Trench multifunctional rink - Diploma project


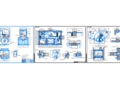

- Added: 16.10.2021
- Size: 6 MB
- Downloads: 5
Description
Engineering Specification
The terms of reference shall be prepared in accordance with the requirements and on the basis of GOST 15.001-88 standard. [10]
1. Name and scope:
Name: trench multi-functional roller
Application: layer-by-layer soil compaction.
2. Basis for development from the Department of TST:
The need to design a trench roller and create a fundamental new working equipment for leveling the ground.
3. Purpose and purpose of development:
The idea proposed in the project for development will increase the level of soil compaction.
4. Development Sources:
- https://www.manualsdir.com/manuals/568560/multiquip-p33_24-hhm_hhmr_hhmr-bd.html?page=7
- https://patents.google.com/patent/US10047500B2/en
5. Technical requirements:
For a multifunctional trench rink:
- drive - hydrostatic;
- control of the trench rink - remote;
- number of hydraulic cylinders - 2;
- number of rollers - 2 cam rollers;
- number of scrapers - 4 on each side
- central connection of roller - articulated with oscillation angle not more than 7;
- remote control principle - through infrared signals
- location of eccentrics - are located below the central axis. Three operating modes shall be allowed:
- rolling without vibration;
- activation of one roller;
- activation of two rollers;
- engine - two-cylinder four-stroke diesel engine with air cooling;
- dump lifting height - 76 mm;
- overall dimensions (DHSHKHV) - 1796x880x1273 mm;
- length of machine with dump - 2046 mm;
- technical characteristics - take from the prototype trench rink Rammax 1575;
For dump of multifunctional trench rink:
- dump control - remote;
- dump drive - hydraulic;
- speed of movement - up to 1.2 km/h;
- dump height relative to ground at maximum lifting - 100 mm;
- width and height of external welded box - 117x394 mm;
- width and height of inner welded box - 73x312 mm;
- number of hydraulic cylinders - 1;
- total number of sliding plates - 13;
- Overall dimensions of a dump (SHKHVKHG) - 880х331х46 mm;
Select the remaining parameters structurally based on the design part of the work.
6. Ergonomic indicators:
To ensure smooth operation of the operator from the remote panel, to ensure safe operation, the levers of the control panel should be conveniently laid in the hand, repeating the shape of the palm fold; ensure compliance with all norms and rules such as SanPiN, SNiP, as well as GOST, GOST-R, OST standards, etc.
7. Economic indicators:
Presumably, such a dump installation will cost no more than 100 thousand rubles. In the future, the production of components and wages of workers will be calculated and the final development cost will be concluded.
Project's Content
![]() ![]() ![]() |
![]() |
![]() |
![]() ![]() ![]() ![]() |
![]() ![]() ![]() ![]() |
![]() ![]() ![]() ![]() |
![]() ![]() ![]() ![]() |
![]() ![]() ![]() ![]() |
![]() ![]() ![]() ![]() |
![]() |
![]() ![]() ![]() ![]() |
Additional information
Contents
Introduction
1. Analytical part
1.1 Organization and procedure of backfilling of trenches
1.2 Analysis of Modern Compaction Methods and Process
1.3 Analysis of modern structures of machinery and equipment for works
1.4. Existing patents and inventions
1.5. Engineering Specification
1.6. Technical proposal and idea of work
2. Design part
2.1.1 Determination of trench roller parameters
2.1.2 Determination of soil digging resistance
2.1.3 Operational capacity
2.1.4 Energy intensity of soil displacement development process
2.1.5 Selection of hydraulic cylinder
2.2 Calculation of movement mechanism of cam trench roller
2.2.1 Calculation of basic parameters of vibration system
2.2.2 Calculation of hydraulic running motor
2.2.3 Traction calculation
2.2.4 Power balance
3. Strength and Stability Calculations
3.1.1 Calculation of strength of suspension parts of guide roller
3.1.2 Calculation of unbalance of trench roller
3.1.3 Check of shaft strength and stiffness at forced oscillations
3.1.4 Calculation of longitudinal stability of the roller according to the tilting condition
3.1.5 Calculation of longitudinal stability of the roller according to the condition of clutch provision
3.1.6 Calculation of roll lateral stability
4. Calculation of trench roller hydraulic system with front dump
4.1 Calculation of hydraulic drive power
4.2 Calculation of main parameters of hydraulic system
4.3 Calculation of the first section of hydraulic system
4.4 Calculation of the second section of hydraulic system
4.5 Calculation of the third section of hydraulic system
4.6 Calculation of hydraulic system fourth section
4.7 Calculation of hydraulic system fifth section
5 Part Manufacturing Process
5.1 Selection of developed part and description of its purpose
5.2 Development of route single prospective process
5.3 Route Description
5.4 Technical Specification of NC Turning and Milling Machine Takisawa TMM 250 module-
6. Project business case
6.1 Calculation of unit cost
6.1.1 Calculation of Component Cost
6.1.2 Calculation of component parts cost
6.1.3 Calculation of wage costs for workers
6.1.4 Calculation of additional wage costs for workers
6.1.5 Calculation of social contributions
6.1.6 Calculation of equipment design costs
6.1.7 Calculation of cost of development works
6.2 Procedure for calculation of article-by-article parameters of machine operation costs
6.2.1 Depreciation charges for full recovery
6.2.2 Repair and maintenance costs
6.2.3 Replacement Costs for Quick Wearing Parts
6.2.4 Remuneration of workers operating the machine
6.2.5 Energy Costs
6.2.7 Hydraulic Fluid Costs
6.2.8 Cost of relocation from one construction site (mechanization base) to another construction site (mechanization base)
7. Technical device safety
7.1 Analysis of harmful factors during works
7.2 Noise pollution and calculation of noise protection
7.3 Emergency Safety Requirements
8. Environmental expertise of production equipment and technologies
8.1 General provisions and regulated documentation
8.2 Potential problems of environmental pollution by the designed machine
8.3 Characteristics of the compaction process
8.4 Atmospheric Air Impact Assessment
8.5 Water Impact Assessment
8.6 Soil Impact Assessment. Waste generation
8.7 Physical contamination
8.8 Measures to reduce pollution
8.9 Conclusion on Environmental Expertise
Conclusion
List of literature
Summary
In this diploma project, the existing methods of compaction of various types of soils were studied, the technical means and equipment used for this type of work were studied. Patents and inventions in this field have been considered. Design options and technical proposal were presented, one of the options was chosen. Technical assignment for design has been drawn up. The machine was calculated according to the main parameters, components were selected. The stability of the machine was calculated during operation, some parts were tested for strength. One part manufacturing routing has been compiled. The project was economically justified, checked for compliance with safety and environmental requirements.
The diploma project contains 144 sheets of explanatory note, 40 - drawings, 20 - tables, 33 - sources used. Attached are 10 A1 drawings and 1 A2 drawing.
KEYWORDS: MACHINE, RAMMING, TRENCH MULTIFUNCTIONAL ROLLER, SEAL, FRONT DUMP, SOIL, ARTICULATED JOINT.
Object of development: Trench multi-functional rink.
The purpose of the work: to design an absolutely new trench multifunctional roller with an additional adjustable hydraulic dump, which before compaction will level the bulk soil.
The result of the work: a trench multifunctional rink with a frontal hydraulically adjustable dump was developed, all component machines were selected and calculated.
Introduction
Vibration rollers, like static ones, are used in the production of repair and construction road works. The main difference between vibration rollers is the presence of an integrated vibrator in one of the rollers (driving or driven), which achieves a significant increase in the efficiency and quality of coating compaction. With the vibrator turned off, such rollers can work like ordinary static ones.
Vibration rollers with smooth rollers in recent years have been increasingly used in compacting gravel, gravel and asphalt concrete mixtures. Vibration self-propelled rollers in comparison with static rollers have lower metal consumption, are more maneuverable and transportable, when properly organized, they provide the required density and evenness of the surface of sealed materials. Self-propelled vibration rollers for compaction of road surfaces are manufactured mainly by two-roller biaxial rollers. In vibratory two-roll rollers, either or both of the rollers may be vibratory.
With a driving vibrating roller, the conditional coefficients of friction and its adhesion to the surface of movement are sharply reduced, which reduces the traction force along the grip and makes it difficult to move on slopes.
If the vibrator is a driven roller roller, control of the roller becomes difficult. Another significant disadvantage of vibrating rollers is the difficulty of providing reliable and durable operator protection against the harmful effects of vibration. To a large extent, these disadvantages are eliminated in vibrating rollers with two vibrators, which operate in opposite phases and are both driving and controlled. When designing vibration rolls, it is desirable to provide a change in the disturbing force for use in the most advantageous operation modes when compacting various materials.
Analytical part
1.1 Organization and procedure of backfilling of trenches
Prior to the start of excavation works for filling trenches, organizational and preparatory measures shall be performed in accordance with SNiP 12012004 "Construction Organization" and SNiP 3.02.0187 "Earthworks, Foundations and Foundations," as well as all works in accordance with the construction plan developed as part of the work execution project for each specific case, i.e. installation of pipelines, cable, etc.
The works considered by the Job Instruction include:
- filling and compaction of soil in pits for butt joints of pipelines (if necessary);
- relocation of soil by bulldozers, up to 10 m with backfilling of the trench;
- filling of soil into trench manually;
- leveling of soil manually with sinus picking between the pipe and the trench bottom;
- filling and levelling of soil with bulldozer;
Backfilling of trenches shall be carried out in accordance with the requirements of the design, which shall indicate the types and physical and mechanical characteristics of soils intended for backfilling devices and special requirements for them, the required degree of compaction (dry soil density or compaction coefficient).
In agreement with the customer and the design organization, backfill soils can be replaced if necessary. [11]
Backfills are made of clay, sandy and coarse soil. Industrial waste (slag, ash, crushed stone) can be used.
Soils of backfills are conditionally divided into connected (content of clay particles is more than 12%), low-connected (4-11%) and disconnected (less than 3%).
Selection of the type of soil for filling trenches is made depending on the location of trenches in the city territory:
- filling of trenches within the roadway with improved overhaul-type coatings shall be made of sandy or large-breaking soils;
-filling of trenches located outside the roadway (on lawns, squares) is carried out by soils taken out of trenches or other local soils (connected or little connected) that do not contain wood residues and rotting inclusions.
In the presence of these soils at the construction site, preference should be given to sandy, gravel and gravel soils.
Backfills of trenches should be made with homogeneous soils and of the same type. When using soils of different types, it is necessary to fulfill the following requirements:
-use of soils of different types in the same layer is not allowed, unless it is provided by the design;
-the surface of layers of less draining soils located under layers of more draining soils shall have a slope within 0.04-0.1 from the fill axis to the edges.
Backfilling of underground trenches with soil shall be performed directly behind laying of pipelines and network devices, taking measures against their displacement along the axis and against damage of pipelines and their insulation. [2]
Project business case
6.1 Calculation of unit cost
6.1.1 Calculation of Component Cost
The technical proposal consists in the modernization and creation of a trench rink as well as the development of a new, additional design, which allows you to simultaneously perform two actions - compacting the trench and leveling the soil, as well as in the design of a fundamental new domestic rink.
The creation of such conditions will be determined by the working body, which is a front dump. The dump is connected through a central attachment to an inner box that is equipped with sliding plates as well as an outer welded box, due to the sheet metal guard, the soil will not fall on important units of the structure, thereby not contaminating the sliding plate.
The introduction of such a structure will result in improved sealing operations. Also, this design is economically advantageous since it contains only one hydraulic cylinder.
After the installation of the front dump with all components to the front of the trench roller is completed, the dump due to the hydraulic cylinder will be adjusted in height.
We will check the economic feasibility of creating additional working equipment.
Conclusion
Relating in its dimensions to minitechnics, a trench rink is a machine capable of qualitatively and evenly compacting the soil to a depth of one meter - in this sense, the alternative to it to this day simply does not exist. In addition, when operating below the surface of the earth, it, being equipped with a remote control system, provides complete safety to the operator who controls the trench roller remotely .
During the diploma design, a trench multifunctional rink with a frontal hydraulically adjustable dump was studied. Rink classifications and scope of their application are considered. The selection and calculation of its main parameters by analogy with the design of existing prototypes was carried out. The idea of creating and calculating a frontal dump, which is technically successful in terms of design, as well as a trench rink, was proposed. For the TMC section, a shaft was taken, which was calculated. The trench rink was also calculated according to all environmental and economic standards. The calculation of life safety has been made. The dump calculation was also checked in the APM FEM plugin of COMPAS3D .
КФБН 01.00.00.617 ВК.cdw

КФБН 02.00.00.617 ВО.cdw

КФБН 03 - 05.cdw

КФБН 06-07.cdw

КФБН 08.00.00.617 ТМС.cdw

кфбн 10.00.00.160617 Г.cdw

КФБН.02.00.00.617 Аксонометрия.cdw

Similar materials
- 30.03.2025
- 04.11.2022
- 04.11.2022