Настройка зубофрезерного станка 5К32 и радиально-сверлильного станка 257




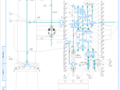
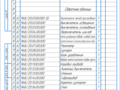
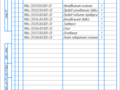
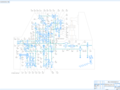
- Добавлен: 25.01.2023
- Размер: 1 MB
- Закачек: 2
Описание
Настройка зубофрезерного станка 5К32 и радиально-сверлильного станка 257
Состав проекта
![]() |
![]() ![]() ![]() ![]() |
![]() ![]() ![]() |
![]() ![]() ![]() ![]() |
![]() ![]() ![]() ![]() |
![]() ![]() ![]() ![]() |
![]() ![]() ![]() ![]() |
![]() ![]() ![]() ![]() |
![]() ![]() ![]() ![]() |
Дополнительная информация
vedomost257.spw

Ведомость технического проекта
Привод шпиндельной бабки
Привод подъема траверсы
Полая поворотная колонна
zapiska.docx
1.1 Область применения и назначение станка5
1.2 Технические характеристики станка5
1.3 Основные узлы принцип работы станка7
1.4 Назначение и обоснование выбора материала режущего инструмента8
1.5 Описание кинематической схемы станка. Уравнения кинематического баланса9
1.6 Определение требуемых режимов резания10
Настройка радиально-сверлильного станка 25712
1 Область применения и назначение технические характеристики станка12
2 Основные узлы станка13
3 Принцип работы и движения в станке14
4 Назначение и обоснование выбора материала режущего инструмента15
5 Описание кинематической схемы станка17
6 Определение оптимальных режимов обработки20
Мероприятия по технике безопасности29
Список используемой литературы39
В нашей стране развитию и совершенствованию парка металлорежущих станков и автоматов уделяется первостепенное внимание. Тираж металлорежущих станков темпы развития станкостроения уровень качества выпускаемых станков удельный вес автоматизированного оборудования в том числе с программным управлением мобильность станочного парка для изготовления разнообразных изделий высокая эффективность при эксплуатации станков — все это во многом определяет промышленный потенциал страны и характеризует уровень развития ее машиностроения.
Современные металлорежущие станки — это высокоразвитые машины включающие большое число механизмов и использующие механические электрические электронные гидравлические пневматические и другие методы осуществления движения и управления циклом. Высокую производительность процесса обработки современные станки обеспечивают за счет быстроходности мощности и широкой автоматизации. Существуют автоматические линии участки и цеха состоящие из десятков сложных станков и включающие контрольные и сборочные операции. Все большее развитие получают станки с программным управлением в том числе многоцелевые обеспечивающие высокую мобильность производства точность и производительность обработки. Автоматика все шире применяется не только для повышения производительности процесса обработки но и для получения его высоких качественных показателей.
1Настройка зубофрезерный станок 5К32
В Таблице 1.1 составим исходные данные для настройки станка модели 5К32
Таблица 1.1 – Исходные данные для настройки станка модели 5К32
Число зубьев колеса z
Направление наклона зуба колеса
Направление винтовой линии фрезы
Обрабатываемый материал:
1.1Область применения и назначение станка
Станок модели 5К32 является универсальным и предназначен для нарезания червячными фрезами прямозубых косозубых и червячных колес среднего размера шлицевых валиков и др. На этом станке можно производить зубонарезание методами встречного и попутного фрезерования.
Станок работает по замкнутому полуавтоматическому циклу имеет механизм для передвижения фрезы что увеличивает стойкость и срок службы фрез; позволяет производить работу при повышенных скоростях резания и подаче.
Повышенная жесткость и мощность станка обеспечивают высокое качество нарезаемых колес и увеличивают производительность.
1.2Технические характеристики станка
В таблице 1.2 приведены технические характеристики зубофрезерного станка модели 5К32:
Таблица 1.2 - Технические характеристики зубофрезерного станка модели 5К32
Наибольший нарезаемый модуль m мм
Наибольший диаметр нарезаемых колес:
Наибольшая ширина обрабатываемого венца колеса мм
Наибольшие размеры зуборезного инструмента мм
Наибольшее вертикальное перемещение суппорта мм
Наибольший угол поворота суппорта град
Расстояние между осями стола и фрезы мм
Наибольшие размеры червячной фрезы мм
Наибольшее перемещение суппортной стойки мм
Ускоренное перемещение каретки суппорта мммин
Наибольшее осевое перемещение фрезы мм
Расстояние от рабочей поверхности стола до оси фрезы мм
Габаритные размеры станка (длина х ширина х высота) мм
1.3 Основные узлы принцип работы станка
Рисунок 1 - Общий вид зубофрезерного станка модели 5К32
На Рисунке 1 представлен общий вид зубофрезерного станка модели 5К32. Станок включает в себя:
Переключатель метода фрезерования
Выключатель освещения
Выключатель охлаждения
Переключатель циклов
Лампочка - станок "Включен
Кнопка "Пуск-Стоп" главного привода
Кнопка "Пуск-стоп" цикла
Кнопка ускоренного подвода и отвода стола
Кнопка включения ускоренного хода суппорта
Кнопка "Пуск-Стоп" и лампочка передвижки фрезы
Рукоятка включения и выключения вертикальной подачи
Коробка распределения
Упор автоматического управления работой станка по циклу
Квадрат для натягивания ременной передачи главного привода
Квадрат шомпола крепленая оправки фрезы
Квадрат подъема и опускания шнека
Линейный выключатель
1.3Назначение и обоснование выбора материала режущего инструмента
Для обработки зубчатого колеса на зубофрезерном станке 5К32 используем червячную фрезу.
В соответствии с техническими требованиями червячные фрезы должны изготавливаться из быстрорежущей стали (ГОСТ 19265-73) с твердостью рабочей части 63-66 HRCЭ при этом твердость рабочей части фрезы изготовленной из быстрорежущей стали с содержанием ванадия 3% и более и кобальта 5% и более должна быть 64-67 HRCЭ.
Назначаем материал инструмента Р6М5Ф3 (для чистовых и получистовых инструментов при обработке нелегированных и легированных конструкционных сталей) [2ст 90].
Согласно ГОСТ 9324-80 принимаем основные размеры фрезы:
m=35мм-модуль колеса
da=80мм-диаметр вершин зубьев
d=40мм-делительный диаметр фрезы
df=60мм-диаметр впадин
l=120мм-длина инструмента
1.5 Описание кинематической схемы станка. Уравнения кинематического баланса
На Рисунке 2 изображена кинематическая схема модели станка 5К32.
Рисунок 2 – Кинематическая схема станка модели 5К32
Движения в станке: главное движение движение обкатки движение подачи дифференциальная цепь.
Цель главного движения.
Вращение фрезы осуществляется от электродвигателя Э1(45 квт при 1460 обмин) по следующей кинематической цепи:
где n – число оборотов фрезы в минуту выбираемое по принятой скорости резания мин-1.
Ведущим звеном в кинематической цепи делительного движения является фреза а ведомым – стол который за оборот фрезы должен поворачиваться вместе с заготовкой на оборотов по следующей цепи:
Вертикальная подача-это перемещение фрезы вдоль оси заготовки за один оборот стола.
Кинематическая цепь от стола к фрезерному суппорту:
Станок имеет устройство для автоматического выключения вертикальной подачи по окончании фрезерования колес.
Радиальная подача-это величина перемещения по направлению к оси заготовки за один оборот стола с заготовкой.
Кинематическая цепь радиальной подачи:
Тангенциальная (осевая) подача-перемещение червячной фрезы вдоль собственной оси.
Кинематическая цепь осевой подачи:
Механизм дифференциала.
Цепь дифференциала предназначена для дополнительного вращения стола с заготовкой. Это вращение должно быть со скоростью равной одному обороту стола за период вертикального перемещения суппорта на длину равную шагу винтовой линии колеса.
1.6 Определение требуемых режимов резания
Режимы резания при фрезеровании - это наивыгоднейшее сочетание скорости резания подачи и глубины резания обеспечивающее наименьшую трудоемкость выполнения операции при наиболее рациональном использовании оборудования и режущего инструмента.
При черновом и получистовом фрезеровании весь припуск целесообразно снимать за один ход. Если мощность станка не обеспечивает обработку за один ход то необходимо фрезерование проводить в несколько ходов.
Угол установки суппорта определяется из выражения:
где -угол подъема фрезы.
Подбор сменных колес гитары скоростей: допустимая скорость резания для материала СЧ15 при стойкости фрезы равной 240 мин и чистоте поверхности зуба 6 равна ммин а подача Sст =15 моб [3 табл. 33].
Находим число оборотов фрезы:
ближайшее число будет 153 обмин [3 табл. 29] и соответственно [3 по графику рис. 62].
Действительная скорость резания:
Подбор смены колес гитары деления: так как z 161 то и пользуясь формулой [3 формула 39] находим:
Устанавливаем сменные колеса: a=73; b=102; c=51; d=73.
Подбор смены колес гитары подач:
По формуле [3 формула 41] определяем:
=99; =110; =42; =84.
Подбор сменных колес гитары дифференциала:
По формуле [3 формула 44] определяем:
a2=115; b2=102; c2=91; d2=86.
Глубина фрезерования h=22535=78 мм.
Настройка радиально-сверлильного станка 257
1 Область применения и назначение технические характеристики станка
Станок радиально-сверлильный модели 257 предназначен для обработки отверстий диаметром до 75 мм главным образом в крупногабаритных и тяжелых деталях в условиях индивидуального и серийного производства.
Обрабатываемая деталь или узел устанавливаются в зависимости от размеров либо на столе либо на основании станка. Режущий инструмент закрепляется непосредственно в конусе шпинделя или при помощи патронов оправок и других приспособлений.
В процессе обработки всего комплекса отверстий с параллельными осями деталь остается неподвижной а совмещение оси режущего инструмента с осями обрабатываемых отверстий достигается поворотом траверсы с колонной и перемещением шпиндельной бабки вдоль траверсы. После совмещения осей производится зажим колонны и шпиндельной бабки на траверсе.
Для каждого перехода с помощью преселективного гидрофицированного механизма устанавливаются наивыгоднейшие скорость вращения шпинделя и величина подачи. Затем шпиндель вручную быстро подводится к обрабатываемому отверстию после чего включается механическая подача которая может быть автоматически отключена по достижении установленной глубины обработки.
В Таблице 1.3 приведены технические характеристики станка 257.
Таблица 1.3 Технические характеристики станка модели 257
Технические характеристики
Наибольший диаметр сверления стали в мм
Пределы вылета оси шпинделя от колонны в мм
Пределы расстояния от торца шпинделя до плиты в мм
Наибольшее осевое перемещение шпинделя в мм
Число скоростей вращения шпинделя
Пределы чисел оборотов шпинделя в минуту
Количество величин подач
Пределы величин подач шпинделя в ммоб
Мощность главного электродвигателя в кВт
2 Основные узлы станка
На Рисунке 3 указан радиально-сверлильный станок модели 257.
Рисунок 3 – Радиально-сверлильный станок 257
Основные узлы радиально-сверлильного станка 257: А — неподвижная колонна; Б — полая поворотная колонна; В — привод гидрозажима колонны и шпиндельной бабки; Г — привод подъема опускания и зажима траверсы; Д — шпиндельная бабка; Е — траверса; Ж — стол; 3 — основание.
На рисунке 1.2 изображены органы управления:
— кнопка освобождения гидравлических зажимов колонны и шпиндельной бабки; 2 — грибок точной настройки глубины сверления; 3 — кнопка включения гидравлических зажимов колонны и шпиндельной бабки; 4 — рукоятка переключения с механического на точное ручное перемещение шпинделя; 5—рычаг управления пусковыми фрикционами тормозом и гидравлическим механизмом переключения скоростей и подач; 6 —крестовой переключатель; 7 — маховичок ручного перемещения шпиндельной бабки по траверсе; 8 — маховичок осевого точного ручного перемещения шпинделя; 9 — флажок включения и отключения лимба настройки глубины сверления; 10—рукоятка быстрого ручного перемещения шпинделя и включения механической подачи шпинделя; 11 — диск предварительного выбора величины подачи 12 — диск предварительного выбора числа оборотов шпинделя.
3 Принцип работы и движения в станке
В приводе движения резания имеется двусторонняя многодисковая фрикционная муфта для включения выключения и реверсирования вращения шпинделя что облегчает управление станком защищает привод станка от перегрузки при высоких числах оборотов шпинделя и улучшает динамику привода при нарезании резьбы метчиками.
Для предохранения привода резания от поломок при низких числах оборотов шпинделя на переборном валу коробки скоростей установлена вторая многодисковая фрикционная муфта.
Станок имеет преселективное гидрофицированное управление коробкой скоростей и коробкой подач. Это позволяет предварительно устанавливать режимы обработки т. е. во время выполнения какого-нибудь перехода предварительно без остановки станка настроить механизм переключения на число оборотов шпинделя и величину подачи которые требуются для выполнения следующего перехода. После остановки шпинделя для смены режущего инструмента и последующего включения пускового фрикциона станок автоматически перестраивается на выбранный режим.
В целях предохранения от поломок и перегрузок механизма подъема и опускания траверсы в приводе этого механизма установлена шариковая предохранительная муфта.
Движение резания — вращение шпинделя. Движение подачи —прямолинейное поступательное перемещение шпинделя вдоль оси. Вспомогательные движения: ручное горизонтальное поступательное перемещение шпиндельной бабки по траверсе; механическое вертикальное поступательное перемещение траверсы по колонне и механический зажим траверсы на колонне; ручное вращение траверсы с колонной и шпиндельной бабкой относительно оси колонны гидравлический зажим поворотной колонны и шпиндельной бабки на траверсе; гидравлическое управление станком.
4 Назначение и обоснование выбора материала режущего инструмента
В соответствии с типом станка радиально-сверлильный 257. Инструментом при нарезании отверстия является сверло представленное на рис 4.
Рисунок 4 – Пример сверла для сверления отверстия
Спиральные свёрла изготавливают из быстрорежущей стали марок Р6М5 Р9 Р18 Р9К5 Р6М5К5.
Сверло с коническим хвостовиком — режущий инструмент с вращательным движением резания предназначено для сверления отверстий в сплошном слое материала. Могут также применяться для рассверливания и засверливания применяются для сверления различных материалов. Режущая часть имеет две режущие кромки по которым сходит стружка угол между главными режущими кромками сверла для сталей и чугунов равен 116 118°.
Различные виды сверл предназначены для обработки различных материалов. Исходя из особенности материала сверла могут существенно различаться по конструкции и особенностям.
Р6М5 – сталь быстрорежущая инструментальная. После отжига твердость составляет HB = 255 МПа. Применяется как правило для изготовления резьбонарезного инструмента режущего инструмента для изготовления сверл по металлу ударного инструмента.
Р6М5– сталь быстрорежущая инструментальная. После отжига твердость составляет HB = 269 МПа. Применяется как правило для изготовления металлорежущего инструмента предназначенного для сверления высокопрочных нержавеющих и жаропрочных сталей.
Для нарезания отверстия данного в условии курсового проекта выбираем материал сверла сталь P6M5 так как материал заготовки СЧ15 отверстие не глубокое (L10D).Твёрдость материала заготовки 180HB.
Основные размеры выбранного сверла приведены в Таблице1.4 и изображены на Рисунке 5:
Таблица 1.4 – Размеры сверла
Длина режущей кромкимм
Рисунок 5 – Выбранное сверло
5 Описание кинематической схемы станка
Рисунок 6 – Кинематическая схема станка
На рисунке 6 показана кинематическая схема проектируемого радиально-сверлильного станка 257. Кинематическая схема состоит из главного движения движения подачи и вспомогательного движения.
От электродвигателя через шесть валов на шпиндель передается 16 скоростей. В шпиндель вставляется режущий инструмент который обрабатывает заготовку установленную на столе.
Движение подачи осуществляется с помощью зацепления с полым валом главного движения.
Вращение от электродвигателя мощностью 55 кВт (рис. 3.1) передается ременной передачей валу I. На валу I установлен двойной подвижный блок шестерен Б1 который передает вращение на вал II при помощи шестерен 30––38 либо 34––34. (соединены с валом соответственно фрикционными муфтами Mф1 и Мф2. Со ступицей шестерни 30 жестко связан барабан колодочного тормоза Тб .)
Валу III движение передается двойной подвижный блок шестерен Б2 установленном на валу II шестернями 32—50 или колесами 41—41.
С вала III на вал IV вращение передается блоком Б3 зацеплениями 20–– 30 или 35––35.
Полый вал V получает движение через установленный на валу IV двойной подвижный блок шестерен Б4 с шестернями 20––80 либо 61––39 а шпиндель VI приводится в движение с помощью шлицевого соединения с полым валом V.
Далее вращение последовательно передается двойными подвижными блоками шестерен Б1 Б2 и Б3 переборному валику VI который связан с сидящими на нем приводными шестернями 47 и 34 предохранительной фрикционной муфтой Мп1.
При выключенной кулачковой муфте М2 полый вал VII и соответственно шпиндель VIII получают высокий ряд чисел оборотов через колеса 47—37 минуя предохранительную муфту Мп1 . При включении муфты М2 колеса 47 и 37 выходят из зацепления и вал VII и шпиндель VIII получают низкий ряд чисел оборотов через предохранительную муфту М п1 и шестерни 14—70.
Вращение от полого вала V передается валу VI коробки подач колесами 43—52. Два тройных подвижных блока шестерен Б5 и Б6 позволяют получить на валу IX коробки подач 9 скоростей вращения. Далее движение передается валу XI либо непосредственно когда включена кулачковая муфта М1 либо через перебор колесами 21—61 и 17—49.
Соосные валы XI и XII соединены кулачковой муфтой Мп1 являющейся одновременно предохранительной. От вала XII через червячную передачу 1—50 вращение получает полый вал XIII. На конце его закреплена шестерня 12 находящаяся в зацеплении с рейкой m=4 мм нарезанной на шпиндельной гильзе Гш .
Червячное колесо 50 сидит на валу XIII свободно и соединяется с ним фрикционно-зубчатой муфтой М2 которая управляется рукояткой Р. При перегрузке механизма подач колесо 50 останавливается а червяк продолжая вращаться перемещается с валом XII вниз и посредством шайбы закрепленной на верхнем торце вала XII. расцепляет предохранительную муфту Мп1. В исходное положение червяк возвращается под действием пружины П.
Вспомогательное движение
Быстрые ручные перемещения шпинделя вдоль оси осуществляются рукоятками Р при выключенной муфте М2. Для этого рукоятки Р оттягивают на себя и поворачивают совместно с валом XIII от которого движение через реечную передачу сообщается гильзе со шпинделем. Точное ручное перемещение шпинделя вдоль оси производится маховиком Мх1 когда отключена кулачковая предохранительная муфта Мп2.
Автоматическое выключение механической подачи по достижении заданной глубины обработки производится упором У который расцепляет фрикционно-зубчатую муфту М2. Грубая установка упора У на заданную глубину обработки осуществляется но делениям лимба Л. Тонкая установка производится по нониусу грибком Гр через червячную передачу 1—53.
Перемещение шпиндельной бабки по направляющим траверсы осуществляется вручную маховичком Мх2. вращение от которого через вал XIV (на схеме условно изогнут) и шестерню 12 передается реечному колесу 19. Последнее находится в зацеплении с закрепленной на траверсе рейкой т = 3 мм.
Вертикальное перемещение и зажим траверсы на поворотной колонне производится электродвигателем мощностью 2.8 кВт. Вертикальный ходовой винт XVI с шагом 8 мм получает вращение от электродвигателя через редуктор с колесами 22—80 и 16—68. Шариковая предохранительная муфта Мп1 ограничивает предельную нагрузку на механизм подъема траверсы.
Закрепление поворотной колонны и шпиндельной бабки производится от отдельного гидромеханического привода. При включении установленного на колонне электродвигателя мощностью 05 кВт связанный с ним гидронасос Н подает масло в зависимости от направления вращения электродвигателя в правую или левую полость гидроцилиндра Ц. Для зажима масло подается в левую полость цилиндра. Тогда плунжер Пр с рейкой перемещается вправо и через колесо 32 вал XVII и шестерню 20 поворачивает зубчатый сектор С3 с кулачками К. Последние воздействуя на рычаги Рг заклинивают трапецеидальные полукольца Пк между поворотной и неподвижной колоннами.
Одновременно с поворотом вала XVII посредством конической передачи 17—17 приводится во вращение вал XVIII и эксцентриковая втулка Э связанная с валом скользящей шпонкой.
При повороте эксцентриковой втулки башмак Бк опускается вниз и. упираясь в направляющую траверсы закрепляет шпиндельную бабку на траверсе.
6 Определение оптимальных режимов обработки
При расчете режимов резания на металлорежущих станках в том числе на агрегатных станках и автоматических станочных линиях необходимо принимать во внимание ряд факторов действующих в процессе обработки детали и накладывающих ограничения на режимы резания. Назовем эти факторы техническими ограничениями.
Техническими ограничениями могут быть различные элементы технологического процесса относящиеся к заготовке к станку к инструменту и т.д.
Режущие возможности инструмента. Это ограничение устанавливает взаимосвязь между скоростью резания обусловленной принятой стойкостью инструмента материалом режущей части инструмент его геометрическими параметрами глубиной резания подачей механическими свойствами обрабатываемого материала с одной стороны и скоростью резания определяемой кинематикой станка с другой.
Первое техническое ограничение. Режущие возможности инструмента
Экономическая скорость резания т. е. скорость соответствующая экономической стойкости учитывающая режущие возможности инструмента экономику производства и организацию инструментального хозяйства определяется для различных инструментов и видов обработки по приводимым ниже формулам: при сверлении в стали с HB > 155 и других металлов [6 стр.276]:
где Т - период стойкости мин; Т = 15 мин [6 стр. 279 табл. 30].
m - показатель степени при T;
s - подача при сверлении в ммоб;
Сv - постоянный коэффициент зависящий от условий обработки;
Kv - общий поправочный коэффициент;
D - диаметр обработки мм;
q y m - показатели степеней.
Согласно [6 cтр. 278 табл. 28] Cv =147; m = 0125; q = 04; у = 05.
Скорость резания определяемая кинематикой станка выражается формулой:
гдеD-диаметр обработки или инструмента в мм;
п- число оборотов изделия или инструмента в мин-1.
Приравнивая правые части формул (2.1) и (2.2) получаем:
При сверлении глубина резания [6 стр.276].
Общий поправочный коэффициент для скорости резания Kv определим по формуле:
где Kv - коэффициент учитывающей влияние материала заготовки;
Кnv - коэффициент учитывающий состояние поверхности заготовки;
Kiv - коэффициент учитывающий материал инструмента.
где nv- показатель степени.
nv=13 [6 cтр. 262 табл. 2];
Knv=115 [6 cтр. 263 табл. 6];
Kiv=06 [6 cтр. 280 табл. 31].
Прологарифмируем уравнение (6):
Обозначив через X1=ln(n) X2=ln(1000S) получим следующее уравнение.
Уравнение первого ограничения:
Второе техническое ограничение. Мощность электродвигателя привода главного движения станка или электродвигателя силовой головки
Крутящие моменты на шпинделе станка возникающие вследствие наличия окружной силы резания для разных случаев обработки определяются [6 стр.277]:
гдеСМ - коэффициент крутящего момента;
Kp- коэффициент учитывающий фактические условия обработки.
По [6 стр.281 табл.32]: Сv = 0021; q = 2; yz = 08.
Крутящий момент на шпинделе станка соответствующий мощности мотора электродвигателя главного привода станка и числу оборотов шпинделя равен:
гдеNn - мощность электродвигателя главного привода станка в кВт;
- коэффициент полезного действия передачи;
п - число оборотов шпинделя в мин-1.
Сравнивая правые части формул (11) и (12) получаем:
Уравнение характеризующее второе ограничение для сверления будет иметь вид:
Согласно исходным данным для обработки применяется станок 257 с наибольшей глубиной сверления 44 мм и мощностью привода главного движения 45 кВт; коэффициент полезного действия привода главного движения станка =081.
Согласно [6 стр.281] коэффициент учитывающий фактические условия обработки вычисляем формуле:
гдеКMp - поправочный коэффициент для стали и чугуна учитывающий влияние качества обрабатываемого материала на силовые зависимости.
По данным [6 стр.264 табл.9]:
Подставляя в формулу (14):
Уравнение второго ограничения:
Уравнение характеризующее третье ограничение (заданную производительность станка) будет иметь вид:
где L – длина рабочего хода инструмента по условию задания равна 46 мм;
R – заданная производительность станка. Принимаем производительность 8 штч. В случае несоответствия уравнений данную величину можно уменьшить для решения задачи;
КЗ – коэффициент загрузки станка для среднесерийного производства принимаем 075;
rR – число деталей обрабатываемых одновременно на одной позиции при обработке равно 1;
ТВ.Н – вспомогательное неперекрываемое время мин. Для среднесерийного производства принимаем 4 минуты.
Уравнение третьего ограничения:
Уравнение характеризующее четвёртое ограничение (наименьшую скорость резания) будет иметь вид:
n cn min- минимальная частота вращения шпинделя станка.
По паспорту станка наименьшая частота вращения шпинделя nmin= 34мин-1. Соответственно лимитирующей частотой вращения будет частота соответствующая скорости Vmin = 10 ммин и коэффициент рассчитаем по формуле:
Уравнение четвёртого ограничения будет иметь вид:
Получим значения соответствующие пятому ограничению (наибольшая возможная скорость резания допустимая кинематикой станка). Рассмотрим общее уравнение учитывающее и максимальную скорость резания исходя из режущих способностей твердосплавного инструмента и максимальную скорость резания которую можно получить для данных условий обработки исходя из кинематики станка.
Как правило теплостойкость твердосплавного инструмента достаточно высока и главным ограничивающим фактором при выборе верхнего предела скорости резания при расчёте данного ограничения является наибольшая частота вращения по станку. По паспорту станка наибольшая частота вращения шпинделя ncт max=1400 мин-1.
Уравнение пятого ограничения будет иметь вид:
Шестое техническое ограничение. Наибольшая подача допустимая прочностью или жесткостью инструмента и обрабатываемой детали условиями размещения стружки в стружечных канавках инструментов требованиями к чистоте обрабатываемой поверхности и прочностью механизма подачи станка.
Осевая сила P0 рассчитывается по формуле [6 стр.277]:
гдеСp - коэффициент осевой силы;
Kp - коэффициент учитывающий фактические условия обработки.
По [6 стр.281 табл.32]: Ср = 427 q = 1 yv = 08.
Усилие подачи действующее при резании на инструмент должно быть меньше усилия подачи допускаемого прочностью механизма подачи станка или силовой головки т. е. должно всегда соблюдаться неравенство:
Уравнение характеризующее шестое ограничение для сверления будет иметь вид приравниваем формулы (2.18) и (2.19):
Согласно паспорту станка наибольшее усилие допускаемое механизмом продольной подачи Рст.доп.=28000 Н.
Общий поправочный коэффициент Кр принимаем значение по формуле:
Уравнение шестого ограничения будет иметь вид:
Уравнение характеризующее седьмое ограничение (наименьшая подача допускаемая кинематикой станка) будет иметь вид:
где Sст min- наименьшая подача допускаемая кинематикой станка.
Уравнение седьмого ограничения будет иметь вид:
Уравнение характеризующее восьмое ограничение (наибольшая подача допускаемая кинематикой станка) будет иметь вид:
где - наибольшая подача допускаемая кинематикой станка.
Уравнение восьмого ограничения:
Существует еще несколько ограничений: прочность режущего инструмента и жёсткость технологической системы. Эти ограничения мы устраним организационно. Для повышения жесткости обработки мы будем использовать люнет. Для устранения ограничения по прочности режущего инструмента мы будем использовать инструмент с сечением достаточным для обеспечения обработки на максимальных условиях обработки.
В результате произведённых расчётов мы получили систему уравнений характеризующих процесс резания для данных условий обработки.
Целевая функция имеет вид:
Найдем графически оптимальные значения и :
Рисунок 7 – Графическое изображение математической модели процесса резания.
На рисунке 7 изображены прямые неравенств системы и выделена область возможных решений этой системы.
Максимальное значение целевой функции при пересечении области значений:
Оптимальную частоту вращения шпинделя nопт определим по формуле:
Оптимальную подачу определим по формуле:
Принимаем nопт = 139409 мин-1 Sопт = 199 ммоб.
Полученные значения режимов резания являются оптимальными для заданных исходных данных.
Мероприятия по технике безопасности
При работе на зубообрабатывающих станках необходимо соблюдать правила техники безопасности общие для металлообрабатывающего оборудования (долбежных фрезерных шлифовальных станков). Наряду с этим зубообработка предъявляет свои специфические требования. Так при проектировании зубообрабатывающих станков необходимо предусматривать защитные экраны предохраняющие зону резания. Как правило зуборезный инструмент многозубый с острыми режущими кромками поэтому при использовании его необходимо соблюдать специальные меры предосторожности: установку и снятие инструмента со станка производить в рукавицах а для очистки инструмента от стружки иметь металлические щетки. Во время работы станка нельзя осуществлять контроль обрабатываемой детали и поднастройку станка на размер. Хранить дорогостоящий режущий инструмент необходимо в специальной таре. Съем и установку заготовок на станок не следует делать при вращающемся инструменте.
1. Работать только на станках к которым имеется допуск и выполнять работу которая поручена.
2. Сосредоточить внимание на выполняемой работе не отвлекаться на посторонние дела и разговоры не отвлекать других.
3. Не допускать на свое рабочее место лиц не имеющих отношения к порученной работе. Без разрешения мастера не доверять свой работающий станок другому рабочему.
4. Не опираться на станок во время его работы и не позволять делать это другим.
5. Заметив нарушение инструкции другим рабочим предупредить его о необходимости соблюдения требований по технике безопасности.
6. О всяком несчастном случае немедленно поставить в известность мастера или бригадира и обратиться в медицинский пункт.
7. При ремонте станка и пусковых устройств на станке должен быть вывешен плакат: «Не включать — ремонт».
8. Нельзя работать на неисправном и не имеющем необходимых ограждений станке. Не производить ремонт и переделку станка самостоятельно.
9. Не разрешать уборщику убирать у станка во время его работы.
10. Запрещается работать на станке в рукавицах или перчатках а также с забинтованными пальцами без резиновых напальчников.
11. Во избежание несчастных случаев и попадания грязи и стружки в механизмы станка запрещается обдувать воздухом из шланга обрабатываемую поверхность и станок.
12. Надежно и жестко закреплять обрабатываемую деталь на станке.
13.и габаритные размеры обрабатываемой детали должны соответствовать паспортным данным станка.
14. Устанавливать и снимать тяжелые детали и приспособления (массой более 16 кг) только с помощью подъемных механизмов. Не превышать нагрузку установленную для грузоподъемных средств.
15. Пользоваться грузоподъемными механизмами только после специального обучения и аттестации.
16. Деталь должна быть надежно застроплена; для подъема применять специально строповочно-захватные приспособления. Освобождать обрабатываемую деталь от стропов или захватных приспособлений только после надежной установки где надо — и закрепления детали на станке.
17. Отрегулировать местное освещение станка так чтобы рабочая зона была достаточно освещена и свет не слепил глаза. Протереть арматуру и светильник. Пользоваться местным освещением напряжением выше 36В запрещается.
18. При всяком перерыве в подаче электроэнергии немедленно выключить электрооборудование станка.
19. Если на металлических частях станка обнаружено напряжение (ощущение тока) электродвигатель работает на две фазы (гудит) заземляющий провод оборван остановить станок и немедленно доложить мастеру о неисправности электрооборудования.
20. Если пол скользкий (облит маслом эмульсией) потребовать чтобы его посыпали опилками или сделать это самому.
21. Пользоваться деревянной решеткой и содержать ее в исправном состоянии.
22. Каждый рабочий обязан:
а) требовать от администрации цеха проведения инструктажа по технике безопасности до назначения на работу и при переводе на станок другой модели;
б) требовать от администрации цеха чтобы печатная инструкция о мерах безопасности при работе на данном станке находилась на рабочем месте станочника;
в) строго выполнять все правила безопасности;
г) обязательно пользоваться полагающейся спецодеждой спец. обувью и индивидуальными защитными средствами (очками респираторами масками и др.);
д) при обнаружении возможной опасности предупредить товарищей и немедленно сообщить администрации цеха;
е) содержать в чистоте рабочее место в течение всего рабочего дня и не загромождать его деталями заготовками металлическими отходами мусором и т. п.;
ж) укладывать устойчиво на подкладках и стеллажах поданные на обработку и обработанные детали; высота штабелей не должна превышать для мелких деталей
м для средних — 1 м для крупных — 15 м;
з) применять только исправные гаечные ключи соответствующих размеров;
и) при работе ключами не наращивать их трубой или другими рычагами; нельзя пользоваться прокладками если ключи не соответствуют размерам гаек.
к) не мыть руки в масле эмульсии керосине и не вытирать их обтирочными концами загрязненными стружкой;
л) не принимать пищу у станка;
м) не оставлять свою одежду на рабочем месте.
23. На территории выполнять следующие правила:
а) быть внимательным к предупредительным сигналам автомашин и других видов движущегося транспорта;
б) не находиться под поднятым грузом;
в) не проходить в местах не предназначенных для прохода;
г) не заходить без разрешения за ограждения технологического оборудования;
д) не прикасаться к токоведущим частям электрооборудования клеммам и электропроводам к арматуре общего освещения не открывать дверцы электрошкафов; в необходимых случаях обращаться к электромонтеру;
е) не включать и не останавливать (кроме аварийных случаев) станки механизмы работа на которых Вам не поручена.
24. Работая с подручным или учеником обучать его безопасным приемам работы и следить за их выполнением.
25. К работе с грузоподъемными кранами могут быть допущены лица не моложе 18 лет специально обученные систематически инструктируемые сдавшие экзамен квалификационной комиссии и имеющие на руках удостоверение.
Требования безопасности перед началом работы:
1. Перед каждым включением станка убедиться что пуск станка никому не угрожает опасностью.
2. Привести в порядок рабочую одежду: застегнуть или подвязать обшлага рукавов надеть головной убор; женщины должны убрать волосы под косынку повязанную без свисающих концов.
3. Проверить хорошо ли убраны станок и рабочее место выявить неполадки в работе станка и принять меры по их устранению.
4. О неисправности станка немедленно заявить мастеру; до устранения неисправности к работе не приступать.
5. Приготовить крючок для удаления стружки ключи и другой необходимый инструмент. Не применять крючок с ручкой в виде петли.
6. Проверить наличие и исправность;
а) ограждений зубчатых колес приводных ремней валиков приводов и пр. а также токоведущих частей электрической аппаратуры (пускателей рубильников трансформаторов кнопок);
б) заземляющих устройств;
в) предохранительных устройств для защиты от стружки охлаждающих жидкостей;
г) устройств для крепления инструмента (отсутствие трещин надломов прочность крепления пластинок твердого сплава или керамических пластинок стружколомающих порогов и пр.);
д) режущего измерительного крепежного инструмента и приспособлений и разложить их в удобном для пользования порядке.
Работать только исправным инструментом и приспособлениями и применять их строго по назначению.
7. Если при обработке металла образуется отлетающая стружка то при отсутствии специальных защитных устройств на станке надеть защитные очки или предохранительный щиток из прозрачного материала.
8. При обработке вязких металлов дающих сливную стружку применять резцы со специальными стружколомающими устройствами.
9. При обработке хрупких металлов (чугуна бронзы и т. д.) дающих отлетающую стружку а также при дроблении стальной стружки в процессе обработки применять следующие защитные устройства: специальные стружкоотводчики прозрачные экраны или индивидуальные щитки (для защиты лица).
10. Проверить на холостом ходу станка:
а) исправность органов управления (механизмов главного движения подачи пуска останова движения и др.);
б) исправность системы смазки и охлаждения (убедиться в том что смазка и охлаждающая жидкость подаются нормально и бесперебойно);
в) исправность фиксации рычагов включения и переключения (убедиться в том что возможность самопроизвольного переключения с холостого хода на рабочий исключена);
г) нет ли заеданий или излишней слабины в движущихся частях станка особенно в шпинделе в продольных и поперечных салазках суппорта.
11. Для предупреждения кожных заболеваний рук при применении на станках охлаждающих масел и жидкостей по указанию врача перед началом работ смазывать руки специальными пастами и мазями.
12. Проверять доброкачественность ручного инструмента при получении его из кладовой:
а) ручка напильника и шабера должна иметь металлическое кольцо предохраняющее ее от раскалывания;
б) молоток должен быть насажен на рукоятку овального сечения расклиненную металлическим клином и изготовленную из твердых и вязких пород дерева; боек молотка должен иметь ровную слегка выпуклую поверхность; нельзя работать молотком со сбитым бойком имеющим трещины или насаженным на рукоятку из дерева мягких пород а также плохо закрепленным на рукоятке:
в) зубило и другой ударный инструмент должны быть длиной не менее 150 мм кернер— 100 мм и не иметь наклепа на бойке;
г) гаечные ключи должны быть исправными и соответствовать размеру гаек; запрещается работать гаечными ключами с прокладками удлинять их трубами и применять контрключи;
д) разложить инструмент и приспособления в удобном для пользования порядке.
13. Пользоваться режущим инструментом имеющим правильную заточку. Применение неисправного инструмента и приспособлений запрещается.
14. Проверить и обеспечить достаточную смазку станка; при смазке пользоваться только соответствующими приспособлениями.
15. Разместить шланги подводящие охлаждающую жидкость так чтобы была исключена возможность соприкосновения их с режущим инструментом и движущимися частями станка. Охлаждающую жидкость подавать только насосом.
16. Запрещается охлаждать режущий инструмент мокрыми тряпками или щетками.
17. Не допускать разбрызгивания масла и жидкости на пол. Для защиты от брызг устанавливать щитки.
Требования безопасности во время работы:
1. Выполнять указания по обслуживанию и уходу за станками изложенные в «Руководстве к станку» а также требования предупредительных таблиц имеющихся на станке.
2. Устанавливать и снимать режущий инструмент только после полного останова станка.
3. Не работать без кожуха прикрывающего сменные шестерни.
4. Остерегаться срыва ключа правильно накладывать ключ на гайку и не поджимать им гайку рывком.
5. Во время работы станка не брать и не подавать через работающий станок какие-либо предметы не подтягивать болты гайки и другие соединительные детали станка.
6. Остерегаться наматывания стружки на обрабатываемый предмет или резец не направлять вьющуюся стружку на себя. Пользоваться стружколомателем.
7. Не удалять стружку от станка непосредственно руками и инструментом пользоваться для этого специальными крючками и щетками-сметками.
8. Следить за своевременным удалением стружки с рабочего места и станка.
9. Остерегаться заусенцев на обрабатываемых деталях.
10. При возникновении вибрации остановить станок. Принять меры к устранению вибрации: проверить крепление резца и детали.
11. Обязательно остановить станок и выключить электродвигатель при:
а) уходе от станка даже на короткое время (если не поручено обслуживание двух или нескольких станков);
б) временном прекращении работы;
в) перерыве в подаче электроэнергии;
г) уборке смазке чистке станка;
д) обнаружении неисправности в оборудовании;
е) подтягивании болтов гаек и других соединительных деталей станка;
ж) установке измерении и съеме детали;
з) проверке или зачистке режущей кромки резца;
и) снятии и надевании ремней на шкивы станка.
12. Передвижение ремня по ступенчатым шкивам на ходу допускается только с применением переводок.
13. При обработке деталей применять режимы резания указанные в операционной карте для данной детали.
14. Не увеличивать установленные режимы резания без ведома мастера.
15. При закреплении детали в кулачковом патроне или использовании планшайб следует захватывать деталь кулачками на возможно большую величину. Не допускать чтобы после закрепления детали кулачки выступали из патрона или планшайбы за пределы их наружного диаметра. Если кулачки выступают заменить патрон или установить специальное ограждение.
16. При установке (навинчивании) патрона или планшайбы на шпиндель подкладывать под них на станок деревянные прокладки с выемкой по форме патрона (планшайбы).
17. Устанавливать тяжелые патроны и планшайбы на станок и снимать их со станка при помощи подъемного устройства и специального захватного приспособления.
18. Не свинчивать патрон (планшайбу) внезапным торможением шпинделя. Свинчивание патрона (планшайбы) ударами кулачков о подставку допускается только при ручном вращении патрона; в этом случае следует применять подставки с длинными ручками (для удержания рукой).
19. В кулачковом патроне без подпора центром задней бабки можно закреплять только короткие длиной не более двух диаметров уравновешенные детали; в других случаях для подпора пользоваться задней бабкой.
20. При обработке в центрах деталей длиной равной 12 диаметрам и более а также при скоростном и силовом резании деталей длиной равной восьми диаметрам и более применять дополнительные опоры (люнеты).
21. При обработке деталей в центрах проверить закреплена ли задняя бабка и после установки изделия смазать центр. При дальнейшей работе нужно периодически смазывать задний центр.
22. При работе с большими скоростями применять вращающийся центр прилагаемый к станку.
23. Нельзя работать со сработанными или забитыми центрами.
24. При обточке длинных деталей надо следить за центром задней бабки: периодически центр следует смазывать и проверять осевой зажим.
25. Во избежание травм из-за инструмента необходимо:
а) включить сначала вращение шпинделя а затем подачу; при этом обрабатываемую деталь следует привести во вращение до соприкосновения ее с резцом врезание производить плавно без ударов;
б) перед остановом станка сначала выключить подачу отвести режущий инструмент от детали а потом выключить вращение шпинделя.
26. Резцовую головку отводить на безопасное расстояние при выполнении следующих операций: центровании деталей на станке зачистке шлифовании деталей наждачным полотном опиловке шабровке измерении деталей а при смене патрона и детали отодвигать подальше также задний центр (заднюю бабку).
27. Следить за правильной установкой резца и не подкладывать под него разные куски металла; пользоваться подкладками равными площади резца.
28. Резец следует зажимать с минимально возможным вылетом и не менее чем тремя болтами. Нужно иметь набор подкладок различной толщины длиной и шириной не менее опорной части резца. Не следует пользоваться случайными подкладками.
29. Не затачивать короткие резцы без соответствующей оправки.
30. При подводке резца к оправке или планшайбе соблюдать осторожность и избегать чрезмерно глубокой подачи резца.
31. При надевании планшайбы на конец шпинделя очистить ее от стружки и загрязнения.
32. При обработке вязких металлов дающих сливную ленточную стружку применять резцы с выкрутками накладными стружколомателями или стружкозавивателями.
33. Не пользоваться зажимными патронами если изношены рабочие плоскости кулачков.
34. При скоростном резании на токарных станках работать с не вращающимся центром запрещается.
35. Обрабатываемую поверхность располагать как можно ближе к опорному или зажимному приспособлению.
36. При установке детали на станок не находиться между деталью и станком.
37. Не класть детали инструмент и другие предметы на станину станка и крышку передней бабки.
38. При отрезании тяжелых частей детали или заготовок не придерживать отрезаемый конец руками.
39. При опиловке зачистке шлифовании обрабатываемых деталей на станке:
а) не прикасаться руками или одеждой к обрабатываемой детали;
б) не производить указанных операций с деталями имеющими выступающие части пазы и выемки (пазы и выемки предварительно заделывать деревянными пробками);
в) стоять лицом к патрону держать ручку напильника левой рукой не перенося правую руку за деталь.
40. Для обработки деталей закрепленных в центрах применять безопасные поводковые патроны (например чашкообразного типа) или безопасные хомутики.
41. После закрепления детали в патроне вынуть торцовый ключ.
42. При закреплении детали в центрах:
а) протереть и смазать центровые отверстия;
б) не применять центр с изношенными или забитыми конусами;
в) следить за тем чтобы размеры токарных центров соответствовали центровым отверстиям обрабатываемой детали;
г) не затягивать туго задний центр надежно закреплять заднюю бабку и пиноль;
д) следить за тем чтобы деталь опиралась на центр всей конусной частью центрового отверстия; не допускать упора центра в дно центрового отверстия детали.
43. Работать на станке без закрепления патрона сухарями предотвращающими самоотвинчивание при реверсе запрещается.
44. Не тормозить вращение шпинделя нажимом руки на вращающиеся части станка или детали.
Эксплуатация металлообрабатывающего оборудования должна отвечать требованиям ГОСТ 12.2.009 СТ СЭВ 538 СТ СЭВ 539 СТ СЭВ 500 в соответствии с которыми при работе на станках сверлильной группы предусматривается выполнение следующих требований:
Проверить хорошо ли убрано рабочее место и при наличии неполадок в работе станка в течении предыдущей смены ознакомиться с ними и с принятыми мерами по их устранению.
Проверить состояние решетки под ногами ее устойчивость.
Проверить состояние ручного инструмента.
Привести в порядок рабочее место: убрать все лишнее подготовить и аккуратно разложить необходимые инструменты и приспособления так чтобы было удобно и безопасно ими пользоваться.
Проверить состояние местных грузоподъемных устройств.
Проверить состояние станка: убедиться в исправности электропроводки заземляющих проводов.
На холостом ходу проверить исправность кнопок “Пуск” и “Стоп”.
Подготовить средства индивидуальной защиты и проверить их исправность.
и габаритные размеры заготовок должны соответствовать паспортным данным станка.
При обработке заготовок массой более 16кг устанавливать и снимать с помощью грузоподъемных устройств причем не допускать превышения нагрузки установленной на них.
При необходимости пользоваться средствами индивидуальной защиты. Запрещается работать в рукавицах и перчатках а также с забинтованными пальцами без резиновых напальчников.
Перед каждым включением станка убедиться что его пуск не для кого не опасен.
Если в процессе обработки образуется отлетающая стружка установить переносные краны для защиты окружающих и надеть защитные очки или предохранительный щиток. Следить за своевременным удалением стружки как со станка так и с рабочего места.
Правильно укладывать обработанные детали не загромождать подходы к станку.
Обязательно выключать станок при уходе даже на короткое время при регулировке уборке и смазывании станка.
По окончании работы стружку смести в поддон или на совок щеткой. Во избежание несчастного случая и попадания стружки в организм запрещается для очистки станка использовать сжатый воздух.
Проверить качество уборки станка выключить местное освещение и отключить станок от электросети.
Осуществить санитарно-гигиенические мероприятия.
Кроме указанного каждый станочник обязан: работать только на том станке к эксплуатации которого он допущен; без разрешения мастера не допускать к работе на станке других лиц; о всяком несчастном случае немедленно ставить в известность мастера и обращаться в медицинский пункт; уметь оказывать первую помощь пострадавшему применять первичные средства пожаротушения и проводить работы по устранению последствий аварийных ситуаций или пожара.
При выполнении курсовой работы по «Металлорежущим станкам» были практически применены знания по данной дисциплине полученные за прошедший период обучения.
Целью данной курсовой работы являлось по исходным данным произвести настройку зубофрезерного станка модели 5К32 на изготовление цилиндрического косозубого зубчатого колеса и произвести настройку радиально-сверлильного станка модели 257 на обработку поверхности заданной в условии.
В результате решения данной курсовой работы были изучены назначения и технические характеристики станков их основные узлы и принципы работы были рассмотрены кинематические схемы станков. Также были выбраны и обоснованы материалы режущих инструментов для каждой операции по обработке с определением требуемых режимов резания. Мы ознакомились с основными положениями по технике безопасности характерными для зубообрабатывающих и сверлильных групп станков. Были получены навыки благодаря которым мы смогли произвести настройку станов моделей 5К32 и 257. По данным курсовой работы была произведена настройка зубофрезерного станка 5К32 на изготовление цилиндрических косозубых зубчатых колес а также радиально-сверлильного станка 257 на обработку заданной поверхности в виде отверстия.
С помощью навыков полученных при выполнении курсовой работы мы можем решать аналогичные задачи которые могут быть поставлены перед нами в других курсовых работах дипломном проекте а также на производстве.
Список используемой литературы
Паспорт зубофрезерного станка модели 5К32.Универсальные зубофрезерные станки.
Ординарцев И.А. Справочник инструментальщика И.А. Ординарцев. –Л. : Новое знание 2009.-1039 с. : ил.
Мерчанский Д.П. Зуборезное дело Д. П. Мерчанский. – Л. : Машиностроение 1987.-846 с. : ил.
Боранчиков В.И. Прогрессивные режущие инструменты и режимы резания металлов В. И. Боранчиков.-М. :Машиностроение 1990-400 с. : ил.
Справочник технолога-машиностроителя Под ред. А.Г. Косиловой Р.К. Мещерякова. –4-е изд. перераб. и доп. – М.: Машиностроение-1 1985. – 944 с.: ил. Т 2.
Горанский Г.К. Расчёт режимов резания при помощи ЭВМ Г. К. Горанский. – Минск.: Выш. шк. 1963. – 192 с. : ил.
Паспорт вертикально-сверлильного станка модели 2А135.
Режущий инструмент: Учеб. пособие Рыжкин А. А. Каганов В. С. Дмитриев В. С.; ДГТУ.- Электронное издание.- Ростов нД 2000.- 1 CD-ROM
Тайц Б. А. Производство зубчатых колес: справочник Б. А. Тайц С. Н. Калашников А. С. Калашников Г. И. Коган – М. : Машиностроение 1990.–464с.
Шевлюга Н. И. Расчет и примеры наладок зубофрезерных и зубодолбежных станков Н. И. Шевлюга –Л.: Машиностроение 1978. – 168 с.
Паспорт зубофрезерного станка модели 5Е32. Универсальные зубофрезерные станки.
Иванов М. И. Детали машин: учебное пособиеМ. И. Иванов – М.: Высшая школа 1998.–383с.
Косилова А. Г. Справочник технолога-машиностроителя: справочник в 2 т. А. Г. Косилова Р. К. Мещерякова – М. :Машиностроение 1985.–Т.2. – 496с.
Vedomost5к32.frw

Ведомость технического проекта
Белорусско-Российский
Переключатель метода фрезерования
Выключатель освещения
Выключатель охлаждения
Переключатель циклов
Кнопка ускоренного подвода и отвода стола
Рукоятка включения и выключения вертикальной подачи
Квадрат шомпола крепленая оправки фрезы
Линейный выключатель
optimizatsia.cdw

Obschiy_vid_5K32.cdw

Белорусско-Российский университет
Kinematika_5K32.cdw

схема кинематическая
Белорусско-Российский университет
Kinematicheskaya_skhema_257.cdw

N=5.5 квт n=1450 мин
Канематическая схема
радиально-сверлильного
Белорусско-Российский
университет гр. АТП-171
Stanok_257_Obschiy_vid.cdw

- полая поворотная колонна;
- привод гидрозажима колонны и шпиндельной бабки;
опускания и зажима траверсы;
- шпиндельная бабка;
радиально-сверлильного
Белорусско-Российский
Рекомендуемые чертежи
- 29.05.2015