Повышение эффективности использования бульдозера при производстве земляных работ




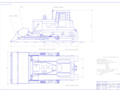
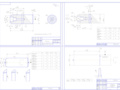
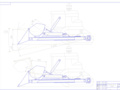
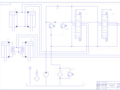
- Добавлен: 25.10.2022
- Размер: 2 MB
- Закачек: 0
Описание
Состав проекта
![]() |
![]() |
![]() ![]() |
![]() ![]() |
![]() ![]() ![]() ![]() |
![]() ![]() ![]() ![]() |
![]() ![]() |
![]() ![]() ![]() ![]() |
![]() ![]() ![]() ![]() |
![]() ![]() ![]() ![]() |
![]() ![]() |
![]() ![]() |
![]() |
![]() ![]() ![]() ![]() |
![]() ![]() |
![]() ![]() ![]() ![]() |
![]() ![]() |
![]() ![]() |
![]() ![]() ![]() ![]() |
![]() ![]() |
![]() |
![]() |
![]() |
![]() |
![]() |
![]() |
![]() |
![]() |
![]() ![]() |
![]() ![]() |
![]() ![]() ![]() ![]() |
![]() ![]() ![]() ![]() |
![]() ![]() |
![]() ![]() |
![]() ![]() ![]() ![]() |
![]() ![]() ![]() ![]() |
![]() |
![]() ![]() ![]() |
![]() ![]() ![]() |
![]() ![]() |
![]() ![]() |
![]() ![]() |
![]() ![]() |
![]() ![]() ![]() |
![]() |
![]() ![]() ![]() |
![]() ![]() ![]() |
![]() ![]() ![]() |
![]() ![]() ![]() |
![]() ![]() ![]() |
![]() ![]() ![]() |
![]() ![]() ![]() |
![]() ![]() ![]() |
![]() ![]() ![]() |
Дополнительная информация
Технология.dwg

Сталь 45 ГОСТ 4543-71
кинематическая схема.dwg

Отвал.dwg

Неуказанные предельные отклонения
Допускаются местные зазоры по прилеганию среднего и крайних
ножей не более 3 мм.
Момент затяжки гаек поз. 9 крепления среднего ножа
гаек поз. 10 крепления боковых ножей
Допускается выступание накладки за плоскость литых ножей не
Технология (булдозер).dwg

Снятие растительного слоя
грунта и его перемещение
за пределы полосы отвода
Разработка и перемещение
Разравнивание грунта
Прицепной каток ДУ-39А
Наименование рабочих
Уплотнение грунта 1-го слоя
ТЕХНОЛОГИЯ СТРОИТЕЛЬСТВА ЗЕМЛЯНОГО ПОЛОТНА
Уплотнение грунта 2-го слоя
Гидросхема.dwg

Экономика.dwg

Заработная плата рабочих
Затраты на технические обслуживания и ремонты
Затраты на смазочные материалы
Затраты на масло для гидросистемы
Затраты на перебазировку
Годовые текущие затраты
Наименование показателей
Годовая эксплуатационная производительность
Годовые текущие издержки потребителя
Экономический эффект
Экономическая эффективность использования бульдозера
с дополнительным ковшом
Прирост производительности в зависимости
от расстояния неремещения грунта
Калькуляция годовых текущих издержек
Расстояние перемещения грунта
Прирост производительности
Рама толкающая.dwg

Неуказанные предельные отклонения
При сборке все сопрягаемые поверхности.
пальцев и отверстий под них смазать солидолом
Вид общий.dwg

Брус толкающий левый
Бульдозер с дополнительным
Техническая характеристика
Масса бульдозера без рыхлителя
Максимальное заглубление отвала
Скорость движения бульдозера
Брус толкающий правый
рама толк.dwg

Брус толкающий левый
Шплинт 545-001 ГОСТ 397-66
отвал.dwg

Гайка М 12 ГОСТ 2524-70
Шайба 12 65Г ГОСТ 6402-70
Экспликация.dwg

ковш.dwg

сверло.dwg

ТЕХКАРТА.doc
Наименование операции
Сталь 45 ГОСТ 4543 – 71
Оборудование устройство ЧПУ
Обозначение программы
абразивно-отрезной станок 8А240
Установить заготовку
ГОСТ 31404 – 86 Форма 2
Сталь 45 ГОСТ 4543 – 71
Токарно – винторезный станок
Произвести наружное точение
Резец проходной Т15К6
Вертикально-сверлильный станок
Установить и закрепить деталь
Произвести сверление отверстия
Сверло 4 ГОСТ 4010-77
точение.dwg

2 РАСЧЕТЫ.doc
Техническая характеристика
Техническая характеристика разработанного бульдозера с усовершенствованным отвалом на базе трактора Т-170.
Максимальное тяговое усилие при общей
эксплуатационной массе kH 1320
Мощность двигателя номинальная кВт 170
Скорость движения бульдозера кмч
Объем призмы волочения перемещаемого грунта м3 277
Вместимость ковша бульдозера м3 25
Ширина рабочего органа мм 3300
Высота рабочего органа мм 1000
Угол резания град 55
Максимальное заглубление отвала мм 350
Масса рабочего оборудования кг
дополнительного 1400
Масса бульдозера (с рыхлителем) кг 20450
Производительность часовая техническая (L=20 м) м3ч 2886
Оптовая цена для промышленности тыс. руб. 14400
1 Выбор параметров отвала
Целью данного раздела является определение основных параметров отвала для дальнейших расчетов а так же для построения профиля отвала.
Базовый трактор Т-170
Сила тяжести бульдозера GБ = 1885 kH
Коэффициент сцепления φСЦ = 07
Высота H неповоротного отвала определяется по формуле:
где TН – номинальная сила тяги бульдозера
H – высота отвала мм;
Номинальная сила тяги бульдозера определяется по формуле:
где GБ – сила тяжести бульдозера
φСЦ – коэффициент сцепления (для гусеничных тракторов);
ТН = 1885 * 07 = 1320
По формуле (4.1) определяем высоту отвала:
Принимаем H = 1000 мм.
Высота козырька H1 определяется как (01-025)H.
Принимаем H1 = 200 мм.
Длина отвала L принимается в 28-3 раза больше H.
Принимаем L = 3300 мм.
Радиус кривизны неповоротного отвала R принимается равным H.
Принимаем R = 1150 мм.
Угол резания по рекомендациям принимаем = 55.
Угол заострения по рекомендациям принимаем = 25.
Задний угол α из условия = α + принимаем α = 30.
Целью данного расчета является сопоставление тяговых возможностей бульдозера с усилием которое требуется преодолеть в процессе резания грунта при работе машины т. е. определение тягового баланса.
Расчетные условия: бульдозер движется по горизонтальной поверхности и производит отделение стружки в работе участвует дополнительный отвал межотвальное пространство (далее ковш) заполнено грунтом.
Номинальная сила тяги бульдозера ТН = 1320 kH
Сила тяжести трактора GТР = 1503 kH
Сила тяжести основного бульдозерного
оборудования G = 202 kH
Сила тяжести дополнительного бульдозерного
оборудования G = 140 kH
Объем ковша бульдозера VК = 25 м3
Длина отвала L = 330 м
Высота отвала H = 10 м
Грунт твердая глина (II категория)
Удельный вес грунта γ = 194 kHм3
Удельное сопротивление лобовому резанию k = 110 kHм2
Коэффициент трения грунта по металлу 1 = 1
Коэффициент трения грунта по грунту 2 = 05
Рассмотрим тяговый расчет применительно к наиболее распространенному способу работы – лобовому толканию грунта при бестраншейном способе работ.
Объем призмы волочения зависит от геометрических размеров отвала и свойств грунта и определяется по формуле:
где L – длина отвала м;
H – высота отвала м;
kпр – коэффициент зависящий от характера грунта; kпр = 08;
Объем призмы волочения определяем по формуле (4.3):
Суммарное сопротивление движению определяется как:
W = W1 + W2 + W3 + W4 (2.4)
где W1 – сопротивление резанию грунта
W2 – сопротивление перемещению призмы волочения
W3 – сопротивление перемещению грунта вверх по отвалу
W4 – сопротивление движению бульдозера при работе
дополнительным отвалом
Сопротивление резанию грунта определяется по формуле:
где k – удельное сопротивление лобовому резанию;
h1 – глубина резания во время перемещения призмы грунта м;
Глубина резания определяется по формуле:
где kП – коэффициент потерь грунта в боковые валики; kП = 007;
Определяем глубину резания по формуле (4.6):
Сопротивление резанию грунта определяем по формуле (4.5):
W1 = 110 * 335 * 0058 = 2137
Сопротивление перемещению призмы определяется по формуле:
где γ – удельный вес грунта в плотном теле kHм3;
– коэффициент трения грунта по грунту;
Сопротивление перемещению призмы определяем по формуле (2.7):
W2 = 277 * 194 * 05 = 2687
Сопротивление перемещению грунта вверх по отвалу определяется как:
W3 = GПР cos2 1 = VПР γ cos2 1 (2.8)
где GПР – сила тяжести призмы волочения
– коэффициент трения грунта по металлу;
Сопротивление перемещению грунта вверх по отвалу определяем по формуле (4.8):
W3 = 277 * 194 * 0329 * 1 = 1768
Сопротивление движению бульдозера определяется по формуле:
W4 = ( GТР + G + G + VК γ ) f (2.9)
где GТР – сила тяжести трактора
G – сила тяжести основного бульдозерного оборудования
G - сила тяжести дополнительного бульдозерного оборудования
VК – объем ковша бульдозера м3;
γ – удельный вес грунта в плотном теле kHм3;
f – коэффициент сопротивления перемещению бульдозера; f = 011;
Сопротивление движению бульдозера вычисляем по формуле (2.9):
W4 = ( 1503 + 202 + 140 + 25 * 194 ) * 011 = 2563
Суммарное сопротивление движению определяется по формуле (2.4):
W = 2137 + 2687 + 1768 + 2563 = 9155
Тяговый баланс можно определить из следующего соотношения: при работе сила сопротивления движению преодолевается силой тяги бульдозера поэтому можно определить неравенство:
где ТН – номинальная сила тяги бульдозера
Неравенство (4.10) будет являться тяговым балансом при котором возможна устойчивая работа бульдозера.
Таким образом можно записать тяговый баланс:
Заключение: на основании тягового баланса можно сделать вывод о том что тягового усилия трактора хватает для преодоления силы сопротивления движению трактора в процессе копания грунта. Тяговый баланс соблюдается.
3 Расчет производительности
Целью данного расчета является определение производительности проектируемого бульдозера со сдвоенным отвалом и базовой модели бульдозера.
Объем призмы волочения VПР = 277 м3
Объем ковша нового бульдозера VК = 25 м3
Скорость переднего хода бульдозера VП = 251 кмч
Скорость заднего хода бульдозера VЗ = 1205 кмч
Производительность бульдозера определяется по формуле:
где VПР – объем призмы волочения м3;
kУ – коэффициент учитывающий уклон местности;
kС – коэффициент учитывающий потери грунта при
ТЦ – время цикла бульдозера с;
При расчетах принимаем kУ = 1 а коэффициент учитывающий потери грунта при транспортировке и время цикла бульдозера рассчитываем по формулам:
tП – время переключения передач и разгона бульдозера с; tП = 5 с;
tО – время опускания отвала с; tО = 2 с;
VП – скорость переднего хода бульдозера кмч;
VЗ – скорость заднего хода бульдозера кмч;
Если обозначить расстояние от начала забоя (копания) до места разгрузки через L то составляющие формулы производительности для бульдозера с дополнительным отвалом запишутся следующим образом.
Для обычного бульдозера:
Для нового бульдозера:
Расчеты производительностей бульдозеров представлены в таблице 2.1
Таблица 2.1 – Производительности бульдозеров.
Обычный бульдозер м3ч
Бульдозер с дополнительным ковшом м3ч
Прирост производительности в %
4 Расчет механизмов управления
Целью данного расчета является определение усилий необходимых для заглубления и выглубления отвала а так же определение основных параметров гидрооборудования и выбор гидроаппаратуры.
4.1 Расчет усилия на заглубление отвала
Для определения и выбора параметров гидрооборудования следует рассчитать усилие необходимое для заглубления отвала.
Рисунок 2.1 – Схема сил к определению усилия заглубления.
Расчетная схема представлена на рисунке 2.1
Максимальное значение силы заглубления определяется из условия устойчивости бульдозера относительно точки опрокидывания K. Это условие выражаем уравнением моментов сил относительно точки K:
где SЗ – сила заглубления отвала
GТР – сила тяжести трактора
zСТ xСТ – реакции рабочего оборудования действующие на
Силы xСТ и zСТ равны и противоположны соответствующим силам действующим на рабочее оборудование xC и zС и могут быть выражены как:
– угол наклона гидроцилиндров град; = 56;
Решая совместно уравнения (2.17) – (2.19) находим величину силы SЗ.
Расчетное значение силы SЗ проверяем по условиям заглубления
где SЗН – сила необходимая для заглубления
Величина силы SЗН определяется из условия равновесия рабочего оборудования:
где R1 – сила трения ножа о грунт
R2 – вертикальная реакция грунта
Реакции грунта определяются по формулам:
где 1 – коэффициент трения грунта по металлу; 1 = 1;
k – коэффициент несущей способности грунта; k = 750 kHм2;
x – ширина площадки нижней поверхности ножа трущейся о грунт
с учетом затупления м;
Силу SЗН получаем совместно решая уравнения (2.21) – (2.23):
По формуле (2.24) определяем силу необходимую для заглубления отвала:
Таким образом можно записать неравенство:
Из данного неравенства видно что условие заглубления выполняется.
4.2 Расчет усилия на управление ковшом
Механизм управления ковшом и его конструкция являются подобием заслонки скрепера следовательно справедливо будет вести расчет усилия на закрывание ковша как для заслонки скрепера.
Для определения усилия необходимого для управления ковшом составим уравнение момента сил относительно точки подвеса O и выразим из него силу S1:
где GЗ – сила тяжести ковша
T1 – сила трения грунта по внутренней поверхности ковша
T3 – сила трения грунта по внешней поверхности ковша от
действия призмы волочения
R4 – сила сопротивления вдавливанию в грунт нижней кромки
R5 – сила сопротивления вдавливанию в грунт боковых щек
R1 – нормальная сила действующая на поверхность ковша со
стороны грунта в ковше
R3 – нормальная сила действующая на поверхность ковша со
стороны призмы волочения
T2 – сила трения грунта о боковые стенки при опускании ковша
LR1 LR3 LR4 LR5 LT1 LT2 LT3 LGз LS – плечи действия сил м;
Рисунок 2.2 – Схема к определению усилия для закрывания ковша.
На рисунке 2.2 показана расчетная схема к определению усилия для закрывания ковша.
Силы трения грунта по внутренней и внешней поверхности ковша определяются по формулам:
где ρ – угол трения грунта о металл град; tgρ = 046;
Нормальная сила действующая на поверхность ковша со стороны грунта в ковше определяется по формуле:
где 1 – нормальное напряжение kHм2;
L – длина развернутой поверхности ковша м;
B – ширина ковша м; B = 335 м;
Нормальное напряжение определяется по формуле:
где γ – удельный вес грунта в плотном теле kHм3; γ = 194 kHм3;
hZ – глубина м; hZ = 025 × HЗ;
kд – коэффициент учитывающий увеличение напряжения в ковше
при свободной засыпке его грунтом; kд = 125;
– коэффициент бокового давления покоя; 1 = 042;
αСР – угол между горизонталью и хордой соединяющей верхнюю и
нижнюю кромки заслонки град; αСР = 743;
По формуле (2.32) определяем нормальное напряжение:
Длина развернутой поверхности ковша определяется по формуле:
где RЗ – радиус заслонки м; RЗ = 085 м;
– центральный угол град; = 676;
По формуле (2.33) определяем длину развернутой поверхности ковша:
По формуле (2.31) определяем нормальную силу действующую на поверхность ковша со стороны грунта в ковше:
Нормальная сила действующая на поверхность ковша со стороны призмы волочения определяется по формуле:
где 0 – коэффициент нормальной составляющей пассивного давления;
GПР – сила тяжести призмы волочения
Коэффициент нормальной составляющей пассивного давления определяется по формуле:
где α1 – угол между плоскостью подпорной стенки и горизонталью град;
По формуле (2.35) определяем коэффициент нормальной составляющей пассивного давления:
По формуле (2.34) определяем нормальную силу действующую на поверхность ковша со стороны призмы волочения:
По формулам (2.29) и (2.30) определяем силы трения грунта:
Сила сопротивления вдавливанию в грунт нижней кромки заслонки определяется по формуле:
где – предельное напряжение kHм2;
B – длина параметра вдавливаемой поверхности м; B = 335;
S – толщина вдавливаемой поверхности м; S = 001 м;
Предельное напряжение определяется по формуле:
где k1 – коэффициент зависящий от угла внутреннего трения; k1 = 1962;
По формуле (2.37) определяем предельное напряжение:
По формуле (4.36) определяем силу сопротивления вдавливанию в грунт нижней кромки заслонки:
Сила сопротивления вдавливанию в грунт боковых щек и тяг ковша определяется по формуле:
где B1 – длина периметра вдавливаемой поверхности щек ковша м;
S1 – толщина вдавливаемой кромки щек и тяг ковша м; S1 = 0015 м;
По формуле (2.38) определяем силу сопротивления вдавливанию в грунт боковых щек и тяг ковша:
По формуле (2.28) определяем усилие необходимое для закрывания ковша:
Заключение: В результате данного расчета было определено усилие необходимое для управления ковшом которое оказалось равным S1 = 3928 kH.
5 Расчет на устойчивость
Целью данного расчета является определение устойчивости бульдозера относительно действующих на него сил. Рассмотрим два расчетных положения:
Транспортный режим – бульдозер движется по горизонтальной поверхности ковш наполнен грунтом а рабочее оборудование находится в транспортном положении.
Режим выглубления рабочего органа – бульдозер движется по горизонтальной поверхности ковш наполнен грунтом сформирована вторичная призма волочения машинист производит выглубление рабочего органа.
Сила тяжести грунта в ковше GГР = 485 kH
Расчетная схема представлена на рисунке 2.4
Рисунок 2.4 – Расчетная схема к определению устойчивости.
5.1 Расчет на устойчивость в транспортном режиме
Целью данного расчета является расчет на устойчивость бульдозера при первом расчетном положении – транспортном режиме работы.
Расчетные условия: Бульдозер движется по горизонтальной поверхности ковш наполнен грунтом а рабочее оборудование находится в транспортном положении.
Момент сил опрокидывающих бульдозер относительно точки B определяется по формуле:
где G – сила тяжести основного бульдозерного оборудования
GГР – сила тяжести грунта в ковше
По формуле (2.54) определяем момент сил опрокидывающих бульдозер относительно точки B:
Момент сил удерживающих бульдозер от опрокидывания относительно точки B определяется по формуле:
По формуле (2.55) определяем момент сил удерживающих бульдозер относительно точки B:
Из расчета видно что момент сил удерживающих больше чем момент сил опрокидывающих трактор. Следовательно в транспортном режиме бульдозер устойчив.
5.2 Расчет на устойчивость в режиме выглубления
Целью данного подраздела является расчет на устойчивость бульдозера при втором расчетном положении – выглубление рабочего органа.
Расчетные условия: Бульдозер движется по горизонтальной поверхности ковш наполнен грунтом сформирована вторичная призма волочения машинист производит выглубление рабочего органа.
Полагаем что горизонтальная составляющая сопротивления копанию Py равна силе тяги т. е. Py = ТН = 1320 kH а вертикальную составляющую сопротивления находим по формуле:
где – угол резания град;
φ0 – угол внешнего трения град; φ0 = 265;
По формуле (2.56) находим вертикальную составляющую сопротивления копанию:
Максимальное усилие при выглублении развиваемое гидроцилиндром подъема и опускания отвала определяем из уравнения суммы моментов относительно точки A:
где MB – сумма моментов сил G GГР и G относительно точки B;
S1 – усилие на штоке гидроцилиндра подъема и опускания отвала
h – толщина стружки м; h = 015 м;
Из формулы (2.57) выражаем максимальное значение вертикальной составляющей сопротивлению копания и определяем ее величину:
Опрокидывающий момент в режиме копания определяется по формуле:
По формуле (2.58) определяем опрокидывающий момент в режиме копания:
Из расчета видно что в режиме копания опрокидывающий момент больше момента удерживающего следовательно в режиме копания необходим противовес трактору.
Силу тяжести противовеса определяем по формуле:
По формуле (2.59) определяем силу тяжести противовеса:
В качестве противовеса рекомендуется применить стандартный серийный рыхлитель для расширения области применения.
6 Расчет на прочность толкающих брусьев
Для расчета толкающего бруса на прочность следует определить силовые факторы действующие на брус:
Максимальное вертикальное усилие на переднем отвале при заглублении определяем приравнивая момент сил удерживающих трактор моменту сил опрокидывающих трактор относительно точки K.
Момент удерживающих сил определяется по формуле:
где h – толщина стружки м; h = 015 м;
MB – сумма моментов сил G GГР и G относительно точки B kHм;
По формуле (4.60) определяем момент удерживающих сил:
Момент опрокидывающих сил определяется по формуле:
где GП – сила тяжести противовеса
Приравнивая опрокидывающий момент к удерживающему определяем максимальное вертикальное усилие:
Максимальное вертикальное усилие на переднем отвале при выглублении определяем приравнивая момент сил удерживающих трактор моменту сил опрокидывающих трактор относительно точки B.
GП – сила тяжести противовеса
По формуле (4.62) определяем момент удерживающих сил:
где MB - сумма моментов сил G GГР и G относительно точки B kHм;
PY – горизонтальная составляющая сопротивлению копания
Величины B1 = 233 м и B2 = 271 м соответственно – расстояния между гусеницами трактора и между толкающими брусьями.
На рисунке 2.5 показана схема сил действующих на бульдозерное оборудование.
Рисунок 2.5 – Схема сил действующих на бульдозерное оборудование.
При расчете полагаем наиболее неблагоприятный случай когда усилия на отвале передается только на один толкающий брус.
Определяем момент внешних сил относительно точки Риттера.
Момент внешних сил действующих на бульдозерное оборудование при выглублении переднего отвала определяется по формуле:
где t1 t2 и t3 – плечи действия соответствующих сил м;
По формуле (4.64) определяем момент внешних сил:
Момент внешних сил действующих на бульдозерное оборудование при заглублении переднего отвала определяется по формуле:
По формуле (4.65) определяем момент внешних сил:
Из расчета видно что наиболее опасным является выглубление т. к. максимален изгибающий момент внешних сил. Принимаем за расчетное значение MИЗГ = 7899 kH×м.
Реакция на гидроцилиндрах привода отвала определяется из уравнения моментов относительно точки A:
где S1 – реакция на гидроцилиндрах привода отвала
Из формулы (4.66) выражаем реакцию на гидроцилиндрах и определяем ее:
Реакция на шарнире A нормальная к толкающему брусу определяется:
где MИЗГ – изгибающий момент kH×м;
По формуле (4.67) определяем нормальную реакцию на шарнире A:
Реакцию на шарнире A направленную по толкающему брусу находим из уравнения суммы проекций сил действующих на бульдозерное оборудование на горизонтальную плоскость.
где – угол наклона гидроцилиндра к горизонтали град; = 56;
γ – угол наклона толкающего бруса к горизонтали град; γ = 5;
yA – нормальная реакция на шарнире A
Из формулы (2.68) выражаем реакцию xA и определяем ее величину:
Изгибающий момент в основном сечении толкающего бруса определяется по формуле:
где MC – изгибающий момент в основном сечении бруса kH×м;
t4 – плечо действия силы yA м;
По формуле (2.69) определяем изгибающий момент:
Определяем геометрические характеристики опасного сечения толкающего бруса.
Находим центр тяжести сечения расположив начало координат в центре тяжести основной коробки (рисунок 2.6).
Площади составляющих элементов определяем по формулам:
Координаты центра тяжести составляющих элементов сечения определяются по формулам:
Рисунок 2.6 – Опасное сечение толкающего бруса.
Общая площадь сечения определяется по формуле:
По формуле (4.70) определяем общую площадь сечения:
Координата центра тяжести сечения определяется по формуле:
где F2 F3 – площади соответствующих сечений элементов см2;
F – общая площадь сечения см2;
z1 z2 – координаты центра соответствующих сечений см2;
По формуле (2.71) определяем координату центра тяжести сечения:
Моменты инерции составляющих сечений определяются по формулам:
Момент инерции всего сечения определяется по формуле:
По формуле (4.72) определяем момент инерции всего сечения:
Момент сопротивления сечения изгибу определяется по формуле:
где J – момент инерции сечения см4;
zMAX – координата максимально удаленной точки см;
По формуле (2.73) определяем момент сопротивления сечения изгибу:
Максимальное нормальное напряжение в опасном сечении определяется по формуле:
где MMAX – максимальный изгибающий момент в основном сечении
толкающего бруса kH×м;
W – момент сопротивления сечения изгибу см3;
F – площадь сечения см2;
По формуле (4.74) определяем максимальное нормальное напряжение:
Максимально допустимое нормальное напряжение [] = 16 kHсм2.
Неравенство (2.75) запишется следующим образом:
Из неравенства видно что условие прочности выполняются следовательно сечение выбрано верно.
4 ЭКОНОМИКА.doc
Исходные данные необходимые для расчета экономической эффективности приведены в таблице 4.1
Таблица 4.1 – Исходные данные.
Наименование показателей
Базовая техника (БТ)
Техническая производительность
капитального ремонта
Периодичность выполнения текущего ремонта:
Емкость гидросистемы
Периодичность смены масла
Цена дизельного топлива
Цена масла гидросистемы
Удельный расход топлива
1 Выявление назначения и область применения
Бульдозер с неповоротным отвалом на гусеничном тракторе Т-170 предназначен для выполнения землеройно-транспортных работ в дорожном строительстве в промышленном и гидротехническом строительстве в горнодобывающей промышленности в мелиорации и ирригации.
Бульдозер может быть применен для разработки и засыпки котлованов и траншей возведения насыпей устройстве выемок а так же выполнения планировочных работ.
2 Выбор базисного варианта
Для сравнения в качестве базисного варианта принимается серийно выпускаемый ЧЗК бульдозер ДЗ-110В. Обе машины эксплуатируются на идентичных видах работ.
3 Выявление конструктивно-эксплуатационных
По сравнению с базовой машиной новый бульдозер имеет большую производительность.
4 Расчет капитальных вложений
Затраты связанные с созданием производством доставкой техники потребителю и ее монтажом определяется по формуле:
где SK – капитальные затраты на технику тыс. руб.;
KБ – коэффициент учитывающий затраты на доставку
и монтаж техники; KБ = 109;
Ц – оптовая цена техники тыс. руб.;
По формуле (6.1) определяем капитальные затраты на технику:
5 Определение годовой эксплуатационной
Годовая эксплуатационная производительность рассчитывается по формуле:
где bЧЭ – часовая эксплуатационная производительность м3ч;
КПР – коэффициент учитывающий простои в работе техники
не учтенные в часовой эксплуатационной производительности;
ТГ – количество машиночасов работы техники в году;
Часовая эксплуатационная производительность определяется по формуле:
где КТ – коэффициент перехода от технической производительности
к эксплуатационной; КТ = 03;
bЧТ – часовая техническая производительность м3ч;
По формуле (6.3) определяем часовую эксплуатационную производительность:
Количество машиночасов работы техники в году определяется по формуле:
где ТФ – годовой фонд рабочего времени техники; ТФ = 247;
tСМ – средняя продолжительность смены маш. час.;
tСМ = 771 маш. час.;
kСМ – коэффициент сменности работы техники; kСМ = 14;
ДР – простои во всех видах технического обслуживания и ремонта;
ТОБ – продолжительность работы техники на одном объекте;
ТОБ = 2000 маш. час.;
dП – продолжительность одной перебазировки; dП = 4;
Простои во всех видах технического обслуживания и ремонта определяются по формуле:
dni – продолжительность ожидания ремонта доставки
в ремонт и обратно дни;
ТЦ – межремонтный цикл маш. час.;
Время на доставку машины в ремонт и его ожидание принимается в размере 10 дней для текущего ремонта и 20 дней для капитального ремонта.
Количество ТО и ремонтов за межремонтный цикл определяются по формулам:
где ТР – средний ресурс до первого капитального ремонта час.;
tР – периодичность ТО и ремонта;
Опредляем средний ресурс до первого капитального ремонта:
По формулам (4.6) – (4.8) определяем количество ТО и ремонтов:
Межремонтный цикл определяется по формуле:
где КЧ – коэффициент перевода моточасов в машино-часы; КЧ = 044;
По формуле (4.9) определяем межремонтный цикл:
По формуле (4.5) определяем простои во всех видах ТО и ремонта:
Продолжительность работы новой техники на одном объекте равно:
По формуле (4.4) определяем количество машиночасов работы техники в году:
По формуле (4.2) определяем годовую эксплуатационную производительность базовой и новой техники:
6 Расчет годовых текущих затрат
Текущие затраты определяются по формуле:
где Sa – амортизационные отчисления на реновацию тыс. руб.год;
SЗП – заработная плата рабочих занятых управлением
машины тыс. руб.год;
SКР – затраты на капитальный ремонт тыс. руб.год;
SЭР – затраты на ТО и ремонт тыс. руб.год;
SТ – затраты на топливо тыс. руб.год;
SСМ – затраты на смазочные материалы тыс. руб.год;
SМГ – затраты на масла для гидросистемы тыс. руб.год;
SПБ – затраты на перебазировку тыс. руб.год;
HP – накладные расходы; НР = 21 %;
Амортизационные отчисления определяются по формуле:
Ha – норма амортизационных отчислений на реновацию %;
По формуле (4.12) определяем амортизационные отчисления:
Заработная плата рабочих занятых управлением машины определяется по формуле:
где КНЗ – накладные расходы; КНЗ = 13;
КР – поправочный коэффициент к тарифной ставке; КР = 1105;
λ – коэффициент учитывающий премии; λ = 125;
Б – количество рабочих занятых управлением машины
Часовая тарифная ставка рабочего определяется по формуле:
где ЗМ – месячная зарплата рабочего тыс. руб.;
ФМ – месячный фонд рабочего времени ч;
Месячная зарплата рабочего соответствующая действующим нормам 4000 руб.
По формуле (4.14) определяем часовую тарифную ставку:
По формуле (4.13) определяем заработную плату рабочих занятых управлением машины:
Затраты на техническое обслуживание и ремонты определяются по формуле:
где SЭРЗ – затраты на заработную плату ремонтных рабочих тыс. руб.;
SЭРМ – затраты на материалы и запасные части тыс. руб.;
Затраты на заработную плату ремонтных рабочих определяются по формуле:
где ТЦ – продолжительность межремонтного цикла техники маш. ч.;
λР – коэффициент учитывающий премии рабочим; λР = 12;
СР – тарифная ставка работы по ремонту машины тыс. руб.ч;
Часовая тарифная ставка рабочего по ремонту определяется как:
Месячная зарплата рабочего соответствующая действующим нормам 3500 руб.
По формуле (4.17) определяем часовую тарифную ставку:
По формуле (4.16) определяем затраты на заработную плату:
Затраты на материалы и запасные части определяются по формуле:
где КЭР – коэффициент перехода от заработной платы к затратам на
материалы и запасные части; КЭР = 135;
По формуле (4.18) определяем затраты на материалы и запасные части:
По формуле (4.15) определяем затраты на технические обслуживания и ремонты:
Затраты на топливо определяются по формуле:
где ЦТ – цена топлива тыс. руб.л;
q – часовой расход топлива q=138 лч;
Т – фонд времени работы бульдозера ч.
По формуле (4.19) определяем затраты на топливо:
Затраты на смазочные материалы для техники с приводом от двигателя внутреннего сгорания рассчитывается по формуле:
где – коэффициент перехода от годовых затрат на топливо к затратам
на смазочные материалы; = 022;
По формуле (4.21) определяем затраты на смазочные материалы:
Затраты на масло для гидросистемы определяются по формуле:
где Г – емкость гидросистемы л;
ЦМГ – оптовая цена масла для гидросистемы руб.;
КД – коэффициент доливок масла в гидросистему; КД = 15;
tМГ – периодичность смены масла в гидросистеме tМГ=2 разагод.;
По формуле (4.21) определяем затраты на масло для гидросистемы:
Затраты на перебазировку определяются по формуле:
где SПЕР – затраты на перевозку машины тыс. руб.;
Затраты на перевозку машины определяются по формуле:
где SЗЭ – заработная плата экипажа перевозимой машины тыс. руб.;
SЗТ – заработная плата такелажников тыс. руб.;
SЭ – затраты на эксплуатацию автомобиля тыс. руб.;
Затраты на заработную плату экипажу перевозимой машины определяется по формуле:
где dП – продолжительность одной перебазировки дни; dП = 1 день;
По формуле (4.24) определяем затраты на заработную плату экипажу:
Затраты на заработную плату такелажникам определяется по формуле:
Затраты на эксплуатацию автомобиля определяются по формуле:
где ЦАЧ – стоимость одного автомобиля-часа в зависимости от
грузоподъемности автомобиля тыс. руб.;
ZT – среднее расстояние перебазировки км;
ЦК – стоимость одного километра пробега тыс. руб.км;
По формуле (4.26) определяем затраты на эксплуатацию автомобиля:
По формуле (4.23) определяем затраты на перевозку машины:
По формуле (4.22) определяем затраты на перебазировку:
По формуле (4.11) определяем окончательную сумму текущих затрат:
В таблице 4.2 представлены годовые текущие издержки базовой и новой техники.
Таблица 4.2 – Калькуляция годовых текущих издержек.
Условное обозначение
Значение показателей руб.
Амортизационные отчисления на реновацию
Заработная плата рабочих управляющих машиной
Затраты на технические обслуживания и ремонты
Затраты на масло для гидросистемы
7Определение экономическогоэффекта
Экономический эффект в расчете на одну машину за год работы Эг тыс.руб.год определяется по формуле:
где В’ В” – годовая эксплуатационная производительность м3год;
U’ U” – себестоимость эксплуатации (текущие издержки) руб.;
Таблица 4.3 - Экономическая эффективность использования бульдозера.
Значения показателей
Годовая эксплуатационная производительность
Годовые текущие издержки потребителя
Экономический эффект на 1 бульдозер за год эксплуатации
Экономический эффект от внедрения новой техники составил 6617 тыс. рублей.
СПИСОК ИСПОЛЬЗОВ. ИСТОЧНИКОВ.doc
Алексеева Т. В. Артемьев К. А. Бромберг А. А. и др. Дорожные машины: в 2-х частях. Ч.1. Машины для земляных работ. – 3-е изд. перераб. и доп. – М.: Машиностроение 1972. - 504 с.
Алексеева Т. В. Артемьев К. А. Бромберг А. А. и др. Машины для земляных работ. Теория и расчет. Под ред. А. А. Бромберга – 2-е изд. перераб. и доп. – М.: Машиностроение 1964. – 467 с.
Алексеева Т. В. Галдин Н. С. Шерман Э. Б. – Гидравлические машины и гидропривод мобильных машин: Учеб. Пособие. – Новосибирск: - Издательство Новосибирского университета 1994. – 212 с.
Анурьев В. И. Справочник конструктора – машиностроителя: в 3-х томах. Т.1. – 5-е изд. перераб. и доп. - М.: Машиностроение 1980. – 728 с. ил.
Анурьев В. И. Справочник конструктора – машиностроителя: в 3-х томах. Т.3. – 5-е изд. перераб. и доп. - М.: Машиностроение 1980. – 559 с. ил.
Баловнев В.И. Дорожно-строительные машины с рабочими органами интенсифицирующего действия. – М.: Машиностроение 1981. – 223с. ил.
Бромберг А. А. и др. Машины для земляных работ. Атлас конструкций. Учебное пособие для вузов. Под ред. А. А. Бромберга. Изд. 3-е переработ. и доп. М.: Машиностроение 1968. – 135 с.
Васильченко В. А. Гидравлическое оборудование мобильных машин. - М.: Машиностроение 1983. – 301 с. ил.
Веледницкий Ю. Б. Новые конструкции отечественных и зарубежных бульдозеров. – М.: ЦНИИТЭ 1975. – 40 с. ил.
Власов А. Ф. Предупреждение производственного травматизма. – М.: Профиздат 1973. – 102 с.
Голубков Е. П. и др. Маркетинг: Выбор лучшего решения. – М.: Экономика 1993. – 205 с.
Зеленин А. Н. Баловнев В.И. Керов И. П. Машины для земляных работ. М.: Машиностроение 1975. – 424 с. ил.
Методические рекомендации по оценке эффективности инвестиционных проектов и отбору их для финансирования. М.: Инфрэлектро 1994. – 105 с.
Расчет скрепера: Методические указания по курсовому и дипломному проектированию для студентов специальности 0511СибАДИ; Сост. Демиденко А. И. – Омск 1985. – 40 с.
Справочник технолога – машиностроителя. В 2-х Т. Т.2 Под ред. А.Г. Косиловой – 4-е изд. перераб. и доп. - М.: Машиностроение 1985. – 496 с. ил.
Филиппов Б.И. Охрана труда при эксплуатации строительных машин. М.: Машиностроение 1984. – 274 с. ил.
Федоров Д. И. Рабочие органы землеройных машин. – 2-е изд. перераб. и доп. – М.: Машиностроение 1989. - 368 с. ил.
Экономика предприятий: Учебник для ВУЗов. Под ред. В. Я. Горфинклея В. А. Швандара. М.: ЮНИТИ – ДАНА 2001. – 267 с.
Экономика предприятий: Учебник для ВУЗов. Под ред. В. П. Грузинова. М.: Банки и биржа ЮНИТИ 1999. – 241 с.
СОДЕРЖАНИЕ.doc
1 Характеристика объекта строительства ..
2 Технология процесса строительства земляного полотна
автомобильной дороги .
3 Организация производства работ .
4 Определение эксплуатационных производительностей машин
5 Определение необходимого количества машиносмен
Конструкторский раздел
1 Выбор параметров отвала
3 Расчет производительности
4 Расчет механизмов управления ..
4.1 Расчет усилия на заглубление отвала .
4.2 Расчет усилия на закрывание ковша ..
4.3 Расчет гидропривода
4.3.1 Определение мощности гидропривода и выбор насоса
4.3.2 Определение внутреннего диаметра гидролиний ..
4.3.3 Расчет потерь в гидролиниях
4.3.4 Расчет и выбор гидроцилиндров ..
5 Расчет на устойчивость
5.1 Расчет на устойчивость в транспортном режиме
5.2 Расчет на устойчивость в режиме выглубления
6 Расчет на прочность толкающих брусьев ..
Технологический процесс изготовления детали ..
1 Назначение детали и описание работы ..
2 Способ получения заготовок
3 Расчет припуска на механическую обработку
4 Операция отрезки ..
5 Токарная операция
Расчет экономической эффективности ..
1 Выявление назначения и область применения
2 Выбор базисного варианта
3 Выявление конструктивно-эксплуатационных особенностей ..
4 Расчет капитальных вложений .
5 Определение годовой эксплуатационной производительности
6 Расчет годовых текущих затрат
7 Определение хозрасчетного экономического эффекта ..
Безопасность жизнедеятельности
1 Анализ опасных и вредных факторов ..
1.1 Производственный микроклимат ..
1.2 Влияние электромагнитных излучений
1.3 Влияние звуковых волн ..
1.4 Влияние вибрации
2 Экологическая безопасность .
3 Расчет сварного соединения ..
Список использованных источников ..
1 Механизация.doc
В настоящее время повышение производительности труда в строительном производстве следует рассматривать с точки зрения применения новых технологий максимального использования потенциальных возможностей средств механизации и широкого внедрения результатов научных разработок.
Комплексная механизация и автоматизация производственных процессов являются одним из основных направлений повышения темпов строительства его качества а также снижения трудоемкости и энергоемкости выпускаемой продукции. Основу этого направления составляют передовые технологии производства в комплекты машин для их реализации.
Проектирование механизации связано с определением типов машин и их количества которые впоследствии объединяются в комплекты для выполнения операций технологического процесса.
Известно что один и тот же технологический процесс может быть выполнен различными машинами отличающимися друг от друга как принципом работы так и техническими параметрами. Поэтому в таких условиях очень важно установить рациональные составы специализированных машинно-дорожных отрядов которые определяют технико-экономические показатели.
Оптимальным будет тот парк машин использование которого обеспечит выполнение заданных объёмов работ в заданные сроки с минимальными трудовыми энергетическими денежными и т. п. затратами.
В проекте рассматривается парк дорожно-строительных машин с ведущей машиной – бульдозер. Бульдозеры применяются для выполнения земляных работ при осуществлении дорожного промышленного и т. д. строительства.
1 Характеристика объекта строительства
Район строительства расположен в южной части Новосибирской области в IV дорожно-климатической зоне. Климат района резко-континентальный колебания положительных и отрицательных температур значительны. Разница между средними температурами самого холодного и самого теплого месяца (января и июля) составляет 475 °С.
Температура наружного воздуха по месяцам
I II III IV V VI VII VIII IX X XI XII
Средне годовая температура составляет 0 °С.
Максимальная температура воздуха +40 °С.
Абсолютный минимум температуры - 49 °С.
По увлажнению район относится к зоне не достаточного увлажнения.
Среднее количество осадков в год составляет 374 мм.
Средняя мощность снегового покрова составляет 24 см.
Продолжительность залегания устойчивого снежного покрова составляет 170-180 дней.
Средняя глубина промерзания грунтов 22 м.
Рельеф местности по которой проходит дорога равнинный отметки поверхности земли колеблются в пределах 11000-11120 м.
Естественный уклон для стока поверхностных вод отсутствует.
Местность по характеру и степени увлажнения относится ко второму типу.
Особенности геологического строения района строительства дороги обусловлены отсутствием каменных материалов и наличием лишь материалов остаточного происхождения: суглинков и глин. Грунты по трассе представлены суглинками тяжелыми пылеватыми.
2 Технология процесса строительства земляного полотна
автомобильной дороги
В проекте для расчета были приняты следующие исходные данные:
Регион строительства Новосибирская область
Протяжённость участка 15 км
Высота земляного полотна 06 м
Под организацией строительства понимают установление очерёдности и сроков выполнения работ обеспечение строящегося объекта материалами машинами автомобилями трудовыми ресурсами электроэнергией связью и т. д.
В дорожном строительстве применяются три метода организации работ:
непоточный (последовательный параллельный);
Наибольшее распространение получил поточный метод. Он состоит в непрерывном и ритмичном производстве работ обеспечивающий равномерный выпуск продукции и эффективное использование трудовых и материально-технических ресурсов оборудования и средств механизации.
Этот метод признан наиболее прогрессивным и научно обоснованным. Сущность поточного метода строительства автомобильных дорог состоит в следующем:
- в равные промежутки времени (смену сутки) заканчивают строительство равных по длине участков дороги;
- все работы выполняются специализированными машинно-дорожными отрядами по видам работ (строительство ЗП дорожных оснований и т. д.);
- машинно-дорожные отряды равномерно друг за другом передвигаются в одном направлении и последовательно выполняют все строительно-монтажные работы;
- после прохода последнего специализированного отряда дорога полностью готова к сдаче в эксплуатацию.
Таблица 1.1 Технология устройства земляного полотна.
Снятие растительного слоя
Разработка и перемещение грунта в нижний слой насыпи
Разравнивание нижнего слоя насыпи
Уплотнение нижнего слоя насыпи
Разработка и перемещение грунта во второй слой насыпи
Разравнивание второго слоя насыпи
Уплотнение второго слоя
Профилировка верха слоя земляного полотна
Бульдозер Д-259 на базе т-ра Т-100
Бульдозер на базе т-ра Т-170
Прицепной каток ДУ-39А
3 Организация производства работ
Под организацией работ понимается установление сроков выполнения работ режима сменности работы обеспечение строящегося объекта материалами машинами транспортными средствами трудовыми ресурсами электроэнергией связью и другими ресурсами.
Число рабочих дней в строительном сезоне Nр.д. вычисляют по формуле:
Nр.д. = Np – Nв – Nп –Nн (1.1)
где Nр. – календарная продолжительность строительного сезона дней; Nв. – число выходных дней приходящихся на строительный сезон дней; Nп. – число праздничных дней дней; Nн. – число рабочих дней по метеоусловиям дней.
Nр.д.=155-44-0-5=106 дней.
Определение объёма работ Vобщ. (м3) по формуле:
Vобщ.=Sтр.*Lд. (1.2)
где Lд. – длина участка дороги м; Sтр. – площадь трапеции м2 (рисунок 1.1).
Рисунок 1.1 - Земляное полотно.
Площадь трапеции Sтр. (м2) определяют по формуле:
где В – ширина земляного полотна м; В - ширина основания земляного полотна м; Н – высота земляного полотна м.
Sтр.= (15+1572)*062=92 м2.
Vобщ.= 92*15000=138300 м3.
В дорожном строительстве наибольшее распространение получил поточный метод организации работ. Основным показателем потока является его темп то есть объём готовой продукции выпускаемый в единицу времени. Темп потока t определяется выражением 12
где Nр.д. – число рабочих дней дней ; Ксм. – коэффициент сменности (Ксм.=1).
t = 138300 = 130471 м3см.
Длину захватки tз. (мсм) вычисляют по формуле:
где Lд. – длина захватки м ; Nр. д. – число рабочих дней дни.
tз. = 15000 = 141.5 мсм.
4 Определение эксплуатационных производительностей машин
Производительность машин Псм. (м3см) определяется по формуле:
где Тсм. – продолжительность рабочей смены ч; Нв – норма времени.
Производительность бульдозера Д-259 на базе трактора Т-100 при снятии растительного слоя:
Псм. = 100*82 = 11884 м3см.
Разработка и перемещение грунта бульдозером на базе т-ра Т-170.
Дальность транспортирования 10 м :
Псм. = 100*82 = 21579 м3см.
Дальность транспортирования 30 м. :
Нв = 038+03*3 = 128 [11]
Псм. = 100*82 = 640625 м3см.
Дальность транспортирования 50 м. :
Нв = 038+03*5 = 188 [11]
Псм. = 100*82 = 43617 м3см
Дальность транспортирования 70 м. :
Псм. = 100*82 = 33064 м3см.
Дальность транспортирования 90 м. :
Псм. = 100*82 = 26623 м3см.
Разравнивание слоя насыпи бульдозером Д-259 на базе трактора Т-100.
Псм. = 100*82 = 31538 м3см
Уплотнение слоя насыпи прицепным катком ДУ-39А.
Псм. = 100*82 = 14643 м3см.
Планировка верха земляного полотна автогрейдером ДЗ-14.
Псм. = 1000*82 = 546667 м2см.
5 Определение необходимого количества машиносмен
Определение машиносмен n (маш-см) по формуле:
где Псм. – эксплуатационная производительность; Vт.раб. – требуемый объём работ.
Снятие растительного слоя бульдозером Д-259 на базе Т-100:
Vт.раб. = В*tз. (1.8)
где В - ширина низа земляного полотна м; tз – длина захватки м.
Vт.раб. = 1572*1415 = 22244 м2.
n = 22244 =19 маш-см.
Разработка и перемещение грунта в нижний слой насыпи высотой 03 м бульдозером на базе т-ра Т-170:
Дальность транспортирования 10 м:
Требуемый объём работ Vт.раб. (м3) определяют по формуле:
Vт.раб. = Sтр. *tз. (1.9)
где Sтр. – площадь трапеции м2; tз. – длина захватки м.
Sтр. = 1536+1572 *03 = 466 м2.
Vт.раб. = 466*1415 = 65939 м3.
n = 65939 = 031маш-см.
Дальность транспортирования 30 м:
n = 65939 = 102 маш-см.
Дальность транспортирования 50 м:
n = 65939 = 151 маш-см.
Дальность транспортирования 70 м:
n = 65939 = 1994 маш-см.
Дальность транспортирования 90 м:
n = 65939 = 248 маш-см.
Разравнивание нижнего слоя насыпи бульдозером Д-259 на базе т-ра Т-100.
n = 65939 = 021маш-см.
Уплотнение нижнего слоя насыпи высотой 03 м. прицепным катком ДУ-39А.
n = 65939 =045 маш-см.
Разработка и перемещение грунта во второй слой насыпи бульдозером на базе трактора Т-170.
Требуемый объём работ Vт.раб. (м3) равен
Sтр. = 15+1536 * 03 = 455 м2.
Vт.раб. = 455*1415 = 64382 м3.
n = 64382 = 03 маш-см.
n = 64382 = 1004 маш-см.
n = 64382 = 147 маш-см.
n = 64382 = 194 маш-см.
n = 64382 = 241 маш-см.
Разравнивание слоя насыпи бульдозером Д-259 на базе т-ра Т-100:
n = 64382 = 02 маш-см.
Уплотнение второго слоя насыпи прицепным катком ДУ-39А:
n = 64382 = 044 маш-см.
Профилировка верхнего слоя земляного полотна автогрейдером ДЗ-14
n = 64382 = 001 маш-см.
В данном проекте был рассчитан состав комплекта машин для проведения работ по возведению земляного полотна который составляет:
- Бульдозер Д-259 3 ед.
- Бульдозер на базе тр-ра Т-170 3 ед. (Lтр=50 м)
- Каток прицепной ДУ-39А 1 ед.
- Автогрейдер ДЗ-14 1 ед.
ВВЕДЕНИЕ.doc
Этого можно добиться путем осуществления мероприятий на базе совершенствования организационно- технологических мероприятий по эффективному использованию имеющегося парка машин а также путем создания и внедрения в производство принципиально новой технологии и материалов создания машин различной единичной мощности и производительности работающих на основе использования новых технических эффектов.
Создание высокопроизводительных машин осуществляется по двум направлениям: совершенствование рабочих органов и машин традиционного типа находящихся в эксплуатации и производство принципиально новых рабочих органов и машин на базе использования достижений фундаментальных наук.
При проведении работ по строительству дорог основной задачей является эффективное использование парков машин выбор специализированных строительных комплектов машин и их правильное обслуживание на эксплуатационных предприятиях.
3 Технология изготовления.doc
1 Назначение детали и описание работы
Палец - деталь которая служит для обеспечения подвижного соединения гидроцилиндра закрывания ковша с дополнительным отвалом.
Палец имеет цилиндрическую форму один торец пальца обрабатывается под стопорную пластину
Палец изготавливается из стали 45 ГОСТ 4543-71 прочность 550 МПа.
2 Способ получения заготовок
При изготовлении детали в целях снижения трудоемкости процесса наиболее оптимальным будет решение применения в качестве заготовки стандартного сортового проката. Все остальные способы получения заготовок являются более трудоемкими.
3 Расчет припуска на механическую обработку
Применим механическую обработку в два этапа:
а)Черновая обработка;
б)Чистовая обработка;
Нормальный припуск на заготовку пальца определим по формуле:
где z1 – припуск на черновое точение мм;
z2 – припуск на чистовое точение мм;
b – допуск на величину припуска мм;
При диаметре пальца D = 30 мм примем z1 = 2 мм z2 = 12 мм и b = 096 мм.
По формуле (3.1) определяем нормальный припуск:
Диаметр заготовки определяется по формуле:
где D – диаметр готовой детали мм;
По формуле (3.2) определяем диаметр заготовки:
По ГОСТ 2590-71 принимаем диаметр заготовки DЗ = 35 мм.
Диаметр пальца после черновой обработки определяется по формуле:
Разрезание прутка производят абразивным кругом на абразивно-отрезном станке 8А240 при частоте вращения круга n = 3820 обмин. При данной частоте вращения скорость резания будет равна 4830 ммин. Станок обеспечивает подачу 136 мммин (S = 36×10-2 ммоб).
Определим штучно-калькуляционное время необходимое для разрезания прутка по формуле:
где ТШТ – время на изготовление одной детали мин;
ТПЗ – время подготовительно-заключительное мин;
N – количество деталей в партии шт;
Время на изготовление одной детали определяется по формуле:
где ТО – время на отрезку одной детали мин;
ТВС – вспомогательное время мин;
ТОБ – время на обслуживание мин;
ТОТ – время на отдых мин;
Время на отрезку одной детали определяется по формуле:
где DЗ – диаметр заготовки мм;
n – частота вращения круга обмин;
По формуле (3.6) определяем время на отрезку одной детали:
Вспомогательное время по рекомендациям ТВС = 02 мин;
Время на обслуживание и отдых определяется по формуле:
По формуле (3.5) определяем время на изготовление одной детали:
Подготовительно-заключительное время определяется как:
По формуле (3.4) определяем штучно-калькуляционное время необходимое для разрезания прутка:
Произведем выбор резца формы передней поверхности и геометрических параметров режущей части резца.
Примем для токарной обработки резец Т15к6 форма передней поверхности - плоская с фаской угол в плане 90 .
Геометрические параметры:
- вспомогательный угол в плане φ = 10 - 15;
- задний угол α = 8;
- передний угол γ = 12 - 15;
Среднее значение стойкости при одноинструментальной обработке равно Т = 60 мин.
Для проведения операции используем станок 16БО5П.
При черновой обработке глубина припуска определяется по формуле:
D – диаметр готовой детали мм;
По формуле (5.8) определяем глубину припуска:
При получистовом и чистовом точении подача выбирается в зависимости от класса шероховатости вида обрабатываемого материала и радиуса при вершине резца.
По рекомендациям примем подачу S = 012 ммоб.
Скорость резания определяется по формуле:
где CV – постоянная для данных расчетных условий резания
Т- среднее значение периода стойкости резца мин;
t – глубина резания мм;
KV – общий поправочный коэффициент;
По рекомендациям принимаем CV = 219 xV = 015 yV = 035 m = 02.
Поправочный коэффициент определяется по формуле:
где KMV – коэффициент механических свойств;
KUV – коэффициент учитывающий влияние материала резца;
КФУ – коэффициент учитывающий форму передней грани резца;
KZV – коэффициент учитывающий чистоту обработки;
По рекомендациям принимаем KMV = 1 KUV = 08 КФУ = 1 KZV = 1.
По формуле (3.10) определяем поправочный коэффициент:
По формуле (5.9) определяем скорость резания для каждого вида точения:
Определяем скорость резания для чистового точения:
Требуемая частота вращения детали определяется по формуле:
где V – скорость резания ммин;
По формуле (3.11) определяем требуемую частоту вращения для каждого вида точения:
Для чернового точения:
Для чистового точения:
Расчет действительной скорости резания VД по уточненной по паспорту станка частоты вращения шпинделя не производим ввиду бесступенчатого регулирования скорости вращения.
Основное время определяется по формуле:
где L – длина прохода резца мм;
n – частота вращения шпинделя обмин;
Длина прохода резца определяется по формуле:
dn – длина перебега мм; примем dn = 1 – 3 мм;
y = 0 т. к. ctgφ = 0;
По формуле (3.13) определяем длину прохода резца для каждого вида точения:
По формуле (3.12) определяем основное время для каждого вида точения:
Суммарное основное время определяется по формуле:
Вспомогательное время определяется как сумма времени на установку детали tУСТ = 18 мин и времени на переключение частоты tПЕР = 12 и определяется по формуле:
Время на обслуживание и отдых определяется по формулам:
По формулам (3.16) и (3.17) определяем время на обслуживание и отдых:
Норму штучного времени определяем по формуле (3.5):
Подготовительно-заключительное время принимаем ТПЗ = 23 мин.
По формуле (3.4) определяем норму штучно-калькуляционного времени:
Произведем выбор сверил и оборудования.
Для выполнения операции сверления применим сверла спиральные универсальные диаметром 4 мм по ГОСТ 10903-77 и диаметром 9 мм и 16 мм по ГОСТ 10902-77 с материалом режущей части Р6М5. Среднее значение стойкости сверл: для сверла диаметром 4 мм - 15 мин для сверил диаметром 9 и 16 мм - 45 мин.
Для выполнения операции применим станок вертикально-сверлильный марки 2Н125 с системой смазки зоны сверления охлаждающей жидкостью.
Подачу режущего инструмента определяем по формуле:
где ST – табличное значение подачи ммоб;
КЕЗ – коэффициент учитывающий относительную глубину
КОЗ – коэффициент учитывающий потребность в последующем
КЖЗ – коэффициент учитывающий недостаточную жесткость
По формуле (3.18) определяем подачу режущего инструмента:
Скорость резания определяется по формулам:
где CV q y m – поправочные коэффициенты;
DC – диаметр сверла мм;
Т – период стойкости сверла мин;
t – глубина сверления мм;
t1 – глубина резания при рассверливании мм;
По формулам (3.19) и (3.20) определяем скорость резания:
Произведем корректировку режимов резания согласно техническим характеристикам станка (по паспорту).
По формуле (3.12) определяем основное время:
Примем вспомогательное время равным ТВС = 11 мин.
Время на обслуживание и отдых определяем по формулам (3.16) и (3.17):
По формуле (3.5) определяем норму штучного времени:
Подготовительно-заключительное время примем равным ТПЗ = 4 мин.
Норму штучно-калькуляционного времени определяем по формуле (3.4):
Режимы по остальным операциям принятые по нормативам приведены в таблице 3.1.
Таблица 3.1 – Режимы операций по нормативам.
Наименование операции
Фрезерно-центровальная
ЗАКЛЮЧЕНИЕ.doc
В дипломном проекте были произведены следующие расчеты: расчет параметров отвала тяговый расчет расчеты усилий в производительных механизмах произведен расчет гидропривода бульдозера разработана гидравлическая схема выполнены расчеты на прочность элементов конструкции расчеты режимов обработки технологического процесса. Рассмотрены вопросы безопасности работы оператора бульдозера.
Экономические расчеты показали что экономический эффект от внедрения разработанного бульдозера составит 6617 тысячи рублей.
5 БЖД.doc
Уровень решения проблем обеспечения безопасности и жизнедеятельности человека в любом современном государстве может служить наиболее достоверным и комплексным критерием для оценки как степени экономического развития и стабильности этого государства так и для оценки нравственного состояния общества. Это объясняется тем что глубокое и всестороннее решение сложных проблем порожденных научно-техническим прогрессом требует громадных капиталовложений и высокой культуры производства а следовательно под силу только экономически высокоразвитому стабильному государству обладающему мощным научно-техническим и интеллектуальным потенциалом. С другой стороны решение проблем безопасности требует активного участия всех членов общества высокого гражданского самосознания готовности к ущемлению сегодняшних интересов а иногда к определенному ограничению индивидуальных свобод во имя жизни человека и развития будущих поколений.
Целью безопасности жизнедеятельности является защита человека работающего на производстве от разного рода возникающих в процессе его работы вредных факторов которые могут привести к травматизму или ухудшению здоровья работника а также обеспечение комфортных условий его труда.
Для того чтобы достигнуть этой цели необходимо решить ряд задач поставленных перед нами в процессе производства:
- создание безаварийных ситуаций при эксплуатации бульдозера;
- предупреждение травматизма на производстве;
- повышение уровня работоспособности;
- создание комфортных условий и качества труда.
Решение этих задач достигается за счет рассмотрения и анализа возникновения вредных факторов а также принятие мер по их предупреждению и устранению или приведению их к допустимым нормам.
Далее мы рассмотрим анализ и устранение вредных факторов возникающих в процессе работы проектируемого бульдозера.
1 Анализ опасных и вредных факторов
Объектом анализа опасностей является система «оператор – бульдозер – окружающая среда» (рисунок 1) в которой в единый комплекс предназначенный для выполнения определенных функций объединены технические объекты люди и окружающая среда взаимодействующие друг с другом. При оценке воздействия негативных факторов и достижения комфортных условий следует учитывать степень влияния их на здоровье и жизнь оператора.
Рисунок 5.1 – Система «оператор – бульдозер – окружающая среда».
1.1 Производственный микроклимат
Метеорологические условия рабочей среды (микроклимат) оказывают влияние на процесс теплообмена и характер работы. Микроклимат характеризуется температурой воздуха его влажностью и скоростью движения а также интенсивностью теплового излучения. Длительное воздействие на оператора неблагоприятных метеорологических условий резко ухудшает его самочувствие снижает производительность труда и приводит к заболеваниям.
Высокая температура воздуха способствует быстрой утомляемости работающего может привести к перегреву организма тепловому удару или профзаболеванию. Низкая температура воздуха может вызвать местное или общее охлаждение организма стать причиной простудного заболевания либо обморожения.
Влажность воздуха оказывает значительное влияние на терморегуляцию организма человека. Высокая относительная влажность (отношение содержания водяных паров в 1м3 воздуха к их максимально возможному содержанию в этом же объеме) при высокой температуре воздуха способствует перегреванию организма при низкой же температуре она усиливает теплоотдачу с поверхности кожи что ведет к переохлаждению организма. Низкая влажность вызывает пересыхание слизистых оболочек дыхательных путей работающего.
Подвижность воздуха эффективно способствует теплоотдаче организма человека и положительно проявляется при высоких температурах но отрицательно при низких.
Для создания нормальных условий труда в кабине оператора обеспечивают нормативные значения параметров микроклимата – температуры воздуха его относительной влажности и скорости движения а также интенсивности теплового излучения (ГОСТ 12.2.120-88).
В ГОСТ 12.1.005-88 указаны оптимальные и допустимые показатели микроклимата в производственных помещениях. Оптимальные показатели распространяются на всю рабочую зону (кабину) а допустимые устанавливают раздельно для постоянных и непостоянных рабочих мест в тех случаях когда по технологическим техническим или экономическим причинам невозможно обеспечить оптимальные нормы.
Методы снижения неблагоприятного влияния микроклимата осуществляется комплексом технологических санитарно-технических организационно-технических и методико-профилактических мероприятий.
Для обеспечения в кабинах микроклимата и предельно допустимых концентраций вредных веществ в воздухе устраивают естественную вентиляцию (люки форточки опускающиеся стекла) и принудительную а также пылеуловители воздухоохладители кондиционеры и отопители.
Ведущая роль в профилактике вредного влияния высоких температур инфракрасного излучения принадлежит технологическим мероприятиям: замена старого и внедрение нового оборудования способствующего снижению неблагоприятных условий труда.
К группе санитарно-технических мероприятий относится применение средств защиты: локализация тепловыделений от двигателя внутреннего сгорания теплоизоляция горячих поверхностей.
1.2 Влияние электромагнитных излучений
Спектр электромагнитного излучения природного и техногенного происхождения оказывающий влияние на человека как в условиях быта так и в производственных условиях имеет диапазон волн от тысяч километров (переменный ток) до триллионной части миллиметра (космические энергетические лучи). Характер воздействия на человека электромагнитного излучения в разных диапазонах различен. В связи этим значительно различаются и требования к нормированию различных диапазонов электромагнитного излучения.
Недостаточное освещение рабочего места затрудняет длительную работу вызывает повышенное утомление и способствует развитию близорукости. Слишком низкие уровни освещенности вызывают апатию и сонливость а в некоторых случаях способствуют развитию чувства тревоги. Длительное пребывание в условиях недостаточного освещения сопровождается снижением интенсивности обмена веществ в организме и ослаблением его реактивности. К таким же последствиям приводит длительное пребывание в световой среде с ограниченным спектральным составом света и монотонным режимом освещения.
Излишне яркий свет слепит снижает зрительные функции приводит к перевозбуждению нервной системы уменьшает работоспособность нарушает механизм сумеречного зрения.
Искусственное освещение помогает избежать многих недостатков характерных для естественного освещения и обеспечить оптимальный световой режим. Однако условия гигиены труда требуют максимального использования естественного освещения так как солнечный свет оказывает оздоровляющее действие на организм. Оно не используется только там где это противопоказано технологическими условиями производства.
Осветление кабины с четырех сторон позволит максимально использовать естественное освещение обеспечит обзорность.
При недостаточном естественном освещении в светлое время суток используют и искусственный свет. В кабине оператора устанавливают лампочки подсветки а на базовой машине обязательно наличие фар. Гигиеническое нормирование искусственного и естественного освещения осуществляется по СНиП 23-05-95.
Освещение в кабине составляет порядка 50лк.
1.3 Влияние звуковых волн
Шум – это беспорядочное сочетание звуков различной частоты и интенсивности (силы) возникающих при механических колебаниях в твердых жидких и газообразных средах. Шум отрицательно влияет на организм человека и в первую очередь на его центральную нервную и сердечно-сосудистую системы. Длительное воздействие шума снижает остроту слуха и зрения оператора повышает кровяное давление утомляет центральную нервную систему в результате чего ослабляется внимание увеличивается количество ошибок в действиях работающего снижается производительность труда. Воздействие шума приводит к появлению профессиональных заболеваний и может явиться также причиной несчастного случая. Источниками производственного шума являются: базовая машина (шум работающего двигателя стук в коробках передач и т. д.) оборудование и инструмент.
Постоянным считается шум уровень которого за восьмичасовой рабочий день изменяется во времени не более чем на 5 дБА непостоянным — более чем на 5 дБА.
ГОСТ 12. 1.003 – 83 устанавливает предельно-допустимые условия постоянного шума на рабочих местах при которых шум действуя на работающего в течение восьмичасового рабочего дня не приносит вреда здоровью.
Производственный шум нарушает информационные связи что вызывает снижение эффективности и безопасности деятельности человека так как высокий уровень шума мешает услышать предупреждающий сигнал опасности. Кроме того шум вызывает обычную усталость. При действии шума снижаются способность сосредоточения внимания точность выполнения работ связанных с приемом и анализом информации и производительность труда.
Наиболее эффективным является борьба с шумом в источнике его возникновения. Шум механизмов возникает вследствие упругих колебаний как всего механизма так и отдельных его деталей. Причины возникновения шума – механические аэродинамические и электрические явления определяемые конструктивными и технологическими особенностями оборудования а также условиями эксплуатации. Так в бульдозере источниками шума являются: двигатель стартер генератор трансмиссия рабочий орган во время копания. В связи с этим различают шумы механического аэродинамического и электрического происхождения. Для уменьшения механического шума необходимо своевременно проводить ремонт оборудования: заменять ударные процессы на безударные шире применять принудительное смазывание трущихся поверхностей применять балансировку вращающихся частей.
Значительное снижение шума достигается при замене подшипников качения на подшипники скольжения зубчатых и цепных передач клиноременными и зубчатоременными передачами металлических деталей – деталями из пластмасс.
Широкое применение получили методы снижения шума на пути его распространения посредством установки звукоизолирующих и звукопоглощающих преград. Например: шумоизоляционные перегородки кабин кожух на двигатель и другое.
Средствами индивидуальной защиты от шума являются ушные вкладыши наушники и шлемофоны ГОСТ 12.4.051-78. Эффективность индивидуальных средств защиты зависит от используемых материалов конструкции силы прижатия правильности ношения.
1.4 Влияние вибрации
Вибрация представляет собой процесс распространения механических колебаний в твердом теле.
Длительное воздействие вибрации ведет к развитию профессиональной вибрационной болезни. Вибрация воздействуя на машинный компонент системы ЧМ (человек – машина) снижает производительность технических установок (за исключением специальных случаев) и точность считываемых показаний приборов вызывает знакопеременные приводящие к усталостному разрушению напряжения в конструкции.
Вибрации могут быть непреднамеренными (например из-за плохой балансировки и центровки вращающихся частей машин и оборудования пульсирующего движения жидкости) и специально используемые в технологических процессах.
Особенно вредны вибрации с вынужденной частотой совпадающие с частотой собственных колебаний тела человека или его отдельных органов (для тела человека 6 9 Гц головы 6 Гц желудка 8 Гц других органов – в пределах 25 Гц).
Частотный диапазон расстройств зрительных восприятий между 60 и 90 Гц что соответствует резонансу глазных яблок.
Для санитарного нормирования и контроля вибраций используется ГОСТ 12.1.012-90.
При работе бульдозера возникают горизонтальные и вертикальные толчки и тряска сопровождающиеся возникновением периодических импульсных ускорений.
На оператора бульдозера действуют общая вибрация – от двигателя трансмиссии рабочего оборудования; локальная – на руки от трансмиссии передаваемая через рычаги коробки передач на ноги от двигателя передаваемая через педали.
Для борьбы с вибрацией машин и оборудования и защиты работающих от вибрации используют различные методы. Борьба с вибрацией в источнике возникновения связана с установлением причин появления механических колебаний и их устранением например замена кривошипных механизмов равномерно вращающимися тщательный подбор зубчатых передач балансировка вращающихся масс и тому подобное. Для снижения вибрации широко используют эффект вибродемпфирования – превращение энергии механических колебаний в другие виды энергии чаще всего в тепловую. Для ослабления передачи вибрации от источников ее возникновения полу рабочему месту сиденью рукоятке широко применяют методы виброизоляции. Для этого на пути распространения вибрации вводят дополнительную упругую связь в виде виброизоляторов из резины пробки войлока асбеста стальных пружин. В качестве средств индивидуальной защиты работающих используют специальную обувь на массивной резиновой подошве. Для защиты рук служат рукавицы перчатки вкладыши и прокладки которые изготовляют из упругодемпфирующих материалов.
Важным для снижения опасного воздействия вибрации на организм человека является правильная организация режима труда и отдыха постоянное медицинское наблюдение за состоянием здоровья лечебно-профилактические мероприятия такие как гидропроцедуры (теплые ванночки для рук и ног) массаж рук и ног витаминизация и другое.
2 Экологическая безопасность
Защита воздушного бассейна от загрязнений регламентируется предельно допустимыми концентрациями вредных веществ в атмосферном воздухе населенных пунктов предельно допустимыми выбросами вредных веществ и временно согласованными выбросами вредных веществ от источника загрязнения. Картерные газы и топливные испарения загрязняют воздушный бассейн в основном углеводородом и учитываются дополнительным коэффициентом. При отсутствии в конструкции машины мембранной замкнутой системы вентиляции картера суммарный выброс углеводородов рекомендуется увеличить в среднем в полтора раза. Предельно-допустимые выбросы машин с двигателем внутреннего сгорания регламентируются ГОСТом 17.2.2.203-87.
Основные компоненты выбрасываемые в атмосферу при сжигании различных видов топлива в двигателях внутреннего сгорания - нетоксичные диоксид углерода и водяной пар. Однако кроме них в атмосферу выбрасываются и вредные вещества такие как оксид углерода оксиды серы азота соединения свинца сажа углеводороды в том числе канцерогенный бенз(а)пирен несгоревшие частицы твердого топлива и тому подобное.
Токсичными выбросами двигателей внутреннего сгорания являются отработавшие картерные газы пары топлива из топливного бака. Основная доля токсичных примесей поступает в атмосферу с отработавшими газами двигателя внутреннего сгорания. С картерными газами и парами топлива в атмосферу поступает около 45% углеводородов от их общего выброса.
Исследования состава отработавших газов двигателей внутреннего сгорания показывают что в них содержится несколько десятков компонентов. Дизельные двигатели внутреннего сгорания выбрасывают в больших количествах сажу которая в чистом виде нетоксична. Однако частицы сажи обладая высокой адсорбционной способностью несут на своей поверхности частицы токсичных веществ в том числе и канцерогенных. Сажа может длительное время находится во взвешенном состоянии в воздухе увеличивая время воздействия токсичных веществ на человека.
Состав отработавших газов двигателей внутреннего сгорания зависит от режима работы двигателя. В дизелях с уменьшением нагрузки содержание токсичных компонентов в отработавших газах уменьшается а при работе на режиме максимальной нагрузки возрастает за счет роста выбросов оксида углерода оксидов азота и углеродов. Количество вредных веществ поступающих в атмосферу в составе отработавших газов зависит от общего технического состояния машин и особенно от двигателя – источника наибольшего загрязнения.
Большое внимание должно быть уделено охране природы в процессе земляных работ (ГОСТ 17.2.203-87). При подготовке трассы сооружения необходимо очищать ее от леса и кустарника с максимально возможным сохранением лесного массива. Деревья ценных пород должны быть пересажены. По возможности следует избегать использования грунта из боковых резервов или ограничивать их глубину до 1 15 м.
В соответствии с действующим законодательством строительные организации работающие на сельскохозяйственных землях и лесных угодьях должны за свой счет приводить эти участки в состояние пригодное для дальнейшего использования (рекультивировать). Работы выполняются в ходе строительства или не позднее чем в течение года после их завершения. При рекультивации растительный слой грунта срезанный во время расчистки под будущее сооружение и перемещенный в сторону возвращают на открытые грунтовые участки резервов.
При эксплуатации бульдозера необходимо также соблюдать следующие правила.
Запрещается работа на машинах с повышенной дымностью при утечках топлива масел рабочих жидкостей. Попадая в грунт эти материалы отрицательно влияют на окружающую природу. Категорически запрещается сливать отработавшие нефтепродукты на землю в водоемы и канализационную сеть. Эти материалы следует собирать и сдавать на нефтебазы или уничтожать методами согласованными с Госсанинспекцией.
3 Расчет сварного соединения
Одним из необходимых условий нормальной жизнедеятельности человека является обеспечение безопасности работающих людей. Безопасность работы человека должна обеспечиваться не только при работе бульдозера но и при его обслуживании.
На рисунке 5.1 представлен рабочий орган бульдозера.
Рисунок 5.1 – Рабочее оборудование проектируемого бульдозера.
При работе бульдозера основным отвалом 1 дополнительный ковш 2 поднимается в положение показанное на рисунке 5.1 а следовательно в сечении сварного шва 3 под действием силы тяжести дополнительного ковша будут возникать напряжения стремящиеся разрушить сварное соединение.
В данном разделе представлен расчет сварного соединения боковой стенки отвала с рычагом подъема и опускания ковша.
Как нам известно данное соединение является нахлесточным следовательно его выполняют угловыми швами. В данном случае по расположению относительно нагрузки этот шов является лобовым.
Лобовые швы во избежание возникновения повышенных напряжений изгиба следует накладывать с двух сторон.
Расчет угловых швов всех видов унифицирован и производится по единым формулам. Напряжение возникающее в опасном сечении шва определяется по формуле:
где F – усилие прикладываемое к сварному шву кН;
– коэффициент характеризующий глубину проплавления; = 07;
k – катет треугольника поперечного сечения шва см; k = 06 см;
[СР] – среднее допустимое напряжение среза кНсм2;
Рисунок 5.2 – Расчетная схема лобового шва.
Расчет основываем на следующих допущениях: швы работают независимо фланговые швы короткие и передают только силы направленные вдоль своей оси сила действует на середину шва.
Сила действующая на сварное соединение определяется по формуле:
где G' – сила тяжести дополнительного отвала кН;
– угол подъема дополнительного отвала град; = 40;
По формуле (5.2) определяем силу действующую на соединение:
По формуле (5.1) определяем напряжение в опасном сечении шва:
Неравенство (5.1) запишется как:
Следовательно имеющийся шов обеспечивает надежное соединение.
Рекомендуемые чертежи
- 04.11.2022
- 04.11.2022
- 25.01.2023
- 24.01.2023
- 04.11.2022
- 04.11.2022