Курсовой проект (техникум) - Разработка технологии обслуживания и ремонта автобусов марки HIGER KLQ-6891 АО «АПОПАТ» г. Альметьев



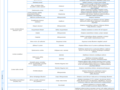
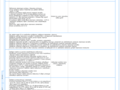
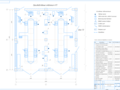
- Добавлен: 04.11.2022
- Размер: 13 MB
- Закачек: 1
Описание
Состав проекта
![]() |
![]() |
![]() ![]() ![]() ![]() |
![]() ![]() ![]() ![]() |
![]() ![]() ![]() ![]() |
![]() |
![]() |
![]() |
![]() ![]() ![]() |
![]() |
Дополнительная информация
карта диагностики автобуса.cdw
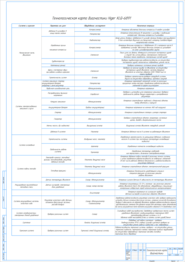
Система подачи топлива
Регулированне приготовления
Система регулирования частоты
Система самодиагностики
электронных блоков управления
Давление в цилиндрах в
понижения компрессии
Шумы и постороние звуки
при работе силового агрегата
Герметичность систем
Система зажигания. стартер
аккумуляторная батарея
генератор и реле-регулятор
Первичная низковольтная цепь
Распределитель высокого
Аккумуляторная батарея
Утечки масла и др. жидкостей
Герметичность системы
Электроде нзонасос. топливный
Датчик температуры двигателя
Регулятор холостого хода
положения дроссельной заслонки:
Проверка различных систем
Пробник аккумуляторный
Манометр. вакуумный насос
Сканер. Автомультиметр
Сканер. Автомультнметр.
Тормозной стенд. Визуальный осмотр
Измерение абсолютной величины компрессии в каждом цилиндре
Измерение относительной (в процентах к цилиндру с наибольшей
величины компрессии в цилиндрах
Замер утечки воздуха
подаваемого в цилиндр. Шипение воздуха прослушивается
в том коллекторе (впускном или выпускном). которому соответствуют
негерметичные клапаны.
Измерение величины компрессии с добавлением 20 г моторного масла в
проверяемый цилиндр. Увеличение величины компрессии указывает
на износ цилиндропоршневой группы
Поиск узла или детали
являющихся источником посторонних шумов
и стуков. При использовании электронного стетоскопа
возможно также определить спектральный состав шумов
Проверка турбокомпрессора работоспособность на отсутствие
механических повреждений
состояния ремней привода
Проверка на наличие ошибок по двигателю
посторонних шумов двигателя
двигателя на холостых оборотах (650-750обмин) по
Проверка герметичности
проверка патрубков системы
впуска на отсутствие повреждений
Измерение параметров элементов систем по различным
программам мотор-тестера. Определение работоспособности
элементов по форме осциллограмм
Измерение напряжения
Проверка и установка угла опережения зажигания. Проверка
правильности работы вакуум-корректора и
Измерение сопротивления: первичной и вторичной обмоток;
между обмотками и корпусом
Измерение напряжения на клеммах АКБ под нагрузкой
Измерения сопротивления статора и ротора стартера
Проверка сопротивления обмоток генератора
диодов и выпрямительного моста
Визуальный осмотр двигателя
Измерения давления масла в системе на работающем двигателе
Определение герметичности по уменьшению давления
насосом в системе (при постоянной температуре охлаждающей
Определение плотности охлаждающей жидкости
Определение температур срабатыва
ния термостата и включения электровентилятора
Измерение давления подачи топлива в различных точках системы
с целью определения работоспособности ее отдельных элементов
(в том числе рабочего давления бензонасоса и работоспособности
регулятора давления).
Измерение сопротивления обмоток электромагнитов форсунок
Измерение длительности управляющего импульса
открытия форсунок на различных режимах
Измерение сигнала датчика в зависимости от температуры двигателя
Измерение концентрации СО
СН и значение при различных режимах
работы двигателя (тест для автомобилей
оборудованных специальным
онтрольным отверстием перед каталитическим нейтрализатором)
Измерения напряжения на сигнальном проводе
датчика кислорода на различных оборотах двигателя
Определение работоспособности регулятора холостого хода
проверка правильности
установки датчика положения дроссельной заслонки
измерение количества всасываемого
воздуха в зависимости от оборотов двигателя
проверка работоспособности прожига
чувствительного элемента для удаления нагара (для некоторых марок автомобилей).
При наличии регулировочного винта необходима регулировка содержания СО в отработавших газах
Считывание кодов неисправностей. Проведение проверочного теста систем:
управления двигателем: кондиционирования: торможения (ABS):
противопробуксовочной системы и т. д.
Удаление кодов неисправностей из памяти систем управления
Свободный ход педали сцепления - проверка.
Пневмоусилитель (ПГУ)
главный цилиндр сцепления проверка на
отсутствие утечек рабочих жидкостей и мех. повреждений.
Работоспособность тормозной системы
проверка - на отсутствие утечки
тормозные (шланги) трубопровод
(на отсутствие повреждений)
тормозные накладки (колодки)
тормозные диски (барабаны).
Технологическая карта
Технологическая карта диагностики Higer KLQ-6891
Карта дефектации суппорта тормоза.cdw
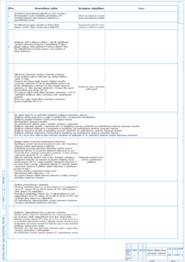
демонтировать колесо (соблюдать рекомендации для
соответствующего транспортного средства или
производителя моста).
На поверхности корпус суппорта не должно быть
сколов и других механических дефектов
Проверить люфт следующим образом - трижды передвинуть
суппорт тормозного механизма в направляющей в одну и
чтобы убедиться в наличии люфта в 25мм.
При необходимости очистить тормоз иили привести в
Подключить тормозную систему к внешнему источнику.
раз привести тормоз в действие при среднем давлении
Измерить расстояние между тыльной стороной накладки
и нажимным элементом (13). Из-за опрокидывания мостика оно
должно одновременно измеряться по всей площади нажимного
элемента и по двум нажимным элементам с помощью двух щупов.
(Использовать щупы длиной 220 мм).
Если разница люфта между двумя нажимными элементами >0
необходимо проверить люфт и возможный износ направляющей
люфт между обоими нажимными элементами
мм необходимо проверить следующие параметры и функции:
Проверить работу тормозного цилиндра в соответствии с инструкциями производителя.
Проверить концевое положение головки рычага внутри тормоза.
Демонтировать тормозные накладки.
При необходимости удалить грязь с накладок
суппорта и кронштейна.
Проверить тормозные накладки и тормозные диски на приработку нажимных элементов
при необходимости заменить тормозные накладки.
Проверить ответные поверхности в кронштейне на приработку
при необходимости заменить кронштейн тормоза.
Проверить тормозные накладки на приработку нажимных элементов
Если же и после этого люфт на обоих нажимных элементах не превышает 0
необходимо заменить суппорт тормозного механизма.
Проверка люфта на участке направляющего подшипника.
Передвинуть суппорт тормозного механизма до конца хода в направлении
внешней стороны транспортного средства.
Установить магнитное крепление индикатора часового типа на
кронштейн тормоза (2) на участке короткого подшипника (см. рис.).
В качестве точек измерения используются углубления в литье суппорта
тормозного механизма (1) - см. стрелки A.
Сбросить индикатор часового типа на нуль. Вставить подходящий
инструмент (например
как показано на рисунке
приблизительно 200 мм) между суппортом тормозного механизма (1)
как можно ближе к центру кронштейна тормоза (2) и отжать суппорт
тормозного механизма в пределах люфта подшипника (с нормальным
Считать показания индикатора часового типа.
Максимальный люфт подшипника = 1 мм.
При слишком большом люфте заменить подшипники в сборе
подходящий сервисный комплект.
Проверка уплотнительных элементов.
Уплотнение направляющих втулок (4) и (5) обеспечивается за счет гофрированного
чехла (9) и крышки (10) или (68). На частях (9)
(10) и (68) не должно
быть трещин или повреждений.
Уплотнение направляющих втулок (4) и (5) обеспечивается за счет
гофрированного чехла (9) и крышки (10) или (68). На частях (9)
не должно быть трещин или повреждений.
При необходимости отремонтировать суппорт тормозного механизма
с помощью подходящего сервисного комплекта
Проверить гофрированные чехлы на нажимных элементах.
Вывернуть нажимные элементы (13) с автоподводчиком (23) с помощью переходника (61) как
чтобы гофрированные чехлы были хорошо видны.
Вывернуть нажимные элементы (13) не менее чем на 35 мм и не более чем на 40 мм
или установить новую внешнюю накладку и вывернуть нажимные элементы до диска.
На гофрированных чехлах нажимных элементов (13) не должно быть трещин или других повреждений.
Проверить правильность посадки.
Проникновение грязи и влаги внутрь тормоза ведет к образованию коррозии и нарушает работу
механики затягивания и автоподвода.
При необходимости заменить нажимные элементы (13) с гофрированными чехлами
Ровная горизонтальная эстакада.
опоры. Пневматический гайковерт.
Визуальный осмотр. Щетка для очистки
загрязнений на поверхности суппорта
Индикатор часового типа
стойка с креплениями
Участок д план.cdw
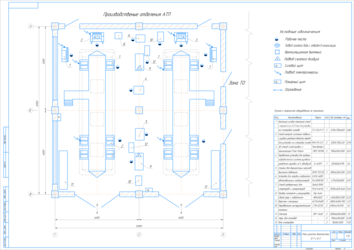
с нагрузкой на ось до 13 тонн
на смотровой канаве.
Стенд контроля состояния подвески
и рулевого управления (детектор люфтов)
для установки на смотровой канаве
технологией Free Motion
Передвижная установка для проверки
гидравлической системы рулевого
управления грузовых ам
Стойка для диагностики насосов
Установка для заправки хладагентом
автомобильных кондиционеров
Стенд проверочный для
стартеров и генераторов
Прибор контроля и регулировки
света фар с наводчиком
Передвижная инструментальная
План участка диагностики
Ручное и переносное оборудование не показанно.
Условные обозначения
Подвод холодной воды с отводом в канализацию
Вентиляционная вытяжка
Подвод сжатого воздуха
Подвод электроэнергии
Производственые отделения АТП
Пояснилка.docx
Так же актуальность указанной задачи подтверждается и тем что на техническое обслуживание автомобиля в ходе его эксплуатации затрачивается во много раз больше труда и средств чем на его производство поэтому совершенствование технологий выполнения работ по ТО и ТР с применением прогрессивных методов и оборудования для снижения трудоемкости и затрат на обслуживание автотранспортной техники является основной задачей данного курсового проекта.
Знание и количественная характеристика закономерностей изменение параметров технического состояния узлов и агрегатов и автомобиля в целом позволяет управлять работоспособностью и техническим состоянием автомобиля в процессе эксплуатации т.е. поддерживать и восстанавливать эффективность работы автотранспортной техники.
Состояние организации труда при техническом обслуживании и текущем ремонте автомобилей проявляется в длительности простоя автомобилей в ЕО ТО-1 ТО-2 и TP трудовых затратах на их выполнение простоях автомобилей на линии и в конечном итоге в себестоимости единицы продукции. Поэтому исходным моментом при внедрении НОТ является изучение использования рабочего времени при выполнении тех или иных операций по ТО и ТР.
Полученные результаты использования рабочего времени при выполнении ТО и ТР позволяют выявить резервы рабочего времени на рабочих местах и в производственных подразделениях автохозяйства а так жедают возможность совершенствования организации и технологии труда.
При сравнении уровня развития машиностроения иностранные автомобили обладают более высокими эксплуатационными показателями по сравнению с отечественным которые основаны на применении более современных технологий оборудования и материалов которые придают большую износостойкость деталям автомобиля делают его прочнее снижая частоту обращения к ремонтным услугам.
Однако не смотря на минимальное количество ремонтно-обслуживающих воздействий автомашина является сложной технической системой и зачастую требует не только узкоспециализированного профессионального подхода но и применение современного и специализированного оборудования для проведения работ по ТО и ТР. Таким образом на настоящее время основной проблемой отечественных автотранспортных предприятий при проведении работ по ТО и ТР зарубежной техники является отсутствие детальной технологии на проведение тех или иных ремонтных воздействий отсутствие специальных навыков и оборудования что может привести к высоким затратам на ТО и ТР.
Для выполнения поставленной цели необходимо провести:
- анализ парка машин;
-анализ работы эксплуатационной и технической службы хозяйства и методов организации работ по ТО и ТР;
- провести необходимые технологические расчеты;
- на основании теоретического анализа технической литературы разработать технологический процесс ТО и ремонта тормозной системы автобусов марки HIGER KLQ-6891;
- разработать мероприятия по охране труда и окружающей среды при проведении ремонтных работ.
Основные методы исследования: анализ подбор и расчет.
Структура проекта соответствует логике расчётов и включает в себя введение организационный раздел в котором представлена характеристика объекта проектирования расчетно-технологическую часть специальную часть с разработкой технологического процесс ТО и ремонта тормозной системы автобусов марки HIGER KLQ-6891 список источников и литературы приложений и графической частью из трех листов формата А1.
ОРГАНИЗАЦИОННЫЙ РАЗДЕЛ
1 Характеристика предприятия
- Автомобильный транспорт – автобусные перевозки в междугородном сообщении;
- Автомобильный транспорт – автобусные перевозки в пригородном сообщении;
- Автомобильный транспорт - автобусные перевозки в городском сообщении с посадкой и высадкой пассажиров только в установленных остановочных пунктах по маршрутам регулярных перевозок.
- Автомобильный транспорт – автобусные перевозки в городском сообщении по заказам.
На территории предприятия функционируют производственные посты технического обслуживания (ТО-1 и ТО-2) и диагностирования (Д-1 и Д-2) зона текущего ремонта (ТР) зона мелко-срочного ремонта моторный цех покрасочный цех кузнечный цех медницкий цех ремонтно-механические мастерские автосервис и автомойка.
2 Списочный состав парка автомобилей и данные по пробегу
Общий парк предприятия обширен (см. таблицу 1.1). Средний возраст всего подвижного состава не превосходит 6 лет так как по меркам данного предприятия выгодную и эффективную работу может гарантировать только относительно новая техника. Состав автопарка разномарочный и представляет собой машины отечественного и импортного производства.
Mercedes-BenzSprinter
КАМАЗ 43502 вахтовый автобус
Наличие такогообширного и разномарочного парка машин затрудняет быстрое и качественное проведение профилактических и ремонтных работ усложняет организацию материально-технического снабжения приводит к излишним затратам на технологическое оборудование при неудовлетворительном его использовании.
Работы по ТО и ТР на данном предприятии организуется путем разбивки данного парка машин на технически совместимые группы.
3 Условия эксплуатации автомобилей
Альметьевский муниципальный район занимает выгодное экономико-географическое положение на юго-востоке Республики Татарстан находится на пересечении важных магистралей соединяющих восток и запад север и юг республики и имеет достаточную ресурсную обеспеченность (нефть лесные водные земельные ресурсы).
На территории Альметьевского муниципального района пересекаются два из трех главных коридоров транспортно-коммуникационного каркаса республики: восточный меридиональный коридор сформированный автомобильной дорогой Набережные Челны – Заинск – Альметьевск и участком железной дороги Агрыз-Акбаш Куйбышевской железной дороги; коридор в направлении северо-запад – юго-восток образованный автомобильной дорогой федерального значения Казань-Оренбург. На пересечении указанных транспортных магистралей формируется Альметьевский транспортный узел.
Исходя из списочного состава парка места расположения транспортных потоков и выполняемым производственными задачам можно сделать вывод о том что основная доля автотранспорта эксплуатируется на дорогах с асфальтобетонным цементобетонным и приравненным к ним покрытиям как в черте города так и за ее пределами.
Небольшая часть автотранспортного парка данного предприятия таких как КАМАЗ 43502 вахтовый автобус УАЗ Pickup Зил 131 УАЗ-390995 и УАЗ-390945 так же эксплуатируются на дорогах с щебеночным или гравийным покрытием а также не профилированным дорогам и временным подъездным путям.
Таким образом эксплуатация данного автотранспортного парка осуществляется по I II и III категории эксплуатации.
Природно-климатические условия размещения данного АТП характеризуется умеренно-континентальным климатом с продолжительной холодной зимой и жарким коротким летом.
Альметьевский муниципальный район представляет собой возвышенную всхолмленную равнину сложенную осадочными породами и расчлененную густой сетью речных долин балок и оврагов.
4 Режим работы подвижного состава
Организация производства ремонтных работ определяет весь ритм работы предприятия и связывает ее в единый организм. От нее зависят рациональная загрузка в течение суток всех линейных пунктов их производственные мощности и оперативные резервы хозяйства в целом.
Перед выездом на линию водитель проверяет техническое состояние автомобиля получает путевой лист в диспетчерской проходит ежедневный медицинский осмотр и подъезжает на автомобиле к контрольному пункту расположенному у выездных ворот.
5 Основные показатели работы службы эксплуатации
Основные показатели работы службы эксплуатации представлены в таблице ниже.
Таблица 1.2 - Показатели службы эксплуатации
Наименование показателей
Объем перевозок тыс. т
Среднее время в наряде час
Среднесуточный пробег км
Общий пробег за год тыс. км
6 Основные показатели работы технической службы
В таблице 1.3 представлены основные показатели работы технической службы данного предприятия.
Таблица 1.3- Показатели технической службы
Коэффициент технической готовности
Общий простой в ТО и ТР дн
Простой в ТО и ТР на 1000 км пробега
7Методы организации технического обслуживания и текущего
ремонта автомобилей
Эти участки являются основной частью производства. Каждый из основных производственных участков выполняют все работы по ТО и ТР одного или нескольких агрегатов (узлов систем механизмов приборов) по всем автомобилям АТП. Моральная и материальная ответственности при данной форме организации производства становятся совершенно конкретными. Работы распределяются между производственными участками с учетом величины производственной программы зависящей от количества подвижного состава на АТП и интенсивности его работы.
Агрегатно-участковый метод организации ТО и ТР предусматривает тщательный учет всех элементов производственного процесса а также расхода запасных частей и материалов.
Текущий ремонт автомобиля состоит в устранении неисправностей его агрегатов и узлов при помощи разборочно-сборочных или ремонтно-восстановительных работ связанных с частичной или полной разборкой агрегатов и узлов автомобиля или в замене агрегатов требующих капитального ремонта.
Текущий ремонт агрегата или узла состоит в замене или ремонте износившихся и поврежденных деталей кроме базовых. Базовой является деталь состояние которой оказывает решающее влияние на работоспособность сопряженных с ней деталей и узлов или агрегата в целом.
При ремонтно-восстановительных работах восстанавливаются изношенные или разрушенные детали с помощью механической обработки пайки сварки холодной или горячей правки и других видов работ восстанавливается окраска автомобиля обивка кузова и т. д.
Ремонт автомобилей может производиться индивидуальным или агрегатным методом.
Прииндивидуальномметоде ремонта агрегаты снятые с автомобиля не обезличиваются их ремонтируют а затем устанавливают на тот же автомобиль. Этот метод характерен длительностью простоя автомобиля в ремонте.
Более прогрессивным являетсяагрегатныйметод ремонта автомобилей при котором неисправные агрегаты заменяют исправными (ранее отремонтированными или новыми) из оборотного фонда имеющегося в автохозяйстве. Неисправный агрегат после ремонта поступает в оборотный фонд.
Ремонт автомобилей может быть организован с использованием готовых запасных деталей. Посты текущего ремонта обычно оснащаются осмотровыми канавами и оборудуются подъемно-транспортными устройствами (кран-балка электротельфер передвижные краны и домкраты) приспособлениями и инструментом. Широко используются специализированные тележки (для снятия и установки переднего моста коробки передач заднего моста рессор колес со ступицей и тормозным барабаном) различные съемники электрогайковерты динамометрические ключи и т. д.
Техническое обслуживание автомобилей выполняют в соответствии с планом-графиком который составляют для каждой единицы подвижного состава исходя из среднесуточной величины пробега между видами технического обслуживания. График утверждается главным инженером АТП.
Перед возвращением автомобиля с линии техник по учету подвижного состава в гаражном листе заранее записывает номера автомобилей которые должны проходить техническое обслуживание с указанием вида технического обслуживания а также смазочных операций.
Автомобиль подвергают контролю общей диагностике и приемке при которых проверяют комплектность и внешнее состояние автомобиля фиксируют отказы и неисправности при необходимости составляют акт о повреждении.
В зависимости от объема работ техническое обслуживание выполняется тупиковым или поточным методом. При тупиковом методе все работы данного вида технического обслуживания выполняются на одном посту а при поточном — на нескольких последовательно расположенных постах.
Поточный метод позволяет специализировать посты обслуживания и рационально использовать квалификацию рабочих механизировать процессы улучшить условия труда повысить производительность труда и снизить себестоимость выполняемых работ. Недостатком поточного метода технического обслуживания является невозможность изменения объема работ на каком-либо посту поточной линии.
Такая организация производства в условиях новых методов планирования и экономического стимулирования повышает эффективность работы АТП за счет более ответственной и заинтересованной работы технического персонала. Основным недостатком этого метода является нарушение принципа выполнения работ применительно к автомобилю в целом.
8 Назначение и номенклатура работ подразделения
Зонатекущегоремонтапредназначенадлявыполнения комплекса работ по агрегатам и узлам автомобиля неисправность которых нельзя устранить путём регулировочных работ с целью восстановления их параметров и работоспособности.
Двигатель— смена поршневых колец поршня поршневого пальца втулки шатуна клапанов; смена ремней вентилятора и водяного насоса; подтяжка подшипников смена вкладышей и притирка клапанов.
Сцепление— смена накладок ведомых дисков подшипника выжимной муфты пружин и регулировка сцепления.
Коробка передач— частичная разборка ремонт с заменой отдельных деталей и сборка.
Карданная передача и задний мост— смена карданного шарнира шпонки сальника и гайки полуоси регулировка подшипников и зацепления шестерен главной передачи.
Колеса ступицы и тормоза— разборка ступиц смена и регулировка подшипников; разборка тормозов переклепка накладок тормозных колодок зачистка колодок смена тормозного барабана и тяг регулировка тормозного механизма и его привода.
Передний мост и рулевое управление— полная разборка переднего моста смена втулок шкворня подшипников и рычагов поворотной цапфы; разборка ремонт сборка и регулировка рулевого управления.
Кабина платформа и оперение— смена капота бортовых крюков дверных петель; крепление крыльев брызговиков подножек бортов кузова и стеклоподъемников смена подножек и их кронштейнов.
Рама рессоры и глушитель— смена рессор рессорных пальцев стремянок сережек рессорных втулок глушителя и кронштейна номерного знака.
РАСЧЁТНО-ТЕХНОЛОГИЧЕСКИЙ РАЗДЕЛ
1 Выбор исходных нормативов
Для упрощения выполнения расчетов весь списочный состав парка автомобилей предприятия приведем к одной основной модели. Основной моделью принимается марка автомобиля составляющая наибольшее количество в данном АТП в данном случае это -
Число приведенных автомобилей определяется по формуле:
где Асп- списочное количество автомобилей данной модели;
Кпр- коэффициент приведения;
где tтр- удельная трудоемкость ТР приведенной модели;
tтр- удельная трудоемкость ТР приводимой модели.
Для удобства ведения расчетов составляем таблицу где на первой строке указываем приведенную модель удельную трудоемкость текущего ремонта принимаем из “Положения о техническом обслуживании и ремонте подвижного состава автомобильного транспорта” с учетом модификации подвижного состава.
Таблица 2.4 - Приведение списочного состава парка автомобилей к одной основной модели
Периодичность ТО-1 и ТО-2 определяется по формулам:
L1= Lн1 К1 К3 км(2.3)
L2= Lн2 К1 К3 км(2.4)
где L1 и L2- расчетные периодичности ТО-1 и ТО-2 км принимаем согласно таблице 8 ОНТП-01-91;
Lн1 и Lн2- нормативные периодичности ТО-1 и ТО-2 км. принимаем согласно таблице 8 ОНТП-01-91.
К1- коэффициент корректирования нормативов в зависимости от категории условий эксплуатации принимаем согласно таблице12 ОНТП-01-91.
К3- коэффициент корректирования нормативов в зависимости от природно-климатических условий и агрессивности окружающей среды принимаем согласно таблице14 ОНТП-01-91.
L2= 200000810=16000 км
Пробег автомобиля до первого капитального ремонта Lк определяется по формуле:
Lк= LкнК1К2К3км.(2.5)
где Lкн- нормативный пробег нового автомобиля до первого капитального ремонта.
К1- коэффициент корректирования учитывающий категорию условий эксплуатации принимаем согласно таблице12 ОНТП-01-91.
К2- коэффициент корректирования учитывающий модификацию подвижного состава принимаем согласно таблице13 ОНТП-01-91.
К3-коэффициент корректирования учитывающий природно-климатические условия принимаем согласно таблице14 ОНТП-01-91.
Lк=2400000810=192000км.
Пробег автомобиля после капитального ремонта до очередного капитального ремонта:
Чтобы не вести два параллельных расчета по группе автомобилей с пробегом до капитального ремонта и после капитального ремонта определяется средневзвешенный пробег до капитального ремонта Lскр км:
где А-число автомобилей с пробегом до капитального ремонта;
А-число автомобилей с пробегом после капитального ремонта.
Округляя до 1000 км принимаем Lкср:
2 Определение годовой программы технического обслуживания автомобилей
Определяем коэффициент технической готовности:
где Lсс- среднесуточный пробег автомобиля;
dТОиТР- расчетная норма дней простоя в ТО и ТР на 1000 км пробега;
dКР- дни простоя автомобиля в капитальном ремонте.
dнТОиТР- исходная норма дней простоя в ТО и ТР на 1000 км пробега принимается согласно ОНТП-01-91.
Определяем годовой пробег парка автомобилей:
Lг= LссaтДргАпр (2.9)
Дрг – количество рабочих дней принимаем по данным табл. 4 ОНТП-01-91.
Апр- число приведенных автомобилей см. таблицу 2.4:
Lг= 250 087 357 480=37270800 км.
Определяем удельную трудоемкость ТР:
tТР= tнтр К1К2К3К4(ср)К5 (2.10)
где tTPн - нормативная трудоёмкость ТР чел-ч1000 км;
К1 К2; К3; К4; К5 – коэффициенты корректирования принимаем по справочным данным таблиц ОНТП-01-91.
Трудоемкость ТО-1 определяется по формуле:
t1=tн1K2K5 челч (2.11)
где tн1 – нормативная трудоемкость ТО-1 челч
Трудоемкость ТО-2 определяется по формуле:
t2= tн2K2K5 челч (2.12)
где tн2 – нормативная трудоемкость ТО-2 чел-ч .
t2= 1351090=1215 челч
Трудоемкость общего диагностирования (tд-1) определяется по формуле:
где t1 – скорректированная удельная трудоемкость ТО-1 чел*ч;
Сд-1 – доля трудоемкости диагностических работ в общей трудоемкости ТО-1.
Трудоемкость поэлементного диагностирования (tд-2) определяется по формуле:
где t2 – скорректированная трудоемкость ТО-2 чел*ч;
Сд-2 – доля трудоемкости диагностических работ в общей трудоемкости ТО-2 .
Количество ежедневных обслуживаний за год определяется по формуле:
Количество УМР за год:
- для грузовых автомобилей определяется по формуле:
NУМР = (075 080) NгЕО; (2.16)
-для легковых автомобилей и автобусов определяется по формуле:
NУМР = (110 115) NгЕО (2.17)
NУМР.л.а.тс = 11 (149083 065)=106594
NУМР.гр.тс = 08 (149083 035)=41743
NУМР = 106594+41743=148337
Количество ТО-2 за год (N2) определяется по формуле:
N2= ΣLгL2 обслуживаний; (2.18)
N2= 37270800 16000=2329
Количество ТО-1 за год (N1) определяется по формуле:
N1 = ( ΣLгL1) - N2 обслуживаний; (2.19)
N1=(372708004000)-2329=6989
Количество общего диагностирования за год (Nд-1) определяется по формуле:
Nд-1 = 11N1 + N2 воздействий; (2.20)
Nд-1 = 116989+2329=10250
Количество поэлементного диагностирования за год (Nд-2) определяется по формуле:
Nд-2 = 12N2 воздействий; (2.21)
Количество сезонных обслуживаний за год (NСО) определяется по формуле:
NСО = 2 Апр обслуживаний (2.22)
Годовая трудоемкость ежедневного обслуживания определяется по формуле:
ТЕО = tЕОNУМР челч (2.23)
ТЕО = 020148337=29667
Годовая трудоемкость ТО-1 определяется по формуле:
Т1 = 115t1N1 челч (2.24)
Т1 = 115 386989=30542
где 115 – коэффициент учитывающий трудоемкость сопутствующего ремонта при проведении ТО-1 челч.
Годовая трудоемкость ТО-2 определяется по формуле:
Т2 = 115 t2 N2 челч (2.25)
Т2 = 115 1215 2329=32542
где 115 – коэффициент учитывающий трудоемкость сопутствующего ремонта при проведении ТО-2.
Трудоемкость сопутствующего ремонта при ТО-1
Тсп.р(1) = Сто-1 t1 N1 челч (2.26)
Тсп.р(1) = 020386989=5312
где Сто-1 = 015 020 – регламентированная доля сопутствующего ремонта при проведении ТО-1.
Трудоемкость сопутствующего ремонта при ТО-2
Тсп.р(2) = СТО-2t2N2 челч (2.27)
где СТО-2 = 015 020 – регламентированная доля сопутствующего ремонта при проведении ТО-2.
Тсп.р(2) =02012.152329=5659челч
Годовой объем работ текущего ремонта автомобилей:
Годовые трудоемкости общего (Д-1) и поэлементного (Д-2) диагностирования определяются по формулам:
Тд-1 = tд-1 Nд-1 челч (2.29)
Тд-2 = tд-2 Nд-2 челч (2.30)
Тд-1 = 03810250=3895челч
Тд-2 = 0732795=2040челч
Годовая трудоемкость сезонного обслуживания определяется по формуле:
ТСО = tсо 2А челч (2.31)
ТСО = 272467=2522челч
Общая годовая трудоемкость всех видов ТО определяется по формуле:
ΣТТО = ТЕО + Т1 + Т2 + ТСО челч (2.32)
ΣТТО = 29667+30542+32542+2522=95273 челч
Общий объем работ по техническим воздействиям на подвижной состав определяется по формуле:
ТТО и ТР = ΣТТО + ТТР+ТД+Тсп.р(12) челч (2.33)
ТТО и ТР=95273+197162+5935+10971=309341челч.
1 Техническая характеристика автобуса Higer KLQ-6891
Городской автобус Higer KLQ-6891 относиться к автобусам среднего класса. Полная вместимость автобуса 58 человек среди которых 27 мест для сидения. Автобус сертифицирован и адаптирован для условий эксплуатации в России.
За счет использования короткой колесной базы он имеет высокую маневренность что позволяет ему уверенно двигаться в плотном городском потоке. В стандартной комплектации 6891GA оснащен пневмоподвеской что позволило значительно улучшить плавность хода автобуса и комфорт пассажиров.
Базовая комплектация: Автономное отопление Webasto отопители салона отопитель лобового стекла ABS противотуманные фары двойные фары головного освещения двухскоростные стеклоочистители омыватель лобового стекла пассажирские двери имеют пневмопривод магнитола вспомогательный тормоз металлическая защита задней части кузова (двигателя) антивандальные сиденья поручни пассажирские окна с левой и с правой стороны имеют сдвижные форточки. Электронные часы автоматическая система смазки зеркала заднего вида с электрообогревом.
Данный автобус оснащается CumminsISBe 185-30ISDe 185-30 (Euro 3)6-цилиндровый 4- тактный дизельный двигатель мощностью (185 л.с.) 21002500 об.мин. крутящий момент 700 Нм при 1200-17001100-1700 об.мин.Рабочий объём – 5883 см3.
КПП - 5-ти ступенчатая синхронизированная
Сцепление - однодисковое сухое с гидравлическим приводом.
Основные параметры автобуса:
Габаритные размеры: 8965x2440x3100мм
Колесная база: 4250мм
Передняя колеязадняя колея: 20201800мм
Снаряженная масса: 7600кг
Полная масса автобуса: 12000кг
Нагрузка на переднююзаднюю ось: 40008000кг
Объем топливного бака: 220л
Средний расход топлива: 20л100км.
Рулевой механизм типа винтовая шариковая передача со встроенным сервоусилителем.
Передняя и задняя подвески пневматические с гидравлическими телескопическими амортизаторами и стабилизатором поперечной устойчивости.
Каркас кузова изготовлен из холоднокатаных стальных труб. Обшивка крыши и боковины из оцинкованного двустороннего листа. Передняя и задняя панели изготовлены из стеклопластика. Днище и колесные арки обработаны антикоррозийным материалом.
Пол – влагостойкая фанера с изоляционным слоем и резиновым - противоскользящим покрытием.
2 Технологический процесс технического обслуживания и диагностики автобусов Higer KLQ-6891
Техническим обслуживанием называется выполнение комплекса профилактических работ по уходу за автомобилем направленных на предупреждение появления и устранение выявленных неисправностей а также продление срока службы автомобиля до ремонта повышение надежности и безопасности эксплуатации.
Ежедневное обслуживание автобуса всегда проводит водитель. Основным назначением
ЕО является: контроль технического состояния направленный на обеспечение безопасности движения; поддержание надлежащего внешнего вида заправка топливом маслом и водой.Ежедневное обслуживание включает следующие операции:
— перед выездом на линию — проверку чистоты автобуса наличия охлаждающей жидкости отсутствия подтекания воды масла топлива а также контрольный осмотр тормозных механизмов рулевого управления колес шин сцепных устройств автопоездов приборов освещения и сигнализации и проверку исправности механизмов открывания и закрывания дверей;
— на линии — систематическое наблюдение за работой агрегатов и механизмов;
— по возвращении с линии — уборку мойку осмотр и заправку автобуса.
Основным назначением ТО-1 и ТО-2 является снижение интенсивности изнашивания деталей выявление и предупреждение отказов и неисправностей путем своевременного выполнения контрольно-диагностических смазочных крепежных регулировочных и других работ.
Сезонное обслуживание проводится 2 раза в год при переходе с осенне-зимней эксплуатации на летнюю и наоборот и в качестве отдельного вида обслуживания планируется для подвижного состава работающего в зоне холодного климата. Для остальных условий сезонное обслуживание совмещают с ТО-2 или ТО-1.
Диагностика автомобилей представляет собой технологический процесс при котором определяют техническое состояние автомобиля (агрегата механизма) без его разборки и дают заключение о необходимом ремонте или техническом обслуживании.
Диагностирование осуществляется по внешним признакам (люфтам вибрациям нагревам потере мощности и т. д.). Таким образом диагностикой выявляют скрытые неисправности без разборки агрегатов предупреждают внезапные отказы.
Периодичность обслуживания Higer KLQ-6891составляет каждые 20000км или каждые 3- 6 месяцев в зависимости от того что наступит ранее. В более тяжелых условиях эксплуатация автомобиля рекомендуется сократить межсервисный интервал до 15 000км или каждые 3 месяца.
Список работ по ТО автобусов Higer KLQ-6891 представим в виде таблицы 3.5.
Таблица 3.5 – Ведомость работ по техническому обслуживанию автобусов Higer KLQ-6891
Предмет контроля и регулировки
Масло моторное в двигателе (замена)
Фильтр масляный (замена)*
Фильтр системы охлаждения
Уровень и состояние охлаждающей жидкости (проверка)
Герметичность трубопроводов системы отопления салона трубопроводов системы охлаждения радиатора системы охлаждения - проверка
Охлаждающая жидкость - замена
Протяжка кронштейнов и хомутов топливного бака
Крепление воздушного компрессора-протяжка
Топливный фильтр тонкой очистки топлива — замена*
Топливный фильтр грубой очистки топлива-замена*
Фильтр воздушный (замена комплект)*
Крепление крыльчатки вентилятора (проверка-затяжка)
Состояние балки передних опор силового агрегата ДВС (подушки кронштейны) - проверка протяжка
Проверка турбокомпрессора — работоспособность на отсутствие посторонних шумов механических повреждений утечек масла.
Проверка натяжения состояния ремней привода (при необходимости замена 03 нч)
Тепловые зазоры в клапанном механизме газораспределения предварительно проверив затяжку болтов головок цилиндров и гаек стоек коромысел. (обращаться к производителю двигателей ). каждые 16000 км (работы выполняются в спец.центре).
Проверка на наличие ошибок по двигателю на отсутствие посторонних шумов двигателя частоты вращения двигателя на холостых оборотах (650-750обмин) по панели приборов
Проверка системы выпуска отработавших газов (выход отработавших газов в соединениях не допускается) болты крепления коллекторов и фланцев системы выпуска – протяжка.
Замена воздушного фильтра-сепаратора SCR-системы (кат.номерFleetguard AS2474
Радиатор охлаждения воздуха(интеркулер) -проверка герметичностипроверкапатрубков системы впуска на отсутствие повреждений протяжка хомутов.
Топливный насос шланги (трубки) топливной системыфорсунки -проверка на утечку топлива на отсутствие механических повреждений.
необходимости) проверка патрубков линии подогрева разъемов датчиков NОx датчиков температуры EGR
Масло в коробке передач (проверка 015нч замена 050нч)***
Механизм переключения натяжение тросов привода - проверка
Разъемы датчиков спидометра нейтрали заднего хода - проверка вт.ч. на наличие заводских пломб; очистка контактов при необходимости
Свободный ход педали сцепления - проверка закрепить
Жидкость в приводе сцепления — проверка 005 нч замена — 05 нч (при отсутствии необходимости замены жидкость меняется через каждые 2 года)****
Пневмоусилитель (ПГУ) главный цилиндр сцепления – проверка на отсутствие утечек рабочих жидкостей и мех. повреждений.
Подвижные соединения проверка герметичности смазка
Карданная передача 010
Проверка люфтов в крестовинах и шлицевом соединении
Шлицевые соединения подшипники (крестовина) – смазка
Масло в заднем мосту (проверка 015нч замена 050нч)***
Сапун -проверкаочистка
Состояние реактивных штанг рычагов резинометаллических изделий
Ходовая часть подвеска колеса 234
Колесные гайки — протяжка запасное колесо проверка.
Шины осмотр степени износа ротация при необходимости — 04 нч з 1шт.
Проверка давления в шинах в случае необходимости довести давление до требуемого значения (согласно табличке в салоне)
Пыльники чехлы защитные брызговики — проверка
Реактивные тяги рычаги резинометаллические изделия (сайлентблоки реактивных тяг втулки) передний мост — проверка протяжка креплений
Шкворни поворотных кулаков-проверка при необходимости смазка — 02 нч
Пневмоопоры монтажные соединения (при наличии) - проверка
Подшипники ступиц колес (проверка на отсутствие посторонних шумов люфтов 050нч замена смазки всех колес — 200нч)
Амортизаторы рессоры стремянки рессор — проверка протяжка
Запуск автоматической системы смазки в принудительном ручном
режиме на панели управления (не менее 35 сек.) контроль
работоспособности масленок
Объем контейнера автоматической смазки (заполнить смазкой класса
NLGI 000 до верхнего уровня)
Слив конденсата из ресиверов
Кран уровня пола - проверка 01 нч регулировка при необходимости — 02нч
Производительность воздушного компрессора наличие конденсата (при необходимости — конденсат удалить) герметичность пневмосистемы подвески -
Фильтр-патрон осушителя — замена (интервал через 40000 км. или 1год.
Крепление ресиверов - проверкапротяжка
Шланги трубопроводы - проверка на отсутствие повреждений
Рулевое управление 055
Жидкость в рулевом механизме ZF уровень - проверка 005нч замена 050нч
Герметичность системы шланги трубопроводы (на отсутствие повреждений утечки жидкости) - проверка
Свободный ход рулевого колеса
Крепление гидроусилителя насоса силового цилиндра
Шарниры рулевого управления рулевые тяги чехлы шарнирных соединений
Тормозная система 080
Работоспособность тормозной системы проверка - на отсутствие утечки тормозной жидкости тормозного клапана тормозные (шланги) трубопровод (на отсутствие повреждений) тормозные накладки (колодки) тормозные диски (барабаны).
Стояночный тормоз проверка — 005 нч при необходимости регулировка 025 нч
Тормозные механизмы (тормозные камеры натяжной регулятор рычага)подвижные соединения — проверка 015 нч при необходимости смазка — 02 нч
Свободный ход педали тормоза - проверка регулировка
Тормозные колодки накладки. Замена при необходимости
Электрооборудование 079
Контрольные лампы указатели панели приборов - проверка
Направление света фар — проверка при необходимости регулировка 08нч — 2шт.
Управление световыми приборами-проверка
Наружное освещение и освещение номерного знака - проверка
Внутреннее освещение и вентиляция
вуковой сигнал - проверка
Уровень и плотность электролита в АКБ очистка
Крепление АКБ. генератора стартера силовых кабелей и клемм блок реле и предохранителей - проверка
Автономный отопитель
Кузов вспомогательные работы и дополнительное оборудование 105
Внешний осмотр лакокрасочного покрытия кузова на наличие повреждений остекление кузова (осмотр на целостность герметичность)
Крепление и регулировка зеркал заднего вида шторок
Крепление и регулировка дверей и люков пневмоклапаны открывания дверей - проверка
Смазка проверка дверных уплотненийзамков и петель
Крепление приборов наружного освещения крепление деталей шасси - проверка протяжка
Осмотр приборов отопления салона
Проверка показаний одометра и тахографа. При каждом обслуживании с фиксацией в сопроводительных документах (Акт выполненных работсервисная книжка и др.)
Регулировка углов установки колес(сход-развал) при необходимости.
3 Назначение и условия работы тормозной системы
Тормозная система автобусов Higer KLQ-6891 состоит из рабочей стояночной и вспомогательных систем.
Рабочая: Пневматический двух контурный привод с разделением на контуры по осям АБС WABCO осушитель воздуха WABCO тормозные механизмы колес: передних колес – дискового типа задних колес – барабанного типа.
Стояночная: привод (автоматические рычаги Haldex) от пружинных энергоаккумуляторов к тормозным механизмам задних колес.
Вспомогательная: Трансмиссионный электродинамический ретардер.
Пневматический тормозной привод - вид конструкции тормозной системы которая использует в качестве энергоносителя сжатый воздух.
Магистраль двухконтурной тормозной система используемая в данном автобусе разделены на две ветки. Одна ветка передает сжатый воздух на передние колеса вторая - на задние. Поток энергоносителя контролируют два тормозных крана - по одному на каждый контур магистралей. Двухконтурная конструкция надежнее чем одноконтурная. Если вышла из строя ветка задней оси передние тормозные узлы продолжают функционировать и наоборот.
Воздух закачивается компрессором во «влажный» ресивер который защищен от избыточного давления предохранительным клапаном. Затем сжатый воздух поступает из «влажного» ресивера в первичный «сухой» ресивер и далее во вторичный «сухой» ресивер. С этого момента двухконтурная тормозная система готова к работе. По воздушным магистралям сжатый воздух из первичного «сухого» ресивера подведен к ножному клапаны с тормозной педалью. Аналогичная ситуация и со вторичным «сухим» ресивером от которого воздух также поступает к ножному клапану. При этом ножной клапан состоит фактических из двух разделов т.е. представляет собой два клапан в одном. Один из отделов обслуживает первичный тормозной контур а второй отдел обслуживает вторичный тормозной контур. Когда выполняется торможение воздух из первичного ресивера через ножной клапан подается на задние тормозные камеры. В то же время воздух из вторичного ресивера подается на передние тормозные камеры. При утечке воздуха в первичном контуре вторичный будет оставаться работоспособным и наоборот. Первичный и вторичный контуры снабжены сигнализаторами о низком давлении которые расположены в кабине. Кроме того автобус оборудуется аварийным или стояночным тормозом. Принцип его работы основан на использовании мощной пружины для приложения тормозного усилия. Дело в том что существует вероятность утечки воздуха из тормозной системы. В аварийном тормозе давление воздуха не дает пружине разжаться и произвести торможение. При утечке воздуха когда давление в системе будет 20-30 фунтов на дюйм пружина разожмется и тормоза автоматически сработают транспортное средство остановится. Аварийный тормоз сильно зависит от регулировки пружины.
Рисунок 3.1 - Общий вид пневматической тормозной системы
- компрессор 2 - говернер 3 - осушитель воздуха 4 - "влажный" ресивер 5 - первичный ресивер 6 - вторичный ресивер 7 - педаль тормоза с ножным клапаном 8 - ограничительный клапан передней оси 9 - ускорительный клапан 10 - задняя тормозная камера 11 - передняя тормозная камера
4 Технологический процесс ремонта тормозной системы
Согласно заданию на курсовой проект в данном разделе рассмотрим технологический процесс ремонта пневматического дисковогосуппорта системы торможения передних колес.
На рисунке 3.2 представлена схема разборка дискового тормоза автобусов Higer KLQ-6891 устанавливаемого на передней оси.
Рисунок 3.2 – Схема разборки
Суппорт тормозного механизма 2 Кронштейн тормоза 4 Направляющая втулка 5 Направляющая втулка 6 Подшипник скольжения 7 Латунная втулка 9 Гофрированный чехол 10 Крышка 11 Скоба-держатель тормозных накладок 12 Тормозная накладка 12.1 Внутренняя накладка 12.2 Внешняя накладка 13 Нажимной элемент с гофрированным чехлом 18 Тормозной цилиндр 22 Внутреннее уплотнение 26 Пружинный шплинт 37 Колпачок 39 Винт с цилиндрической головкой 40 Винт с цилиндрической головкой 44 Болт 45 Шайба 58 Кольцо 61 Переходник 68 Крышка 161 Втулка подшипника скольжения.
При проведении работ по ТО необходимо проверять функцию автоподвода и подвижность суппорта по всему пути перемещения обе стороны в осевом направлении. Также необходимо проверять гофрированный чехол нажимного элемента (13) колпачок (37) уплотнительные элементы (9 58) и крепление суппорта на участке подшипников скольжения (6) на предмет люфта и повреждений выполнять проверку тормозных дисков и колодок.
Перед началом работ по ремонту и сервисному обслуживанию принять меры исключающие возможность отката транспортного средства.
Рабочие и стояночные тормоза а также используемые во время остановок тормоза автобусов должны находиться в отпущенном состоянии.
Технология производства работ представлена в таблице ниже.
Таблица 3.5 Технология ТО и ТР пневматического дискового суппорта системы торможения передних колес автобуса Higer KLQ-6891.
Проверка автоподвода
Проверить давление в тормозной системе (требуемое значение > 65 бар); подключить ее к внешнему источнику для предотвращения падения давления.
Установить транспортное средство или мост на опоры и демонтировать колесо (соблюдать рекомендации для соответствующего транспортного средства или производителя моста).
Проверить люфт следующим образом - трижды передвинуть суппорт тормозного механизма в направляющей в одну и другую сторону чтобы убедиться в наличии люфта в 25мм. При необходимости очистить тормоз иили привести в норму подшипники.
Привести в действие тормоз при среднем давлении (прибл. 2-3 бар). Если их приведение в действие невозможно передвинуть суппорт тормозного механизма по направляющему пальцу в направлении центра транспортного средства.
С помощью подходящего инструмента отжать внутреннюю тормозную накладку (12) от нажимного элемента (13).
Убедиться в отсутствии грязи между тыльной стороной внешней накладки и ответной поверхностью суппорта которая может исказить результат измерений. При необходимости очистить.
Потянув за язычок снять колпачок (37) (следите чтобы не потерялся переходник (61).
Снятие колпачка (37) с помощью какого-либо инструмента может привести к повреждению уплотнения на автоподводчике.
После отворачивания путем последующего затягивания тормоза с помощью переходника (61) отрегулировать люфт 13 мм. Отрегулировать люфт на той стороне тормоза где вращается переходник.
раз привести тормоз в действие при среднем давлении (прибл. 2-3 бар).
Измерить расстояние между тыльной стороной накладки и нажимным элементом (13).
Из-за опрокидывания мостика оно должно одновременно измеряться по всей площади нажимного элемента и по двум нажимным элементам с помощью двух щупов. (Использовать щупы длиной 220 мм).
Если разница люфта между двумя нажимными элементами >025 мм необходимо проверить люфт и возможный износ направляющей суппорта.
Кроме того люфт между обоими нажимными элементами должен составлять 06 – 12 мм
При слишком большом люфте тормозное действие может отсутствовать. При недостаточном люфте тормоз может перегреваться что приведет к повреждениям.
При люфте свыше 12 мм необходимо проверить функцию автоподвода следующим образом:
Провернуть автоподводчик с помощью переходника (61) на три щелчка против часовой стрелки (увеличение люфта).
Надеть на переходник кольцевой или торцовый ключ. 5-10 раз привести тормоз в действие (прибл. 2 бар). При работающем автоподводчике кольцевой или торцовый ключ должен пошагово проворачиваться в направлении указанном стрелкой.
Если кольцевой или торцовый ключ либо не поворачивается совсем либо поворачивается только при первом приведении тормоза в действие или же при каждом приведении тормоза в действие перемещается вперед и обратно это свидетельствует о неисправности автоподводчика и о необходимости его замены.
Смазать уплотнительную поверхность колпачка консистентной смазкой.
Следите за монтажным положением (см. стрелку) колпачка (37). В противном случае при установленном на фланец тормозном цилиндре доступ к колпачку (37) будет невозможным.
При люфте менее 06 мм необходимо проверить следующие параметры и функции:
Проверить работу тормозного цилиндра в соответствии с инструкциями производителя.
Проверить концевое положение головки рычага внутри тормоза.
Демонтировать тормозные накладки. При необходимости удалить грязь с накладок суппорта и кронштейна.
Проверить тормозные накладки и тормозные диски на приработку нажимных элементов при необходимости заменить тормозные накладки.
Проверить ответные поверхности в кронштейне на приработку при необходимости заменить кронштейн тормоза.
Проверить тормозные накладки на приработку нажимных элементов при необходимости заменить тормозные накладки.
Если же и после этого люфт на обоих нажимных элементах не превышает 06 мм необходимо заменить суппорт тормозного механизма.
Установить колеса (соблюдать рекомендации соответствующего производителя транспортного средства).
Проверка подвижности суппорта тормозного механизма
Суппорт должен перемещаться от руки в обе стороны в осевом направлении (см. стрелки) в пределах люфта в 25мм. см. п.3 данной таблицы.
Если указанный ход> 25мм отрегулировать невозможно или если суппорт не перемещается необходимо отрегулировать направляющую суппорта.
Проверка люфта на участке направляющего подшипника
Для выполнения измерения необходимо установить пару новых тормозных накладок (см. Гл. 6) поскольку измерение должно проводиться на суппорте тормозного механизма в состоянии максимально приближенном к состоянию новых тормозных накладок. Если проверка выполняется не в ходе замены накладок необходимо отметить монтажное положение уже использующихся тормозных накладок чтобы их затем можно было установить в прежнее положение.
Передвинуть суппорт тормозного механизма до конца хода в направлении внешней стороны транспортного средства
Установить магнитное крепление индикатора часового типа на кронштейн тормоза (2) на участке короткого подшипника (см. Рис.).
В качестве точек измерения используются углубления в литье суппорта тормозного механизма (1) - см. стрелки A.
Сбросить индикатор часового типа на нуль.
Вставить подходящий инструмент (например как показано на рисунке отвертку длиной приблизительно 200 мм) между суппортом тормозного механизма (1) как можно ближе к центру кронштейна тормоза (2) и отжать суппорт тормозного механизма в пределах люфта подшипника (с нормальным усилием от руки).
Считать показания индикатора часового типа. Максимальный люфт подшипника = 1 мм.
При слишком большом люфте заменить подшипники в сборе используя подходящий сервисный комплект.
Проверка уплотнительных элементов
Демонтировать тормозные накладки
Уплотнение направляющих втулок (4) и (5) обеспечивается за счет гофрированного чехла (9) и крышки (10) или (68). На частях (9) (10) и (68) не должно быть трещин или повреждений.
При необходимости отремонтировать суппорт тормозного механизма с помощью подходящего сервисного комплекта
Проверить гофрированные чехлы на нажимных элементах.
Вывернуть нажимные элементы (13) с автоподводчиком (23) с помощью переходника (61) как раз настолько чтобы гофрированные чехлы были хорошо видны.
Вывернуть нажимные элементы (13) не менее чем на 35 мм и не более чем на 40 мм или установить новую внешнюю накладку и вывернуть нажимные элементы до диска.
На гофрированных чехлах нажимных элементов (13) не должно быть трещин или других повреждений.
Проверить правильность посадки.
Проникновение грязи и влаги внутрь тормоза ведет к образованию коррозии и нарушает работу механики затягивания и автоподвода.
При необходимости заменить нажимные элементы (13) с гофрированными чехлами
Демонтаж и установка суппорта тормозного механизма
Демонтировать мембранный или комбинированный цилиндр (см. Гл. 11.1 или 11.3). При наличии кабеля потенциометра снять его.
С помощью подходящего инструмента пробить крышку (10) посредине.
При этом крышка (10) может сдвинуться внутрь прибл. на 10 мм.
С помощью подходящего инструмента выжать крышку (10).
Проверить участок подшипника отверстия суппорта на наличие коррозии и при необходимости отремонтировать с использованием подходящего комплекта направляющих и уплотнений. При наличии повреждений или сильной коррозии суппорт тормозного механизма необходимо заменить.
Демонтировать крышку (68) с помощью подходящего инструмента как показано на рисунке рядом.
Указание: Не выбивать крышку (68) в направлении суппорта тормозного механизма поскольку это может привести к его повреждению или к повреждению его частей.
Демонтаж суппорта тормозного механизма с кронштейна тормоза.
Вывернуть винты с цилиндрической головкой (39) и (40). Держать суппорт тормозного механизма (1) только снаружи не вставлять пальцы между суппортом тормозного механизма (1) и кронштейном тормоза 2 (2)! Ни в коем случае не зацеплять грузоподъемное устройство к скобе-держателю тормозных накладок (11) так как это может привести к ее повреждению.
Снять суппорт тормозного механизма (1) с кронштейна тормоза.
Ремонт суппорта тормозного механизма
Ремонт подшипниковый узел суппорта осуществляется путем замены всех деталей поз. 4 5 9 58 а также крышки поз. 10 и 68 новыми.
Демонтаж гофрированного чехла (9)
Демонтировать суппорт тормозного механизма Снять кольцо (58) извлечь направляющие втулки (4 и 5).
С помощью отвертки выжать гофрированный чехол (9). Проверить уплотнительную поверхность гофрированного чехла (9) на наличие коррозии и повреждений (см. Рис. стрелка A).
Для демонтажа и монтажа используйте комбинацию инструментов для запрессовки и зачеканки втулки (7) из комбинации инструментов (D). Вместе с этим комбинацию инструментов (D) можно использовать и для зачеканки втулки (7).
Очистить цековку (стрелка A) и втулку (7)
Выпрессовка втулки (7).
Установить комбинацию инструментов (D) для выпрессовки втулки (7) в указанное положение и сдвинуть втулку (7) по шпинделю (T13).
Указание: Убедиться что латунная гайка (T14) вошла во втулку (7).
Стакан (T12) должен по всей площади прилегать к цековке (стрелка A).
Запрессовка втулки (7).
Завернуть латунную гайку (T14) на шпинделе (T13) до упора и надеть фланец (T08). Надеть новую втулку (7) на нажимную часть (T16) и через канал для накладок вставить в отверстие в суппорте (см. рис.).
Установить комбинацию инструментов (D) для запрессовки и зачеканки втулки (7) в указанное положение (см. Рис.).
От руки завернуть шпиндель (T13) до упора в нажимную часть (T16). Проверить свободу хода нажимной части (T16). Фланец (T8) должен по всей площади прилегать к цековке (стрелка A) (см. рис.).
Запрессовать втулку (7) с помощью латунной гайки (T14) до упора (см. рис.).
Зачеканить втулку (7) в суппорте тормозного механизма исключив возможность ее продольного перемещения. Для этого завернуть до упора болт с шестигранной головкой (стрелка B) нажимной части (T16) (см. Рис.).
Отвернуть болт с шестигранной головкой (стрелка B) нажимной части (T16) приблизительно на 20 мм отпустить латунную гайку (T14) и повернуть нажимную часть (T16) приблизительно на 60°. Повторить процесс зачеканки.
Теперь втулка (7) зачеканена в канавке суппорта тормозного механизма (стрелка A).
Вывернуть шпиндель (T13) из нажимной части (T16) и снять комбинацию инструментов.
Проверить седло втулки (7) на наличие заусенцев и при необходимости удалить их. Смазать втулку (7) белой консистентной смазкой (входит в ремонтный комплект).
Замена подшипника скольжения (6) на короткой стороне подшипникового узла.
Для замены подшипников скольжения (6) используйте комбинацию инструментов (S) (см. Рис.).
Выпрессовка подшипника скольжения (6).
Снять направляющую втулку (4).
Очистить подшипник на участке канала для накладок.
Установить комбинацию инструментов (S) как показано на рисунке (см. Рис.).
Слегка зажать гайку (T14) от руки.
Удерживая кольцевым гаечным ключом SW24 гайку (T14) (например ключом с трещоткой SW24) выпрессовать подшипник скольжения (6) вращая T20 (см. Рис.).
Запрессовка подшипника скольжения (6)
Как показано на рисунке с помощью медного молотка и компонента инструмента (T14) наживить втулку подшипника скольжения (6) в отверстии суппорта (см. Рис.).
Вставить комбинацию инструментов (S) в подшипник скольжения (6) (см. Рис.).
Немного провернуть шпиндель (T20) от руки.
Удерживая кольцевым гаечным ключом SW24 гайку (T14) и вращая динамометрическим ключом винт (T20) запрессовать подшипник скольжения (6) до упора. Соблюдать при этом максимальный момент затяжки 25 Нм (см. Рис.).
Снять монтажный инструмент.
Если во время запрессовки момент затяжки составляет 4Нм или > 25 Нм суппорт необходимо заменить.
Не вращать гайку (T14) так как при этом подшипник скольжения (6) может провернуться.
Установка гофрированного чехла (9).
Для установки гофрированного чехла (9) используйте комбинацию инструментов (C) с компонентом инструмента (T08).
Вставить новый гофрированный чехол (9) в приемную втулку (T07) комбинации инструментов (C). Убедиться что складки чехла находятся внутри инструмента (см. Рис. стрелка B).
Вставить приемную втулку (T07) комбинации инструментов (C) с гофрированным чехлом (9) в отверстие и от руки затянуть винт (T10) (см. Рис.).
Затем запрессовать гофрированный чехол (9) с максимальным моментом затяжки 8 Нм (см. Рис.). После этого снять комбинацию инструментов.
Проверить правильность посадки гофрированного чехла (9). Выполнить испытание на вытягивание.
Смазать латунную втулку (7) и подшипник скольжения (6) белой консистентной смазкой (входит в ремонтный комплект).
Установить направляющие втулки (4 5).
Вставить гофрированный чехол (9) в паз (стрелка A).
Убедиться в том что кольцо на гофрированном чехле правильно сидит по всей окружности в пазе.
Установить суппорт тормозного механизма на кронштейн тормоза
5Расчет нормы времени на технологический процесс ремонта
Расчет нормы времени на ремонт суппорта тормозного механизма выполняем по нормативным нормам технологического процесса ТО и ТР принятого на основании справочника нормативов на техническое обслуживание и ремонт автобусов HIGER.
Затраты в нормо-часах определяют трудоемкость провидения ремонтных работ в условиях сертифицированной сервисной станции с использованиемнеобходимого оборудования и квалифицированных специалистов. Нормы времени установлены заводом-изготовителем путем усредненных замеров затратвремени для опытного сотрудника.
Таблица 3.6 –Пооперационные затраты времени на ремонт суппорта тормозного механизма Higer KLQ-6891
Наименование и содержание работ
Среднее значение нормы временимин
Проверить давление в тормозной системе
Установить транспортное средство или мост на опоры
Демонтировать колеса с проверяемой оси
Устранить загрязнения. На узлах и элементах тормозной системы должно быть остатков посторонних материалов грязи и влаги.
Проверить внешний вид люфты работу автоподвода проверить подвижность суппорта тормозного механизма проверить состояние тормозных накладок и дисков проверить состояние уплотнительных элементов.
Демонтаж суппорта тормозного механизма
Замена (демонтаж монтаж) гофрированного чехла (9)
Замена подшипника скольжения (6) на короткой стороне подшипникового узла
установка суппорта тормозного механизма
Таким образом общее время проведения ремонтных работ суппорта тормозного механизма Higer KLQ-6891 составляет 129мин. или 215 часа.
6 Подбор технологического оборудования и расчет площади участка
Подбор технологического оборудования технологической и организационной оснастки для объекта проектирования осуществляется с учетом рекомендаций Типовых проектов рабочих мест на АТП Руководства по диагностике технического состояния подвижного составаи Табеля гаражно-технологического оборудования.
К технологическому оборудованию относят стационарные передвижные и переносные стенды станки всевозможные приборы и приспособления занимающие самостоятельную площадь на планировке необходимые для выполнения работ по ТО ТР и диагностированию подвижного состава. К организационной оснастке относят производственный инвентарь (верстаки стеллажи шкафы столы) занимающий самостоятельную площадь на планировке.
К технологической оснастке относят всевозможный инструмент приспособления приборы необходимые для выполнения работ по ТО ТР идиагностированию подвижного состава не занимающие самостоятельной площади на планировке. При выборе технологического оборудования и организационной оснастки следует учитывать что количество многих видов стендов установок иприспособлений не зависит от числа работающих в цехе тогда как верстаки или рабочие столы принимаются исходя из числа рабочих занятых в наиболее нагруженной смене.
В данном курсовом проекте необходимо подобрать оборудование для участка диагностики Д1 и Д2 автобусов Higer KLQ-6891 и произвести расчет его площади.
Выбор необходимого оборудования принимаем из специфики работ данного отделения АТП.
Таблица 3.7 – Ведомость оборудования
Габаритные размеры мм
Напольный силовой тормозной стенд с нагрузкой на ось до 13 тонн для установки на смотровой канаве.
Стенд контроля состояния подвески и рулевого управления (детектор люфтов) для установки на смотровой канаве
D стенд сход-развал с технологией Free Motion
Техно Вектор 6 FREE MOTION
Стенд для диагностики пневматического привода тормозной системы грузового автотранспорта и автобусов
Переносное оборудование
Передвижная установка для проверки гидравлической системы рулевого управления грузовых ам автобусов
Стенд для определения неисправности и регулировки форсунок дизельных двигателей.
Дизель-тестер для регулировки ТНВД
настольный переносной
Стойка для диагностики насосов высокого давления
Установка для заправки хладагентом автомобильных кондиционеров
CLIMA 6000 Plus BRAIN BEE
Стенд проверочный для стартеров и генераторов
TopAuto EB380 Profi Inverter
Комплект для проверки и очистки свечей зажигания из двух приборов Э-203-О и Э-203-П
Автомобильный сканер с измерительным модулем J2534 DoIP D-PDU для углубленной диагностике электронных систем управления
Манометр для измерения давления воздуха
Прибор контроля и регулировки света фар с наводчиком
Стетоскоп технический
Устройство для очищения фильтров сажевых у дизельных авто
Набор для проверки герметичности системы охлаждения кейс 13 предметов
Наборы и оснастка для проверки технологических люфтов
Вакуумметр для измерения и создания разряжения в различных точках вакуумной магистрали кейс
Комплект инструмента в состав которого входят – тиски шуруповерт набор гаечных ключей и головок и т.д.
Передвижная инструментальная тележка
Ящик пожарный для песка
В проектах по техническому обслуживанию диагностике и зоне текущего ремонта определение производственной площади производится по формуле:
FЗ = (f а· n + Fоб) · Кп м2 (3.34)
где f а – площадь горизонтальной проекции автомобиля 2187м2;
n– количество постов в зоне ТО и ТР и постов диагностики.
Fоб – суммарная площадь горизонтальной проекции оборудования расположенного вне площади занятой постами или линиями м2;
Кп – коэффициент плотности расстановки постов и оборудования. Принимается (35 5).
Коэффициент Кп представляет собой отношение площади занимаемой автомобилями проездами проходами к сумме площадей проекции автомобилей в плане. Значение Кп зависит от габаритов автомобиля и расположения постов. При двустороннем расположении постов Кп = 3.5 4.5 меньшие значения принимают Кп для крупногабаритного состава и при числе постов на АТП более 10 шт.
При технологическом проектировании зон ТО и ТР режим их работы выбирается с учетом режима работы подвижного состава на линии в частности он должен согласоваться с графиком возврата и выпуска автомобилей.
Расчет количества постов произведем по формуле:
где -годовой объём работ данного вида (чел-ч) Т=5935 чел.час определенная в разделе 2.2 по формулам - 2.29 и 2.30;
-коэффициент неравномерности загрузки постов;
- число рабочих дней в году;
- число рабочих смен в сутки;
- продолжительность смены;
- принятое среднее число рабочих на одном посту;
- коэффициент использования рабочего времени поста.
Расчет ведем в табличной форме ниже.
Принимаем два поста для проведения диагностических работ Д1 и Д2.
Тогда: FЗ = (2187· 2 + 5127) · 30=144 м2
Окончательная площадь принимается исходя из рекомендаций ОНТП-01-91 и СНиП II-93-74 и эскизной компоновке (см. графическую часть проекта).
ОХРАНА ТРУДА И ОКРУЖАЮЩЕЙ СРЕДЫ
1 Инструкции по технике безопасности на участке
При определении места диагностических постов в плане производственного корпуса автотранспортного предприятия следует иметь в виду что посты (участки) диагностики должны размещаться таким образом чтобы диагностируемые автомобили могли поступать на посты (и с постов) из любой и в любую зону (хранения ожидания ТО и ТР) с минимальным числом переездов и маневров.
Габариты помещений для постов (участков) диагностирования устанавливаются с учетом размещения в них необходимого диагностического оборудования и с соблюдением действующих норм рабочих зон обеспечивающих нормальные условия работы на постах.
В соответствии с принятой технологией диагностирования посты диагностики оборудуются осмотровыми канавами. Помещения постов (участков) диагностирования должны отвечать всем требованиям высокой культуры рабочих мест. Стены и полы помещений постов диагностирования осмотровые канавы должны быть облицованы плиткой светлых тонов.
Освещение в помещении постов диагностики должно обеспечивать хороший осмотр автомобиля сверху и снизу со степенью искусственной освещенности не менее 150 люкс.
Помещения постов (участков) диагностирования должны быть оборудованы эффективно действующей системой приточно-вытяжной вентиляции.
Конструкция ворот дверей должна исключать возможность возникновения сквозняков. Должны предусматриваться тепловые завесы и устройства для автоматического открывания (закрывания) ворот и т.д.
Посты (участки) диагностирования должны оборудоваться системой световой сигнализации управление которой должно осуществляться как с поверхности пола помещения так и из осмотровой канавы. Сигнализация предназначается для передачи указаний оператора-диагноста или мастера находящегося во время осмотра в осмотровой канаве оператору (или перегонщику) находящемуся в кабине диагностируемого автомобиля.
АТП должна быть обеспечена противопожарным оборудованием и инвентарем в число которых входят огнетушители ящики с песком ведра багры. Инвентарь размещается на всех участках и отделениях АТП.
Заряженные огнетушители должны быть опломбированы и размещены в легкодоступных местах или на пожарных щитах. Не реже одного раза в три месяца их следует проверять путем взвешивания.
Песок является эффективным средством при тушении небольших количеств на полу органических растворителей. Он охлаждает горящее вещество и затрудняет доступ воздуха.
Эвакуация производственного персонала в случае возникновения ЧС осуществляется через основные ворота для заезда техники.
Инструкция по технике безопасности участка диагностики.
Перед началом работ:
Надеть и привести в порядок спецодежду. Застегнуть или обвязать обшлага рукавов заправить одежду так чтобы не было развевающихся концов подготовить к работе средства индивидуальной защиты.
Подготовить рабочее место к безопасной работе: убрать посторонние предметы освободить проходы убедиться что рабочее место хорошо освещено. Рабочий инструмент приспособления разложить в удобном и неопасном для использования порядке и проверить их исправность.
При обнаружении неисправного инструмента приспособлений оборудования и электроосвещения сообщить мастеру.
При диагностике систем автомобиля связанных с заводкой двигателя обеспечить отвод отработавших газов из помещения диагностического участка при помощи местной вытяжной вентиляции.
При диагностике автомобиля на стенде для проверки тяговых качеств автомобиля необходимо подставить упорные колодки и убедиться что впереди автомобиля не находятся люди.
Запрещается осуществлять установку автомобилей на посты диагностики без разрешения обслуживающего персонала. Скорость автомобиля должна быть не более 5-ти кмч.
Запрещается работать на оборудовании участка лицам не имеющим специального допуска.
Нельзя допускать попадания смазочных материалов на пол.
Пpи попадании этилиpованного бензина на кожу или на глаза необходимо немедленно пpомыть место попадания бензина водой или мыльным раствором.
При получении травмы на производстве нужно немедленно обратиться за помощью и сообщить мастеру.
После окончания работы:
Выключить оборудование и привести в порядок оборудование и рабочее место убрать инструменты и приспособления в отведенное для них место.
Сообщить мастеру обо всех недостатках обнаруженных во время работы.
Запрещается мыть руки в масле бензине керосине и вытирать их ветошью загрязненной опилками и стружкой.
2 Расчет освещения на участке
Свет создает нормальные условия для трудовой деятельности. Недостаточное освещение вызывает не только зрительный дискомфорт но и может привести к ряду негативных последствий связанных с нарушением зрения.
Основной задачей производственного освещения является поддержание на рабочем месте освещенности соответствующей характеру зрительной работы. Аварийное освещение устраивают для продолжения работы в тех случаях когда внезапное отключение рабочего освещения.
В данном разделе курсовой работы проведем расчет естественного и искусственного освещения.
Ширина окон принимается кратной 600 мм а высота определяется по формуле:
где hп.д. - расстояние от пола до подоконника 08 - 12 м;
hпод. - размер подоконного пространства 03 - 05 м;
H - высота здания. Согласно типовым проектам предприятий H - 375 - 425 м.
Световая площадь проемов определяется по формуле:
α - световой коэффициент α =035.
Глубина освещения определена по формуле:
Задавшись шириной окна определил число окон:
где b - ширина окна (54 м).
Таким образом согласно расчетам для обеспечения нормального естественного освещения необходимо выполнение трех окон с размерами 600х3150х5400. В данном случае с учетом размещения двух распашных ворот (см. план участка) имеется возможность размещения двух световых проемов. Для получения оптимальной степени освещения участка произведем расчет искусственного освещения.
Высота подвеса светильника рассчитывается по формуле:
где H - высота помещения м
hС - расстояние от светильника до потолка равное 02 - 025 м;
hР - расстояние от пола до рабочей плоскости равное 08 - 12 м.
Световой поток необходимый для освещения участка равен:
где К - коэффициент запаса освещения К = 13;
Е - норма искусственной освещенности;
сп - коэффициент использования светового потока i · сп = 045.
Для освещения участка используем лампы марки ДРЛ мощностью 200 Вт каждая.
Количество ламп определено по формуле:
принимаем 11ламп.(4.42)
где - световой поток одной лампы =2510лм
Количество электроэнергии которая расходуется на освещение в смену определяется по формуле:
00·11·1·200=4620000Вт(4.43)
где Т - время работы лампы (принимается в среднем 2100 ч);
N - количество светильников;
n - количество ламп в светильниках;
Wл – мощность лампы.
3 Расчет вентиляции на участке
При расчете вентиляции определяют необходимый воздухообмен подбирают вентилятор и электродвигатель.
Из значений объема исследуемого помещения и кратности обмена воздуха устанавливают производительность вентилятора W:
V – объем помещения участка зоны м3;
V= L ·B·H=12·12·4.25=612м3(4.44)
где L B H длина ширина и высота участка м.
K – кратность объема воздуха 1ч (табл. 4.8 ) (значения K приведены согласно разработкам Г.М. Напольского (МАДИ ГТУ))
Таблица 4.8- Значение коэффициента кратности объема воздуха K на участках АТО
Разборочно-сборочный (моторный агрегатный и др.) моечный
Ремонт топливной аппаратуры
Ремонт электрооборудования аккумуляторный
Постовые работы ТО ТР
Таким образом для проектируемого участка кратности обмена воздуха составит:
На основании приведенных расчетов выберем тип вентилятора из моделей рекомендуемых к использованию в помещениях АТО представленных в таблице ниже.
В настоящее время вентиляторы комплектуются соответствующими электродвигателями поэтому отдельно подбор двигателя не требуется
Таблица 4.9 - Типы вентиляторов для помещений АТО
Развиваемое давление Па
Частота вращения мин-1
Таким образом принимаем один вентилятор ЦАГИ-5. Вентиляторы осевые ЦАГИ-5 применяются в системах кондиционирования вентиляции и воздушного отопления производственных общественных и жилых зданий а также для других санитарно-технических и производственных целей.
Данные вентиляторы осевые общепромышленного исполнения предназначены для перемещения воздуха и других газовых смесей агрессивность которых по отношению к углеродистым сталям обыкновенного качества не выше агрессивности воздуха с температурой от -40° до +40°С не содержащих пыли и других твердых примесей в количестве более 10 мгм3 а также липких веществ и волокнистых материалов. Вентиляторы осевые из разнородных металлов В-06-300-5А В-06-300-63А предназначены для перемещения газопаровоздушных смесей I IIА IIВ категорий.
4 Мероприятия по охране окружающей среды
Снизить воздействие автомобилей на окружающую среду позволяют следующие мероприятия:
- совершенствование нормативно-правовой базы для обеспечения экологической безопасности автомобилей;
- создание экологически безопасных конструкций объектов транспорта эксплуатационных конструкционных строительных материалов технологий их производства;
- разработка ресурсосберегающих технологий защиты окружающей среды от транспортных загрязнений;
- разработка алгоритмов и технических средств мониторинга окружающей среды на транспортных объектах и прилегающих к ним территориях методов управления исправным техническим состоянием автомобилей;
- совершенствование системы управления природоохранной деятельностью на транспорте.
Системы очистки и рассеивания в атмосфере вентиляционных и технологических выбросов (оксида углерода оксидов азота альдегидов и др.) на СТО должны соответствовать требованиям «Санитарных норм проектирования промышленных предприятий» и «Указаний по расчету рассеивания в атмосферу вредных веществ содержащихся в выбросах предприятий».
Предельно допустимый выброс вредных веществ в атмосферу устанавливают для каждого их источника.
Мероприятия по защите атмосферного воздуха должны рассматриваться как составная часть общего плана по охране окружающей среды.
По санитарным нормам (СНиП II-93-74) концентрация загрязнений в воде подаваемой для мойки автомобилей системами оборотного водоснабжения после ее очистки не должна превышать: взвешенных веществ – 70 мгл при мойке грузовых 40 мгл – легковых автомобилей и автобусов; нефтепродуктов – соответственно 40 и 15 мгл тетраэтилсвинца – 0001 мгл.
При сливе сточных вод в канализационные коллекторы в них должно быть не более 025 075 мгл взвешенных веществ и 005 03 мгл нефтепродуктов а наличие тетраэтилсвинца не допускается. В производственных помещениях предусматривают оборотное водоснабжение для мойки автомобилей устройство локальных очистных сооружений для очистки производственных стоков от постов (аккумуляторного медницко-радиаторного кузнечно-рессорного участков и др.) а также сточных вод от мытья полов.
Характеристики АТП и объекта проектирования дает представление об условиях эксплуатации подвижного состава определяет тип предприятия по производственному назначению и указывает его производственные функции.
В характеристике объекта проектирования дано: наименование назначение перечисленные основные виды работ выполняемые на ней.
В расчетно-технологическом разделе выбраны исходные нормативы ТО и ремонта произведено их корректирование для заданных условий эксплуатации модификации подвижного состава природно-климатических условий.
В ходе работы над проектом согласно заданию представлен список работ по ТО автобусов Higer KLQ-6891 а так же разработан технологический процесс ремонта проведения ремонтных работ суппорта тормозного механизма передней оси автобуса Higer KLQ-6891. Произведен расчет нормы времени на технологический процесс которое составило 129мин. или 215 часа. Так же в специальной части согласно заданию подобрано необходимое оборудование для диагностического участка.
В разделе охрана труда и окружающей среды представлено обоснование размещения проектируемого участка в производственном корпусе с точки зрения техники безопасности и промышленной санитарии; техника безопасности при выполнении технологических операций; расчет искусственного по допустимым нормативам схема расположения светильников вентиляции и мероприятия по охране окружающей среды.
Поставленные задачи при проектировании курсового проекта выполнены в полном объеме. Решение этих задач при создании реального предприятия позволит организовать работу предприятия с наилучшей стороны.
СПИСОК ИСПОЛЬЗУЕМОЙ ЛИТЕРАТУРЫ
Положение о техническом обслуживании и ремонте подвижного состава автомобильного транспорта. – М.: - Транспорт 2011
Секирников В.Е. Охрана трудана предприятиях автотранспорта.- М.: Издательский центр "Академия" 2018 - 192с.
КузнецовА.С. Техническое обслуживание и ремонт автомобиля. В 2-хч. Ч.2.: учебник для студентов СПО -6-е изд.стер. - М.: Издательский центр "Академия" 2018 - 256 с.
Туревский И.С. Техническое обслуживание автомобилей зарубежного производства: учеб. пособие И.С. Туревский. - М. : ИД «ФОРУМ» : ИНФРА-М 2019. - 208 с. - (Среднее профессиональное образование).
Котлияров Р.Р. Подопрелов Е.М. Шаймарданов Р.Р. Методические рекомендации по выполнению курсового проекта. ПМ. 01. «Техническое обслуживание и ремонт автотранспорта» МДК 01.02. «Техническое обслуживание и ремонт автомобильного транспорта» Альметьевск 2020
Рекомендуемые чертежи
- 02.05.2021
- 23.05.2021
- 04.11.2022
- 04.11.2022
- 12.10.2016
- 04.11.2022