходную подачу sKP — 035 ммдв. хoд. из таблицы получаем А- 50 В - 39.
Настройка гитары радиальных подач. Величина радиальных подач устанавливается в зависимости от твердости материала нарезаемого колеса и модуля.
Радиальная подача для данного в примере материала и модуля принимается равной 048 мм что требует установки в гитаре радиальных подач сменных колес а-40 и d-40.
6 Техника безопасности на зубообрабатывающих станках
При работе на зубообрабатывающих станках необходимо соблюдать правила техники безопасности общие для металлообрабатывающего оборудования (долбежных фрезерных шлифовальных станков). Наряду с этим зубообработка предъявляет свои специфические требования. Так при проектировании зубообрабатывающих станков необходимо предусматривать защитные экраны предохраняющие зону резания. Как правило зуборезный инструмент многозубый с острыми режущими кромками поэтому при использовании его необходимо соблюдать специальные меры предосторожности: установку и снятие инструмента со станка производить в рукавицах а для очистки инструмента от стружки иметь металлические щетки. Во время работы станка нельзя осуществлять контроль обрабатываемой детали и поднастройку станка на размер. Хранить дорогостоящий режущий инструмент необходимо в специальной таре. Съем и установку заготовок на станок не следует делать при вращающемся инструменте.
Спецификация.spw

Ведомость технического проекта
Белорусско-Российский университет
Пояснительная записка
СЗД 31111.00.00.000 КЗ
Схема кинематическая
Кривошипно-шатунный механизм
привода шпинделя с долбяком
Механизм радиальной подачи
лист 1.cdw

Наибольший нарезаемый модуль m
Наибольший диаметр нарезаемых колес d
Максимальная ширина венца колеса В
Число зубьев обрабатываемого колеса z
Расстояние между осями шпинделя и стола в мм
Максимальный диаметр долбяка d
Максимальная длина хода L
Число двойных ходов в минуту n
Круговая подача долбяка (d
Мощность главного привода N
Белорусско-Российский университет
Зубодолбежный станок
Titulnyy_list_Enni.docx
Министерство образования и науки Российской Федерации
Государственно учреждение высшего профессионально образования
«БЕЛОРУССКО–РОССИЙСКИЙ УНИВЕРСИТЕТ»
Кафедра «Металлорежущие станки и инструменты»
По дисциплине: Металлорежущие станки
На тему: Настройка зубодолбежного и токарно-винторезного
станка на обработку деталей
Лист 3.cdw

Наибольший диаметр обрабатываемой заготовки D
- над поперечными салазками суппорта
Наибольший диаметр прутка
проходящего через отверстие в
Расстояние между центрами
Наибольшая длина обтачивания
Число частот вращения шпинделя
Пределы частот оборотов прямого вращения n
Пределы шагов нарезаемых резьб:
число ниток на 1 дюйм
Мощность электродвигателя главного привода N
Число оборотов вала электродвигателя n
Белорусско-Российский университет
токарно-винторезный модели 16К20П
лист 2.cdw

Зубодолбежный станок
Схема кинематическая
Белорусско-Российский университет
лист 0.cdw

Зубодолбежный станок
Схема кинематическая
Белорусско-Российский университет
Лист 4.cdw

N=10 кВт; n= 1460 мин
токарно-винторезный модели 16К20П
Белорусско-Российский университет
Ходовой винт p=12 мм
Рекомендуемые чертежи
- 24.01.2023
Свободное скачивание на сегодня
Другие проекты
- 17.05.2023