Piston compressor 2-stage, V-shaped
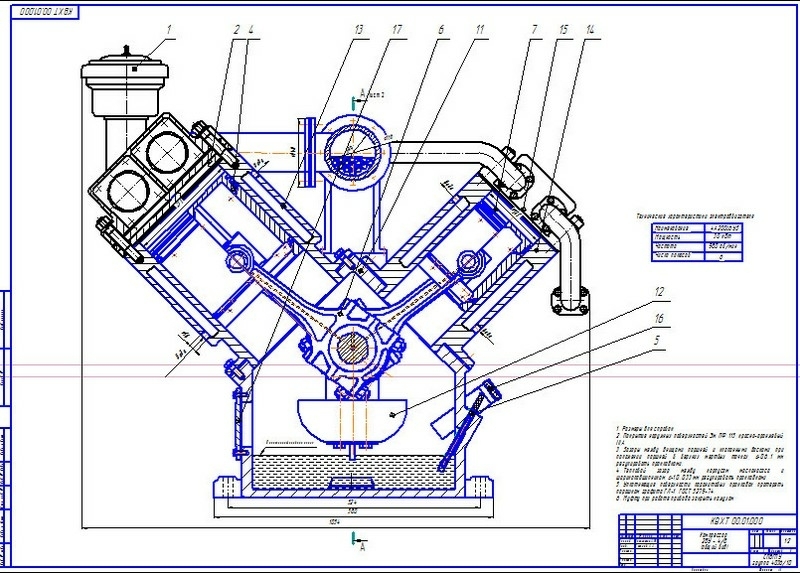
- Added: 09.07.2014
- Size: 1 MB
- Downloads: 6
Description
Project's Content
![]() |
![]() |
![]() ![]() ![]() ![]() |
![]() ![]() ![]() |
Additional information
Contents
Introduction
Terms of Reference
Select Compressor Diagram
1. Thermodynamic calculation of two-stage compressor
1.1 Determination of required number of compression stages in compressor
1.2 Pressure distribution by compression stages
1.3 Determination of second volumes described by pistons of the first and second stage
1.4 Determination of active area of pistons
1.5 Determination of preliminary values of cylinder diameters
1.6 Determination of compressor crankshaft speed
1.7 Determination of compressor indicator power
1.8 Determination of compressor power consumption
1.9 Determining the Useful Effect of the Compressor
1.10 Engine selection
2. Dynamic calculation of compressor
2.1 Determination and balancing of inertia forces
2.2 Flywheel calculation
2.2.1 Construction of indicator diagrams
2.2.2 Construction of power diagrams
2.2.3 Diagram of total counter moment
3. Compressor check calculation
3.1 Calculation of compressor first stage
3.2 Calculation of the second stage of the compressor
4. Strength calculation
4.1 Calculation of piston pins for strength
4.2 Calculation of connecting rod for strength
4.3 Calculation of pistons for strength
4.4 Calculation of piston rings for strength
4.5 Crankshaft strength calculation
5. Calculation of heat exchanger
5.1 Determination of coolant flow rate
5.2 Determination of heat exchange surface area
5.3 Determination of main geometrical parameters of gas cooler
6. Grease Selection
Conclusion
Literature
Applications:
Item 1. The KBXT 00.00.000 specification Compressor 2VU - 4/
Item 2. General view of the KBXT 00 compressor.
Introduction:
The course project is devoted to the development of the design of a two-stage piston compressor in accordance with the requirements of the specification. The technical documentation developed includes the following main documents:
Compressor specification - 1 sheet f. A4
General view of compressor - 2 sheets f. A1
Explanatory note - 60 sheets f. A4
The design of the piston compressor is a cast base on which cast, cast iron cylinders of both stages with a collapse of 90 deg are mounted, cooled by water in the provided jackets. Also mounted in base is single-ring shaft, with connected stamped connecting rods with I-rod, which are attached to pistons in cylinders through piston pin. The pistons are cast, the first is made of aluminum alloy, and the second is made of cast iron. Each piston has two sealing (compressor) rings.
Air sucked from the room is supplied through the filter to the cylinder of the first stage. Initial temperature tn = 12 deg and initial pressure pn = 0.1 MPa is accepted according to TA. From the first step air comes to the intermediate water gas cooler after which gas compresses in the second step and =0.8 MPas come to the delivery pipeline of network with Rk.
To obtain the diameters of the pistons and select the drive, a thermodynamic calculation of a two-stage compressor was carried out, during which the diameters of the pistons of the first and second stages 230 mm and 140 mm, respectively, were determined.
The Compressor is driven by an asynchronous motor 4A200L6UZ with a capacity of 30 kW. A flange clutch is provided for torque transmission. Standard prismatic keys are used to connect the shaft to the half-couplings. To ensure safe maintenance of the compressor, the rotary clutch shall be covered by a protective enclosure.
In order to balance the inertia forces of rotating masses and the inertia forces of the first order of reciprocating moving masses of the compressor, a dynamic calculation was carried out, as a result of which the masses of cast iron counterweights were determined. It has also been determined that the flange clutch and the motor rotor act as a flywheel.
The calculation of losses in band valves was carried out using the computer program of the Department of KVKhT.
The check calculation of the crankshaft in two dangerous sections showed that the cyclic strength condition is met. A strength calculation of the piston rings, the piston pin and the connecting rod was also carried out, during which it was determined that all of them met the strength conditions.
Rolling bearings were selected in accordance with the mounting diameters of the shaft. Elimination of axial plays in bearings is performed by means of set of adjusting gaskets and fitting with compensating rings.
Lubrication of cylinders and bearing units with connecting rods is performed separately. To lubricate the cylinders, industrial oil 30 is used and a crankcase method is used - by dipping special rods fixed to counterweights into an oil bath, the level of which is controlled by a rod oil indicator. To remove oil from the cylinders, 2 oil removal rings and holes are provided in the piston for more abundant lubrication of the piston pin. Lubrication of connecting rods, piston pins and bearing assemblies is carried out in a forced manner using a vane pump, which can be adjusted to supply the necessary amount of oil by selecting the appropriate bevel gears. For inspection of the crankshaft, a viewing hatch is provided in the compressor housing. Waste oil is drained through an oil drain hole in the crankcase closed with a threaded plug.
Compressor cooling - water. Water passing through the gas cooler and cylinders enters the drain funnels. Cooling water pressure shall not exceed 0.25 MPa.
Terms of Reference
Angular Piston Compressor Design Assignment
Compressed gas - air;
Final pressure of R_k air is =0.8 MPas;
Compressor capacity V ̅_h=4 m ^ 3/min;
Reference temperature of air - T_n =285 K;
Relative air humidity A = 0.7;
Initial pressure of air - R_n of =0.1 MPa;
Temperature of the cooling water - τ _ 1=20 ℃;
Undercooling temperature 〖 ∆t 〗 _ (insufficient) =15℃;
Coefficient α for the determination of γ _ t - α = 0.95
Tightness coefficient - γ _ herm = 0.98
Relative dead space of stage I - a ^ I = 0.05
Relative dead space of the II stage - a ^ II = 0.06
Relative losses at suction of I stage β _ start ^ I = 0.05
Relative losses at suction of II stage β _ start ^ II = 0.04
Relative losses at injection of I stage β _ kon ^ I = 0.04
Relative pressure losses of stage II β _ con ^ II = 0,032
Calculation of heat exchanger
The purpose of the cooling chamber (inter-stage and end) is to reduce the temperature of the gas before it is supplied to the working chamber. The need to use an interstage refrigerator is due to the fact that after compression the gas can have a very high temperature, the action of which can result in a decrease in productivity or even in ignition of lubricants and, therefore, breakage of the power machine. The use of end coolers can be explained by the requirements for the temperature of the customer of the project, as well as the fact that when gas is injected under pressure into a certain cavity at a certain temperature, the value of the gas pressure during cooling will decrease according to the basic law of thermodynamics.
6. Grease Selection
When choosing a lubricant, a number of requirements should be provided: sufficient viscosity at operating temperatures, stability of properties, good mobility, as well as some important details: ignition temperature, compressible gas (when using mineral oil in a compressor where oxygen is compressed or other aggressive gases can lead to explosion), the higher the speed, the lower the viscosity.
Let's choose industrial oil 30 with a viscosity of 27-33 cSt and a flash point of 180 degrees Celsius.
The lubrication system (circulation) is designed to use the rotation of the crankshaft, that is, the oil created by the pressure difference created by the vane pump is supplied to the internal channel of the crankshaft, then the part is sprayed into the bearings by means of exits from the channel, and the other part comes through the channel in the connecting rod upwards and lubricates the piston pin.
Conclusion
During the task, a two-row air piston compressor 2VU4/8 was designed to supply compressed air with some pneumatic device or equipment in various industries. The compressor is a two-stage raceless power machine with a 90-degree cylinder collapse.
The machine compresses air from atmospheric pressure to a pressure of 0.8 MPa, and in the interval between the stages the air is cooled in a water intermediate gas cooler.
Поршневой Компрессор 2ВУ-4.8.cdw

Similar materials
- 04.11.2022
- 24.04.2014
- 20.04.2020