Two-story residential building of manor type


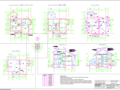
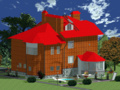
- Added: 20.02.2021
- Size: 16 MB
- Downloads: 1
Description
We design a two-story residential one-apartment building with a basement and a built-in garage.
According to the conclusion of engineering and geological conditions, medium-strength limestone lies at the base of the foundations, tiled, fractured with layers of wood soil, watered from a depth of 3.9 m. Design resistance = 90kg/cm2. The waters are pressure-free, non-aggressive.
Climatic indicators for the construction area:
Climatic area: B. Temperatura of the coldest five-day week security 0.92: t of N =-26 wasps. Design temperature of internal air: t in = 20 wasps. Relative humidity: 60%. The humidity mode of the rooms is normal. The average temperature of the period with an average daily temperature of vozdukha≤ 8 ° C is 4.2 ° C. The duration of the period with an average daily air temperature of ≤ 8 ° C is 202 days .
Project's Content
![]() |
![]() |
![]() |
![]() ![]() ![]() |
![]() ![]() ![]() |
![]() ![]() ![]() |
![]() |
![]() ![]() ![]() ![]() |
![]() ![]() ![]() |
![]() ![]() ![]() |
![]() ![]() ![]() |
![]() ![]() ![]() |
![]() |
![]() |
![]() |
![]() ![]() ![]() ![]() |
![]() |
![]() ![]() ![]() |
![]() ![]() ![]() |
![]() ![]() ![]() ![]() |
![]() ![]() ![]() |
![]() |
![]() ![]() ![]() |
![]() |
![]() ![]() ![]() |
![]() |
![]() ![]() |
![]() ![]() ![]() |
![]() ![]() ![]() |
![]() |
![]() ![]() ![]() |
![]() |
![]() ![]() ![]() |
![]() ![]() ![]() |
![]() ![]() ![]() |
![]() ![]() ![]() |
![]() ![]() ![]() |
Additional information
Contents
Contents
Architectural part
Source Data
General Plan Solution
Architectural and construction solution
Space Planning Solution
Technical and economic indicators
Interior and exterior finishes
Structural solution of the building
Heat Engineering Calculation
Fire fighting measures
Engineering equipment
Rendered Drawings in Perspective
Literature used
Structural part
Introduction
Calculation and Design of Multi-Stop Railway Plate
Grid Calculation
Calculation of rafter leg
Calculation of diagonal rafter leg
Rack calculation
Literature used
Organizational and technical part
Contents
Definition of construction period
Define Scope of Work
Stroygenplan
List of used literature
Process Part
Introduction
Technical map for masonry and installation works
Organization and technology of main construction works
Logistical resources
Statement of labour costs and wages
Selection of installation methods and installation cranes
Production Process Schedule
Quality control during stone installation works
Safety precautions during stone installation works
Technical map for roofing works
Organization and technology of main construction works
Logistical resources
Statement of labour costs and wages
Production Process Schedule
Quality control during roofing works
Safety precautions during roofing works
List of used literature
Source Data
We design a two-story residential one-apartment building with a basement and a built-in garage.
The geographical area of construction is the Leningrad region.
According to the conclusion of engineering and geological conditions, medium-strength limestone lies at the base of the foundations, tiled, fractured with layers of wood soil, watered from a depth of 3.9 m. Design resistance = 90kg/cm2. The waters are pressurized, non-aggressive.
Climatic indicators for the construction area:
Climatic area: B. Temperatura of the coldest five-day week security 0.92: t of N = 26 wasps. Design temperature of internal air: t in = 20 wasps. Relative humidity: 60%. The humidity mode of the rooms is normal. The average temperature of the period with an average daily temperature of vozdukha≤ 8 ° C is 4.2 ° C. The duration of the period with an average daily air temperature of ≤ 8 ° C is 202 days.
Accepted design temperatures in rooms:
The living room - 18 (20) wasps .
Kitchen - 18 wasps .
The joint room of the bathroom and the bathroom - 25 wasps.
Corridor - 16 wasps.
Standard value of wind pressure 0.27 kPa
Standard value of snow cover 100 kg/sq.m.
Degree of durability: II
Building class: II
Fire resistance rating: II
Standard depth of ground freezing: 1.36 m
The relief is calm.
Master Plan
Volume and planning parameters:
• area of the site - 2944.5 sq.m.
• building area - 196.25 sq.m.
• landscaping area - 1923.14 sq.m.
The master plan for a two-story residential building was developed in accordance with the requirements of SNiP 2.07.0189 "Urban planning. Planning and development of cities and rural settlements, "with a design assignment and other initial data. The construction site is constrained by a forest band on two sides.
Are provided by the general plan: an entrance to the house from existing before the road, walking paths of free planning the covered with stone blocks, decorative pool, a garden, a kitchen garden, greenhouses, a bath, warehouse, recreation areas. It is proposed to shield the site of the general plan with a fence, in places made of silicate blocks, in places from a metal grille.
Covering the passage to the garage and parking lot - paving stones with a heating system to prevent the formation of snow embankments in the winter .
The coverage of footpaths is paving stone.
Landscaping provides for the construction of flower beds and the construction of lawn in recreation areas and areas free from any buildings and footpaths. Shrubs and trees enclosing recreation areas shall be planted along the perimeter of the site in accordance with the general plan. To the right of the facade is planned the location of a fruit and berry garden. To create a border between the site and the external volume, along the fence, a strip of densely growing shrub is provided.
Technical solutions adopted in the working drawings comply with the requirements of environmental, fire safety regulations in force on the territory of the Russian Federation and ensure safe operation of the facility for life and health of people.
Architectural and construction solution
Space-planning solution.
The house is designed for settlement by one family in the amount of 3-6 people and has 4 residential rooms. The dimensions of the building in the axes are 13200 X 13800 meters. The planning structure of the house is based on the principle of functional zoning of premises with their placement in various levels.
The entrance to the residential part of the house is organized through cold canopies with stairs. The first level rooms are designed to meet guests and consist of a comfortable front with a corner for relaxation, built-in cabinets and a bathroom. On the second level are the kitchen and dining room. On the third level there is a living room with a fireplace and an office, on the fourth - bedrooms and a hall with access to the loggia. The upper level with a pantry has access to the attic. All levels are combined by an intraquarter ladder that starts from the front. The second apartment staircase leads from the kitchen level and the dining room to the basement with pantries, boiler room and workshop. From the intermediate platform of the staircase, access to the veranda and, further, to the house section is organized.
The garage for one passenger car and sauna are designed in the total volume of the house, are built-in.
The height of the floor of the premises in the residential part is 2500 mm, in the front - 3100 mm, in the office - 2800, in the sauna and garage - 2600, in the living room - 3000 mm. An erker is designed in the house, forming the living room space and rest rooms at the sauna.
The house has an attic with access to the roof through a dormer window.
Technical and economic indicators.
The building area is 196.25 sq.m.
Useful area - 529.87 sq.m.
Construction volume - 1530.76 cubic meters.
More detailed areas of the premises are indicated below in the room decoration list.
Building engineering equipment
The water supply system is local, produced from the well by a water pump. The entire hot water wiring and heating system is carried out in a boiler house located in the basement (see basement plan). The universal double-circuit boiler CTC 1100 Maxi (77kW;18kW electric pipes) of liquid fuel B20 is used as a heat source for hot water supply and heating systems. Steel panel radiators "HENRAD" are used as heating devices. All pipelines are made of HENCO metal plastic pipes. Coolant in the heating system - low-freezing liquid "Argushatdip" with temperatures: supply line + 85 ° C, reverse - + 70 ° C, in the floor heating system, respectively: + 60 ° C - + 50 ° C. The system diagram allows automatic differential temperature adjustment and maintenance by means of "HERZ" thermostats installed in each main room, as well as general programming of the temperature mode of the building using an electronic boiler controller. The system is closed, with forced circulation.
The system provides for the possibility of filling through the drain valve on the boiler and makeup from the water supply (at the same time, the possibility of ingress of liquid from the system into the water supply system is automatically excluded). Wiring is done in a tree diagram (with a decrease in pipe diameters during successive branches). Lower feed to radiators is applied. Horizontal pipe runs are laid in the floor structure. Vertical and inclined sections of pipelines are laid in the wall structure (in bars) or along the walls (in this case, the pipe must be fixed on the wall using retainers located at a distance of 0.4 - 1.0 m depending on the diameter and location of the pipe).
Recommended installation sequence:
Floor preparation in rooms heated by the floor (finishing ties with a tolerance of not more than ± 5mm).
Preparation of niches for distribution cabinets, fines and holes in wall and floor structures.
Assembly of radiators .
Assembly of distribution manifolds.
Installation of distribution cabinets, laying of central mains.
Installation of radiators, installation of distribution headers in cabinets .
Laying and connection of radiator heating branches.
Installation of remote floor heating sensors.
Installation and connection of heating planes.
Installation and connection of heating boiler .
Fill and start the system.
Leak check and system adjustment (air removal, manual adjustment).
Disconnection of the system and filling of ties of heating planes (at that coils must be cold and under pressure).
Installation of thermal heads on radiators (preferably after finishing of rooms).
Technical requirements:
For horizontal sections of pipelines, bends ("waves") convex upwards (to avoid air loss) are not allowed.
Horizontal sections of supply to coils of heating planes of floor must be located at the level of coils themselves.
Each coil must be made of one pipe cut without joints.
Maximum permissible bending radius of pipes is not less than 5 diameters (when using bending springs - not less than 3). For H026 pipes the corresponding numbers are 8 and 4.
The heating plane contour shall envelope the projecting sewer pipes attached to the "black" floor of the plumbing support, etc.
The capillary tubes of the remote temperature sensors shall be insulated from heat sources (piping, heating planes, etc.).
At intersections with walls and floors, piping shall be protected by corrugated plastic pipe.
Piping areas laid in cold floors (basement floors, floors above non-heated rooms, etc.) and passing through non-heated rooms shall be insulated to avoid excessive heat loss. Particularly important areas are further indicated on the diagrams.
It is also necessary to insulate the central lines connecting the heating boiler with the distribution cabinets .
The lower floor distribution manifolds shall be located above the level of the circulation pump. Reverse slope of pipelines in the boiler section - distributors is not allowed.
The sewerage system is gravity, local, developed for a group of several neighboring estates. Waste water coming from the premises (toilets, showers) is household and before discharge is purified biologically in the filter located behind the site of the plot plan. Pipes from PVC TU 61930786 with a diameter of 50200mm are used for water removal.
The watershed is external.
Ventilation is natural.
Power supply - from the external network, is carried out from an underground electric cable located at a depth of 3 m. Voltage from the cable is supplied to the electric panel. Mains voltage 380/220 V.
Lighting - filament lamps and fluorescent lamps, depending on the purpose of the room and natural light.
Communication device - radio, telephony, satellite body network. Telephone communication, security and fire alarms are carried out through devices installed by the relevant services and connected to the city telephone network. Fire alarm sensors are installed in each room from 1 to 6 pieces depending on the area. Alarm sensors are installed on windows and doors.
Sun appliances - there is a shower, toilet, bath, washbasin in bathrooms.
Rain water is drained from the territory along the natural slope in the direction of the storm sewage collector.
Calculation of technical and economic indicators for the construction of a single-storey residential building made of brick
The estimated cost of the facility is 2874454.2 rubles.
Estimated cost of construction works - 1039328.11 rub.
Labor intensity of performed works - 322 people-days
Production per person per day - 8926.27 rubles.
Building volume 1530 m3
The estimated cost of 1m3 of the building volume is 1878.71 rubles.
Estimated cost 1msq. the total area of the building is 14466.31 rubles.
Standard construction duration 133 days
Construction duration 121 days
Reduced construction time of 12 days
Designing the Task List for the Masonry Assembly Process
1. Organization and technology of basic construction works.
Prior to brickwork, the following works shall be performed:
◦ Access roads, temporary roads and storage areas are arranged;
◦ crane provided;
◦ construction materials imported and laid;
◦podgotovleny and mechanization tools, equipment and accessories are submitted to workplaces in accordance with the work organization scheme;
◦ Zero cycle work completed;
◦ laying axes on the foundation;
◦ elevations of the first row of brickwork are taken out;
◦ mortar, brick are supplied to workplaces in accordance with the organization scheme of workplaces.
Process sequence of brickwork maintenance:
◦ separation of axes and marking of walls, setting of order and tensioning of berth;
◦ feeding and laying bricks on the wall;
◦ supply, dilution and leveling of the solution;
◦ laying brick on the "bed" of mortar;
◦ verification of masonry correctness ;
◦ stitching and grout cutting;
◦rubka and the text of bricks (if necessary).
The production of brickwork using the norm complex is rational with the links "two" and "three."
To conduct stone and related work, the building is divided into two grabs. When assigning gripping boundaries, it is taken into account that the volumes of stone work on each gripping should be approximately the same and their boundaries were linked to the location of lifting mechanisms.
Quality Control
Quality of brickwork shall meet the requirements set out in SNiP 3.03.0187 "Load-bearing and enclosing structures."
Quality control begins with the acceptance of the delivered prefabricated elements. All of them shall conform in appearance and dimensions to the design requirements and shall not have deviations exceeding those permitted by SNiP.
Acceptance of completed stone structures shall be accompanied by inspection of:
◦ correctness of dressing, filling and thickness of joints, vertical, horizontal and straightforward surfaces and masonry units;
◦ correctness of smoke and ventilation channels;
◦ availability of installed embedded parts - links and anchors for the project;
◦ provision of surface water removal from the building and protection of basements and foundations from them.
The main criterion for the quality of installation work is welding and sealing of joints, as well as the accuracy of installation of structures.
During stone works vertical surfaces of walls and corners, thickness of seams filling with mortar are checked.
Acceptance of completed stone structures shall be accompanied by inspection of :
◦ correctness of dressing, filling and thickness of seams, verticality, horizontal and straightforward surfaces and masonry units;
◦ correctness of smoke and ventilation channels;
◦ availability of installed embedded parts - links and anchors for the project;
◦ provision of surface water removal from the building and protection against them.
For cases of acceptance of stone works to be built in winter, the work log must reflect the conditions of construction and maintenance of the structure, for which daily it should be noted:
◦ ambient air temperature during the works execution period;
◦ presence of precipitation;
◦ solution temperature at the moment of laying;
◦ types and grades of used solutions;
◦ amount of additives introduced into the solution.
The quality of materials, semi-finished products and products of factory manufacture used in stone structures must meet the certificates and certificates of manufacturers, as well as the data of control laboratory tests carried out by construction organizations.
The quality of the elements is checked several times: in the warehouse, during installation, sealing the joints and after final fixation. Upon completion of installation, all works are accepted according to the certificate, which indicates whether they are installed in accordance with the design, determine the quality of installation work and issue a conclusion on the readiness of the building .
The following documentation shall be provided during acceptance inspection:
◦ as-built drawings with deviations (if any) approved by the structural manufacturer, as well as installation organization, agreed with the design organizations-developers of the drawings, and documents on their approval;
◦ factory technical certificates for steel, reinforced concrete and wooden structures;
◦ documents (certificates, passports) certifying the quality of materials used in construction and installation works;
◦ Acts of examination of hidden works;
◦ acts of intermediate acceptance of critical structures ;
◦ as-built geodetic diagrams of structures position;
◦ work logs;
◦ documents on quality control of welded joints;
◦ Acts of structural testing (if the tests are provided for by additional regulations of these codes and regulations or working drawings);
◦ other documents specified in additional rules or detailed drawings.
3D модель без благоустройства.dwg

Генплан.dwg

Готовая 3D модель.dwg

готово для рендеринга 1.dwg

готово для рендеринга 2.dwg

Подрамник.dwg

Рисуночки для пояснилки.dwg

Similar materials
- 07.12.2021
Free downloading for today
- 22.08.2014
- 29.08.2014