Бегуны СМ-21Б



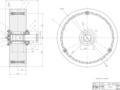
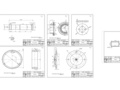
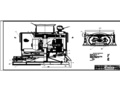
- Добавлен: 25.10.2022
- Размер: 4 MB
- Закачек: 0
- ВКонтакте
- РћРТвЂВВВВВВВВнокласснРСвЂВВВВВВВВРєРСвЂВВВВВВВВ
- Telegram
Описание
Состав проекта
![]() |
![]() ![]() ![]() ![]() |
![]() ![]() ![]() |
![]() ![]() |
![]() |
![]() ![]() ![]() |
![]() ![]() ![]() |
![]() ![]() |
![]() ![]() |
![]() ![]() ![]() ![]() |
![]() ![]() ![]() ![]() |
Дополнительная информация
Мурзанаев А1 Общий вид с модернизацией.dwg

Частота вращения чаши
Техническая характеристика
БГТУ им. В.Г. Шухова гр. МО-25
Спецефикация на каток.doc
Гайка М20 ГОСТ 5915-70
Винт М12х60 ГОСТ 1491-80
Подшипник 128 ГОСТ 8338-76
БГТУ им. В.Г.Шухова гр.МО-32
Спецификация на общий вид.doc
Устройство амортизации
БГТУ им. В.Г.Шухова гр.МО-32
Болт 2.1.М20х400.ВСт3пс2
Винт 2 М16х60 ГОСТ 50383-92
Гайка М20 ГОСТ 5915-70
Гайка М30 ГОСТ 5915-70
Шпонка 36х32х163 ГОСТ 10748-79
кп пз Бегуны СМ-21Б .docx
Белгородский государственный технологический университет
Кафедра: Механическое оборудование
По дисциплине: «Механическое оборудование»
На тему «Модернизация бегунов СМ-21Б»
Ст. пр. Бражник Ю.В.
ТЕХНОЛОГИЧЕСКАЯ ЧАСТЬ4
1Описание технологической схемы производства4
2Техническая характеристика бегунов6
СПЕЦИАЛЬНАЯ ЧАСТЬ ПРОЕКТА8
1 Описание конструкции и принципа действия бегунов мокрого помола8
3 Сущность модернизации23
4 Расчет основных параметров бегунов мокрого помола26
4.1 Расчет производительности бегунов26
4.2 Расчет потребляемой мощности бегунов28
5 Прочностные и проверочные расчеты отдельных деталей и узлов машины31
5.1 Прочностные расчёты шпонки31
5.2 Расчет подшипников на долговечность33
5.3 Расчет вертикального вала бегунов34
В настоящее время широкое распространение получила асбестоцементная керамическая стекольная промышленность. В связи с этим для производства строительных материалов машиностроительные заводы выпускают и модернизируют различные машины и оборудование с целью одновременного улучшения качества продукции и снижения затрат на производство.
Одними из основных машин при производстве строительных и сырьевых материалов являются машины для измельчения которые подразделяются на две группы: дробилки и мельницы. Бегуны как машина для измельчения является наиболее универсальной так как предназначена как для мелкого дробления так и для грубого помола а так же обеспечивает специальные технологические требования: уплотнение растирание обезвоздушивание поэтому модернизация бегунов является целесообразным решением [2].
В связи с большими финансовыми издержками при производстве строительных материалов важно оптимизировать процесс производства и модернизировать оборудование.
К основным направлениям модернизации бегунов можно отнеси:
увеличение производительности;
снижение потребляемой мощности;
повышение надежности;
улучшение ремонтопригодности;
повышение качества готового продукта;
увеличение срока службы основных деталей и узлов.
Правильная и качественная модернизация рабочего оборудования позволяет избежать ненужных финансовых затрат обеспечить непрерывность рабочего процесса позволяет свести к минимуму время простоя оборудования а так же увеличить качественные характеристики готового продукта [7].
ТЕХНОЛОГИЧЕСКАЯ ЧАСТЬ
1Описание технологической схемы производства
Технологическая схема производства асбестоцементных изделий с использованием бегунов мокрого помола представлена на рисунке 1.1. Номенклатура производимых асбестоцементных изделий насчитывает свыше 40 наименований. Они могут быть разделены на следующие основные группы: профилированные листы — волнистые и полуволнистые для кровель и обшивки стен; плоские плиты — обыкновенные и офактуренные или окрашенные для облицовки стен; панели кровельные и стеновые с теплоизоляционным слоем; трубы напорные и безнапорные и соединительные муфты к ним; а так же специальные изделия. В качестве вяжущего компонента при производстве асбестоцементных изделий используют специальный портландцемент для асбестоцементных изделий. В данном случае применяется портландцемент М400.
При приготовлении асбестоцементной массы необходимо подать в производство сырье — цемент асбест различных марок воду. Затем составить смеску из асбеста различных марок обмять и распушить а затем из асбестовой смески цемента и воды приготовить порцию асбестоцементной массы и выдать ее в промежуточную емкость — накопитель для питания формовочных машин.
По этой схеме асбест подается в приемный бункер 1 и далее — в бункера питателей 3. Из бункеров асбест периодически выдается в дозаторы 4 для весового составления смески. Приготовленная порция смески поступает на бегуны 5 куда из дозаторов 2 подается вода. Обмятая порция асбеста через приемный бункер 6 поступает для промежуточного хранения в бункер одного из питателей 7. Питатель периодически выдает асбест на весовой дозатор 8. Отвешенная порция обмятого асбеста и вода в заданном количестве поступают поочередно в одну из мешалок 9 для приготовления водной суспензии асбеста. Из мешалок порция суспензии проходит через дезинтегратор 10 в один из турбосмесителей 11 куда из бункера 13 с помощью дозатора 12 подается весовая порция цемента а из бака 14 — порция воды. Приготовленная в турбосмесителе асбестоцементная масса периодически выдается в ковшовую мешалку (на схеме не показана)[8].
Рисунок 1.1 Технологическая схема приготовления асбестоцементной массы:
— приемный бункер асбеста; 2 — дозатор воды; 3 — питатель асбеста;
— дозатор асбеста; 5 — бегуны; 6 — приемный бункер бегунов; 7 — питатель обмятого асбеста; 8 — дозатор обмятого асбеста; 9 — мешалка; 10 — дезинтегратор; 11 — турбосмеситель; 12 — дозатор цемента; 13 — бункер цемента; 14 — дозирующий бак воды; 15 — сборник осветленной воды; 16 — рекуператор.
Обмятая порция асбеста выдается из бегунов в мешалку туда же подается вода в заданном количестве. Приготовленная в мешалке водная суспензия асбеста насосом перекачивается в голлендер куда из дозатора подается весовая порция цемента. Приготовленная порция асбестоцементной массы выдается в ковшовую мешалку для промежуточного накопления и непрерывной подачи на листоформовочные машины [3].
2Техническая характеристика бегунов
Качество готовой продукции на заводах по производству строительных материалов в очень большой мере зависит от качества переработки асбеста или шихты. Брак в формовке сушке и обжиге во многих случаях является результатом неудовлетворительного размола включений и недостаточного перемешивания массы. По этой причине на реконструируемых и вновь строящихся механизированных строительных заводах часто устанавливаются бегуны [1].
Процесс измельчения в бегунах заключается в том что в чаше перекатываются тяжелые катки раздавливающие насыпанную на чашу породу. Встречаются конструкции в которых катки остаются неподвижными а вращается чаша. В обоих случаях измельчение материала производится раздавливанием его тяжестью катков. Бегуны имеют скребки непрерывно перегребающие измельчаемый материал под катки.
Измельчение производимое бегунами имеет двоякий характер. Во-первых каток тяжестью собственного веса раздавливает и тем измельчает материал. Во-вторых скольжение катков при движении их истирает раздавленный материал. Средняя величина получаемых зерен после размола твердых пород колеблется от 15 до 3 мм. Одновременно получается и некоторое количество пыли в молотом материале. Зерна материалов получаются с несколько заостренными углами. Бегуны обеспечивают хорошее перемешивание массы[2].
Достоинства бегунов в сравнении с другими машинами для измельчения:
возможность точно соблюдать дробление до определенной величины зерна (гранулометрический состав массы);
легкость конструкции;
простота обслуживания;
широкий диапазон использования;
обеспечивание специальных технологических требований (уплотнение растирание обезвоздушивание).
Бегуны должны размещаться в закрытом сухом и теплом производственном помещении. Бегуны обычно размещаются в действующем цехе помола вблизи от склада с материалом который подвергается помолу. Загрузку материала под катки производят вручную или питателем. Постоянная подача материала для раздавливания и истирания так же и автоматическое перемешивание производится скребками. В таблице 1.1 представлена техническая характеристика бегунов [8].
Производительность тч
Частота вращения чаши обмин
Мощность электродвигателя кВт
СПЕЦИАЛЬНАЯ ЧАСТЬ ПРОЕКТА
1 Описание конструкции и принципа действия бегунов мокрого помола
Бегуны являются машиной непрерывного действия с неподвижной чашей 5 укреплённой на станине. Днище чаши выложено стальными плитами на которых материал раздавливается и истирается двумя катками 1. На верхнем конце вертикального вала 4 прикреплена втулка 3 соединяющая его с осью катка 2. Благодаря такому креплению катков при вращении вертикального вала втулка увлекает за собой и оси катков. Катки катятся по днищу чаши а при попадании под кусок не дробимого материала каток поднимаемся и перекатывается через него. Привод 6 представляет собой вертикального вала движение которому передаётся от электродвигателя через редуктор на приводной вал и конические шестерни . В станине имеется разгрузочное отверстие через которое выгружается измельченный материал.
Рис 2. 1. Кинематическая схема бегунов:
– катки; 2 – полуоси каков; 3 – втулка (водило); 4 – вертикальный вал; 5 – чаша; 6 – привод; 7 – скребки.
Каток состоит из ступицы и бандажа соединенных клиновыми вкладышами которые стягиваются болтами. Такое устройство обеспечивает быструю смену бандажей. Ступицы катков изготавливают из чугуна бандажи – из стали. Для повышения срока службы бандажей из поверхность наплавляют твердыми сплавами. Кривошипные оси испытывают большие нагрузки так как они противостоят центробежным силам возникающим при вращении тяжёлых катков вокруг оси вертикального вала; их изготавливают из стали. Катки обычно монтируют на разных расстояниях от вертикального вала. При таком расположении катков измельчаемый материал вначале поступает на внутреннюю дорожку состоящую из сплошных плит где растирается и проминается катком расположенным ближе к центру чаши а затем направляется скребками на внешнюю периферийную дорожку из дырчатых плит с овальными отверстиями. Катком более удаленным от центра чаши глина продавливается сквозь отверстия в дырчатых плитах на вращающуюся вместе с валом тарелку с которой снимается неподвижно укрепленным скребком.
Плиты чаши бегунов мокрого измельчения укладывают на опорные поверхности неподвижной чаши так что 10 плит образуют кольцевой под по которому катятся катки. Каждая плита имеет около 150 продолговатых отверстий шириной до 16 мм. Вследствие большой массы катков и возникающих в процессе работы динамических нагрузок плиты для большей прочности выполняют в виде стальной отливки с ребрами жесткости высотой 100мм и толщиной у основания 20мм. Ребра жесткости располагают как по периметру каждой плиты так и внутри ее [2].
Рабочая часть плиты имеет толщину 30мм и в процессе работы быстро изнашивается так как на ней тяжелые катки раздавливают и истирают абразивный материал. Несмотря на высокое качество материала и закалку плит они требуют замены после 2 - 3 месяцев работы при износе доо 15% от первоначальной массы (вес каждой плиты примерно 106 кг). Сложная форма плит затрудняет их изготовление и требует много металла.
Скребки 7 также относятся к быстроизнашивающимся деталям и являются сменными. Крепят скребки к приспособлению обеспечивающему точную установку и возможность подъема скребка для предотвращения поломки. Скребковые устройства равномерно подают поступающий сверху из загрузочной воронки исходный материал под катки а измельченный - на кольцевое сито. Не прошедшие сквозь отверстия сита куски снова подаются скребками под катки. Просеянный материал поступает на неподвижный поддон с которого подается скребком в сборный лоток. Производительность бегунов лимитируется частотой вращения вертикального вала [3].
Измельчение в бегунах осуществляется в результате раздавливания с одновременным истиранием между цилиндрической поверхностью катков и плоской поверхностью чаши (пода) бегунов по которой перекатываются катки.
Рис 2.2 Конструкция бегунов СМ-21Б:
– фрикционная муфта; 2 – редуктор; 3 – цилиндрическая шестерня; 4 – зубчатое колесо; 5 – вращающаяся чаща; 6 – подшипники качения с витыми роликами; 7 – оси чаши; 8 – внутренние цельные плиты; 9 – внешние дырчатые плиты; 10 – каток; 11 – скребки; 12 – каток в разрезе; 13 – диск; 14 – скребок; 15 – разгрузочный латок.
Даная конструкция бегунов мокрого помола работает таким образом. Чаша 5 которая вращается вместе с осью 7 под действием сил трения приводит во вращение катки 10 и 12 установленные свободно на валу 16 который в зависимости от толщины слоя материала может вместе с катками перемещаться по вертикали. Поддон в центральной части выполнен из сплошных плит а по его периферии расположено кольцевое сито 9. Материал прошедший сквозь сито 9 выпадает на диск (тарельчатый питатель) 13 из которого скребком 14 сбрасывается в разгрузочный лоток 15.
Достоинства бегунов мокрого помола:
можно загружать значительно большие куски материала;
проще регулировать тонкость измельчения;
улучшаются пластические свойства глиняных материалов из-за многократного воздействия катков.
обеспечение специальных технологических требований (уплотнение растирание обезвоздушивание) [7].
Недостатки бегунов мокрого помола:
повышенный удельный расход энергии на единицу массы перерабатываемого материала [8].
При выполнении патентного исследования мы сделали вывод что для уменьшения времени активирования твердеющей смеси путем установления устройства подготовки пресс-порошка используется авторское свидетельство №200221277603.
Бегуны с использованием цилиндрического перфорированного корпуса.
Для увеличения эффективности производительности бегунов и структурного улучшения материалов используется патент № 2054327.
Отличительной особенностью является использование цилиндрического перфорированного корпуса который выполнен в виде реечного барабана. Рейки которого установлены на кольцевых шпангоутах.
Для лучшего взаимодействия с обрабатываемым материалом каток может быть выполнен в виде цилиндрической спирали причем спираль может быть как однонаправленной так и комбинированной из двух половин со встречным направлением навивки что позволяет стабилизировать ее положение в поперечном направлении при движении.
Рис. 2.3 Бегуны общий вид:
– кольцевые шпангоуты; 4 – приводной вал; 7 – опоры; 8 – рама; 9 –приводная звездочка; 12 – вал; 13 – шкив; 14 – опоры; 15 – ведущий шкив; 16 – электродвигатель; 17 – натяжное устройство; 18 – ограждение; 19 – лоток; 20 – каток; 21 – гибкие петли; 2223 – натяжные устройства; 24 – рельсовый ход.
Рис 2.4 Бегуны разрез А-А:
– корпус; 4 – приводной вал; 7 – опоры; 9 – приводная звездочка; 10 – цепь; 11 – ведущая звездочка; 12 – вал; 13 – шкив; 14 – опоры; 15 – ведущий шкив; 16 – электродвигатель; 17 – натяжное устройство; 18 – ограждение; 19 – лоток; 20 – каток; 21 – гибкие петли; 2223 – натяжные устройства; 24 – рельсовый ход.
Рис. 2.5 Схема расположения гибких петель.
Рис 2.6 Бегуны разрез Б-Б:
– реечный барабан; 4 – вал; 5 – рейки; 6 – опорные кольца; 8 – рама; 9 – приводная звездочка; 18 – ограждение; 19 – загрузочный лоток; 20 – каток; 24 – рельсовый ход.
Рис. 2.7 Вариант выполнения катка
Устройство работает следующим образом: Включением привода 16 приводят корпус 1 установленный на валу 4 во вращение. При этом каток 20 также начинает катиться по внутренней поверхности корпуса 1. Перерабатываемую глину подают транспортером или другим механизмом в загрузочный лоток 19 по которому глина поступает внутрь корпуса 1. Под воздействием катка 20 глина перемешивается и продавливается через зазоры между рейками 2 корпуса 1. Рейки 5 приводного вала 4 одновременно с передачей вращения корпусу 1 выталкивают попавшую в зазоры между рейками 2 глину способствуя очищению корпуса. Налипшая на внешней поверхности корпуса 1 глина счищается (срезается) гибкими петлями 21. Петли 21 также устраняют раскачивание корпуса 1. Натяжение гибких петель 21 регулируют натяжными устройствами 22 23. Перемещают агрегат по рабочему участку с помощью рельсового хода 24.
Целью данной модернизации является снижение энергопотребления габаритов и увеличение производительности а также простота обслуживания и ремонта [9].
Бегуны с использованием механизма прижима катков
Для увеличения эффективности измельчения глиняной массы путем уменьшения веса катков и использования прижимного механизма используется патент №2036008.
Отличительной особенностью является использование бегунов с катками которые прижимаются ко дну чаши механизмом прижима. Сами катки свободно установлены на горизонтальные полуоси крестовины а крестовина установлена на вертикальной оси. Крестовина может свободно вращаться вокруг оси. Так же дно чаши выполнено в виде решетки образованной длинномерной пластиной свернутой по спирали с зазорами между витками.
Рис. 2.8 Бегуны предлагаемой конструкции:
– чаша; 4 – клиноременная передача; 11 – ось; 12 – крестовина; 13 – катки; 14 – кольцевые элементы; 15 – кожух; 16 – пружина; 17 – станина; 18 – винтовой паз; 19 – скребки; 20 – чаша.
Рис. 2.9 Бегуны разрез А-А:
– катки; 14 – кольцевой элемент; 15 – кожух; 16 – пружины; 18 – винтовой паз.
– решетка; 3 – боковина; 5 – пластина; 6 – штыри; 7 – ступица; 8 – крепежные элементы; 15 – кожух.
Рис 2.11 Разрез Б-Б узла 1:
– длинномерная пластина.
Бегуны работают следующим образом: При включении привода через клиноременную передачу 4 приводится во вращение чаша 1 с решеткой 2. Вследствие того что катки прижаты к вращающейся решетке и свободно смонтированы на полуосях крестовины 12 которая в свою очередь свободно смонтирована на оси 11 вращательное движение передается каткам и они перекатываются по измельчаемому материалу. Перерабатываемая масса раздавливается и истирается между цилиндрическими поверхностями катков и совокупностью плоскостей ребер решетки режется кромками вращающихся витков и продавливается в зазоры. На выходе из решетки полосы измельченной массы в плоскости перпендикулярной плоскостям реза витками еще раз разрезаются скребками 19.
В результате такой переработки глина приобретает необходимую для качественного изготовления изделий степень измельчения при этом расход энергии на единицу массы перерабатываемого материала значительно ниже чем в конструкциях известных бегунов.
Целью данного изобретения является повышение эффективности измельчения глиняных масс с одновременным снижением массы и габаритов бегунов [9].
Бегуны с использованием модернизированных катков
Для возможности использования бегунов для дробления пористых материалов используется патент № 1348450.
Изобретение позволяет сократить выход мелкой фракции раздрабливаемого материала и увеличить срок службы рабочих органов.
Изобретение относится к промышленности строительных материалов и может быть использовано преимущественно при дроблении аглопоритового спека.
Рис. 2.12. Модернизированные катки бегунов:
– катки; 2 – бандажи; 3 – шпильки; 4 – чаша; 5 – основание; 6 – решетчатая дорожка; 78 – отверстия; 9 – кулак; 10 – вертикальный вал.
Бегуны содержат катки 1 на которых смонтированы съемные бандажи 2 закрепленные на шпильках 3. Рабочая поверхность бандажей 2 в поперечном сечении имеет форму выпуклой сферы. Катки 1 перекатываются по днищу чаши 4 которая состоит из основания 5 и кольцевой решетчатой дорожки 6 с отверстиями 7. Поверхность дорожки 6 контактирующая с бандажами 2 выполнена вогнутой по форме рабочих поверхностей бандажей катков.
Применение предлагаемых бегунов позволяет исключить переизмельчение материала вследствие кривизны решетки раздробленные куски требуемых размеров сразу же попадают в отверстия тем самым обеспечивается снижения выхода мелкой фракции.
Кроме того благодаря сокращению времени контактирования рабочих органов с абразивным раздрабливаемым материалом повышается срок службы бегунов.
Целью изобретения является снижение выхода мелкой фракции и увеличение срока службы рабочих органов бегунов [9].
Бегуны с применением дозаторов
Для обеспечения точной дозировки поступающей массы применяется патент № 55717.
Совершенствование устройства для дозировки материала поступающего на измельчение крайне актуально так как это положительным образом влияет на возможность регулировки времени обработки и равномерности обработки материала.
Отличительной особенностью данной модернизации является применение дозаторов периодическим и притом автоматически приводимых в действие т главного вала при помощи цепной передачи обеспечивающей периодическое расцепление зубчатого колеса и несущего вала.
Рис. 2. 13 Боковой вид модернизируемых бегунов:
– Вертикальный вал; 3 – обойма.
Рис 2. 14 Общий вид разгрузочного устройства в разрезе:
– диски; 16 – вал; 17 – шестерни; 18 – конический сектор; 19 – вертикальный вал; 20 – зубчатая рейка; 21 – зубчатка; 22 – храповик; 23 – дисковый сектор ; 24 – собачка храповика; 25 – распределительная коробка.
Рис. 2. 15 Вид зубчаток в разрезе:
– швеллер; 2 – вертикальный вал; 3 – обойма; 4 – зубья; 5 – зубчатое колесо; 6 – подвесной вал; 7 – шестерня; 8 – звездочки; 9 – фасонная втулка; 10 – зубчатый венец; 11 – зубчатые диски; 12 – палец; 13 – дозатор; 14 – шарикоподшипниковый вал.
Дозатор действует следующим образом Вертикальный вал 2 бегунов вращает надетую на него обойму 8 с зубьями 4 приводящими во вращение подвесной вал б передаточного механизма и вместе с ним звездочки 8 соединенные цепями Галля с зубчатыми венцами 10 периодически включающими во вращение валы дозатора и разгрузочного устройства.
Цепь Галля вращает свободно насаженный на вал зубчатый венец 10 до того момента пока палец 12 цепи не зацепит боковых зубчатых дисков 11. С этого момента вал дозатора или разгрузочного устройства получает вращение производящее операции загрузки и разгрузки массы.
Дозаторы расположены под бункером загружающим массой цилиндры дозаторов через отверстия в верхнем диске 1 в то время как сплошная плоскость нижнего диска закрывает выпускные отверстия цилиндров.
Разгрузка дозатора происходит в тот момент когда отверстия нижнего диска совпадают с выпускными отверстиями цилиндров дозатора причем в этот момент верхние отверстия цилиндров закрыты сплошной плоскостью верхнего диска.
Разгрузочное устройство действует следующим образом. Вал 19 получая периодически вращение от главного вала бегунов передает его через конический сектор 18 и поочередно взаимодействующие с ним конические шестерни 17 и 17 на вал 1б несущий зубчатки 21 двигающие вверх или вниз рейки 20 скребка. фиксирование верхнего и нижнего положений скребка необходимое в виду большого веса последнего происходит помощью тормозного устройства состоящего из храповика 22 и дискового сектора 28 действующего при сцеплении зубьев конического сектора 18 с конической шестерней 17. До начала сцепления конического сектора с шестерней 17 дисковый сектор 23 нажимая на собачку 24 храповика освобождает от торможения конические шестерни сидящие на валу 16.
Целью изобретения является совершенство устройства дозировки и разгрузки материала выполненное с помощью применения дозаторов и разгрузочного устройства автоматически приводимых в действие от главного вала при помощи цепной передачи обеспечивающей периодическое расцепление ведомого зубчатого колеса и несущего его вала [9].
3 Сущность модернизации
Сущность данной модернизации заключается в использовании устройства подготовки пресс-порошка которое содержит тарельчатый питатель с бункером [9]. Привод тарели выполнен в виде электродвигателя и зубчатой передачи. Выходное колесо зубчатой передачи жестко связано с тыльной диаметральной плоскостью тарели а осевым отверстием жестко установлено на вертикальную ось вращения катков.
Рис 2.16 Общий вид модернизируемого устройства:
– тарельчатый питатель; 2 – бункер; 3 – направляющий патрубок; 4 – вращающаяся тарель; 5 – сбрасывающие ножи; 6 – бегуны; 11 – электродвигатель; 13 – конусная течка.
Рис 2.17 Разрез А-А устройства:
– перфорированная чаша; 8 – катки; 9 – скребки; 10 – тросовые щетки.
Рис 2.18 разрез Б-Б устройства:
– направляющий патрубок; 4 – вращающаяся тарель; 5 – сбрасывающие ножи; 7 – перфорированная чаша; 8 – катки; 11 – электродвигатель; 12 – зубчатая передача.
Работа модернизированных бегунов мокрого помола осуществляется по следующему принципу: Включением электродвигателя 11 одновременно приводятся в движение посредством зубчатой передачи 12 тарель 4 тарельчатого питателя 1 и бегуны 6. Пресс-порошок из бункера 2 через направляющий патрубок 3 поступает на вращающуюся тарель 4 питателя 1 сбрасывается двумя ножами 5 на неподвижную перфорированную чашу 7 разравнивается двумя скребками 9 растирается и продавливается двумя катками 8 через отверстия перфорированной чаши 7 в конусную течку 13 и далее подается по ленточному транспортеру в пресс для прессования кирпича. Пресс-порошок поступает в чашу в два потока одновременно под каждый каток. Застрявшие в отверстиях перфорации гранулы из пресс-порошка проталкиваются закрепленными на кронштейнах и перемещающимися вместе с катками тросовыми щетками 10. Количество подаваемого материала в бегуны регулируется скоростью вращения тарели 4 высотой подъема направляющего патрубка 3 и положением сбрасывающих ножей 5.
Техническим результатом данной модернизации является использование устройства подготовки пресс порошка данное устройство позволяет осуществлять вылежку растирание точную дозировку и крупную грануляцию сырья чем достигается высокая степень его обезвоздушивания и повышение качества готового изделия [9].
Недостатком описываемого изобретения является использование дополнительного электродвигателя вследствие чего увеличивается энергопотребление и удельная металлоёмкость конструкции так-же увеличиваются габаритные размеры бегунов. К достоинствам можно отнести простоту и дешевизну модернизации и незначительное усложнение конструкции.
4 Расчет основных параметров бегунов мокрого помола
4.1 Расчет производительности бегунов
Исходные данные необходимые для расчета производительности и потребляемой мощности бегунов: Ширина катков: 350мм; диаметр катка: 1200мм; диаметр чаши: 2368мм.
Расчёт производительности:
n – число оборотов чаши бегунов обсек.
ρ – плотность материала (7700 кгм3).
Расчёт объема катка:
Расчёт числа оборотов чаши бегунов:
f – коэффициент трения материала о дно чаши (для мягких пород f = 0.45);
R – средний радиус катания катков.
Для обеспечения надежности работы полученные результаты рекомендуется уменьшить на 10%. Тогда окончательно получим:
Расчёт среднего радиуса катания катков:
Учитывая что материал в бегунах уплотняется под катками и следовательно появляется общая связность массы радиус круга катания рекомендуется принимать равным радиусу средней точки внутреннего катка (по его ширине).
R1 R2 – радиус катания первого и второго катков соответственно м.
4.2 Расчет потребляемой мощности бегунов
Потребляемая мощность электродвигателя определяем по формуле:
N1 – Мощность затрачиваемая на перекатывание катков Вт;
N2 – Мощность затрачиваемая на преодоление сил трения скольжения катков Вт;
N3 – Мощность затрачиваемая на скребки Вт;
– КПД привода ( = 0.75).
Расчёт мощности затрачиваемой на перекатывание катков:
k – количество катков;
G – Давление катка на дно чаши Н;
- средняя окружная скорость качения катков (принимаем радиусы качения обоих катков одинаковыми) мсек.;
R – средний радиус качения катков м;
n – число оборотов чаши бегунов обсек;
- коэффициент тяги (.
Расчёт мощности затрачиваемой на преодоление сил трения скольжения катков:
G – давление (вес) катка на дно чаши Н;
- средняя скорость скольжения мсек.
Для определения рассмотрим скорости движения различных точек катка внешней (а) внутренней (г) и средней (б) (см. рис. 3 в). Скорости указанных точек будут равны:
Средняя точка катка катится без скольжения все остальные точки со скольжением тем большим чем дальше они находятся от средней плоскости катка. Разность между скоростями точек а б г определяет величину максимального скольжения:
b – ширина катка м.
Абсолютная величина скольжения тем больше чем шире каток. Следовательно с увеличением ширины катка истирающая способность бегунов повышается.
Расчёт мощности расходуемой скребками:
P` - сила нажима скребков на тарель (Р` = 1000Н);
f1 – коэффициент трения скребка о тарель (f1 = 0.2).
5 Прочностные и проверочные расчеты отдельных деталей и узлов машины
5.1 Прочностные расчёты шпонки
Для выполнения условия при котором не будет происходить среза шпоночного соединения необходимо обеспечить выполнение следующего условия:
Расчёт шпоночного соединения на срез:
– предельно допустимое напряжение возникающее при срезе Мпа;
Fср – предельно допустимая сила Н · мм;
Аср - площадь поверхности среза шпонки мм2.
Расчет предельно допустимого напряжения возникающего при срезе:
– фактически и допускаемое напряжение среза на рабочих гранях шпонки Мпа.
Расчёт предельно допустимой силы:
Т - передаваемый крутящий момент Н. мм.
Расчёт передаваемого крутящего момента:
N - мощность электродвигателя кВт;
n - номинальная частота вращения электродвигателя мин-1.
Расчёт площади поверхности среза шпонки:
dв – диаметр вала мм;
b – ширина шпонки мм;
lр – рабочая длина шпонки мм.
Расчёт рабочей длины шпонки со скругленными торцами:
l – длина шпонки мм.
В соответствии с ГОСТ 6636 – 69 выберем призматическую шпонку со скругленными гранями с длиной 100мм. шириной 36мм. высотой 22мм. изготовленной из стали Ст45. Данная шпонка соответствует условиям прочности.
5.2 Расчет подшипников на долговечность
Номинальная долговечность это число циклов (или часов) которые подшипник должен проработать до появления признаков усталости.
Расчёт долговечности подшипника по количеству оборотов:
C – динамическая грузоподъемность подшипника по каталогу Н;
P – эквивалентная нагрузка Н;
ρ – показатель степени (для шарикоподшипников ρ = 3 для роликоподшипников ρ = 033).
Расчёт долговечности подшипника в часах:
n – частота вращения вала.
Расчёт эквивалентной нагрузки:
V – коэффициент вращения кольца (при вращении внутреннего кольца V = 1 при вращении наружного V = 13);
X – табличное значение для подшипников (X = 056);
Fr – радиальная нагрузка Н;
Kb Kt – табличное значение для подшипников (Kb = 1.1 1.5; Kt = 1).
Исходя из значений расчётов выберем подшипник средней серии №7313А с внутренним диаметром 140мм с максимальной динамической нагрузкой 183000Н.
Так как Lh = 17143 часов > 10000 часов следовательно данный подшипник удовлетворяет показателям долговечности.
5.3 Расчет вертикального вала бегунов
Валы обычной конструкции если она установлены на подшипниках качения рассчитывают как балки на шарнирных опорах.
Материал вала сталь 45 n = 610 Нмм и т = 360 Нмм.
Расчёт передаваемого момента:
N – мощность на валу кВт;
– угловая скорость радс.
Расчёт мощности на валу:
Nдв – Мощность электродвигателя кВт;
– КПД редуктора и передачи соответственно.
Расчет угловой скорости:
n – частота вращения вертикального вала обмин.
Расчет окружного усилия в зацеплении:
dср – средний делительный диаметр колеса
Расчет среднего делительного диаметра колеса:
b – длина зуба колеса;
- половина угла при вершинах начальных конусов.
Расчет длины образующей делительности конуса:
- половина угла при вершине начальных конусов.
Расчет радиального усилия в зацеплении:
α – угол зацепления (α = 20 о).
Расчет осевого усилия в зацеплении:
Расчет опорных реакций в вертикальной плоскости:
Расстояние от нижней опоры до колеса b = 200 мм от верхней опоры до приложения силы равно d = 310 мм. Расстояние между опорами l = 700 мм.
Рассчитаем сумму моментов в точке B:
Рассчитаем сумму моментов в точке A:
Рассчитаем изгибающий момент в вертикальной плоскости:
Рассчитаем опорные реакции в горизонтальной плоскости:
Рассчитаем изгибающий момент в горизонтальной плоскости:
Рассчитаем суммарный изгибающий момент в критической точке сечения:
Рассчитаем эквивалентный момент:
Рассчитаем диаметр вала под механизм:
В соответствии с ГОСТ 6636-69 примем диаметр вала d=150мм.
Рассчитаем диаметр вала под колесо:
В соответствии с ГОСТ 6636-69 примем диаметр вала под колесо d=130мм.
Рассчитаем предел выносливости для вала при изгибе:
Рассчитаем предел выносливости для вала при кручении:
Рассчитаем нормальные напряжения сечения под шестеренкой:
W – момент сопротивления м3.
Рассчитаем момент сопротивления для сечения с канавкой для шпонки:
Для вала d=150мм по ГОСТ 8788-68 ширину выточки примем b=36мм и глубину канавки t=12мм.
Для вала d=130мм по ГОСТ 8788-68 ширину выточки примем b=32мм глубину канавки t=11мм.
Рассчитаем касательные напряжения от нулевого цикла для сечения под колесо и механизмом обработки асбеста:
Wk – момент сопротивления при кручении м3.
Рассчитаем момент сопротивления при кручении:
Коэффициенты напряжений шпоночных канавок для стали 45 с пределом прочности 100 Нмм2: = 175; = 15.
Коэффицент учитывающий влияние постоянной составляющей цикла на усталостную прочность для среднеуглеродистых сталей: = 02; = 01.
Масштабные факторы для вала
d1 = 150 мм d2 = 130 мм
Рассчитаем запас прочности по нормальным напряжениям -1:
Рассчитаем коэффициент запаса прочности по касательным напряжениям:
Рассчитаем общий коэффициент прочности:
[n] – коэффициент прочности ([n] = 13 15).
Так как n1 и n2 ≥ [n] следовательно прочность вала обеспечена.
В ходе работы над данным курсовым проектом была изучена технологическая схема по производству асбестоцементных изделий конструкция и принцип работы бегунов СМ-21Б производительностью до 10 тч.
На основании анализа четырех патентов была выбрана модернизации описанная в разделе 2.3 за счет которой удается уменьшения времени активирования твердеющей смеси а так же дозировать попадающий на измельчение материал. В разделах 2.4 и 2.5 были проведены расчеты по определению конструктивных и прочностных параметров машины таких как: энергопотребление производительность расчет шпонки и подшипников а так же вертикального вала.
М.Т. Макридина Н. Н. Дубинин. Методические указания к проведению учебной практики для студентов специальности 270101 – Механическое оборудование и технологические комплексы предприятий строительных материалов изделий и конструкций Белгород: изд-во БГТУ 2010. – 96с.
Н.П. Несмеянов Ю.В. Бражник Е.Б. Александрова . Учебное пособие для выполнения лабораторных работ студентами направления бакалавриата 15.03.02 – Технологические машины и оборудование - Механическое оборудование (общий курс): лабораторный практикум Белгород: Изд-во БГТУ 2017. — 100 с.
В.А. Бауман Б.В. Клушанцев В.Д. Мартынов . Механическое оборудование предприятий строительных материалов изделий и конструкций Издательство: Машиностроение 1981г. - 327 с.
З. Г. Гиберов М. Я. Сапожников С. Г. Силенок ; под ред. М. Я. Сапожникова. Механическое оборудование предприятий строительных материалов. Атлас конструкций : учеб. пособие М. : Машиностроение 1978. - 112 с.
Н.П. Несмеянов Ю.В. Бражник Горшков П.С. Механическое оборудование (общий курс). Курсовое проектирование: учебное пособие Белгород: изд-во БГТУ 2017. – 99с.
М. Я. Сапожников Н. Е. Дроздов. Справочник по оборудованию заводов строительных материалов: справочное издание М : Стройиздат 1970. - 487 с.
М. Я. Сапожников. - М. : Машгиз Механическое оборудование для производства строительных материалов и изделий учебник 1962. - 522 с.
Реестр патентов [Электронный ресурс]
Деталировка А1.dwg

КП ПМО-08 054 010000 СБ
- размеры для справок
Неуказанные предельные отклонения: валов по h15 остальные ±js T2
Неуказанные предельные отклонения: отверстий по h15 остальные ±js T2
БГТУ им. В.Г. Шухова гр. МО-32
Неуказанные предельные отклонения: отверстий по H15 остальные ±js T2
Узел А1.dwg
