Модернизация привода главного движения на базе станка 2Н 135


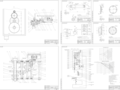
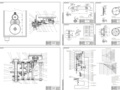
- Добавлен: 25.01.2023
- Размер: 776 KB
- Закачек: 0
Узнать, как скачать этот материал
Подписаться на ежедневные обновления каталога:
Описание
Модернизация привода главного движения на базе станка 2Н 135
Состав проекта
![]() |
![]() ![]() ![]() |
![]() ![]() ![]() |
![]() ![]() ![]() ![]() |
![]() ![]() ![]() ![]() |
![]() ![]() ![]() |
![]() ![]() ![]() |
![]() ![]() ![]() |
Дополнительная информация
Контент чертежей
На печать.frw

На печать.dwg

Рекомендуемые чертежи
- 22.11.2015
- 16.03.2019
Свободное скачивание на сегодня
Обновление через: 10 часов 14 минут