Проект организации то и ремонта оборудования линии производства консервов “Морковь гарнирная” разработкой технологической документации на то моечно-встряхивающей машины КМЦ


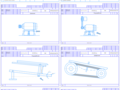
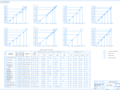
- Добавлен: 04.11.2022
- Размер: 471 KB
- Закачек: 0
Узнать, как скачать этот материал
Подписаться на ежедневные обновления каталога:
Описание
Курсовой проект - Проект организации то и ремонта оборудования линии производства консервов “Морковь гарнирная” разработкой технологической документации на то моечно-встряхивающей машины КМЦ
Состав проекта
![]() |
![]() ![]() ![]() |
![]() ![]() ![]() ![]() |
![]() ![]() ![]() |
Дополнительная информация
Контент чертежей
Графики_Дима.cdw

Рекомендуемые чертежи
- 08.02.2022
- 02.05.2021
- 23.05.2021
- 24.01.2023
- 24.01.2023
- 24.01.2023
Свободное скачивание на сегодня
Обновление через: 16 часов 33 минуты
- 22.08.2014
- 29.08.2014