Модернизация катка бегунов мокрого измельчения СМ-21Б




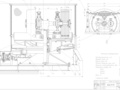
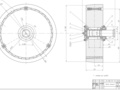
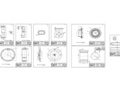
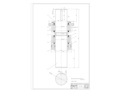
- Добавлен: 25.10.2022
- Размер: 1016 KB
- Закачек: 0
Описание
Состав проекта
![]() |
![]() ![]() ![]() ![]() |
![]() ![]() ![]() ![]() |
![]() |
![]() ![]() ![]() |
![]() ![]() ![]() ![]() |
![]() ![]() ![]() ![]() |
![]() ![]() ![]() |
![]() ![]() ![]() |
![]() ![]() ![]() |
Дополнительная информация
rss-srsre-rrrsrrr-rr-21rrrrrrr.dwg

rrsrrye-rrrerrrer-rrrsrrr-rr-21rrrrrrr.dwg

rrsrrresrrryer-rrrsrrr-rr-21rrrrrrr.dwg

rrrsrs-rr-21r-rrrsrsrsr-srssrrrrrrrr.dwg
