Настройка зубодолбежного станка 5в12 и универсального фрезерного станка 679




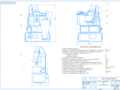
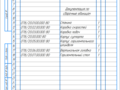
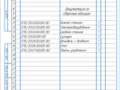
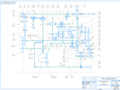
- Добавлен: 25.01.2023
- Размер: 1 MB
- Закачек: 0
Описание
Настройка зубодолбежного станка 5в12 и универсального фрезерного станка 679
Состав проекта
![]() |
![]() ![]() ![]() ![]() |
![]() ![]() ![]() |
![]() ![]() ![]() ![]() |
![]() ![]() ![]() ![]() |
![]() ![]() ![]() ![]() |
![]() ![]() ![]() ![]() |
![]() ![]() ![]() ![]() |
![]() ![]() ![]() ![]() |
![]() ![]() ![]() |
Дополнительная информация
Ведомость технического проекта 5B12.frw

Ведомость технического проекта
Белорусско-Российский
станок 1 5в12.docx
Режимы резания являются исходными данными для расчетов узлов и приводов станка. Они служат в большинстве случаев основой для разработки кинематики станка – чисел оборотов чисел ходов величины подач; динамики станка – мощности электромотора усилий возникающих при резании величин крутящих моментов на шпинделях и валах станка прочности и жёсткости отдельных деталей и узлов станка и т.д. На основе выбранных режимов резания устанавливается периодичность и порядок смены режущих инструментов расход инструментов определяется число работающих фонды зарплаты число станков необходимых для выполнения заданной программы площади цехов и участков необходимые капиталовложения и многие другие элементы организации и экономики производства.
Зубодолбежный станок 5В12
1Область применения назначение и технические характеристики станка
На зубодолбежных станках можно нарезать цилиндрические колеса прямозубые и косозубые как наружного так и внутреннего зацепления. Кроме того на этих станках можно нарезать короткие шлицевые валики храповые колеса звездочки для цепных передач зубчатые муфты колеса с торцовыми зубьями а также червяки. При специальном исполнении долбяков можно на зубодолбежных станках изготовлять дисковые кулачки и рейки.
Для некоторых разновидностей зубчатых колес (например ступенчатые блоки шестерен для коробок скоростей колеса с внутренними зубьями небольшого диаметра зубчатые венцы близко примыкающие к буртику или фланцу шлицевые отверстия) зубодолбление является основным способом изготовления. На зубодолбежных станках можно нарезать и неполнозубые колеса для передачи прерывистого вращения между сопряженными колесами при этом долбяк должен иметь специальную конструкцию. Зубодолбежные станки выгодны при нарезании зубчатых секторов тогда как на зубофрезерных станках такой вид работы связан с большими потерями на холостой пробег стола при каждом его обороте.
Таблица 1.1 - основные данные технической характеристики полуавтомата 5В12
Наименование параметров
Модуль нарезаемых зубьев
Наименьший и наибольший диаметры нарезаемых колес наружного зацепления
Наибольший наружный диаметр нарезаемых колес с внутренними зубьями
Наибольшая ширина нарезаемого зубчатого венца
с внутренними зубьями
Наибольший ход шпинделя с долбяком
Наименьшее и наибольшее расстояния от стола до торца шпинделя
Наибольшее продольное перемещение суппорта
Продолжение таблицы 1.1
Цена деления шкалы установки на глубину впадины нарезаемого колеса
Наибольшее расстояние от оси шпинделя станка до оси шпинделя стола
Наибольший отвод стола от долбяка
Числа двойных ходов в минуту долбяка
Пределы круговых подач на один двойной ход долбяка
Мощность электродвигателя главного движения
Частота вращения вала электродвигателя
Мощность электродвигателя гидросистемы
Мощность электродвигателя насоса охлаждения
2Основные узлы принцип работы и движения в станке
Рисунок 1.1 – Общий вид зубодолбежного полуавтомата 5В12
– нижняя станина; 2 – электрооборудование; 3 – линейный выключатель подвода тока к станку; 4 – средняя станина; 5 – квадрат для перестановки пальцев с кривошипа для изменения длины хода шпинделя с долбяком; 6 – квадрат для поворачивания кривошипно-шатунного механизма; 7 – гайка для закрепления пальца кривошипа; 8 – квадрат для изменения длины шатуна; 9 – гайки для закрепления установленной длины шатуна; 10 – винт для изменения зазора в зацеплении сектора с круговой рейкой шпинделя; 11 – квадрат для установочного перемещения суппорта; 12 – квадрат для вращения при наладке кулачков радиальной подачи; 13 – рукоятка реверсирования хода суппорта; 14 – кнопки пуска и выключения гидронасоса; 15 – кнопки пуска и выключения главного привода станка; 16 – кнопка толчкового типа для наладки станка; 17 – выключатель для включения и выключения местного освещения; 18 – квадрат для установки суппорта на глубину врезания долбяка; 19 – суппорт; 20 – кран подачи СОЖ; 21 – квадрат для вращательного поворота шпинделя с долбяком; 22 – квадрат фиксации суппорта; 23 – гайки для фиксации суппорта; 24 – шпиндель с долбяком; 25 – квадрат для вращения стола вручную; 26 – рукоятка гидрозажима заготовки; 27 – стол.
На нижней станине 1 укреплена средняя станина 4 а на средней – верхняя. На направляющих верхней станины находится суппорт 19 несущий шпиндель 24 с долбяком. В среднюю станину вмонтирован стол 27.
Рисунок 1.2 – Схема постепенного врезания долбяка в заготовку
Для резания долбяку одновременно с вращательным сообщается возвратно-поступательное движение параллельное оси заготовки. Вначале суппорт в который вмонтирован шпиндель с долбяком медленно перемещается на заготовку в радиальном направлении. Дойдя до заготовки (рисунок 1.2) долбяк 1 вращаясь постепенно врезается в материал заготовки 2 пока не достигнет полной глубины впадины нарезаемого колеса. В этот момент радиальная подача суппорта прекращается и он остается неподвижным в течение всего периода нарезания зубчатого венца осуществляемого при продолжающемся вращательном движении долбяка и заготовки. Если нарезание зубчатого колеса производится за два или три прохода то после каждого предыдущего прохода суппорт получает дополнительное радиальное смещение при этом каждый проход рассчитан на полный оборот нарезаемого колеса.
Вращательное движение долбяка и заготовки производится непрерывно как во время рабочих так и во время холостых ходов долбяка.
Чтобы при холостом ходе долбяк не нанес повреждения нарезаемому колесу стол с заготовкой отводится от долбяка на зазор около 05 мм. К началу рабочего хода долбяк вновь возвращается в исходное рабочее положение.
Зубодолбежный станок 5В12 выполняет следующие движения: главное возвратно-поступательное движение шпинделя с долбяком для резания; вращательные движения шпинделя с долбяком и стола с заготовкой для взаимного перекатывания зуборезного инструмента и нарезаемого зубчатого колеса; движение радиальной подачи долбяка и качательное движение стола для отвода заготовки от инструмента при обратном ходе.
3Назначение и обоснование выбора материала режущего инструмента. Параметры режущего инструмента и нарезаемого зубчатого колеса
Зуборезный инструмент на зубострогальных станках – строгальный резец. По данным нарезаемого зубчатого колеса необходимо выбрать соответствующий строгальный резец. Модуль и профильный угол исходного контура строгального резца должны соответствовать нарезаемому колесу.
Обычно долбяки изготавливают из быстрорежущей стали и очень редко снабжают твердосплавными пластинами так как долбяки этой конструкции сложны в изготовлении вследствие трудоемкости точного базирования твердосплавных пластин при напайке.
ГОСТом 9323-79 регламентировано: долбяки чистовые изготавливают из инструментальных быстрорежущих сталей Р18 Р6М5 Р12. Инструментальные быстрорежущие стали (ГОСТ 9373-60) приобретают после термообработки высокую твердость прочность и износостойкость сохраняя режущие свойства при нагреве во время работы до 600-650.
В современном машиностроении применение быстрорежущих сталей Р18 Р12 экономически нецелесообразно поэтому выбираем материал долбяка – Р6М5.
По таблице 7.7 [5 стр.153]: диаметр делительной окружности долбяка При получаем что число зубьев долбяка равно:
Основные параметры долбяка выбираем по ГОСТ 9323-79.
Определим параметры колеса [5 стр.117]:
где делительный диаметр колеса;
диаметр вершин зубьев;
4Описание кинематической схемы станка
Рисунок 1.3 – Кинематическая схема зубодолбежного полуавтомата 5В12
Рукоятки: для вертикального перемещения шпинделя с долбяком;
для поворачивания кулачка радиальной подачи;
для реверсирования направления вращения шпинделя с долбяком;
для поворачивания шпинделя с долбяком;
для поворачивания стола с заготовкой;
для реверсирования направления вращения стола с заготовкой;
для быстрого установочного перемещения суппорта несущего шпиндель с долбяком;
для точного установочного перемещения суппорта по градуированному лимбу.
кулачок радиально подачи.
Э эксцентрик управляющий колебательным движением стола для отвода заготовки от долбяка.
толкатели передающие колебательные движения столу с заготовкой.
буферная пружина уравновешивающая ход шпинделя сдолбяком.
пружина отвода стола.
Станок получает движение от главного электродвигателя мощностью и частотой вращения через четырехступенчатую клиноременную передачу.
Шпинделю с долбяком сообщается возвратно-поступательное движение от главного электродвигателя по цепи: шкивы 1-2 кривошипный диск 39 шатун-коромысло с зубчатым сектором 24 и круговая рейка 23. Главный привод шпинделя рассчитан на получение четырех ступеней чисел двойных ходов шпинделя с долбяком в минуту: 200; 315; 425; 600. Рукоятка позволяет проворачивать вручную кривошипный диск 39 для проверки хода шпинделя с долбяком. Рукоятка служит для реверсирования вращения шпинделя.
Колебательное движение отвода стола с заготовкой от долбяка во время его холостых ходов осуществляются от помещенного на главном приводном валу эксцентрика Э через промежуточные толкатели . Установка эксцентрика на одном валу с кривошипным диском 39 обеспечивает необходимую синхронизацию отвода стола с возвратными ходами долбяка.
Вращательное движение шпинделя с долбяком осуществляется по цепи: главный приводной вал – червячная передача 42-43 – сменные колеса гитары круговых подач – цилиндрические колеса 4-7-9 – узел шестерен реверса 11-12-13 и червячная передача 21-22.
Столу с нарезаемым зубатым колесом вращение сообщается по цепи: главный приводной вал – червячная передача 42-43 – сменные колеса гитары круговых подач – сменные колеса делительной гитары – цилиндрические колеса 20-19-25 – узел шестерен реверса 26-27 – цилиндрическое колесо 28 – червячная передача 29-30.
5Уравнения кинематического баланса
Уравнение цепи деления:
где частота вращения нарезаемого колеса;
частота вращения долбяка.
Уравнение цепи подач связывающая вращение шпинделя с долбяком с его возвратно-поступательным движением:
Подставив числа зубьев получим:
Уравнение цепи радиальной подачи долбяка:
где передаточное отношение одной из цилиндрических передач 16-15 14-13 8-10 в зависимости от положения скользящего блока шестерен 10-13-15; поворот кулачка в долях оборота.
6Вывод формул настройки цепей
Формулу для подбора сменных колес гитары деления получим из уравнения 1.6.
где – окружная скорость вращения заготовки и долбяка
модель долбяка и нарезаемого колеса мм;
диаметр делительной окружности нарезаемого колеса мм;
число зубьев нарезаемого колеса;
диаметр делительной окружности долбяка мм;
число зубьев долбяка.
Окончательная формула настройки делительной гитары примет вид:
Формулу для подбора сменных колес гитары круговых подач получим из уравнения 1.8.
Тогда подставив в формулу 1.15 получим что:
Так как то округлив численный коэффициент примем:
Для цепи радиальной подачи т.е. для врезания долбяка на глубину прохода применяются кулачки (рисунок 1.4) однопроходные двухпроходные и трехпроходные.
Рисунок 1.4 – Кулачки радиальной подачи
Для определения углов поворота каждого из кулачков воспользуемся уравнением 1.10.
После сокращений получим .
Теперь можем найти угол поворота каждого из кулачков за один оборот нарезаемой заготовки:
Подставив возможные передаточные отношения получаемые перемещением скользящего блока шестерен 10-13-15 найдем:
7Определение требуемых режимов резания
Режимы резания больше всего зависят от материала заготовки и вида обработки. Для быстрорежущих сталей режимы резания определяются по таблице 1.2
Таблица 1.2 – определение режимов резания
Скорость резания ммин
Круговая подача ммдв.х. долбяка при обработке
Так как у нас чистовая обработка и обрабатываемый материал сталь 45ХН то:
8Подбор сменных колес
Произведем подбор для нарезания цилиндрического прямозубого колеса со следующими данными: модуль число зубьев длина зуба b = 46 мм материал серый чугун СЧ20 вид обработки – чистовая.
Длину хода долбяка можем определить по формуле:
Суммарный перебег долбяка определяем по длине зуба :
Полная длина хода долбяка . Эту длину после настройки можно проверить отсчетом по линейке установленной сбоку шпинделя.
Число двойных ходов долбяка . Подставив численные значения получим:
Ближайшим числом двойных ходов в минуту долбяка на которое может быть настроен станок является .
После этого установим конечные положения режущих кромок долбяка относительно торцов нарезаемого колеса. В данном случае это расстояние можем принять равным половине суммарного перебега:
Подбор сменных колес делительной гитары произведем по формуле:
В зависимости от наличия сменного колеса с числом зубьев равным или кратным числу зубьев нарезаемого колеса подбираем остальные колеса из имеющегося комплекта.
Так как должно выполняться условие: и то для нашего случая получим:
Для подбора сменных колес гитары круговых подач так как диаметр делительного цилиндра долбяка отличается от положенного в основу вывода расчетной формулы для гитары подач пользуемся формулой:
Так как при подборе сменных колес гитары подач допускается некоторое отклонение то можем принять:
Тогда фактическая круговая подача:
Число двойных ходов долбяка приходящихся на один оборот определим по формуле:
Исходя из заданных значений нарезаемого модуля и требуемой точности нарезаемого зубчатого колеса выбирают один из трех имеющихся кулачков – одно- двух- или трехпроходного. Чем выше значение модуля тем больше проходов следует назначить для обработки зубчатого колеса. Для выбираем двухпроходной кулачок.
optimizaciya.cdw

технических ограничений
процесса обработки детали
Оптимизация режимов резания
Белорусско-Российский
kinematika679kpopo.cdw

obschiy vid 5v12.cdw

Модуль нарезаемых зубьев
Наименьший и наибольший диаметры нарезаемых колес наружного зацепления
Наибольший наружный диаметр нарезаемых колес с внутренними зубьями
Наибольшая ширина нарезаемого зубчатого венца
-с наружными зубьями 50
-с внутренними зубьями 30
Наибольший ход шпинделя с долбяком
Наименьшее и наибольшее расстояния от стола до торца шпинделя
Наибольшее продольное перемещение суппорта
Цена деления шкалы установки на глубину впадины нарезаемого колеса
Наибольшее расстояние от оси шпинделя станка до оси шпинделя стола
Наибольший отвод стола от долбяка
Числа двойных ходов в минуту долбяка 200; 315; 425; 600
Пределы круговых подач на один двойной ход долбяка
Мощность электродвигателя главного движения
Частота вращения вала электродвигателя 950обмин
Мощность электродвигателя гидросистемы
Станок зубодолбежный
Белорусско-Российский
кинематика 5в12.cdw

Ведомость технического проекта 679.frw

Белорусско-Российский
Корпус горизонтального
Вертикальная головка
obschiyvid679.cdw

Наибольший ход стола в мм
Наибольшие вертикальное перемещения шпинделя в мм
Наибольшие поперечное перемещение шпиндельнои бабкив мм
Количество частот вращение шпинделя
Пределы частот вращение горизонтального шпинделя
Пределы частот вращение вертикального шпинделя
Пределы скоростей подач стола в мммин
Мощность главного двигателя в кВт
Фрезерный станок модели 679
Белорусско-Российский
станок 2 679.docx
1 Назначение и технические характеристики станка. Основные узлы принцип работы и движения в станке
Фрезерные станки предназначены для выполнения следующих работ: а) обработки плоскостей; б) обработки фасонных поверхностей; в) изготовления прямых и винтовых канавок; г) обработки зубчатых колес и других работ. Для выполнения всех указанных работ в качестве инструмента используются фрезы: цилиндрические дисковые угловые модульные фасонные торцовые и др.
Фрезерные станки делятся на две основные группы: станки общего назначения и специализированные станки. К первой группе относятся горизонтально-фрезерные вертикально-фрезерные и продольно-фрезерные. Ко второй группе — резьбофрезерные копировально-фрезерные барабанно-фрезерные шпоночно-фрезерные и фрезер но-обточные т. е. станки для круглого фрезерования.
Рисунок 2.1 – Общий вид универсального фрезерного станка модели 679
Назначение станка. Станок предназначен для горизонтального фрезерования различных изделий сравнительно небольших размеров цилиндрическими дисковыми и фасонными фрезами для вертикального фрезерования торцовыми концевыми и шпоночными фрезами а также для выполнения различных сложных инструментальных работ.
Наличие горизонтального шпинделя и поворотной головки с вертикальным шпинделем а также ряда дополнительных приспособлений (углового универсального стола делительной головки круглого делительного стола и др.) обеспечивает станку модели 679 широкую универсальность. Его целесообразно использовать для работы в инструментальных и экспериментальных цехах при изготовлении приспособлений штампов пуансонов пресс-форм различных инструментов и т. д. На «станке могут быть установлены долбежная головка и копировальное устройство.
Таблица 2.1 – Техническая характеристика станка
Рабочая поверхность стола (ширина х длина) в мм
Наибольший ход стола в мм:
Наибольшее вертикальное перемещение вертикального шпинделя в мм
Наибольшее поперечное перемещение шпиндельной бабки в мм
Наибольший угол поворота вертикального шпинделя в град
Число скоростей вращения шпинделя
Пределы чисел оборотов горизонтального шпинделя в минуту
Пределы чисел оборотов вертикального шпинделя в минуту
Количество скоростей подач стола
Пределы скоростей продольных и вертикальных подач стола в мммин
Мощность главного электродвигателя в кВт
Рисунок 2.2 – Основные узлы универсального фрезерного станка модели 679
Основные узлы станка (рис. 2.1). А — поворотная головка; Б — шпиндельная бабка; В — станина с коробкой скоростей и коробкой подач; Г — стол.
Органы управления. 1 — рукоятка ручного перемещения вертикального шпинделя; 2 — зажим вертикальной головки; 3 — зажим хобота горизонтального шпинделя; 4 — рукоятка реверсирования подачи шпиндельной бабки; 5 — маховичок ручного перемещения шпиндельной бабки; 6 — маховичок ручного проворачивания шпинделей; 7 — рукоятка управления коробкой скоростей; 8 — рукоятка управления коробкой подач; 9 — кнопочная станция; 10— маховичок ручного вертикального перемещения стола; 11 — рукоятка ручного продольного перемещения стола.
Движения в станке. Движения резания — вращение горизонтального или вертикального шпинделя. Подачами являются продольное и вертикальное перемещения стола с обрабатываемой деталью и горизонтальное перемещение шпиндельной бабки. Вспомогательные движения — ручные перемещения стола и шпиндельной бабки в тех же направлениях а также перемещение вертикального шпинделя.
Принцип работы. Обрабатываемую деталь устанавливают непосредственно на столе или в универсальных приспособлениях: тисках делительной головке на круглом столе и т. п
Для выполнения всевозможных работ станок модели 679 снабжается следующими приспособлениями: угловым горизонтальным столом; делительной головкой с трехкулачковым патроном серьгой и центром; универсальными поворотными тисками и копировальным приспособлением. Копировальное приспособление механического типа позволяет производить фрезерование наружных и внутренних фасонных линейчатых поверхностен по жестким шаблонам. Для этой цели на столе устанавливается с одной стороны обрабатываемая деталь а с другой стороны — жесткий шаблон. Щуп закрепляется посредством кронштейна на станине станка.
Технологические возможности станка могут быть значительно расширены применением быстроходных сверлильных и долбежных головок укрепленных на направляющих бабки горизонтального шпинделя.
Режущий инструмент закрепляют в горизонтальном или вертикальном шпинделе с помощью различных оправок. Настройка станка в соответствии с конфигурацией и размерами детали производится продольным или вертикальным перемещением стола а также поперечным перемещением шпиндельной бабки.
Конструктивные особенности станка. В отличие от других типов универсально-фрезерных станков у которых поперечная подача сообщается столу в станке модели 679 поперечная подача сообщается шпиндельной бабке в которой смонтирован горизонтальный шпиндель. Передней опорой горизонтального шпинделя является цельная бронзовая втулка обеспечивающая точную ра- -боту шпинделя в качестве задней опоры применены радиальный и упорный шариковые подшипники
Вертикальный шпиндель смонтирован в передвижной гильзе находящейся в корпусе поворотной головки.
2 Назначение и обоснование выбора материала режущего инструмента
Основными инструментами при обработке шпоночных пазов являются шпоночные фрезы.
Шпоночные фрезы являются одной из разновидностей концевых фрез. Они предназначены для обработки шпоночных пазов. Шпоночные двухзубые фрезы подобно свёрлам входят в материал до нужной глубины а затем движутся вдоль канавки. Эти фрезы применяются на вертикально фрезерных станках или на станках с маятниковой подачей.
Фрезерование является одним из наиболее распространенных методов обработки. По уровню производительности фрезерование превосходит строгание и в условиях крупносерийного производства уступает лишь наружному протягиванию. Кинематика процесса фрезерования характеризуется быстрым вращением инструмента вокруг его оси и медленным движением подачи. Движение подачи при фрезеровании может быть прямолинейно-поступательным вращательным либо винтовым. При прямолинейном движении подачи фрезами производится обработка всевозможных цилиндрических поверхностей: плоскостей всевозможных пазов и канавок фасонных цилиндрических поверхностей.
В качестве материала для режущей части наиболее часто используют спечённые твёрдые сплавы состоящие из карбидов вольфрама (WC) титана (T цифры в вольфрамовой группе – количество (процентный объём) кобальта а остальное карбид вольфрама; первые цифры в титановольфрамовой группе – количество карбида титана вторые – количество кобальта а остальное карбид вольфрама. Первые цифры в титано-тантало-вольфрамовой группе – суммарное процентное количество карбидов титана и тантала вторые – количество кобальта а остальное карбид вольфрама.
Твёрдые сплавы используют в виде пластинок определённой формы и размеров которые получают путём прессования порошков карбидов и кобальта в изделия необходимой формы и последующего спекания при 1250 – 1450 °С в атмосфере водорода или в вакууме. Твёрдосплавные пластинки припаивают к стержням резцов медными или латунными припоями или крепят механическим способом. Марку материала твердосплавной пластинки вместе с товарным знаком завода-изготовителя клеймят на боковой поверхности стержня.
Теплостойкость твёрдых сплавов 800 – 1000 °С.
Карбиды вольфрама и титана обеспечивают сплавам высокую твёрдость теплостойкость и износостойкость а добавка тантала увеличивает усталостную прочность снижает склонность к трещинообразованию при циклических изменениях температуры; кобальт обеспечивает сплавам необходимую прочность и связывает порошки карбидов.
Сплавы ТК имеют высокую износостойкость и теплостойкость и поэтому их применяют для обработки сталей дающих сливную стружку.
С учетом выше сказанного а так же с учётом материала заготовки характера обработки назначения для обработки шпоночного паза выбираем шпоночную фрезу 2234-0351 из ГОСТ 9140-78 изготовленную из быстрорежущей стали (рис. 2.2).
Рисунок 2.3 – Фреза шпоночная 2234-0351 ГОСТ 9140-78
3 Описание кинематической схемы. Уравнения кинематического баланса
Рисунок 2.4 – Схема кинематическая универсального фрезерного станка модели 679
Цепь главного движения фрезерного станка 679
От электродвигателя мощностью 28 кВт движение передается на вал 1 клинноременной передачей. От вала I через шестерни коробки скоростей сидящих на валах II и III зубчатое колесо 56 сидящее на валу IV через зубчатое колесо 47 передается вращение горизонтальному шпинделю V.
Вертикальный шпиндель VII получает вращение от вала V через коническую пару 4142 вал VI и цилиндрическую пару 4344. Осевое перемещение вертикального шпинделя осуществляется рукояткой реечной шестерни (46) перемещающей гильзу с рейкой (45) вручную.
Различное положение двойных зубчатых колес коробки скоростей (1—2; 3—4; 10—11) позволяет сообщить восемь различных чисел оборотов (см. таблицу 1) горизонтальному шпинделю (от 110 до 1230 обмин.) и восемь чисел оборотов (см. таблицу 2) вертикальному шпинделю (от 150 до 1660 обмин.).
Приведенные в таблицах 1 и 2 числа оборотов составляют стандартный ряд; отклонения фактических значений чисел оборотов от стандартного ряда колеблются в пределах 5%.
Цепь подач фрезерного станка 679
Привод подач станка устроен следующим образом.
Механические перемещения стола осуществляются механизмом подач получающим вращение от вала 1 коробки скоростей через цилиндрические зубчатые колеса 12; 15; 16; 17 и коробку подач.
От вала XI через цепную передачу 58; 59 вращение передается валу XII конической паре 60; 61 вертикальному валу XIII.
Зубчатые колеса 33; 34 передают вращение свободно сидящим колесам 31 и 35 а через колесо 30—зубчатым колесам 29 и 32.
Продольное механическое перемещение стола осуществляется включением муфты вала XV с муфтой зубчатого колеса 31 (перемещение влево) —и с муфтой колеса 32 — (перемещение вправо). Через коническую пару 27; 28 вращение сообщается винту продольного хода XVI.
Ручное продольное перемещение стола осуществляется двумя рукоятками сидящими на концах винта XVI.
Вертикальное механическое перемещение суппорта со столом вверх производится включением муфты винта XIV с муфтой шестерни 29 а вниз — с муфтой шестерни 35.
Ручное вертикальное перемещение суппорта осуществляется маховичком сидящим на валу XVII через коническую пару 37; 36 и вертикальным винтом XIV.
Поперечное механическое перемещение горизонтальной бабки заменяющее обычно принятое в фрезерных станках поперечное Перемещение стола по консоли осуществляется следующим образом: от вала XI коробки подач через цепную передачу 57; 53 вращение передается валу XVIII на котором свободно сидят конические зубчатые колеса 52 54.
Включением муфты вала XVIII с муфтой колеса 54 вращение передается цилиндрической зубчатой паре 50; 51 и гайке 49. При этом горизонтальная бабка несущая винт 48 перемещается вперед (к рабочему столу). При включении муфты вала XVIII с муфтой колеса 52 горизонтальной бабке сообщается движение в обратную сторону.
Ручное перемещение горизонтальной бабки производится Маховичком сидящим на валу XIX.
В зависимости от произведенных переключений двойных зубчатых колес 13—14; 18—19; 20—21 валу XI можно сообщить восемь разных чисел оборотов. В результате получаем восемь продольных подач (см. таблицу 3) восемь вертикальных подач (см. таблицу 4) и восемь поперечных подач (см. таблицу 5).
Подачи выражаются значениями стандартного ряда. Отклонение фактических величин минутных подач от стандартных значений колеблется как и для чисел оборотов шпинделей в пределах 5 %.
4 Оптимизация режимов резания
Таблица 2.2 – Исходные данные для настройки станка
Размер шпоночного паза
Твердость материала заготовки
Для правильного решения вариационной технико-экономической задачи определения оптимальных режимов резания большое значение имеет выбор критерия оптимальности.
В большинстве случаев при определении режимов резания на металлорежущих в том числе на агрегатных станках и автоматических станочных линиях в качестве критерия оптимальности принята себестоимость одной операции или одной детали. Иногда в качестве такого критерия принимается производительность операции. Такие критерии как капиталоемкость энергопотребление и т. п. при расчете режимов резания почти не применяются.
В данном случае для решения технико-экономической задачи используем следующие технические ограничения:
) режущие возможности инструмента определяемые его материалом геометрией расчетной стойкостью и условиями обработки;
) мощность электромотора привода главного движения станка;
) заданная производительность станка;
) наименьшая возможная скорость резания (число оборотов) зависящая или от наименьшего числа оборотов шпинделя станка или от режущих свойств инструмента при обработке того или иного металла;
) наибольшая возможная скорость резания (число оборотов) допускаемая кинематикой станка или режущими свойствами инструмента;
) наибольшая подача допускаемая прочностью и жесткостью станка а также требованиями к чистоте обработки;
) наименьшая подача допускаемая кинематикой станка;
) наибольшая подача допускаемая кинематикой станка;
) наименьшая технологически приемлемая глубина резания для данного инструмента;
) наибольшая возможная глубина резания равная припуску на обработку.
4.1 Режущие возможности инструмента
При фрезерования шпоночного паза составим таблицу 2.3 коэффициентов и показателей степеней в формуле скорости резания [1: табл. 81 стр. 408].
Таблица 2.3. – Коэффициенты и показатели степени в формуле скорости резания при фрезеровании шпоночного паза.
Общий поправочный коэффициент на скорость резания определяющий фактические условия резания [1: стр. 385]:
поправочный коэффициент учитывающий влияние физико-механических свойств обрабатываемого материала на скорость резания [1: стр. 358 таблица 1].
– показатель степени в формуле для расчета коэффициента обрабатываемости стали Kmv [1: стр. 359 таблица 2].
Т.к. шпоночный паз обрабатывается на валу без обработанном предварительно точением следовательно коэффициент Kv примем равным 1.
– поправочный коэффициент учитывающий влияние инструментального материала на скорость резания [1: стр. 361 таблица 6].
Средние значения периода стойкости фрезы [1: стр. 411 таблица 82] Т = 60 мин.
Режущие возможности инструмента определяются по формуле [1: стр. 406]
Скорость резания определяемая кинематикой станкавыражается формулой [2: стр. 24]:
Приравняем правые части формул 2.7 и 2.8
перенесем неизвестные в левую часть а известные – в правую
Подставим известные коэффициенты и переменные и перенесем неизвестные в левую часть а известные – в правую.
упростим правую часть
4.2 Мощность электродвигателя привода главного движения станка
Таблица 2.4 – Значение коэффициента Cp и показателей степени в формуле окружной силы при фрезеровании [1: стр. 412 таблица 83]
Поправочный коэффициент для Kmp для стали учитывающий влияние качества обрабатываемого материала на силовые зависимости [1: стр. 362 табл. 9]
где n - показатель степени.
Крутящий момент Нм на шпинделе станка [1: стр. 411]
Сила резания. Главная составляющая силы резания при фрезеровании – окружная сила Н [1: стр. 406]
Подставив в формулу 2.14 формулу 2.15 получим
Максимально возможный крутящий момент который может обеспечить станок определяем по формуле [1: стр. 386]:
где – мощность главного привода станка
Приравнивая правые части формул (2.16) и (2.17) и выделив в левую часть уравнения подлежащие определению получаем:
перенесем неизвестные переменные в левую часть
подставим известные переменные и коэффициенты и упростим выражение
4.3 Заданнная производительность станка.
Третьим ограничением учитывается взаимосвязь рассчитываемых скорости резания и подачи с заданной производительностью станка. Оно имеет важное значение так как никакой режим не может быть признан оптимальным если он не обеспечивает требуемой производительности.
Учитывая что время цикла определенное исходя из заданной производительности должно быть больше времени цикла станка включающего время на рабочий ход и на вспомогательные операции получаем уравнение третьего ограничения при работе в один проход [2 стр. 31 (48)]:
L – длина рабочего хода инструмента по условию задания равна 100 мм;
R – заданная производительность станка. Принимаем максимальную производительность 8 штч. В случае несоответствия уравнений данную величину можно изменить для решения задачи.
КЗ – коэффициент загрузки станка для серийного производства принимаем 0.75.
rR – число деталей обрабатываемых одновременно на одной позиции при обработке данной дети равно 1;
ТВ.Н – вспомогательное неперекрываемое время мин. Для серийного производства принимаем 3 минуты согласно [4 стр.221-214].
Правая часть содержит известные коэффициенты следовательно для упрощения уравнения упростим правую часть подставив значения коэффициентов:
Упрощённое уравнение имеет вид:
4.4 Наименьшая допустимая скорость резания
Скорость резания любым инструментом не может быть меньше некоторой определенной величины так как при чрезмерном занижении ее изменяются и ухудшаются условия стружкообразования а на режущей кромке появляется нарост усиливаются выкрашивание и износ режущих кромок инструментов.
Неравенство соответствующее этому ограничению имеет вид [2 стр. 32 (53)]:
где – минимальная скорость резания для материала;
– минимальная станочная скорость.
Уравнение характеризующее четвёртое ограничение будет иметь вид:
Первая часть уравнения в скобках характеризует выбор минимальной скорости резания исходя из вида обработки и условий обработки. Так как для обработки применяется быстрорежущая сталь то целесообразность использования наступает от скорости резания Vmin = 20ммин тогда частота вращения шпинделя соответствующая обработке нашей детали при принятой минимальной скорости nmin мин-1:
По паспорту станка наименьшая частота вращения шпинделя nmin = 71 мин-1. Соответственно лимитирующей частотой вращения будет частота соответствующая скорости Vmin = 20 ммин и коэффициент рассчитаем по формуле
Уравнение четвертого ограничения будет иметь вид:
4.5 Наибольшая возможная скорость резания
Для многих инструментов чистовой и получистовой обработки отверстий скорость резания не может быть больше некоторой величины определяемой для каждого инструмента на основании практических данных. При значительном увеличении скорости резания за пределы практически допустимой наблюдается быстрая потеря инструментом размера вследствие повышенного износа режущих кромок и разбивания диаметра отверстия обрабатываемой данным инструментом детали.
Получим значения соответствующие пятому ограничению. Рассмотрим общее уравнение учитывающее и максимальную скорость резания исходя из режущих способностей твердосплавного инструмента и максимальную скорость резания которую можно получить для данных условий обработки исходя из кинематики станка.
Как правило теплостойкость быстрорежущего инструмента достаточно высока и главным ограничивающим фактором при выборе верхнего предела скорости резания при расчёте данного ограничения является наибольшая частота вращения по станку nст.max. По паспорту станка наибольшая частота вращения шпинделя nст.max = 1660 мин-1.
4.6 Прочность механизма подач
Уравнение характеризующее шестое ограничение для точения будет иметь вид:
Сила резания не может быть больше чем допустимое усилие подачи обеспечиваемое механизмом подач. Согласно паспорту станка наибольшее усилие допускаемое механизмом продольной подачи РДОП.СТ = 2000 Н.
Приравняем формулы 2.32 и 2.33 и вынесем неизвестные переменные
Подставим известные коэффициенты и переменные из табл. 2.4
4.7 Наименьшая подача допустимая кинематикой станка.
Ограничение устанавливает взаимосвязь расчетной величины подачи с минимальной подачей допускаемой кинематикой станка. Следовательно технологически допустимая подача всегда должна быть больше или равна минимальной подаче имеющейся на станке:
Уравнение характеризующее седьмое ограничение для фрезерования будет иметь вид:
Подача на зуб будет равна
4.8 Наибольшая подача допустимая кинематикой станка
Ограничение устанавливает взаимосвязь расчетной величины подачи с максимальной подачей допускаемой кинематикой станка. Следовательно технологически допустимая подача не может быть больше наибольшей подачи имеющейся на станке т. е. должно соблюдаться следующее неравенство:
где szст.max – максимальная станочная подача на зуб.
По паспорту станка максимальная подача станка s = 125 ммоб.
4.9 Математическая модель технических ограничений
На основе этих уравнений и неравенств может быть решена задача о выборе оптимальных режимов резания и рамках заданных ограничений. В ряде случаев когда имеющиеся технические ограничения не обеспечивают этих режимов может быть решена задача о корректировке данных ограничений до их значений обеспечивающих оптимальность режима резания.
По заданным исходным данным определяются элементы режима резания на металлорежущем станке: число оборотов шпинделя n величина подачи на 1 оборот изделия или инструмента s при которых производительность была бы максимальной.
Необходимо найти такую комбинацию элементов режима резания n и s при которой принятый критерий оптимальности достигал бы максимума в зависимости от его характера.
Задача должна решаться с учетом имеющихся между отдельными параметрами связей отражающих физические закономерности при резании металлов и заданных ограничений технологического технического организационно-производственного и экономического характера. При этом как указывалось выше многие технические и организационно-производственные ограничения по возможности должны устраняться и не лимитировать эффективность режима резания.
Аналитическое решение задачи сводится к определению условий максимума функции многих переменных связанных между собой многими ограничивающими зависимостями.
В наших условиях такой функцией будет оценочная функция или уравнение критерия оптимальности.
Для нахождения оптимальных параметров режимов резания па металлорежущих станках используем метод решения экстремальных задач получивший широкое практическое применение а именно так называемый метод линейного программирования.
Основанием для выбора этого метода являлось также и то что он достаточно удобен для применения автоматических вычислительных машин при решении систем линейных уравнений и неравенств с которыми оперируют при данном методе. Это чрезвычайно упрощает и ускоряет решение даже очень сложных и громоздких задач при большом числе неизвестных и ограничивающих условий.
Линейное программирование охватывает методы решения ряда оптимальных задач имеющих дело со многими взаимосвязанными переменными подчиняющимися определенным ограничивающим условиям.
Математическая модель может быть представлена как в аналитическом так и в графическом виде что во многих случаях облегчает экспериментирование с ней причем многие функциональные зависимости в природе и технике проще и удобнее выражаются графически чем аналитически.
В данной работе решение возникающих перед нами задач линейного программирования будет решаться графически с помощью САПР «Компас». Точное построение уравнений в электронной графической форме позволит получить точные значения координат решений и наглядно просмотреть область ограничений. Что для решения технической задачи более предпочитаемо чем аналитический метод при сопоставимой точности результатов.
Для приведения полученных нами уравнений и неравенств технических ограничений к линейным формам необходимо их логарифмировать но до логарифмирования произведем в этих уравнениях и неравенствах некоторые преобразования. Входящие в уравнения и неравенства величина s в ряде случаев имеет значения порядка 001 - 1 мм и им будут соответствовать отрицательные логарифмы.
Для того чтобы исключить возможность появления отрицательных логарифмов умножим во всех уравнениях и неравенствах технических ограничений величину s на 1000:
Обозначив через х1 = ln(n) x2 = ln(1000Sz) получим следующую математическую модель оптимального режима резания:
Существует еще несколько ограничений: прочность режущего инструмента и жёсткость технологической системы. Эти ограничения мы устраним организационно. В результате произведённых расчётов мы получили систему уравнений характеризующих процесс резания для данных условий обработки.
4.10 Графическое решение математической модели оптимизации процесса резания
На рисунке 2.5 изображены прямые неравенств системы и выделена область возможных решений этой системы.
Рисунок 2.5 – Графическое решение математической модели процесса резания
Максимальное значение целевой функции при пересечении области значений: Х1опт = 741; Х2опт. = 874.
Оптимальная частоту вращения шпинделя nопт мин-1
nопт = ех1 = 1652.(2.67)
Оптимальная подача на S ммоб
Полученные значения режимов резания являются оптимальными.
n = 1652 мин-1 S = 624 ммоб
5 Мероприятия по технике безопасности
1. Работать только на станках к которым имеется допуск и выполнять работу которая поручена.
2. Сосредоточить внимание на выполняемой работе не отвлекаться на посторонние дела и разговоры не отвлекать других.
3. Не допускать на свое рабочее место лиц не имеющих отношения к порученной работе. Без разрешения мастера не доверять свой работающий станок другому рабочему.
4. Не опираться на станок во время его работы и не позволять делать это другим.
5. Заметив нарушение инструкции другим рабочим предупредить его о необходимости соблюдения требований по технике безопасности.
6. О всяком несчастном случае немедленно поставить в известность мастера или бригадира и обратиться в медицинский пункт.
7. При ремонте станка и пусковых устройств на станке должен быть вывешен плакат: «Не включать — ремонт».
8. Нельзя работать на неисправном и не имеющем необходимых ограждений станке. Не производить ремонт и переделку станка самостоятельно.
9. Не разрешать уборщику убирать у станка во время его работы.
10. Запрещается работать на станке в рукавицах или перчатках а также с забинтованными пальцами без резиновых напальчников.
11. Во избежание несчастных случаев и попадания грязи и стружки в механизмы станка запрещается обдувать воздухом из шланга обрабатываемую поверхность и станок.
12. Надежно и жестко закреплять обрабатываемую деталь на станке.
13.и габаритные размеры обрабатываемой детали должны соответствовать паспортным данным станка.
14. Устанавливать и снимать тяжелые детали и приспособления (массой более 16 кг) только с помощью подъемных механизмов. Не превышать нагрузку установленную для грузоподъемных средств.
15. Пользоваться грузоподъемными механизмами только после специального обучения и аттестации.
16. Деталь должна быть надежно застроплена; для подъема применять специально строповочно-захватные приспособления. Освобождать обрабатываемую деталь от стропов или захватных приспособлений только после надежной установки где надо — и закрепления детали на станке.
17. Отрегулировать местное освещение станка так чтобы рабочая зона была достаточно освещена и свет не слепил глаза. Протереть арматуру и светильник. Пользоваться местным освещением напряжением выше 36В запрещается.
18. При всяком перерыве в подаче электроэнергии немедленно выключить электрооборудование станка.
19. Если на металлических частях станка обнаружено напряжение (ощущение тока) электродвигатель работает на две фазы (гудит) заземляющий провод оборван остановить станок и немедленно доложить мастеру о неисправности электрооборудования.
20. Если пол скользкий (облит маслом эмульсией) потребовать чтобы его посыпали опилками или сделать это самому.
21. Пользоваться деревянной решеткой и содержать ее в исправном состоянии.
22. Каждый рабочий обязан:
а) требовать от администрации цеха проведения инструктажа по технике безопасности до назначения на работу и при переводе на станок другой модели;
б) требовать от администрации цеха чтобы печатная инструкция о мерах безопасности при работе на данном станке находилась на рабочем месте станочника;
в) строго выполнять все правила безопасности;
г) обязательно пользоваться полагающейся спецодеждой спец. обувью и индивидуальными защитными средствами (очками респираторами масками и др.);
д) при обнаружении возможной опасности предупредить товарищей и немедленно сообщить администрации цеха;
е) содержать в чистоте рабочее место в течение всего рабочего дня и не загромождать его деталями заготовками металлическими отходами мусором и т. п.;
ж) укладывать устойчиво на подкладках и стеллажах поданные на обработку и обработанные детали; высота штабелей не должна превышать для мелких деталей
м для средних — 1 м для крупных — 15 м;
з) применять только исправные гаечные ключи соответствующих размеров;
и) при работе ключами не наращивать их трубой или другими рычагами; нельзя пользоваться прокладками если ключи не соответствуют размерам гаек.
к) не мыть руки в масле эмульсии керосине и не вытирать их обтирочными концами загрязненными стружкой;
л) не принимать пищу у станка;
м) не оставлять свою одежду на рабочем месте.
23. На территории выполнять следующие правила:
а) быть внимательным к предупредительным сигналам автомашин и других видов движущегося транспорта;
б) не находиться под поднятым грузом;
в) не проходить в местах не предназначенных для прохода;
г) не заходить без разрешения за ограждения технологического оборудования;
д) не прикасаться к токоведущим частям электрооборудования клеммам и электропроводам к арматуре общего освещения не открывать дверцы электрошкафов; в необходимых случаях обращаться к электромонтеру;
е) не включать и не останавливать (кроме аварийных случаев) станки механизмы работа на которых Вам не поручена.
24. Работая с подручным или учеником обучать его безопасным приемам работы и следить за их выполнением.
25. К работе с грузоподъемными кранами могут быть допущены лица не моложе 18 лет специально обученные систематически инструктируемые сдавшие экзамен квалификационной комиссии и имеющие на руках удостоверение.
Требования безопасности перед началом работы:
1. Перед каждым включением станка убедиться что пуск станка никому не угрожает опасностью.
2. Привести в порядок рабочую одежду: застегнуть или подвязать обшлага рукавов надеть головной убор; женщины должны убрать волосы под косынку повязанную без свисающих концов.
3. Проверить хорошо ли убраны станок и рабочее место выявить неполадки в работе станка и принять меры по их устранению.
4. О неисправности станка немедленно заявить мастеру; до устранения неисправности к работе не приступать.
5. Приготовить крючок для удаления стружки ключи и другой необходимый инструмент. Не применять крючок с ручкой в виде петли.
6. Проверить наличие и исправность;
а) ограждений зубчатых колес приводных ремней валиков приводов и пр. а также токоведущих частей электрической аппаратуры (пускателей рубильников трансформаторов кнопок);
б) заземляющих устройств;
в) предохранительных устройств для защиты от стружки охлаждающих жидкостей;
г) устройств для крепления инструмента (отсутствие трещин надломов прочность крепления пластинок твердого сплава или керамических пластинок стружколомающих порогов и пр.);
д) режущего измерительного крепежного инструмента и приспособлений и разложить их в удобном для пользования порядке.
Работать только исправным инструментом и приспособлениями и применять их строго по назначению.
7. Если при обработке металла образуется отлетающая стружка то при отсутствии специальных защитных устройств на станке надеть защитные очки или предохранительный щиток из прозрачного материала.
8. При обработке вязких металлов дающих сливную стружку применять резцы со специальными стружколомающими устройствами.
9. При обработке хрупких металлов (чугуна бронзы и т. д.) дающих отлетающую стружку а также при дроблении стальной стружки в процессе обработки применять следующие защитные устройства: специальные стружкоотводчики прозрачные экраны или индивидуальные щитки (для защиты лица).
10. Проверить на холостом ходу станка:
а) исправность органов управления (механизмов главного движения подачи пуска останова движения и др.);
б) исправность системы смазки и охлаждения (убедиться в том что смазка и охлаждающая жидкость подаются нормально и бесперебойно);
в) исправность фиксации рычагов включения и переключения (убедиться в том что возможность самопроизвольного переключения с холостого хода на рабочий исключена);
г) нет ли заеданий или излишней слабины в движущихся частях станка особенно в шпинделе в продольных и поперечных салазках суппорта.
11. Для предупреждения кожных заболеваний рук при применении на станках охлаждающих масел и жидкостей по указанию врача перед началом работ смазывать руки специальными пастами и мазями.
12. Проверять доброкачественность ручного инструмента при получении его из кладовой:
а) ручка напильника и шабера должна иметь металлическое кольцо предохраняющее ее от раскалывания;
б) молоток должен быть насажен на рукоятку овального сечения расклиненную металлическим клином и изготовленную из твердых и вязких пород дерева; боек молотка должен иметь ровную слегка выпуклую поверхность; нельзя работать молотком со сбитым бойком имеющим трещины или насаженным на рукоятку из дерева мягких пород а также плохо закрепленным на рукоятке:
в) зубило и другой ударный инструмент должны быть длиной не менее 150 мм кернер— 100 мм и не иметь наклепа на бойке;
г) гаечные ключи должны быть исправными и соответствовать размеру гаек; запрещается работать гаечными ключами с прокладками удлинять их трубами и применять контрключи;
д) разложить инструмент и приспособления в удобном для пользования порядке.
13. Пользоваться режущим инструментом имеющим правильную заточку. Применение неисправного инструмента и приспособлений запрещается.
14. Проверить и обеспечить достаточную смазку станка; при смазке пользоваться только соответствующими приспособлениями.
15. Разместить шланги подводящие охлаждающую жидкость так чтобы была исключена возможность соприкосновения их с режущим инструментом и движущимися частями станка. Охлаждающую жидкость подавать только насосом.
16. Запрещается охлаждать режущий инструмент мокрыми тряпками или щетками.
17. Не допускать разбрызгивания масла и жидкости на пол. Для защиты от брызг устанавливать щитки.
Требования безопасности во время работы:
1. Выполнять указания по обслуживанию и уходу за станками изложенные в «Руководстве к станку» а также требования предупредительных таблиц имеющихся на станке.
2. Устанавливать и снимать режущий инструмент только после полного останова станка.
3. Не работать без кожуха прикрывающего сменные шестерни.
4. Остерегаться срыва ключа правильно накладывать ключ на гайку и не поджимать им гайку рывком.
5. Во время работы станка не брать и не подавать через работающий станок какие-либо предметы не подтягивать болты гайки и другие соединительные детали станка.
6. Остерегаться наматывания стружки на обрабатываемый предмет или резец не направлять вьющуюся стружку на себя. Пользоваться стружколомателем.
7. Не удалять стружку от станка непосредственно руками и инструментом пользоваться для этого специальными крючками и щетками-сметками.
8. Следить за своевременным удалением стружки с рабочего места и станка.
9. Остерегаться заусенцев на обрабатываемых деталях.
10. При возникновении вибрации остановить станок. Принять меры к устранению вибрации: проверить крепление резца и детали.
11. Обязательно остановить станок и выключить электродвигатель при:
а) уходе от станка даже на короткое время (если не поручено обслуживание двух или нескольких станков);
б) временном прекращении работы;
в) перерыве в подаче электроэнергии;
г) уборке смазке чистке станка;
д) обнаружении неисправности в оборудовании;
е) подтягивании болтов гаек и других соединительных деталей станка;
ж) установке измерении и съеме детали;
з) проверке или зачистке режущей кромки резца;
и) снятии и надевании ремней на шкивы станка.
12. Передвижение ремня по ступенчатым шкивам на ходу допускается только с применением переводок.
13. При обработке деталей применять режимы резания указанные в операционной карте для данной детали.
14. Не увеличивать установленные режимы резания без ведома мастера.
15. При закреплении детали в кулачковом патроне или использовании планшайб следует захватывать деталь кулачками на возможно большую величину. Не допускать чтобы после закрепления детали кулачки выступали из патрона или планшайбы за пределы их наружного диаметра. Если кулачки выступают заменить патрон или установить специальное ограждение.
16. При установке (навинчивании) патрона или планшайбы на шпиндель подкладывать под них на станок деревянные прокладки с выемкой по форме патрона (планшайбы).
17. Устанавливать тяжелые патроны и планшайбы на станок и снимать их со станка при помощи подъемного устройства и специального захватного приспособления.
18. Не свинчивать патрон (планшайбу) внезапным торможением шпинделя. Свинчивание патрона (планшайбы) ударами кулачков о подставку допускается только при ручном вращении патрона; в этом случае следует применять подставки с длинными ручками (для удержания рукой).
19. В кулачковом патроне без подпора центром задней бабки можно закреплять только короткие длиной не более двух диаметров уравновешенные детали; в других случаях для подпора пользоваться задней бабкой.
20. При обработке в центрах деталей длиной равной 12 диаметрам и более а также при скоростном и силовом резании деталей длиной равной восьми диаметрам и более применять дополнительные опоры (люнеты).
21. При обработке деталей в центрах проверить закреплена ли задняя бабка и после установки изделия смазать центр. При дальнейшей работе нужно периодически смазывать задний центр.
22. При работе с большими скоростями применять вращающийся центр прилагаемый к станку.
23. Нельзя работать со сработанными или забитыми центрами.
24. При обточке длинных деталей надо следить за центром задней бабки: периодически центр следует смазывать и проверять осевой зажим.
25. Во избежание травм из-за инструмента необходимо:
а) включить сначала вращение шпинделя а затем подачу; при этом обрабатываемую деталь следует привести во вращение до соприкосновения ее с резцом врезание производить плавно без ударов;
б) перед остановом станка сначала выключить подачу отвести режущий инструмент от детали а потом выключить вращение шпинделя.
26. Резцовую головку отводить на безопасное расстояние при выполнении следующих операций: центровании деталей на станке зачистке шлифовании деталей наждачным полотном опиловке шабровке измерении деталей а при смене патрона и детали отодвигать подальше также задний центр (заднюю бабку).
27. Следить за правильной установкой резца и не подкладывать под него разные куски металла; пользоваться подкладками равными площади резца.
28. Резец следует зажимать с минимально возможным вылетом и не менее чем тремя болтами. Нужно иметь набор подкладок различной толщины длиной и шириной не менее опорной части резца. Не следует пользоваться случайными подкладками.
29. Не затачивать короткие резцы без соответствующей оправки.
30. При подводке резца к оправке или планшайбе соблюдать осторожность и избегать чрезмерно глубокой подачи резца.
31. При надевании планшайбы на конец шпинделя очистить ее от стружки и загрязнения.
32. При обработке вязких металлов дающих сливную ленточную стружку применять резцы с выкрутками накладными стружколомателями или стружкозавивателями.
33. Не пользоваться зажимными патронами если изношены рабочие плоскости кулачков.
34. При скоростном резании на токарных станках работать с не вращающимся центром запрещается.
35. Обрабатываемую поверхность располагать как можно ближе к опорному или зажимному приспособлению.
36. При установке детали на станок не находиться между деталью и станком.
37. Не класть детали инструмент и другие предметы на станину станка и крышку передней бабки.
38. При отрезании тяжелых частей детали или заготовок не придерживать отрезаемый конец руками.
39. При опиловке зачистке шлифовании обрабатываемых деталей на станке:
а) не прикасаться руками или одеждой к обрабатываемой детали;
б) не производить указанных операций с деталями имеющими выступающие части пазы и выемки (пазы и выемки предварительно заделывать деревянными пробками);
в) стоять лицом к патрону держать ручку напильника левой рукой не перенося правую руку за деталь.
40. Для обработки деталей закрепленных в центрах применять безопасные поводковые патроны (например чашкообразного типа) или безопасные хомутики.
41. После закрепления детали в патроне вынуть торцовый ключ.
42. При закреплении детали в центрах:
а) протереть и смазать центровые отверстия;
б) не применять центр с изношенными или забитыми конусами;
в) следить за тем чтобы размеры токарных центров соответствовали центровым отверстиям обрабатываемой детали;
г) не затягивать туго задний центр надежно закреплять заднюю бабку и пиноль;
д) следить за тем чтобы деталь опиралась на центр всей конусной частью центрового отверстия; не допускать упора центра в дно центрового отверстия детали.
43. Работать на станке без закрепления патрона сухарями предотвращающими самоотвинчивание при реверсе запрещается.
44. Не тормозить вращение шпинделя нажимом руки на вращающиеся части станка или детали.
Эксплуатация металлообрабатывающего оборудования должна отвечать требованиям ГОСТ 12.2.009 СТ СЭВ 538 СТ СЭВ 539 СТ СЭВ 500 в соответствии с которыми при работе на станках сверлильной группы предусматривается выполнение следующих требований:
Проверить хорошо ли убрано рабочее место и при наличии неполадок в работе станка в течении предыдущей смены ознакомиться с ними и с принятыми мерами по их устранению.
Проверить состояние решетки под ногами ее устойчивость.
Проверить состояние ручного инструмента.
Привести в порядок рабочее место: убрать все лишнее подготовить и аккуратно разложить необходимые инструменты и приспособления так чтобы было удобно и безопасно ими пользоваться.
Проверить состояние местных грузоподъемных устройств.
Проверить состояние станка: убедиться в исправности электропроводки заземляющих проводов.
На холостом ходу проверить исправность кнопок “Пуск” и “Стоп”.
Подготовить средства индивидуальной защиты и проверить их исправность.
и габаритные размеры заготовок должны соответствовать паспортным данным станка.
При обработке заготовок массой более 16кг устанавливать и снимать с помощью грузоподъемных устройств причем не допускать превышения нагрузки установленной на них.
При необходимости пользоваться средствами индивидуальной защиты. Запрещается работать в рукавицах и перчатках а также с забинтованными пальцами без резиновых напальчников.
Перед каждым включением станка убедиться что его пуск не для кого не опасен.
Если в процессе обработки образуется отлетающая стружка установить переносные краны для защиты окружающих и надеть защитные очки или предохранительный щиток. Следить за своевременным удалением стружки как со станка так и с рабочего места.
Правильно укладывать обработанные детали не загромождать подходы к станку.
Обязательно выключать станок при уходе даже на короткое время при регулировке уборке и смазывании станка.
По окончании работы стружку смести в поддон или на совок щеткой. Во избежание несчастного случая и попадания стружки в организм запрещается для очистки станка использовать сжатый воздух.
Проверить качество уборки станка выключить местное освещение и отключить станок от электросети.
Осуществить санитарно-гигиенические мероприятия.
Кроме указанного каждый станочник обязан: работать только на том станке к эксплуатации которого он допущен; без разрешения мастера не допускать к работе на станке других лиц; о всяком несчастном случае немедленно ставить в известность мастера и обращаться в медицинский пункт; уметь оказывать первую помощь пострадавшему применять первичные средства пожаротушения и проводить работы по устранению последствий аварийных ситуаций или пожара.
При выполнении курсовой работы по «Металлорежущим станкам» были практически применены знания по данной дисциплине полученные за прошедший период обучения.
В результате решения данной курсовой работы были изучены назначения и технические характеристики станков их основные узлы и принципы работы были рассмотрены кинематические схемы станков. Также были выбраны и обоснованы материалы режущих инструментов для каждой операции по обработке с определением требуемых режимов резания. Мы ознакомились с основными положениями по технике безопасности характерными для зубообрабатывающих и сверлильных групп станков. Были получены навыки благодаря которым мы смогли произвести настройку станов моделей 5В12 и 679.
С помощью навыков полученных при выполнении курсовой работы мы можем решать аналогичные задачи которые могут быть поставлены перед нами в других курсовых работах дипломном проекте а также на производстве.
Список использованной литературы
Косиловой А.Г. и Мещерякова Р.К. Справочник технолога-машиностроителя Под ред. А.Г. Косиловой Р.К. Мещерякова. – 4-е изд. перераб. и доп. – М.: Изд-во «Машиностроение» 1985. 496 с.: ил.
Горбацевич А.Ф. и Шкред В.А. Курсовое проектирование по технологии машиностроения. Издание 3-е дополн. и переработ. - Мн.: «Вышэйш. школа» 1983. – 288 с.: ил.
Шавлюга Н.И. Расчет и примеры наладок зубодолбежных и зубофрезерных станков. Изд. 3-е перераб. и доп. – Л.: «Машиностроение». Ленингр. отделение 1978. – 168 с.: ил.
Кирсанов Г.Н. и др. Руководство по курсовому проектированию металлорежущих инструментов: Учеб. Пособие для вузов по специальности «Технология машиностроения металлорежущие станки и инструменты» Под общ. ред. Г.Н. Кирсанова – М.: «Машиностроение» 1986. – 288 с.: ил.
Иванов М.Н. Детали машин: Учеб. для студентов высш. техн. учеб. заведений. - 5-е изд. перераб. – М.: «Высшая школа» 1991. – 383 с.: ил.
Сидоров В.Н. Безопасность труда при работе на металлообрабатывающих станках. –Л.: Лениздат. 1985. – 216 с.: ил.
Власов А.Ф. Безопасность труда при работе на металлорежущих станках. М. «Машиностроение» 1977. – 120с.
Короткевич А.Ф. Методические указания к самостоятельной работе для студентов специальности 1-36 01 03 «Технологическое оборудование машиностроительного производства». Оптимизация режимов резания. ГУ ВПО «Белорусско-Российский университет» 2010.
Короткевич А.Ф. Методические указания к курсовой работе для студнтов специальностей 1-36 01 01 «Технология машиностроения» часть 1. Металлорежущие станки. ГУ ВПО «Белорусско-Российский университет» 2011.
Рекомендуемые чертежи
- 26.04.2023
- 09.07.2014