Повышение эффективности оборудования для укрепления стен пускового котлована при бестраншейной прокладки нефтепровода




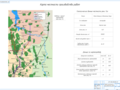
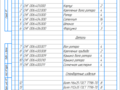
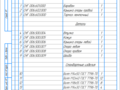
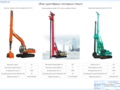
- Добавлен: 04.11.2022
- Размер: 6 MB
- Закачек: 1
Описание
Состав проекта
![]() |
![]() |
![]() ![]() ![]() ![]() |
![]() ![]() ![]() |
![]() ![]() ![]() ![]() |
![]() ![]() ![]() |
![]() ![]() ![]() ![]() |
![]() ![]() ![]() ![]() |
![]() ![]() ![]() ![]() |
![]() ![]() ![]() ![]() |
![]() ![]() ![]() |
![]() ![]() ![]() |
![]() ![]() ![]() |
![]() ![]() ![]() ![]() |
![]() ![]() ![]() ![]() |
![]() ![]() ![]() ![]() |
![]() ![]() ![]() |
Дополнительная информация
6. Гидросхема.cdw

Мотор гидравлический 210.25.13.21
Мотор гидравлический 310.3.56
Мотор гидравлический 310.12.00
Насос аксиально-поршневой
сдвоенный 223.25.01.00
Насос шестеренный 46У-Л
Распределитель гидравлический
Фильтр У. 491. 045. 000
Фильтр У. 491. 033 Б. 000
Цилиндр гидравлический
Схема гидравлическая
ДИПЛОМ ЛМ.docx
1 Описание трассы трубопровода8
2 Технология микротоннелирования11
3 Технология производства работ методом «стена в грунте»15
4 Обзор и анализ существующих конструкций с оборудованием20
КОНСТРУКТОРСКИЙ РАЗДЕЛ27
1 Выбор основных параметров27
2 Выбор основных параметров фрезерных роторов27
3 Выбор основных параметров и гидромотора вспомогательной лебёдки33
4 Выбор гидроцилиндра наклона стрелы с навесным оборудованием.38
5 Расчет гидравлической системы экскаватора41
5.1 Определение мощности гидропривода и насоса.43
5.3 Определение внутреннего диаметра гидролиний скоростей движения жидкости46
5.4 Выбор гидроаппаратуры и кондиционеров рабочей жидкости.47
5.5 Расчет потерь давления в гидролиниях49
5.6 Тепловой расчет гидропривода52
ТЕХНИЧЕСКИЙ СЕРВИС56
1 Исходные данные для расчета проведения ТО и Р57
2 Планирование ТО и Р экскаватора на текущий год57
2.1 Расчет числа ТО и Р экскаватора на текущий год57
3 Планирование ТО и Р экскаватора на выбранный месяц59
3.1 Расчет числа месяца по видам ТО и Р для экскаватора на июль 2015 г59
4. Технологическая карта смазки и заправки узлов экскаватора и рабочего оборудования61
5. Расчет трудоёмкости номерных видов ТО и Р для экскаватора63
6 Расчет численности производственных рабочих65
8 Расчет энергетики отделения66
9 Расчет площади зоны ТО69
БЕЗОПАСНОСТЬ ЖИЗНЕДЕЯТЕЛЬНОСТИ73
4 Выбор каната по разрывному усилию80
ЭКОНОМИЧЕСКИЙ РАЗДЕЛ83
1 Выбор базисного варианта83
3 Определение годовых текущих издержек потребителя88
3.1 Амортизационные отчисления на реновацию89
3.2 Затраты на выполнение текущих неплановых ремонтов и технических обслуживаний91
3.3 Затраты на выполнение капитальных ремонтов93
3.4 Заработная плата машиниста управляющего техникой94
3.5 Затраты на топливо для двигателя внутреннего сгорания95
3.6 Затраты на смазочные материалы96
3.7 Затраты на гидравлическую жидкость96
3.8 Затраты на перебазировки при перевозке техники на большегрузном прицепе-тяжеловозе97
Затраты на выполнение ТО и ремонтов100
Затраты на топливо100
4 Определение экономического эффекта100
СПИСОК ИСПОЛЬЗОВАННЫХ ИСТОЧНИКОВ104
При выполнении общестроительных дорожных мелиоративных и других видов строительных работ значительную долю составляют земляные работы производство которых происходит в сложных условиях. К таким условиям в первую очередь относятся работы производимые на грунтах повышенной прочности - мерзлых грунтах. Специфичность физико-механических свойств мёрзлых грунтов их высокая прочность соизмеримая с прочностью рабочих органов машин и высокая абразивность затрудняют использование известных технологий и существующего оборудования для выполнения земляных работ. Производство таких работ требует применения машин повышенной мощности и соответственно повышенных энергетических затрат.
Несмотря на имеющееся огромное разнообразие средств механизации методов и совершенствования технологий вопрос механизации зимних земляных работ до настоящего времени остается до конца не решенным. В первую очередь остается открытым вопрос механизации трудоемких работ выполняемых в стесненных условиях. Значительная доля земляных работ в том числе и на мерзлых грунтах производится вблизи существующих строений действующих предприятий линий электропередач и других близко расположенных объектов. Близость к месту производства работ существующих объектов и сооружений а также ограничения связанные с малыми размерами строительной площадки сдерживают применение целого ряда способов разработки грунтов (механических ударных взрывных).
Существующий парк землеройных машин в основном содержит мощную крупногабаритную технику которую невозможно использовать в стесненных условиях строительства. Машиностроительная промышленность в связи с масштабными объемами строительства в предшествующие годы была ориентирована на выпуск землеройных машин повышенной мощности.
Альтернативным вариантом повышения эффективности разработки мерзлых грунтов является использование новых методов воздействия рабочих органов на разрабатываемый грунт. В связи с этим внимание многих ученых направлено на проведение исследований и разработку теорий способствующих созданию новых видов рабочих органов машин и новых технологических принципов их воздействия на грунт дающих возможность наиболее эффективно осуществлять рабочие процессы. В поле поиска новых эффективных решений входило и применение новых физических методов разработки грунтов. Наибольшее внимание уделялось и уделяется вопросам интенсификации разработки мерзлых и прочных грунтов с применением оборудования для укрепления стен пускового котлована при бестраншейной прокладке нефтепровода.
Несмотря на значительные теоретические и экспериментальные исследования в области разработки мерзлых грунтов вопросы повышения эффективности производства земляных работ на мерзлых грунтах направленные на снижение силовых и энергетических затрат все еще требуют дальнейшего своего решения.
В связи с этим в дипломном проекте рассматривается тема «Повышение эффективности оборудования для укрепления стен пускового котлована при бестраншейной прокладке нефтепровода».
Основанием для выполнения данного дипломного проекта стало задание выданное кафедрой «Техника для строительства и сервиса нефтегазовых комплексов и инфраструктур (ТНКИ)» СибАДИ.
ОРГАНИЗАЦИОННО-ТЕХНИЧЕСКИЙ РАЗДЕЛ
1 Описание трассы трубопровода
Крупнейшая стройка Западной Сибири – нефтепровод «Заполярье - Пурпе - Самотлор» станет третьим трубопроводом в мире работающим в условиях полярной тундры. К объекту сейчас приковано повышенное внимание. Добыча нефти в ХМАО и на юге Ямала упала нефтяники начали разведочное бурение на севере ЯНАО в Красноярском крае и нашли большие запасы. Строительство трубопроводной системы необходимо для того чтобы нефть из северных регионов была перенаправлена не только на Запад но и на Восток.
Рисунок 1.1.1 – Нефтепровод «Заполярье - Пурпе - Самотлор»
Строительство первой очереди было крайне сложным. Менее чем за 2 года был построен нефтепровод «Пурпе - Самотлор». В строительстве участвовало более двух тысяч человек 700 единиц тяжелой техники.
В 2012 году «Сибнефтепровод» приступил к строительству «Заполярье - Пурпе». На втором этапе возникли еще более сложные условия так как севернее Пурпе встречаются мерзлые грунты. Экология данного района предельно ранима и чтобы ее сохранить около 2 км трубопровода проводились под рекой Таз в районе Тазовской губы. Организация подводного перехода нефтепровода через реку Таз вступила в решающую стадию – началось бурение скважины под основную нитку магистрали. Прокладка трубы осуществляется методом микротоннелирования.
Рисунок 1.1.2 – Нефтепровод «Заполярье - Пурпе»
На сегодняшний день в русловой части завершены работы по бурению скважины диаметром 600 мм сейчас идет процесс ее расширения в несколько этапов. Согласно проекту диаметр тоннеля необходимо довести до отметки 1600 мм затем можно будет произвести протаскивание рабочей нитки диаметр которой с учетом защитного кожуха будет составлять 1220 мм. Параллельно ведутся работы и по прокладке резервной нитки нефтепровода.
В месте строительных работ постоянное русло реки составляет расстояние около километра а глубина местами доходит до 20 метров. Но в период половодья зеркало воды разливается по всему пойменному участку ширина которого достигает 27 километров а уровень воды поднимается на пять с половиной метров. При этом вскрываются и многочисленные пойменные озера старицы и протоки сливаясь и затапливая пойму.
Согласно проекту русловая часть перехода производится методом наклонно-направленного бурения а на обширной территории поймы – методом подземной прокладки. Это позволяет минимизировать негативное воздействие на северную природу как во время проведения строительных работ так и в процессе эксплуатации нефтепровода. В технических решениях нефтепроводчики применяют самые современные технологии и материалы.
Сложность проекта заключается в том что от начала строительства объекта и до его завершения у подрядных организаций есть всего лишь несколько зимних месяцев. Все работы включая и рекультивацию земель должны быть завершены до наступления паводка.
Реализация этого проекта производится в условиях сложной геологической структуры. Промерзание грунтов достигает глубины пяти метров. На пойменном участке нефтепровода где производится разработка траншеи для подземной прокладки даже мощь современной техники не позволяет все работы проводить только механическим способом. Чтобы уложиться в предельно сжатые сроки строителям приходится применять методику буровзрыва.
Все работы на одном из самых сложных участков магистрали – в пойме реки Таз ведутся под контролем специалистов служб надзора и полностью соответствуют строгим нормативам технической и экологической безопасности.
Нефтепровод «Заполярье - Пурпе» обеспечит доступ к освоению крупных месторождений - Сузунское и Русское (ТНК-ВР) Мессояхинское (ТНК-ВР «Газпром нефть») Пякяхинское (ЛУКОЙЛ) Тазовское и Заполярное
Трубопровод «Заполярье - Пурпе - Самотлор» позволит переориентировать экспорт российской нефти дисбаланс которого сегодня смещен в сторону запада в страны Азиатско-Тихоокеанского региона. Строительство трубопровода создаст предпосылки для дальнейшего освоения северных территорий будет способствовать социальному развитию ЯНАО. Реализация проекта позволит обеспечить до 10 тыс. рабочих мест.
2 Технология микротоннелирования
В работах по прокладке трубопроводов и трубопроводных систем в коммунальной сфере а также сооружении системы водо- и тепло- и газоснабжения наряду с традиционными технологиями используются и новейшие технологии. Технология микротоннелирования не требует раскопки традиционных траншей по всей протяженности прокладки труб что позволяет свести к минимуму воздействие на экологию в процессе строительства.
Эта технология применялась в странах Европы и США ещё с конца прошлого столетия и на сегодняшний день является одним из главных методов прокладки труб и коллекторов в крупных городах.
Любые проекты в которых осуществляется прокладка подземных коммуникаций при технологии микротоннелирования не имеют препятствий. Это сооружение проходов под автострадами и взлетно-посадочными полосами работы в районах города с исторической застройкой и сооружение тоннелей под реками и железнодорожными путями. Универсальная технология не использующая в строительстве сооружение траншей позволяет эффективно решать задачи развития инфраструктуры города в том числе и те решение которых до недавнего времени было проблематичным.
Проход в грунте осуществляется при помощи проходческой машины или другими словами щита (проходческий щит) который двигает домкратная станция устанавливаемая на глубине необходимой для прокладки трубопровода.
Рисунок 1.2.1 –Проходческий щит
На подготовительном периоде разрабатываются два котлована (стартовый и приемный). Расстояние между стартовой и приемной шахтами составляет от 50 до 500 м. Домкратная станция устанавливается в стартовом котловане на глубине необходимой для осуществления прокладки трубопровода. При длине проходки свыше 200 метров используется промежуточная домкратная станция. В плане шахты могут быть круглыми или квадратными. Размеры их сторон до 6 м в зависимости от типа щита.
Разработка грунта производится режущим инструментом проходческой машины. Грунт перемешивается с водой (или бентонитовым раствором) которая подаётся в забой по подводящим линиям а по отводящим линиям полученная взвесь попадает в отстойник который находится у стартового котлована.
Поэтапное продвижение проходческого щита вперед заканчивается в приемном котловане после чего он демонтируется оставив за собой готовый коллектор. Методом микротоннелирования прокладываются стальные или специальные железобетонные трубы для микротоннелирования (тюбинги).
Перед началом работ проводятся подготовительные работы включающие в себя строительство стартового и приемного котлована на уровне ожидаемого расположения труб. Расстояние между котлованами составляет от 50 до 500 м. Затем в стартовом котловане монтируется домкратная станция и проходческий щит. Домкрат продвигает щит в грунте на расстояние равное длине труб продавливания и таким образом процесс повторяется. При длине проходки свыше 200 метров используется промежуточная домкратная станция.
Рисунок 1.2.2 – Домкратная станция
Режущее колесо машины разрабатывает породу которая впоследствии смешивается с водой подающейся насосом питания в зону режущих колёс и подаётся в отстойник на поверхность шахты.
Разработка грунта производится режущим инструментом проходческого щита. Грунт перемешивается с водой (или бентонитовым раствором) которая подаётся в забой по подводящим линиям а по отводящим линиям полученная взвесь попадает в отстойник который находится у стартового котлована.
Особое внимание уделяется точности проходки которое обеспечивается лазером.
Электронная лазерная система управления ELS для прямолинейных участков длиной до 200 метров состоит из трех основных составляющих.
Рисунок 1.2.3 – Электронная лазерная система управления ELS
Для прямолинейных участков длиной от 200 до 400 метров применяется ELS-HWL (электронная лазерная система с гидростатическим водяным уровнем). Поскольку при большой длине проходки внутри трубы может быть разная температура воздуха это приводит к преломлению лазера что в свою очередь изменяет направление машины по вертикали. Гидростатический уровень определяет точные данные по высоте независимо от температуры.
Для проходки криволинейных участков в микротоннелировании применяется система с гироскопом GNS-P.
Рисунок 1.2.5 – Электронная лазерная система с гироскопом GNS-P
Данная система применяется без лазера с ориентированным на север гироскопом при внутреннем диаметре трубы от 800мм.
Отличительной чертой данного метода является высокая точность проходки отклонение от проектной оси составляет не более 30мм. Это обеспечивается специальным компьютерным комплексом управления на основе системы лазерного наведения щита. Микротоннелирование осуществляется в автоматическом режиме. Вся проходка наблюдается непосредственно оператором его местонахождение базируется в центре управления микротоннеля.
Рисунок 1.2.5 – Отклонение от проектной оси на приборе оператора
Технология микротоннелирования помогает прокладывать трубопроводы в разных категориях грунтов: от суглинков и водонасыщенных песков до скальных пород. Так же немаловажным преимущество метода микротоннелирования является высокая скорость проходческих работ – до 15 метров в сутки.
3 Технология производства работ методом «стена в грунте»
Сущность способа «стена в грунте» заключается в образовании под защитой глинистого раствора траншеи (выработки) с вертикальными стенками и последующим заполнением траншеи материалами или конструкциями. При заполнении выработки бетоном железобетоном и сборными конструкциями «стена в грунте» выполняет роль ограждающей или несущей конструкции. При заполнении траншеи противофильтрационными материалами она выполняет роль противофильтрационного устройства (завесы).
Способ «стена в грунте» используют при возведении подземных частей промышленных энергетических и гражданских зданий гидротехнических транспортных и коммунальных инженерных сооружений а также при микротоннелировании. Обычно глубина конструкций ограничивается возможностями применяемой землеройной машины. Ширина траншеи может быть 02—12 м что также ограничивается имеющимися в строительстве механизмами.
Способ «стена в грунте» может быть использован в различных инженерно-геологических и гидрогеологических условиях и во многих случаях позволяет отказаться от забивки шпунта различного рода креплений водопонижения и замораживания. Применение способа «стена в грунте» целесообразно при высоком уровне подземных вод; заглублении конструкции в прочный и водоупорный слой
В отечественной практике применяют два типа стен возводимых способом «стена в грунте»: свайные – образуемые из сплошного ряда буронабивных свай и траншейные – образуемые сплошной стеной из монолитного или сборного железобетона.
Устойчивость стенок траншей возрастает с увеличением плотности глинистого раствора и уменьшением проницаемости образованного экрана.
Конструкции возводимые способом «стена в грунте» по способу изготовления бывают: монолитные сборные и сборно-монолитные.
Данный способ рекомендуется использовать для защиты от загрязнений грунтовых вод инфильтрационными водами из различного рода отстойников шламохранилищ иловых площадок; для предотвращения фильтрации в обход гидротехнических сооружений; защиты от подтоплений и заболачивания территорий и магистральных каналов водохранилищ.
– Буровая головка. 2 – Циркуляционный насос. 3 – Корпус гидрофрезы. 4 – Кран. 5 – Гидросиловая установка. 6 – Шланг отвода бурового раствора с обломками породы на установку регенерации бурового раствора с грохочением для удаления из него песка. 7 – Домкрат регулирующий нагрузку на буровую головку 8 – Секция траншеи постоянно заполненная раствором на бентонитовой основе. 9 – Гидравлические шланги.
Рисунок 1.3.1 – Разработка траншеи
Метод разработки траншеи гидрофрезерным способом заключается в том что сначала сооружения возводят в узких и глубоких (до 60 м) траншеях заполняемых при выемке грунта бентонитовым раствором который создает избыточное гидростатическое давление на вертикальные стенки траншеи благодаря чему они остаются ровными. Затем траншею заполняют заглинизированным грунтом грунтобетоном монолитным бетоном или железобетоном.
Рисунок 1.3.2– Технологический процесс устройства конструкции «Стена в грунте»
Технологические этапы производства «Стены в грунте»:
Устройство временной монолитной железобетонной конструкции - форшахты. Форшахта предотвращает обрушение грунта верхней части траншеи а также является направляющей конструкцией для устройства «Стены в грунте»;
Разработка траншеи гидрофрезой при подаче воды для улучшения заглубления роторов в грунт которые вращаются друг от друга;
Извлечение рабочего органа из траншеи при одновременной подаче бетона при этом роторы вращаются навстречу друг другу;
Установка армированного каркаса;
После окончания работ по сооружению «Стены в грунте» бетон набирает прочность форшахту демонтируют и производят разработку котлована.
По назначению различают три типа стен: несущие ограждающие и противофильтрационные. По материалу различают следующие виды стен: железобетонные бетонные; грунтоцементные глинистые комбинированные. По способу изготовления подземные стены делятся на: монолитные сборные и сборно-монолитные.
По грунтовым условиям «Стена в грунте» может применяться в любых дисперсных грунтах за исключением текучих глинистых грунтов илов и плывунов а также при наличии подземных вод с большими скоростями фильтрации. При наличии грунтов содержащих твердые включения природного или техногенного происхождения (крупные валуны обломки бетонных конструкций каменной кладки и др.) при проходке траншеи необходимо использовать технику оснащенную фрезерным оборудованием например фирм Casagrande Bauer TONE Boring.
При устройстве «Стены в грунте» жесткие требования должны предъявляться к глинистому раствору. При устройстве монолитных стен в грунте методом вертикально перемещающейся трубы (ВПТ) необходимо применять более совершенную технологию бетонирования с использованием вибрирования.
Так как конфигурация подземных сооружений может быть достаточно сложной то необходимо обратить внимание на проходку первичных и вторичных панелей особенно в углах и в торцах сооружения (Т-образные соединения).
Для повышения индустриальности ведения работ и качества стен рекомендуется применять сборный или сборно-монолитный вариант.
Сборная или сборно-монолитная «Стена в грунте» позволяет:
увеличить скорость возведения конструкции
снизить ее трудоемкость
снизить расход бетона.
4 Обзор и анализ существующих конструкций с оборудованием
Для укрепления котлована по технологии «стена в грунте» применяются несколько видов машин.
Нарезку траншей при прокладке трубопроводов кабелей и других инженерных сооружений выполняют с помощью баровой машины - колесным или гусеничным трактором со смонтированной на нем направляющей рамой и режущей кулачковой цепью с зубьями.
Существуют различные виды баровых грунторезных машин навешиваемых на колесные или гусеничные трактора.
Баровая грунторезная машина состоит из трактора имеющего привод заднего вала отбора мощности. К нему прикреплена рама с рабочим грунторезным инструментом установленным с возможностью подъемаопускания и вращения от гидравлического привода. Рама выполнена с элементами ее прикрепления к заднему мосту трактора и представляет собой короб с коробчатыми кронштейнами.
Рисунок 1.4 – Баровая грунторезная машина на гусеничном тракторе
Баровая грунторезная машина устанавливается в начале траншеи подается вращение от приводного двигателя на шестерню привода заднего вала отбора мощности (ВОМ) и на гидравлический насос связанный с этой шестерней. Гидронасос через гидравлическую магистраль подает рабочую жидкость в гидромотор и приводит вал его во вращение которое через планетарный редуктор приводит во вращение ведущий вал и закрепленную на нем ведущую звездочку находящуюся в зацеплении с режущей цепью рабочего органа. Рабочий орган с движущейся режущей цепью гидроцилиндром плавно опускают на грунт со скоростью подачи обеспечивающей выемку грунта без перегрузки привода рабочего органа. Заглубление производится до величины определяемой глубиной траншеи. При достижении заданной глубины траншеи трактор начинает движение вдоль траншеи в сторону противоположную отрытой части. Движение трактора обычно посредством гидроходоуменьшителя производится до конца намеченной траншеи.
Основными достоинствами цепных и баровых землерезных машин являются простота конструкции и удобство в эксплуатации небольшая металлоемкость и достаточно высокая (до 70 м3ч) производительность недостатками - большие затраты мощности (до 60 % от всей потребляемой) на измельчение грунта и преодоление трения в цепях низкая долговечность рабочего органа работающего в абразивной среде малая глубина копания.
Для разработки узких глубоких траншей при устройстве подземных сооружений методом «стена в грунте» и небольших в плане глубоких котлованов с вертикальными стенками в стесненных условиях целесообразно применять грейферное оборудование на телескопической напорной штанге. Базовой машиной для такого оборудования служит гидравлический экскаватор или кран. Напорная штанга обеспечивает возможность фиксации грейферного ковша в пределах значительной глубины копания создания принудительного усилия его внедрения быстрой корректировки вертикального положения штанги погрузки разрабатываемого грунта в транспортные средства. детство
Рисунок 1.4.2 – Кран с грейферным оборудованием на телескопической напорной штанге
Разработка грунта грейферным оборудованием производится на всю глубину по различным технологическим схемам. Наиболее часто используют схему последовательной разработки грунта в траншее которая после выемки грунта заполняется сборным или монолитным железобетоном с установкой ограничителей захваток. Захватки назначаются из условия максимального раскрытия ковша грейфера. Грунт разрабатывается с одной стоянки экскаватора на проектную глубину траншеи.
Грейферный ковш после каждого цикла наполнения извлекается из траншеи и удерживается над ней в течение 15—20 с. для стекания глинистого раствора. После этого грунт из ковша выгружается в отвал или автосамосвал. Затем рабочий цикл повторяется. По мере разработки грунта в траншею подается глинистый раствор в количестве обеспечивающем постоянный уровень не ниже чем 20 см от верха траншеи.
Достоинством грейферных устройств является большая глубина копания однако данные машины имеют низкую производительность в результате цикличности работы.
Сооружение подпорной стенки может выполняться также с помощью последовательного устройства буронабивных свай. В скважины под давлением закачивается бетон песчано-цементная смесь или водоцементный раствор.
Буронабивные сваи устраивают без использования обсадных труб в маловлажных породах. В этом случае бурение можно осуществлять без крепления стенок скважин. В водонасыщенных породах устройство буронабивных свай проводят под защитой обсадных труб или полимерного или глинистого бурового раствора.
Ограждение формируется из цемента срок схватывания которого должен быть не менее 2 ч. Подвижность бетонной смеси обеспечивается подбором ее состава и введением в смесь поверхностно-активных пластифицирующих добавок.
Основные этапы устройства ограждения последовательной установкой буронабивных свай:
Подготовительные работы;
Подготовка обсадных труб;
Бурение скважин для свай;
Установка арматурного каркаса;
Установка бетонолитной трубы;
Подача бетонной смеси;
Извлечение секций обсадной трубы;
Уплотнение бетонной смеси.
Рисунок 1.4.4 – Стадии формирования свай
Бурение скважин выполняется с применением инвентарной обсадной трубы и режущего наконечника. В процессе бурения скважин совершаются непрерывные возвратно-вращательные движения обсадной трубы во избежание ее засасывания. По достижении забоем проектной отметки его тщательно зачищают от бурового шлама грейфером или ковшовым буром. При извлечении и демонтаже обсадных труб должно учитываться возможное понижение уровня бетона в скважине и опускание бетонолитной трубы величина которого устанавливается опытным путем.
В качестве оборудования для погружения обсадных труб и для бурения применяются бурильно-крановые машины а поэтапный демонтаж секций обсадной трубы производится бурильно-крановой машиной по мере бетонирования свай.
Рисунок 1.4.3 – Бурение скважины бурильно-крановой машиной
После завершения бурения скважины и ее зачистки производится установка арматурного каркаса – сваи. Арматурные каркасы для буронабивных свай изготавливают обычно на специализированных участках с обязательной маркировкой. Диаметр арматурного каркаса должен быть на 80-100 мм меньше внутреннего диаметра обсадной трубы во избежание заклинивания его в трубе.
Способ строповки подъем и опускание арматурного каркаса в скважину должны исключить появление в нем деформаций. Каркас опускается в положение обеспечивающем его свободное прохождение в скважину.
Заполнение скважины бетонной смесью начинается после зачистки забоя и проверки глубины скважины но не позднее чем через 2 ч после окончания бурения. При более длительном перерыве производится повторная зачистка забоя.
Укладка бетонной смеси в скважину производится методом вертикально перемещающейся трубы (ВПТ). Установка бетонолитной трубы в скважину перед бетонированием производится так чтобы ее нижний конец был расположен выше забоя скважины на 200-250 мм (начальное положение). Нижнее звено бетонолитной трубы в процессе укладки бетонной смеси должно быть постоянно заглублено в восходящую смесь не менее 2000 м. Перерывы в бетонировании не допускаются.
Бурение скважин производится при помощи буровых установок BAUER BG 28 или Casagrande B175.
Достоинством устройства ограждения с применением буровой машины роторного типа является использование универсальных машин однако недостатками являются нерациональное сечение стены большие затраты большие объемы строительства следовательно низкий уровень производительности.
КОНСТРУКТОРСКИЙ РАЗДЕЛ
1 Выбор основных параметров
При проектировании технологического процесса разработки скважины гидравлическими роторами необходимо выбрать такие значения момента и частоты её вращения которые позволят обеспечить непрерывный и качественный процесс разработки скважины. Для расчёта необходимы следующие исходные данные а именно
ширина роторов L = 25 м;
ширина захвата фрезы В = 09 м;
диаметр ротора D = 12 м;
толщина кромки лопасти b = 50 мм;
число лопастей на одной фрезе z = 20
масса стрелы с рабочим оборудованием mc = 9 тонн;
давление в гидросистеме Pгид=32 МПа;
плотность грунта = 2200 кгм3.
2 Выбор основных параметров фрезерных роторов
Основными параметрами определяющими эффективность работы фрезы являются скорость резания толщина срезаемой стружки грунта за один оборот ротора поступательная скорость мощность силовой установки и производительность фрезы.
По частоте вращения ротор дорожной фрезы относится к рабочим органам имеющим повышенные скорости резания. Проведенные исследования показывают что скорость резания должна находиться в пределах 9 14 мс.
Скорость резания зависит от частоты вращения фрезерного ротора и его диаметра. Под диаметром ротора подразумевается диаметр окружности описываемой режущими кромками лопастей.
Частоту вращения роторов определяем по формуле
где vрез – скорость резания мс vрез= 12 мс;
D – диаметр ротора м D= 12 м.
Степень измельчения грунтов зависит от толщины срезаемой стружки. Исследования показали что толщина стружки должна находиться в пределах 2 5 мм. Меньшее значение толщины стружки относится к связным грунтам.
На толщину срезаемой стружки при расчетной частоте вращения влияет число лопастей в поперечном сечении ротора и рабочая поступательная скорость фрезы. На роторе рассматриваемой буровой установки в поперечном сечении установлено 5 лопастей.
Рабочая поступательная скорость фрезы определяется по формуле
где h1 – толщина стружки м h1= 0005 м;
n – частота вращения роторов обс; n =318 обс;
z – число лопастей в сечении ротора z = 5.
К основным параметрам фрезы относится также мощность затрачиваемая на работу фрезы. Мощность расходуется на передвижение машины фрезерование грунта и работу дозирующей системы.
Основная часть мощности расходуется на резание грунта. Находим её по формуле
где P0 – сопротивление грунта резанию Па P0 = 210000 Па;
b – ширина лопасти м b = 005 м;
h – глубина резания м h = 12 м;
h1 – толщина стружки м h1 = 0005 м;
z – число лопастей на одной фрезе z = 20;
n – частота вращения роторов обс n =318 обс.
Так как рабочий орган состоит из двух фрез следовательно значение мощности резания грунта принимаем N1 = 8012 Вт.
Мощность расходуемая на перемещение фрезы находим по формуле
где k0 – коэффициент отбрасывания для узких лопастей k0 = 075;
m – масса грунта отбрасываемая за 1 с кг;
vокр – окружная скорость на концах лопастей мс vокр = 12 мс;
В – ширина захвата роторов м В = 09 м;
– плотность грунта кгм3 =2000 кгм3.
Мощность расходуемая на преодоление сопротивления трению в трансмиссии то вала отбора мощности до ротора считается по формуле
где N1 – мощность резания грунта Вт N1 = 8012 Вт;
N2 – мощность расходуемая на перемещение фрезы Вт N2 = 9331 Вт;
– КПД трансмиссии = 075.
Таким образом общая мощность двигателя определяется по следующей формуле
N3 – мощность расходуемая на преодоление сопротивления трению в трансмиссии то вала отбора мощности до ротора Вт N3 = 4336 Вт.
Крутящий момент на валу фрезерного ротора определяется по следующей формуле
где n – частота вращения роторов обс n =318 обс;
Nдв – мощность двигателя Вт Nдв = 21679 Вт;
– КПД трансмиссии от двигателя до ротора = 07.
Основным элементом фрезы является фрезерный барабан с приводом. Расчет ротора и его трансмиссии производят по максимальному крутящему моменту на оси ротора с учетом динамических перегрузок
где k1 – коэффициент динамичности k1 = 20;
Mкр – крутящий момент на валу фрезерного ротора Нм Mкр=4772 Нм.
Окружное усилие по которому рассчитывают усилия в лопастях и других элементах ротора определяется по формуле
Производительность на различных технологических операциях (измельчение грунта перемешивание смеси) определяют по формуле
где vп – рабочая поступательная скорость фрезы мс vп= 008 мс;
В – ширина захвата фрезы м В = 09 м;
kп – размер перекрытия полос kп = 01 м;
kв – коэффициент использования машины внутри смены по времени kв = 085;
n2 – число проходов фрезы по одному следу n2 = 1.
Имея требуемую мощность (Nдв = 21679 Вт) можно подобрать гидромотор проектируемой буровой установки.
Марка гидромотора HVK-A F2-7317
Таблица 2.2.1 – Техническая характеристика гидромотора HVK-A F2-7317
Продолжение таблицы 2.2.1
Номинальное давление
Крутящий момент (при номинальном давлении)
Коэффициент полезного действия
Рисунок 2.2.1 – Гидромотор лопастной HVK-A F2-7317
3 Выбор основных параметров и гидромотора вспомогательной лебёдки
Исходными данными для расчета основных параметров гидравлической лебёдки принимаем: DБ – диаметр барабана DБ = 402 мм; dК – диаметр каната
dК = 15 мм; UП - кратность полиспаста UП = 1 (т.к. канатно-блочная система в данном случае отсутствует); vб - скорость барабана vб = 01 мс; б - коэффициент полезного действия барабана б = 095; с - суммарный коэффициент полезного действия всех механических передач между барабаном и валом гидромотора с = 089.
Линейная скорость намотки каната на барабан лебёдки в первом слое определяется по следующей формуле
где vб – скорость барабана vб= 01 мс;
Uп – кратность полиспаста Uп = 1.
Частоту вращения барабана определяем по следующей формуле
где v0 – линейная скорость намотки каната на барабан лебёдки v0= 01 мс;
D6 – диаметр барабана Dб = 0402 м;
dк – диаметр каната dк = 0015 м.
Скорость движения каната в слое намотки определяем по следующей формуле
где Dб – диаметр барабана Dб = 0402 м;
с – номер слоя с = 1;
dк – диаметр каната dк = 0015 м;
n0 – частота вращения барабана n0 = 458 обмин.
Тяговое усилие вспомогательной лебёдки при неподвижном рабочем органе в момент поднятия груза определяется по следующей формуле
где б – коэффициент полезного действия барабана б = 095;
Gг – сила тяжести поднимаемого груза Gг = 7500 Н.
Крутящий момент на барабане грузовой лебёдки в первом слое определяется по следующей формуле
Dк – диаметр каната dк = 0015 м;
Тб – тяговое усилие вспомогательной лебёдки при неподвижном рабочем органе в момент поднятия груза Тб = 78947 Н.
При Mб = сonst тяговое усилие каната грузовой лебёдки изменяется в зависимости от слойности намотки и для первого слоя определяется по следующей формуле
где Мб – крутящий момент на барабане в первом слое Мб = 1646 Нм;
Dб – диаметр барабана Dб = 0402 м;
с – номер слоя с = 1;
При Мб = const тяговое усилие каната изменяется в зависимости от слойности намотки и для второго слоя определяется по следующей формуле
Мощность потребляемая барабаном грузовой лебёдки определяется по следующей формуле
где Тб – тяговое усилие наматываемой на барабан ветви каната Tб = 78947 Н;
v0 – линейная скорость намотки каната на барабан лебёдки v0 = 01 мс;
б – коэффициент полезного действия барабана б = 095.
Мощность потребляемая грузовой лебёдкой определяется по следующей формуле [9]
где Nб – мощность потребляемая барабаном грузовой лебедки Nб = 1108 кВт;
с – суммарный коэффициент полезного действия всех механических передач между барабаном и валом гидромотора с = 089.
Имея требуемую мощность Nл = 1245 кВт можно подобрать гидромотор вспомогательной гидравлической лебёдки (Таблица 2.3.1) проектируемой буровой установки.
Рисунок 2.3.1 – Гидромотор аксиально-поршневой Г15-25Р
Таблица 2.3.1 – Техническая характеристика гидромотора Г15-25Р
Марка гидромотора Г15-25Р
Номинальное давление на входе
Максимальное давление на входе
Минимальное давление на входе
Максимальное давление дренажа
Номинальная частота вращения
Максимальная частота вращения
Номинальная мощность
Масса без рабочей жидкости
4 Выбор гидроцилиндра наклона стрелы с навесным оборудованием.
В конструкции проектируемой буровой установке предусмотрена система наклона всего рабочего оборудования. Данная система представляет собой гидроцилиндр неподвижно закрепленный на направляющей. Усилие гидроцилиндра приходиться на подвижный кронштейн стрелы и должно быть достаточным чтобы полностью поднимать все рабочее оборудование. Такая система позволяет оператору регулировать угол наклона стрелы. Это позволяет осуществлять разработку скважины на неровной поверхности.
Усилие на штоке гидроцилиндра находим по формуле
где Pгид - давление в гидросистеме Pгид=32 МПа;
F– площадь поршня со стороны штоковой полости гидроцилиндра м2 вычисляется по формуле
где D – диаметр штока гидроцилиндра наклона стрелы м.
Чтобы найти значение усилия на штоке гидроцилиндра составим систему моментов сил.
Рисунок 2.1 – Система моментов сил
Из формулы (2.4.3) выражаем значение усилия на штоке гидроцилиндра
где Gстр – сила тяжести стрелы Н Gстр = 90000 Н.
Расчет произведем для нескольких положений так как невозможно установить заранее в каком положении рабочего органа усилие на штоке гидроцилиндра будет максимальным.
Из формул (2.4.1) и (2.4.2) выражаем диаметр штока гидроцилиндра
Округляем до ближайшего большего значения и выбираем гидроцилиндр наклона рабочего оборудования с диаметром штока 180 мм.
Рисунок 2.4.1 – Гидроцилиндр с проушинами с обеих сторон со сферическими подшипниками ГЦС 250х180-2500-06-С-0-0
Таблица 2.4.1 – Технические характеристики гидроцилиндра ГЦС 250х180-2500-06-С-0-0
Марка гидроцилиндра ГЦС 250х180-2500-06-С-0-0
Давление номинальное
Давление максимальное
Толкающее усилие на штоке
Тянущее усилие на штоке
Максимальная скорость
5 Расчет гидравлической системы экскаватора
Исходные данные для расчета объемного гидропривода
Рабочее давление МПа 32
Усилие на штоке Н 32000
Скорость движения штока мс05
Длина трубопроводов м
а) от бака к насосу21
б) от насоса к распределителю08
в) от распределителя к гидродвигателю70
г) от распределителя к баку29
Местные сопротивления шт:
а) сверленый угольник4
б) присоединительный штуцер4
г) плавное колено 900-
д) угольник с поворотом на 9002
Температурный режим работы0С
а) рабочей жидкости30 - 70
б) окружающей среды-20 - +15
Рисунок 2.5.1 - Расчетная схема механизма наклона стрелы
Гидравлический привод (рисунок 2.5.1) состоит из гидробака Б насоса Н секционных четырехпозиционных гидрораспределителей Р гидроцилиндров подъема стрелы Ц фильтра Ф с переливным клапаном. Контроль давления рабочей жидкости ведется с помощью манометра МН1.
Рабочая жидкость из гидробака Б по всасывающей гидролинии насосом Н подается в напорную гидролинию через центральное вращающееся соединение к секционному гидрораспределителю Р и одновременно к предохранительному клапану КП с переливным гидроклапаном.
При перемещении золотника гидрораспредилителя Р перемещается дополнительный золотник вследствие чего переливной гидроклапан закрывается рабочая жидкость от насосов поступает к гидроцилиндрам. Противоположная полость гидроцилиндров при этом соединяется со сливной гидролинией. Гидроцилиндры Ц подъема стрелы подключаются к соответствующим секциям гидрораспределителя Р. которые устанавливаются в гидролиниях являющихся сливными при опускании стрелы. Предохранительный клапан КП2 предохраняет систему от давления рабочей жидкости превышающего установленное путем слива жидкости в гидробак Б.
5.1 Определение мощности гидропривода и насоса.
Мощность гидропривода определяется по заданным нагрузкам и скоростям гидродвигателей обеспечивающих привод исполнительных механизмов.
Полезная мощность гидродвигателя возвратно-поступательного действия (гидроцилиндра) определяется по формуле
где F - усилие на штоке гидроцилиндра кН;
v - скорость перемещения штока мс.
Nгдв = 32 05 =16 кВт
Получаемая мощность насоса определяется из мощности гидродвигателя с учетом потерь энергии при ее передаче от насоса к гидродвигателю по формуле
Nнп = kзу kзс Nгдв (2.5.2)
где kзу- коэффициент запаса по усилию зу=11 13;
kзс- коэффициент запаса по скорости зс=11 13;
Nгдв – мощность гидродвигателя кВт Nгдв = 16 кВт
Зная необходимую полную мощность насоса определяемую по формуле (2.5.2) и учитывая что полезная мощность насоса связана с номинальным давлением и подачей зависимостью Nнп = pном Qн можно найти подачу или рабочий объем насоса по формулам
qн= Nнп Pном nн (2.5.4)
где Qнд –подача насоса дм3с;
Nнп – мощность насоса кВт Nнп =25 кВт;
Pном - номинальное давление Мпа Pном = 32 МПа;
qн - рабочий объем насоса дм3;
nн - частота вращения вала насоса обс nн = 25 обс.
Насос выбирается из технической литературы по двум параметрам ближайшим к расчетным: номинальному давлению Pном и рабочему объему насоса qн
Техническая характеристика аксиально-поршневого насоса НАМ с электромагнитным механизмом изменения подачи
Давление на выходе МПа:
Частота вращения вала обс (обмин)
номинальная 25 (1500)
максимальная25 (1500)
Номинальная подача дм3мин57
Номинальная потребляемая мощность кВт25
КПД насоса не менее083
По технической характеристике выбранного насоса производится уточнение действительной подачи насоса по формуле
Qнд=gндnндоб (2.5.5)
где gнд – действительный рабочий объем насоса дм3 gнд = 0045 дм3;
nнд – действительная частота вращения вала насоса обс nнд = 25 обс;
об – КПД насоса об = 083.
5.3 Определение внутреннего диаметра гидролиний скоростей движения жидкости
Расчетные значения внутренних диаметров всасывающей напорной и сливной гидролинии определяют из уравнения неразрывности потока жидкости
где Qнд - действительный расход жидкости дм3с Qнд = 093 дм3с;
- скорость движения жидкости в гидролинии мс.
Скорости движения жидкости выбираются из литературы : вс = 12 мс; нап = 5 мс; сл = 2 мс.
По ГОСТу 8734-75 выбираются стандартные значения внутренних диаметров гидролиний при толщине стенки 3мм: dвс = 32 мм; dнап = 16 мм; dсл = 26мм.
Действительные скорости движения жидкости во всасывающей напорной и сливной гидролиниях определяются по формуле
d - действительное значение внутреннего диаметра гидролинии м dвс = 0032 м; dнап = 0016 м; dсл = 0026 м.
5.4 Выбор гидроаппаратуры и кондиционеров рабочей жидкости.
Гидроаппаратуру выбирают по условному проходу и номинальному давлению.
dу вс=32мм; dу нап= 16 мм; dу сл=25 мм.
Гидроаппаратуру выбирают из литературы
Техническая характеристика секционного гидрораспределителя
Условный проход мм25
Расход рабочей жидкости дм3мин:
Максимальное усилие для перемещения золотника
из нейтральной позиции в рабочие при номиналь-
ных давлении и расходе Н400
Давление в сливной гидролинии МПа не более08
Обратный клапан типа 61200
Номинальный расход дм3мин200
Техническая характеристика линейного фильтра типа 1.2.40-25
Номинальный расход дм3мин160
Номинальная тонкость фильтрации мкм25
Номинальное давление МПа 063
Ресурс работы фильтро-элемента до замены или
Масса сухого фильтра кг82
Рабочая жидкость МГ-30 у
кинематический коэффициент вязкости мм2с25
5.5 Расчет потерь давления в гидролиниях
Потери давления определяются отдельно для каждой гидролинии при определенной температуре рабочей жидкости по формуле
где - сумма путевых потерь МПа;
- сумма потерь в местных сопротивлениях МПа;
Потери давления по длине гидролинии
где - коэффициент путевых потерь (коэффициент Дарси);
- длина гидролинии м;
d - внутренний диаметр гидролинии м;
- скорость движения жидкости мс;
- плотность рабочей жидкости кгсм3 = 890 кгсм3.
При подстановке в формулу (2.5.9) длины гидролинии l следует учитывать что для всасывающей гидролинии l = lвс для напорной гидролинии l = lнап + lисп а для сливной гидролинии l = lсл + lисп.
Коэффициент путевых потерь:
для турбулентного режима (Rе > 2320)
для ламинарного режима (Rе 2320)
где - скорость движения жидкости в гидролинии мс вс = 116 мс; нап = 463 мс; сл = 175 мс;
d - внутренний диаметр гидролинии м dвс = 0032 м; dнап = 0016 м; dсл = 0026 м.;
- кинематический коэффициент вязкости рабочей жидкости м2с = 25106 м2с.
Потери давления в местном сопротивлении
где - коэффициент местного сопротивления;
- скорость движения жидкости мс вс = 116 мс; нап = 463 мс; сл = 175 мс;
Местные сопротивления
а) сверленый угольник2
б) присоединительный штуцер01 015
г) угольник с поворотом на 90015 2
Потери давления в гидролиниях
5.6 Тепловой расчет гидропривода
Тепловой расчет гидропривода производится с целью определения температуры рабочей жидкости объема гидробака и выяснения необходимости применения специальных теплообменных устройств.
Количество тепла выделяемое в гидроприводе в единицу времени эквивалентно теряемой в гидроприводе мощности.
Тепловой расчет гидропривода ведется на основе уравнения теплового баланса
Qвыд = Qотв (2.5.14)
где Qвыд - количество тепла выделяемого гидроприводом в единицу времени Вт;
Qотв - количество тепла отводимого в единицу времени Вт.
Количество выделяемого тепла определяется по формуле
где Pном- номинальное давление Па Pном = 32 МПа;
Qнд- действительная подача насоса м3с Qнд = 09510-3 м3с;
- полный КПД насоса = 083;
- гидромеханический КПД гидропривода;
- коэффициент продолжительности работы;
- коэффициент использования номинального давления.
Гидромеханический КПД гидропривода определяется по формуле
где - гидромеханические КПД насоса
- гидравлический КПД гидропривода учитывающий потери давления в гидролиниях.
Гидравлический КПД гидропривода равен
где Pном - номинальное давление МПа Pном = 32 МПа;
- потери давления в напорной сливной и всасывающей гидролиниях соответственно МПа = 1968 МПа = 01783 МПа = 001132 МПа.
Следует отметить что в технических характеристиках насосов и гидромоторов обычно приводят значения полного и объемного КПД. Поэтому гидромеханический КПД определяют из выражения для полного КПД гидромашины
где н – полный КПД насоса (или гидромотора);
гн - гидравлический КПД;
мн - механический КПД;
гмн - гидромеханический КПД.
Количество тепла отводимого в единицу времени определяется по формуле
где - коэффициент теплопередачи от рабочей жидкости в окружающий воздух Вт(м2·град) = 12 Вт(м2·град);
tж - установившаяся температура рабочей жидкости 0С tж60 70 0С;
t0 - температура окружающего воздуха 0С t0 = 10 0С;
- суммарная площадь наружной теплоотводящей поверхности трубопроводов м2 Sr -толщина стенки; - длина
SБ - площадь поверхности гидробака м2.
Srвс = 314·(0032+2·0003)·21 = 0251 м2
Srнап = 314·(0016+2·0003)·708 = 4891 м2
Srслив = 314·(0026+2·0003)·729 = 6638 м2
Площадь поверхности бака
Объем гидробака рассчитывается по формуле
где SБ - площадь поверхности гидробака м2 SБ = 32 м2;
V - объем гидробака дм3.
Из формулы (2.5.20) выводим объем гидробака
Так как объем превышает 08 30 минутной подачи насоса следовательно необходимо установить теплообменник.
В данном разделе был осуществлен выбор гидродвигателя фрезерных роторов и вспомогательной лебедки и рассчитаны их основных параметры также выбран гидроцилиндр наклона стрелы и произведен расчет гидросистемы. Исходя из полученных данных был выбран лопастной гидромотор HVK-A F2-7317 для фрезерных роторов аксиально-поршневой гидромотор Г15-25Р для вспомогательной лебедки и гидроцилиндр наклона с проушинами с обеих сторон со сферическими подшипниками ГЦС 250х180-2500-06-С-0-0.
Организации которые имеют на балансе машины должны осуществлять проведение ТО и ремонта в соответствии с утвержденными месячными и годовыми планами.
Ремонтные работы и работы по ТО должны быть выполнены в соответствии с требованиями Технического описания и инструкции по эксплуатации ДСМ завода изготовителя.
Инженерно-технологическая подготовка к работам по ТО и ремонту должна быть заранее организованной. Это позволит выполнять ТО и ремонт в указанные сроки и качественно.
В данную подготовку входят:
обеспечение материально-технической базой и ремонтно-эксплуатационными материалами;
оснащение технологических процессов ТО и ремонта специальным оборудованием оснасткой и инструментом для механизации работ;
подготовку и повышение квалификации машинистов и рабочих связанных с проведением работ по ТО и ремонту;
обеспечение эксплуатационной и ремонтной документацией;
контроль качества выполняемых работ по ТО и ремонту.
ТО и ремонт ДСМ должен быть выполнен в соответствии со сроком поставленным месячным планом-графиком который согласован с организацией использующей машины. Согласование проводится не менее чем за три дня до начала планируемого месяца.
План-график ТО и ремонта может быть изменен в течение месяца с учётом фактической наработки только с согласия организаций на балансе которой имеются машины и в эксплуатации которой они находятся.
1 Исходные данные для расчета проведения ТО и Р
Необходимые данные для расчёта числа ТО и Р на текущий год составления плана ТО и ремонта на год а также трудоёмкости ТО и Р для модернизируемого экскаватора занесены в таблицу 3.1.1
Таблица 3.1.1 – Периодичность выполнения ТО и Р
Экскаватор JINT SH-36W
В таблице 3.1.1 приведены данные необходимые для определения дней постановки на ТО и Р в выбранный месяц. Показано сколько отработано мото-часов после проведения последнего номерного ТО.
Таблица 3.1.2 – Количество отработанных мото-часов экскаватором
Услов. экспл. (зона)
Плани-руемая нара-ботка мото.-ч
Отработано мото.-ч с начала эксплуатации после выполнения ТО и Р
Наработка модернизируемого экскаватора на планируемый год с учётом V-ой зоны эксплуатации составит 1800 мото-часов (согласно данным МДС 81-3.99) общая наработка экскаватора на начало текущего года составляет 3570 мото-часов.
2 Планирование ТО и Р экскаватора на текущий год
2.1 Расчет числа ТО и Р экскаватора на текущий год
Количество ТО и Р каждого вида N которые должны быть проведены в планируемом году для рассматриваемого ЭО определяется по формуле
где – величина фактической наработки машины на начало планируемого года со времени проведения последнего аналогичного расчетному вида ТО и ремонта или с начала эксплуатации ч;
– планируемая наработка на расчетный год ч;
– периодичность выполнения соответствующего вида ТО и ремонта по которому ведется расчет ч;
– число всех видов ТО и ремонта с периодичностью большей периодичности того вида по которому ведется расчет (при расчете капитального ремонта = 0)
Расчеты по формуле (3.2.1) должны производиться в следующей последовательности: капитальный ремонт текущий ремонт плановые технические обслуживания (ТО-2 ТО-1).
Результаты расчета по формуле (3.2.1) следует округлять до целых чисел в меньшую сторону.
Расчёт для модернизируемого экскаватора:
принимаем как 0 в планируемом году капитальный ремонт проводится не будет;
принимаем как 2 в планируемом году будет проведено два текущих ремонта;
принимаем как 5 в планируемом году будет проведено пять раз ТО-2;
принимаем как 29 в планируемом году будет проведено 29 раз ТО-1.
Полученные данные заносим в таблицу 3.2.3.
Таблица 3.2.1 – Количество проводимых ТО и Р
Число ТО и ремонтов в планируемом году
3 Планирование ТО и Р экскаватора на выбранный месяц
3.1 Расчет числа месяца по видам ТО и Р для экскаватора на июль 2015 г
Исходные данные берём из таблиц 3.1.1 и 3.1.2. Месячным планом–графиком ТО и Р экскаватора устанавливается дата остановки на техническое обслуживание или ремонт и продолжительность его простоя в днях. Число рабочего дня месяца в который начинается проведение ТО или ремонта машин определяется по формуле
где количество рабочих дней в планируемом месяце с учетом условий организации труда на данном предприятии;
планируемая наработка на расчетный месяц мото-часы.
Если при расчёте формулы (3.1.2) величина окажется большей чем число рабочих дней в планируемом месяце то данный вид ТО или ремонт в этом месяце проводиться не будет.
Для определения календарного числа месяца в которое должен начинаться ТО или ремонт необходимо к полученному числу рабочих дней месяца рассчитанному по формуле (3.3.1) добавить число календарных выходных дней приходящихся на найденное количество рабочих дней.
Проводим расчёты для модернизируемого экскаватора:
на планируемый месяц ТР не выпадает;
б) техническое обслуживание № 2
ТО-2 выпадает на 21 рабочий день июля (25 июля по календарю);
в) техническое обслуживание № 1
ТО-1 выпадает на 6 рабочий день июля (8 июля по календарю).
Учитывая периодичность проведения ТО-1 в 50 мото-часов определим другие дни месяца постановки на указанное профилактическое мероприятие.
выпадает на 13 рабочий день июля (16 июля по календарю).
выпадает на 20 рабочий день июля (25 июля по календарю).
Полученные значения заносим в таблицу 3.3.1.
Таблица 3.3.1 – План-график ТО и Р экскаватора на выбранный месяц
Число месяца проведения ТО и Р
4. Технологическая карта смазки и заправки узлов экскаватора и рабочего оборудования
Технологическая карта смазки и заправки включает в себя все необходимые этапы для проведения ежесменного профилактического мероприятия (рисунок. 3.4.1).
Рисунок 3.4.1 – Схема точек смазывания и заправок ЭО и навесного рабочего оборудования
Работы связанные с обслуживанием навесного оборудования требуют дополнительных трудозатрат оператора экскаватора. Смазка направляющих подвижного кронштейна смазка и заправка подшипников лебедки вращения блоков позволят сохранить высокую производительность навесного оборудования и предотвратить преждевременные поломки.
Таблица 3.4.1 – Операционно-технологическая карта смазки и заправки
5. Расчет трудоёмкости номерных видов ТО и Р для экскаватора
Расчет трудоёмкости производится по следующей формуле:
где kI – количество машин kI = 1;
PI – количество проводимых ТО и Р;
tI – единичная трудоемкость выполнения ТО и Р чел.-час.
Расчет трудоёмкости для модернизированного экскаватора
а) трудоемкость текущего ремонта
б) трудоемкость ТО-2
в) трудоемкость ТО-1
Для остальных машин расчет аналогичный. Данные расчета занесены в таблицу 3.5.1.
Таблица 3.5.1 – Трудоемкость выполнения ТО и Р для экскаватора
Трудоемкость выполнения ТО и Р чел.-ч.
Общая трудоёмкость производимых работ по видам машин чел.- ч.
Общая трудоемкость % (100 %)
6 Расчет численности производственных рабочих
Определение штатного (списочного) количества производственных рабочих
где ТГ – общая трудоёмкость производимых работ по видам машин чел.- ч ТГ = 557 чел.- ч
ФДР – действительный годовой фонд времени рабочего ч;
где Дотп – количество дней отпуска Дотп=28 дней;
Дб – количество дней по болезни Дб=6 дней;
Дго – государственная обязанность Дго=3 дня.
Численность вспомогательных рабочих принимаем в размере 20% численности производственных рабочих
где РШ – штатное количество производственных рабочих РШ = 1 чел.
Численность инженерно-технических работников составляет 15% от численности производственных и вспомогательных рабочих
РВС – штатное количество вспомогательных рабочих РВС = 1 чел.
7 Расчет количества постов ТО и Р
λ – интенсивность потока λ = 01 для экскаватора JINT-36W;
– коэффициент учитывающий уровень использования рабочего времени поста =085-09;
Исходя из полученных данных принимаем 1 пост.
8 Расчет энергетики отделения
Расчет отопления отделения
где VП – объем помещения занимаемого отделением м3;
qО – удельный расход тепла на отопление при разности наружной и внутренней температуры в 1 оС qО =045-055ккал(чм3оС);
qВ – удельный расход тепла на вентиляцию при разности наружной и внутренней температуры в 1 оС qВ =015-025ккал(чм3оС);
tВ – внутренняя температура помещения для шиномонтажного отделения tВ = +20 оС;
tМ – минимальная наружная температура воздуха во время отопительного сезона tМ = - 30оС.
Определение площади нагревательных приборов
kt – коэффициент теплопередачи kt = 74 ккал(чм3оС);
t’cр – средняя расчетная температура воды в системе отопления t’ cр= +80 оС.
Определение количества нагревательных приборов
где FНП – площади нагревательных приборов м2 FНП =662 м2;
FП – площадь поверхности нагревательного прибора м2 FП = 18 м2.
Расчет энергетики для зоны ТО и Р
где – площадь зоны ТО и Р м2; = 8072 м2;
– годовое количество часов искусственного освещения для работы в одну смену = 400 ч;
– удельная мощность освещения =0015–002 кВтм2;
kсп – коэффициент спроса =08.
Расчет расхода силовой электроэнергии
где – суммарная мощность оборудования кВт;
kсп – коэффициент спроса =015-02;
kз – коэффициент загрузки оборудования kз = 075-082.
ФДО – действительный годовой фонд отделения ФДО =163344 ч.
Расчет расхода сжатого воздуха
где – удельный расход сжатого воздуха м3мин.
где – минутное потребление сжатого воздуха оборудованием для пневмо -инструмента =06 м3мин;
– коэффициент спроса для пневмо–инструмента = 02 04;
- количество потребителей сжатого воздуха в отделении n = 2.
9 Расчет площади зоны ТО
Для тупиковых параллельных постов в один ряд без проезда площадь зоны определяют по формуле
где ПЗ – количество постов находящихся в зоне ПЗ =1 пост;
SМ – площадь одной машины в плане м2; SМ = 3243 м2
fМ – площадь рабочих мест организуемых для одного рабочего поста м2; fМ = 60 – 80 м2.
10 Выбор основного технологического оборудования и инвентаря для зоны ТО и Р модернизируемого экскаватора
Необходимо предусмотреть что бы были: местные отводы выхлопных газов средство механизации установки машин на посты в зоне ремонта что бы были установлены кран-балка или мостовые краны. Обязательно при проведении ТО и Р должны быть устройства для сбора масел должна быть всегда в запасе дистиллированная вода для АБ.
Ларь для использованных фильтров грубой очистки топлива масляных центрифуг фильтров турбокомпрессора сапунов двигателя или специальные ёмкости для промывки фильтров и др. оборудования. Бак для сбора отработавшего масла с габаритными размерами 800х600.
Шкаф для зарядки АКБ типа 2268 ванна для слива или приготовления электролита 2252.
Необходимый перечень оборудования для проведения ТО и Р модернизируемого экскаватора JINT SH-36W приведен в таблице 3.10.1
Таблица 3.10.1 - Перечень основного оборудования и инвентаря для зоны ТО и Р
Наименование оборудования
Шкаф инструментальный
Противопожарный инвентарь
продолжение таблицы 3.9.1
Смазачно-заправочная установка
Система сбора отработавших масел
Установка для промывки фильтров
Компрессорная установка
Модернизированный экскаватор незаменим при выполнении запланированной технологической операции он обеспечивает высокую производительность безопасность и высокий процент работоспособности. Все это достигается при небольшом износе. В случае большого процента износа происходят частые поломки увеличиваются простои и все это влечет к большим материальным затратам.
Износ определяется соотношением фактической наработки машины с момента проведения капитального ремонта к периодичности выполнения капитального ремонта. Для модернизированного экскаватора это показатель будет равен – 562 %. По процентному износу экскаватора можно сделать вывод о том что он немного изношен что в свою очередь может приводить к появлению и выполнению неплановых ТО и Р.
На выбранный месяц будет приходится 3 технических воздействия на 23 рабочих дня что говорит о небольшой загрузке рабочего персонала. Наибольшей трудоёмкостью выполнения среди профилактических мероприятий будет приходится на текущий ремонт в связи с наибольшей энергоемкостью выполнения и затратами обслуживающих рабочих.
Также в данном разделе приведены данные по расчёту зоны ТО и Р для модернизируемого экскаватора. Определено количество рабочих количество постов требуемое годовое количество сжатого воздуха и электроэнергии затраты на освещение и обогрев помещения. Было определено и выбрано необходимое оборудование для проведения качественного ТО и Р.
БЕЗОПАСНОСТЬ ЖИЗНЕДЕЯТЕЛЬНОСТИ
Создание более благоприятных условий для улучшения санитарно- гигиенических условий деятельности – это одно из важнейших задач экологического и социального развития при улучшении условий труда человека оператора станочника машиниста водителя и т.д. Огромную роль играет защита рабочей зоны от вредных для человека воздействий внешней среды и работающего оборудования. Воздействие неблагоприятных факторов на человека его организм приводит к нарушению функции жизнедеятельности организма человека ухудшению здоровья на его работоспособность и на производительность машины в целом. На оператора экскаватора влияют также такие вредные факторы как ухудшение микроклимата шум вибрация.
Земляные работы являются весьма трудоемким процессом и безопасность их выполнения во многом зависит от вида и способов их производства условий рельефа местности рода грунта и вида сооружений. Грунты в зависимости от структуры подразделяются на связные в которых кроме сил трения существуют силы сцепления между частицами и несвязные в которых отсутствуют указанные факторы и создается потенциальная опасность заключающаяся в возможности обрушения грунта в процессе его разработки или при выполнении последующих видов работ. К первой группе относятся глинистые суглинистые а ко второй - песчаные гравелистые и насыпные а также лессовидные грунты которые обладают высокой прочностью в сухом состоянии но при замачивании теряют связность между частицами и незакрепленные стенки траншей и котлованов в таких грунтах обрушиваются. Могут быть случаи обрушения мерзлых грунтов которые при отрицательных температурах имеют достаточную прочность чтобы держаться в вертикальных стенках но при переменной температуре и оттепелях теряют ее в них появляются трещины в результате чего незакрепленные вертикальные стенки и крутые откосы также обрушиваются.
Анализ фактических материалов последних лет по производственному травматизму показывает что около 10% всех несчастных случаев с тяжелыми исходами связано с выполнением земляных работ. Основные причины несчастных случаев:
отсутствие или недостаточное крепление грунта;
превышение критической высоты разработки грунта без крепления;
нарушение правил разборки креплений.
Другие причины травматизма при производстве земляных работ:
скатывание по откосу кусков грунта или камней на работающих в котлованах и траншеях;
движение транспортных средств и механизмов в пределах призмы обрушения;
несоблюдение безопасных способов погрузки грунта в транспортные средства;
недостаточный надзор за безопасным состоянием забоя особенно в туман и ночное время;
возможные падения людей по откосу в зимнее время вследствие его обледенения.
Микроклимат кабины оператора экскаватора определяется комплексом физических параметров которые определяют тепловой обмен на рабочем месте между оператором и внешней средой. Параметры микроклимата нормированы по ГОСТ 12.1.005-88 «Воздух рабочей зоны. Общие требования» и ГОСТ 12.1.011 -75 «Машины строительные и дорожные».
Микроклимат кабины оператора экскаватора определяется действующими на организм человека факторами: температура влажность скорость движения воздуха и температура окружающих человека поверхностей.
Микроклимат кабины оператора должен обеспечивать нормальный уровень теплообмена организма человека со средой комфортные теплоощущения высокую работоспособность труда повышать устойчивость организма.
Нормализация микроклимата кабины осуществляется за счет процессов отопления вентиляции и кондиционирования воздуха.
Оптимальные микроклиматические условия характеризуются сочетанием параметров микроклимата который при деятельном систематическом воздействии на человека обеспечивает сохранение нормального функционирования и теплового состояния организма.
При изменении физического состояния воздуха то есть при метеорологических колебаниях состояние человека так же изменяется. Как известно для каждой температуры воздуха имеется свой предел содержания водяных паров называемой абсолютной влажностью воздуха. Кроме того воздух характеризуется относительной влажностью %. Высокий уровень насыщенности воздуха водяными парами отрицательно действует на организм человека. С другой стороны понижая влажность вызывает сухость оболочек дыхательных путей.
При высокой температуре окружающей среды отдача тепла теплом затрудняется. В этом случае теплоотдача идёт путём выделения пота что отрицательно влияет на состав крови в связи с уменьшением количества солей в организме. При длительном воздействии высокой температуры отдача тепла телом практически прекращается: при перегреве организма нарушается деятельность нервных центров и может произойти солнечный удар.
Инфразвук возникает при работе дизельных и реактивных двигателей компрессоров и вентиляторов. В обычном понимании орган слуха оператора буровой установки не воспринимает инфразвук. Особенностью действия инфразвука является высокая специфическая чувствительность органов слуха к низкочастотным колебаниям. Инфразвук с частотой 7 Гц совпадает с а - ритмом биотоков мозга поэтому эта частота наиболее опасна.
Кроме того инфразвук воспринимается поверхностью тела. Шум (слышимый звук) возникает при работе экскаваторов бульдозеров тракторов и других строительных машин.
Совокупность слышимых звуков сочетание множества различных тонов и частот с беспорядочной интенсивностью называют шумом. Но под шумом понимают также всякие нежелательные для оператора экскаватора звук мешающий восприятию необходимых звуков или нарушающий тишину.
Таблица 4.1 — Допустимые уровни звукового давления дБ.
Допустимые уровни звукового давления дБ в октавных полосах со среднегеометрическими частотами Гц
Длительные воздействия громкого шума на буровой установки ведет к снижению производительности труда на 10-60 %. Громкий звук влияет не только на слух. Он приводит к нарушению деятельности центральной нервной системы сердечно-сосудистой системы повышенной утомляемости ослабления внимания памяти происходит изменение кожной чувствительности.
Допустимые уровни шума на рабочих местах регламентированы ГОСТ 12. 1.003-88 «Шум. Общие требования безопасности».
В экскаваторах с навесным оборудованием основным источником шума является двигатель внутреннего сгорания. Уровень шума от отдельных элементов строительных машин меньше уровня шума от двигателя. Основным источником шума экскаватора являются вентилятор системы охлаждения системы впуска и выпуска двигатель (механизм газораспределения процесс сжатия кривошипно-шатунный механизм) силовая установка.
Средствами индивидуальной защиты от шума являются ушные вкладыши
наушники и шлемофоны. Эффективность индивидуальных средств защиты зависит от используемых материалов конструкции силы прижатия правильности ношения. Ушные вкладыши вставляют в слуховой канал уха. Их изготавливают из лёгкого каучука эластичных пластмасс резины эбонита н ультратонкого волокна. Они позволяют снизить уровень звукового давления на 10 15 дБ. В условиях повышенного шума рекомендуется применять наушники которые обеспечивают надёжную защиту органов слуха. Для предохранения от воздействия шума с общим уровнем 120 дБ н выше рекомендуется применять шлемофоны которые герметично закрывают всю околоушную область и снижают уровень звукового давления на 30 40 дБ в диапазоне частот 125 8000 Гц. Классификация средств и методов зашиты от шума установлены ГОСТом 12.1.029 - 80 «Средства и методы зашиты от шума».
Звукоизоляцию шумных узлов рассматриваемой техники обеспечивают с помощью звукоизолирующих кожухов для двигателей звукоизолирующий капот. Для глушения шума возникающего в системе впуска и выпуска при работе двигателя внутреннего сгорания устанавливают глушители. В самоходных машинах одновременно тепло и звукоизоляционным устройством служит кабина. Так же применяют средства индивидуальной защиты от шума. Классификация средств индивидуальной защиты работающих изложена в ГОСТ 12.4.011 - 75 «Средства защиты работающих».
Различают общую и локальную вибрацию. Общая вибрация вызывает сотрясения всего организма местная вовлекает в колебательное движение отдельные части тела (у работающих с ручным механизированным инструментом).
Общие вибрации с частотой менее 07 Гц (качка) хотя и неприятна но не приводит к вибрационной болезни. Колебания с частотой 5 7 Гц вызывают расстройства вследствие резонансных колебаний головы желудка кишечника в конечном счете всего тела. При колебаниях с частотой 11 45 Гц ухудшается зрение возникает тошнота нарушается нормальная деятельность других органов. Колебания с частотой больше 45 Гц вызывают повреждения сосудов головного мозга; происходит расстройство циркуляции крови и высшей нервной деятельности с последующим развитием вибрационной болезни.
Степень вредного воздействия колебаний на организм человека зависит от частоты продолжительности и действия вибрации. Для экскаватора характерен случай передачи вибрации телу человека через сидение от неровностей дороги и неуравновешенности двигателя.
Различают санитарно-гигиеническое и техническое нормирование вибрации. В первом случае обеспечиваются нормальные условия с точки зрения защиты от вибрации человека во втором – машин и оборудования. Действующие гигиенические оценки вибрации изложены в ГОСТ 12.1.012- 78.
Нормируемым параметром при частотном анализе являются средние квадратические значения виброскорости (их логарифмические уровни) или виброускорение для локальной вибрации в активных полосах частот а для общей вибрации в октавных 13 октавных полосах частот.
Под вибрационной защитой имеют в виду совокупность средств и методов уменьшения вибрации воспринимаемой защищаемыми объектами. Под уменьшением вибрации понимают уменьшение каких-либо определенных величин характеризующих вибрацию.
Методы и средства вибрационной защиты изложены в ГОСТ 12.1.012- 90. Методы виброзащиты: по виду реализации снижающие передачу вибрации при контакте оператора с вибрирующим объектом (использование дополнительных устройств встраиваемых в конструкцию машины демпфирующие покрытия); по принципу действия (виброизоляция динамическое виброгашение); по использованию дополнительного источника энергии (активная виброизоляция) пассивное и активное динамическое виброгашение.
В практике на дорожно-строительных предприятиях применяют следующие виды инструктажа: вводный или предварительный инструктаж; инструктаж на рабочем месте; повторный инструктаж.
Вводный инструктаж проводится до момента допуска рабочего к работе инженером по технике безопасности или главным инженером. Рабочий не прошедший вводного инструктажа к работе не допускается.
В процессе вводного инструктажа рабочему сообщают сведения о правилах внутреннего трудового распорядка дисциплине в бригаде во время работы и в нерабочее время на территории строительства или предприятия о сигналах предупредительных надписях и плакатах по технике безопасности; о порядке пользование спецодеждой инвентарными защитными приспособлениями; об устройстве защитных при механизмах и оборудовании и порядке обращения с ними; о требованиях техники безопасности при работе с ручным и механизированным инструментом; об основных требованиях электробезопасности. Во время вводного инструктажа разбирают характерные несчастные случаи имеющее место на таких работах какие будет выполнять рабочий рассказывают о способах оказания первой помощи пострадавшим о порядке регистрации и расследования несчастных случаев.
Продолжительность вводного инструктажа 2-4 часа. Проводить инструктаж следует в специально отведённом месте оборудованном необходимыми плакатами таблицами и другими наглядными пособиями. На крупных объектах необходимо организовывать кабинет по технике безопасности. Проведённый инструктаж оформляется документом.
Инструктаж на рабочем месте проводится примерно по тому же плану что и вводный инструктаж отличаясь от него тем что все вопросы рассматриваются применительно к данному рабочему месту. Рабочий знакомиться с технологическим процессом и обстановкой на данном рабочем месте. Ему демонстрируют безопасные методы работы и примеры пользования защитными приспособлениями. Инструктаж на рабочем месте проводится техническим руководителем работ в непосредственном распоряжении которого находиться рабочий его продолжительность составляет 4-6 часов.
В обязанности технического руководителя входит постоянное консультирование рабочего по охране труда и безопасным приёмам работы. При переводе на работу иного вида рабочий проходит новый инструктаж на новом рабочем месте. При переводе на работу по другой специальности рабочий обязан заново пройти вводный инструктаж.
При повторном инструктаже внимание рабочего обращают на изменения происшедшие в технологическом процессе разбираются допущенные нарушения техники безопасности и их результаты. Необходимо указать на положительные и отрицательные факторы при организации рабочих мест.
Все инженерно-технические работники ежегодно в порядке технического обучения или специально организованных занятий изучают правила техники безопасности производственной санитарии Противопожарной безопасности и трудовое законодательство.
4 Выбор каната по разрывному усилию
Определяем максимальное натяжение каната наматываемого на барабан вспомогательной лебедки по следующей формуле
Принимаем максимальную массу поднятия груза с помощью вспомогательной лебедки – 7500 кг
Q – сила тяжести поднимаемого груза Q = 7500 Н;
g – ускорение свободного падения g= 98 мс;
а – число ветвей ведущих к источнику усилия а = 1;
Uп – кратность полиспаста U= 1;
б – коэффициент полезного действия барабана п= 095.
Определяем разрывное усилие каната по следующей формуле
где Spaз – разрывное усилие каната Н;
k – наименьший допускаемый коэффициент запаса прочности k = 5.
Выбираем канат двойной свивки типа ЛК - Р 6x19 проволок с одним органическим сердечником (рисунок 4.4.1) ГОСТ 2688 – 80. Основные параметры для данного типа каната приведены в таблице 4.1.
Рисунок 4.1 – Канат двойной свивки типа ЛК - Р 6x19.
Таблица 4.1 – Основные параметры каната
Расчётная площадь сечения всех проволок
Ориентировочная масса 1000 м смазанного каната кг
Маркировочная группа МПа
Разрывное усилие каната в целом Н
В данном разделе был произведен расчет каната по разрывному усилию. В результате расчета максимальное натяжение каната наматываемого на барабан вспомогательной лебедки составило 193 кН а разрывное усилие составило 967 кН. Исходя из данных полученных при расчете был выбран канат двойной свивки типа ЛК - Р 6x19 который будет обеспечивать безопасные условия работы.
ЭКОНОМИЧЕСКИЙ РАЗДЕЛ
В качестве основной машины используется установка для разработки скважины с помощью гидравлических роторов. Применив данную установку мы сможем значительно уменьшить затраты и время на разработку буроввых скважин.
Для сопоставления вариантов конструктивных решений технического объекта на стадии научных исследований проектирования применяется метод сравнительной эффективности в котором оценка осуществляется по разности текущих и разности капитальных затрат.
Эффективность использования машины характеризуется соотношением затрат и полученных с их помощью результатов.
Источником информации при расчете экономической эффективности являются различные нормативы методические и другие документы.
Текущие затраты на выполнение технологических процессов с использованием базисной и новой техники включают следующие статьи: основная заработная рабочим затраты на выполнение ТО и ТР отчисления на амортизацию средств механизации затраты на энергоносители затраты на смазочные материалы рабочую жидкость для гидросистем на перебазировку машины.
Задачей данного раздела является определение экономического эффекта установки для разработки скважины с помощью гидравлических роторов.
1 Выбор базисного варианта
В качестве базисного варианта принимается буровую установку на базе экскаватора на гусеничном ходу с устройством для разработки скважины с помощью шнека и буровой головки который позволяет осуществлять разработку скважины с производительностью 3262 м3ч.
Целью создания нового сменного оборудования для экскаватора является разработка скважины для создания пускового котлована методом «стена в грунте» тем самым улучшение технико-эксплутационных показателей разработки скважины.
2 Определение годовой эксплуатационной производительности
Годовую эксплуатационную производительность буровой установки с гидравлическими фрезами определяем по формуле:
где Пэч – эксплуатационная среднечасовая производительность буровой установки м3ч;
Тг – количество машино-часов работы экскаватора в году маш.-чгод.
Количество машино-часов работы буровой установки в году определяем по формуле:
где Тф – годовой фонд рабочего времени экскаватора дни Тф = 247 дней;
Тсо – продолжительность сезонного обслуживания дни Тсо = 1 день;
Др – простои во всех видах ремонтов и технических обслуживаний днимаш.-ч;
dп – продолжительность одной перебазировки дни;
Тоб – время работы на объекте маш.-ч Тоб = 200 600 маш.-ч принимаем Тоб = 200 маш.-ч;
kсм – коэффициент сменности принимаем kсм = 15;
tсм – продолжительность рабочей смены маш.-ч принимаем tсм = 767 маш.-ч.
Продолжительность одной перебазировки dп определяем по формуле
где Lт – среднее расстояние перебазировки км принимаем Lт = 25 км;
Vтер – средняя скорость переезда кмч принимаем Vтер = 10 кмч;
tп – средняя продолжительность погрузки перевозимого экскаватора на автотранспорт и её разгрузки маш.-ч принимаем tп = 1 маш.-ч.
Простои во всех видах ремонтов и технических обслуживаний определяем по формуле
где rудТО – удельная оперативная трудоемкость ТО чел-чмоточас принимаем rудТО = 014 чел-чмото-час;
kов – коэффициент перевода оперативного времени в общее время работы kов = 25;
Б – число рабочих осуществляющих ТО чел Б = 2 чел;
dтр dкр – продолжительность пребывания экскаватора в текущем и капитальном ремонте дни dтр = 9 дней dкр = 20 дней;
атр – количество текущих ремонтов в межремонтном цикле;
Тотк – наработка на отказ мото-час Тотк = 126 мото-час;
tотк – среднее время на устранение одного отказа маш.-час;
kч – коэффициент перевода мото-час в машино-часы принимаем kч = 045;
Тр – средний ресурс до капитального ремонта мотто-час.
где – гамма–процентный ресурс мото-час принимаем = 11300 мото-час;
- коэффициент перевода гамма–процентного в средний ресурс =12.
Количество текущих ремонтов в межремонтном цикле определяем по формуле
где tтр – периодичность текущего ремонта мото-час tтр = 960 мото-часов.
Среднее время на устранение одного отказа tотк определяем по формуле
где – коэффициент перевода гамма-процентного в средний ресурс =12;
Тотк – наработка на отказ мото-час Тотк = 126 мото-часов;
kов – коэффициент перевода оперативного времени в общее время работы kов = 25.
Определим количество машино-часов работы экскаватора в году
Эксплуатационную среднечасовую производительность буровой установки определяем по формуле
где Птч – техническая производительность м3ч;
kт – коэффициент перехода от технической производительности к эксплуатационной kт = 04.
Техническая производительность буровой установки зависит от объема грунта в разрабатываемой скважине.
где D – диаметр скважины разрабатываемой базисной машиной м D = 05 м;
h – глубина скважины м h = 20 м;
Z –количество скважин которое разрабатывает буровая установка Z = 831;
a – ширина роторов новой машины м a =25 м
b – захват роторов новой машины м b = 09 м.
Годовая эксплуатационная производительность буровой установки П равна
3 Определение годовых текущих издержек потребителя
Годовые текущие издержки потребителя при использовании буровой установки с гидравлическими роторами
C= Нр(Са + Ср + Скр + Сз + Сзт + Ссм + Сгид + Спб) (5.3.1)
где Са– амортизационные отчисления на реновацию руб.;
Ср– затраты на выполнение текущих неплановых ремонтов и технических обслуживаний руб.;
Скр – затраты на выполнение капитальных ремонтов руб.;
Сз– заработная плата рабочих управляющих техникой руб.;
Сзт – затраты энергоносителей руб.;
Ссм – затраты на смазочные материалы руб.;
Сгид – затраты на гидравлическую жидкость руб.;
Спб – затраты на перебазировки руб.;
Нр – норма накладных расходов связанных с эксплуатацией строительных и дорожных машин Нр = 21%.
3.1 Амортизационные отчисления на реновацию
Амортизационные отчисления на реновацию определяются по формуле
где На – норма амортизационных отчислений на реновацию % Ha = 12 %;
К – капитальные вложения потребителя связанные с приобретением буровой установки его первоначальной доставкой и монтажом определяется по формуле
где Кд – коэффициент перехода от цены к балансовой стоимости Кп = 109;
Ц – цена техники руб. определяем по формуле
где – цена базисной машины руб. К1= 6000000 руб.
Кдоп – стоимость рабочего органа руб.
Наименование и цену расходных материалов которые требуются для сооружения устройства уплотнения сводим в таблицу 5.3.1
Таблица 5.3.1 – Наименование и цена расходных материалов
Лист металла. S=1 м2
Труба ø80 мм; =40мм.
Труба ø70 мм; =110мм.
Амортизационные отчисления на реновацию для базисной техники
Амортизационные отчисления на реновацию для новой техники
3.2 Затраты на выполнение текущих неплановых ремонтов и технических обслуживаний
Затраты на выполнение текущих внеплановых ремонтов и технических обслуживаний определяется по формуле
где Тг – количество машино-часов работы техники в году маш-чгод определяется по формуле
где Тс – число календарных дней в году Тс = 365 дней;
Dв – количество выходных и праздничных дней Dв = 104+11=115 дней;
Dp – количество дней в ремонте и ТО Dp = 20 дней;
tсм – продолжительность смены маш.-ч tсм = 767 маш.-ч;
Ксм – количество смен работы Ксм = 1;
Тг = (365-115-20)·8·1 = 1836 маш-чгод.
Срз – средняя тарифная ставка работы по ремонту машин руб.чел-ч Срз =74 руб.чел-ч;
Кр – средний коэффициент к тарифной ставке Кр=115;
λρ– коэффициент учитывающий премии ремонтным рабочим λρ =13;
rудТО – удельная оперативная трудоемкость ТО чел-чмоточас
rудТО = 014 чел-чмоточас;
Ков – коэффициент перевода оперативного времени в общее Ков=25;
αТР – количество ТР определяется по формуле
где tp – периодичность ТР мото-час tp = 960 мото-часов;
Тρ – средний ресурс до КР мото-час определяется по формуле
где ργ – гамма - процентный ресурс мото-ч.;
kγ – коэффициент перевода гамма - процентного в средний ресурс kγ = 12.
Средний ресурс до КР определяется по формуле (5.3.7)
Трб = 11300·12 = 13560 мото-ч.;
Трн = 11400·12 = 13680 мото-ч.
Количество текущих ремонтов определяется по формуле
rтр – трудоемкость ТР чел-ч rтр = 2400 чел-ч;
tотк – среднее время на устранение одного отказа маш-ч tотк = 4 маш-ч;
Бр – количество рабочих занятых устранением отказа чел. Бр=1 чел.;
Тотк – наработка на отказ моточас Тотк = 126 моточас;
Кг – коэффициент перевода мото-часов в машино-часы Кг = 04;
Сзчр – расход запасных частей на год работы техники руб.год Сзчр = 12870 руб.год.
Тогда затраты на выполнение текущих внеплановых ремонтов и технических обслуживаний определяется по формуле
3.3 Затраты на выполнение капитальных ремонтов
Затраты на выполнение капитальных ремонтов определяются по формуле
где rкр– трудоемкость КР чел-ч rкр = 2400 чел-ч;
– коэффициент учитывающий социальные отчисления =131
СзчКР – расход запасных частей на один КР руб. СзчКР = 44830 руб.
Тогда затраты на выполнение капитальных ремонтов определяются по формуле (5.3.8)
3.4 Заработная плата машиниста управляющего техникой
Заработная плата рабочих управляющих техникой определяется по формуле
где Кдоп – коэффициент учитывающий доплаты за работу во вторую третью смены;
Б – количество рабочих занятых управлением техники в одну смену чел. Б = 1 чел.;
СTi – часовая тарифная ставка машиниста соответствующая действующим в данном периоде сметным нормам и расценкам руб.ч СТi = 100 руб.ч.
При 1≤ Ксм ≤2 Кдоп определяется по формуле
Тогда заработная плата рабочих управляющих техникой определяется по формуле (5.3.9)
3.5 Затраты на топливо для двигателя внутреннего сгорания
Затраты на топливо для двигателя внутреннего сгорания определяются по формуле
где ЦТ – цена топлива руб.кг;
WТ – часовой расход топлива кгмаш.-ч определяется по формуле
где Nен – номинальная мощность двигателя кВт Nен = 300 кВт;
gен – удельный расход топлива по номинальной мощности гкВтч. gен = 180 гкВтч.;
KN – коэффициент учитывающий изменение расхода топлива в зависимости от степени использования двигателя по мощности KN =112;
Кдв – коэффициент использования двигателя по времени Кдв = 079;
Кдм – коэффициент использования двигателя по мощности Кдм=050.
Часовой расход топлива кгмаш.-ч определяется по формуле (70)
Затраты на топливо для двигателя внутреннего сгорания определяются по формуле (5.3.11)
3.6 Затраты на смазочные материалы
Затраты на смазочные материалы определяются по формуле
где Кст – коэффициент перехода от годовых затрат на топливо к затратам на смазочные материалы Кст = 022.
Затраты на смазочные материалы определяются по формуле (5.3.13)
3.7 Затраты на гидравлическую жидкость
Затраты на гидравлическую жидкость определяются по формуле
где Цмг – оптовая цена гидравлической жидкости руб.кг Цмг = 60 руб.кг;
Тм – периодичность замены гидравлической жидкости маш-ч. Тм = 1000 маш-ч.;
Ом – объемная масса гидравлической жидкости Ом = 0865 кгдм3;
Vг – емкость гидросистемы дм3 Vг = 200 дм3;
Кд – коэффициент доливок Кд = 15.
Затраты на смазочные материалы определяются по формуле (5.3.14)
3.8 Затраты на перебазировки при перевозке техники на большегрузном прицепе-тяжеловозе
Затраты на перебазировки при перевозке техники на большегрузном прицепе-тяжеловозе определяются по формуле
где Сзп – заработная плата экипажа перевозимой машины руб.;
Сж – заработная плата такелажников руб.;
Сза – затраты на эксплуатацию автомобиля (автопоезда) руб.
Заработная плата экипажа перевозимой машины определяется по формуле
где dn – продолжительность одной перебазировки дни;
Б – количество рабочих занятых управлением машины в одну смену чел. Б = 1 чел.;
CTi – часовая тарифная ставка рабочего 3-гo разряда соответствующая действующим в данном периоде сметным нормам и расценкам руб.ч СТi = 80 рубч.
Заработная плата экипажа перевозимой машины определяется по формуле (5.3.16)
Заработная плата такелажников определяется по формуле
где Бт – количество такелажников чел. Бт = 2 чел;
СТКi – часовая тарифная ставка рабочего 3-гo разряда такелажников руб.ч.
Заработная плата такелажников определяется по формуле (5.3.16)
Затраты на эксплуатацию автомобиля (автопоезда) определяется по формуле
где Ца – стоимость одного автомобиля - часа в зависимости от грузоподъемности автомобиля руб.ч Ца = 400 руб.ч;
Цд – плата за один километр пробега руб.км Цд = 13 руб.км.
Затраты на эксплуатацию автомобиля (автопоезда) определяется по формуле (5.3.18)
Сза = 10·1·400 + 2·25·13 = 4650 руб.ч.
Затраты на перебазировки при перевозке техники на большегрузном прицепе-тяжеловозе определяются по формуле (5.3.15)
Накладные расходы определяются по формуле
СН = Нр · Спр (5.3.19)
где Нр – норма накладных расходов связанных с эксплуатацией строительных и дорожных машин Нр = 21 %;
Спр – прямые издержки потребителя определяемые по формуле
Спр = Са + Ср + Скр + Сз + Сзт + Ссм + Сгид +Спб (5.3.20)
Накладные расходы для базовой техники
СНб = 021·(858048+55633+92208+35957141354968+298093+285865+71549) = 637491 руб.
Накладные расходы для новой техники
СНн = 021·(907752+55393+94158+3595714+1354968+298093+285865+
+71549) = 647919 руб.
Таблица 5.3.2 – Калькуляция годовых текущих издержек
Условные обозначения
Значения показателей
Амортизационные отчисления на реновацию
Продолжение таблицы 5.3.2
Затраты на выполнение ТО и ремонтов
Затраты на выполнение капитального ремонта
Заработная плата рабочих управляющих техникой
Затраты на смазочные материалы
Затраты на гидравлическую жидкость
Затраты на перебазировки
Общая сумма годовых текущих издержек
4 Определение экономического эффекта
Экономический эффект в расчете на одну машину за год работы определяется по формуле
Таблица 5.4.1 – Калькуляция годовых текущих издержек
Наименование показателей
Годовая эксплуатационная производительность
Годовые текущие издержки потребителя
Экономический эффект на 1 буровую установку за год работы
В результате применения спроектированной установки для бурения скважины в мёрзлом грунте рассчитан экономический эффект в 38375234 рубля за год эксплуатации. На основе проведенного расчета можно сделать вывод что применение установки для бурения скважин в мёрзлом грунте более рационально и экономически выгодно чем применение базисной техники.
В настоящем проекте наибольшее внимание уделялось вопросам интенсификации разработки мерзлых и прочных грунтов с применением оборудования для укрепления стен пускового котлована при бестраншейной прокладке нефтепровода
В организационно-техническом разделе рассмотрено описание трассы трубопровода технология микротоннелирования технология производства работ методом «стена в грунте» технология производства работ методом «стена в грунте» подробно описаны обзор и анализ существующих конструкций с оборудованием.
В конструкторском разделе был осуществлен выбор гидродвигателя фрезерных роторов и вспомогательной лебедки и рассчитаны их основных параметры также выбран гидроцилиндр наклона стрелы и произведен расчет гидросистемы. Исходя из полученных данных был выбран лопастной гидромотор HVK-A F2-7317 для фрезерных роторов аксиально-поршневой гидромотор Г15-25Р для вспомогательной лебедки и гидроцилиндр наклона с проушинами с обеих сторон со сферическими подшипниками ГЦС 250х180-2500-06-С-0-0.
Важным моментом является замена установки для разработки скважины с вращающимся буровым инструментом на фрезерные роторы. С использованием данного оборудования увеличивается производительность выполняемых работ так как площадь сечения фрезерных роторов в 10 раз больше чем буровой головки.
В разделе технический сервис приведены данные по расчёту зоны ТО и Р для модернизируемого экскаватора. Определено количество рабочих количество постов требуемое годовое количество сжатого воздуха и электроэнергии затраты на освещение и обогрев помещения. Было определено и выбрано необходимое оборудование для проведения качественного ТО и Р.
В проекте рассмотрены вопросы безопасной жизнедеятельности и промышленной безопасности был произведен расчет каната по разрывному усилию. В результате расчета максимальное натяжение каната наматываемого на барабан вспомогательной лебедки составило 193 кН а разрывное усилие составило 967 кН. Исходя из данных полученных при расчете был выбран канат двойной свивки типа ЛК - Р 6x19 который будет обеспечивать безопасные условия работы.
В экономической части проекта в результате применения спроектированной установки для бурения скважины в мёрзлом грунте рассчитан экономический эффект в 38375234 рубля за год эксплуатации. На основе проведенного расчета можно сделать вывод что применение установки для бурения скважин в мёрзлом грунте более рационально и экономически выгодно чем применение базисной техники.
СПИСОК ИСПОЛЬЗОВАННЫХ ИСТОЧНИКОВ
Баловнев В. И. Дорожно-строительные машины с рабочими органами интенсифицирующего действия В. И. Баловнев. М.: Машиностроение 1981. -223 с.
Иванов В.И. Салихов Р.Ф. «Организация эксплуатации технология технического обслуживания и ремонта дорожно-строительных машин» СибАДИ.:Метод.указ.2008.-81с.
Дубков В.В. «Технологический расчет эксплуатационной базы: Методические указания к курсовой работе». - Омск: Издательство СибАДИ 2007. – 47 с.
ШлойдоГ. Л. К вопросу об определении прочности мёрзлых грунтов Г. Л.Шлойдо: Исследование ударных вибрационных строительных машин: науч. тр. ВНИИстройдормашМ. 1976. - Вып. 71. - С. 61-67.
СНиП2.05.06-85 «Магистральные трубопроводы».
Кузьмин А.В. Марон Ф.Л. Справочник по расчётам механизмов подъёмно-транспортных машин. – Минск: Высшая школа 1983. –272 с.
Курсовое проектирование грузоподъёмных машин Под ред. С.А. Казака.- М.: Высшая школа 1983. – 319 с.
Алексеева Т.В. Галдин Н.С. Шерман Э.Б. «Гидравлические машины и гидропривод мобильных машин». - Новосибирск: Издательство НГУ 1994г. 212с.
МартюченкоИ. Г. Методы снижения энергозатрат при разработке мерзлых и прочных грунтов И. Г.Мартюченко; Сарат. гос. техн. ун-т. Саратов. :СГТУ 2004. - 150 с.
Филиппов Б.И. Охрана труда при эксплуатации строительных машин: Учебник для студентов вузов по спец. "Строительные и дорожные машины". 3-е изд. перераб. и доп. - М. Высш. шк. 1984.- 247 с.
Белов С.В. «Безопасность жизнедеятельности» -М.: Высшая школа 1999г. 386с.
Витушкин А.Н. Калугин В.Е. Шаронов В.Н. Экономика производства и эксплуатации строительных дорожных машин. Методические указания по технико–экономическому обоснованию дипломных проектов. - Омск: СибАДИ 1991.- 68с.
9. Экономика.cdw

Амортизационные отчисления на реновацию
Затраты на выполнение технических обслуживаний
текущих и внеплановых ремонтов
Затраты на выполнение капитального ремонта
Заработная плата операторов машины
Затраты на смазочные материалы
Затраты на гидравлическую жидкость
Затраты на перебазировку
Общая сумма гдовых издержек
Наименование показателей
Значения показателей
Годоая эксплуатационная
Годовые текущие издержки потребителя
Экономический эффект за год работы
Технико-эксплуатационные
Технико -эксплуатационные показатели
Сумма годовых текущих издержек
Результат расчета экономической эффективности
График эффективности новой техники
График годовых текущих издержек
0. Общий вид.cdw
Тяговое усилие двигателя
Крутящий момент поворотной
Частота вращения поворотной
Частота вращения двигателя
Скорость передвижения
Максимальная глубина бурения
Максимальная ширина бурения
Платформа поворотная
Лебедка вспомогательная
Кронштейн направляющий
5. Лебёдка.cdw

После сборки проконтролировать размер В
Обкатать без нагрузки со сменой направления вращения 30 минут
и под нагрузкой в течении 1 часа.
Неуказанные предельные отклонения размеров
Технические требования
2. Обзор конструкций.cdw

Эксплуатационная масса
Эксплуатационная мощность двигателя
Максимальный диаметр бурения
Максимальная глубина бурения
Обзор существующих конструкций (машин)
Гусеничный грейфер на базе экскаватора Hitachi 225 EX
Роторная буровая установка SANY на базе экскаватора Caterpillar
Универсальная буровая установка JINTAI SD25
Л 222.cdw

Подшипник 7000114 ГОСТ 8338-75
Подшипник 7000108 ГОСТ 8338-75
Подшипник 1000840 ГОСТ 8338-75
Подшипник 210 ГОСТ 8338-75
Шайба 2 12 ГОСТ 6402-70
Шайба 2 18 ГОСТ 6402-70
1. Карта.cdw

Площадь басейна реки
Высота над уровнем моря
Глубина реки в месте
Пропускная способность
Общая протяженность нефтепровода
Диаметр трубопровода
Диаметр скважины подземного перехода
нефтепровода через реку Таз
Длина руслового участка нефтепровода в
месте пересечения с рекой Таз
Протяженность подземного перехода
Карта местности производства работ
Геологические данные местности реки Таз
Данные по нефтепроводу
Л 111.cdw
Болт М14x30 ГОСТ 7798-70
Болт М14х50 ГОСТ 7798-70
Болт М12х40 ГОСТ 7798-70
Болт М12х70 ГОСТ 7798-70
Болт М12х80 ГОСТ 7798-70
РО 111.cdw
Болт М6х25 ГОСТ 7798-70
Болт М12х35 ГОСТ 7798-70
Болт М6х18 ГОСТ 7798-70
Болт М8x12 ГОСТ 7798-70
8. БЖД.cdw
Канат двойной свивки типа ЛК-Р 6х19
Выбор каната по разрывному усилию
7. Схема смазки и заправки.cdw

и рабочего оборудования
Технические условия и указания
поворота и насосного агрегата
Ежесменно (8 мото-ч.)
При необходимости долить
до уровня масло ТАп-12В
Шарнирное соединение
кронштейна с поворотной
Литол-24 до появления
Шарнирное соединение кронштейна
крепления стрелы нижнее
крепления стрелы верхнее
(количество - 10 шт.)
Оси роликов направляющего
Крепление гидроцилиндра
Шарнирное соединение гидроцилиндра
Шарнирное соединение штока
гидроцилиндра наклона стрелы
Вспомогательная лебедка
Пополнить внутренние полости
смазочным материалом
Схема смазки и заправки
Операционно-технологическая карта смазки и заправки
Произвести смазку солидолонагнетателем
Условные обозначения
4. Рабочий орган СБ.cdw

3. Схема производства работ.cdw

Устройство временной
монолитной железобетонной
конструкции - форшахты
Извлечение рабочего органа из
при одовременной подаче
бентонитового раствора
Установка армированного
Заглубление рабочего органа
Переезд машины и разработка
Техническая характеристика
проходческого щита ПЩМ-2
Наружный диаметр щита
Длина щита без козырька
Производительность щита
Объём сборного железобтона
Технология микротоннелирования
Технология устройства укрепления стен котлована
Схема производста работ
РО 222.cdw
Шайба 2 10 ГОСТ 6402-70
Болт М30x160 ГОСТ 7798-70
Болт М10x28 ГОСТ 7798-70
Болт М20х50 ГОСТ 7798-70
Винт А. М4х10 ГОСТ 1476-93
Гайка М12 ГОСТ 5915-70
Подшипник 2007948А ГОСТ 27365-87
Шайба 2 6 ГОСТ 6402-70
Шайба 2 12 ГОСТ 6402-70
Шайба 2 8 ГОСТ 6402-70
Шайба 2 30 ГОСТ 6402-70
Шайба 2 20 ГОСТ 6402-70
Рекомендуемые чертежи
- 25.01.2023
- 04.11.2022
- 07.03.2023
- 04.11.2022