Проект цеха получения отливок по выплавляемым моделям из специальных сплавов мощностью 2000 тонн в год




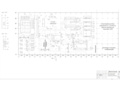

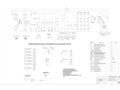
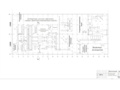
- Добавлен: 24.01.2023
- Размер: 45 MB
- Закачек: 2
Описание
Состав проекта
![]() |
![]() |
![]() ![]() ![]() |
![]() |
![]() |
![]() ![]() ![]() ![]() |
![]() |
![]() ![]() ![]() ![]() |
![]() ![]() ![]() ![]() |
![]() ![]() ![]() ![]() |
![]() |
![]() ![]() ![]() ![]() |
![]() ![]() ![]() ![]() |
![]() |
![]() ![]() ![]() ![]() |
![]() ![]() ![]() ![]() |
![]() |
![]() ![]() ![]() ![]() |
![]() |
![]() ![]() ![]() ![]() |
![]() |
![]() |
![]() |
![]() |
![]() |
![]() |
![]() |
![]() |
![]() |
![]() |
![]() |
![]() |
![]() |
![]() |
![]() |
![]() |
![]() |
![]() |
![]() |
![]() |
![]() ![]() ![]() |
Дополнительная информация
02.План цеха.2-й этаж.dwg

01.План цеха.1-й этаж.dwg

10.Разрез электропечи мод. ПВП 12.15.11.dwg

14.Схема защитного заземления.dwg

12.Схема разводки и данные спиралей электропечи мод. ПВП 12.15.11.dwg

09.Электропечь мод. ПВП 12.15.11.Габаритный чертеж.dwg

Спецификация.dwg

04.Схема MJM процесса.dwg

03.Разрез цеха.dwg

11.Принципиальная электическая схема электропечи мод. ПВП 12.15.11.dwg

Рекомендуемые чертежи
- 24.01.2023
- 13.05.2023
- 24.01.2023
- 25.01.2023