Проектирование отливок и поковок




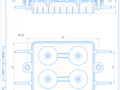
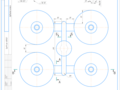
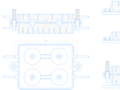
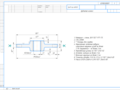
- Добавлен: 24.01.2023
- Размер: 1 MB
- Закачек: 0
Описание
Состав проекта
![]() |
![]() |
![]() ![]() ![]() |
![]() ![]() ![]() ![]() |
![]() ![]() ![]() ![]() |
![]() ![]() ![]() |
![]() ![]() ![]() ![]() |
![]() ![]() ![]() |
Дополнительная информация
Зубчатое колесо.frw

Заготовка.frw

Опока.cdw

Отливки в рамке.frw

Отливки.frw

Рекомендуемые чертежи
- 24.01.2023
- 24.01.2023
- 24.01.2023
- 13.05.2023