Повышение эффективности использования теплоты отходящих газов и модернизация ГТК 10-4 путем замены регенератора ООО «Газпром трансгаз Сургут» филиал «Ортьягунское ЛПУМГ»




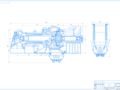
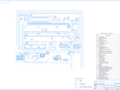
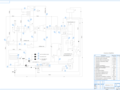
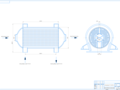
- Добавлен: 04.11.2022
- Размер: 3 MB
- Закачек: 5
Описание
Состав проекта
![]() |
![]() ![]() ![]() |
![]() ![]() ![]() |
![]() ![]() ![]() |
![]() |
![]() ![]() ![]() |
![]() ![]() ![]() |
![]() ![]() ![]() |
Дополнительная информация
1. Принципиальная тепловая схема.cdw
- Резервный маслонасос;
- Пусковой маслонасос;
- Регенератор РГУ-1800-01;
- Регулирующий клапан;
- Главный маслонасос;
- Ааккумулятор масла;
- Подогреватель газа;
- Поплавковая камера;
- Сигнализатор помпажа;
- Регулятор перепада;
- Маслонасосы уплотнения;
- Подогреватель масла.
Принципиальная тепловая схема
Кафедра "Промышленная
Повышение эффективности использования теплоты
отходящих газов и модернизация ГТК 10-4 путем замены регенератора
Масло предельной защиты
ПОЯСНИТЕЛЬНАЯ.docx
Федеральное государственное автономное образовательное учреждение
«Южно-Уральский государственный университет
(национальный исследовательский университет)»
Кафедра «Промышленная теплоэнергетика»
Направление подготовки 13.03.01 «Теплоэнергетика и теплотехника»
КВАЛИФИКАЦИОННАЯ РАБОТА
Заведующий кафедрой
«Промышленная теплоэнергетика»
Повышение эффективности использования теплоты отходящих газов
и модернизация ГТК 10-4 путем замены регенератора
ПОЯСНИТЕЛЬНАЯ ЗАПИСКА
К ВЫПУСКНОЙ КВАЛИФИКАЦИОННОЙ РАБОТЕ БАКАЛАВРА
ЮУрГУ–13.03.01.2020.443.20 ПЗ ВКР
Консультант по разделу
«Безопасность жизнедеятельности»
«Экономика и управление»
старший преподаватель
Федеральное государственное автономное образовательное учреждение высшего
на выпускную квалификационную работу студента
утверждена приказом по университету от «24» апреля 2020 г. №627
Срок сдачи студентом законченной работы «15» мая 2020 г.
Исходные данные к работе: технологическая схема газотурбинного двигателя ГТК 10-4; характеристика и потребность в тепловой нагрузке топливо – природный газ; режимная карта работы газотурбинного двигателя
Содержание расчетно-пояснительной записки (перечень подлежащих разработке вопросов)
ОБОСНОВАНИЕ И АКТУАЛЬНОСТЬ ТЕМЫ ВКР
ОБЗОР ЛИТЕРАТУРНЫХ ИСТОЧНИКОВ
СРАВНЕНИЕ ОТЕЧЕСТВЕННЫХ И ЗАРУБЕЖНЫХ РЕГЕНЕРАТОРОВ
2 Выбор параметров элементов регенератора
3 Описание конструкции регенератора
4 Тепловой расчет регенератора
5 Расчет регенератора на прочность
6 Модернизация вспомогательных систем ГТК 10-4
ПОВЫШЕНИЕ ЭФФЕКТИВНОСТИ И МОДЕРНИЗАЦИЯ ГТК 10-4
1 Алгоритм расчета показателей энергоэффективности КС
2 Регенеративное использование теплоты отходящих газов ГТУ
1 Недостаточная газодинамическая устойчивость ГТК 10-4
2 Повышение газодинамической устойчивости ГТК 10-4
3 Изготовление направляющего аппарата ГТК 10-4
1 Устройство системы регулирования
2 Предпусковое состояние системы регулирования
3 Работа системы регулирования при подачи заданной нагрузке
1 Воздействие работы ГТК 10-4 на окружающую среду
2 Отвод дымовых газов
БЕЗОПАСНОСТЬ ЖИЗНЕДЕЯТЕЛЬНОСТИ
1 Вывод ГТК 10-4 в ремонт
2 Вывод ГТК 10-4 из ремонта
3 Эксплуатация регенератора
ЭКОНОМИКА И УПРАВЛЕНИЕ
1 Расчет капитальных затрат на модернизацию ГТК 10-4
2 Расчет текущих затрат на эксплуатацию ГТК 10-4
3 Расчет эффективности проекта модернизации ГТК 10-4
4 SWOT-анализ для реализации проекта модернизации ГТК 10-4
5 Планирование целей проекта в дереве целей
6 Планирование мероприятий по реализации проекта (график Ганта)
БИБЛИОГРАФИЧЕСКИЙ СПИСОК
Перечень графического материала (с точным указанием обязательных чертежей плакатов в листах формата А1)
Принципиальная тепловая схема ГТК 10-4 – 1 лист формата А1
План оборудования на отметке 000– 1 лист формата А1
ГТК 10-4 – 1 лист формата А1
Регенератор РГУ-1800-01 – 1 лист формата А1
Автоматика ГТК 10-4 – 1 лист формата А1
Консультанты по работе с указанием относящихся к ним разделов работы:
задание выдал (консультант)
Экономика и управление
выдачи задания «23» декабря 2019 г.
К А Л Е Н Д А Р Н Ы Й П Л А Н
выпускной квалификационной работы бакалавра
Срок выполнения этапов работы
Отметка о выполнении
Обоснование и актуальность темы ВКР
Обзор литературных источников
Сравнение отечественных и зарубежных
Повышение эффективности и модернизация
Безопасность жизнедеятельности
Библиографический список
Оформление пояснительной записки
Цель выпускной квалификационной работы – повышение эффективности использования теплоты отходящих газов ГТК 10-4 путем замены регенератора. Работа состоит из введения 10-ти глав заключения и библиографического списка.
В первой главе дана характеристика объекта описана необходимость модернизации ГТК 10-4 предложены технические варианты решения задачи.
Во второй главе сделан обзор литературных источников на основании которых выполнена ВКР.
Третья глава дает информацию о современных регенераторах российского и иностранного производства в сравнении по основным технико-экономическим показателям.
В четвертой части сделаны основные расчеты тепловых нагрузок выбор параметров элементов регенератора тепловой расчет регенератора и его расчет на прочность выполнен расчет ГТК 10-4 после установки регенератора РГУ-1800-01 а также предложена модернизация вспомогательных систем ГТК 10-4.
В пятой главе предложена научно-исследовательская работа по повышению эффективности использования отходящих газов ГТК 10-4.
Шестая глава представляет сведения о мероприятиях по энергосбережению.
В седьмой главе приведено описание функциональной схемы автоматизации и контрольно-измерительных приборов регенератора РГУ-1800-01.
В восьмой главе представлены мероприятия по снижению негативного воздействия работы оборудования на окружающую среду.
В девятой главе приведены мероприятия по охране труда в период вывода в ремонт из ремонта и эксплуатации регенератора и ГТК 10-4 в целом.
В десятой главе выполнен технико-экономический расчет проекта сделан SWOT-анализ для реализации проекта и др.
В заключении подведены итоги технических показателей и решений.
Графическая часть выполнена на 5-ти листах формата А1 в системе «Компас (САПР)».
СРАВНЕНИЕ ОТЕЧЕСТВЕННЫХ И ЗАРУБЕЖНЫХ
Выбор параметров элементов регенератора
Описание конструкции регенератора
Тепловой расчет регенератора
Расчет регенератора на прочность
Модернизация вспомогательных систем ГТК 10-4
Уплотнение на всасе компрессора
Уплотнение на нагнетании компрессора
Напыление металлокерамических покрытий
НАУЧНО-ИССЛЕДОВАТЕЛЬСКАЯ РАБОТА
Недостаточная газодинамическая устойчивость ГТК 10-4
Повышение газодинамической устойчивости ГТК 10-4
Регенеративное использование теплоты отходящих газов ГТУ
Алгоритм расчета показателей энергоэффективности КС
Оптимизация режимов работы ГТК 10-4
Устройство системы регулирования
Предпусковое состояние системы регулирования
Работа системы регулирования при поддержании заданной
Воздействие работы ГТК 10-4 на окружающую среду
Вывод ГТК 10-4 в ремонт
Вывод ГТК 10-4 из ремонта
Эксплуатация регенератора
Расчет капитальных затрат на модернизацию ГТК 10-4
Расчет текущих затрат на эксплуатацию ГТК 10-4
Расчет эффективности проекта модернизации ГТК 10-4
SWOT-анализ для реализации проекта модернизации ГТК 10-4
Планирование целей проекта в дереве целей
Оценка движущих и сдерживающих сил и ресурсов
Планирование мероприятий по реализации проекта
Освоение новых рентабельных источников добычи газа– государственная задача. ПАО«Газпром» всостоянии еёреализовать опираясь наопыт ипотенциал таких предприятий как «Газпром трансгаз Сургут». Это открывает новые перспективы длясургутских газовиковкоторые активно внедряют прогрессивные методы транспортировки сырья участвуют вреализации рационализаторских проектов проявляя профессионализм высочайшую работоспособность целеустремленность преданность своему делу.
ООО«Газпром трансгаз Сургут» является лидером среди дочерних обществ ПАО«Газпром» вобласти автоматизации производства выделяется подругим ключевым показателям. ВОбществе всегда делали ставку нановаторский подход врешении производственных задач. Рационализаторские предложения помогают существенно усовершенствовать технологический процесс. Сургутские газовики начали внедрение автоматизированных систем управления еще в1996 году. Масштабная автоматизация процессов управления сегодня поправу считается конкурентным преимуществом ООО«Газпром трансгаз Сургут».
Большое внимание уделяется охране окружающей среды ивыполнению требований природоохранного законодательства. ВОбществе утверждена Экологическая политика которая содержит принципы обязательства истратегические цели ООО«Газпром трансгаз Сургут» вобласти охраны окружающей среды. Основным принципом деятельности Общества является устойчивое развитие подкоторым понимается динамичный экономический рост при максимально рациональном использовании природных ресурсов исохранении благоприятной окружающей среды длябудущих поколений.
транспортировка природного газа по системам магистральных газопроводов;
поставка газа потребителям через газораспределительные станции по газопроводам-отводам и автомобильные газовые наполнительные компрессорные станции;
эксплуатация химически опасных производственных объектов;
развитие и эксплуатация газотранспортных систем;
строительно-монтажные ремонтно-строительные и наладочные работы;
выработка электроэнергии теплоэнергии добыча воды их транспортирование очистка стоков организация теплоснабжения объектов.
Для поддержания режима работы газотранспортной системы (ГТТ) необходимо поддерживать состояние ГГПА на таком уровне чтобы обеспечивать транспорт запланированных объёмов газа к потребителям. ГГПА образно выражаясь являются «сердцами» КС.
Известно что основное потребление природного газа на собственные нужды КС приходится на топливный газ используемый в качестве топлива в ГТУ и составляющий примерно 8–10% общего объёма транспортируемого газа. В связи с этим достижение снижения энергетических затрат на КС заключается прежде всего в экономии топливного газа.
С ухудшением технического состояния ГТУ для обеспечения мощности необходимой для транспорта одного и того же объёма газа как правило требуется увеличение расхода топливного газа.
Для ГТК 10-4 предлагается установить газотурбинный агрегат-регенератор для использования теплоты уходящих газов. При этом состав основного оборудования ГТК 10-4 остается неизменным.
Также необходимо разработать мероприятия по увеличению ресурса и срока службы ГТК 10-4 путем установки более эффективных элементов компрессора.
Состав топлива поступающего в ГТК 10-4: СН4 – 949%; С2Н6 – 32%; С3Н8 – 04%; С4Н10 – 01%; С5Н12 – 01%; N2 – 09%; СО2 – 04%; = 3672 МДжкг.
Отвод дымовых газов предлагается осуществлять в существующую дымовую трубу 25 м.
Также необходимо разработать систему автоматического управлении и регулирования включающую в себя:
системы автоматического управления и регулирования;
система централизованного контроля и управления КС включающая в себя: автоматизированное рабочее место диспетчера КС (АРМД КС) мнемощит КС и шкаф общестанционной сигнализации и управления (ШОС);
системы безопасности КС включающие в себя: систему управления кранами узла подключения общестанционными и охранными кранами (ЩТУ-11М) систему пожарной сигнализации в т.ч. устройство представления информации (УПИ) АСП систему контроля загазованности и ключ аварийной остановки станции.
Газотурбинная установка ГТК 10-4 состоит из блока турбогруппы двух механически несвязанных между собой турбин (турбины высокого давления – для привода воздушного компрессора и силовой турбины – для привода газового нагнетателя) воздушного компрессора камеры сгорания воздухоподогревателя пускового турбодетандера а также систем смазки регулирования защиты и управления обеспечивающих нормальную работу и обслуживание установки.
Основной расчетно-теоретический материал выпускной квалификационной работы выполнен в соответствии с нормативно-справочной научно-методической нормативно-законодательными актами.
В справочнике Бажан П. И. по теплообменным аппаратам систематизированы важнейшие сведения по теплообменным аппаратам систем судовых тепловозных автомобильных и авиационных энергетических установок. Освещены современные конструкции теплообменных аппаратов вопросы их проектирования и расчета средствами автоматизированного проектирования методы анализа работы даны программы расчета и обработки экспериментальных данных.
В справочнике Мартыненко О.Г. по теплообменникам содержится точное изложение классических основ теории теплообмена и современных методов расчета и проектирования теплообменной аппаратуры самого разного назначения.
Важными источниками которые раскрывают теоретические основы при проектировании тепломеханической части котельных тепловых и гидроэлектростанций являются книги: «Производственные и отопительные котельные» Е.Ф. Бузникова К.Ф. Роддатиса; «Тепловые электрические станции» Э.Я. Берзиньша Бурова В.Д. Дорохова Е.В. Елизарова Д.П; «Промышленная теплоэнергетика и теплотехника» Клименко А.В.; «Котельные установки и парогенераторы» Липова Ю.М.; «Котельные установки промышленных предприятий» Сидельковского Л.Н. Юренев В.Н.; «Теплоэнергетика и теплотехника» А.В. Клименко; «Газотурбинные и парогазовые установки тепловых электростанций» Цанева С.В.; «Проектирование котельных» Палей Е.Л.
В данной литературе мы можем найти все интересующие нас вопросы о конструкциях теплоэнергетического оборудования в книгах содержатся все необходимые материалы для разработки принципиальных схем котельных тепловых и гидроэлектростанций. Авторы книг рекомендуют различные методики по выбору размеров котлов топочных камер поверхностей нагрева и в целом компоновки котельных работающих на различных видах топлива. В этой литературе приведены способы усовершенствования тепловых схем котельных. Данная информация необходима для проектирования монтажа и эксплуатации.
При рассмотрении вопросов экологии в выпускном квалификационном проекте использовалась следующая литература: «Повышение экологической безопасности тепловых электростанций» Абрамова А.И.; «Методы защиты окружающей среды» Рослякова П.В.; «Дымовые трубы» Ижорина М.Н. В данной литературе рассмотрены основные вопросы по экологической безопасности работы тепловых и гидроэлектростанций на современных предприятиях уделено большое внимание применяемому оборудованию благодаря которому можно создавать экологически безопасную тепловую энергию а также приведены методики по выбору дымовых труб их основные конструкции и расчеты высот и диаметров.
В вопросах энергосбережения использовалась следующая литература – «Основы энергосбережения» Арутюняна А.А.; «Энергосбережение в теплоэнергетике и теплотехнологиях» Данилова О.Л.; «Энергосбережение» Полонского В.М.; Федеральный закон РФ от 23 ноября 2009 года № 261-ФЗ. Об энергосбережении и о повышении энергетической эффективности и о внесении изменений в отдельные законодательные акты Российской Федерации [4]; «Энергосбережение при производстве и распределении тепловой энергии» Гаряева А.Б. В данном перечне книг рассматриваются вопросы энергосбережения на промышленных предприятиях предлагаются методики внедрения энергосберегающих мероприятий на тепловых и гидроэлектростанциях а так же приведены примеры по применению энергосберегающих технологий и их результаты при использовании на предприятии.
При изучении вопроса автоматизации технологического процесса мы пользовались следующей литературой: «Автоматизация технологических процессов и производств в теплоэнергетике» Плетнева Г.П.; «Теплотехнические измерения и приборы» Бурова А.Л. Назарова В.И.. В данных источниках подробно рассмотрены вопросы автоматизации технологических процессов в теплоэнергетики и теплотехнологиях большое внимание уделено системам защиты и управления котлов горелок котлов деаэраторов и других элементов тепловой схемы указана расстановка показывающих и управляющих процессом приборов.
В вопросах безопасности жизнедеятельности на предприятии мы использовали литературу: «Безопасность жизнедеятельности» С.В. Белова; «Охрана труда» Девисилова В.А.; СП 52.13330.2011 СНиП 23-05-95* «Естественное и искусственное освещение»; СП 61.13330.2012 «Тепловая изоляция оборудования и трубопроводов»; СП 12.13130.2009 «Определение категорий помещений зданий и наружных установок по взрывопожарной и пожарной опасности. Требования пожарной безопасности»; «Снижение шума от энергетического оборудования» Тупова В.Б.; «Шумовое воздействие энергетических объектов на окружающую среду и методы его снижения» Тупова В.Б. В данных книгах рассмотрены основные проблемы безопасности на промышленных предприятиях и их воздействие на персонал обслуживающий эти предприятия а также приведены методики по повышению безопасности и разработки различных мер по улучшению работы персонала.
В учебном пособии Алабугина А.А. «Экономико-управленческая часть выпускных квалификационных работ для направления подготовки «Теплоэнергетика и теплотехника» приведены методы оценки эффективности и экономической целесообразности проекта: метод приведенных затрат расчет срока окупаемости SWOT-анализ реализации проекта принципы построения графика Ганта и др.
Для разработки чертежей приложенных к выпускной квалификационной работе мы использовали: «Атлас конструкций деталей турбин» Трухний А.Д. Кру- пенникова Б.Н. Троицкого А.Н.; СП 18.13330.2011 «СНиП II-89-80* Генеральные планы промышленных предприятий»; СП 90.13330.2012 Электростанции тепло- вые. Актуализированная редакция СНиП II-58-75; ГОСТ 20995-75* Котлы паро- вые стационарные давлением до 39 МПа. Показатели качества питательной воды и пара. В данных источниках указаны все нормы и правила по расположению основного и вспомогательного оборудования на промышленных предприятиях указаны необходимые расстояния для безопасного обслуживания агрегатов.
В библиографическом списке приведен основной состав литературных источников [1 – 47].
СРАВНЕНИЕ ОТЕЧЕСТВЕННЫХ И ЗАРУБЕЖНЫХ
На компрессорных станциях России в качестве ГПА используются в основном регенеративные газотурбинные установки на долю которых приходится около 85% от общего парка ГПА. Как показывает анализ многолетнего опыта эксплуатации этих агрегатов эффективность их работы в немалой степени зависит от совершенства регенераторов.
Регенераторы подразделяются на два основных типа: трубчатые и пластинчатые. Каждый из них имеет свои достоинства и недостатки однако опыт проектирования и эксплуатации ТОА обоих типов позволяет сделать вывод о несомненном преимуществе трубчатого регенератора перед пластинчатым. Так например фирма GEA (Германия) занимающаяся разработкой регенераторов различного типа с 1957 года в основном для ГТУ General Electr утверждая что удлинением труб с увеличением их числа можно достигнуть эффективности регенератора повышая КПД всей ГТУ без применения давления на стороне газа и воздуха.
Конструкция первого поколения трубчатых регенераторов представляла собой кожухотрубчатый ТО одноходовой по выхлопным газам и восьми ходовой по воздуху с общим противоточным движением теплоносителей. Ее основной недостаток – большая масса и необходимость в связи с этим осуществлять сборку при строительстве.
Следующее поколение трубчатых регенераторов – регенераторы гексагонального типа они отличаются большей поверхностью теплообмена и требуют меньше затрат на монтаж. Трубчатый регенератор гексагонального типа состоит из шести вертикальных трубных пучков выхлопные газы входят снизу и делают шесть или восемь ходов перед выходом в атмосферу.
Сжатый воздух поступает снизу по центральной трубе поднимается вверх где распределяется по трубным пучкам и затем направляется вниз. Такая система обеспечивает общее противоточное движение теплоносителя. Обычно в первом ходе используют гладкие трубы для сведения к минимуму возможности окисления металла а в остальных ходах – трубы с небольшим коэффициентом оребрения.
В 1973 году была разработана новая конструкция трубчатых регенераторов – башенного типа. В новой конструкции также имеется центральная труба но в трубных пучках используются гладкие трубы с небольшим шагом чтобы уменьшить относительно компактный теплообменник. Выхлопные газы входят снизу обтекают трубы и выходят в атмосферу. Воздух поступает также снизу проходит через центральную трубу и далее идет вниз чистым противотоком. В этом типе регенератора применяют трубки из углеродистой или легированной стали для повышенных температур. Опорная трубная доска выполненная в виде «сот» обеспечивает устойчивость труб.
Башенный регенератор пригоден для работы ГТУ с низкосортным топливом.
В 1975 году была создана новая конструкция трубчатого регенератора (без центральной колонны с U-образными трубками). Такие регенераторы обеспечивают хорошее тепловое расширение и необходимую компенсацию в случае неравномерного температурного поля теплоносителей.
Основные достоинства трубчатых регенераторов – их надежность и отсутствие утечек. Гексагональные регенераторы установленные на Транс канадском газопроводе проработали 14 лет без обслуживания и ремонта. За этот период утечек воздуха не было. Высокая надежность и ресурс постоянство характеристик трубчатых регенераторов делают их преимущественнее по сравнению с пластинчатыми. На ряде компрессорных станций пластинчатые регенераторы были заменены на трубчатые. Средняя наработка составила 51400 часов без утечек и с минимальным обслуживанием.
В процессе разработки и проектировании регенераторов различного типа перед фирмами-разработчиками ставится задача связанная с проблемой интенсификации теплообмена.
Шведская фирма Tbolaget United Sterling AB&Co предлагает свой способ решения проблемы интенсификации процесса теплообмена. В запатентованном фирмой трубчатом теплообменнике предлагается на внешней поверхности труб накатывать винтовые канавки встречных направлений которые создают на внутренней поверхности труб выступы способствующие турбулизации потока газов в трубах. Накатка кроме того делает трубы более эластичными и повышает прочность ТО.
Для турбулизации потока вокруг труб предлагается пространство между трубами заполнить мелкими шариками из материала с большой теплопроводностью собранных в пакеты.
Кроме проблемы интенсификации теплообмена немаловажной проблемой является компенсация напряжений возникающих в регенераторах. Одним из способов решения этой задачи является способ предложенный и запатентованный фирмой Joseph Lucas Ltd. (Англия).
Трубчатый теплообменник в котором возникают растягивающие напряжения в трубах предлагается компенсировать путем стягивания торцов теплообменных аппаратов равномерно расположенными вокруг кожуха стержнями причем стягивающие усилия пропорционально растягивающим силам. С этой целью каждый стержень одним концом жестко скреплен с кронштейном кожуха а другой конец соединен с поршнем в цилиндре к которому подводится масло под давлением. Давление масла создается плунжером соединенным с двумя поршнями в воздушном цилиндре причем один поршень нагружен давлением в межтрубном пространстве а другой – давлением в трубках. При увеличении какого-либо из этих давлений (или обоих) поршни перемещают плунжер и натяжение стержней увеличивается. Положительное давление в магистрали поддерживается насосом.
В этой же связи необходимо отметить что фирма GЕА (Германия) для компенсации термических напряжений на протяжении ряда лет занимается разработкой трубчатого регенератора с промежуточным теплоносителем утверждая что к преимуществам таких теплообменников относятся простота конструкции малое гидравлическое сопротивление отсутствие смещения и утечек рабочего тела. Общий КПД энергетической ГТУ с такими теплообменниками только за счет устранения утечек может быть повышен с 20 до 25%.
Проблема высоких термических напряжений очень тесно связана с проблемой соединения регенератора с корпусом ГТГ. Довольно интересное решение предлагает фирма Caterpillar Tractor Co. Запатентованная конструкция фланцевого соединения допускает осевые и поперечные смещения. Осевое смещение соединений (например при изменении температуры) допускается за счет податливости конических стенок трубопровода.
Наконец вопрос компактности и простоты сборки регенератора который каждая фирма решает по-своему. Так например фирма Вгеslа (Нидерланды) выпускает регенераторы в блочном виде решая таким образом проблему агрегатно-узлового метода ремонта. Один блок соответствует ГТУ мощностью 11 МВт. Путем объединения нескольких блоков можно собрать ТОА для ГТУ мощностью 100МВт.
В то же время дочернее предприятие фирмы Westing House (США) в Германии Lohse Glong Inc. запатентовала конструкцию трубчатого противоточного теплобменника в котором охлаждаемая среда перемещается по трубкам представляющим собой многорядную спираль расположенную внутри цилиндрического корпуса и навитую вокруг центральной трубы. Ряды спирали разделены листовыми сегментными перегородками образующими спиральный канал по которому подается хладагент. Теплообменный аппарат отличается простотой изготовления и сборки.
По типу поверхности теплообмена регенераторы разделяются на пластинчатые и трубчатые. Выбор того или иного типа регенератора для каждой установки должен рассматриваться индивидуально но зависит в той или иной степени от двух факторов:
а) внешних по отношению к ГТУ исходных данных;
б) технического совершенства характеристик элементов ГТУ. Внешние исходные данные – это прежде всего стоимость топлива удельная стоимость регенератора стоимость сопутствующих капитальных вложений (транспортировка объём строительно-монтажных работ) базовый и пиковый характер использования. Внутренние факторы – это правильный учет или предсказание технических характеристик ГТУ: КПД турбомашины в регенеративном и безрегенеративном варианте соотношение между гидравлическими сопротивлением и тепловой экономичностью регенератора наличие и величина утечек воздуха стабильность степени регенерации в процессе эксплуатации ресурс ГПА и регенератора.
Рассмотрим некоторые из этих определений для пластинчатых и трубчатых регенераторов. На основе анализа зарубежного опыта и робот наших специалистов был сделан вывод что основной недостаток у пластинчатых регенераторов - появление неплотностей в процессе эксплуатации. Обычно в этом случае возникают две ситуации:
а) периодичность и затраты на ремонт достаточно велики и экономически не оправдывают получаемые эффекты;
б) ремонтные работы в полной мере не обеспечивают получение исходных характеристик ГТУ или их восстановление носит кратковременный характер то есть появляется плохая ремонтопригодность регенератора.
Чтобы увеличить срок службы регенератора необходима комбинация двух факторов:
а) увеличение времени пуска и нагрузки;
Рисунок 3.1 – Регенератора типа РВП-3600-02
Данный регенератор предназначен для реконструкции газотурбинных установок ГТК-10. Также заводом ведутся работы по разработке и подготовке производства регенераторов для установки ГТ-750-ОА2 а также ГТК 10И ГТК-25И и др. Наиболее известные западные фирмы – разработчики трубчатых регенераторов - GEA (Германия) и Breda (Нидерланды).
Также следует отметить некоторые особенности такого регенератора: корпус является силовым трубки диаметром 18 мм выполнены круглыми гладкими бесшовными и в трубных досках крепятся вальцовкой и сваркой.
Как уже отмечалось выше существует большой парк газотурбинных установок (ГТУ) компрессорных станций отработавших довольно большой срок у которых наблюдается коробление корпуса турбины и осевого компрессора.
Для выбора типа регенератора необходимо произвести расчет необходимой теплоты на отопление зданий. Расчет ведется по укрупненным показателям: по объему здания [26].
Определение тепловых нагрузок потребителей производится по укрупненным показателям. Максимальный расход теплоты на отопление зданий определяется по формуле (4.1):
где V – объем зданий по наружному обмеру м³;
q0 – отопительная характеристика зданий Втм³К;
t – поправочный коэффициент определяемый по формуле (4.2):
где tВ – внутренняя расчетная температура воздуха в здании °C;
tН – расчетная температура наружного воздуха °C;
– коэффициент инфильтрации для расчета теплопотерь зданиями определяемый по формуле (4.3):
где b=30÷4010-3 для отдельно стоящего здания;
g = 98 мс2 – ускорение свободного падения;
Н – высота здания (10÷15) м;
В – скорость ветра мс;
qBT – относительные внутренние тепловыделения кВткВт;
q0 – отопительная характеристика здания Втм3К.
В таблице 4.1 представлены тепловые нагрузки зданий находящихся на газокомпрессорной станции с указанием этажности геометрических и климатических исходных данных и расчетом теплопотребления [33].
Таблица 4.1 – Тепловые нагрузки зданий на газокомпрессорной станции
Температура внутреннего воздуха°С
Максимальное теплопотребление при самой низкой наружной температуре воздуха составляет 514 Гкалч.
Определение технического состояния ГТК-10-4:
давление газа на входе в нагнетатель Р1=352 МПа;
давление на выходе Р2=402 МПа;
температура на входе в нагнетатель t1=40 °С;
температура на выходе t2=170 °С;
частота вращения вала ТНД n=3800 обмин;
температура газов на входе в ТВД =726 0C;
температура воздуха на входе в осевой компрессор Р=01 МПа;
низкая теплота сгорания топливного газа Qнр=36283 кДжнм3.
Для расчёта КПД по первому способу необходимо знать химический состав природного газа. На практике целесообразно использовать упрощённые эмпирические состояния предложенные в работе для определения основных термодинамических величин природного газа по метану (4.4):
где: – комплекс кДжкг МПа;
– изобарная теплоемкость метана кДжкгС ;
– коэффициент Джоуля – Томсона СМПа;
t – температура выхода газа из нагнетателя С;
Р – давление входа газа в нагнетатель МПа;
Изобарная теплоемкость метана определяется по (4.5):
Потенциальная функция определяется по формуле (4.6):
где Р – потенциальная функция кДжкг;
Потенциальная функция по метану определяется по формуле (4.7):
Тогда политропический коэффициент полезного действия нагнетателя найдем по формуле (4.8):
где – потенциальная работа сжатия кДжкг;
– среднее значение потенциальной функции P при условиях входа и выхода кДжкг·МПа;
Δh – разность энтальпии газа по нагнетателю кДжкг
Потенциальная работа сжатия определяется по формуле (4.9):
где –степень сжатия нагнетателя определяемая по формуле (4.10):
Разность энтальпии газа по нагнетателю определим по формуле (4.11):
где t – разница температуры газа на выходе и входе нагнетателя С;
P – разница давлений на выходе и входе нагнетателя МПа.
Разница температуры газа на выходе и входе нагнетателя определим по формуле (4.12):
Приведенная относительная частота вращения находится по формуле (4.13):
где Tnp – температура газа при всасывании нагнетателя К;
Т – фактическая температура газа на всасе нагнетателя К;
n – фактическая частота вращения ротора ТНD обмин;
n0 – номинальная частота вращения ротора ТНD обмин;
Z Znp– коэффициент сжимаемости газа на входе в нагнетатель приведенная и фактическая величины соответственно;
R Rnp – газовая постоянная фактическая и приведенная ДжкгК;
Приведенная газовая постоянная определяется по формуле (4.14):
где в – относительная плотность по воздуху.
Определяем паспортное значение КПД нагнетателя коэффициент технического состояния нагнетателя (4.15):
где – политропный КПД нагнетателя;
– политропный КПД (паспортный) нагнетателя.
Плотность газа на входе в нагнетатель (4.16):
где ρ – плотность газа на входе в нагнетатель кгм3.
Расход газа через нагнетатель (4.17):
где Gн – расход газа через нагнетатель м3мин;
Qпр – приведённый расход через нагнетатель по условиям всасывания м3мин.
Мощность потребляемая нагнетателем (4.18):
где Nhн – мощность потребляемая нагнетателем кВт.
Эффективная мощность ГТУ (4.19):
где Nе – эффективная мощность ГТУ кВт;
Nмех – потери мощности механические кВт.
Относительная приведённая температура газа перед ТВД (4.20):
где – относительная приведенная температура газа перед ТВД;
– фактическая температура газа перед ТВД К;
– номинальная температура газов перед ТВД К;
– номинальная температура воздуха на входе компрессора К;
– фактическая номинальная температура воздух на входе в компрессор К.
Приведённая мощность ГТУ (4.21):
где – приведенная относительная мощность (4.22):
Коэффициент технического состояния ГТУ по мощности (4.23):
Теплота сгорания топлива с учётом ухудшения технического состояния ГТУ (4.24):
Расход газа на ГТУ (4.25):
где Втг – расход топливного газа м3ч.
Коэффициент полезного действия ГТУ (4.26):
Рассчитаем диаметры трубопроводов для подвода воздуха от компрессора к регенератору и от регенератора к камере сгорания (4.27):
где d – диаметр воздуховода мм;
Gв – расход воздуха кгс;
W – скорость воздуха в патрубках мс;
ρв – плотность воздуха кгм3.
Рассчитаем плотность воздуха (4.28):
где Рв – давление воздуха на входе в регенератор МПа;
Rв – газовая постоянная Джкг·К;
Tв –температура воздуха на входе в регенератор К;
По всему трубопроводу осевого компрессора – регенератора примем скорость
течения воздуха 25 мс. Рассчитаем диаметр:
Принимаем d=800 мм [29].
Рассчитаем плотность воздуха:
и диаметр по формуле
Принимаем диаметр 1022 мм.
Рассчитаем длину и количество трубок. Учитывая стесненные условия несущую способность фундаментов определяем поверхность теплообмена одной секции регенератора F=1800 м2 .
По рекомендации принимаем скорость движения газов 20 мс. И определяем площадь S одного метра трубы диаметром 25 мм S=0079 мм2 [29].
Найдем общую длину трубок (4.29):
Определим расход газов через одну трубку при скорости 20 мс (4.30):
где ρ – плотность газов кгм3;
W – скорость газов мс.
Определяем количество трубок (4.31):
где Vг – расход газов от ГТУ м3с.
Длина одной трубки (4.32):
Шаг трубной решетки принимаем равным 33 мм.
Газотурбинный агрегат-регенератор пластинчатый трубчатый РГУ-1800-01.
Основные конструктивные и расчетные характеристики приведены для одной секции регенератора. Основные конструктивные параметры секции регенератора приведены в таблице 4.2 [43].
Таблица 4.2 – Конструктивные параметры РГУ-1800-01
Наименование параметра
Диаметр и толщина корпуса
Диаметр и толщина гладких теплообменных труб
Количество теплообменных труб не менее
Диаметр и толщина воздушных патрубков
Расчетные номинальные параметры воздуха и продуктов сгорания секции регенератора приведены в таблице 4.3.
Таблица 4.3 – Расчетные параметры работы РГУ-1800-01
Наименование показателя
Продолжение таблицы 4.3
Рабочая температура не более
Расход (на одну секцию)
Степень регенерации не менее
Суммарное относительное аэродинамическое сопротивление не более
Число циклов (пуск-останов) секции за весь срок службы не более
В конструкции регенератора применяются стали перлитного и хромомолибденового классов.
Конструкция регенератора обеспечивает:
доступ к трубным доскам через люки-лазы в камерах подвода и отвода продуктов сгорания;
опорожнение и свободный сток в горизонтальном положении при изготовлении и эксплуатации.
Полный ресурс регенератора – 100 тыс. часов.
Расчетный срок службы – 15 лет.
Регенератор должен быть гидроиспытан по межтрубному пространству. Давление гидроиспытании (пневмоиспытаний) по межтрубному пространству должно быть не более 078 МПа (80 кгссм2) температура воды(+5 +40) °С. Количество испытании на заводе и в эксплуатации – не более 10.
После проведения гидравлических испытаний обеспечить слив воды из полостей секции регенератора при всех снятых колпачковых гайках дренажных трубок линзовых компенсаторов и заглушках.
Регенератор состоит из 2-х секций с присоединяемыми трубопроводами (до здания компрессорной станции). Секция регенератора посредством фланцевых соединений присоединяется к поставляемым в комплекте газоходам и воздуховодам до здания компрессорной станции и далее к существующим газоходу и воздуховодам ГТК-10-4. Компенсатор газохода устанавливается внутри здания компрессорной станции.
Секция регенератора представляет собой горизонтальный теплообменный аппарат кожухотрубного типа с линзовым компенсатором на корпусе.
Для подогрева воздуха проходящего в межтрубном пространстве используется тепло продуктов сгорания газотурбинных газоперекачивающих агрегатов типа ГТК-10-4.
Поверхность теплообмена секции регенератора выполнена из труб с интенсификаторами теплообмена 25×1 мм из стали 15ХМ ГОСТ 8733-74.
Теплообменные трубы расположены по равностороннему треугольнику с шагом 33 мм. Концы труб закреплены в трубных досках при помощи вальцовки и сварки. Трубная доска входной камеры изготовлена из стали 12ХМ трубная доска выходной камеры – из стали 22К. Положение труб в осесимметричном трубном пучке фиксируется кольцевыми и дисковыми перегородками организующими четырехходовое поперечное обтекание теплообменых труб. Перегородки выполнены из стали 16ГС ГОСТ 5520-79 и закреплены на 18-ти маячных стержнях 20 мм из стали 20 ГОСТ 1050-88.
Koрпyc секции регенератора выполнен из обечаек с наружным диаметром 3214 мм с толщиной стенки 12 мм из стали 09Г2С 16ГС ГОСТ 5520-79. К обечайкам корпуса приварены трубные доски к которым приварены камеры подвода и отвода продуктов сгорания. Для обеспечения компенсации разницы температурных линейных расширении по длине корпуса и труб на корпусе установлен 3-х линзовый компенсатор толщиной 8 мм из стали 20К ГОСТ 5520-79.
Камера подвода продуктов сгорания представляет собой коническую обечайку с толщиной стенки S мм выполненную из стали 12ХМ ГОСТ5520-79. Камера отвода продуктов сгорания представляет собой коническую обечайку с толщиной стенки 8 мм выполненную из стали 16ГС ГОСТ 5520-79.
Для обеспечения осмотра и ремонта узлов соединения «труба – трубная доска» в камерах подвода и отвода продуктов сгорания установлены люки – лазы Ду 600 мм крышки которых снабжены поворотным устройством.
Для компенсации разницы температурных расширений на трубопроводах подвода и отвода воздуха установлены линзовые компенсаторы толщиной 6 мм выполненные из стали 16ГС ГОСТ 5520-79 (подвод воздуха) и 12ХМ ГОСТ 5520-79 (отвод воздуха). Для подьема и строповки при установке секции регенератора на монтаже имеются четыре уха. Полость по межтрубному пространству снабжена воздушниками и дренажами используемыми при проведении гидравлических испытаний. Необходимо обеспечить сохранность дренажных штуцеров на компенсаторе от механических повреждений. На корпусе аппарата имеются скобы для крепления теплоизоляции.
Секция регенератора имеет две опоры воспринимающие весовые нагрузки. Имеется одна неподвижная опора – для фиксирования положения секции регенератора. Вторая опора подвижная – для обеспечения свободы перемещения от температурных расширений.
Основополагающими соотношениями для теплового расчета любого теплообменного аппарата являются уравнения теплового баланса и теплопередачи. Основным моментом расчета является как правило определение значения среднего для всей поверхности теплообмена коэффициента теплопередачи k [26].
Для расчёта теплообменного аппарата примем противоточную схему теплоносителей. В качестве поверхностного теплообмена будем использовать трубчатую матрицу. Для начала необходимо составить уравнение теплового баланса для трёх участков теплообменного аппарата. Уравнение теплового баланса для поверхностного аппарата в общем случае имеет вид (4.33):
где Q – тепловая мощность аппарата кВт;
G1 G2 – массовые расходы первичного и вторичного теплоносителей кгс;
Сp1 Ср2 – теплоемкости первичного и вторичного теплоносителей кДж(кг·К);
– температуры первичного и вторичного теплоносителей на входе в аппарат С;
– температуры первичного и вторичного теплоносителей на выходе из аппарата С.
Тогда выражение для нахождения температуры дымовых газов будет выглядеть так (4.34):
Используя уравнение теплового баланса найдем температуру дымовых газов для этого определим количество теплоты передаваемого в единицу времени (4.35):
Далее необходимо рассчитать средний температурный напор (4.36):
Наибольший температурный напор (4.37):
Наименьший температурный напор (4.38):
Уравнение теплопередачи запишем следующим образом (4.39):
Тогда площадь теплоотдачи (4.40):
Средняя температура воды (4.41):
Средняя температура дымовых газов (4.42):
Площадь поперечного сечения (4.43):
Найдем число Рейнольдса для течения теплоносителя в трубочках (4.44):
Количество трубочек (4.45):
Далее находим число Нуссельта (4.46):
Коэффициент теплоотдачи внутри трубок (4.47):
Находим скорость дымовых газов обтекающих трубочки (4.48):
где F – площадь площади входа и выхода теплоносителя м2 (4.49):
Определим коэффициент теплоотдачи со стороны дымовых газов. Найдем число Нуссельта (4.50):
Коэффициент теплоотдачи (4.51):
Определим коэффициент теплопередачи по формуле для цилиндрической поверхности (4.52):
Рассчитаем площадь теплообмена по формуле (4.53):
Определим общую длину труб теплообменника как (4.54):
где – средний диаметр трубочек мм.
Величина теплового потока для всего рекуператора (4.55):
Параметры дымовых газов:
Расход: G1 = 28 кгс.
Теплоёмкость: Ср1 = 1154 кДжкг·К.
Определим расход пара:
Величина теплового потока на первом участке:
Температура дымовых газов в начале участка испарения воды:
Величина теплового потока на втором участке:
Величина теплового потока на третьем участке:
Температура дымовых газов на выходе из участка испарения:
При средней температуре 124 С на первом участке вода имеет физические характеристики:
Примем скоростью движения воды в трубочках w2 = 05 мс. При заданных параметрах условию удовлетворяет значение внутреннего диаметра трубки dвн=0016 м. Найдём число Рейнольдса [26]:
Так как Re > 104 то режим движения потока является турбулентным.
Рассчитаем количество трубочек на первом участке:
Принимаем количество трубок 32трубки размещаются в шахматном порядке (рисунок 4.1).
Рисунок 4.1 – Схема расположения трубок
Принимаем шаг между осями труб в ряду s = 23dнар = 00414 м.
Рассчитаем длину трубки на всём участке теплообмена.
Примем коэффициент теплопередачи К=350 Втм2·К.
Рассчитаем средний температурный напор:
Общая площадь теплообмена:
Общая длинна труб теплообменника:
При средней температуре 292 С на третьем участке перегретый пар имеет физические характеристики:
Q1 = 472·10-2 Вт(м·К);
Определим скорость на участке перегрева водяного пара. Для унификации конструкции теплообменника примем такой же диаметр трубочек как и на участке подогрева воды а так же их количество. Принимаем количество трубок 32 шт.
Для нахождения коэффициента теплоотдачи от жидкости αж используем:
Найдём коэффициент теплоотдачи от перегретого пара αПП для третьего участка. Подставляем численные значения:
Найдём коэффициент теплоотдачи αКИП при движении кипящей воды в трубах на втором участке тогда (4.56):
Подставляем численные значения:
Для нахождения коэффициента теплоотдачи на втором участке нужно посчитать коэффициент теплоотдачи кипения (4.57):
Рассчитаем тепловой поток q:
Задаёмся давлением Р = 3 МПf.
Для правильности расчета значение берём в барах.
Подставляем численные значения и определяем коэффициент теплоотдачи на втором участке:
Теперь необходимо найти коэффициенты теплоотдачи со стороны дымовых газов. Для этого зададимся размерами проточной части (рисунок 4.2) [43].
Рисунок 4.2 – Проточная часть (вид спереди)
Высота корпуса: Н = 04 м;
Высота трубки: Hтруб = 035 м;
Ширина корпуса: b = 23dнар·(Nтр1+1).
Ширина рассчитывается с учетом того что 32 трубочки расположены в два ряда в шахматном порядке таким образом что расстояние между осями трубочек одного ряда составляет 23·dнар.. Найдем площадь газа (4.58):
Для того что бы найти число Рейнольдса на третьем участке определим скорость дымовых газов. Определяем параметры дымовых газов на третьем участке при средней температуре 525 С:
Qг3 = 676·10-2 Вт(м·К).
Рассчитаем скорость движения дымовых газов при обтекании трубочек:
Рассчитаем коэффициент теплоотдачи на третьем участке при поперечном обтекании трубочек дымовыми газами:
Рассчитаем коэффициент теплоотдачи на втором участке при поперечном обтекании трубочек дымовыми газам. Определяем физические характеристики при средней температуре 427 С.
nг2 = 6467·10-6 м2с;
Qг2 = 593·10-2 Вт(м·К).
Найдем число Рейнольдса:
Коэффициент теплоотдачи:
Рассчитаем коэффициент теплоотдачи на первом участке при поперечном обтекании трубочек дымовыми газам. Определяем параметры при средней температуре 299 С:
nг1 = 4567·10-6 м2с;
Qг1 = 483·10-2 Вт(м·К).
Корпус котла утилизатора выполнен из нержавеющей стали марки 12Х18Н9Т [43]. Определяем физические характеристики: ρн.с = 7950 кгм3; Qн.с = 144+0016t Вт(м·К).
Коэффициент теплопередачи трех участков теплообменного аппарата.
Температура дымовых газов 525 С.
Температура дымовых газов 427 С
Температура дымовых газов 299 С.
Рассчитаем средний температурный напор для трех участков.
Определим длину трубочек на трех участках.
Уточним коэффициент теплоотдачи на втором участке с новым значением длинны L2 = 408 м.
Коэффициент теплоотдачи кипения:
Коэффициент теплоотдачи на втором участке:
Коэффициент теплопередачи на втором участке:
Найдем новую длину второго участка при новых значениях:
При пересчёте было выяснено что длина второго участка увеличилась. В дальнейших расчётах принимаем LII = 424 м.
Определим количество загибов трубочек на участках (4.59):
Примем число загибов равным 57.
Примем число загибов равным 21.
Цель расчета на прочность – определение способности конструкции теплообменного аппарата сопротивляться статическим и динамическим нагрузкам которые возникают при эксплуатации аппарата и обусловлены как его конструкцией так и режимом его работы. Расчет на прочность элементов конструкции теплообменного аппарата может выполниться как конструкторский и как поверочный. При конструкторском расчете определяются основные размеры аппарата удовлетворяющие условиям прочности.
Расчет на прочность может выполняться по предельным напряжениям или по предельным нагрузкам. Расчет по предельным нагрузкам применяется для аппаратов выполненных из пластичных материалов таких как малоуглеродистые стали медь и ее сплавы и т.д. В этом случае за опасное значение принимается величина напряжения вызывающего общую пластическую деформацию всего нагруженного узла.
Расчет по предельным напряжениям производится для аппаратов выполненных из хрупких материалов (например закаленной стали) разрушение которых наступает без заметных пластических деформаций. В расчете по предельным напряжениям пределом несущей способности конструкции является достижение в любом сечении конструкции предела текучести.
Расчеты теплообменных аппаратов на прочность должны производиться в соответствии с требованиями нормативных документов. За расчетную температуру по которой определяются физико-механические характеристики материалов и допускаемые напряжения в отдельных узлах аппарата принимается наибольшее значение температуры протекающего в аппарате теплоносителя.
Расчетное давление принимается равным наибольшему давлению теплоносителя с учетом давления срабатывания предохранительных клапанов на соответствующих подводящих трубопроводах.
Для элементов разделяющих пространства с разными давлениями за расчетное принимается либо каждое давление по отдельности либо то которое требует наибольшей толщины стенки либо разница давлений между средами.
Кроме определения уровня усилий и напряжений в элементах конструкции и удовлетворяющих условиям прочности размеров этих элементов к прочностным относятся также расчеты тонкостенных оболочек на устойчивость расчет термических напряжений от различного теплового удлинения трубок поверхности теплообмена и кожуха аппарата а также расчет трубок на вибрацию.
Расчет на прочность производится по номинальным допускаемым напряжениям. Под номинальным допускаемым напряжением понимается напряжение используемое в расчетах для определения минимальной допускаемой толщины стенки и максимального допускаемого давления в зависимости от принятых расчетных условий работы аппарата и марки стали или сплава из которого изготовлен аппарат или его узел [43 46].
Характеристиками прочности материала являются следующие величины:
временное сопротивление или предел прочности при комнатной и расчетной температурах;
физический предел текучести при расчетной температуре;
предел длительной прочности при расчетной температуре.
При выборе допускаемых напряжений величины пределов прочности и текучести принимаются равными минимальным значениям установленным в соответствующих стандартах или технических условиях для металла данной марки.
Физико-механические характеристики материалов применяемых в аппарате приняты в соответствии с государственными стандартами (таблица 4.3).
Таблица 4.3 – Физико-механические характеристики материалов
Конус входной обечайка корпуса патрубок отвода воздуха (лист) S=816 мм
Ст 12ХМ ГОСТ 5520-79
Обечайка камеры выходной обечайки корпуса патрубок подвода воздуха ребра опорные (лист) S=816 мм
Ст 16ГС ГОСТ 5520-79
Опора (плиты опорные) (лист) S=25 мм
Обечайки корпуса (лист) S=12 мм
Ст 09Г2С ГОСТ 5520-79
Труба теплообменная 25×1 мм (труба)
Ст 15ХМ ГОСТ 8733-74
Фланец на входе воздуха поковка КП245 гр. VI
Допускаемые напряжения для материалов определяют по формуле 4.60:
nb = 24 для расчетного режима гидроиспытания;
nТ = 2 для элементов крепежа.
Расчетные группы категорий напряжений не должны превышать значений:
в расчетном режиме – ()Rma
()Rmax ≤ 13 [] – напряжение изгиба МПа.
Величины расчетных групп категорий напряжений для элементов конструкции приведены в таблице 4.4. для элементов крепежа - в таблице4.5.
Таблица 4.4 – Расчетные группы категорий напряжений
Ст 12ХМ (лист) S=816 мм ГОСТ 5520-79
Ст 16ГС (лист) S=25 мм ГОСТ 5520-79
Ст 20 (круг) ГОСТ 1050-88
Ст 12ХМ (поковка) ГОСТ 8479-70
Продолжение таблицы 4.4
Ст 15ХМ (труба) 25×1 ГОСТ 8733-74
Величины расчетных групп категорий напряжений для элементов крепежа – в таблице 4.5.
Таблица 4.5 – Расчетные группы категорий напряжений для элементов крепежа
Расчетные параметры в аппарате приведены в таблице 4.6.
Таблица 4.6 – Расчетные параметры в регенераторе
Межтрубное пространство
Максимальное рабочее абсолютное давление МПа
Максимальная рабочая температура °С
Абсолютное давление на входе МПа
Рабочая температура не более на входе °С
Число циклов нагружения не более
Температура и давление гидроиспытания составляют (4.61):
Поверочный расчет камер входной и выходной проведен по программе реализующей метод конечных элементов для пространственных конструкций. В качестве базовых конечных элементов приняты четырехузловые плоские конечные элементы с шестью степенями свободы в каждом узле (три перемещения и три угла поворота) [37].
В месте сварки конуса с трубной доской задано условие закрепления (UX=UY=UZ=RX=RY=RZ=0) по внутренней кромке обечайки патрубка выхода воздуха задано условие шарнирного закрепления (UX=UY=UZ=0). Давление в патрубке Р = 039 МПа. Нагрузки передаваемые трубопроводом отвода воздуха (с учетом монтажной растяжки в рабочем состоянии) взяты из и приложены к патрубку выхода воздуха.
max = 1190 МПа 13 []500 = 1250 МПа
Статическая прочность камеры входной обеспечена.
В месте сварки конуса с трубной доской задано условие закрепления (UX=UY=UZ=RX=RY=RZ=0)по внутренней кромке обечайки патрубка входа воздуха задано условие шарнирного закрепления (UX=UY=UZ=0). Давление в патрубке Р = 0.39 МПа. Нагрузки передаваемые трубопроводом подвода воздуха (с учетом монтажной растяжки в рабочем состоянии) приложены к патрубку входа воздуха. Максимальное напряжение в патрубке входа воздуха
max = 324 МПа 13 []370= 1440 МПа
Максимальное напряжение в конусе выходном
max = 293 МПа 13[ ] = 1440 МПа
Статическая прочность камеры выходной обеспечена.
Подводящий газоход к секции регенератора РГУ-1800-01 имеет конструкцию аналогичную подводящему газоходу к секции регенератора РГУ-1800.
Трубопровод отвода воздуха от секции регенератора РГУ-1800-01 имеет конструкцию аналогичную трубопроводу отвода воздуха от секции регенератора РГУ-1800.
Трубопровод подвода воздуха к секции регенератора РГУ-1800-01 отличается от трубопровода подвода воздуха к секции регенератора РГУ-1800 тем что он имеет меньшую длину на участке от зеркала фланца до продольной оси трубопровода (на 90 мм). Такое отклонение от геометрических параметров расчетной схемы существенно не влияет на результаты расчета напряженного состояния.
Поверочный расчет элементов трубопроводов выполнен по программе реализующей метод конечных элементов для расчета пластинчатых пространственных конструкций. В качестве базовых конечных элементов приняты элементы с шестью степенями свободы в каждом узле (три перемещения и три угла поворота).
Внутренний диаметр D = 8080 мм.
Толщина стенки S = 80 мм.
Прибавки к толщине стенки С11 = 08 мм; С12 = 00 мм; С2= 10 мм С=С11+С12+С2 =18 мм.
Расчетное давление Р = 04 МПа.
Допускаемое напряжение [] v=1630 МПа.
Материал обечайки 16ГС.
Начальное значение коэффициента снижения прочности FI = 10.
Зона влияния сварных швов на FI патрубков L = 500 мм.
Расчетная толщина обечайки при FI = 10; с учетом прибавок S = 279 мм.
Конструкция смоделирована четкрехузловымми конечными элементами. В месте соединения переходника с регенератором задано условие шарнирного закрепления (UZ=0). Внутреннее давление в переходнике Р = 0006 Мпа [43].
max =685 МПа 13[]370 = 1440 МПа
Условие статической прочности выполнено.
Компенсатор смоделирован плоскими четырехугольными конечными элементами. По одной из кромок расчетной схемы компенсатора задано условие шарнирного закрепления (U2 = 0). Компенсатор находится под действием внутреннего давления Р = 0006 МПа и температурного расширения вычисленного по формуле (4.62):
где α – температурный коэффициент линейного расширения;
L – расстояние от неподвижной опоры регенератора до оси дымовой трубы мм;
Т – температура в компенсаторе (максимальная рабочая температура в утилизаторе) °С.
Монтажная растяжка компенсатора принята равной 10 мм в этом случае компенсатор принимает на себя 12 мм сжатия от температурного расширения газохода. Расчет проведен для трех режимов нагружения компенсатора: от давления от монтажной растяжки на 10 мм и от давления и температурного расширения с учетом монтажной растяжки на 10 мм (сжатие компенсатора на 12 мм) [43].
Максимальное напряжение возникает:
от монтажной растяжки на 10 мм в элементе 315:
от давления и сжатия на 12 мм в элементе 315:
max = 2640 МПа ( )370Rv= 2940 МПа.
Статическая прочность прямоугольного компенсатора обеспечена.
6 Модернизация вспомогательных систем ГТК-10-4
Эти системы обеспечивают эксплуатацию газоперекачивающего агрегата и другого оборудования компрессорной станции а также нормальные условия обслуживающего персонала.
6.1 Уплотнение на всасе компрессора
На всасе компрессора вместо обычного концевого лабиринтного уплотнения с закатными усиками устанавливается лабиринтно-винтовое уплотнение выполненное в виде микрокомпрессора винтового типа.
Оно состоит из втулки статорной установленной во всасывающей камере и втулки роторной насаженной с натягом на вал компрессора и зафиксированной в нём винтом.
На указанных втулках выполнено трапецеидальное многозаходная резьба противоположного направления (на роторной втулке правая а на статорной – левая). Профиль зуба выполнен одинаковым на обоих втулках.
Втулка статорная состоит из двух половин закреплённых на горизонтальном разъёме всасывающей камеры с помощью стопорных шайб. Центровка статорной втулки относительно ротора осуществляется с помощью 6-ти штифтов. Лабиринтно-винтовое уплотнение при вращении вала создают в кольцевом зазоре между ним и корпусом небольшой поток воздуха с необходимым перепадом давления направленный с входа в первую ступень компрессора наружу в машинный зал. На производительность компрессора выброс воздуха в атмосферу через лабиринтно-винтовое уплотнение практически не влияет так как отбор этого воздуха осуществляется до рабочих лопаток компрессора.
Установка уплотнения такого типа позволяет устранить подсос паров и капель масла в проточную часть компрессора через полость переднего подшипника без подачи запирающего воздуха на всасе компрессора [37].
6.2 Обойма компрессора
В обойме компрессора в местах расположенных над рабочими лопатками 6 10-й ступеней выполнены профильные кольцевые проточки в которые установиваются чугунные вставки. Над каждым рабочим колесом устанавливается по 12 вставок которые на разъёме обоймы крепятся стопорными шайбами.
Указанные вставки позволяют обеспечить заданный радиальный зазор между рабочими лопатками и обоймой при быстрых изменениях температурного состояния ротора и статора [46].
6.3 Уплотнение на нагнетании компрессора
На нагнетании компрессора вместо концевого ступенчатого лабиринтного уплотнения устанавливается прямоточное уплотнение с металлокерамическими вставками.
Для этого в существующей уплотнительной обойме выполнена кольцевая проточка и в неё закатана вновь изготовленная обойма с металлокерамическим уплотнением состоящая из двух половин. Для фиксации обоймы в осевом направлении установлена прокладка.
На выходном конце вала удалены закатные усики заднего уплотнения и на их месте выточены уплотнительные усики высотой 6 мм.
Данная конструкция уплотнения позволяет обеспечить минимальные радиальные зазоры в уплотнении и применить вместо ступенчатого прямоточное уплотнение не требующее подгонки в осевом направлении а следовательно увеличить экономичность и уменьшить трудоёмкость изготовления компрессора а также повысить ремонтопригодность агрегата [46].
Цель модернизации – увеличение надёжности работы камеры сгорания и улучшение её экологических характеристик.
Увеличение надёжности работы камеры сгорания достигается за счёт изменения конструкции пламенной трубы: пламенная труба изготавливается двухсекционной что позволяет при необходимости удалять её из корпуса камеры без нарушения (в отличие от камер сгорания с длинным смесителем) целостности. Секции связываются между собой фланцевыми соединениями представляющими из себя два кольца скрепляющиеся шпильками с корончатыми гайками а кольца соединены секциями планками приваренными к пламенным обечайкам и имеющими овальной формы отверстия для прохода шпилек позволяющие пламенным обечайкам свободно расширяться при нагреве.
Такая конструкция с одной стороны позволяет предохранить кольца от перегрева а с другой стороны оставляет фиксированным зазор в телескопическом соединении между соседними секциями. Тем самым гарантируется постоянство расхода воздуха идущего на охлаждение пламенной трубы со стороны горячего потока. На выходной секции пламенной трубы установлен кран предохраняющий корпус камеры сгорания от излучаемого пламенной трубой тепла.
Окна смесительного устройства выполнены прямоугольными и меньшего сечения чем в исходной камере за счёт чего улучшается качество перемешивания вторичного воздуха с продуктами сгорания и увеличивается доля первичного (идущего в зону горения) воздуха.
Пламенная труба подвешивается верхней своей секцией в корпусе камеры сгорания на шести пальцах в шести наварышах соответственно. Каждая пара «палец – наварыш» имеет промежуточную шаровую втулку устраняющую возможность «закусывания» при неравномерном нагреве пламенной трубы (если таковой возникнет в силу каких-либо причин: на пример при забросе в камеру сгорания газового конденсата) а также при сборке – разборке камеры.
Подвеска пламенной трубы (в отличие от установки трубы на пальцах размещающихся в нижней её части как в камерах типа 188.131.СБА или 188.131.СБ41) улучшает её вибрационные характеристики устраняя маятниковый эффект с которым в предыдущих конструкциях приходилось бороться применением например телескопических соединений в верхней части камеры [27].
Вибрационную устойчивость камеры сгорания повышают также два крепления типа «шпонка-паз» установленные в средней части пламенной трубы и позволяющие ей свободно расширяться в осевом и радиальном направлении и устраняющее тангенциальные перемещения.
Экологические характеристики агрегатов улучшаются за счёт применения комбинированных двухканальных горелок в одном из каналов которых заранее готовится и затем подаётся в зону горения топливно-воздушная смесь.
Камера сгорания модернизированного агрегата ГТК-10-4 так же как и исходная является семигорелочной. Внешние каналы периферийных горелок предназначены для подготовки гомогенной ТВС и оснащены дефлекторами для выравнивания скоростного поля перед завихрителями воздушного потока и трубками подачи топлива в эту зону. Расстояние между топливоподающими трубками и завихрителями достаточно чтобы организовать ТВС с приемлемой степенью концентрационной равномерности. Из внутреннего (плотного) канала топливо через отверстия расположенные непосредственно за завихрителями попадает воздух образуя плохо перемешанную смесь которая и сгорает диффузионным образом.
Центральная (дежурная) горелка имеет три канала два из которых запитываются топливом также как и у периферийных от регулирующего клапана системы регулирования. Третий канал выполняет роль дежурной горелки камеры сгорания (также как и центральная горелка в исходной камере сгорания) и запитывается через штатную дроссельную шайбу от стопорного клапана системы регулирования [26].
Зажигание дежурного факела осуществляется электроискровым способом от свечи зажигания. В диффузоре фронтового устройства установлен экран «Э» устраняющий контакт зоны горения с охлаждающим воздухом и тем самым способствующий повышению равномерности температурного поля в зоне горения.
Камера сгорания оснащена дополнительным топливным коллектором из которого топливо подаётся во внешние (предварительного перемешивания) каналы всех семи горелок. Внутренние (диффузионные) каналы всех горелок запитываются от штатного коллектора. Оба коллектора получают топливо от регулирующего клапана но на входе в дополнительный коллектор установлен автоматический клапан управляющийся давлением топлива перед собой.
Таким образом при запуске агрегата работают только пилотные каналы горелок обеспечивающие выход агрегата на холостой ход. После того как давление топлива в магистрали после регулирующего клапана достигает необходимого значения автоматический клапан начинает постепенно открываться и топливо перераспределяется в сторону внешнего канала горелок. На максимальном режиме работы агрегата распределение является примерно следующим: 70% топлива – во внешний 30% – во внутренний каналы.
При этом концентрация оксидов азота в выхлопных газах агрегата не превышает 50 ррm условной концентрации кислорода 15%.
6.5 Напыление металлических покрытий
Существует большой парк газотурбинных установок (ГТУ) компрессорных станций отработавших достаточно больной срок у которых наблюдается коробление корпуса турбины и осевого компрессора (ОК). В этом случае мощность ГТУ может быть увеличена за счет восстановления оптимальных радиальных зазоров газодинамическим напылением металлокерамических покрытий на статорную часть ОК.
При эксплуатации газотурбинных агрегатов на КС магистральных газопроводов их техническое состояние со временем ухудшается что приводит к падению мощности и КПД ГТУ и следовательно к пережогу топливного газа. Существует целый ряд причин такого ухудшения
увеличение радиальных зазоров в проточной части ОК происходит из-за коробления корпуса и стирания металла статора рабочими лопатками;
увеличение средних радиальных зазоров в уплотнении высокого давления компрессора (воздушной обойме) связанное преимущественно также с изменением ее формы и стиранием металла «усами»;
не герметичность разъемов внутреннего и внешнего корпуса турбины вызванная короблением корпуса.
Ухудшение расходно-напорных характеристик компрессора увеличение утечек сжатого компрессором воздуха и рабочего тела обусловленные указанными причинами могут приводить к значительному снижению наиболее важных характеристик ГТУ мощности – на 10 20 % КПД – на 5 10 % (относительных).
Дефекты оборудования обусловленные изменением первоначальных геометрических размеров металлических деталей или узлов можно устранить напылением металлических покрытий восстанавливающих первоначальные размеры.
При газодинамическом способе напыления покрытий мелкие частицы металла и керамики (порошок) ускоряются сверхзвуковым газовым потоком до скорости несколько сот метров в секунду и находясь при этом в твердом состоянии сталкиваются с подложкой. В процессе высокоскоростного удара частицы с подложкой происходит преобразование кинетической энергии этой частицы в энергию связи (механическая межмолекулярная химическая) ее с подложкой.
Получаемые таким образом газодинамические покрытия отличаются высокой прочностью сцепления с основой и по своей структуре представляют собой практически однородный металлический слой структурированный частицами керамики [37 46].
В настоящее время значительная часть ГПА на КС имеют эксплуатационный КПД существенно ниже паспортного значения что приводит к значительному перерасходу топливного газа на перекачку [20].
Это связано с двумя факторами – снижением технического состояния ГПА (и их недозагрузкой что требует решения задачи оптимизации режима работы КС.
Периодическое обновление ГПА на КС – необходимый и закономерный путь улучшения показателей транспорта газа в целом и уменьшения энергозатрат на его осуществление.
Расчеты осуществляются в соответствии с блок-схемой приведенной на рисунке 5.1.
Рисунок 5.1 – Блок-схема определения параметров работы КЦ:
P1н (P2н) – давление на входе (на выходе) КЦ;
T1н (T2н) – температура на входе (температура на выходе) КЦ К; qкц – производительность; Z1н (Z2н) – коэффициент сжимаемости на входе (коэффициент сжимаемости на выходе) КЦ; Zср – средний коэффициент сжимаемости; н – степень повышения давления; R – газовая постоянная; п – политропный КПД; м – механический КПД; Gкц – массовый расход КЦ; N Qкц – объемный расход КЦ; ρ1н – плотность газа на входе; Nкц – мощность потребляемая КЦ; Hп – политропный напор
Первый этап выбора оптимального количества и типоразмера компримирующего оборудования предусматривает применение расчетно-оценочного метода для определения потребляемой мощности компрессорного цеха (КЦ).
На следующем этапе расчеты проводятся по конкретным характеристикам ЦБН и ГТУ: определяются величины КПД ЦБН и ГТУ на всех заданных режимах; проверяются условия соответствия потребляемой и располагаемой мощностей ГТУ с целью обеспечения их соотношения в пределах от 09 до 095 для среднегодового режима; определяются частоты вращения ЦБН и ГТУ на всех заданных режимах и проверяются положения режимных точек в зонах допустимой длительной эксплуатации [26].
Рассмотрим в качестве примера реконструкцию одной из компрессорных станций магистрального газопровода Уренгой-Петровск с заменой восьми существующих агрегатов ГТК-10М с центробежным нагнетателем (ЦБН) Н-370-18-1 (схема работы 3х2+2) по двум возможным вариантам: с заменой на 4 агрегата ГПА-16 (при схеме работы 3х1+1) с заменой на 3 агрегата ГПА-25 (при схеме работы 2х1+1) [32].
Эффективность вариантов будем рассматривать по следующим показателям: потребляемая мощность коэффициент загрузки по мощности и годовой расход топливного газа.
Для сравнения эффективности эксплуатации энергопривода с тепловым двигателем по длине газопровода в зависимости от числа последовательно расположенных КС предложен коэффициент полезного использования (или сохранения) газа (КПИ) представляющий собой отношение количества фактически транспортируемого газа по данному участку газопровода (за вычетом топливного) к его количеству в начале участка (5.1):
где – расход транспортируемого газа в начале участка ГТС МВт;
– расход топливного газа на всех КС по длине участка ГТС МВт.
Зависимости для основных показателей (на примере ГТУ I-ой группы):
фактическая мощность:
давления воздуха на выходе из ОК температуры воздуха на входе в ОК атмосферного давления низшей теплоты сгорания топлива на фактическом режиме работы установки; – мощность ГТУ для режима «нулевой» точки (в качестве «нулевого» чаще всего используется номинальный режим) [27].
эталонная мощность мощность которую развивала бы ГТУ;
располагаемая мощность.
Здесь под индексом «0» обозначены значения газодинамических параметров в приведенном виде для номинальной точки аргумента. Переход к относительным критериальным параметрам обеспечивает возможность описания характеристик в виде одномерных массивов относительных параметров и использования их для любой гаммы сочетаний технического состояния основных узлов ЦБН.
Сравнение значений FсаТВД и FсаТНД рассчитанных с использованием газодинамических функций и по зависимости для адиабатного истечения показало занижение значений площадей сечений сопловых аппаратов по зависимости для адиабатного истечения относительно их размерности по заводским данным: по ТВД – на 17 18 % по ТНД – на 117 13 % [29].
Это позволяет рекомендовать в качестве основной расчетной зависимости применительно к реальному процессу выражение с использованием газодинамической функции. Площади сечений сопловых аппаратов ТВД и ТНД могут являться диагностическими признаками подтверждающими оценки состояния турбин ГТУ при условии непрерывного наблюдения в процессе эксплуатации. При этом по соотношению динамики изменения FсаТВД и FсаТНД в сочетании с измеряемым термодинамическим параметром Т2ТНД и определяемыми показателями (Ne KN) может быть по отдельности оценено через ТВД и ТНД изменение технического состояния ТВД и ТНД.
Проанализирован метод поузлового параметрического диагностирования с использованием линейных диагностических матриц (ДМ) применительно к использованию для ГТУ стационарного типа. Для получения реально работоспособных ДМ при формировании решаемой системы уравнений необходимо поочередно исключать измеряемые параметры (ИП) и диагностические параметры (признаки – ДП) образующие избыточность относительно всей системы например ТНД и FсаТНД. В результате формируемые диагностические системы не содержат (в форме допущения) соответственно ТНД и FсаТНД: «B» – ТНД = 0; «C» – FсаТНД = 0.
Сравнение при заданных неисправностях по узлам ГТУ относительных отклонений Ne и e для системы с допущением FсаТНД = 0 («С») и «полной» (без допущений) системы выявило следующую связь (5.2):
где и –фактические и фиктивные отклонения мощности и КПД.
Получаемая диагностическая (матричная) модель может выдавать адекватные диагнозы по узлам лишь при использовании фиктивного отклонения мощности либо допущении FсаТНД = 0. При использовании же фактического (по внешнему замеру) значения мощности получаемые диагнозы по всем параметрам будут несколько отличаться от действительных значений. В итоге при использовании полученных (при условии Fса ТНД = 0) диагностических матриц предварительно должна быть локализована величина FсаТНД: определена каким-либо другим способом или приравнена нулю. Это обосновывается единичным влиянием FсаТНД лишь на мощность и эффективный КПД ГТУ [32].
При сравнении двух методов поузлового параметрического диагностирования проточной части ГТУ стационарного типа предпочтение для дальнейшего применения и развития отдается методу последовательного газодинамического расчета как более наглядному информативному обеспечивающему возможность непрерывного контроля измерительных каналов.
В шестой главе проанализированы вопросы обеспечения энергосбережения за счет оптимизации режимов работы ГПА КС. Оптимизация технологических режимов с учетом реального технического состояния ГПА определяемого с использованием методов параметрической диагностики является основным малозатратным мероприятием по обеспечению энергосбережения на эксплуатируемых газопроводах.
Для решения задачи оптимизации обозначен и реализован комплекс задач которые обеспечивают:
распределение потока газа из многониточной трубопроводной системы по цехам КС;
учет фактического расхода газа проходящего через нагнетатели КЦ и КС;
расчеты режимов компримирования по КЦ с ГГПА и ЭГПА с выбором оптимального варианта загрузки ГГПА.
Необходимо решить задачи оперативного параметрического диагностирования ГПА определения характеристик линейных участков режимов компримирования с оптимизацией загрузки до уровня агрегата. Реализация предварительного распределения потока газа выбора для работы цехов и агрегатов априорно еще до непосредственного компримирования обеспечивает оптимальный выбор имеющихся на КС ГПА и тем самым на системном уровне минимальные затраты энергоресурсов.
Задача распределения заключается в оптимальном наборе из имеющихся на КС агрегатов располагаемой мощности необходимой для данного технологического задания («плановой») Ne план путем предварительного выбора Ne располагаемый КС номеров загружаемых ГПА в списке упорядоченных КЦ. Распределение расхода газа по цехам производится с учетом приоритетности типа ГПА технического состояния ГТУ (KN) наличия котлов-утилизаторов и сезона года.
Оперирование величиной фактического расхода газа как на уровне всей КС так и отдельно по компрессорным цехам повышает адекватность расчетов режимов загрузки ГПА и потребления ТЭР [32 37].
Сравнение рассчитанного на основе мощностей ГПА расхода газа через КС фактически перекачиваемого нагнетателями и по диспетчерским данным обнаружило его расхождение от 1 до 8 % (чаще всего в сторону увеличения).
Эта разница может обусловливаться как инструментальными и методическими погрешностями так и наличием внутристанционных перетоков через запорную и регулирующую арматуру а также внутри самого ЦБН через уплотнение покрывающего диска рабочего колеса.
Соотношение между фактическим расходом газа и расходом по диспетчерским данным предложено описывать через «коэффициент рециркуляции» или «связи».
При расчетах режимов компримирования коммерческий расход Qк в задании следует задавать с учетом Ксв получаемого по результатам предварительного диагностического расчета по рабочим ГПА КЦ или КС. Расчеты режимов компримирования выполняются по алгоритмам использующим в основе элементы метода имитационного моделирования. Оптимальный вариант загрузки по критерию «минимум затрат топливного газа агрегатами КЦ» получается в результате экстремального выбора из реализованных вариантов последовательного перебора [30].
Моделирование технологического режима КС с заменой морально устаревших агрегатов на ГПА нового поколения укрупненной мощности с помощью предложенного алгоритма и результаты эксперимента [26 35].
Таким образом реконструкция компрессорной станции с установкой агрегатов нового поколения с эффективным КПД ГТУ 35÷36% позволяет сократить потребление топливного газа на 416% за год при установке четырех агрегатов ГПА-16 (3х1+1) на 382% за год при установке трех агрегатов ГПА-25 (2х1+1). Потребляемая мощность компрессорного цеха снижается на 8÷10% при установке ГПА-16 на 65÷77% при установке ГПА-25.
В настоящее время на компрессорных станциях России преобладает классическая схема технологической обвязки оборудования и трубопроводов. К особенностям классической обвязки можно отнести разбивку основного технологического оборудования на три основные функциональные группы:
группу пылеуловителей;
группу газоперекачивающих агрегатов;
группу аппаратов воздушного охлаждения газа.
Каждая группа оборудования объединена между собой через коллекторную трубопроводную обвязку компрессорного цеха. Недостатками классической коллекторной обвязки помимо высокой металлоемкости трубопроводной обвязки и значительной площади территории КС являются высокие газодинамические потери в технологических трубопроводах.
Основной акцент при проведении реконструкции компрессорных станций с применением технологических модулей сделан на следующем: снижении гидравлических потерь в технологическом оборудовании и трубопроводах; повышении технико-экономических показателей КС в том числе увеличении надежности оборудования и трубопроводов КС; уменьшении сроков и стоимости строительства снижении эксплуатационных затрат.
Особенностями компоновки КС с применением блочно-модульной установки являются:
размещение линии рециркуляции газа непосредственно в технологическом модуле что позволяет исключить общецеховую линию рециркуляции газа и значительно сократить общую длину станционных трубопроводов;
индивидуальная поагрегатная обвязка АВО газа что ведет к снижению турбулентной вибрационной составляющей и позволяет повысить надежность технологических трубопроводов.
Переход на блочно-модульную компоновку КС позволит снизить суммарные потери давления газа в фильтр-сепараторах и в АВО газа от 017 до 005 МПа что приведет к снижению необходимой степени повышения давления в нагнетателе газа потребляемой мощности нагнетателя и позволит за счет этого получить экономию до 8–9 % топливного газа на каждом ГПА.
Снижение гидравлических сопротивлений за счет применения труб с внутренним покрытием
В проектах новых магистральных газопроводов (МГ) трубы с внутренним покрытием используются в первую очередь для повышения производительности. Применение данного технического решения при реконструкции линейной части эксплуатируемых МГ является одним из методов повышения энергоэффективности позволяющим сократить потребляемую мощность и расход топлива на КС.
Основным достоинством «гладкостных» покрытий является снижение трения при транспортировке газа.
Наряду с этим можно выделить ряд положительных факторов применения «гладкостных» внутренних покрытий:
экономия энергозатрат на перекачку и сжатие в процессе эксплуатации трубопровода обеспечивает окупаемость внутреннего покрытия за 3–5 лет;
улучшенный режим движения газа. Турбулентность потока значительно снижается при наличии внутреннего покрытия что ведет к снижению критических состояний определяемых режимом движения газа;
значительное снижение капитальных затрат за счет возможности уменьшения диаметра трубопровода обусловленной повышением его пропускной способности.
Установлено что для газопроводов достаточно нанести покрытие толщиной 40 75 мкм. Для магистральных газопроводов эффективность применения гладкостных покрытий прямо пропорциональна диаметру трубопровода.
Замена 1 км участка газопровода с применением труб с внутренним покрытием снижает потребляемую мощность КС на 305 706 кВт; при применении труб с внутренним покрытием вдоль всего участка газопровода между КС (110 км) потребляемая мощность эксплуатируемой станции снижается на 22–23%. Локальный энергосберегающий эффект зависит от места применения внутреннего покрытия: с увеличением протяженности реконструируемой части МГ снижается потребляемая мощность КС.
Как показал анализ замена 1 км в начале и в конце участка газопровода даёт одинаковый результат. Поскольку МГ преимущественно работают в квадратичной зоне сопротивления то увеличение степени расширения транспортируемого газа на участке газопровода между КС описывается параболической зависимостью.
При замене 1 км с применением внутреннего покрытия в начале участка газопровода снижение степени расширения газа меньше однако данный эффект распространяется вдоль всего участка между КС обусловливая в конце участка одинаковое снижение скорости газа как и при замене 1 км трубы с применением внутреннего покрытия в конце участка газопровода.
Величина энергосберегающего эффекта при применении внутреннего покрытия определяется геометрической конфигурацией участка газопровода (внутренний диаметр протяженность) газодинамическими параметрами транспорта газа и в условиях режимно-технологической неравномерности работы МГ имеет переменное значение [43].
Применение рассмотренных в статье подходов при проектировании на стадии реконструкции компрессорных станций позволит улучшить показатели энергоэффективности КС уменьшить потребляемую мощность компрессорных станций и снизить затраты топливного газа [20 23].
В соответствии с Федеральным законом Российской Федерации от 23.11.2009 г. № 261-ФЗ «Энергосбережение – реализация организационных правовых технических экономических и иных мер направленных на уменьшение объёма используемых энергетических ресурсов при сохранении соответствующего полезного эффекта от их использования».
Основными методами повышения энергоэффективности работы КС применяемыми при реконструкции и новом строительстве являются:
выбор оптимального количества и типоразмера ГПА обеспечивающий снижение энергозатрат (замена морально устаревших и физически изношенных ГПА на агрегаты нового поколения с высоким эффективным КПД ГТУ применение на КС агрегатов с различной удельной мощностью и т.д.);
регенеративное использование теплоты отходящих газов ГТУ;
применение модульной компоновки ГПА;
снижение гидравлических сопротивлений за счет применения труб с внутренним покрытием.
Компрессорные цеха и компрессорные станции реальное техническое состояние которых не обеспечивает компримирование планируемых объемов транспортируемого газа выступают в качестве «узких мест» магистральных газопроводов.
1 Регенеративное использование теплоты отходящих газов ГТУ
Снижение энергозатрат на транспорт газа по газопроводу в значительной степени связано с эффективностью работы самих газоперекачивающих агрегатов (ГПА) и в первую очередь газотурбинных установок (ГТУ) как основного вида энергопривода центробежных нагнетателей на компрессорных станциях.
Схема ГТУ с регенерацией теплоты показана на рисунке 5.2.
Рисунок 5.2 – Схема ГТУ с регенерацией теплоты уходящих газов:
– компрессор; 2 – регенератор; 3 – камера сгорания; 4 – турбина;
Повышение экономичности газотурбинных установок как одного из основных видов энергопривода КС может быть осуществлено различными способами и в частности за счет теплотехнического совершенства схемы ГТУ посредством введения в нее регенерации тепла отходящих газов [35].
Суть метода заключается в снижении расхода топлива за счёт сокращения потерь теплоты с уходящими газами.
Основные потери в газотурбинной установке - это потери теплоты с уходящими газами которые составляют 60 70 % а иногда и более процентов от подводимой с топливом энергии. В простой ГТУ газы покидающие турбину имеют высокую температуру 400 450°С. Поэтому энергоэффективность ГТУ существенно повысится если применить регенерацию теплоты т.е. использовать часть уходящей теплоты для подготовки сжатого воздуха поступающего в камеру сгорания.
Воздух после компрессора 1 пропускался через регенератор 2 который представляет собой теплообменный аппарат поверхностного типа. Туда же в регенератор 2 после газовой турбины 4 направляются отработавшие газы которые отдают часть своего тепла воздуху и затем удаляются в атмосферу. В регенераторе температура воздуха повышается на 180 250°С так что необходимое количество топлива расходуемое на подогрев воздуха в камере при этом уменьшается энергоэффективность ГТУ возрастает но сравнению с энергоэффективностью простой ГТУ без регенерации.
2 Алгоритм расчета показателей энергоэффективности КС
Расход топливного газа ГТУ тыс.м3ч вычисляют по формуле (6.1):
где – номинальный расход топливного газа м3ч;
Kтг – коэффициент технического состояния ГТУ (по топливу);
Nн – мощность потребляемая ЦБН МВт;
e – номинальный КПД ГТУ;
Qтс – теплота сгорания топливного газа кДжм3.
Номинальный расход топливного газа определяют по формуле (6.2):
Потребление топливного газа КЦ млн.м3 за расчетный период вычисляют по формуле (6.3):
где np – количество рабочих ГПА;
– время расчетного периода ч.
Коэффициент использования мощности показывает насколько эффективно будет использоваться установленная мощность (6.4):
где – располагаемая мощность ГТУ МВт;
– потребляемая мощность МВт.
Располагаемую мощность ГТУ определяют согласно по следующей формуле (6.5):
где – номинальная мощность ГТУ;
KN – коэффициент технического состояния ГТУ (по мощности) принимают равным 095 если не имеется оснований для принятия другой величины;
Kt – коэффициент учитывающий влияние температуры атмосферного воздуха;
Ky – коэффициент учитывающий наличие утилизатора тепла;
KРа – коэффициент учитывающий влияние высоты над уровнем моря;
Kn – коэффициент влияния относительной скорости вращения ротора силовой турбины; обычно учитывается в составе коэффициента КN.
Учёт влияния температур атмосферного воздуха рекомендуется рассчитывать по формуле (6.6):
где Тa – расчетная температура атмосферного воздуха на входе в ГТУ К;
kt – коэффициент величину которого для оценочных расчетов рекомендуется принимать 30.
Расчётная температура атмосферного воздуха на входе в ГТУ определяется по формуле (6.7):
где – средняя температура атмосферного воздуха расчетного календарного периода К.
3 Оптимизация режимов работы ГТК 10-4
Общий характер зависимости обусловливается алгоритмом расчета а также принятыми при переборе значениями QПОМП QРЕЖ QNe описывающими дискретные изменения объемного расхода через ЦБН соответственно при парировании помпажа изменении режима дефиците мощности.
При последовательно-параллельном соединении ЦБН оптимизация режима загрузки ГПА КЦ обеспечивается как за счет выбора расходов на входах групп (оптимизация по Q) так и за счет назначения соответствующей степени повышения давления в нагнетателе каждой ступени. Производится выбор числа ступеней сжатия а также предлагается априорное назначение начальной степени сжатия на ЦБН 1-х ступеней при –переборе что обеспечивает возможность быстрого выполнения расчетов режимов компримирования по КЦ с ЦБН группами от 1 до 3-х. Оптимизация обеспечивает дополнительную экономию топливного газа относительно Q-оптимального варианта [29].
Исследование влияния технического состояния ГГПА на выходные показатели компримирования для оптимального варианта загрузки агрегатов производится с использованием моделей отражающих работу КЦ с газотурбинным приводом при параллельном в 1 ступень соединении ЦБН и последовательно-параллельном в 2 ступени соединении ЦБН. Реализующие программы обеспечивают работу КЦ при условиях P2н = const и P2н = var.
Сравнение по топливным затратам 1-ступенчатого и 2ступенчатого сжатия в КЦ (на примере газотурбинного привода ГТК-10-4 с ЦБН 235-21-1 и 370-18-1(зауж.)) для режимов с умеренным и относительно малым расходом компримируемого по КЦ газа для газопровода с р = 745 МПа. При этом для режимов до умеренного по уровню коммерческого расхода технологического задания (Qк = 65 млн. нм3сут. Р = 505653 МПа) схема с 2-ступенчатым соединением ЦБН экономичнее схемы с 1-ступенчатым: разница в расходе топливного газа по КЦ составляет порядка 1 %.
Преимущества 1-ступенчатой схемы перед 2-ступенчатой реализуются с понижением расхода по КЦ и повышением степени сжатия соответственно напорной характеристике ЦБН: Qк = 50 60 нм3сут. н = 142 148. При изменении структуры КЦ (сокращение числа рабочих агрегатов) экономия топливного газа согласно расчетам по оптимальному варианту загрузки ГГПА для 1-ступенчатой схемы соединения ЦБН может составить более 15 % [32].
Алгоритм реализации оптимального варианта загрузки ГПА в эксплуатационных условиях на уровне КЦ для дополнения действующих систем контроля и управления агрегатного уровня. Алгоритм включает последовательно выполняемые задачи:
параметрическое диагностирование ГТУ и ЦБН на фактическом режиме эксплуатации;
расчет режима работы с выбором оптимального варианта загрузки по минимальному расходу топливного газа агрегатами КЦ;
расчет значений управляющего и базового параметров ГТУ на уровень загрузки по оптимальному варианту для установки на работающих в КЦ агрегатах;
повторное параметрическое диагностирование ГТУ и ЦБН на установленном оптимальном режиме.
Анализ влияния технического состояния ЦБН на энергозатраты при компримировании в КЦ с электроприводными ГПА для параллельного и последовательно-параллельного соединения нагнетателей (на примере ЭГПА СТД-12500-2 с ЦБН 235-21-3 и 370-18-2). Выбор ЭГПА для работы из состава КЦ производится по техническому состоянию ЦБН. Из двух коэффициентов описывающих техническое состояние ЦБН (KНп и Kп) выбор рабочих агрегатов целесообразно осуществлять по коэффициенту по политропному КПД (Kп). Эффективность работы КС или КЦ с ЭГПА оценивается по суммарным затратам мощности на компримирование.
В зависимости от задаваемого условия расчета реализуется режим компримирования: Qк зад = const р2н = = var либо р2н зад = const Qк = var.
При реализации расчетов режимов компримирования КЦ с ЭГПА при последовательно-параллельном соединении ЦБН дополнительными осложняющими факторами выступают условия материального баланса между ступенями сжатия и идентичности значений давления газа на выходах групп.
Особенностью расчета режима компримирования КЦ с ЭГПА для 2ступенчатой схемы соединения ЦБН является изначальное выделение группы ЭГПА с минимальным значением KНп ср – nгр min с целью последующего расчета давления р2н для всего КЦ. Поскольку основной компоновочной схемой работы существующих КС с ЭГПА является работа в составе одного или нескольких (замыкающих) цехов с газотурбинными ГПА наиболее характерным и практически реализуемым режимом работы КЦ с ЭГПА является р2н = const.
При выборе ЭГПА для реализации режимов компримирования достаточно ориентироваться на коэффициент K п. При наличии диагностических данных о состоянии проточных частей ЦБН КЦ при формировании рабочих групп агрегаты с худшим состоянием по политропному КПД (Kп) следует по возможности включать для работы во 2-й ступени. Это обеспечит более надежную реализацию детерминированного по выходному давлению режима КЦ с ЭГПА в составе КС со смешанными типами ГПА (ЭГПА + ГГПА).
На основе проведенного анализа результатов расчетов режимов КЦ с газотурбинным и электрическим приводом ЦБН рекомендован порядок реализации расчетов режимов многоцеховой КС со смешанными типами ГПА (ГГПА + ЭГПА) который может отличаться от порядка расположения цехов на КС [37].
Объем экономии топливного газа (ГГПА) и электроэнергии (ЭГПА) указан соответственно уровню улучшения коэффициента технического состояния газотурбинной установки на 10 % и ЦБН на 5 %. На основании выполненных оптимизационных расчетов режимов с учетом имеющего место уровня загрузки газопроводов и реального технического состояния парка ГГПА следует принять величину экономии топливного газа за счет собственно оптимизации загрузки (без изменения структуры КЦ):
– для параллельного соединения ЦБН – 1 2 % от фактического уровня;
– для последовательно-параллельного соединения ЦБН – 1 %.
С учетом изменения структуры компрессорных цехов по числу ГГПА экономия топливного газа за счет оптимизации загрузки агрегатов может составить более 15 %.
Обобщенно за счет улучшения технического состояния проточных частей ГТУ и ЦБН экономия топливного газа может составить величину порядка 08 % на 1 % улучшения технического состояния каждого из этих блоков ГГПА.
В ЭГПА экономия электроэнергии может составить 1 11 % на 1 % улучшения технического состояния ЦБН по коэффициенту ТС по политропному КПД.
С учетом поэтапного ввода новых агрегатов (существующей схемы) с относительно высокоэффективным газотурбинным приводом в сочетании с находящимися в эксплуатации агрегатами более ранних выпусков и ГГПА с продленным сроком эксплуатации следует оценивать улучшение эффективного КПД привода и соответственно снижение расхода топливного газа не более чем на 4 5 % в течение ближайших 10 лет.
Реализация высокоэффективных мероприятий газосбережения агрегатного профиля (применение ЭГТА) вместе с малорасходными мероприятиями эксплуатационного характера (поддержание нормативного технического состояния привода и газового компрессора оптимальное распределение расходов между цехами КС и оптимизация загрузки ГГПА в КЦ) качественно при широкомасштабном использовании может обеспечить экономию до 47 70 % от нынешнего уровня затрат природного газа в форме топливной составляющей в том числе по ЭГТА – 23 46 %; по электроэнергии – на 5 % от нынешнего уровня затрат по ЭГПА [27 32 35 38].
Система регулирования пневматического типа и система автоматического управления обеспечивают:
поддержание заданной частоты вращения силового вала;
управление операциями пуска и остановки;
защиту от недопустимых режимов и условий работы.
Операции по пуску нагружению управлению и остановки могут выполнятся автоматически как с центрального щита так и через щит агрегат. Эксплуатационные параметры изменяются дистанционно.
В состав АСУ ТП КС входят:
системы автоматического управления и регулирования (САУиР) ГПА в том числе устройства представления информации (УПИ) и пожарный контроллер (ПК 4510) автоматической системы пожаротушения (АСП);
системы безопасности КС включающие в себя: систему управления кранами узла подключения общестанционными и охранными кранами (ЩТУ-11М) систему пожарной сигнализации в т.ч. устройство представления информации (УПИ) АСП систему контроля загазованности и ключ аварийной остановки станции (КАОС);
САУ и Р АВО (аппараты воздушного охлаждения) газа;
САУ вспомогательных объектов;
система линейной телемеханики (СЛТМ).
Система автоматического управления ГПА предназначена для выполнения функций управления регулирования и контроля обеспечивающих длительную безаварийную работу ГПА.
САУ ГПА обеспечивает автоматическое выполнение следующих функций:
Управляющие функции:
автоматическая проверка готовности к пуску включая проверку защит;
автоматический пуск ГПА – по команде САУ КЦ верхнего уровня или по команде оператора со стойки управления (СУ);
изменение задания по частоте вращения турбины нагнетателя по командам САУ КЦ или оператора с СУ;
автоматическая нормальная остановка ГПА: по команде САУ КЦ или оператора с СУ;
автоматическая аварийная остановка ГПА по сигналам устройств защит по команде САУ КЦ или оператора с СУ.
К основным защитам устройств относятся:
защита по температуре в камере сгорания;
защита по перепаду «масло–газ»;
защита по давлению масла смазки;
защита по вибрации и осевому сдвигу;
защита по превышению оборотов ТВД и ТНД и защита по температуре подшипников;
экстренная остановка: по команде оператора с СУ;
холодная прокрутка газотурбинного двигателя (ГТД);
технологическая прокрутка ГТД;
включение средств пожаротушения: автоматическое или по команде оператора с СУ;
дистанционное управление основными и вспомогательными механизмами на неработающем ГПА.
Информационные функции:
сбор и обработка аналоговых технологических параметров ГПА;
сбор и обработка дискретных параметров характеризующих состояние и положение исполнительных механизмов ГПА;
обмен информацией с САУ КЦ;
обмен информацией между устройствами САУ ГПА;
непрерывное отображение и запись ряда важнейших параметров характеризующих работу ГПА таких как: частота вращения ТНД ТВД; температура газа в камере сгорания; перепад давления масло–газ; вибрация двигателя нагнетателя; давление газа до и после нагнетателя;
отображение по запросу оператора информации о текущих значениях технологических параметров положения исполнительных механизмов и устройств ГПА;
оценочный расчет ряда косвенных параметров таких как: расход топливного газа; объемная производительность; эффективная мощность и КПД; учет наработки ГПА при работе в трассу и количество пусков и остановок;
автоматическое представление информации о предупредительных и аварийных ситуациях связанных с выходом технологических параметров за установленные пределы или срабатыванием защиты ГПА;
автоматическое запоминание срабатывания аварийной сигнализации до момента снятия ее оператором;
представление информации о невыполненных предпусковых условиях и отклонениях от нормального течения процессов пуска и остановки ГПА;
сигнализация основных режимов работы ГПА: готовность к пуску пуск кольцо магистраль нормальная остановка аварийная остановка готовность к холодной или технологической прокрутке технологическая прокрутка;
звуковая сигнализация о предупредительных и аварийных ситуациях связанных с выходом технологических параметров за установленные пределы или срабатыванием защиты ГПА (аварийная – непрерывный звуковой сигнал предупредительная – прерывистый).
Функции регулирования САУ ГПА:
регулирование частоты вращения ТН обеспечивает поддержание частоты вращения турбины нагнетателя в соответствии с заданием вышестоящего уровня или по командам оператора с учетом ограничений по температуре продуктов сгорания приемистости частоте вращения турбин высокого и низкого давления;
антипомпажное регулирование обеспечивает стабилизацию режима работы нагнетателя вне зоны помпажа на основании непрерывного расчета расстояния между рабочей точкой нагнетателя и линией помпажа а также скорости приближения рабочей точки к линии помпажа.
По принципу построения САУ ГПА подразделяются на релейные релейно-электронные и микропроцессорные.
При замыкании контакта КСД срабатывает реле ППМГ – предупредительная сигнализация.
Разработаем микропроцессорной САУ ГПА на примере ГПА.
Конструктивно САУ ГПА состоит из 4 стоек:
стойка центрального вычислительного комплекса и устройств нормализации сигналов (ЦВК-УНС);
стойка релейных коммутаторов нагрузки (РКН);
стойка кроссировочная (СК);
стойка управления (СУ).
Стойки ЦВК-УНС РКН СК размещаются в отсеке автоматики ГПА и выполнены в виде шкафов одностороннего обслуживания.
Стойка управления размещается в операторной и обеспечивает возможность управления и контроля ГПА.
В состав САУ ГПА входят:
программно-аппаратные средства «Ser
аппаратура для представления и регистрации информации;
приборы контроля вибрации;
топливный клапан с сервоприводом
антипомпажный клапан;
датчик перепада давления;
барьеры искробезопасности;
панель для установки барьеров искробезопасности;
датчики и сигнализаторы;
исполнительные механизмы входящие в состав ГПА.
САУ ГПА осуществляет сбор преобразование и обработку полученной отдатчиков сигнализаторов и исполнительных механизмов (ИМ) агрегата информации автоматическое управление и защиту агрегата во всех режимах его работы антипомпажное регулирование а также отображение оперативной информации о состоянии ГПА на экране станции контроля и управления. Все необходимые функции регулирования технологическими параметрами и предотвращения аварийных режимов ГПА осуществляются программно-аппаратными средствами «Series 4» установленными в стойке ЦВК-УНС.
Датчики температуры устанавливаемые в отсеке нагнетателя обыкновенного исполнения аналоговые сигналы подаются через барьеры искробезопасности (БР) установленные на панели ЕN.
Управление ГПА будет осуществляться централизованно по цифровому каналу связи от САУ КЦ;
Команды управления со стойки СУ поступают в стойку ЦВК-УНС по двум интерфейсным каналам обеспечивающим обмен цифровыми данными между программно-аппаратными средствами «Series 4» и станцией контроля и управления ХYСОМ а также по физическим каналам с помощью которых передаются дискретные команды от кнопок и принимаются донесения на органы индикации.
Команды управления исполнительными механизмами ГПА от программно-аппаратных средств «Series 4» выдаются через релейный коммутатор нагрузок (РКН).
Автоматическое поддержание заданной частоты вращения ТНД на всех режимах работы осуществляется за счет управления топливным клапаном РК.
Противопомпажное регулирование на всех режимах работы ГПА осуществляется управлением антипомпажным клапаном рециркуляции АПК с корректировкой частоты вращения ТНД.
Питание составных частей САУ ГПА осуществляется от стабилизированных преобразователей напряжения. Питание установки осуществляется переменным током с напряжением 220 В и постоянным током с напряжением 27 В от резервного источника (аккумуляторных батарей).
Вся система автоматизации компрессорных станций базируется на работе различного типа датчиков и приборов.
Система автоматического управления компрессорного цеха представляет собой комплекс программно-технических средств включающий в себя:
шкаф контроля управления и сигнализации со встроенным плоскопанельным компьютером и выдвижной клавиатурой с манипулятором типа TouchPad (АСА2.556.498);
автоматизированное рабочее место выполненного на базе ПЭВМ
пульт аварийного останова устанавливаемый на рабочем столе оператора.
Для автоматизации расхода газа необходимо большое количество измерений параметров. Средства измерения расхода газа должны удовлетворять жестким требованиям взрывобезопасности надежности и иметь приемлемый показатель ценакачество.
Для этой цели используется комплексный датчик «Гипер-Флоу-3Пм» в основу конструкции которого положен метод переменного перепада давления на сужающем устройстве и в системе с применением счетчиков и датчиков объемного расхода газа (работа в режиме корректора). Поэтому при проведении патентного поиска особое внимание было уделено анализу средств измерения расхода газа сужающим устройством.
Система автоматического регулирования ГТУ выполнена по схеме непрямого регулирования с пневматическими серводвигателями и усилителями. Воздух для работы системы отбирается из станционного коллектора сжатого воздуха в который подается через отборы из осевых компрессоров работающих ГПА или от поршневого компрессора с приводом от электродвигателя переменного тока. Перед использованием в системе воздух охлаждается и очищается в блоке воздухоподготовки. Давление воздуха в САР поддерживается 014 МПа регулятором давления «после себя». Электромагнитный вентиль (ЭМВ5) на подводящем трубопроводе к регулятору давления (РД) используется для отключения подачи воздуха к системе когда агрегат остановлен.
Основными регулирующими органами системы являются стопорный (СК) и регулирующий (РК) клапаны. Положение РК определяет количество газового топлива подводимого к камере сгорания. В качестве привода этих клапанов используются мембранные пневматические сервомоторы.
Основным регулятором в системе является регулятор скорости (РС) поддерживающий заданную частоту вращения вала нагнетателя. Импульсом РС служит напор масла от насоса-импеллера установленного на валу ТНД. Регулятор скорости снабжен механизмом датчика частоты вращения подключенным к системе автоматического управления. На работающем агрегате ДРС можно управлять дистанционно с помощью кнопок «РС ВЫШЕ» и «РС НИЖЕ» расположенных на пульте управления ГПА.
Основные связи в пневматической системе обеспечиваются тремя линиями - постоянного давления проточной и предельного регулирования. В проточную линию воздух поступает из линии постоянного давления через дроссельную шайбу диаметром 4 мм. Проточная линия осуществляет связь между РС ограничителем приемистости (ОП) золотником с электромагнитным приводом (ЭМП) малоинерционного регулятора температуры золотником отсечным (ЗО) и серводвигателем регулирующего клапана. В РС ЭМП и ОП воздух из проточной линии может выпускаться в атмосферу.
Количество выпускаемого воздуха определяет давление в проточной линии а оно в свою очередь положение РК и выпускных клапанов (ВВК1 ВВК2). По мере снижения давления в проточной линии РК прикрывается а при увеличении давления – открывается.
Воздух в линию предельного регулирования поступает из линии постоянного давления через дроссельную шайбу диаметром 33 мм. Эта линия связывает регулятор скорости электромагнитные вентили ЭМВ1 и ЭМВ2 серводвигатель стопорного клапана пневматические выключатели (ПВ) автоматов безопасности вала силовой турбины (АБ тнд) вала турбокомпрессора (АБ твд) и вала турбодетандера (АБ тд). Давление в линии предельного регулирования определяет положение стопорного клапана.
Стопорный клапан открыт если в РС ЭМВ1 ЭМВ2 и ПВ выпуск воздуха в атмосферу перекрыт и давление в линии предельного регулирования равно 014 МПа. При открытии сброса воздуха в одном из перечисленных устройств давление в линии снижается и СК закрывается.
Ограничитель приемистости (ОП) предназначен для ограничения максимальной температуры (не более плюс 800 С) продуктов сгорания поступающих в ТВД. Ограничитель приемистости устанавливает максимально возможное открытие РК по подаче топлива в камеру сгорания в зависимости от давления воздуха за компрессором. Работает ОП по принципу ограничения давления воздуха в проточной линии.
В нагнетании осевого компрессора установлены два воздушных выпускных клапана (ВВК1 и ВВК2) работающих параллельно. Эти клапаны сбрасывают в атмосферу воздух при остановке ГПА или при сбросе нагрузки. В первом случае выпуск воздуха сокращает время выбега роторов турбины и продувки горячей проточной части холодным воздухом во втором – снижает заброс частоты вращения ротора силовой турбины.
Отсечной золотник (ЗО) используется для усиления управляющего импульса к выпускным клапанам. К золотнику подводится воздух из двух линий – постоянного давления и проточной. При снижении давления в проточной линии до 004 005 МПа золотник отсекает подвод воздуха из линии постоянного давления к выпускным клапанам и они открываются под действием потока воздуха из ОК.
В целях предохранения осевого компрессора от помпажа на пуске ГТУ за его четвертой ступенью установлено непосредственно на корпусе компрессора восемь сбросных клапанов (СБК) для выпуска части воздуха в атмосферу. В период пуска ГТУ когда давление за четвертой ступенью ОК низкое клапаны под действием пружины удерживаются в открытом положении. По мере увеличения частоты вращения компрессорного вала растет перепад давления воздуха действующий на тарелку клапана и создающий усилие для его закрытия. СБК закрываются при достижении частоты вращения вала компрессора 4200 4300 мин-1.
Автоматы безопасности (АБ) предназначены для остановки турбоагрегата при увеличении частоты вращения роторов до предельно допустимого значения. ТВД ТНД и ТД защищают бойковые автоматы безопасности. При вращении вала ротора на боек АБ действует центробежная сила которая при частоте вращения ниже допускаемой уравновешивается натяжением пружины. При достижении предельной частоты вращения центробежная сила действующая на боек и натяжение пружины сравниваются. Дальнейшее повышение оборотов вызывает увеличение центробежной силы и боек сжимая пружину выходит из вала ударяет по рычагу вызывая срабатывание пневматического выключателя (ПВ).
В пневматическом выключателе открывается клапан давление в линии предельного регулирования падает закрывается стопорный клапан турбина останавливается. Автоматы безопасности турбодетандера (АБтд) и турбокомпрессорного вала (АБтвд) воздействуют на один пневматический выключатель. Автомат безопасности силового вала (АБтнд) воздействует на свой выключатель. Все три АБ конструктивно оформлены одинаково. Отличаются они в основном только размерами бойка.
Перед пуском газоперекачивающего агрегата электромагнитный вентиль ЭМВ5 закрыт. Воздух из станционного коллектора не подается в систему регулирования.
Регулятор скорости находится в исходном состоянии – «РС МАХ». Открыты в нем полностью сбросы воздуха из линий предельного регулирования и проточной. Избыточное давление воздуха в этих линиях отсутствует стопорный и регулирующий клапаны под действием своих пружин удерживаются в закрытом положении. Выпускные воздушные клапаны (ВВК1 и ВВК2) закрывают выход воздуха из нагнетателя компрессора.
Отсутствует напряжение на электромагнитных вентилях ЭМВ1 ЭМВ2 и они закрыты. Выпуск воздуха из линии предельного регулирования через эти вентили перекрыт.
В дроссельном золотнике с электромагнитным приводом и ограничителе приемистости (ОП) отверстия для выпуска воздуха из проточной линии перекрыты.
Пневмовыключатели автоматов безопасности находятся в рабочем положении. Сброс воздуха из линии предельного регулирования через их клапаны перекрыт.
3 Работа системы регулирования при поддержании заданной нагрузки
Поддержание заданной частоты вращения силового вала (в пределах от минимальной 3300 мин-1 до максимальной 5000 мин-1) осуществляется следующим образом. Если по какой-либо причине частота вращения ТНД снизится то из-за уменьшения напора на импеллере поршень в регуляторе скорости опустится вниз. Выпуск воздуха из проточной линии уменьшится давление в ней возрастет. Регулирующий клапан приоткроется и снижение частоты вращения прекратится. При повышении частоты вращения ТНД регулятор скорости действует в обратном порядке. Снижается давление в проточной линии и регулирующий клапан прикрывается. Неравномерность работы регулятора скорости при номинальной частоте вращения составляет 4–5. При работе агрегата давление в проточной линии изменяется в пределах от 006 до 012 МПа. Это изменение соответствует полной перестановке регулирующего клапана.
В случае мгновенного сброса нагрузки и резком увеличении частоты вращения ТНД регулятор скорости может увеличить выпуск воздуха из проточной линии настолько что закроется регулирующий клапан и откроются выпускные клапаны. После открытия выпуска воздуха за ОК увеличение частоты вращения вала ТНД прекратится.
Когда частота вращения с учетом имеющейся неравномерности восстановится и выпускные клапаны закроются регулирующий клапан откроется на величину необходимую для поддержания заданной частоты вращения уже для сниженной нагрузки.
Устройство нормализации и сигнализации (УНС) предназначено для преобразования (нормализации) сигналов первичных преобразователей датчиков постоянного и переменного тока в унифицированный выходной сигнал 0–10в отрицательной полярности пропорциональный значению контролируемого параметра (температура давление и т.п.) и для сравнения унифицированных сигналов с уставками предельных значений параметров.
Устройство позволяет принимать по 36 каналам сигналы низкого уровня от первичных по 20 каналам унифицированный сигнал 0 10 В. Каждая группа из 28 каналов обеспечивается 30 уставками сигнализации.
В настоящее время к загрязнению среды принято относить все факторы которые оказывают вредное воздействие как на самого человека так и на организм живой природы.
В ГТУ не всё подводимое с топливом тепло превращается в полезную работу. Большая часть его (65-75% в зависимости от КПД) выбрасывается в окружающую среду. Тепло попадает в атмосферу при выбросе выхлопных газов что изменяет микроклимат в зоне расположения источника выброса. Это тепло интенсивно рассеивается и не представляет для окружающей среды большой опасности.
Более серьёзные последствия влечёт за собой сброс в водоёмы нагретой охлаждающей воды. Повышая температуру воды в водоёмах и уменьшая тем самым концентрацию растворённого в ней кислорода что неблагоприятно влияет на биологические и химические процессы определяющие жизнедеятельность растительных и животных организмов населяющих водоёмы.
В основе рабочего процесса ГТУ лежит процесс горения топлива поэтому их развитие и применение сопровождается как возрастанием потребления топлива так и увеличением масштабов загрязнения атмосферы выхлопными газами. Эти газы представляют собой смесь продуктов сгорания с избыточным горением. В общем случае продукты сгорания могут содержать:
продукты полного сгорания горючих компонентов топлива;
компоненты неполного сгорания топлива;
золовые частицы образующиеся из негорючих минеральных примесей.
Выхлопные газы загрязняя атмосферу приводят к уменьшению потока солнечной энергии на поверхности земли к ухудшению видимости в результате поглощения и рассеивания света взвешенными частицами. Эти частицы представляют также серьёзную угрозу для здоровья человека – попадая в органы дыхания они приводят к тяжёлым заболеваниям.
Отрицательные воздействия на организм человека оказывают также вибрация и шум производимые ГТУ. Поражаются органы слуха зрения возникают различные заболевания.
Все вышеперечисленные вредные воздействия ГТУ необходимо устранить либо уменьшить. Применение регенерации тепла отработанных газов повышает КПД цикла ГТУ на 6%снижает тепловые выбросы в атмосферу на 200 С и экономит расход топливного газа около.
Газоходы являются обязательными составляющими газовых трактов. Газоходы изготавливаются из металла. Чаще всего они имеют круглое сечение а для восприятия температурных удлинений оснащены компенсаторами. Газоходы помогают отводить продукты сгорания: дымовые и газовые смеси. Они вырабатываются в процессе горения газа. Газоход способствует и достаточному поступлению в агрегат воздуха создавая хорошую тягу.
При одновременном совместном присутствии в выбросах веществ однонаправленного вредного действия их безразмерная суммарная концентрация не должна превышать единицы (8.1).
где – фактические концентрации вредных веществ в атмосферном воздухе мгм3;
– предельно допустимая концентрация вредных веществ в атмосферном воздухе мгм3.
Главным фактором влияющим на рассеивание токсичных веществ является ветер.
Основным мероприятием по снижению концентраций загрязняющих веществ в атмосфере является выброс дымовых газов на максимально возможную высоту. Для этого проектом предусмотрен расчет минимальной высоты дымовой трубы которая обеспечит требуемые параметры концентрации загрязняющих веществ в призменном слое.
При высоких температурах в ядре факела топок происходит частичное окисление азота содержащегося в воздухе и топливе поэтому при работе на природном газе уходящие газы содержат вредные вещества – оксиды азота.
По сложившейся методике расчет выбросов ведется в пересчете на диоксид азота .
Основным топливом является природный газ = 3672 МДжкг – низшая теплота сгорания; = 0758 кгм3 – плотность газа при температуре и давлении Р = 010132 МПа. При правильной эксплуатации основными токсичными примесями содержащимися в дымовых газах являются окислы азота. Максимальный расход газа на ГТК 10-4 составит 2939 м3ч.
Состав газа: СН4 – 949%; С2Н6 – 32%; С3Н8 – 04%; С4Н10 – 01%; С5Н12 – 01%; N2 – 09%; СО2 – 04%; = 3672 МДжкг.
Теоретический необходимый объем воздуха (8.2):
где m и n – число атомов углерода и водорода в химической формуле углеводородов входящих в состав топлива.
Теоретические объемы продуктов сгорания топлива:
а) Объем трехатомных газов (8.3):
б) объем двухатомных газов (8.4):
в) объем водяных паров (8.8):
где d – влагосодержание топлива отнесенное к 1 м3 сухого газа d = 10 гм3.
Теоретический объем дымовых газов (8.9):
Полный объем продуктов сгорания зпри нормальных условиях при сжигании 1 м3 природного газа с м3м3:
В топочной камере образуется окись азота NO (более 95 %). Образование двуокиси азота NO2 за счет окисления NO происходит при низких температурах.
Выброс окислов азота рассчитывается по NO2 (8.10):
где – коэффициент зависящий от степени снижения выбросов окислов азота в результате применяемых технических решений = 001;
В – расход топлива м3с;
– низшая теплота сгорания топлива МДжкг (= 3672 МДжкг);
– параметр характеризующий количество окислов азота образующихся на МДж теплоты кгМДж.
Расчет высоты дымовой трубы. Отвод дымовых газов от турбины ГТК-10-4 производится в дымовую трубу высотой 25 м диаметром устья 09 м.
Минимально допустимая высота дымовой трубы при которой максимальная концентрация вредных выбросов не превышает ПДК определяется по формуле (8.11):
где А – коэффициент зависящий от метеорологических условия в данном районе;
z – число дымовых труб;
F – коэффициент учитывающий характер выбрасываемых веществ.
m – коэффициент учитывающий влияние скорости выхода газов из устья трубы;
n – коэффициент связанный с опасной скоростью ветра;
– объёмный расход дымовых газов через дымовую трубу;
– разность температур дымовых газов и атмосферного воздуха в теплый период года С (8.12):
где tгазов – температура дымовых газов С;
tвозд – температура воздуха в теплый период С.
ПДКNOx = 0085 мгм3 – концентрация вредных выбросов в атмосферном воздухе которая может быть создана дымовой трубой без превышения ПДК:
Существующая труба высотой 25 м удовлетворяет рассеиванию вредных веществ дымовых газов до концентрации меньше чем ПДК.
Ремонт ГПА – это технически сложный и трудоемкий процесс выполняемый с использованием грузоподъемных механизмов пневмо- и электроинструмента газо- и электросварки специальных приспособлений и механизмов.
Процесс ремонта производится в действующем цехе где работают другие ГПА а трубопроводы находятся под давлением газа масла воды и воздуха предъявляет повышенные требования к организационно техническим мероприятиям по подготовке агрегата к ремонту с целью создать безопасные условия труда для ремонтного персонала.
К основным организационно- техническим мероприятиям следует отнести:
Отключение ГПА от технологических коммуникаций и обеспечение невозможности случайной или преднамеренной подачи газа в трубопроводы обвязки нагнетателя. С этой целью необходимо: закрыть краны №1 2 4 6 и стравить газ через кран №5; отключить систему управления кранами - электрическую цепь и импульсный газ; обеспечить невозможность случайной или преднамеренной перестановки кранов обвязки нагнетателя посредством установки замков демонтажа органов ручного управления блокировкой переключателей и насосов демонтажем подводящих трубок. На открытые краны вывесить плакаты «Не закрывать» на закрытые краны – «Не открывать». Вскрыть люки-лазы на трубопроводах между нагнетателями и кранами №1 и 2 установить специальные шары со стороны нагнетателя обеспечивающие закрытие обвязки нагнетателя.
Отключение ГПА от трубопроводов топливного и пускового газа и обеспечение невозможности случайной или преднамеренной подачи газа к узлам агрегата. С этой целью необходимо: закрыть краны №12 12 бис 11 и стравить газ через крап №9 кран №10 при этом открыт; отключить систему управления кранами – электрическую цепь и импульсный газ; обеспечить невозможность случайной или преднамеренной перестановки кранов топливного и пускового газа выполнив мероприятия аналогичные в пункте 1; вывесить в необходимых местах запрещающие и предупреждающие таблички установить на трубопроводах топливного и пускового газа силовые заглушки.
Отключение ГПА от электропитающих систем посредством выкатывания ячейки вводных автоматов с установкой плакатов «Не включать работают люди!».
Опорожнение всех масляных систем ГПА в том числе и маслобаков. На подводящих маслопроводах устанавливаются силовые заглушки.
Оформление всей необходимой документации по выводу ГПА в ремонт с оповещением об этом всего персонала КС.
Проведение всех мероприятий по выводу агрегата в ремонт проверяется представителями эксплуатационной и ремонтной организаций о чем составляется соответствующий акт.
Вскрытие агрегата проводят после подписания акта о его сдаче в ремонт. К акту сдачи прилагается ведомость технических показателей ремонтные формуляры предварительная ведомость дефектов. Основные требования к ремонтным работам сводятся к следующему:
соблюдение установленной технологии ремонта;
устранение выявленных дефектов;
ведение работ в строгом соответствии с сетевым графиком;
сдача эксплуатационному персоналу отремонтированных деталей и узлов.
Все работы по ремонту агрегата производятся только по технологии разработанной заводом- изготовителем ГПА. Конструктивные изменения основного оборудования изменение технологических и принципиальных схем агрегата во время ремонта могут производиться по согласованию с заводом изготовителем.
В процессе ремонта ГПА начальник КС или инженер по ремонту производят приемку из ремонта отдельных отремонтированных узлов вспомогательных механизмов с оформлением соответствующих актов и формуляров.
Перед сборкой ГПА рабочие поверхности деталей воздушные и масляные каналы должны быть очищены промыты и продуты сжатым воздухом трущиеся поверхности притерты и смазаны маслом используемым в маслосистеме ГПА. Узлы необходимо собирать согласно маркировке с установкой только отремонтированных деталей. Для предохранения резьбы крепежа турбины от пригорания можно использовать специальные составы на основе порошка дисульфид молибдена или серебристого графита. Перед нанесением состава резьбовая поверхность должна быть очищена и обезжирена бензином или ацетоном. Состав необходимо наносить мягкой льняной тряпкой до получения равного тонкого слоя. Для предохранения вкладышей от ржавчины и обойм лабиринтовых уплотнений от пригорания их контактируемые поверхности рекомендуется натирать сухим графитом.
При сборке резьбовых соединений для обеспечения прилегаемости стыков и сохранения целостности резьбы необходимо выполнять следующие правила:
использовать крепеж только с исправной резьбой;
в целях избежания пригорания не применять смазку резьбы маслом или составом разведенном на олифе;
не допускать люфта резьбовых соединений;
затяжку производить последовательным обходом диаметрально противоположных болтов и шпилек;
крутящий момент приложенный при затяжке к болту или шпильке должен вызывать в них напряжение не более (05 06)g где g – предел текучести;
торцы гаек должны быть перпендикулярны резьбе и параллельны фланцам;
шпильки должны заворачиваться до упора торцевой части и не до конца резьбовой части если резьбовая вворачиваемая часть шпильки окажется короче глубины резьбовой части фланца необходимо в отверстие положить шайбу;
при сборке фланцев трубопроводов необходимо обеспечить их соосность и параллельность причем площадь прилегания торцевых поверхностей по краске не должна быть не менее 70%;
для обеспечения герметичности разъемов необходимо применять уплотняющие составы и материалы.
Начинать и заканчивать работу по сборке узлов должен один исполнитель. Объем контрольных измерений зазоров и натягов при сборе должен соответствовать объему измерений при разборке.
Сборку турбины и компрессора необходимо выполнять в такой последовательности:
установить нижние половины обойм лабиринтовых уплотнений вкладышей;
плавающие кольца главного масляного насоса и импеллера обоймы масляных уплотнений;
уложить роторы согласно карте технологического процесса соблюдая при этом все размерные цепи;
установить нижние половины колец с рабочими и установочными колодками;
установить верхние половины вкладышей и кольца с колодками упорного подшипника;
поставить установочные штифты и обтянуть крепеж;
установить в крышке подшипников верхние обоймы масляных уплотнений и закрыть подшипники крышками;
установить верхние половины обойм лабиринтных уплотнений поставить установочные штифты обтянуть крепеж;
перед закрытием турбины и компрессора для проверки отсутствия задеваний провернуть ротор;
после нанесения мастики закрыть крышки корпусов;
по направляющим стойкам опустить крышку оставляя 3 5 мм до нижнего разъема установить контрольные штифты.
При сборке нагнетателя следует обратить особое внимание на установку торцевых уплотнений и подшипников проверку осевого разбега ротора.
Вывод агрегата из ремонта и приемка его в эксплуатацию производит комиссия в полном соответствии с положением о планово- предупредительном ремонте ГПА. Перед пуском агрегата в работу проверяется вся ремонтная документация: данные ремонтных формуляров наличие актов на закрытие агрегата и его узлов на осмотр и очистку воздушного и газового трактов на опрессовку системы регулирования и маслоснабжения ГПА а также системы уплотнения центробежного нагнетателя. Проверяются установочные величины системы регулирования и защит проводится контрольный анализ масла.
Перед пуском агрегата в работу необходимо провести:
осмотр воздухозаборной камеры с целью проверки отсутствия в ней посторонних предметов;
проверку положений запорной арматуры подвергшейся открытию или закрытию во время ремонта а также заполнение гидросистем кранов гидравлической жидкостью;
проверку действия и включение всех контрольно-измерительных приборов систем автоматики аварийной и предупредительной сигнализации с оформлением протокола проверки;
проверку пусковых резервных аварийных и уплотнительных насосов а также устройств их автоматического включения и соответствия давления масла в системе величинам указанным в инструкции завода изготовителя;
проверку работы регулятора перепада давления «масло- газ» совместно с проверкой кранов «гитары» и заполнением контура нагнетателя;
осмотр системы маслоснабжения агрегата.
Особый контроль при пуске ГПА после его ремонта уделяется:
системе маслоснабжения агрегата;
узлам системы регулирования и их взаимодействию;
механическим задеваниям в узлах и проточных частях ГПА;
уровню вибрации узлов агрегата;
тепловому расширению корпусов ГПА;
наличию утечек воздуха продуктов сгорания и масла.
После обкатки ГПА при отсутствии дефектов и соответствии его параметров техническим условиям завода- изготовителя производится приемка агрегата в эксплуатацию. Качество проведенного ремонта ГПА оценивают по таким критериям как приведенная мощность ГПА коэффициент полезного действия вибрационное состояние агрегата.
После приемки агрегат проверяется в работе непрерывно под нагрузкой в течение 72 ч после чего дается предварительная оценка качества проведенного ремонта. Если в процессе этой работы обнаруживаются какие-либо дефекты ремонт считается незаконченным. Дефекты устраняются после чего ГПА вновь проверяется в работе под нагрузкой в течение 24 ч.
В течение месяца работы под нагрузкой после приемки агрегата из ремонта должны быть проведены эксплуатационные испытания ГПА в результате которых необходимо определить его основные входные показатели (мощность КПД) сравнить их с соответствующими показателями агрегата до проведения ремонта и на основании этого сделать оценку качества проведенного ремонта.
Перед пуском произвести внешний осмотр секции опор для определения их исправности и готовности к пуску и проверку приборов контролирующих работу регенератора с составлением акта проверки.
Режим использования регенератора – базовый: среднегодовой коэффициент использования (по времени) не более 80 % число пусков ГПА в год не более 50.
Регенератор предназначен для работы в макроклиматических районах с умеренным климатом. Климатическое исполнение «УХЛ» (установка на открытом воздухе при температуре от +45 °С до -55 °С) категория перемещения 1 по ГОСТ 15150-69.
Время запуска агрегата до режима холостого хода (нижний предел регулируемых оборотов силовой турбины: 20 30 мин. График изменения температуры продуктов сгорания после турбины (перед регенератором) при пуске и нагружении:
увеличение температуры до величины не более 120 °С в течении 2 5 минут;
увеличение температуры с темпом 20 25 °Смин в течении 7 9 мин;
выдержка на режиме холостого хода в течении 1 2 мин.;
нагружение агрегата с темпом 10 °Смин.
Температура продуктов сгорания за турбиной (перед регенератором) на режиме холостого хода составляет величины указанные в таблице 9.1.
Таблица 9.1 – Температуры продуктов сгорания перед регенератором
Температура атмосферного воздуха С
Предельно допустимая температура за турбиной С
Остаточная запыленность сжатого воздуха после компрессора ГТУ не более 03 мгмЗ (при этом концентрация пыли с размерами частиц не более 20 мкм не выше 003 мгм3; допускается кратковременная концентрация пыли до 5 мгмЗ с частицами размером не более 30 мкм (не более 100 ч в год).
Секции генератора допускают очистку внутри трубного пространства от возможных отложений механическим способом и обдувку сжатым воздухом.
Работу регенератора должны контролировать следующие приборы:
для измерения давления межтрубного пространства;
для измерения температуры сред на входе и на выходе межтрубного и на входе трубного пространства.
Обслуживающий персонал должен следить за состоянием тепловой изоляции и не допускать ее разрушения. При эксплуатации должно быть обеспечено свободное перемещение подвижной опоры секции регенератора которое необходимо периодически визуально проверять.
В процессе работы регенератора не требуется техническое обслуживание.
Bo время планово-предупредительных ремонтов необходимо производить внешний осмотр и периодический контроль плотности не реже 1 раза в 3 года.
К обслуживанию могут быть допущены лица не моложе 18 лет прошедшие медицинское освидетельствование и профессиональную подготовку.
Техническое освидетельствование проводить 1 раз в четыре года гидравлические или пневматические испытания пробным давлением один раз в 8 лет.
Перемещение подвижной опоры контролировать при пусках и остановах. Периодичность контроля перемещения подвижной опоры – не менее 1 раза в год.
Ремонт выполняется персоналом имеющим соответствующую квалификацию и ознакомленным с настоящей инструкцией.
Перед остановом на ремонт провести общий осмотр регенератора зафиксировать параметры работы установки по приборам.
Осмотр ремонт проводить при отключенном регенераторе и всей установки.
Провести проверку плотности регенератора по межтрубному пространству с целью установления наличия неплотностей и мест их распространения.
При проведении ремонтных работ соблюдать необходимые требования по чистоте исключающие попадание пыли грязи посторонних предметов в трубное и межтрубное пространства.
Секции регенератора при необходимости должны быть обеспечены площадками обслуживания с ограждениями необходимыми для безопасного ведения работ.
Ремонт регенератора должен производиться по технологии разработанной в соответствии с настоящей инструкцией.
Для осмотра и проведения ремонта имеются люки-лазы в камерах входа и выхода продуктов сгорания. Перед осмотром и проведением ремонта должна быть обеспечена вентиляция внутренних полостей регенератора в соответствии с требованиями техники безопасности.
Ремонт регенератора связанный с устранением неплотности в трубном пространстве необходимо проводить в следующем порядке:
открыть люки-лазы в камерах подвода и отвода продуктов сгорания;
установить технологические заглушки на трубопроводах подвода и отвода воздуха в наиболее доступных местах;
собрать схему для создания избыточного давления в межтрубном пространстве с подключением к линии сжатого воздуха;
для контроля неплотности создать небольшое избыточное давление воздуха в межтрубном пространстве не более Ризб=02 05 кгссм2;
рекомендуется первоначально на ощупь с использованием бумажных лепестков путем обмыливания или другим способом целить наличие течей.
В случае обнаружения течи с помощью технологических пробок соблюдая меры техники безопасности уточнить конкретное место дефекта – сварной шов или собственно труба при этом поверхность противоположной трубной доски закрыть бумагой пленкой или другим аналогичным материалом с целью исключения влияния естественной тяги через трубы. Места подлежащие ремонту отметить мелом снять давление.
В таблице 9.2 приведен анализ возможных аварийных ситуация на КС.
Таблица 9.2 – Анализ возможных аварийных ситуаций на КС
Наименование аварийной ситуации
При каких условиях возможна аварийная ситуация
Возможное развитие аварии последствий в т.ч. за пределами цеха
Способы и средства предотвращения аварий
Меры по локализации аварии
Разрыв газопроводов природного газа
Механическое повреждение электрохимическая коррозия
Выброс газа возможно возгорание или взрыв
Профилактические мероприятия по контролю за сварными швами газопроводов выполнение антикоррозийной обработки
Отключить поврежденный участок открыть свечи на поврежденном участке
Разрыв трубопроводов горячей воды
Выброс горячей воды попадание воды в электрические щиты или на электро-оборудование
Профилактические мероприятия по контролю за сварными швами трубопроводов выполнение антикоррозийной обработки
Отключить поврежденный участок
Возгорание газоперекачивающего агрегата
Попадание масла на нагретые поверхности турбоагрегата
Разрушение ГПА вспомогательного оборудование
Профилактические мероприятия по контролю за целостностью маслопроводов
Аварийный останов турбоагрегата с последующем включением системы пенопожаротушения
Продолжение таблицы 9.2
Исчезновение напряжения на устройствах дистанционного и автоматического управления
Прекращение электроснабжения щитов управления
Отсутствие контроля за работой ГПА выход турбоагрегата в помпаж с последующем его разрушением
Профилактические мероприятия
Аварийный останов ГПА
Экономическая часть проекта включает в себя оценку выбранного варианта технического решения на основе сравнения капитальных затрат на модернизацию текущих затрат на эксплуатацию и срока окупаемости проекта. Управленческая часть проекта выполняется для создания структуры реализации проекта модернизации.
Стоимость оборудования и монтажных работ определяется по прейскуранту завода-изготовителя и сведена в таблицу 10.1 [38 41 43 44 46].
Таблица 10.1 – Стоимость оборудования и материалов
Газотурбинный агрегат-регенератор пластинчатый трубчатый РГУ-1800-01
Лабиринтно-винтовое уплотнение на всасе компрессора
Чугунная всавка в обойме компрессора
Прямоточное уплотнение с металлоерамической вставкой на нагнетании компрессора
Пламенная труба камеры сгорания компрессора
Газодинамическое напыление металлокерамического покрытия
Программно-аппаратное средство «Series 4» со станцией XYCOM
Топливный клапан с сервоприводом Baltur BT 17 SPN
Антипомпажный клапан АМ332
Датчик перепада давления
Продолжение таблицы 10.1
Светозвуковые сигнализаторы
Исполнительные механизмы
Шкаф контроля TouchPad (ACA2.556.498)
Определим остальные составляющие капитальных затрат:
– монтажные работы (10.1):
где К1 – общая стоимость оборудования тыс. руб.;
– транспортные расходы на доставку и складирование оборудования (10.2):
где К1 – итоговая стоимость оборудования тыс. руб.;
Общие капитальные вложения в реконструкцию котельной (10.3):
где Км – итоговая стоимость монтажных работ тыс. руб.;
Кпр – стоимость проектных работ тыс. руб.;
Годовые затраты на природный газ (10.4):
где Цт – тариф на природный газ руб.м3 (Цт = 2970 руб.м3 – по данным ПАО «Газпром трансгаз Сургут» [40]);
Вгод – годовой расход газа млн.м³год.
Годовой фонд основной и дополнительной зарплаты всех категорий персонала составит 22800 тыс. руб.год (по данным ПАО «Газпром трансгаз Сургут»).
Отчисления на социальные нужды (10.5):
где НС – процент отчислений на социальные нужды % (34%).
Содержание и эксплуатация энергооборудования включая содержание оборудования и его текущий ремонт (10.6):
где 001 – 1% на содержание и эксплуатацию энергооборудования;
– 10% на амортизацию энергооборудования;
К2 – балансовая стоимость оборудования ГТК 10-4 тыс.руб.
Цеховые расходы включая зарплату персонала управления цеха содержание и текущий ремонт цеховых зданий и сооружений (10.7):
где 00025 – 025% на цеховые расходы;
Прочие производственные расходы (10.8):
где 01 – 10% на прочие производственные расходы;
– сумма зарплат всех категорий персонала тыс.руб.год.
Сумма всех затрат (10.9):
Сводная таблица результатов расчетов калькуляции текущих затрат на энергетическое обслуживание ГТК 10-4 с учётом модернизации представлена в таблице 10.2.
Таблица 10.2 – Сводная таблица результатов расчетов калькуляции текущих затрат на обслуживание ГТК10-4 с учетом модернизации
Показатели и статьи затрат
Годовые затраты на природный газ
Основная и дополнительная зарплата всех категорий персонала
Отчисления на социальные нужды
Содержание и эксплуатация энергооборудования включая содержание оборудования и его текущий ремонт амортизацию оборудования
Цеховые расходы включая зарплату персонала управления цеха содержание и текущий ремонт цеховых зданий и сооружений
Прочие производственные расходы
Проведем расчет текущих затрат на энергетическое обслуживание ГТК 10-4 до модернизации.
Годовые затраты на природный газ:
Содержание и эксплуатация энергооборудования включая содержание оборудования и его текущий ремонт:
Цеховые расходы включая зарплату персонала управления цеха содержание и текущий ремонт цеховых зданий и сооружений:
Сводная таблица результатов расчетов калькуляции текущих затрат на энергетическое обслуживание ГТК 10-4 до модернизации представлена в таблице 10.3.
Таблица 10.3 – Сводная таблица результатов расчетов калькуляции текущих затрат на обслуживание ГТК 10-4 до модернизации
Экономия текущих затрат составит (10.10):
где И1 – общая сумма затрат на обслуживание ГТК 10-4 после модернизации;
И2 – общая сумма затрат на обслуживание ГТК 10-4 до модернизации.
И =553565830 – 407467260 = 1460970 тыс. руб.год
Экономическая эффективность принятых технических решений может быть определена таким показателем как срок окупаемости. Для определения срока окупаемости проекта модернизации используют формулу (10.11):
где К капитальные затраты;
И экономия текущих затрат тыс. руб.год.
Вывод: по результатам расчета получили срок окупаемости проекта менее 5 лет соответственно данный проект модернизации экономически эффективен. Основная экономия текущих затрат достигается за счет снижения затрат на топливо (природный газ).
SWOT-анализ – это определение сильных ислабых сторон проекта атакже возможностей иугроз исходящих изего ближайшего окружения (внешней среды): сильные стороны (Strengths)– преимущества предприятия (проекта); слабые стороны (Weaknesses)– недостатки предприятия (проекта); возможности (Opportun угрозы (Threats)– факторы которые могут потенциально ухудшить положение предприятия нарынке.
Так как работа посвящена модернизации ГТК 10-4 то рассмотрим вариант «ГТК 10-4 без модернизации» (таблица 10.4).
Таблица 10.4 – SWOT-анализ работы ГТК 10-4 без модернизации
) Опыт работы с существующим оборудованием;
) Отсутствие затрат на разработку проекта и переобучение персонала;
) Отсутствие затрат на покупку оборудования;
) Большие затраты на текущий ремонт оборудования;
) Менее надежная автоматизация;
) Возможность отказа существующего оборудования;
Продолжение таблицы 10.4
) Устойчивый спрос на тепловую энергию;
) Увеличение цен на природный газ;
ГТК 10-4 с проведением модернизации приведена в таблице 10.5.
Таблица 10.5 – SWOT-анализ работы ГТК 10-4 с проведением модернизации
) Эффективное использование теплоты уходящих газов;
) Повышение уровня автоматизации производства;
) Увеличение межремонтного периода;
) Бесперебойная работа оборудования;
) Поиск новых поставщиков оборудования;
) Затраты на переоборудование КИПиА;
) Затраты на разработку проекта;
) Существование новых технологий в сфере газотурбинного и регенерационного оборудования;
) Задержки с поставкой нового оборудования и материалов;
Модернизация ГТК 10-4 является лучшим вариантом так как мы получим больше преимуществ сможем использовать больше возможностей но при этом недостатки проекта решаются проведением данного проекта.
Дерево целей представляет структурную модель показывающую подчиненность и связь целей подразделений в иерархии управления. Дерево целей решает две актуальные задачи:
Показывает кратчайший путь к достижению сложных стратегически важных результатов;
Объединяет все возможные цели предприятия в стройную систему.
Суть методики в том чтобы структурировать и выстроить иерархию целевых установок от сложных к простым и отобразить её в формате графа – наглядной графической схемы.
Существует несколько определений для дерева целей проекта. Его характеризуют как:
иерархическую систему целевых установок организации;
графическую модель стратегического развития компании;
совокупность целей предприятия на долгосрочную перспективу;
комплексную систему разноуровневых задач.
Воспользоваться деревом целей нельзя: оно уникально для каждого проекта и зависит от её специализации организационной структуры и других параметров.
На рисунке 10.1 изображено дерево целей проекта модернизации ГТК 10-4.
Рисунок 10.1 – Дерево целей проекта модернизации ГТК 10-4
6 Оценка движущих и сдерживающих сил и ресурсов
Соотношение влияния движущих сил и сдерживающих сил показано на рисунке 10.2.
Рисунок 10.2 – Поле сил изменений системы «ГТК 10-4»
К самой сильной движущей силе можно отнести постоянный спрос на тепловую энергию и более дешевая себестоимость 1 Гкал тепла с техническое перевооружение котельной так как при постоянном спросе продукции проект окупится через расчетные 04 года а далее сможет приносить прибыль. На одной линейке средней значимости стоят движущие силы применение новых технологий стимулирование персонала и снижение текущих затрат потому что все это сказывается на косвенном снижении себестоимости тепла повышении автоматизации производства и качественном выполнении своих задач обслуживающим и ремонтным персоналом.
Среди сдерживающих сил к сильной отнесем затраты на разработку и внедрение проекта потому что капитальные затраты на техническое перевооружение котельной являются большим вложением но при этом единоразовым что минимизируется расчетным сроком окупаемости. По данному полю сил можно сделать вывод о том что движущие силы в совокупности с потенциалом изменений преобладают над сдерживающими. Это значит что проект может быть реализован а после проведения реконструкции котельная будет обеспечивать теплом потребителей эффективнее чем в настоящее время.
7 Планирование мероприятий по реализации проекта (график Ганта)
Небольшой комплекс работ может быть показан в виде ленточного графика по этапам проектных работ. График отражает распределение процессов во времени и их последовательность. График отображен в таблице 10.6.
Таблица 10.6 – График Ганта
Продолжительность этапов
с 15.05.2021 по 01.10.2021
Тепловые и мощностные испытания
Составление отчета по результатам испытаний
Инженер-комплектовщик
Доставка оборудования
Транспортная компания
Монтаж регенератора РГУ-1800-01
Монтаж вспомогательных систем
ПНР регенератора РГУ-1800-01
ПНР вспомогательных систем
На основании анализа проделанной работы можно сделать следующие выводы:
Повышение эффективности и модернизация ГТК 10-4 разработана путем установки газотурбинного агрегата-регенератора пластинчато- трубчатого РГУ-1800-01.
Необходимая тепловая мощность составит 514 Гкалч для отопления компрессорной станции.
Для увеличения срока службы и ресурса ГТК 10-4 запланировано установка лабиринтно-винтовых уплотнений на всасе компрессора прямоточных уплотнений с металлокерамическими вставками на нагнетании компрессора чугунные вставки в обойме компрессора и газодинамическое напыление металлокерамических покрытий.
При выборе регенератор ГТК 10-4 рассмотрены котлоагрегаты немецкого итальянского и российского производства.
При хороших технических характеристиках российские регенераторы хорошо совмещаются с существующим основным оборудованием.
В проекте произведён поверочный расчёт дымовой трубы. Существующая дымовая труба 25 м минимизирует влияние выбросов окислов азота на окружающую среду объем выбросов не изменится в процессе модернизации.
Срок окупаемости проекта подсчитан в экономико-управленческой части и составляет приблизительно 04 года.
В заключении хочется отметить что проект показал что модернизация ГТК 10-4 с установкой регенератора РГУ-1800-01 своевременна экономична и экологически эффективна.
Приказ Ростехнадзора от 25.03.2014 №116 «Об утверждении Федеральных норм и правил в области промышленной безопасности правила промышленной безопасности опасных производственных объектов на которых используется оборудование работающее под избыточным давлением» № 38 от 21 сентября 2015 г.;
Приказ Минтруда РФ от 17.08.2015 №551н Об утверждении правил по охране труда при эксплуатации тепловых энергоустановок. Опубликован 07.10.2015 на
Приложение к приказу Министерства труда и социальной защиты Российской Федерации от 24 июля 2013 г. N 328н «Об утверждении правил по охране труда при эксплуатации электроустановок»;
Федеральный закон РФ от 23 ноября 2009 г. № 261-ФЗ Об энергосбережении и о повышении энергетической эффективности и о внесении изменений в отдельные законодательные акты Российской Федерации;
Федеральный закон РФ от 21 июля 2011 г. № 256-ФЗ О безопасности объектов топливно-энергетического комплекса;
Федеральный закон РФ от 18 июля 2011 г. №223-ФЗ О закупках товаров работ услуг отдельными видами юридических лиц;
Приказ Минтруда РФ от 17.08.2015 №551н Об утверждении правил по охране труда при эксплуатации тепловых энергоустановок;
Распоряжение Правительства Российской Федерации от 13.11.2009 г. №1715-р. Об Энергетической стратегии России на период до 2030 года Собрание законодательства РФ. – 2009. –103 с.;
ГОСТ 12.4.011-89. Система стандартов безопасности труда. Средства защиты работающих. Общие требования и классификация. М.: Издательство стандартов 2015. – 44 с.;
ГОСТ 23290–78. Установки газотурбинные стационарные. Термины и определения. М.: Госстандарт России 1978. – 32 с.;
ГОСТ 4.433–86. Установки газотурбинные стационарные. Номенклатура показателей. М.: Госстандарт России 1986. – 23 с.;
ГОСТ31532-2012. Энергосбережение. Энергетическая эффективность. Состав показателей. Общие положения. М.: Госстандарт России 2012. – 64 с.;
ГОСТ 31607-2012. Энергосбережение. Нормативно-методическое обеспечение. М.: Стандартинформ 2013. – 28 с.;
СП 131.13330.2012. Строительная климатология. М.: Минрегион России 2012. – 113 с.;
Стандарт НП АВОК 1.05.2012. Условные графические обозначения в проектах отопления вентиляция кондиционирование воздуха и теплоснабжения. М.: Москва АВОК-пресс 2012. – 24 с.;
СТО ЮУрГУ 04-2008. Стандарт организации. Курсовое и дипломное проектирование. Общие требования к содержанию и оформлению. Челябинск: Издательство ЮУрГУ 2008. – 57 с.;
Алабугин А.А. Экономико-управленческая часть выпускных квалификационных работ для направления подготовки «Теплоэнергетика и теплотехника»: учебное пособие для бакалавров и магистрантов А. А. Алабугин Р.А. Алабугина. Ответственный редактор А.А. Алабугин – Челябинск: Издательский центр ЮУрГУ 2018. – 44 с.;
Алабугина Р.А. Выпускная квалификационная работа: структура требования к оформлению и нормоконтролю: методические указания Р.А. Алабугина. – Челябинск: Издательский центр ЮУрГУ 2017. – 43 с.;
Белов С.В. Безопасность жизнедеятельности: учебник для вузов С.В. Белов В.А. ДевисиловА.В. Ильницкая и др.; Под общей редакцией С.В. Белова.— 8-е издание стереотипное – М.: Высшая школа 2009. — 616 с.;
Булкин А.Е. Автоматическое регулирование энергоустановок – М.:Издательский дом МЭИ 2009. – 508 с.;
Грибанов А.И. Расчёт дымовой трубы А.И. Грибанов. – Челябинск: Издательство ЮУрГУ 2008. – 22 с.;
Зайцев Н.Л. Экономика организация и управление предприятием: учебное пособие Н.Л. Зайцев. – М.: Инфра-М 2008. – 455 с.;
Клименко А.В. Промышленная теплоэнергетика и теплотехника: справоч. лист Изм№ докум.Дата 79 13.03.01.2017.269.05 ПЗ ник А.В. Клименко В.М. Зорина. – М.: Издательство МЭИ 2004. – 327 с.;
Козаченко А.Н. Энергетика трубопро-водного транспорта газов: учебное пособие А.Н. Козаченко В.И. Никишин Б.П. Поршаков. – М.: ГУП Издательство «Нефть и газ» РГУ нефти и газа им. И.М. Губкина 2001. – 400 с.;
Плетнев Г.П. Автоматизация технологических процессов и производств в теплоэнергетике: учебник для студентов вузов Г.П. Плетнев. – М.: Издательский дом МЭИ 2007. – 352 с.;
Поршаков Б.П. Газотурбинные установки на газопроводах Б.П. Поршаков А.А. Апостолов А.Н. Козаченко. – М.: Издательство «Нефть и газ» 2004. – 215 с.;
Прахова М.Ю. Основы автоматизации производственных процессов нефтегазового производства: учебное пособие М.Ю. Прахова Э.А. Шаловников Н.А. Ишинбаев С.В. Щербинин. – М.: Издательский центр «Академия» 2012. – 256 с.;
Росляков П.В. Методы защиты окружающей среды П.В. Росляков. – М.: Издательство МЭИ 2007. – 336 с.;
Рудаченко А.В. Газотурбинные установки для транспорта природного газа: учебное пособие А.В. Рудаченко Н.В. Чухарева. Томск: Издательство Томского политехнического университета 2010. – 217
Соколов Е.Я. Теплофикация и тепловые сети: учебник для вузов Е.Я. Соколов. – М.: Издательский дом МЭИ 2009. – 472 с.;
Соколова Н.А. Аутсорсинг как инструмент сокращения затрат в условиях мирового финансового кризиса Н.А. Соколова Экономика управление и инвестиции: Сборник научных трудов. – Челябинск: Издательский центр ЮУрГУ 2009. – 95 с.;
Трухний А.Д. Основы современной энергетики А.Д. Трухний. – М.: Издательство МЭИ 2008. – 472 с.;
Тупов В.Б. Шумовое воздействие энергетических объектов на окружаю- щую среду и методы его снижения. В справочнике: «Промышленная теплоэнерге тика и теплотехника» под общ.ред. А.В. Клименко В.М. Зорина Издательство МЭИ 2004. – 598 с.;
Щуровский В.А. Энергоэффективность магистрального транспорта газа и потребности в газоперекачивающей технике В.А. Щуровский В.В. Зюзьков М.: Издательство «Компрессорная техника и автоматика» 2011. – 41 с.;
Официальный сайт интернет-магазин сантехники «Сантех-март» –
Официальный сайт Строительство технологии организация –
5. Автоматика ГТК 10-4.cdw
Термопара хромель-алюмелевая
Термопара двойная малоинерционная
Термометр сопротивления медный
Термометр показывающий
пневмотаический электроконтактный
Датчик-реле температуры
Реле давления воздуха
Реле давления дифференциальное
Дифманометр мембранного типа
Дифманометр показывающий сильфонный
Манометр пружинный с электрическим выходом
Милиамперметр узкопрофильный
Кафедра "Промышленная
Повышение эффективности использования теплоты
отходящих газов и модернизация ГТК 10-4 путем замены регенератора
Масло предельной защиты
Спецификация оборудование:
4. РГУ-1800-01.cdw
Кафедра "Промышленная
Повышение эффективности использования теплоты
отходящих газов и модернизация ГТК 10-4 путем замены регенератора
Вход уходящих газов ГТК-10-4
Выход уходящих газов ГТК-10-4
3. ГТК 10-4.cdw
Повышение эффективности использования теплоты
отходящих газов и модернизация ГТК 10-4 путем замены регенератора
2. План оборудования на отметке 0,00.cdw
Кафедра "Промышленная
Повышение эффективности использования теплоты
отходящих газов и модернизация ГТК 10-4 путем замены регенератора
Пункт редуцирования пускового
Емкость сбора конденсата
Установка охлажения газа
Установка очистки газа
Экспликация зданий и сооружений
Блок водопроводных сооружений
(МКНУ) 0-5 куб.мчас с насосами 1865 м
Малогабаритная канализационная установка
в) резервуары хоз.противопожарного
Мойка автомашин с очистными сооружениями
Заглубленный склад инвентаря и оборудования
Вспомогательное здание столовой
е) наливные устройства метанола
д) насосы керосина и одоранта
Стоянка для механизмов
Служебно-эксплуатационный и ремонтный
Резервуары пенного пожаротушения
Емкость аварийного слива масла
Вспомогательные сооружения
Стелажи для хранения труб
д) бункер-отстойник для осадка
г) колодец очистной воды
в) блок-бокс "Кристал
установка перекачки промстоков
б) малогабаритная канализационная
а) эстакада для мойки автомашин
- датчик пожарной сигнализации
Условные обозначения:
Рекомендуемые чертежи
- 24.01.2023
Свободное скачивание на сегодня
Другие проекты
- 24.04.2014