Power supply and electrical equipment of the mechanical workshop of VK Promenergoremont LLP










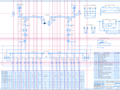
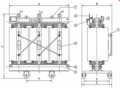
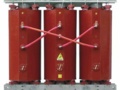
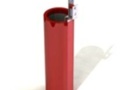
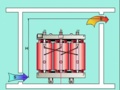
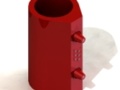
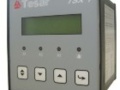
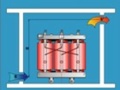
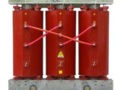
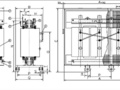
- Added: 21.11.2021
- Size: 3 MB
- Downloads: 5
Description
DIPLOMA PROJECT
Topic: Power supply and electrical equipment of mechanical workshop of "VK Promenergoremont" LLP
Project's Content
![]() ![]() ![]() |
![]() ![]() ![]() |
![]() ![]() ![]() |
![]() ![]() ![]() |
![]() |
![]() ![]() ![]() |
![]() ![]() ![]() |
![]() ![]() ![]() |
![]() ![]() ![]() |
![]() ![]() ![]() |
![]() ![]() ![]() |
![]() ![]() ![]() |
![]() ![]() ![]() |
![]() ![]() ![]() |
![]() ![]() ![]() |
![]() ![]() ![]() ![]() |
![]() ![]() ![]() |
![]() ![]() ![]() ![]() |
![]() ![]() ![]() |
![]() ![]() ![]() |
![]() ![]() ![]() ![]() |
![]() ![]() ![]() |
![]() ![]() ![]() |
![]() ![]() ![]() ![]() |
![]() ![]() ![]() |
![]() ![]() ![]() |
![]() ![]() ![]() |
![]() ![]() ![]() |
Additional information
Contents
1 Production technology
2 Selection and substantiation of power supply scheme of installed electrical equipment for mechanical workshop of "PEER" VK LLP
3 Calculation of electrical loads
3.1 Calculation of electrical loads up to 1000V
3.2 Calculation of lighting load by specific power
3.3 Calculation of reactive power compensation at 0.4kV side
3.4 Power Transformer Selection
4 Calculation of short-circuit currents
4.1 Calculation of short-circuit currents on 10 kV buses of the main lowering substation
4.2 Selection of input cable for power transformer power supply
4.3 Calculation of short-circuit currents on the 10 kV side of FPCS
4.4 Calculation of short-circuit currents on the 0.4kV side
5 Selection of protective switching equipment and conductor products for 0.4kV
5.1 Determination of peak current for SR
5.2 Selection of input and section circuit breakers
5.3 Selection of protective, switching equipment and conductor products to the unit and one electric receiver
6 Selection of electrical equipment and conductor products up to and above 1000V
6.1 Selection of busbars on the 0.4kV side
6.2 High Voltage Fuse Selection
6.3 Selection of load switch and disconnector
6.4 Selection and check of current measuring transformer
7 Relay protection and automation
7.1 Power transformer relay protection
8 Calculation of grounding device and check of operating conditions of protective equipment for 0.4kV with blind neutral grounding
8.1 Calculation of grounding device of shop transformer substation
8.2 Check of operating conditions of protective devices at single-phase closure in networks with voltage up to 1000V
9 Operation and repair of dry power transformer "Tesar" 250kVA
9.1 Comparison of dry and oil transformers
9.2 Operation of dry transformers
9.3 Tesar 250kVA power transformer design
9.4 Advantages of 250 kVA dry transformers
9.5 Dry Transformer Repair
9.6 Repair technology of individual units
10 Electric drive of bridge crane Q = 20t
10.1The purpose and arrangement of the crane
10.2 Calculation of static power of bridge movement mechanism
10.3 Selection of bridge engine type and power
10.4 Calculation and construction of mechanical characteristic
10.5 Calculation of starting resistances
10.6 Selection of bridge electrical equipment
10.7 Selection of main trolls
10.8 Description of electrical circuit operation
11 Economics and organization of production
11.1 Planning of repair and maintenance of workshop equipment
11.2 Calculation of the number of personnel required for repair and maintenance of electrical equipment of the workshop
11.3 Calculation of the number of repair personnel
11.4 Calculation of the number of maintenance electricians
electrical equipment of the workshop
11.5 Calculation of the planned annual wage fund of workers (F.Z.P.)
11.6 Calculation of tax contributions to the budget
11.7 Calculation of energy costs (power and lighting)
12 Safety, Fire and Environment
12.1 Organization of safe operation of electrical installations
12.2 Safety measures taken in the designed electromechanical workshop of VK PEER LLP
12.3 Electrical Machine Maintenance Safety
12.4 Regulations for the use and testing of protective equipment used in electrical installations
12.5 Fire Protection Measures
12.6 Safety precautions for maintenance and repair of crane electrical equipment
13 List of literature used
1 manufacturing technology
In the repair shop of electric machines, asynchronous and synchronous motors and generators of any power are repaired, as well as transformers with a voltage of up to 1000 V are repaired. On the site of non-standard equipment, industrial and boiler equipment is repaired, as well as the manufacture of turbines, impellers, cooling systems, and water supply.
The mechanical workshop is equipped with machines (more than 70) for various purposes, including a lathe-carousel of type 1M557 with Ø tablets 2800 mm, a longitudinal-strict machine model 7212 with the ability to process a 4m long part, a sheet bending press model IB1430A with a force of 100 tons, surfacing machines and other unique equipment according to repair technology. For heat treatment of parts and tools there are 4 furnaces.
The availability of special equipment for the preparation of transformer oil and the drying of transformers allows you to carry out work at the factory repair level.
The workshop for the repair of electric motors and generators is equipped with a full set of technological equipment and repair equipment, including a special machine for welding collectors of DC electric machines at the level of factory characteristics.
The different orientation of the workshops and their equipment make it possible to carry out comprehensive repair of equipment by the industrial-factory method, to manufacture non-standard products and special devices, tools, spare parts.
SELECTION AND justification of power supply scheme of installed electrical equipment for mechanical workshop of VK "PEER" LLP
According to the task, the workshop belongs in terms of reliability of power supply to consumers of the second category, since the break in power supply will be associated with underfilling of products and the downtime of a large amount of equipment. The network does not require overload protection, in the workshop the ambient temperature is + 25C, the environment is clean.
Equipment class 1 (protection against electric shock is provided by the main insulation and connection of open conductive parts accessible to touch, by the protective conductor of the stationary installation, in this case the open conductive parts accessible to touch cannot be energized when the insulation is broken, after the protection is activated).
Based on the above, the designed workshop receives power from 2 independent sources, i.e. from different TDP5 buses. The workshop receives power from two power transformers "Tesar" 25010/0.4.
High-voltage switchgear is equipped with KSO292 cells. Two power transformers "Tesar" 25010/0.4 are powered from the high-voltage switchgear.
Input on shop substation is carried out by a cable of brand AAShvU-10-2 (3х16) Idop = 75A, on one cable on input. In a cell of CSR the following equipment is installed: RVZ104001UZ disconnectors, high-voltage PKT1021031,531,5UZ, switch safety locks of loading like VNPup10/40010UZ, transformers of current of the TPL1030/5UZ type.
The low-voltage substation is equipped with ShchO70 panels with VA7440 machines at the inlet and a sectional automatic.
Two compensating devices of UKM630,412525UZ grade are installed in the substation. All electrical equipment of the workshop is powered from ten SR by the APV wire, SR is powered from the substation by the AVVG cable.
To control electrical equipment, magnetic starters of the PML type with RTL thermal relays were selected, equipment protection is carried out by VA series machines.
In the workshop, working lighting is made with lamps with DRL, emergency consecration is made with lamps with incandescent lamps.
All equipment of the workshop is grounded and busy.
Relay protection and automation
7.1 Power transformer relay protection
7.1.1 To protect the power transformer from damage, the following types of protections are used: maximum current protection against through short-circuit currents, protection against single-phase ground faults on the low voltage side, current cut-off in case of short-circuits on the high side and protection against ground faults on the 10 kV side.
7.1.2 Protection against single-phase ground faults in a network with a de-grounded neutral is performed for disconnection and is carried out by a circuit breaker with a maximum disconnector installed on the 0.4 kV side.
Operation and repair of dry power transformer "tesar" 250kva
9.1 Comparative analysis of dry and oil transformers:
Recently, consumer interest in the use of dry transformers has increased significantly.
Of course, in some cases, the choice of the KTP option with a dry transformer is the only one, when there is no other possibility at the site for the construction of a substation, as soon as inside the structure - for example, in the production shop, in the basement or on the floor floor of a residential building, or on the territory of the educational institution, in the park area, etc., i.e. in places where requirements to transformer design are dictated by increased requirements in terms of environmental and fire safety.
On the other hand, the transformer, even dry, refers to high voltage equipment and is itself an object of increased danger. Accordingly, the transformer is always located only inside the complete transformer substation in the protected compartment. It also has low and high voltage switchgears inaccessible from the outside, and this is the only way to ensure the required level of safety against electric shock. Moreover, it should be noted that touching the outer surface of the cast winding of the connected dry transformer results in electric shock, thereby, in a dry transformer in the absence of a fence, the damaging surface is much larger than that of an oil transformer.
Now you can often hear that the introduction of dry transformers significantly saves time for servicing electrical installations, up to the complete absence of the need for such. As you know, in the total working time for maintenance of electrical installations, one of the most significant operations is periodic inspection. If you familiarize yourself with the content of the standard inspection card of the FTC, which, depending on local conditions, is carried out at different intervals, but at least once a quarter, it becomes clear that the scope of work during the inspection of the FTC practically does not depend on the design of the transformer used in it.
It is known that a significant proportion of damage to distribution transformers occurs due to weakening of bus connections at the LV output external contacts and, independently, a dry transformer or oil, these contacts require periodic attention and care. On the oil transformer, overheating of the contact will cause destruction of the insulator or depressurization of the seal, in any case the repair of such damage is not a special problem. On the dry transformer at this type of damage, due to less efficient cooling of the overheating zone and intense heat transfer through the conductor to the winding, the cast insulation in the zone of the leads from the winding is destroyed, which will certainly lead to the need to replace the winding unit in the damaged phase. Of course, measures can be taken to improve the quality of current collection, but even in the presence of hardware clamps that can be equipped with all oil transformers of production, starting from 16 kVA and above, these units should still be periodically inspected and maintained. And if we are talking about a dry transformer, then even more so.
Despite the use of deep vacuum in the manufacture of monolithic windings of dry transformers, there is still a difference in the coefficients of thermal volumetric expansion of conductor materials and cast insulation, in connection with which, the blocks of windings of dry transformers during operation are subject to micro-damage, which leads to the appearance of so-called partial discharges. What is partial discharge and what is it dangerous? The microcrack creates a boundary contact between two different dielectric media, so that an increased electric field strength occurs in this zone, which inevitably causes a continuous, as if smoldering, breakdown inside the microcrack. At this point, the insulation is gradually charred, which subsequently develops into an interturn or interlayer short circuit and leads to the winding burnout. The process can develop for weeks, even months, but almost remains invisible, up to the time of the accident. Partial discharges can be detected only by special devices. As a matter of fact, the problem of monitoring the absence of partial discharges in distribution transformers arose in connection with the appearance of dry transformers. In oil transformers, partial discharges can theoretically occur when there are microbubbles of air somewhere in paper-oil insulation, but, thanks to the evacuation technology during oil preparation and filling, oil transformers are usually not susceptible to this type of damage.
Defects in insulation in dry transformers can also occur in case of violation of permissible climatic conditions of their use. This means not only the operating conditions of transformers, but also the conditions for their storage before commissioning. As a rule, the lower limit of the temperature of use of dry transformers is limited to a value of -25 ° C.
In conclusion, it should be noted that in each case it is necessary to take into account the actual operating conditions of the equipment, which will ensure a more complete reflection of the compared technical and economic indicators and its optimal selection.
9.2 Operation of dry transformers:
9.2.1 250 kVA dry transformers with cast insulation:
Dry transformer with cast insulation 250 kVA is designed to distribute electricity with a rated capacity of 250 kVA and voltage up to 36 kV. Dry transformers with cast insulation from epoxy resin type TR250 kVA are manufactured by the Italian plant TESAR SRL, which is one of the international leaders in the production of power dry transformers. Tesar dry transformers have high reliability, ease of operation, compactness, fire and environmental safety. Dry transformers are used in various industries with stringent fire and explosion safety requirements.
9.2.2 Dependence of characteristics on insulation type:
Experience in the operation of oil-filled power transformers of medium voltage classes shows that these transformers work reliably for decades, provided that their condition is properly monitored and defects are eliminated in a timely manner. In other words, this equipment requires periodic maintenance and repairs, resulting in significant operating costs.
9.2.3Cast insulation:
At the initial stage of the development of dry transformers, vacuum filling of manufactured windings with epoxy compounds was used. Such cast-insulated transformers are now produced both abroad and in Russia and the CIS countries. With all the advantages associated with ecological cleanliness, fire safety, small dimensions, etc., the main disadvantage of these transformers is that in harsh climatic conditions, with a large temperature difference, it is possible to form microcracks in the epoxy compound, penetrate water into them and ultimately damage the winding.
9.2.4 Glass fiber reinforced epoxy insulation:
In recent years, another type of dry transformers offered by ABB has appeared - Resibloc. By design type, they approach rather cast transformers, however, glass bundles are used to increase the cracking resistance of the epoxy compound. According to ABB, in 20 years of operation, cracking was never detected in these transformers.
9.2.5 Challenges and Prospects:
The main problem of dry transformers is the limitation of their maximum power due to cooling conditions. Until recently, it was believed that the power limit for dry transformers is 15 MVA. According to the ABB concern, dry transformers of the Resibloc type with a capacity of up to 40 MBA are already being produced and in the future the company is going to bring this value to 60 MVA.
Considering that today dry transformers are used only in middle voltage classes, these values with a margin cover the needs of distribution networks.
9.3 Tesar 250kVA power transformer design:
9.3.1 Dry power three-phase transformers 250 kVA consist of three main parts:
- Low voltage winding;
- High voltage winding;
- Magnetic core.
9.3.2 Windings of 250 kVA dry transformer:
The low voltage windings of Tesar dry transformers are made of a single aluminum sheet, which is pre-impregnated with Class F insulation materials. The coils are then subjected to heat treatment polymerization. Special structural geometry allows, in addition to high resistance to electrodynamic forces, to also minimize the scattering flow for electromagnetic compatibility.
The high voltage windings of Tesar dry transformers are made of aluminum tape. Special assembly technology (vacuum filling of the active part of the winding with an insulating material) and special compatibility of the materials used (aluminum and epoxy resin have very similar expansion factors during heating) make it possible to obtain a winding in which there are practically no internal mechanical stresses. During the casting process, each parameter is monitored electronically to obtain uniform dielectric characteristics of the resin.
9.3.3 Magnetic core of dry transformer TR-250:
The magnetic core of the dry transformer is made of high-quality electrical textured steel with low specific losses. When manufacturing a dry transformer core, a complete "Steplap" packing scheme is used, which is carried out using the most modern cutting and assembly technologies. The low noise level of the dry transformer is achieved by combining the correct shape of the core with reinforced metal frames.
9.4 Advantages of 250 kVA dry transformers:
No labor-intensive maintenance of dry transformer such as sealing, restoration of corrosion protection of tanks and oil cleaning. Dry transformers with moulded resin insulation Tesar are designed to work in the most difficult climatic conditions of the environment, so preventive maintenance is reduced to a simple inspection of the transformer and verification of connections and temperature sensors.
Save on installation of dry transformer:
Simple and inexpensive preparatory installation works;
Compact dimensions of dry transformers;
Possibility to install dry transformers of higher power in existing transformer substations of KTP at reconstruction due to small dimensions of dry transformers.
Resistance of dry transformers to dusty or wet environment.
Maximum Security:
- high resistance of dry transformers to spontaneous combustion and low level of toxic gases release;
- natural cooling of dry transformers, carried out by atmospheric air, and not by fire hazardous and polluting liquids;
- absence of possibility of dry transformer overheating: temperature measurement and control is carried out using a thermal controller and temperature sensors. Thermal sensors also help control the fans installed on the dry transformer.
-Energy saving: reduction of losses in electric power lines and cable costs in low voltage networks due to the closest possible arrangement of a dry transformer to electric power consumers.
- Economy during operation of dry transformer due to low losses in magnetic core and windings.
-Low noise level of dry transformer.
High reliability of dry transformers:
- Absence of partial discharge;
-Expressed product reliability due to high processability of winding production process;
- The ability of dry transformers to operate at temperatures lower than those allowed by the insulation materials used;
- Possibility to increase load capacity of dry transformers up to 40% due to application of forced ventilation system.
9.5 Repair of dry transformers:
9.5.1 Servicing:
Careful inspection of the transformer during its operation allows preventing faults, as well as extending the average service life.
Under normal operating conditions, it is sufficient to perform the following operations at least once a year:
- Cleaning of Medium/Low Voltage winding from possible deposits of dust, condensate and contaminants with a stream of dry compressed air under low pressure and dry rags
- Cleaning of cooling and ventilation channels between windings to prevent overheating during operation.
- Check of tightening of high and low voltage connection and plates of voltage adjustment devices, tightening of yoke bolts.
-Control correct functioning of thermal protections (temperature sensors and temperature control unit), as well as correct intervention of overload and short-circuit protections, as well as disconnection of the corresponding circuit breaker. The monitoring should preferably be carried out by means of special devices that simulate a real fault.
Electric drive of bridge crane, q = 20t
10.1 Purpose and arrangement of the crane
In the workshops of the enterprise there are cranes of various types: bridge, goat, crane - beams.
The design of the installed crane is mainly determined by the specifics of the workshop and its technology. However, many crane equipment units, such as the lifting and moving mechanism, are of the same type for many crane designs. Therefore, there is much in common in the selection and operation of electrical equipment of cranes for various purposes.
The electrical equipment of cranes usually works in difficult conditions from the point of view of the influence of the environment: increased dust content, increased temperature or sharp temperature fluctuations, high humidity, the influence of various chemical reagents. Therefore, the electrical equipment of the cranes must be selected in the appropriate design.
Given the responsibility of cranes, their electrical equipment is subject to a number of stringent requirements, the most important of which are: ensuring high performance, uninterrupted operation, service safety, ease of operation and repair.
It should be understood that cranes of different design and purpose are equipped with typical controllers, brake electromagnets, resistances, limit switches, protection and control panels and other electrical equipment.
The electric motors of most cranes operate again - in short-term mode. The operation of the crane drive motors is characterized by significant overloads, frequent starts and reverses. The steady state time of the crane motor is usually not long compared to the duration of the starting and braking modes. In this regard, the operation of the motor is significantly affected by the dynamic load. Electric motors of crane mechanisms operate in conditions of increased shaking and vibration. In a number of workshops, they are also exposed to high temperatures (about 60700C), vapors and gases. Therefore, crane motors have special requirements regarding reliability and serviceability in heavy operating conditions. Reliability of operation of electric equipment of cranes, in particular their electric motors, is a matter of primary importance. Failure of the crane motor can cause a simple technique with all the ensuing consequences - an economic one. Therefore, special crane-metallurgical electric motors of a short-term mode are produced for driving the crane mechanisms, differing from general-purpose electric motors by increased overload ability, mechanical strength by reduced rotor flywheel moment, lower costs of non-ferrous metal of windings and steel of the magnetic system, etc.
Three-phase asynchronous electric motors and DC motors are used to drive crane mechanisms. Asynchronous motors with a phase rotor are most useful, providing speed control, smooth start and start at a moment equal to the maximum (with appropriate selection of resistance).
Asynchronous short-circuited rotor motors are used less often (for the movement mechanisms of some slow-moving cranes), since they have a slightly reduced starting torque, significant starting currents and do not provide smooth speed control. A significant advantage of asynchronous motors (compared to DC motors) is their relatively lower cost, ease of maintenance and repair.
Расчётно-пояснительная записка(6).pdf
Лист 4 Схема крана 20тонн.cdw

Лист 1. План ВК ПЭР.cdw

Лист 2_Схема снабжения.cdw

Лист 3.cdw.cdw

Similar materials
- 04.11.2022
- 07.04.2021
- 04.11.2022
Free downloading for today
- 24.01.2023