Повышение эффективности работы скреперов


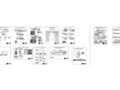
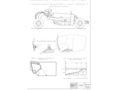
- Добавлен: 25.10.2022
- Размер: 22 MB
- Закачек: 1
Узнать, как скачать этот материал
Подписаться на ежедневные обновления каталога:
Описание
Повышение эффективности работы скреперов
Состав проекта
![]() |
![]() ![]() ![]() |
![]() ![]() ![]() |
![]() |
![]() ![]() ![]() ![]() |
![]() ![]() ![]() ![]() |
![]() ![]() ![]() |
Дополнительная информация
Контент чертежей
!!!!!!!!!!!!.dwg

ДП.dwg

Рекомендуемые чертежи
- 04.11.2022
- 23.06.2024
- 04.11.2022
- 04.11.2022
Свободное скачивание на сегодня
Обновление через: 12 часов 19 минут
- 06.06.2020