Rotary excavator










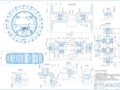
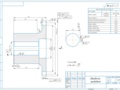
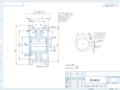
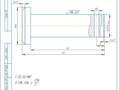

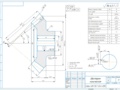
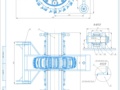
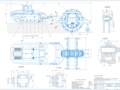
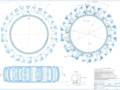
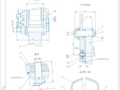
- Added: 15.05.2021
- Size: 16 MB
- Downloads: 5
Description
In the work, equipment was developed for mechanizing the process of arranging trenches. Based on the patent and literary analysis, the direction of development of the working organ of the rotary trench excavator was chosen. The design was worked out, the rotor and rotor drive parameters were calculated. A process diagram of the rotor excavator operation during the trench arrangement has been developed, a work schedule has been developed, calculations of the scope of work and the needs of auxiliary equipment have been made. The section "Automation of construction processes" introduced leveling laser control of rotor excavator operation. Maintenance and safety regulations have been developed.
Project's Content
![]() ![]() |
![]() |
![]() |
![]() |
![]() |
![]() |
![]() |
![]() |
![]() |
![]() |
![]() ![]() ![]() ![]() |
![]() ![]() ![]() ![]() |
![]() ![]() ![]() ![]() |
![]() ![]() ![]() ![]() |
![]() ![]() ![]() ![]() |
![]() ![]() ![]() ![]() |
![]() ![]() ![]() ![]() |
![]() ![]() ![]() ![]() |
![]() ![]() ![]() ![]() |
![]() ![]() ![]() ![]() |
![]() ![]() ![]() ![]() |
![]() ![]() ![]() |
![]() ![]() ![]() |
![]() ![]() ![]() ![]() |
![]() ![]() ![]() ![]() |
Additional information
Contents
Contents
Introduction
Selection and justification of the topic of graduation qualification work
Review and analysis of existing rotary excavators
Patent-literature analysis
Design Section
Select Base Machine
Calculation of rotor parameters
Calculation of rotor drive chain transmission
Calculation of taper gear train
Process Section
Types of work performed by rotary trench
excavators
Work on continuous excavators
Determination of excavation quantities
Safety precautions during operation of rotary excavator
General Safety Requirements
Responsibilities of the rotor excavator driver
Hazardous and harmful production factors
The driver is prohibited
Automation of construction processes
Purpose and tasks of machine automation
Automation of multi-tower excavators
Technical safety
Safety precautions
General characteristics of sources of hazardous and harmful factors in the production of a rotary excavator
Assessment of working area illumination
Assessment of operating area air temperature
Assessment of dust content, gas content of working area air
5.1.5. Noise Level Assessment
5.1.6 Moving parts of machines and mechanisms
5.1.7 Ensuring electrical safety during operation and maintenance of the rotor excavator
5.2 Maintenance of trench rotor excavators
5.3 Regulation of mechanisms
Conclusion
List of sources used
Introduction
Any construction and installation processes in the construction of main pipelines are carried out mainly by machines. At the same time, both general-purpose construction machines and machines created specifically for the construction of main pipelines are used. The use of these machines made it possible to almost completely mechanize all technological processes and give construction the character of in-line production with a high degree of industrialization .
Trench digging is an integral part of the construction complex and is one of the most time-consuming and responsible for the timing and quality of technological processes. For digging trenches at the construction of main pipelines, both universal single-bucket and special trench rotary excavators are used. In the latter case, the transverse profile of the trench is determined by the contour of the profile projection of the excavator working member. This makes it possible to optimize the excavator operation most fully by the volume of soil taken out of trenches [1].
Thanks to their high technical and operational performance, trench rotor excavators are becoming increasingly common in pipeline construction, as well as cable communication lines, in the construction of buildings for digging trenches for foundations, etc. [1].
For more efficient execution of technological processes, new equipment is needed for trench rotor excavators with improved characteristics.
On the basis of the above, the purpose of the graduation qualification work is to upgrade the equipment set for the trench rotor excavator.
Automation of construction processes
4.1 Purpose and objectives of machine automation
The need for the use of microprocessor equipment and robots in construction is caused by a number of reasons: an increasing shortage of personnel of machine operators engaged in construction work; the increased risk of many construction works; difficult working conditions of road construction machine operators; the complexity of machine management, which does not allow to ensure high quality of work and labor productivity .
Most machines are a source of dangerous noise and vibration levels. At the same time, the average acceleration amplitude of the operator's workplace in the vertical direction when the car is moving is 2 times higher than when the truck is moving, and the acceleration amplitude of the workplace when the truck is moving is 3... 4 times higher than when the car is moving .
Operators of single-bucket excavators when digging soil and loading machines mainly perform monotonically repeated operations, consisting of 12 elements, the average duration of which is 24 seconds. During the shift, the operator performs more than 350 such operations; at the same time, the number of necessary clutch switches and clutch switches of many road construction machines in 2... is 3 times the number of clutch switches and clutch switches of cars operating in the city .
Such working conditions of road construction machine operators are the cause of their rapid fatigue and occupational diseases, which negatively affects the quality of work and labor productivity. In order to overcome these disadvantages, which are exacerbated by the complexity of the designs of modern machines, with increasing their speeds and workloads, it is necessary to implement automation tools. The main tasks of machine automation are as follows:
1. Increasing productivity and freeing the workforce through the introduction of advanced construction technologies and the reduction of the duration of the work cycle;
2. Improving the quality of works by improving the accuracy of installation of working elements and constant tracking and adjusting their position in the process ;
3. Improve operator working conditions by automating frequently repeated operations and freeing the operator from heavy physical activity;
4. Improvement of occupational safety during operation in unfavourable and dangerous conditions by remote control of the machine and its working equipment, as well as installation of sensors and safety devices based on microcomputers, which signal the approach of dangerous situations and block the machine drive in case of overloads and malfunctions;
5. Improving reliability of machines and working equipment by optimizing power and speed modes of operation of the drive and operator information on the state of machine systems and assemblies;
6. Increase of economic efficiency of machines operation due to optimal use of engine power, creation of optimal conditions of fuel combustion in the engine, as well as more economical consumption of construction materials during planning works, concreting of structures and other types of works [9].
Automation of machine control and monitoring systems. Automated control and monitoring systems perform functions of control of machine drive by constant comparison of actual characteristics and parameters of machine and its operating equipment with optimal characteristics and parameters programmed in microcomputer memory. Such a system can control the sparking moment to ignite the working mixture in the cylinders of the engine, or control the economizer through which the fuel is supplied to the mixing chamber of the carburetor, from where the enriched mixture enters the cylinders of the engine.
Computer systems that control the torque and speed of the machine by acting on its gearbox are becoming increasingly common. The automatic selection and shift of gears in these machines is based on the readings of sensors located on the engine shaft and on the output shaft of the gearbox. These sensors perceive a change in the load and speed modes of operation of the engine and transmission and transmit this information to the computer in the form of input signals. Input signals entering the computer are compared with programmed analogue and already in the form of output signals-commands are transmitted through signal amplifiers to magnetic gear shifters, which directly perform gear shifting corresponding at the given moment of time to optimal mode of operation of the machine [9].
4.2 Automation of multi-tower excavators
A chain multichannel excavator is an excavating machine, the working element of which is a bucket chain moving in a vertical plane coinciding with the direction of movement of the machine. Soil separated from the massif rises into the unloading zone at the upper end of the bucket chain and is laid along the edges of the trench with the help of a belt conveyor.
The process of the chain excavator is automated in terms of maintaining a given slope of the bottom of the trench and optimizing the ground intake mode.
In copy systems preset slope of trench bottom is achieved by means of connection of tracking device of system installed on moving machine with base line in the form of light beam or cable, which is carried out parallel to future bottom of trench [10].
Operation of excavator with copy control system is performed as follows. After the route is split, the baseline is determined and the machine is set to the target of the future trench. Then, in the manual control mode, the working member of the machine is buried at the design mark, after which the servo device of the system is adjusted for operation in automatic mode.
During operation of the system with the base line in the form of a copy cable 1, two contact displacement sensors 2 mechanically connected to the frame of the bucket chain, between which the copy cable 1 passes, are used as sensors of the position of the working element. Touching the cable by either of the two sensors causes the corresponding contact of the sensor 2 to close. If the cable does not touch any of the sensors, the bottom of the trench is at the design elevation [10].
The system has two modes of operation: manual and automatic. The required mode is set by the switch. If a beam is used as a base line, then a laser installation is used (Figure 4.1 c). It consists of a LI laser emitter mounted on a rack 4 and a photodetector (PCF) with a movement mechanism (MT) (electric motor with a reduction gear) located on a working machine. The laser emitter has a laser with a collimator 1, a rotating prism 2, an electric motor with a reduction gear 3, a level and micrometric screws for setting the inclination angle of the base line, which can be set from 0 to 3 °. A laser beam with a diameter of 1... 1.5 mm with an angle of divergence 7... 8 is supplied to a collimator, which reduces the divergence of the beam to 30 "and increases its diameter to 3 cm. From the collimator, the beam is supplied to a rotating prism 2, where it is refracted by 90 ° and goes into space at height H3, scanning the plane. Laser emitter is fed from accumulator 6. The electrical circuit operates as follows: using the universal switch SA, the mode is set to manual or automatic, respectively, contacts 12.56 for manual mode and 34.78 for automatic mode are closed. By pressing the button SB1 or when the limit switch SQ1 is actuated, voltage is supplied to coil K1, contacts K1.3 and K1.2 are magnetized and contact K1.4 is opened, thereby starting the time relay and electric bolt, the trench excavator rotor rises until the contact of coil KT1 opens. Analogous to deepening of trench excavator rotor.
Conclusion
As a result of the work, equipment was developed for mechanizing the trench arrangement process.
Based on the patent and literary analysis, the direction of development of the working organ of the rotary trench excavator was chosen. The design was worked out, the rotor and rotor drive parameters were calculated.
A process diagram of the rotor excavator operation during the trench arrangement has been developed, a work schedule has been developed, calculations of the scope of work and the needs of auxiliary equipment have been made.
The section "Automation of construction processes" introduced leveling laser control of rotor excavator operation.
Maintenance and safety regulations have been developed.
звездочка.cdw

спецификация ротор.spw

чертеж ротора.cdw

Т СП.cdw

Траверса.cdw

сбор. ротор.cdw

палец.cdw

Комплект оборудования для устройства траншей.cdw

КОЛЕСО.cdw

рабочий орган.spw

Спецификация РОТОР СБОР.spw

Спецификация экскаватор.spw

Шестерня.cdw

Similar materials
- 29.07.2014
Free downloading for today
- 20.03.2023