Выпускная квалификационная работа - Повышение эффективности работы оборудования Костромской ГРЭС


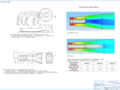
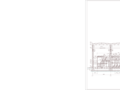
- Добавлен: 04.11.2022
- Размер: 1 MB
- Закачек: 0
Описание
Состав проекта
![]() |
![]() ![]() ![]() ![]() |
![]() ![]() ![]() |
![]() ![]() ![]() ![]() |
![]() ![]() ![]() |
Дополнительная информация
Поперечный разрез гл.корпуса.frw

корпуса блока N9 КГРЭС
Повышение эффективности работы
оборудования Костромской ГРЭС
Пояснительная записка.docx
«ИВАНОВСКИЙ ГОСУДАРСТВЕННЫЙ ЭНЕРГЕТИЧЕСКИЙ
УНИВЕРСИТЕТ ИМЕНИ В.И. ЛЕНИНА»
ПОЯСНИТЕЛЬНАЯ ЗАПИСКА
к выпускной квалификационной работе на тему:
Повышение эффективности работы
оборудования Костромской ГРЭС
федеральное государственное бюджетное образовательное учреждение
«Ивановский государственный энергетический университет
на выпускную квалификационную работу студента
Содержание расчетно-пояснительной записки (перечень подлежащих разработке вопросов):__
Выпускная квалификационная работа. ИГЭУ 2017. Повышение эффективности работы оборудования Костромской ГРЭС.
Ключевые слова: Тепловая электрическая станция паровой котел паровая турбина тепловая схема аэродинамическая схема.
Стр. 65 рис. 13 табл. 7 литература 16.
В данной выпускной работе предлагается реконструкция оборудования Костромской ГРЭС.
В записке приведены общие сведения о Костромской ГРЭС описание основного и вспомогательного оборудования. Представлен расчёт тепловой схемы блока 1200 МВт.
В специальной части рассмотрен вопрос о повышении эффективности оборудования Костромской ГРЭС с помощью внедрения новой аэродинамической схемы участка сопряжения «дымосос – газоход».
ОБЩИЕ СВЕДЕНИЯ О КОСТРОМСКОЙ ГРЭС9
1.Основные сооружения электростанции10
2.Выбор места строительства КГРЭС11
3.Выбор мощности КГРЭС11
4.Сооружения электрической части11
5.Управление и автоматика12
6.Топливоснабжение ГРЭС14
7.Водоснабжение ГРЭС15
КОМПОНОВКА ГЛАВНОГО КОРПУСА ЭЛЕКТРОСТАНЦИИ18
ОПИСАНИЕ ВСПОМОГАТЕЛЬНОГО ОБОРУДОВАНИЯ26
1.Конденсационная установка26
2.Конденсаторные насосы26
3.Система регенерации турбины27
4.Питательная установка блока27
5.Турбоприводы воздуходувок28
6.Особенности тепловой схемы турбины К-1200-24029
8.Характеристика НКК30
9.Характеристика секции калориферов31
10.Характеристика дымососов31
11.Высоконапорный дутьевой вентилятор ВДН-36*232
РАСЧЕТ ТЕПЛОВОЙ СХЕМЫ ТУРБИНЫ К-1200-240 И ВЫБОР ВСПОМОГАТЕЛЬНОГО ОБОРУДОВАНИЯ БЛОКА 1200 МВт33
1.Расчет расхода пара на ПВД33
2.Питательная установка блока33
3.Параметры пара и воды на ПВД35
4.Параметры питательной воды35
5.Параметры конденсата греющего пара38
6.Определение расходов пара на ПВД38
7.Определение параметров воды за ПВД и величины погрешности38
8.Определение параметров воды за выносным пароохладителем и параметров воды на входе в котел43
9.Определение параметров пара и воды в ПНД44
10.Расчет деаэратора47
11.Определение расходов пара на ПНД47
12.Определение параметров воды за ПНД48
13.Определение в долях расхода пара в конденсатор49
14.Определение расхода пара на турбоустановку по hs-диаграмме49
15.Определение количественных расходов пара и воды50
16.Определение мощности по отборам и сведение баланса по мощности50
17.Определение энергетических показателей50
18.Выбор оборудования блока53
19.Общестанционное оборудование55
СПЕЦИАЛЬНАЯ ЧАСТЬ: ПОВЫШЕНИЕ ЭФФЕКТИВНОСТИ РАБОТЫ ОБОРУДОВАНИЯ КОСТРОМСКОЙ ГРЭС56
2.Анализ аэродинамической эффективности существующей схемы участка сопряжения «дымосос – газоход»58
3.Разработка новой аэродинамической схемы участка сопряжения «дымосос – газоход»63
БИБЛИОГРАФИЧЕСКИЙ СПИСОК:65
За время перехода нашего общества к новым социально-экономическим отношениям и перестройки промышленности на рельсы рыночной экономики Российская электроэнергетика в лице РАО "ЕЭС России" и её дочерних обществ переживает состояние острого кризиса обусловленного как общими проблемами российской экономики так и рядом специфических факторов обусловленных структурным построением и управлением электроэнергетикой.
В проекте для обсуждения (одобрен решением правления РАО "ЕЭС России" 27.03.2000 г.) новой концепции реструктуризации РАО "ЕЭС России" основной целью которой является формирование финансово-устойчивой компании обеспечение условий для привлечения инвестиций роста капитализации компаний электроэнергетического комплекса России и надёжное и бесперебойное энергоснабжение платёжеспособных потребителей предложены пути преодоления кризиса.
Основными принципами реструктуризации РАО "ЕЭС России" являются: повышение инвестиционной привлекательности и капитализации как РАО "ЕЭС России" так и отрасли в целом: разделение генерации транспорта и диспетчеризации сбыта вспомогательных производств.
Обеспечение единства управления транспортом электроэнергии и диспетчеризация путём создания единой сетевой компании регулируемой государством.
Проведение экспортной политики с постепенной либеризацией внешнеэкономической деятельности.
Пересмотр механизмов ценового регулирования в электроэнергетике с сохранением государственного регулирования в сфере естественной монопольной деятельности и развитием рыночного ценообразования на конкурентных направлениях.
Монетаризации расчётов в электроэнергетике за счёт последовательного применения принципа надёжного и бесперебойного снабжения платёжеспособного потребителя.
Проведение социально-ответственной политики предусматривающей первоочередное решение возникающих в процессе реструктуризации социальных вопросов.
Проведение научной и технической политики направленной на ускоренное обновление технологий и оборудования на современной технической основе стимулирование инновационного процесса.
Осуществление реструктуризации разбито на три этапа:
Реструктуризация по видам бизнеса.
Привлечение инвестиций в электроэнергетику.
Развитие комплекса РАО "ЕЭС России".
Рассмотрим одну из целей реализации первого этапа – снизить себестоимость производства электроэнергии за счёт загрузки самых эффективных мощностей вывода неэффективных мощностей из работы рационализация закупок топлива материалов и услуг снижение уровня неоправданных затрат и улучшение организации производства.
Выбор оптимальных направлений технического перевооружения и реконструкции ТЭС и котельных от устойчивости которых зависит надёжность и экономичность энергоснабжения является на ближайшие годы одной из важнейших научно-технических проблем в энергетике. Это связано с тем что значительная часть основного оборудования действующих ТЭЦ достигла предельных сроков службы.
Реальные объёмы ввода новых энергетических мощностей и осуществление намеченных программ по энергосбережению не позволяют рассчитывать на компенсацию выбывающих энергетических мощностей в ближайшем будущем. Это обстоятельство подчеркивает важность задачи технического перевооружения ныне действующего оборудования ТЭС. В последнее время ведётся значительная работа по обновлению тепловых электрических станций.
Применительно к тепловым электрическим централям приняты следующие направления технического перевооружения и реконструкции:
Повышение эффективности теплофикации за счёт увеличения доли комбинированной электрической энергии привлечение КЭС или отдельных конденсационных агрегатов для работы по теплофикационному циклу.
Применение прогрессивного технологического оборудования улучшение маневренных характеристик оборудования.
Продление срока эксплуатации оборудования отработавшего расчётный ресурс времени с заменой изношенных деталей и узлов.
Модернизация действующего оборудования для повышения его надёжности и экономичности.
ОБЩИЕ СВЕДЕНИЯ О КОСТРОМСКОЙ ГРЭС
Костромская ГРЭС – одна из крупнейших станций в Европейской части России. Электростанция входит в РАО «ЕЭС России». КГРЭС расположена на юго-западе Костромской области на реке Волга которая служит источником водоснабжения для станции.
Строительство электростанции осуществлялось в три очереди. На первой очереди было установлено четыре дубль-блока мощностью по 300 МВт с двухкорпусными газомазутными котлами паропроизводительностью 950 тч. На второй очереди - четыре моноблока по 300 МВт с однокорпусными газомазутными котлами паропроизводительностью 950 тч. В состав всех энергоблоков входят паровые турбины мощностью по 300 МВт с начальными параметрами пара: давление 240 кгссм2 температура острого пара 540 °С; температура вторичного перегретого пара 540 °С. Суммарная установленная мощность энергоблоков первой и второй очереди – 2400 МВт.
На третьей очереди электростанции устанавливается головной энергоблок мощностью 1200 МВт с однокорпусным газоплотным подвесным газомазутным котлом паропроизводительностью 3950 тч одновальной турбиной мощностью 1200 МВт и генератором с бесщёточным возбудителем.
Энергоблоки мощностью по 300 МВт вводились в эксплуатацию с июня 1969 года по июль 1973 года а энергоблок 1200 МВт был введён в эксплуатацию в 1980 году.
После завершения строительства Костромская ГРЭС имеет установленную мощность 3600 МВт.
1.Основные сооружения электростанции
К основным сооружениям электростанции относятся: главный корпус энергоблоков 300 МВт главный корпус энергоблока 1200 МВт инженерно-бытовой корпус химводоочистка топливное хозяйство сооружения системы технического водоснабжения сооружения электрической части.
Главный корпус энергоблоков 300 МВт – трёхпролётный:
машинный зал – 45 метров деаэраторное отделение – 12 метров котельное отделение дубль-блоков – 33 метра моноблоков – 39 метров
шаг колонн – 12 метров.
Главный корпус выполнен из сборного железобетона (за исключением металлических ферм и подкрановых балок машинного и котельного отделений) с применением новых строительных материалов и конструкций фундаменты под колонны выполнены облегчёнными. Стеновое ограждение впервые в практике энергостроительства выполнено из керамзитобетонных панелей. Световые проёмы выполнены из стеклопрофилита.
Расположение турбоагрегатов в машинном зале – поперечное. Тепловая схема – блочная.
Машинный зал обслуживают три мостовых крана грузоподъёмностью по 12520 тс котельное отделение – три мостовых крана по 5010 тс.
На открытой площадке за главным корпусом расположены дымососы дутьевые вентиляторы и регенеративные воздухоподогреватели. Для отвода дымовых газов от котлоагрегатов сооружены две дымовые трубы высотой по 250 м.
Дымовая труба моноблоков выполнена из несущей железобетонной оболочки в которой установлено четыре стальных отводящих ствола каждый из которых обслуживает один энергоблок.
Главный корпус энергоблока 1200 МВт – пятипролётное здание. Машинный зал имеет два пролёта – 30 и 54 метра деаэраторная
этажерка – 15 метров котельное отделение – 45 метров помещение воздуходувок – 15 метров. Каркас главного корпуса запроектирован в металлических конструкциях что обусловлено большими нагрузками на колонны котельного отделения от подвесного котла который опирается на хребтовые балки с шагом 6 метров. Стеновое ограждение принято комбинированным с применением напряжённо-армированных керамзитобетонных панелей из стального профилированного листа с синтетическим утеплением. Междуэтажные перекрытия выполнены сборными железобетонными оконные проёмы – из световых панелей в металлических переплётах и стеклопрофилита.
Машинный зал обслуживают четыре мостовых крана грузоподъёмностью по 12520 тс котельное отделение – два крана по 10010 тс.
Дымососы и регенеративные воздухоподогреватели расположены на открытой площадке за главным корпусом. Для выброса дымовых газов сооружена дымовая труба высотой 320 метров с кремнебетонным газоотводящим стволом в железобетонной оболочке.
Инженерно-бытовой корпус расположен между главными корпусами энергоблоков 300 МВт и 1200 МВт. он состоит из нескольких сблокированных зданий. В нём размещаются центральный щит управления автоматизированная система управления технологическими процессами электростанции цеха и отделы. Инженерно-бытовой корпус соединяется переходными мостиками с главными корпусами.
2.Выбор места строительства КГРЭС
Выбор площадки для строительства КГРЭС на правом берегу Волги в устье небольшого волжского притока реки Шача в сорока километрах от Костромы определяется тремя основными условиями:
Дефицитом электрической мощности в близлежащем экономическом районе.
Обеспеченностью водой. (Горьковское водохранилище на Волге).
Наличием удобных транспортных связей.
3.Выбор мощности КГРЭС
Технико-экономические исследования определили конечную мощность электростанции 4800 МВт. Наращивание мощности электростанции осуществлялось тремя очередями. Мощность первой очереди 1200 МВт - обеспечена четырьмя дубль-блоками по 300 МВт. Турбоагрегаты первой очереди ГРЭС введены в эксплуатацию за период с июня 1969 г. по декабрь 1970 г. Вторая очередь также имеет мощность 1200 МВт обеспеченную более совершенными моноблоками по 300 МВт. Энергоблоки второй очереди вводились с декабря 1971 г. по июнь 1973 г. Третья очередь в настоящее время представлена одним блоком мощностью 1200 МВт пущена в 1980г. В настоящее время мощность КГРЭС составляет 3600 МВт.
4.Сооружения электрической части
Выдача электрической мощности от электростанции производится на напряжениях 220 и 500 кВ. Энергоблоки 300 МВт через трехфазные повышающие трансформаторы мощностью 400 МВА соединяются с ОРУ 220 кВ и
Генератор энергоблока 1200 МВт присоединяется к ОРУ 500 кВ через три однофазных трансформатора мощностью 533 МВА.
ОРУ 220кВ выполнено с двумя системами шин и обходной системой шин. ОРУ 500 кВ выполнено по схеме многоугольника. Связь между ОРУ 220кВ и ОРУ 500 кВ осуществляется через группу автотрансформаторов суммарной мощностью 801 МВА которая одновременно служит для выдачи мощности одного из дубль-блоков 300 МВт.
Собственные нужды энергоблоков 300 МВт покрываются на напряжении 6 кВ от трансформаторов мощностью 25 МВА энергоблока 1200 МВт - от трансформатора мощностью 40 МВА.
Для энергоблоков 300 МВт имеется два резервных трансформатора напряжением 2206 кВ мощностью по 32 МВА для энергоблока 1200 МВт мощностью 63 МВА.
5.Управление и автоматика
Управление и контроль за работой оборудования блоков осуществляется
с блочных щитов управления. На блоках 300 МВт таких щитов четыре (1 БЩУ на два блока). Энергоблок 1200 МВт имеет свой отдельный щит управления.
На блочные щиты установлены приборы регулирования работы основного и
вспомогательного оборудования а также аппаратура необходимая для
пуска и останова энергоблока. Все основные технологические процессы
автоматизированы. На блочных щитах установлены информационно-
вычислительные комплексы а также панели защиты и сигнализации. В
состав ИВК блоков 300 МВт входят: 6 комплексов ТВСО-РМОТ на блоках 24-8. На блоках 2 и 4 ТВСО и два РМОТ на остальных блоках по одному РМОТ. ТВСО (терминалы вычислительной связи с объектом) предназначены для сбора предварительной обработки и передачи в локальную вычислительную сеть (ЛВС) аналоговой и дискретной информации электрической части ГРЭС и общестанционного уровня. РМОТ (рабочее место оператора технолога) отображает аналоговую и дискретную информацию на экранах телевизоров.
На каждом комплексе функционирует программная система ОПРОС и программа КВП (контроль выбегов параметров).
Автоматизированная система управления технологическими процессами (АСУ ТП) энергоблока 1200 МВт представляет собой сложную систему для выработки и реализации управляющих воздействий на энергоблок с применением методов оптимального управления современных средств вычислительной техники функционально-группового управления автоматического регулирования связи а также традиционных средств контроля и управления. В состав ИВК блока 1200 МВт входят два вычислительных комплекса СМ-2М с периферийным оборудованием и информационный комплекс М-60.
В состав М-60 входят 2 УКДД (устройства коммутации дискретных датчиков) 12 УКНП (устройств коррекции нормирования преобразования для аналоговых данных) ПИК (пульт информационного комплекса) 8 цифровых приборов (расположенных на БЩУ-5) 2 УСВК (устройства связи с вычислительным комплексом).
Аналоговая информация от датчиков поступает в УКНП где она преобразуется в спец. коды. Дискретная информация от датчиков поступает в УКДД где она так же преобразуется в спец. коды. Из УКНП и УКДД информация через УСВК поступает в ВК. Там она поступает в программные комплексы решающие целый ряд задач:
-ОКО - обобщённый контроль и отображение информации на экране ЭЛИ (электронно-лучевых индикаторов а проще говоря цветных телевизоров);
-РАС - регистрация аварийных ситуаций;
-АДЗ - анализ действия защит;
-ТЭП - расчёт технико-экономических показателей;
-СОВ - система оптимизации вакуума;
-ФСОТ - функция связи с оператором-технологом;
-СПИПП - сбор и представление информации о переходных процессах.
Выходная информация ИВК в виде фрагментов таблиц графиков поступает к потребителю: персоналу КТЦ-2 ПТО ЦНИО и т. д. На каждом блоке есть ПК с системой вибродиагностики . Кроме этого есть 4 ПК (по 2 на каждую очередь) с системой контроля водно-химического режима. На блоке также 2 ПК с системой контроля водно-химического режима.
АСУ ТП энергоблоков связана с автоматизированной системой управления технологическими процессами электростанции АСУ ТП ГРЭС центрального щита управления. АСУ ТП ГРЭС производит расчет технико-экономических показателей работы электростанции и оптимизацию распределения нагрузок между энергоблоками. В состав ИВК АСУ ТП ГРЭС центрального щита управления входят:
ТВСО ЦЩУ – осуществляет сбор и предварительную обработку информации об оперативных параметрах главной схемы электрических соединений ГРЭС основных параметрах ГРП 1-3 других общестанционных параметрах а также о переключении выключателей 6 кВ собственных нужд блоков 1-9.
ТВСО РЩ-220 – осуществляет сбор и предварительную обработку информации о состоянии коммутационных аппаратов ОРУ-220 кВ. Программный оперативно-информационный комплекс (ОИК) работающий на персональных компьютерах (PC) под управлением М8В08 (операционная система) по локальной вычислительной сети (ЛВС). ОИК включает в себя следующие устройства:
PC ОИК - выполняет следующие функции:
-сбор информации с ТВСО РЩ-220 через PC РЩ-220 ТВСО ЦЩУ ВК СМ-2М блока 9 через PC ИВК бл.9 ее обработку и передачу на сервер "А8И8ТАК";
Сервер АСУ ТП ГРЭС "А8ШТАК" :
-хранит архивы базы данных и адреса PC АСУ ТП ГРЭС;
-организует обмен данными с клиентами сетевых задач;
-обеспечивает поддержание единого времени на PC АСУ ТП ГРЭС.
PC пользователей (оперативный и управленческий персонал) -
производят представление оперативному персоналу и другим
пользователям по запросу технологической информации имеющейся на сервере "А8и8ТАК".
АСУ ТП ГРЭС решает следующие основные задачи:
-коммерческий учет выработки и распределение электроэнергии;
-коммерческий и технический учет потребления природного газа ГРЭС;
-регистрация и представление оперативному персоналу ЦЩУ а также пользователям сети АСУ ТП следующей технологической информации:
по потреблению природного газа;
по параметрам работы основного электрооборудования ГРЭС;
по диспетчерскому графику нагрузки;
по переключению коммутационных аппаратов на ОРУ-220 кВ и срабатыванию устройств РЗА на РЩ-220 кВ;
по переключению выключателей 6 кВ питания СН блоков 1-9;
6.Топливоснабжение ГРЭС
Топливом для электростанции является высокосернистый мазут и природный газ. Мазут доставляется по железной дороге а в период навигации – водным путём по реке Волга. Мазут хранится в железобетонных резервуарах полуподземного типа и рассчитан на 15-ти суточный расход при работе станции с номинальной нагрузкой. Разогрев мазута в железнодорожных цистернах производится открытым паром из 13-ти атмосферного коллектора с температурой 255 °С. После разогрева мазут подаётся в резервуары. К форсункам котлоагрегата мазут подаётся с давлением 47 кгссм2 и температурой
Подача природного газа осуществляется от магистрального газопровода. Газовое хозяйство включает газораспределительную станцию откуда газ под давлением 11 кгссм2 подаётся к газораспределительным пунктам электростанции. Таких ГРП на электростанции три. На каждую очередь предусмотрен свой ГРП. При работе электростанции на газовом топливе мазут непрерывно циркулирует по внешнему мазутному кольцу которое проходит непосредственно вокруг топочной камеры котлоагрегата на уровне третьего яруса горелок. Пройдя по мазутному кольцу мазут возвращается на мазутное хозяйство где вновь подогревается до определённой температуры и затем мазутными насосами 1-го и 2-го подъёма подаётся либо вновь во внешнее мазутное кольцо либо к мазутным форсункам в зависимости от необходимости.
7.Водоснабжение ГРЭС
Система технического водоснабжения Костромской ГРЭС прямоточного типа. Источником водоснабжения является Горьковское водохранилище на реке Волга. Подводящий канал открытый земляной с укреплёнными бетоном берегами. Водозабор циркуляционной воды – глубинный осуществляется тремя береговыми насосными станциями. Каждая БНС снабжает циркводой отдельную очередь электростанции. На каждый энергоблок приходится по два циркуляционных насоса. Таким образом береговые насосные станции блоков 300 МВт т.е. блоков 1-ой и 2-ой очереди оборудованы восьмью циркнасосами каждая а БНС блока 1200 МВт оборудована двумя циркнасосами. Каждый циркнасос как на блоках 300 МВт так и на блоке 1200 МВт вертикально-пропеллерного типа. Насосы снабжены поворотно-лопастными устройствами что позволяет регулировать их производительность в зависимости от нагрузки блока. Кроме того циркнасосы блока 1200 МВт являются двухскоростными агрегатами что также существенно повышает их маневренность.
Отводящие каналы выполнены двух видов: закрытые – из сборного железобетона и открытые – земляные.
Водоснабжение ГРЭС включает комплекс гидротехнических сооружений обеспечивающих поступление воды из реки Волги через глубинный водозабор и рыбозаградитель по подводящему каналу шириной по дну 20 метров проложенному параллельно главному корпусу по территории пристанционного узла до блочной насосной станции энергоблока № 9 на нужды энергоблоков с последующим возвратом теплой воды в реку Волга. Максимальный расход воды на нужды энергоблоков № 1-8 в летний период составляет 288000 м3час.
Вдоль главного корпуса проложены четыре подземных железобетонных канала (по одному на два энергоблока) по которым вода сливается через сбросное сооружение по отводящему каналу в залив реки Шачи. Четвертый железобетонный канал соединен со сбросным сооружением энергоблока № 9 для обеспечения теплой водой рыбоводное хозяйство на случай его останова.
Выход воды со сбросного сооружения энергоблока № 9 выведен вверх реки Волги на 5 км. Для предотвращения забивания вращающихся сеток циркуляционных насосов шугой выполнена перемычка между 4-м сбросным и подводящим каналом с установкой в колодце ШК-IV двух поворотных шандор. Перемычка смонтирована в районе рыбозаградителя.
Часть воды поступающей от ЦЭН отбирается подъемными насосами эжекторов (ПНЭ) на эжекторы энергоблоков а также используется на охлаждение масла огнестойкой жидкости систему охлаждения газа генератора воздухоохладителя электродвигателя ПЭН и резервных возбудителей подшипники вращающихся механизмов и другие нужды энергоблока.
Насосами сырой воды циркуляционная вода подается на химводоочистку а также в пожарные водопроводы мазутного хозяйства внутренние и внешние пожарные кольца главного корпуса.
Для проведения ремонта и осмотра железобетонных каналов имеется система железобетонных колодцев и отключающих шандор. Большая площадь отводящих каналов с трех очередей ГРЭС создала благоприятные условия для организации рыбоводного хозяйства в теплых водах.
Характеристика волжской воды:
-содержание кремния общее:
Для обеспечения потребностей всей электростанции в химобессоленной воде на Костромской ГРЭС введена в эксплуатацию химводоочистка производительностью 500 тч. Она работает по схеме коагуляции и трехступенчатого обессоливания. Все процессы приготовления обессоленной воды полностью автоматизированы.
Рис. 1. Схема водоочистки.
КОМПОНОВКА ГЛАВНОГО КОРПУСА
Исходя из условий надёжной работы металла в области критических температур по конструктивным соображениям учитывая что модернизируемый котёл ориентирован на параметры тепловой схемы с турбиной мощностью 1200 МВт и предназначен для работы в базовой части графика нагрузок целесообразно принять следующие параметры пара:
Р0 = 235 МПа; t0 = 540 °C; Рпп = 39 МПа; tпп = 540 °С.
При выборе элементов основного оборудования блока необходимо отметить что оборудование является уникальным по своей конструкции.
Однокорпусный котёл Таганрогского котельного завода газомазутный
П-образной компоновки заводская марка ТГМП-1202 по
ГОСТ-ПП-3950225-ГМ.
Техническая характеристика котла:
-паропроизводительность:
-расход пара через промперегреватель:
-давление пара на выходе из котла:
-температура острого пара:
-давление пара на выходе из вторичного пароперегревателя:
-температура вторичного пара:
-температура питательной воды:
-температура горячего воздуха:
-температура уходящих газов:
-основное – высокосернистый мазут: QHP – 9500 ккалкг;
-резервное – природный газ: QHP – 8100 ккалкг.
В настоящее время котлоагрегат большую часть рабочего периода функционирует на природном газе. Таким образом мазут как основное топливо утратил данное значение. КПД котельного агрегата брутто:
-при сжигании мазута – 9386 %;
-при сжигании газа – 946 %.
Масса котла – 13500 т.
Топочная камера призматическая открытая является восходящим газоходом. В нижней её части на фронтальной и задней стенках в три яруса размещены 56 комбинированных газомазутных горелок (по 10 горелок в верхнем и нижнем ярусе с каждой стороны и 8 горелок в среднем ярусе с каждой стороны).
Цельносваренные экраны на высоте топочной камеры разделены на три радиационные части: нижнюю (НРЧ) среднюю (СРЧ) верхнюю (ВРЧ). В горизонтальном газоходе размещают вертикальный ширмовой пароперерегреватель высокого давления первую и вторую ступени конвективного пароперегревателя высокого давления выходную ступень промперегревателя. В опускном конвективном газоходе последовательно по ходу газов расположены промежуточная и входная ступень промперегревателя и водяной экономайзер.
Расчётная производительность по газу горелки составляет 153 м3с (554·103 м3ч) по мазуту – 143 кгс (514 тч).
Площади сечения для прохода воздуха по внутреннему каналу – 0194 м2 по периферийному каналу – 0308 м2 по каналу газов рециркуляции – 03 м2.
На номинальном режиме работы котла воздух и газы рециркуляции имеют следующие скорости на выходе из горелки: воздух внутренний
5 мс воздух периферийный – 705 мс газы рециркуляции – 199 мс.
Котлоагрегат не имеет собственного несущего каркаса и подвешивается к металлоконструкциям здания котельного цеха.
Главными элементами металлоконструкций воспринимающими нагрузки массы котлоагрегата и передающими их на колоны здания являются хребтовые балки расположенные перпендикулярно фронту котла с шагом 12 м. Пароводяной тракт СКД выполнен двухпоточным с самостоятельным регулированием питания и температуры по каждому потоку. Среда последовательно проходит последующим поверхностям нагрева: водяной экономайзер подвесные трубы КПП НД первый ход НРЧ второй ход НРЧ СРЧ ВРЧ потолочный пароперегреватель экраны поворотной камеры конвективной шахты. Далее среда двумя потоками проходит ширмовый пароперегреватель конвективный пароперегреватель первой и второй ступени. Пар из ЦВД турбины поступает в перегревательный тракт низкого давления который выполнен двухпоточным с самостоятельным регулированием температуры пара каждого потока. Конвективный пароперегреватель выполнен двухступенчатым. Топочная камера потолок горизонтальный и опускной газоходы полностью экранированы унифицированными цельносваренными газоплотными панелями сваренными из плавниковых труб диаметром 32 мм с толщиной стенки 6 мм (сталь 12Х1МФ) с шагом 46 мм.
Ширмовой пароперегреватель состоит из одного ряда ширм расположенных вертикально. Расстояние между ширмами 644 мм. Каждая ширма состоит из двух камер (входной и выходной) диаметром 159 х 28 мм и 47 параллельно включенных U-образных труб диаметром 32 х 6 мм (сталь 12Х1МФ). Шаг между трубами 35 мм.
Конвективный пароперегреватель состоит из двух частей – выходной и входной. Входная часть состоит из однопетлевых пакетов 12 входных камер диаметром 273 х 40 мм (сталь 12Х1МФ) и 4 выходных камер диаметром
5 х 65 мм (сталь 12ХШФ).
Каждые 74 пакета и четвертая камера (три входные и одна выходная) составляют самостоятельный блок – контур. Таких блоков по ширме газохода четыре. Змеевики из труб диаметром 42 х 7 мм (сталь 12Х1МФ) устанавливаются в них с продольным шагом 65 мм и шагом по ширине газохода
Выходная часть конвективного пароперегревателя по ширине газохода состоит из четырёх блоков в которых имеются 222 двухпетлевых пакета змеевиков 8 входных и 24 выходных камеры диаметром 465 х 65 мм (сталь 12Х1МФ) и диаметром 273 х 63 мм (сталь 12Х1МФ) соответственно.
Каждый пакет состоит из пяти параллельно включенных змеевиков диаметром 42 х 7 мм (сталь 12Х18Н12Т в обогреваемой зоне) установленных с шагом 65 мм. В горизонтальном газоходе расположена выходная ступень пароперегревателя низкого давления. Выходная ступень каждого из четырёх потоков состоит из одной входной камеры диаметром 650 х 30 мм (сталь 12Х1МФ) и одной выходной камеры диаметром 420 х 40 мм (сталь 12Х1МФ ). В двух крайних потоках имеется 112 однопетлевых шестизаходных змеевиков из труб диаметром 60 х 5 мм (всего 672 змеевика) а в средних потоках – 110 однопетлевых шестизаходных змеевиков (всего 660 змеевиков). Змеевики в обогреваемой зоне выполнены из аустенитной стали 12Х18Н12Т вне обогреваемой зоны из стали 12Х1МФ. Диаметр труб 60 х 5 мм. С целью уплотнения потолка в случае возможных повреждений под ним смонтирован "тепловой ящик шатёр".
В опускном газоходе все поверхности нагрева располагаются последовательно: промежуточная и входная ступени пароперегревателя низкого давления и водяной экономайзер.
Все поверхности нагрева КПП НД включены последовательно (по пару) для удобства перебросов пара с одной стороны на другую.
Входящая ступень каждого из шести потоков состоит из одной входной камеры диаметром 465 х 20 мм (сталь 12Х1МФ) и одной выходной камеры диаметром 465 х 30 мм (сталь 12Х1МФ). По высоте КШ входная ступень состоит из двух пакетов с разъёмом между ними 1140 мм.
Промежуточная ступень каждого потока состоит из одной входной и двух выходных камеры диаметром 465 х 30 мм (сталь 12Х1МФ) и 112 трехходовых и четырех заходных змеевиков диаметром 50 х 4 мм (сталь 12Х1МФ) расположенных параллельно фронту в коридорном порядке с шагом 90 мм.
Водяной экономайзер состоит из 12 входных и 12 выходных камер диаметром 273 х 40 мм (сталь 12Х1МФ) и 756 четырехзаходных змеевиков диаметром 32 х 6 мм (сталь 20). Водяной экономайзер выполнен шести поточным и десяти ходовым и по высоте состоит из двух пакетов с разъёмом между ними 1540 мм. Весь водяной экономайзер подвешен на подвесных трубах выходящих из верхних камер. Из каждого выходного коллектора выходит 108 труб диаметром 36 х 6 мм (сталь 12Х1МФ) с шагом 90 мм.
Регулирование температуры перегрева первичного пара осуществляется поддержанием соотношения топливо – вода а также впрыском питательной воды перед ширмами и второй ступенью конвективного пароперегревателя. Регулирование температуры перегретого (вторичного) пара осуществляется изменением расхода рециркулируемых газов и впрыском.
С целью понижения максимального уровня тепловых потоков в зоне максимального тепловыделения и снижения опасности возникновения высокотемпературной коррозии экранов выполнен ввод рециркуляции дымовых газов вниз топочной камеры. Газы на рециркуляцию отбираются за водяным экономайзером и вводятся в топку по наружному каналу горелок. Доля дымовых газов отбираемых на рециркуляцию составляет 15 % (r = 015). Кроме всех перечисленных значений рециркуляции она понижает образование вредных окислов азота при горении топлива. А это имеет немаловажное значение.
Первоначально с целью выравнивания тепловых потоков по ширине газохода предусматривалась рециркуляция дымовых газов вверх топки. Но в настоящее время этим вводом рециркуляции не пользуются ввиду его малой эффективности. Ввод газов вверх топочной камеры должны были осуществлять 2 дымососа рециркуляции газов вверх топки (ДРГВ). Но так как этой рециркуляцией не пользуются то эти дымососы работают в помощь основным дымососам котла и получили новую аббревиатуру – ДРН – дымососы расчетной нагрузки. Это важно тем что с переводом котла на работу с уравновешенной тягой мощности основных дымососов стало не хватать для работы котлоагрегата с номинальной нагрузкой. Поэтому использование ДРН-ов дает возможность котлу работать с максимальной мощностью практически при любых погодных условиях (в частности речь идет об атмосферном давлении).
Котлоагрегат ТГМП-1202 оборудован 56 комбинированными газомазутными горелками. Производительность каждой горелки по мазуту составляет 514 тч а по газу – 545·103 м3ч. Горелки размещены в общих распределительных коробах на фронтовой и задней стенах топки в 3 яруса по высоте. Все 56 горелок вихревые.
Очистка поверхностей нагрева в поворотном газоходе осуществляется обдувкой.
Для очистки поверхностей конвективной шахты (КПП НД и ВЭ) применяется три контура дробеструйной установки с пневмозабором дроби.
Цельносварные экраны изолируются изоляцией = 160 мм и зашиваются сверху металлическими листами.
К–1200–240 ЛМЗ – паровая конденсационная турбина без регулированных отборов пара с промперегревом номинальной мощностью
00 МВт и частотой вращения 3000 обмин предназначена для непосредственного привода генератора переменного тока типа ТВВ–1200–2 ЛЭО «Электросила» выходным напряжением 24 кВ. Турбина устанавливается для работы в блоке с прямоточным однокорпусным газомазутным котлоагрегатом ТГМП–1202 ТКЗ паропроизводительностью 3950 тч.
Турбина рассчитана для работы при следующих основных параметрах:
-номинальная мощность:
-абсолютное давление свежего пара:
-температура свежего пара:
-абсолютное давление холодного промперегрева при номинальной нагрузке:
-температура холодного промперегрева:
-абсолютное давление горячего промперегрева при номинальной нагрузке:
-температура горячего промперегрева:
-номинальный расход свежего пара:
-расчетное абсолютное давление пара в конденсаторе:
-расчетная температура охлаждающей воды:
-номинальный расход охлаждающей воды через конденсатор:
Турбина допускает длительную работу при следующих параметрах:
-максимальный расход пара на турбину:
-максимальная мощность при максимальном расходе свежего пара номинальных его параметрах и отключенных ПВД:
-максимальное давление свежего пара:
-максимальная температура свежего пара:
-абсолютное давление ХПП при расходе пара на турбину 3950 тч:
-абсолютное давление ГПП при расходе пара на турбину 3950 тч:
-максимальная температура ГПП:
-максимальная температура охлаждающей воды:
Турбина имеет 9 нерегулируемых отборов для регенеративного подогрева питательной воды до 274 °С при номинальной мощности.
Кроме регенеративных отборов предусматриваются отборы пара к следующим потребителям:
-на калориферы котлоагрегата;
-на мазутное хозяйство и общестанционные нужды;
-на подогреватели сетевой воды для покрытия теплофикационной нагрузки в количестве 40 Гкалч.
Турбина представляет собой одновальный пятицилиндровый агрегат состоящий из одного ЦВД одного ЦСД трех ЦНД и имеющий 6 выхлопов пара на 2 продольно расположенных конденсатора. Общая длина турбины без генератора составляет 479 м а с генератором – 71.8 м. Общий вес турбины без конденсатора и трубопроводов составляет около 1900 т.
Свежий пар из котла четырьмя паропроводами диаметром 377x60 мм подводится к двум блокам клапанов высокого давления расположенных по обе стороны ТВД. Каждый блок клапанов представляет собой паровую коробку стопорного клапана сблокированную посредством коротких патрубков с двумя паровыми коробками регулирующих клапанов ЦВД. От регулирующих клапанов пар по четырем перепускным трубам диаметром 377x60 мм подводится в среднюю часть ЦВД. Ввод пара в ЦВД осуществляется двумя патрубками внутренним диаметром 380 мм.
Парораспределение турбины дроссельное: все 4 регулирующих клапана ЦВД открываются одновременно и на одинаковую высоту.
ЦВД турбины 2-х корпусный с петлеобразной схемой движения пара и включает 8 ступеней давления четыре из которых расположены во внутреннем корпусе образуя левый поток пара а последующие четыре – в наружном корпусе образуя правый поток. Переток пара из левого в правый поток осуществляется по межкорпусному зазору.
Рис. 2. Схема движения пара в ЦВД.
Вторично перегретый пар по 4-м паропроводам диаметром 720 x 25 мм подводится к двум стопорным клапанам ЦСД а от них четырьмя перепускными трубами к 4-ем регулирующим клапанам ЦСД расположенным непосредственно на ЦСД: два сверху и два по бокам цилиндра. Из выхлопных патрубков ЦСД пар по двум ресиверным трубам расположенным по обеим сторонам турбины перепускается в ЦНД. Все ЦНД конструктивно выполнены одинаково: двухкорпусные двухпоточные и имеют по пять степеней в каждом потоке.
Роторы ЦВД и ЦСД цельнокованые; а роторы ЦНД ковано-сварные с высотой рабочих лопаток последних ступеней 1200 мм.
Генератор завода " Электросила" ТВВ–1200–3 номинальная мощность
N = 1200 МВт напряжение U = 24 кВ.
Главный корпус энергоблока 1200 МВт – пятипролётное здание. Машинный зал имеет два пролёта 30 и 54 метра деаэраторная этажерка (пролет) –
метров котельное отделение – 45 метров помещение турбо- воздуходувок – 15 метров.
Каркас главного корпуса запроектирован в металлических конструкциях что обусловлено большими нагрузками на колонны котельного отделения от подвесного котла который опирается на хребтовые балки с шагом 6 м.
Стеновые ограждения комбинированные с применением армированных железобетонных панелей и панелей из стального профилированного листа с синтетическим уплотнением. Междуэтажные перекрытия выполнены сборными жб оконные проёмы из световых панелей в металлических переплётах и стеклопрофилита. В бесподвальном котельном отделение расположен 1 котёл ТГМП–1202 однокорпусного исполнения.
Для проведения ремонтных работ котельное отделение оборудовано двумя мостовыми кранами. Также имеется грузоподъёмные лифты грузоподъёмностью 1000 кг. Дымососы и регенеративные воздухоподогреватели расположены на открытой площадке за главным корпусом.
Для увеличения площади рассеивания и уменьшения концентрации вредных выбросов дымовых газов на два блока третьей очереди установлена одноствольная дымовая труба высотой 324 метра.
В машинном зале в поперечном направлении расположен один турбоагрегат К–1200–240–3 Ленинградского металлического завода с генератором ТВВ–1200–3 объединения "Энергосила".
В конденсационном отделении машинного зала под отметкой 03 расположены циркуляционные водоводы трубопроводы технического снабжения насосы и трубопроводы конденсатных установок распределительные узлы пенно-тушения со щитами управления.
Выше отметки 06 расположена питательная установка – подогреватели высокого и низкого давлений системы маслоснабжения турбоагрегатов бойлерная установка и другое вспомогательное оборудование.
Машинное отделение оборудовано четырьмя мостовыми кранами грузоподъемностью 12520 тс.
В осях деаэраторной этажерки расположены деаэраторы питательные трубопроводы паропроводы острого пара и промперегрева с импульсно-предохранительными устройствами вспомогательные трубопроводы тепловой схемы блока.
На отметке 122 этажерки расположены воздуховоды и кондиционеры блочного щита управления (БЩУ) вспомогательные помещения эксплуатационного и ремонтного персонала блока.
На отметке 156 расположен БЩУ. На отметке 00 этажерки размещена блочная обессоливающая установка (БОУ). Аэрация главного корпуса выполнена приточно-вытяжной. Приток свежего воздуха осуществляется в зависимости от температуры наружного воздуха.
ОПИСАНИЕ ВСПОМОГАТЕЛЬНОГО ОБОРУДОВАНИЯ
1.Конденсационная установка
Конденсационная установка блока 1200 МВт состоит из конденсационной группы типа 1200 КЦС-1 трех основных водоструйных эжекторов типа
ЭВ-7-1000 двух водоструйных эжекторов типа ЭВ-1-230 и двух ПНЭ типа
Техническая характеристика конденсатора:
-расход пара в конденсатор:
-гидравлическое сопротивление конденсатора:
-кратность охлаждения:
-поверхность охлаждения:
-диаметр охлаждающих трубок:
-длина охлаждающих трубок:
Конденсатор оборудован паро- и водоприемными устройствами
предназначенными для приема:
-постоянного добавка обессоленной воды:
-аварийного добавка обессоленной воды:
2.Конденсаторные насосы
В тепловой схеме блока 1200 МВт предусмотрена установка двух групп КЭН: первая группа состоит из трех насосов типа КСВ-1600-90 и предназначены для откачки конденсата из конденсатора главной турбины и подаче его через БОУ на всас насосов 2-ой ступени. Вторая группа включает 3 насоса типа
КС-1600-220 и предназначены для подачи основного конденсата через систему регенерации низкого давления в деаэратор (Д-7 ата).
Техническая характеристика насосов КСВ-1600-90:
-производительность:
-температура перекачиваемой жидкости:
Техническая характеристика насосов КС-1600-220:
-производительность:
3.Система регенерации турбины
Регенеративный подогрев питательной воды осуществляется в пяти ПНД и в двух параллельно включенных группах подогревателей ВД каждая из которых состоит из трех последовательно включенных ПВД.
По конструктивному исполнению все ПНД близки к друг другу и имеют типовое обозначение ПН-2300-29-7-1; 11; Ш; 1У; У где римскими цифрами указываются модификации аппарата по диаметру парового присоединительного патрубка.
Все ПНД вертикальные однокорпусные четырехходовые выполнены из нержавеющей стали.
Все ПВД конструктивно выполнены одинаково имеют типовое обозначение ПВ-2500-320-17; 37; 61 и отличаются только толщиной стенки корпуса по паровой стороне.
Все ПВД поверхностного типа вертикальные однокорпусные с трубной системой выполнены из однорядных круглых спиральных бифилярных (двухтрубных) змеевиков расположенных в шести вертикальных колоннах. Каждый ПВД оборудован встроенным пароохладителем и охладителем дренажа греющего пара. Причем ПВД-7 кроме встроенного ПО имеет вынесенный пароохладитель. Через него пропускается часть питательной воды после ПВД-9.
4.Питательная установка блока
Питательная установка включает в себя три турбонасосных агрегата предназначенных для работы в качестве питательных насосов блока и состоящих из питательного насоса типа ПН-1500-350 приводной конденсационной турбины ОК-18ПУ с редуктором Р-1А и навесного бустерного насоса типа ПД-1600-180-1 (в схеме три).
Унифицированная приводная турбина ОК-18-ПУ одноцилиндровая конденсационная рассчитана на работу с переменным числом оборотов при переменных начальных параметрах пара поступающего из III-го отбора главной турбины.
Основные технические данные турбины ОК-18ПУ:
-номинальная частота вращения:
-регулируемый диапазон оборотов:
-номинальный расход пара:
-абсолютное давление пара в конденсаторе:
-температура охлаждающей воды:
Питательный насос ПН-1500-350 – горизонтальный центробежного типа имеет 7 рабочих ступеней давления предназначен для работы с переменным числом оборотов.
Техническая характеристика насоса:
-давление в напорном патрубке:
-номинальное число оборотов:
-температура перекачиваемой воды:
Бустерный насос ПД-1600-180 центробежный горизонтальный спирального типа одноступенчатый навесной с приводом от турбины ОК-18ПУ через понижающий редуктор Р-1 А.
Техническая характеристика БН:
-давление на напоре:
5.Турбоприводы воздуходувок
Подача воздуха в топку котла производится тремя воздуходувками. Каждый агрегат состоит из приводной турбины ОК-18-ГТВ-1200КТЗ и высоконапорного дутьевого вентилятора ВДН-36х2.
Привод вентиляторов осуществляется через понижающий редуктор.
Основные технические данные турбины ОК-18ПВ:
Приводная турбина ОК-18ПВ-1200 - одноцилиндровая конденсационная с восемью ступенями давления рассчитана на работу с переменным числом оборотов при переменных начальных параметрах пара поступающего из IV-oгo отбора главной турбины:
-диапазон рабочей частоты вращения:
-расход охлаждающей воды:
6.Особенности тепловой схемы турбины К-1200-240
Как уже говорилось в описании турбины она имеет 9 нерегулируемых отборов пара на регенерацию. Первый отбор выполнен из ЦВД турбины и идет на ПВД-9. Отбор на ПВД-8 выполнен из нитки холодного промперегрева. ПВД-7 и деаэраторы питаются паром соответственно из третьего и четвертого отборов которые питаются паром из цилиндра среднего давления турбоагрегата. Из этого же цилиндра выполнен пятый отбор на ПВД-5. Остальные четыре отбора идущие на ПНД-1234 питаются паром от цилиндров низкого давления турбины.
Характерной особенностью тепловой схемы является использование в ней деаэраторов скользящего давления. Эта особенность привела к увеличению экономичности работы агрегата. В частности отпала необходимость переключения деаэраторов на отбор более высокого давления при уменьшении нагрузки на турбину. Скольжение по давлению в деаэраторе происходит в пределах 015 ÷ 1 МПа.
Пар сконденсировавшийся в конденсаторе главной турбины попадает в два конденсатосборника (точнее будет сказать что конденсат отработавшего в турбине пара попадает в конденсатосборники). Из конденсатосборников основной конденсат насосами обессоливающей установки (НОУ) последовательно прокачивается через ОГК сальниковый подогреватель (ПС-340) блочную обессоливающую установку (БОУ) и поступает на всас насосов КЭН 2-ой ступени. Эти насосы прокачивают основной конденсат через систему регенерации низкого давления после которой он поступает в два параллельно включенных деаэратора (Д-7). Подогреватель низкого давления № 34 и 5 как и ПВД оборудованы встроенными охладителями пара и охладителями дренажа греющей среды.
После деаэраторов питательная вода проходит через питательную установку блока и систему регенерации высокого давления. В данной системе регенерации питательная вода нагревается до расчетной температуры (274 °С) и затем поступает в котлоагрегат. Пар из парогенератора с параметрами
Р = 255 кгссм² и t = 545 °С поступает к ЦВД турбоагрегата.
Для осуществления рециркуляции дымовых газов вниз топочной камеры применены дымососы рециркуляции типа ГД-26*2.
-максимально допустимая температура газов:
-мощность электродвигателя:
Эти машины центробежного типа.
Для подогрева воздуха поступающего к горелочным устройствам котлоагрегат оборудован тремя регенеративными воздухоподогревателями
РВП-145. Они представляют собой противоточные теплообменные аппараты использующие для подогрева воздуха тепло уходящих дымовых газов. Регенеративный воздухоподогреватель состоит из вращающегося цилиндрического ротора внутренним диаметром 388 м который радиальными перегородками разделен на 24 сектора. Этот ротор заключен в неподвижный цилиндрический корпус. По высоте теплообменная набивка состоит из двух слоев: горячего высотой 14 м и холодного высотой 045 м. Набивка представляет собой металлические листы специального профиля. Ротор РВП ступицей соединен с валом и имеет номинальную частоту вращения птм = 15 обмин.
РВП также снабжен системой уплотнительных устройств с перемещающимися радиальными плитами и аксиальными уплотнениями. Пред тем как холодный воздух попадает в регенеративные подогреватели он проходит через калориферы котла. Энергетические калориферы предназначены для подогрева воздуха перед РВП до 90°С что предотвращает низкотемпературную коррозию холодных пакетов РВП. Подогрев воздуха осуществляется паром V-гo отбора основной турбины а также через РУ-1324 от коллекторов собственных нужд.
Конденсат калориферов отводится насосами КО-125-5 через расширительный бак охладители конденсата и гидрозатвор в конденсатор главной турбины. При отмывке системы схема собирается на циркводовод.
Насосы конденсата калориферов (НКК) центробежные трехступенчатые горизонтальные спирального типа с 2-х сторонним подводом жидкости к рабочему колесу 1-ой ступени и односторонним подводом к рабочим колесам последующих ступеней.
8.Характеристика НКК
-допустимый кавитационный запас:
Секции калориферов набраны из отдельных блоков СО-170 (всего в схеме 3 секции калориферов).
9.Характеристика секции калориферов
-поверхность нагрева секции:
-поверхность нагрева первого блока:
Для удаления дымовых газов из топочной камеры котла и подачи из хвоста парогенератора в дымовую трубу котлоагрегат оборудован тремя дымососами типа ДОД-43ГМ.
10.Характеристика дымососов
-потребляемая мощность:
Способ регулирования направляющий производительности аппарат.
Для очистки поверхностей нагрева конвективной шахты от залоговых отложений на котле применяется дробеструйная установка с пневмозабросом дроби. Очистка производится свободно падающей дробью диаметром 3 – 4 мм.
Очистка пароперегревателя в горизонтальном газоходе осуществляется глубоко выпадающимися в горизонтальный газоход аппаратами паровой обдувки.
Котел ТГМП-1202 в полном объеме оборудован контрольно-измерительными приборами автоматикой технологическими и тепловыми защитами.
11.Высоконапорный дутьевой вентилятор ВДН-36*2
Характеристика ВДН 36*2:
Это центробежная машина стороннего всасывания левого вращения с углом разворота нагнетательного патрубка 0° и всасывающих патрубков -165°. Приводится в движение через понижающий редуктор Р-7А с передаточным числом 51.
-расчетная температура воздуха:
-расчетная скорость вращения:
-максимально допустимая температура воздуха:
-максимально допустимая скорость вращения:
-минимально допустимая скорость вращения:
-диаметр рабочего колеса:
РАСЧЕТ ТЕПЛОВОЙ СХЕМЫ ТУРБИНЫ К-1200-240 И ВЫБОР ВСПОМОГАТЕЛЬНОГО ОБОРУДОВАНИЯ БЛОКА 1200 МВт
1.Расчет расхода пара на ПВД
Требуется определить величину расхода пара на ПВД в долях от расхода пара на главную турбину т. е. dh = DhD где Dh – расход пара на h-ый подогреватель; D – расход пара на главную турбину.
Расчет начинается с определения количества питательной воды проходящей через ПВД.
Применяем упрощенный метод расчета потерь пара и конденсата в цикле протечек через концевые уплотнения и уплотнения штоков и расходы пара на эжекторную установку.
Считаем что все утечки сосредоточены в точке с наиболее высоким потенциалом - на паропроводе от котла к турбине.
В соответствии принимаем утечки цикла:
Dут = 1% т. е. Dyт = 001 · D.
Тогда расход пара на концевые уплотнения:
Dк.у. = 05% т. е. Dк.у. = 0005 · D.
Расход пара на эжекторную установку:
Dэж = 03% т. е. Dэж = 0003 · D.
Так как в схеме установлен прямоточный котел то расход пара из котла соответствует расходу питательной воды:
Dп.в. = Dк.a. = D + Dут + Dк.у. + Dэж = (1 + 001 + 0005 + 0003) · D.
Dп.в. = 1018 · D; αп.в. = Dп.вD = 1018.
Количество добавочной воды подаваемой в цикл на компенсацию утечек для схемы блока составляет:
αд.в = αут = 001 (т.е. 1%).
2.Питательная установка блока
Питательная установка блока состоит из трех бустерных и трех питательных насосов. В качестве привода питательных насосов используется конденсационная приводная турбина ОК-18-ПУ а бустерные насосы приводятся в движение понижающим редуктором от вала основного питательного насоса.
Давление воды на всасе бустерного насоса:
Рбнвс = Рд + (Нд – Нм.а.)10 – ΔРс
Рд = 06867 МПа (7 ата) – рабочее давление среды в деаэраторе;
Нд = 342 м – высота установки деаэратора;
Нм.а. = 95 м – высота установки питательного агрегата;
ΔРс = 000981 МПа – сопротивление трубопроводов от деаэратора до насосов;
м.вод.ст. = 1 ата = 00981 МПа;
Рбнвс = 06867 + (342 – 95)10 · 00981 – 000981 = 09192 МПа;
Параметры воды в деаэраторе при принятом давлении в нем
t д = 16418 °C; h' = 69368 кДжкг; v' = 110707·10-3 м3кг.
При давлении на нагнетании бустерных насосов:
Pбн н = (09192 + 21157)2 = 1517 МПа
и средней температуре воды: vcp = 11077 · 10-3 м3кг (это средний объем перекачиваемой воды в бустерных насосах). Тогда повышение энтальпии воды в бустерных насосах составит:
Δhбн = [(Рбнн – Pбнвс) · vcp ·103](бн · ред) = [(21157 – 09192)· 11077 · 10-3 · 103](08 · 0975) = 1699 кДжкг
где бн = 08 – КПД бустерного насоса;
ред = 0975 – КПД редуктора.
Принимаем давление воды на напоре питательного насоса:
Рпнн = 3237 МПа и пн = 083 при среднем давлении питательной воды:
Рпвср = (3237 + 21157)2 = 1724 МПа
и средней температуре воды tпнcp = 1683 °С; определяем средний удельный объем перекачиваемой воды:
vпнср = 10985·10-3 м3кг.
Тогда повышение энтальпии в питательном насосе:
Δhпн = [(Рпнн – Рпнвс) · vпнcp · 103]пн = [(3237 – 21157) · 10945 · 10- 3
· 103]083 = 4053 кДжкг.
Определим повышение энтальпии в питательной установке:
Δhпу = Δhпн + Δhбн = 4053+1699 = 4223 кДжкг.
Определяем долю расхода пара на турбоприводы питательных насосов:
αпн = (αп · Δhпу)[(hпн – hтпк) · пн] = (108 · 4243)[(33604 – 25062) · 083] =
3.Параметры пара и воды на ПВД
Составим расчетную схему ПВД и определим все необходимые для расчета параметры:
ΔР9 = 4 %; Р9' = Р0 · (1 – ΔР9100) = 595 МПа; h9 = 30507 кДжкг.
Аналогично для ПВД-8 и 7:
ΔР8 = 45 %; Р8' = 372 МПа; h8 = 29516 кДжкг;
ΔР7 = 5 %; Р7' = 171 МПа; h7 = 33604 кДжкг;
По значениям параметров Ph' и Hh по таблице термодинамических свойств воды и водяного пара определяем параметры пара на входе в пароохладители ПВД и заносим их в таблицу.
Принимаем потери давления в пароохладителях ΔPпо h и величину пароохлаждения пара до температуры насыщения Δt = 10 °C.
ΔРпо9 = 15 %; Р9'' = Р9' · (1 – ΔРпо9100) = 595 · (1 – 15100) = 586 МПа;
tH9 = f(P9") = 274 °C;
t9" = tH9 + Δt = 274 + 10 = 284 °С;
ΔРпо8 = 2 %; Р8" = Р8' · (1 – ΔРпо8100) = 365 МПа;
tH8 = f(P8") = 24496 °C;
t8" = tH8 + Δt = 24496 + 10 = 25496 °С
По значению Ph" и th" определяем параметры пара на входе в собственно подогреватель ПВД (в частности энтальпию hс.п.) и значения заносим в таблицу.
Примем потерю давления за вынесенным пароохладителем:
Р'7(за вын. п.о.) = Р'7 · (1 – 07100) = 1698 МПа;
Оцениваем температуру пара за выносным ПО:
t"7(за вын .п о) = 3314 °С; из учета температурного напора на холодном конце вынесенного ПО равным 50 – 55 °С на схему наносим все остальные параметры за вынесенным пароохладителем:
H (за вын .п о) = 3099 кДжкг
4.Параметры питательной воды
Принимаем гидравлическое сопротивление ПВД ΔР2 = 05 МПа и недогрев воды выходящей из собственно подогревателя ПВД; t = 5 °C. Зная давление развиваемое питательным насосом число ПВД (m) и tнас в собственно подогревателе определим параметры питательной воды за собственно подогревателем:
ПВД-9: Рв9 = РпH – m · ΔР2 = 3237 – 3 · 05 = 3087 МПа;
tв9 = tн9 – t = 274 – 5 = 269 °C;
ПВД-8: Рв8 = РпH – (m – 1) · ΔР2 = 3237 – 2 · 05 = 3137 МПа;
tв8 = tH8 – t = 2449 – 5 = 2399 °C;
ПВД-7: Рв7 = Рпн – (m – 2) · ΔР2 = 3237 – 1 · 05 = 3187 МПа;
tв7 = tH7 – t = 2037 – 5 = 1987 °С;
По значению PBh и tBh определяем остальные параметры за собственно подогревателем и заносим их в таблицу.
Рис. 3. Расчетная схема ПВД.
5.Параметры конденсата греющего пара
Принимаем что конденсат греющего пара сливаемого из ПВД-7 горячее чем вода после питательных насосов на Δt = 3 °C.
Тогда: Р"к7 = 168 МПа; t k7 = tпн + 3 = 1695 + 3 = 1725 °С.
Принимаем что разность температур между температурой конденсата сливаемого из вышестоящего ПВД и температурой воды за собственно подогревателем нижестоящего ПВД равно 8 °С.
ПВД-8: Р"к8 = 365 МПа; tк8 = tв7 + 8 = 1987 + 8 = 2067 °С;
ПВД-9: Р"к9 = 586 МПа; t k9 = t b8 + 8 = 2399 + 8 = 2479 °C
По значениям P"кh и tкh определим остальные параметры конденсата и занесем их в таблицу.
6.Определение расходов пара на ПВД
На основании определенных параметров пара и конденсата составляем уравнения тепловых балансов для трех участков схемы с ПВД:
)α9 · (h'9 – hk9) + α 8 · (h8 – h'8) = α пв · к9 · (hв9 – hв8);
)α 9 · (hk9 – hk9) + α 8·(h8 – hk8) + α 7·(h'7за вын по – h”7) = αпв·к8·(hB8 – hB7);
)α 9 · (h'k8 – hk7) + α 8·(h8 – hk7) + α 7 · (h"7 – hk7) = α пв · к7 · (hв7 – hпB);
где кh – коэффициент рассеивания тепла в окружающую среду: к9=1008; к8=1007; к7=1006.
Подставим найденные значения энтальпий в уравнения тепловых балансов:
)α 9·(2839–10755)+α 8·(29516–28412)=1018·1008·(11772–10426);
)α9·(10755–8833)+α8·(28412–8833)+α7·(28234–7301)=1018·1007· ·(10426 – 8604);
)α9·(8833–7301)+α8·(8833–7301)+α7·(28234-7301)=1018·1006·(8604 – – 7159).
Решив данную систему уравнений получим: α9 = 007265; α8 =008146;
7.Определение параметров воды за ПВД и величины погрешности
Начальное давление – Р0 = 235 МПа; начальная температура –
t0 = 540 °C; число ПВД в тепловой схеме – 3; расходы пара на ПВД и турбопривод:
Повышение энтальпии воды в насосах в кДжкг: питательный насос – 40517; бустерный насос – 156574.
Расход питательной воды через ПВД в долях αпв = 1018 (питательный насос приводится турбиной бустерный – через редуктор).
Параметры пара воды и конденсата в рассматриваемой точке ПВД:
Пар в камере отбора турбины
Пар перед пароохладителем
Пар за ПО перед собств. подогрев-лем
Конденсат выходящий из ПВД
Недогрев воды из ПВД
Недоохлаждение паpa за ПО
Потери давления в пароохладителе
Потери давления воды в ПВД
Принятое недоохл. конденсата в ПВД
Питательная вода на выходе из ПВД
Питательная вода за собст. подогрев-лем
Пар перед вынесенным ПО
Пар за вынесенным ПО перед встроенным ПО
Потери давления в вынесенном ПО
Питательная вода на вынесенном ПО
Вода прошедшая через вынесенный ПО
Питательная вода на входе в котел
Питательная установка:
Вода на всасе бустерного насоса
Вода на напоре бустерного насоса
Вода на напоре питательного насоса
Пар в отборе на турбопривод
Потери в трубопроводе к ТПН
Пар перед стопорным клапаном ТПН
Потери в стопорном клапане ТПН
Пар перед первой ступенью ТПН
Параметры на линии Х=1
Пар за последней ступенью ТПН
Выходные потери турбопривода
Зная расходы пара на каждый ПВД из уравнения теплового баланса для пароохладителя может быть найдена величина энтальпии воды за ПВД.
α9 · (h9 – h'9) = αпв · (hпв – hв9);
hпв = hв9 + [α 9 · (h9 – h'9)α пв];
hпв = 117735 + [007265 · (30507 – 2839)1018] = 1192 кДжкг.
По Рпв = 299 МПа и hпв = 1192 кДжкг определяем все остальные параметры питательной воды (в частности ее температуру tпв)
α8 · (h8 – h'8) = αпв · (h'в8 – hв8);
h'в8 = 10428 + [008146 · (295158 – 284122)1018] = 1051 кДжкг.
По Рв8 = 3137 МПа и hв8 = 1051 кДжкг определим все остальные параметры воды.
α7 · (h'7(за вын. по) – h"7) = αпв · (h'в7 – hв7);
h'в7 = 860 + [0050037 · (307555 – 282333)1018] = 8722 кДжкг.
По Рв7 = 3187 МПа и hв7 = 8722 кДжкг определим все остальные параметры воды за ПВД-7.
Зная все параметры воды и пара по каждому ПВД определяем расходы пара из уравнения теплового баланса в целом для каждого ПВД и находим погрешность расчета.
α9 · (h9 – h'9) = αпв · (hпв – hв9) · к9;
α9 = αпв · [(hпв – h'в8)(h9 – hк9)] · к9;
α9 = 1018 · [(1102 – 1051)(30507 – 107535)] · 100 = –00727;
Погрешность: = (Δα 9α 9) · 100 = [(007265 + 00727)007265] · 100 =
α8 · (hк9 – hк8) + α8 · (h8 – hк8) = αпв · к8 · (h'в8 – h'в7);
α8 = [1018 · 1007 · (1051 – 8728) – 007265 · (107563 – 883287)](295158 – 83287) = 008156;
Погрешность: = (Δα8α8) · 100 = [(008146 – 008156)008146] · 100 =
= [–0048] % = 0048 %.
(α9 + α8) · (hк8 – hк7) + α7 · (h'7 – hк7) = αпв · к7 · (h'в8 – h'пн);
α7 = [1018 · 1.006 · (8728 – 7159) – (007265 + 008146) · (8833 – 730)](3099 – 30) = 005;
Погрешность: = (Δα7α7) · 100 = [(0050037 – 005)0050037] · 100 =
8.Определение параметров воды за выносным пароохладителем и параметров воды на входе в котел
Вода в паровой котел поступает после смешения двух потоков: основного потока питательной воды W1 и потока W2 после выносного пароохладителя ПВД-7. Причем α пв = W1 + W2 = 1012. Исходя из геометрических размеров трубопроводов к вынесенному пароохладителю и к ПВД-7 и исходя из одинаковой скорости воды в них решая уравнение неразрывности находим:
Wвынпo = W2 = 79 % от αпв;
Решая уравнение теплового баланса для вынесенного пароохладителя определяем энтальпию воды за вынесенным ПО:
α7 · (h7 – h'7 (за вын. по)) = 0079 · αпв · (h"в – hпв);
h"в = [0050037 · (33604 – 3099)(0079 · 1018)] + 1192 = 13585 кДжкг.
Тогда tв за вынесенным ПО равна 305 °С.
Решая уравнение теплового баланса для точки смешения потоков находим параметры воды на входе в котел (истинные параметры питательной воды). Обозначим их с индексом «кв» – котловая вода.
W1 · hпв + W2 · h"B = αпв · hкв;
W1 = αпв – W2 = αпв · (1 – 0079);
hкв = [αпв · (1 – 0079) · hпв + 0079 · h"в · αпв]αпв = hпв + 0079 · (h"в – hпв) =
= 1192 + 0079 · (13585 – 1192) = 12052 кДжкг.
9.Определение параметров пара и воды в ПНД
Принимаем давление питательной воды за ПНД-5:
Рпв = 1 МПа; ΔРоп = 2 %; Δtоп = 10 °C; Δtок = 7 °С; t = 5 °С.
Сальниковый подогреватель.
При Рк = 00035 МПа tк = 2669 °C ctк = 11344 кДжкг.
Принимаем (Δtкэн + Δtcп + Δtэж) = 8 °С – увеличение температуры в КЭН-I КЭН-II сальниковом и эжекторном подогревателях. Заметим что в существующей тепловой схеме блока 1200 МВт эжекторного подогревателя нет.
При Рпв = 15 МПа и tсп = 2669 + 8 = 3469 °С ctсп = 1482 кДжкг.
Пусть Р'1 = 00184 МПа tк = 5829 °С;
По tпв: tв = tк – t = 5829 – 5 = 5329 °С;
По Рв = 14 МПа и tв = 5329 °С hв
Слив конденсата: по P'1 и tк hк1 = 2439 кДжкг.
При Р'2 = 00463 МПа tн = 7954 °С;
По tпв: tв2= 7954 – 5 = 7454 °С hв2 = 313 кДжкг (при Рпв = 13 МПа);
Слив конденсата: по Р'2 и tн hк2 = 3311 кДжкг.
Р"3 = 098 · 0112 = 01098 МПа t"3 = 1025 °C;
tоп-3 = t"3 + Δtоп = 1025 + 10 = 1125 °С;
По Р"3 и tоп-3 h'3= 27002 кДжкг.
Питательная вода после собственно подогревателя:
Рпв = 12 МПа; tв3 = t"3 – t = 1025 – 5 = 975 °С;
По Рпв и tв3 hB3 = 4085 кДжкг;
tк3 = tв2 + Δtок = 7454 + 7 = 8154°С;
По Р"3 и tк3 hк3 = 3415 кДжкг.
Р"4 = 098 · 0234 = 023 МПа t"4 = 12471 °C;
toп-4 = t"4 + Δtoп = 12471 + 10 = 13471 °С;
По Р"4 и toп-4 hв4 = 5032 кДжкг.
Рпв = 11 МПа t'4 = tв4 = t"4 – t = 12471 – 5 = 11971 °С;
По Рпв и tв4 h'4 = 5032 кДжкг.
tк4 = tв3 + Δtок + Δtoп-3 = 973 + 7 + 9 = 1133 °С;
По Р"4 и tк4 hк4 = 4458 кДжкг.
Р"5 = 098 · 0376 = 037 МПа t"5 = 14084 °C;
toп-5 = t"5 + Δtoп = 15084 °С;
По Р"5 и toп-5 hв5 = 275644 кДжкг.
Рпв = 1 МПа t'5 = tв5 = t"5 – t = 13584 °C;
По Рпв и tв5 hв5 = 57173 кДжкг.
tк5 = tв4 + Δtок + Δtоп-4 = 11071 + 7 + 11 = 12871 °C;
По P"5 и tк5 hк5 = 541 кДжкг.
Рис. 4. Расчетная схема ПНД.
10.Расчет деаэратора
Рис. 5. Расчетная схема деаэратора.
αпв = αд + α'пв + Σαпвд;
αпв · hд = αд · h' + α'пв · hпв (за пнд-5) + Σαпвд · hк7;
αд = αпв – α'пв – Σαпвд;
18 · 69368 = αд · 3170 + 1018 · 5803 – αд · 5803 – 020415 · 5803 +
897 · αд = 70616 – 59075 + 11862 – 14925;
αд = 1018 – 00327 – 020415 = 078.
11.Определение расходов пара на ПНД
На основании определенных параметров пара и конденсата составляем уравнения тепловых балансов для четырех участков схемы с ПНД.
α5 · (h'5 – hк5) + α4 · (h4 – h'4) = α'пв · (hпв – hв4) · к5;
α5 · (27564 – 541) + α4 · (2904 – 27346) = 078 · (57173 – 5032) · 1005;
α4 · (h'4 – hк4) + α5 · (hк5 – h'к4) + α3 · (h3 – h'3) = α'пв · (hв4 – hв3) · к4;
α4 · (27346 – 4458) + α5 · (541 – 4458) + α3 · (2775 – 27002) = 078 ·
· (5032 – 4085) · 1004;
α3 · (h'3 – hк3) + (α5 + α4) · (hк4 – h'к3) = [(α'пв – α5 – α4 – α3 – α2) · (hв3 – hв2) +
+ (α5 + α4 + α3 + α2) · (hв3 – hк2)] · к3;
α3 · (27002 – 3311) + (α5 + α4) · (4458 – 3311) = [(078 – α5 – α4 – α3 –
– α2) · (4085 – 313) + (α5 + α4 + α3 + α2) · (4085 – 3311 )] · 1003;
α2 · (h2 – hк2) + (α5 + α4 + α3) · (hк3 – hк2) = [(α'пв – α5 – α4 – α3 – α2) · (hв2 –
– hв1) + (α5 + α4 + α3 + α2) · (hв2 – hк1)] · к2;
α2 ·(2648 – 3311) + (α5 + α4 + α3) · (3415 – 3311) = (078 – α5 – α4 – α3 –
– α2) · (4085 – 313) + (α5 + α4 + α3 + α2) · (313 – 22415)] · 1.002;
Решая совместно систему уравнений находим расходы пара на ПНД в долях от расхода пара на главную турбину:
α5 = 002248; α4 = 003136; α3 = 00288; α2 = 002616.
12.Определение параметров воды за ПНД
Зная расход пара на каждый ПНД и уравнения теплового баланса для пароохладителей можно найти величину энтальпии за ПНД:
α5 · (h5 – h'5) = α'пв · (h5пнд – hв5);
h5пнд = hв5 + [α5 · (h5 – h'5)]α'пв = 57173 + [002248 · (3025 – 27564)]078 =
По параметрам Рпв = 1 МПа и h5пнд находим t5 = 1383 °С.
α4 · (h4 – h'4) = α'пв · (h4пнд – hв4);
h4пнд = hв4 + [α4 · (h4 – h'4)]α'пв = 5032 + [003136 · (2904 – 27346)]078 =
По параметрам Рпв = 11 МПа и h4пнд находим t4 = 1217 °С.
α3 · (h3 – h'3) = α'пв · (h3пнд – hв3);
h3пнд = hв3 + [α3 · (h3 – h'3)]α'пв = 4085 + [00288 · (2775 – 2700)]078 =
По параметрам Рпв = 12 МПа и h3пнд находим t3 = 982 °С.
В данном разделе ПНД-2 и ПНД-1 не рассматриваются т.к. они не имеют пароохладителей и параметры питательной воды за ними найдены в разделе «Определение параметров пара и воды в ПНД». В частности была определена температура и энтальпия питательной воды за ПНД-1 и ПНД-2 и за собственно подогревателями ПНД-345 Составим уравнение теплового баланса для ПНД-1:
α1 = [к1 · (α'пв – α5 – α4 – α3 – α 2) · (hв1 – hcп)](h1 – hк
α1 = [1001 · (078 – 002248 – 003136 – 00288 – 002616) · (2242 –
– 1482)](2525 – 2242) = 002352.
13.Определение в долях расхода пара в конденсатор
αVIII = α8 = 008146;
αVII = α7 + αпн = 0050037 + 005942 = 0109457;
αк = 1 – 042916 = 057084.
14.Определение расхода пара на турбоустановку по
Δhпп = h"пп – h'пп = 3540 – 2948 = 592 кДжкг;
hh9 = h0 – h9 = 3323 – 3050 = 273 кДжкг;
hh8 = h0 – h8 = 3323 – 29516 = 3714 кДжкг;
hh7 = h0 – h7 + Δhпп = 3323 – 3360 + 592 = 555 кДжкг;
hh6 = h0 – h6 + Δhпп = 3323 – 3170 + 592 = 745 кДжкг;
hh5 = h0 – h5 + Δhпп = 3323 – 3025 + 592 = 890 кДжкг;
hh4 = h0 – h4 + Δhпп = 3323 – 2904 + 592 = 1011 кДжкг;
hh3 = h0 – h3 + Δhпп = 3323 – 2775 + 592 = 1140 кДжкг;
hh2 = h0 – h2 + Δhпп = 3323 – 2648 + 592 = 1267 кДжкг;
hhк = h0 – hк + Δhпп = 3323 – 2335 + 592 = 1580 кДжкг.
Определяем Σαm · hhm:
αIX · hh9 = 007265 · 273 = 1987 кДжкг;
αVIII · hh8 = 008146 · 3714 = 3232 кДжкг;
αVII · hh7 = 0109457 · 55 = 608 кДжкг;
αVI · hh6 = 00327 · 745 = 2436 кДжкг;
αV · hh5 = 002248 · 890 = 200072 кДжкг;
αIV · hh4 = 003136 · 1011 = 347 кДжкг;
αIII · hh3 = 00288 · 1140 = 32832 кДжкг;
αII · hh2 = 002616 · 1267 = 3515 кДжкг;
αI · hh1 = 002352 · 1390 = 337 кДжкг;
Σαm · hhm = 27388 кДжкг.
αк · hhк = 057084 · 1580 = 91643 кДжкг.
Σαm · hhm + αк · hhк = 27388 + 91643 = 119031 кДжкг.
Расход свежего пара на турбину:
D = (1200 · 103)(119031 · 099 · 0994) = 1036 кгс = 37292 тс.
15.Определение количественных расходов пара и воды
ПВД-9: Д9 = α9 · Д = 007265 · 37292 = 27137 тч;
ПВД-8: Д8 = α 8 · Д = 008146 · 37292 = 30402 тч;
ПВД-7: Д7 = α7 · Д = 0050037 · 37292 = 1874 тч;
Д-7: Дд = αд · Д = 00327 · 37292 = 1869 тч;
Дпн: Дпн = αпн · Д = 005942 · 37292 = 2216 тч;
ПВД-5: Д5 = α5 · Д = 002248 · 37292 = 8383 тч;
ПВД-4: Д4 = α4 · Д = 003134 · 37292 = 11695 тч;
ПВД-3: Д3 = α3 · Д = 00288 · 37292 = 1074 тч;
ПВД-2: Д2 = α2 · Д = 002616 · 37292 = 9556 тч;
ПВД-1: Д1 = α1 · Д = 002352 · 37292 = 8771 тч;
Конденсатор: Дк = αк · Д = 057084 · 37292 = 2163 тч;
Утечки: Дут = 001 · 37292 = 37292 тч;
Уплотнения: Дупл = 0005 · 37292 = 1865 тч;
На эжекторы: Дэж = 0003 · 37292 = 1119 тч;
Расход питательной воды: Дпв = 1018 · 37292 = 379632 тч.
16.Определение мощности по отборам и сведение баланса
Nэ = (h0 – hотб)3600 · Дh · m · г;
NIX = 2025 МВт;NVIII = 3306 МВт;
NVII = 62 МВт;NVI = 248 МВт;
NV = 204 МВт;NIV = 354 МВт;
NIII = 335 МВт;NII = 3583 МВт;
NI = 3435 МВт;NK = 3342 МВт;
Невязка [] = [(1200 – 121012)1200] · 100 = 084 %.
17.Определение энергетических показателей
Полный расход тепла на турбоустановку:
Qтy = Д · (h0 + hпв) + Дпп · (h"пп – h'пп);
Дпп = αпп · Д = Д – ΣДЧВДh = 315379 тч;
Qтy = 37292 · (3323 – 1367) + 315379 – (3540 – 2948) = 91614 ГДжч.
Тепловая нагрузка парового котла:
Qпк = Дпв · (hпе – hпв) + Дпп · (h"пп – h'пп);
Qпк = 379632 · (3323 – 1367) + 315379 · (3540 – 2941) = 92926 ГДжч.
КПД транспорта тепла:
тр = QтyQпк = 9161492926 = 0986.
Количество теплоты топлива на паровой котел:
Qс = Qпкпк = 92926092 = 1010065 ГДжкг.
Эффективная мощность приводов питательных насосов:
Nпн = (Дпв · Нпа)(3600 · н) = [379632 · (103 · 11 · (3237 –
– 21))](3600 · 083) = 4230457 кВт.
Удельный расход теплоты турбоустановки на выработку электрической энергии:
Qэту = Qту(Nэ · Nптн) = (91614 · 106)(1200 · 103 + 4230457 · 103) =
КПД турбоустановки по выработке электрической энергии:
эту = 3600Qэту = 360073745 = 0488.
Абсолютный электрический КПД турбоустановки:
ату = (3600 · Nэ)Qтy = (3600 · 1200 · 103)(91644 · 106) = 0471.
КПД энергоблока нетто:
нс = (3600 · Nэ · (1 – 005))Qc = (3600 · 1200 · 103 · (1 – 005))(1010065 ·
КПД энергоблока брутто:
бс = (3600 · Nэ)Qc = (3600 · 1200 · 103) (1010065 · 106) = 0407.
Удельный расход условного топлива нетто:
Bну = 123нс = 1230396 = 31595 гкВт·ч.
Часовые расходы условного и натурального топлива:
Ву = QcQру = (1010065 · 106)29308 = 34464 · 103 кгч;
Вн = Qc Qрн = (1010065×106)36125 = 2796 · 103 кгч.
У собственно подогревателей
)* и 2)* – параметры непосредственно у подогревателей
** – непосредственно у деаэратора
18.Выбор оборудования блока
). Исходя из расхода пара на турбоустановку Д = 37292 тч выбираем паровой котел ТГМП-1202 паропроизводительностью 3950 тч. При выборе котлоагрегата был учтен запас по паропроизводительности котла:
Дпг = 1015 – Д = 1015 – 37292 = 37851 тч;
Пп-3950-255-545545-ГМ;
Давление острого пара:
Температура острого и вторичного пара:
). Генератор трехфазный переменного тока ТВВ-1200-2 электрической мощностью 1200 МВт.
). Конденсатор основной турбины принимаем типа 1200-КЦС-1.
Поверхность охлаждения:
Расход охлаждающей воды:
Кратность охлаждения:
m = GДк = 29100601 = 4875.
). Конденсаторные насосы главной турбины выбираются с запасом по производительности в 20%. Тогда производительность КЭН выразится:
Qкw = 12 · (Дк + Дподпитки) = 12 · (2163 + 67) = 2676 тч.
Принимаем по три конденсаторных насоса I и II ступени из расчета 2 рабочих и 1 резервный. По каталогу тепломеханического оборудования выбираем:
КЭН-1: КСВ-1600-90: Q = 1600 м3час; Н = 90 м.вод.ст.;
КЭН-II: КВС-1600-220: Q = 1600 м3час; Н = 220 м.вод.ст..
). Питательная установка блока:
Согласно нормам технологического проектирования необходимая производительность питательной установки:
Дп.уст. = (105 ÷ 108) · Дmа
По каталогу выбираем питательный насос типа ПН-1500-350 (3 на блок): Q = 1500 м3ч; Н = 250 ата;
Для бустерного насоса принимаем тип ПД-1600-180 в количестве 3 шт:
Q = 1600 м3ч; давление на напоре Н = 235 кгссм2.
). Для деаэрации питательной воды и исходя из величины Дmаx = 3950 тч выбираем две деаэрационные колонки типа ДСП-2000 производительностью 2000 тч.
Выбираем два деаэрационных бака объемом 185 м3 каждый. Согласно нормам технологического проектирования запас воды в деаэрационных баках блочных установок должен обеспечивать надежную работу питательной установки а значит и блока в течении не менее 35 мин. В данном случае запас питательной воды в баках 370 м3. При работе блока с максимальной производительностью котла (3950 тч) расход питательной воды составляет 70 м3мин. Таким образом запас питательной воды в деаэраторных баках обеспечит надежную работу блока даже в течении 5 минут.
). Циркуляционные насосы:
а). Расход воды на маслоохладители принимаем в размере 12 ÷ 25 % от расхода охлаждающей воды на конденсатор главной турбины:
Wмо = 002 · 105 · 103 = 2160 тч;
б). Расход воды на ОГЦ принимается в размере 25 ÷ 4 % от расхода охлаждающей воды:
Wохл = 003 · 105 · 103 = 3150 тч;
в). Расход воды на эжектора: 4000 тч.
Расход воды через циркнасосы равен сумме всех этих расходов плюс расход охлаждающей воды через конденсатор главной турбины. Необходимо также учесть расход охлаждающей воды через конденсаторы приводных турбин. Он равен: 16000 м3ч (через все конденсаторы приводных турбин). Тогда:
Qц.н. = 105000 + 16000 + 2160 + 3150 + 4000 = 130310 м3ч.
По каталогу тепломеханического оборудования выбираем два циркнасоса на блок типа: ОПЮ-185: Q = 49320 – 74880 м3ч. Насос оборудован поворотно-лопастным механизмом.
). Система регенерации турбины:
Подогреватели низкого давления ПНД-12345 выбираем типа
ПН-23000-29-7 с поверхностью нагрева F = 23000 м2. Подогреватели высокого давления: ПВД-7 типа ПВ-2500-380-17 F = 2485 м2; ПВД-8 типа ПВ-2500-380-42 F = 2200 ПВД-9 типа ПВ-2500-380-61 F = 1285 m2.
). Подъемные насосы эжекторов:
НДС (2 насоса на блок);
Насос дренажного бака:
). Для покрытия тепловых нагрузок на блоке установлена бойлерная установка мощностью 40 Гкалчас. Используется только для общестанционных нужд. Бойлерная включает в себя основной сетевой подогреватель типа
ПВС-315-3-23 и пиковый подогреватель сетевой воды типа ПСВ-315-14-23.
19.Общестанционное оборудование
Бак конденсата калориферов и слива из котла:
Тип: МВН-2148-02 емкостью 300 м3;
Насос бака: КСД-120-5 53.
Бак запаса конденсата:
Тип: МВН-2148-08 емкостью 2000 м3.
Бак загрязненного конденсата:
Тип: МВН-2148-06 емкостью 1000 м3.
Насос аварийной добавки конденсата из БЗК:
Насос постоянной добавки конденсата из БЗК:
Насос кислотной промывки котлов:
Насос бака загрязненного конденсата:
Устанавливаем фильтр сырой воды: ФС-600-1.
ПОВЫШЕНИЕ ЭФФЕКТИВНОСТИ РАБОТЫ
ОБОРУДОВАНИЯ КОСТРОМСКОЙ ГРЭС
Газоотводящий тракт третьей очереди (дымовая труба №3 и примыкающие к ней газоходы) предназначен для удаления дымовых газов от котла типа ТГМП-1202 паропроизводительностью 3950 тч в составе энергетического блока с турбиной 1200МВт. Топливом служит природный газ (резервное - мазут М100).
Паровой котел ТГМП-1202 проектировался для работы под наддувом. Для обеспечения работы котла и удаления уходящих газов установлены три турбовоздуходувки. Уходящие газы эвакуировались по трем ниткам внешних газоходов выполненных из сборных кремнебетонных плит. В качестве резерва помимо трактов воздуходувок были установлены тракты дымососов
ДОД-43ГМ. В процессе эксплуатации котла под наддувом наблюдалась большая загазованность в помещениях главного корпуса и на прилегающей территории. В связи с этим котел перевели на уравновешенную тягу а основные тракты от воздуходувок были отсоединены. В основные газоходы ниток «А» и «В» включены дымососы расчетной нагрузки (ДРН) типа ГД-31. Их необходимость вызвана недостаточной производительностью основных дымососов из-за высокого сопротивления газоотводящего тракта. При температуре наружного воздуха 25 ÷ 27°С по данным эксплуатации блок № 9 набирает нагрузку в пределах 1172 ÷ 1180МВт даже с учетом работы ДРН.
В результате разрушения кремнебетонных плит от сернокислотной коррозии и нарушения герметизации швов между ними увеличились присосы воздуха в газоотводящий тракт. В связи с этим для увеличения газоплотности внутренняя поверхность газоходов была усилена слоем силикатполимербетона толщиной 100 мм. В результате этого их сечение было уменьшено. Это привело к увеличению скорости уходящих газов и еще большим аэродинамическим потерям.
Обследование проведенное в 2006 году сотрудниками УНЦ ТЭБЭ ИГЭУ совместно с эксплуатационным персоналом Костромской ГРЭС показало что силикатполимербетонное покрытие панелей отслоилось и разрушилось.
В целях обеспечения надежности и экономичности работы блока 1200МВт на основе вариантных модельных исследований был разработан технический проект реконструкции внешних газоходов который был взят за основу при рабочем их проектировании Нижегородским теплоэлектропроектом. По этому проекту внешние газоходы выполняются металлическими по улучшенной аэродинамической схеме (рис.6). Реконструкция позволяет снизить сопротивление внешних газоходов на 15 ÷ 20 мм.вод.ст. что способствует сокращению мощности на привод дымососов до 500 кВт и работе блока в номинальном режиме.
Рис. 6. Новая схема внешних газоходов энергоблока 1200МВт Костромской ГРЭС: 1 – железобетонный ствол дымовой трубы; 2 – цокольная часть;
– газоход от ДРН; 4 – дымососы ДОД-43ГМ; 5 – диффузор-переход.
Неоптимизированными остались участки сопряжения осевых дымососов ДОД-43ГМ с газоходами. Схема осевого дымососа представлена на рис. 7. Он состоит из всасывающего кармана поворотных направляющих аппаратов с общим приводом вала с рабочими лопатками спрямляющего аппарата и выходного диффузора образованного внешним коническим и внутренним цилиндрическим кожухами. За выходным диффузором дымососа имеется участок сопряжения с газоходом (рис. 7поз. 7) который имеет форму диффузор-перехода с круглого сечения на прямоугольное. С аэродинамической точки зрения эти участки выполнены нерационально. За выходным диффузором дымососа из-за резкого среза внутреннего кожуха образуется вихревая зона отрыва потока. Это приводит к увеличению местных потерь напора расхода электроэнергии на привод дымососа и расхода сжигаемого топлива.
Рис. 7. Схема осевого дымососа и участка сопряжения с газоходом:
– всасывающий карман; 2–поворотный направляющий аппарат; 3 – рабочие лопатки; 4 – спрямляющий аппарат; 5–выходной диффузор дымососа;
– внутренний кожух выходного диффузора; 7 – участок сопряжения дымососа с газоходом; 8 – обтекатель; 9 – газоход.
Одним из способов снижения сопротивления данного участка является установка обтекателя на срезе внутреннего кожуха осевого дымососа. Поиск оптимальной формы обтекателей и участка сопряжения выходного диффузора дымососа с газоходами является весьма трудоемкой задачей. Решить ее не представляется возможным без привлечения современной вычислительной техники и проведения экспериментальных исследований на моделях.
2.Анализ аэродинамической эффективности существующей схемы участка сопряжения «дымосос – газоход»
Существует несколько методов решения поставленной задачи. Первый метод – проведение экспериментальных аэродинамических исследований на физических моделях. Это метод надежен и позволяет с достаточной точностью смоделировать процессы протекающие на участке сопряжения «дымосос-газоход» при течении уходящих газов однако проведение физического эксперимента требует разработки и выполнения аэродинамической модели наличия мощных тягодутьевых механизмов и специализированного приборного парка а так же проведения объемных расчетов при обработке результатов исследований. Таким образом в условиях ВКР данный метод не применим.
Существует менее затратный метод аэродинамических исследований основанный на использовании специализированных программных средств расчетной гидрогазодинамики. В настоящее время существует большое количество прикладных программных комплексов позволяющих моделировать трехмерные течения а так же процессы сопровождающие их (горение свободная поверхность тепломассообмен и т.д.). Наиболее известными являются: Ansis Fluent и CFX Flow Simulation (Solid Works) Flow Vision.
Моделируемые течения включают в себя стационарные и нестационарные сжимаемые слабосжимаемые и несжимаемые потоки жидкости и газа. Использование различных моделей турбулентности и адаптивной расчетной сетки позволяет моделировать сложные движения жидкости включая течения с сильной закруткой горением течения со свободной поверхностью.
FlowVisionоснован на конечно-объемном методе решения уравнений гидродинамики и использует прямоугольную адаптивную сетку с локальным измельчением. Для аппроксимации криволинейной геометрии с повышенной точностью FlowVision использует технологию подсеточного разрешения геометрии. Эта технология позволяет импортировать геометрию из систем САПР и обмениваться информацией с системами конечно-элементного анализа. Использование этой технологии позволило решить проблему автоматической генерации сетки – чтобы сгенерировать сетку достаточно задать всего лишь несколько параметров после чего сетка автоматически генерируется для расчетной области имеющей геометрию любой степени сложности. Основной задачейFlowVisionявляется численное решение уравнений вычислительной гидродинамики.
Рассмотрим основные этапы моделирования течения уходящих газов на примере существующего участка сопряжения дымососа с газоходом ниткиА.
На первом этапе была разработана геометрическая модель участка сопряжения «дымосос-газоход» (рис. 8).
При разработке геометрических моделей были учтены следующие требования:
-объемы составляющие геометрическую модель должны быть замкнуты;
-объемы составляющие геометрическую модель должны быть вложены друг в друга и не пересекаться.
Модель включает в себя выходной кольцевой диффузор дымососа участок сопряжения «дымосос-газоход» и прямолинейный участок необходимый для исключения возможных ошибок при моделирование связанных с образованием вихрей на выходном граничном условии.
Рис. 8. Геометрическая модель участка сопряжения «дымосос-газоход»:
– выходной диффузор дымососа; 2 – участок сопряжения «дымосос-газоход»;
– прямолинейный участок.
На втором этапе осуществляется загрузка геометрической модели в FlowVision для дальнейшей физической постановки задачи. Результат переноса модели в FV приведен на рис. 9.
Рис. 9. Результат переноса геометрической модели в FV.
Далее задается физическая модель течения уходящих газов в газоходе. Задание физической модели осуществляется путем задания вещества фазы и модели течения.
В данной работе решалась однофазная задача внутреннего течения (т.е. течения в ограниченном канале) однокомпонентной среды поэтому задавалось только одно вещество – воздух. Фаза была задана непрерывной. В связи с тем что число Маха в газоходах не превышает 03 в качестве модели течения газов была выбрана модель турбулентного течения несжимаемой жидкости. В качестве модели турбулентности выбрана стандартная k-e модель.
На третьем этапе задавались граничные условия. В общем случае процедура граничных условий включает в себя следующие этапы:
-создание граничных условий;
-расстановка граничных условий;
-задание параметров граничных условий.
Были созданы следующие граничные условия:
-на входном сечении модели создано граничное условие «ВходВыход» в качестве параметра выбрана нормальная скорость;
-на выходном сечении (выход из прямолинейного участка) создано граничное условие «Выход» тип «Свободный выход» (переменная - давление);
-на стенках газохода было создано граничное условие “Cтенка”. Шероховатость стенок выполненных из металла была выбрана равной 005 мм.
На четвертом этапе была произведена генерация расчетной сетки. Пример расчетной сетки модели представлен на рис. 10. Общее количество расчетных ячеек было выбрано с учетом предварительных исследований на сеточную сходимость. Итоговое число расчетных ячеек необходимое для разрешения геометрии и особенностей структуры течения составило порядка 123000 элементов. Данное количество было получено исходя из условия что дальнейшее измельчение сетки не приводило к ощутимому увеличению точности результата. На данном этапе также задавались параметры управляющие расчетом (шаг по времени задавался числом Куранта-Фридрихса-Леви равным 100).
Рис. 10. Пример расчетной сетки в FV.
В ходе выполнения расчета сходимость решения определялось по величине невязок скорости на выходном сечении и полном давлении на входном сечении модели.
Необходимость окончания расчета оценивалась по величине невязки искомой величины в качестве которой выступал коэффициент сопротивления моделируемого участка газохода.
Коэффициенты сопротивления на участке “дымосос – газоход” определялся по формуле:
где РПвх и РДвх – полное и динамическое давления на входе в модель;
РПвых – полное давление на выходе из модели.
Оценка аэродинамической эффективности существующей схемы участка сопряжения «дымосос – газоход» выполнена визуально используя средства визуализации программного комплекса FV и количественно по значению коэффициента сопротивления данного участка. Пример визуализации слоя по переменной «скорость» в продольном сечении модели приведена на рис. 11.
Рис. 11. Пример визуализации слоя «скорость».
Из рис. 10 видно что на выходе из осевого дымососа имеет место резкое расширение сечения что приводит к образованию обширного отрыва потока (вихря). При этом длина стабилизационного участка (Lстаб) оказывается весьма значительной (Lстаб 10·Dэкв где Dэкв – эквивалентный диаметр прямого участка газохода). Из условия компоновки непосредственно за участком сопряжения расположен поворот газохода(рис. 6). В результате этого поток дымовых газов не успевает стабилизироваться и на входе в поворот он имеет неравномерный профиль скоростей что еще больше увеличивает сопротивление внешних газоходов и способствует образованию вихревых зон.
Аэродинамические исследования показали что сопротивление рассматриваемого участка зависит от его длины. Далее приведены результаты расчета коэффициента сопротивления участков сопряжения дымососов с газоходами ниток А Б В блока №9.
Длина диффузор-перехода Lдп (м)
Коэффициент сопротивления
3.Разработка новой аэродинамической схемы участка сопряжения «дымосос – газоход»
Одним из способов снижения сопротивления рассматриваемых участков является установка за кольцевым диффузором дымососа обтекателя. Это позволит обеспечить более плавный выход дымовых газов из кольцевого диффузора дымососа и по возможности сократить интенсивность явлений связанных с отрывом потока. Схема и место установки обтекателя приведены на рис. 7 (поз. 8). Исследование эффективности установки обтекателя за выходным диффузором дымососа проводилось аналогичным методом аэродинамических исследований описанных раннее. Геометрическая модель нового участка сопряжения «дымосос-газоход» приведена на рис. 12.
Рис. 12. Геометрическая модель нового участка сопряжения дымососа с газоходом: 1 – внутренний кожух выходного диффузора дымососа;
–выходной диффузор дымососа; 3– обтекатель; 4 – диффузор-переход;
–прямолинейный участок газохода.
Результаты аэродинамических исследований новой схемы участка сопряжения приведены на рис. 12 и сведены в таблицу ниже.
Рис.13. Пример визуализации слоя «скорость» для варианта с обтекателем.
Снижение сопротивления %
Из данной таблицы и рис. 12 видно что установка обтекателя за срезом внутреннего кожуха выходного диффузора дымососа позволяет обеспечить плавный характер течения потока на этом участке и снизить его сопротивление в 2 ÷ 3 раза за счет существенного снижения размера вихревой зоны. При этом чем меньше длина диффузор-перехода тем выше его сопротивление. Это объясняется тем что с уменьшением длины данного участка происходит увеличение угла раскрытия его стенок. Это способствует более быстрому падению скорости что приводит к отрыву пограничного слоя от стенок и увеличению аэродинамических потерь.
БИБЛИОГРАФИЧЕСКИЙ СПИСОК:
Идельчик И.Е. Справочник по гидравлическим сопротивлениям. - М.Л.:Госэнергоиздат. - 1960.
Левин М.Л. Боткачик И.А. Дымососы и вентиляторы мощных электростанций. - М.Л.: Госэнергоиздат. - 1962.
Волков Э.П. Гаврилов Е.И. Дужих Ф.П. Газоотводящие трубы ТЭС и АЭС. - М: Энергоатомиздат. - 1987.
Инструкция по эксплуатации энергоблока 1200 МВт.
«Термодинамические свойства воды и водяного пара» Ривкин С.Л. 1980г. «Энергия»
«Тепловой расчёт паровых турбин» Копелович Б.Э.
Мошкарин А.В. Барочкин Е.В. Зорин М.Ю. «Расчет тепловой схемы энергетического блока конденсационной электростанции» Учебно- методическое пособие 2006 г.
«Охрана водного и воздушного бассейнов от выбросов ТЭС» Рихтер Л.А. 1981г.
«Методические указания по дипломному проектированию ТЭС» Орлов Г.Г. 1985г.
«Исследование реальных тепловых схем ТЭС и АЭС» Рубенштейн Я.М. Щепятильников М.И.
Типовая энергетическая характеристика турбоагрегата К -1200 - 240 ЛМЗ.
Правила техники безопасности при эксплуатации тепломеханического оборудования электростанций и тепловых.
hS-диаграмма водяного пара.
«Электрические станции» Энеропрогресс №12 2003.
Орлов Г.Г. Зорин М.Ю. «Расчет термодинамических циклов ТЭС» Учебное пособие ГОУ ВПО «Ивановский гос. энергетич. ун-т им. В.И. Ленина». – Иваново 2011.
Результаты моделирования.cdw

- железобетонный ствол дымовой трубы; 2 - цокольная часть; 3 - газаход от ДРН;
- дымососы ДОД-43 ГМ; 5 - диффузор-переход.
Схема осевого дымососа и участка сопряжения с газоходом:
- всасывающий карман; 2 - поворотный направляющий аппарат; 3 - рабочие лопатки;
- спрямляющий аппарат; 5 - выходной диффузор дымососа; 6 - внутренний кожух выходного диффузора;
- участок сопряжения дымососа с газоходом;8 - обтекатель; 9 - газоход
Таблица результатов расчета коэффициента сопротивления участков
сопряжения дымососов с газоходами ниток А
Результаты моделирования
Повышение эффективности работы
оборудования Костромской ГРЭС
Тепловая схема блока 1200МВт.frw
оборудования Костромской ГРЭС
от береговой насосной
из системы охлаждения
в канал пола маш.зала
в верхнюю часть кон-ра
в нижнюю часть кон-ра
в расширитель др. В. Д.
Охладитель уплотнений
Конденсатный насос 1 ступени
Конденсатный насос 2 ступени
Деаэраторная колонка
Охладитель газоохладителей генератора конденсатом
Охладитель газоохладителей генератора цирк.водой
Питатель сетевой воды (пиковый)
Питатель сетевой воды (основной)
Паросбросное быстродействующее устройство
Бак расширителя дренажей Н. Д.
Растопочный расширитель
Расширитель дренажей Н. Д.
Расширитель дренажей В. Д.
Конденсатные насосы ТПН
Конденсатные насосы ТВД
Насосы рециркуляции среды
Растопочный сепаратор
Рекомендуемые чертежи
- 07.04.2018
- 17.07.2020
- 04.11.2022
- 01.01.2025